浅议数控机床加工中c刀具补偿下的过切现象
浅析数控铣床加工中的过切现象

浅析数控铣床加工中的过切现象数控铣床加工过程中的过切现象是指刀具加工零件时,部分物料被过度去除,导致零件尺寸超出设计要求或失去原有的几何形状。
在数控铣床加工中,过切现象是一个常见的问题,它会导致零件的精度和质量下降,同时也会增加生产成本。
造成过切现象的原因通常有以下几个方面:1. 零件破碎或变形:在铣削过程中,零件可能会由于切削力过大或刀具与工件接触过度,导致零件变形或破碎,进而出现过切现象。
2. 刀具磨损:刀具磨损也是过切现象的主要原因之一,因为磨损过多会导致刀具几何形状发生变化,从而影响零件的尺寸和形状。
3. 刀具切削参数不合适:切削参数,如进给速度、切削速度和切削深度等,都会影响加工质量。
如果这些参数设置不合适,就会导致刀具切削过度,出现过切现象。
4. 机床刚度不足:机床刚度不足也是导致过切现象的一个原因,因为当刀具受到振动或弯曲的影响时,就容易出现过度切削的情况。
针对过切现象,可以采取以下措施:1. 合理选择刀具:合理选择刀具也是避免过切现象的重要措施之一。
不同零件加工需要不同类型刀具,因此需要根据加工情况确定刀具种类和规格,以达到最优的加工效果。
2. 优化加工参数:要避免过切现象,需要对加工参数进行优化调整,以使刀具与工件的接触optimal。
3. 提高机床刚度:提高机床的刚度也是减少过切现象的一个有效手段。
可以在加工过程中适当减少工件的振动或采用一些减震控制器或减振装置等。
4. 完善的加工流程:完善的加工流程对于避免过切现象也是非常重要的。
加工前需要对零件进行充分的工艺规划和准备,防止出现过渡加工和不良的加工流程,从而降低过切现象的发生率。
总之,避免过切现象需要全面、合理的加工参数和工艺规划,并保证机床刚度优化和刀具选择合适。
只要提高零件加工的精度和质量,相信会有效提高产品的竞争力和市场占有率。
浅析数控铣床加工中的过切现象

浅析数控铣床加工中的过切现象数控铣床是一种高精密度金属加工设备,常常用于制造汽车零件、航空零件、医疗设备等高精密度产品。
但是,在数控铣床加工中,经常会出现过切现象,对产品质量造成不良影响。
本文将浅析过切现象的成因和解决方法。
一、过切现象的成因1. 刀具和夹具的不匹配:刀具和夹具的不同规格和型号会影响加工过程的精度和质量。
如果刀具和夹具不匹配,就容易造成加工过切现象。
2. 刀具磨损:随着使用时间的增加,刀具会逐渐磨损,磨损会使刀具变得钝,不能有效切削工件,从而导致过切现象。
3. 工件夹紧力度不足:工件夹紧力度过小会导致工件移位或振动,从而使工件表面出现过切现象。
4. 动态误差:数控铣床中的动态误差是由于加工时机床的动态特性所造成的。
例如,加工过程中刀具和工件的振动会导致误差和过切现象。
5. 加工参数的选取不合适:加工参数是影响加工过程的重要因素。
如果加工参数选择不合适,就会导致加工过程出现过切现象。
二、过切现象的解决方法1. 更换刀具和夹具:当刀具和夹具不匹配或磨损时,需要及时更换刀具和夹具,以保证加工精度和质量。
2. 调整工件夹紧力度:工件夹紧力度过小时,可以适当加大夹紧力度,以防止工件移位或振动。
3. 优化加工参数:通过调整加工参数,提高加工效率,降低加工过程中出现过切现象的概率。
4. 加工前校准机床:对数控铣床进行定期校准,以减小动态误差,提高精度和稳定性。
5. 加强工件定位和支撑:加工前需要将工件正确定位和支撑,防止工件在加工过程中移动或振动,从而导致过切现象的出现。
三、结论过切现象在数控铣床加工中是一个普遍存在的问题。
为了避免这种现象的出现,需要从刀具、夹具、工件夹紧力度、加工参数、机床精度等多个方面进行考虑和优化。
同时,还需要加强操作技能和定期对设备进行维护,以确保加工质量的稳定和持续提高。
浅析数控铣床加工中的过切现象

浅析数控铣床加工中的过切现象数控铣床加工是现代制造业中常用的加工方法之一,它利用数控系统控制刀具在工件上进行不同形状的切削加工。
在数控铣床加工中,经常会出现过切现象,这给加工质量和加工效率带来了一定的影响。
本文将对数控铣床加工中的过切现象进行浅析,从而帮助读者更好地理解和解决这一问题。
一、过切现象的定义过切是指在数控铣床加工过程中,刀具在工件加工轮廓时,由于刀具路径计算或者机床控制系统的误差,导致刀具对工件轮廓进行了过量的切削,使得零件超出了设计尺寸。
在数控铣床加工中,过切现象是一个很常见的问题,特别是在高速加工和精密加工中更容易出现。
二、过切现象的原因1.数控程序编程错误:在数控加工中,过切现象最主要的原因之一就是数控程序编程错误,例如在程序编写过程中,误将刀具路径数据输入错误或者计算路径出现偏差等,都会导致刀具对工件进行过度切削。
2.刀具磨损和破损:刀具的磨损和破损也会导致过切现象的出现。
当刀具磨损过度或者受到撞击损坏时,切削刃失去原有的形状和尺寸,从而导致无法精准切削工件。
3.机床系统误差:数控铣床机床系统的误差也是导致过切现象的一个重要原因。
例如机床传动系统的间隙、螺杆传动系统的游隙、伺服系统的误差等,都有可能导致刀具的位置偏差,从而引起过切。
4.工件夹紧和定位误差:在数控加工中,工件的夹紧和定位对加工精度起着至关重要的作用。
如果工件夹紧不稳或者定位出现偏差,就会导致刀具对工件的切削位置偏差,出现过切现象。
三、过切现象的危害1.降低加工精度:过切现象会导致工件超出设计尺寸,从而降低工件的加工精度,影响产品的质量和外观。
2.增加加工成本:由于过切会导致工件超出设计尺寸,为了保证产品质量,通常需要进行二次加工或者退货重做,这将增加加工成本和人力资源成本。
3.影响加工效率:出现过切现象后,需要花费额外的时间和成本进行修复和调整,从而影响了加工效率和生产进度。
4.影响设备寿命:过切现象会导致刀具和机床的额外磨损,影响了设备的寿命和稳定性。
浅析数控铣床加工中的过切现象

浅析数控铣床加工中的过切现象数控铣床加工中的过切现象是指在加工过程中出现的一种误差,即刀具在加工完一个曲线轮廓后,继续行进一段距离,导致加工出的曲线轮廓线条比原本设计的轮廓更细或者更粗。
过切现象在数控铣床加工中是难以避免的,尤其是在高速加工时更容易发生。
过切现象发生的原因主要有以下几点:1.刀具半径与加工轮廓半径不一致当刀具的半径与被加工曲线轮廓的半径不一致时,就会出现过切现象。
如果当刀具的半径小于曲线轮廓的半径时,刀具就会过切,形成过切现象;反之,如果刀具的半径大于曲线轮廓的半径时,则会产生欠切现象。
2.工件表面的不均匀性当工件表面存在小凹坑或者凸起时,刀具在经过这些区域时,容易出现过切现象。
3.刀具磨损刀具经过长时间使用后,其切削边易出现磨损,此时刀具的半径就会发生变化,容易导致过切现象的发生。
4.加工速度过高在高速加工时,刀具在切削过程中,由于惯性的作用,使刀具在完成一次切削后继续行进一段较远的距离,导致刀具再次切削,形成过切现象。
针对过切现象的解决方法:1.调整刀具半径当发现过切现象时,可以通过加大或减小刀具半径的方式进行调整,使刀具半径与被切削轮廓的半径相匹配,从而避免过切现象的发生。
2.使用更加平滑的刀具在刀具切削外形曲线时,曲线的平滑度越高,过切现象发生的机率就越小,所以选择更加平滑的刀具会减少过切现象的发生。
通过降低加工速度可以减小刀具的惯性作用,从而减少刀具在切削完曲线轮廓后继续行进而导致过切现象的发生。
4.改善工件表面在加工前,先对工件表面进行研磨处理,尽量避免工件表面的凹坑或凸起。
总之,对于过切现象,我们需要从多方面来进行分析和解决,通过适当的调整机器参数和使用一些专业的研磨工具等办法,可以有效地控制和减少过切现象的发生。
浅析数控铣床加工中的过切现象

浅析数控铣床加工中的过切现象数控铣床加工是一种将工件用刀具进行切削加工的方法,通过控制刀具沿着工件表面的不同方向进行切削来加工出所需的形状和尺寸。
然而在数控铣床加工中,常常会出现一种现象,即过切现象。
本文将对数控铣床加工中的过切现象进行浅析。
过切现象是指数控铣床在加工过程中,刀具切入和退出工件表面时产生的过度切削现象。
它通常会导致工件表面出现明显的凹陷或突起,并且对工件的尺寸和形状也会产生一定的影响。
过切现象的产生原因有多种,首先是由于数控铣床加工过程中的进给速度不稳定所导致的切削过深。
当进给速度过快或过慢时,刀具与工件的相对速度就会发生变化,进而影响刀具对工件的切削深度。
若进给速度过快,切削深度就会增加,从而导致过切现象的产生;若进给速度过慢,则切削深度会减小,工件表面就会出现明显的凹陷。
刀具的刃磨状态和切削参数的选择也是影响过切现象的重要因素。
刃磨不良的刀具会导致切削力分布不均匀,进而引起过切现象的发生。
切削参数的选择也会对过切现象产生影响。
切削速度过快或切削深度过大,都会增加切削力,从而加重过切现象。
工件材料和工件形状也会对过切现象产生一定的影响。
不同的材料具有不同的硬度和切削性能,因此在加工过程中可能会产生不同程度的过切现象。
工件的形状也会影响切削力的分布,进而影响过切现象的产生。
为了减少和避免过切现象的发生,有以下几种方法可以采取。
合理选择刀具类型和磨削状态,确保刀具的刃磨良好,切削力分布均匀。
合理选择切削参数,控制好切削速度和切削深度,避免过大或过小。
还可以通过改变刀具进给角度和退刀角度来调整刀具与工件的相对运动速度,有效地减少过切现象的发生。
浅析数控铣床加工中的过切现象

浅析数控铣床加工中的过切现象数控铣床是一种用数控技术控制刀具在工件上进行铣削加工的机床。
在数控铣床加工过程中,常常会出现一种现象,即过切。
过切在工件加工中是一种不利的现象,不仅会影响加工质量,还会增加工件的成本和加工时间。
本文将从过切的原因、对工件的影响以及解决办法等方面进行浅析。
过切是指刀具在铣削加工中切削进入工件表面的深度超过了设计或要求的尺寸。
造成过切的原因主要有以下几点:刀具刚度不够、刀具偏心、切削力过大或切削参数设置不当等。
刀具刚度不够是指刀具在切削过程中容易发生振动或弯曲,导致刀具切削深度超过设计要求。
刀具偏心是指刀具与工件之间的相对位置偏移,导致刀具在切削过程中超出了设计要求的切削深度。
切削力过大常常是由于切削参数设置不当,如进给速度过快、切削深度过大或切削量过大等。
这些原因都会导致刀具在切削过程中超出了设计要求的切削深度,产生过切现象。
过切现象在数控铣床加工中有很大的不利影响。
过切会导致加工尺寸偏大,与设计要求不符,影响工件的质量。
过切会导致工件表面粗糙度增大,影响工件的表面质量。
过切会增加切削力和切削温度,加剧了刀具的磨损和损坏。
过切还会增加工件的成本和加工时间,因为需要进行修复或重新加工。
为解决数控铣床加工中的过切现象,可以采取以下几种措施。
选择刚度较高的刀具,提高刀具的抗振性。
要确保刀具与工件之间的相对位置准确,避免刀具偏心。
合理设置切削参数,如进给速度、切削深度和切削量等,避免切削力过大。
及时更换磨损严重的刀具,保持刀具的良好状态。
过切是数控铣床加工中常见的问题,对加工质量和加工成本有着不利影响。
只有正确分析过切的原因,采取科学的解决办法,才能提高数控铣床加工的效率和质量。
浅谈数控铣削加工中的过切现象及对策
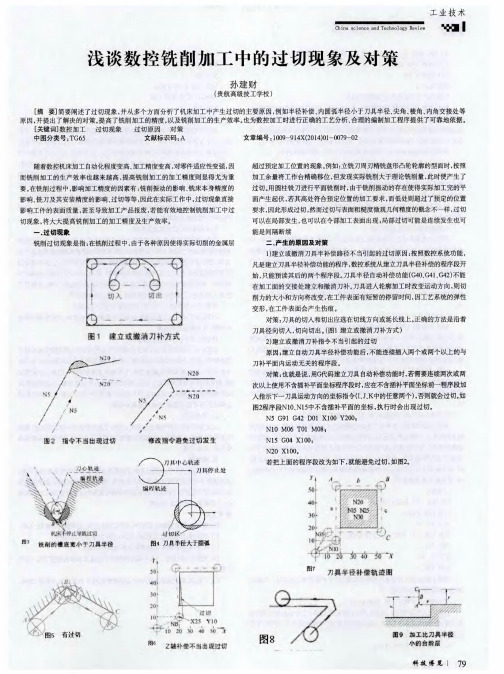
原因: 角为直角的工件轮廓 , 其刀具 中心正好沿着两正交轴移动, 在某一坐 标伺服系统的位置为加工终点, 而另一个正交轴伺服系统紧接着接受位置指 令, 度瞬间从零加速至指定值。 但在两正交轴改变的瞬间, 第一正交轴对指令位 置有滞后性, 使得第二正交轴加速时 , 第一正交轴未到达拐点 , 出现过切。
原因: 加工的图形中若圆弧半径小于切削刀具半径时, 则刀具实际加工的
量大于 理论加 工的量 , 因此 圆弧切 削加工会 出现过切 。 此时机 床不会产 生报警 ,
也要沿切线方向切人切出, 此时切线方向切人应为圆弧与圆弧相切 l ( 2 ) X t 于精 度要求高的零件分为粗、 精加工, 分配加工余量时精加工应取 ( 0 .1 mm - 0 . 4 ) mm。 在加工要求较高的凹槽时 , 宜用直径较小一些的立铣刀铣槽的中部 , 然后利用刀具半径补偿铣削两边, ( 3 ) 为了减少不必要的换刀定位误差 , 将零 件上用一把刀加工的部位全部加工完后, 再换另一把刀来加工。 9 ) 尖角棱角的过切现象及对策 原因: 有时在用折线逼近曲线时没有注意到其尖角是凸是凹, 尤其是在曲 线拐弯点附近不太容易分辨 , 这时若在尖角处采用过渡圆弧编程就很容易产生 过切 ・ ( 图8 ) 有时候凸型尖角附近有轮廓限制, 例如铣刀直径过大 , 尖角采用过
N2 0 X1 0 0 ・
3 ) 加 工小 于刀 具直径 的沟槽 引起过 切 原因: 如 图哳 示 的槽 , 槽底 宽度小 于刀具直 径 , 在 加工过程 中会产生过 切 。
随着刀具的进给, 刀具首先与槽左侧面相切, 随着加工的进行, 刀具中心走到0 1 点, 这时刀具到切削到B 点, 然而左侧槽面 已经过切。 加工槽底直线A B 段时, 刀
渡 圆弧编程 也会产 生过切 。 在铣 削棱角 轮廓 时 , 若刀 具 中心位移 量与 轮廓尺 寸
浅析数控铣床加工中的过切现象

浅析数控铣床加工中的过切现象数控铣床加工程序中的工艺失误及编程错误均会导致切削过量状况的发生,这种过切现象影响数控铣床的加工密度,可能导致整个产品报废,通过工艺处理及数控编程改进数据铣床的加工势在必行。
本文旨在通过分析数据铣床加工中的过切现象,探究过切现象的影响因素,并提出相关解决措施以供参考。
标签:数控铣床;过切;原因与对策随着科技的发展,在机械加工领域,数控机床已经成为了机械制造业的主要生产设备。
数控铣床虽然具备自动化、智能化、效率化等优点而广泛应用于现代工业生产,但是数据铣床加工依赖于数据编程,其加工过程中不可避免的会因程序误差和技术失误产生过切现象,同时过切现象又不能普通机床一样进行人工调整,因此,如何更新技术以有效避免数控铣床加工中过切现象的发生是必须要解决的问题。
1 加工拐角时的过切现象分析在数控铣床加工的过程中必须注重每一个微小的细节,这样才能有效避免过切现象的发生。
就数控铣床加工的实践来看,过切现象在加工拐角时出现较多,直接影响工件加工的精度和效果,简要分析如下:(1)内角交接处产生的过切。
数控铣床加工的过程中,在铣削机床零件的内角处时,由于计算的误差可能会导致过切现象。
此时引起过切的主要原因包括:首先,当铣刀运转到零件的内角处时,此时刀具和工件之间接触的面积扩大,切削便跟着扩大,之后过拐角时,从铣两面变为一面,也导致切削随之减小,工艺系统弹性变形恢复,这样就自然造成刀具向工件加工的内侧变形,产生过切。
其次,导致内角交接处过切的因素还有可能是物理上的惯性作用力。
简单来讲,在内角交接处,当刀具一开始运转的速度过高的时,基于运动的惯性,也可能导致过切现象发生。
针对数控铣床加工中内角处的过切,可以采取以下措施加以应对:其一,工厂在刀具的选择方面加以改进。
要综合考虑刀具的刚性、抗热性和抗震性,选择质量相对优质的刀具。
数控铣床的加工实践表明,选择好的刀具固然使工厂的投入成本有所提升,但是质量过关的刀具可以减少不必要的过切现象产生,避免了产品的报废,整体上可以提高效益。
- 1、下载文档前请自行甄别文档内容的完整性,平台不提供额外的编辑、内容补充、找答案等附加服务。
- 2、"仅部分预览"的文档,不可在线预览部分如存在完整性等问题,可反馈申请退款(可完整预览的文档不适用该条件!)。
- 3、如文档侵犯您的权益,请联系客服反馈,我们会尽快为您处理(人工客服工作时间:9:00-18:30)。
浅议数控机床加工中C刀具补偿下的过切现象
摘要:随着计算机技术的发展,在数控机床中运用计算机技术也得到了较快的发展。
早期数控机床主要由数字逻辑电路组成硬件数控系统,即NC系统,随着计算技术的运用,该系统已被淘汰,取而代之的是计算机数控系统,即CNC系统。
CNC系统在存储能力及运算速度方面大幅提高,且柔性较为良好。
本文主要是在装备CNC系统基础上的数控车床进行分析,对其C刀具补偿下的过切现象进行研究,并提出解决的措施。
关键词:C刀具;CNC系统;数控机床;补偿
数控机床中有一种特殊的功能,即刀具补偿,其作用是数控系统在工件轮廓程序及刀具中心偏移量的条件下,自动对刀具的轨迹进行计算。
在CNC系统中,刀具补偿分为B刀具补偿和C刀具补偿。
B刀具补偿采用读、算、走依次进行的控制方法,对程序间的过渡问题很难解决,工作人员需要先对刀补后的交叉点及间断点情况进行预计,然后人为进行处理,其加工工艺较差。
而C刀具补偿很好的解决了B刀具补偿的不足,可直接求出刀具中心轨迹焦点,刀具加工的路径大大缩短,加工工艺大幅提高,这也是目前数控系统中比较先进的刀具补偿方法。
但是在加工过程中,要是编程方法不合适,就会出现过切现象,对零件的质量及精度都有严重的影响,本文主要对C刀具补偿中的过切现象进行分析研究,提出消除过切的方法。
1、C刀具补偿中的过切现象分析
1.1刀补平面内两段及以上没有移动指令时的过切现象
刀具补偿时,平面内两段及以上没有移动指令时,往往会出现过切的现象。
如图1所示,某工件经过数控铣削加工时,其程序如下:
图1 过切现象一
O0002
N10 S800 M03
N20 G90 G54 G00 X0 Y0
N30 Z100
N40 G41 X20 Y10 D01 //刀补建立
N50 Z5 //Z方向下刀
N60 G01 Z-1 F80 //Z方向下刀
N70 Y50 //加工外轮廓
N80 X50
……
N120 M30
对其主要原因进行分析可知,刀具补偿从N40程序段开始,其建立时,数控程序只能读出两个程序间断,此时N50、N60两程序段都在z轴上移动,与x、y轴无关,因此,数控车床不能正确的判断出下一个补偿的方向,虽然采用了G41进行刀补,然而刀补的中心却没有加上刀补值,直接到达A点完成了N50、N60段的补偿后进行N70段补偿,从A点移动向B点使,刀具中心将工件的一部分切掉,因此产生了过切现象。
1.2刀补平面内存在一个移动距离为0的指令产生过切现象
在刀补状态下,平面内两个运动指令间存在一个移动为0的指令,就会产生过切现象,如图2所示,某工件经过数控铣削加工时,其程序如下:
图2 过切现象二
O0003
N10 M03 S1000
N20 G54 G00 X0 Y0 Z5
N30 G01 Z-1 F100
N40 G41 G01 X20 Y10 D01
N50 Y40
N60 Y40
N70 X30
……
N120 M30
对其原因进行分析,刀具加工至N40段时,可以对N50、N60两段进行预读,这两段的位移量均为0,此时没有零件的轮廓信息,因此不存在矢量变化,这时刀补中心也没有加上刀补值,刀具中心停留在A点,刀补中心向B点移动时,向下预读到N70段时,出现过切现象。
1.3连续两辅助功能程序段产生过切现象
刀具补偿状态下,存在两个连续辅助功能程序段时,往往会产生过切现象,如图3所示,某工件经过数控铣削加工时,其程序如下:
图3 过切现象三
O0004
N10 M03 S1000
N20 G54 G00 X0 Y0 Z5
N30 G01 Z-1 F100
N40 G41 G01 X20 Y10 D01
N50 Y40
N60 M08
N70 M09
N80 G01 X30
……
N120 M30
对其原因进行分析,在刀具补偿加工N50段的时候,对N60、N70段进行预读,这两段均为辅助功能指令,因此缺乏零件轮廓信息,沿AB轮廓的垂直矢量缺失,没有刀补值。
从A点向B点移动时,经过N80段时出现过切现象。
2、C刀具出现过切现象的解决方法
从以上分析可以知道,C刀具在补偿时的过切现象虽然形式不一,但本质都是要严格根据C刀补规则进行。
第二、三种过切现象主要是由于编程不合理造成,是可以避免的,第一种过切解决的主要方向是深度的进给。
因此本文主要针对第一种过切现象提出以下几种解决的方法:
2.1切至切削深度后,启动刀补
在进行刀补之前,首先选择安全的位置将刀具一次性进给到切削深度,然后进行刀具补偿,其程序如下:
O0005
N10 S1000 M03
N20 G54 G00 X0 Y0 Z5
N30 G01 Z-1 F100 //z轴进给至切削深度
N40 G41 G01 X20 Y10 D01 //建立刀具补偿
N50 Y50
……
N120 M30
2.2首先启动刀补,然后在深度方向一次进给到切削深度
启动刀具补偿后,选择安全位置,在深度方向上一次性进给到切削的深度。
程序如下:
O0006
N10 S1000 M03
N20 G54 G00 X0 Y0 Z5
N30 G41 G01 X20 Y10 D01 //建立刀具补偿
N40 G01 Z-1 F100 //z轴一次进给到切削深度
N50 Y50
……
N120 M30
2.3刀补启动时,3个坐标同时进给
刀具补偿启动的时候,选择安全位置,使刀具在坐标三个方向同时进给,且使z轴进给到切削的深度,其程序如下:
O0007
N10 S1000 M03
N20 G54 G00 X0 Y0 Z5
N30 G41 G01 X20 Y10 Z-1 D01 F100 //三个坐标同时制定刀具偏置
N40 Y50
……
N120 M30
2.4同一方向,两次进给至切削深度
启动刀具补偿后,选择安全位置,在平面内同一直线方向,向深度两次进给至切削深度,如图4所示程序:
图4 防止过切措施
O0008
N10 S1000 M03
N20 G54 G00 X0 Y0 Z40
N30 G41 X20 Y10 D01
N40 Y12
N50 Z5
N60 G01 Z-1 F100
N70 Y50
……
N120 M30
3、结束语
在数控机床中,应用最广泛的就是C刀具补偿指令,也是最重要的指令,如果没有该指令,数控铣削编程是非常复杂的,零件的质量和精度也不能得到保证。
对铣削中的过切现象,只要对C刀具补偿动作严格按照编程规则,是可以避免的。
参考文献:
[1]康家乐,桂贵生. C机能刀具半径补偿算法与应用[J].组合机床与自动化加工技术.2009(7).
[2]郑龙燕.数控铣削加工中的刀具补偿[J].精密制造与自动化.2008(4).
[3]梁增众.对数控铣削加工中刀具补偿的探讨[J].计算机光盘软件与应用.2011(12).
[4]浦艳敏.数控铣床刀具半径补偿的分析与应用[J].科学技术与工程.2009(23).
[5]李艳霞.C功能刀具半径补偿中过切的分析与改进措施[J].机床与液压.2010(18).。