数控刀具补偿原理
刀具补偿原理
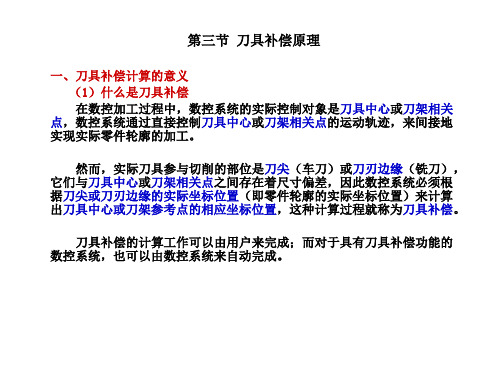
X F X B X FP 15 35 50 Z F Z B Z FP 70 20 50
讨论: 1)利用(2-3)式,我们可以得到测量刀具长度参数的计算公式:
l X X F X P lZ Z F Z P
其中: ①(ZF,XF):刀架相关点F的坐标; ②(ZP,XP):新刀具刀尖点坐标。
下一个程序段包含G40功能字
刀具半径补偿撤消状态
非半径补偿状态 假设数控系统的当前工作状态为非半径补偿状态。 ① 如果当前程序段不包含G41或G42功能字,则数控系统保持非半径补 偿状态。 ② 如果当前程序段包含G41或G42功能字,则数控系统转入刀具半径补 偿建立状态。 在非半径补偿状态下,当前编程轮廓的终点就是当前编程轮廓的转接点。 数控系统控制刀具中心直接运动到该点位置。
LX X FP X PF LZ Z FP Z PF
此时刀具长度补偿计算公式可写成:
X F X P LX Z F Z P LZ
(2-3)
② 而在有些数控系统中,刀具参数表中的刀具长度参数采用刀尖点P相对于 刀架参考点F的坐标值(ZPF,XPF) ,即
F F X XPF
M
Z
X
Z
ZPF
W
ZWM Z FM Z PF Z PW Z FM LZ Z PW X WM X FM X PF X PW X FM LX X PW
(2)假设刀尖圆弧半径RS ≠ 0
此时,刀具的补偿算法比较复杂,一方面要考虑刀尖圆弧半径的补偿 (刀具半径补偿类型),另一方面还要考虑刀具长度补偿。 但是,一般情况下RS很小,在有些生产场合可以不考虑它对零件轮廓的影 响,另一方面,在对刀过程中已经把RS在平行于坐标轴方向所引起的误差进行 了补偿,因此零件表面上平行于坐标轴的轮廓不会再产生附加误差(但斜线 或圆弧还是会有误差),在此暂时不考虑刀尖圆弧的补偿计算。
刀具长度补偿的原理是什么
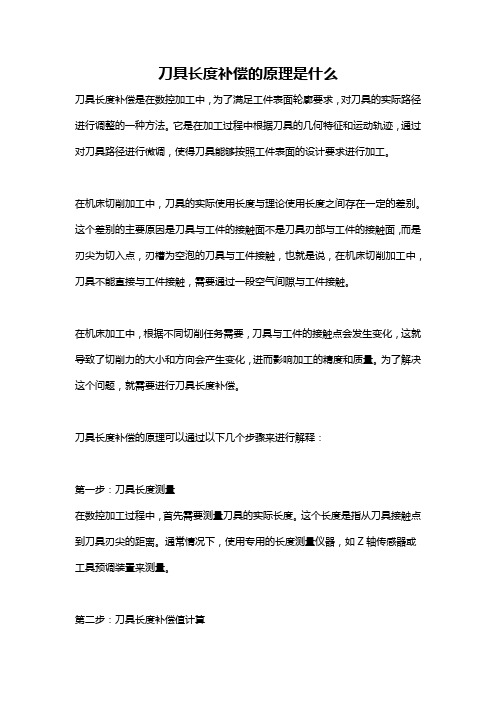
刀具长度补偿的原理是什么刀具长度补偿是在数控加工中,为了满足工件表面轮廓要求,对刀具的实际路径进行调整的一种方法。
它是在加工过程中根据刀具的几何特征和运动轨迹,通过对刀具路径进行微调,使得刀具能够按照工件表面的设计要求进行加工。
在机床切削加工中,刀具的实际使用长度与理论使用长度之间存在一定的差别。
这个差别的主要原因是刀具与工件的接触面不是刀具刃部与工件的接触面,而是刃尖为切入点,刃槽为空泡的刀具与工件接触,也就是说,在机床切削加工中,刀具不能直接与工件接触,需要通过一段空气间隙与工件接触。
在机床加工中,根据不同切削任务需要,刀具与工件的接触点会发生变化,这就导致了切削力的大小和方向会产生变化,进而影响加工的精度和质量。
为了解决这个问题,就需要进行刀具长度补偿。
刀具长度补偿的原理可以通过以下几个步骤来进行解释:第一步:刀具长度测量在数控加工过程中,首先需要测量刀具的实际长度。
这个长度是指从刀具接触点到刀具刃尖的距离。
通常情况下,使用专用的长度测量仪器,如Z轴传感器或工具预调装置来测量。
第二步:刀具长度补偿值计算在获得刀具的实际长度后,需要根据加工的需求,计算出刀具长度补偿值。
这个补偿值也称为沿刀具轴向的刀具净延伸长度。
这个值可以通过以下公式计算得到:刀具净延伸长度=刀具实际长度-刀具理论长度第三步:刀具长度补偿在加工过程中,根据刀具的几何特征和工件的设计要求,通过控制系统中的刀具长度补偿参数,对刀具路径进行微调。
根据刀具长度补偿值,可以调整刀具在机床工作过程中的实际位置,使得刀具的切入点与工件的接触点保持一致。
第四步:刀具路径调整在进行刀具长度补偿后,刀具的实际路径会相应地进行调整。
在程序中,刀具路径的坐标值会根据刀具长度补偿值进行调整,从而保证刀具能够按照工件的设计要求进行加工。
总结起来,刀具长度补偿的原理是通过测量刀具的实际长度,计算出刀具长度补偿值,然后根据这个补偿值对刀具路径进行微调,使得刀具能够按照工件表面的设计要求进行加工。
数控系统的插补原理与刀具补偿原理

整理课件
上一页 下一页 返回12
3.2 逐点比较插补法
设偏差函数为
F (x,y)xayixiya (3-1)
综合以上分析,可把偏差函数与刀具位置的关系归结为 如表3-1所示。
整理课件
上一页 下一页 返回13
3.2 逐点比较插补法
2.进给方向与偏差计算
插补前刀具位于直线的起点O。由于点O在直线上,由表 3-1可知这时的偏差值为零,即:
A(x a
数为
,
ya
y a),沿轴应走的总步数为 x a ,沿轴应走的总步
。那么,加工完直线OA,刀具沿两坐标轴应走的总
步数为
N= x a + y a
(3-6)
整理课件
上一页 下一页 返回18
3.2 逐点比较插补法
在逐点比较插补法中,每进行一个插补循环,刀具或者沿 轴走一步,或者沿轴走一步。也就是说,插补循环数与刀具 沿、轴已走的总步数相等。这样,就可根据插补循环数与刀 具应走的总步数N是否相等来判断终点,即直线加工完毕的 条件为
127。若寄存器长度为16位,则直线终点坐标最大值为32
整理课件
上一页 下一页 返回17
3.2 逐点比较插补法
3.终点判断
由于插补误差的存在,刀具的运动轨迹有可能不通过直
线的终点A( x a , y a )。因此,不能把刀具坐标与终点坐标
相等作为终点判断的依据。
可以根据刀具沿、两轴所走的总步数来判断直线是否加
工完毕。刀具从直线起点O(图3-2),移动到直线终点
整理课件
上一页 下一页 返回10
3.2 逐点比较插补法
3.2.1 逐点比较法直线插补
1.偏差函数
刀补原理

y
B′(Xb′,Yb′)
ΔY B(Xb,Yb) K ΔX R r A′(Xa′,Ya′) A(Xa,Ya) x
β O
图9-6 圆弧刀具半径补偿 X ∆ X = r cos β = r b R Yb ∆ Y = r sin β = r R rX b ′ Xb = Xb + R rY b Y b′ = Y b + R
图93a建立刀具半径补偿的过程图93a建立刀具半径补偿的过程图93b刀具半径补偿的过程图93b刀具半径补偿的过程图93c撤消刀具半径补偿的过程图93c撤消刀具半径补偿的过程4过切过切有以下两种情况
数控装置的刀具补偿原理
一、刀具补偿概述
轮廓加工中,刀 具总有一定半径(如铣 刀或线切割钼丝),刀 具中心运动轨迹并不 等于加工零件的编程 轨迹。
G42为右偏刀具半径补偿(右刀补) ,定义:假设 工件不动,沿刀具运动方向向前看,刀具在零件右侧 的补偿, G40为取消刀具补偿指令。
图9-2b 右刀补补偿
3、工作过程 、 刀具半径补偿过程分为三个步骤:刀补建立、刀 补进行 、刀补撤销。 刀具半径补偿建立,一般是直线且为空行程,以 防过切。以G42为例,图9-3a表示建立刀补过程。 图9-3b表示的刀具半径补偿的工作过程。 刀具半径补偿结束用G40撤销,撤销时同样要防 止过切,图9-3c表示撤消刀具半径补偿的过程。 上述各图中,实线表示编程轨迹;点划线表示刀 具中心轨迹;r等于刀具半径,表示偏移向量。
图c
图d
图9-12 外轮廓直线转接过渡
3、结论
C刀补中对内轮廓过渡均采用缩短型处理,对外轮 廓过渡可根据两矢量加工轨迹间夹角的大小采用伸长型或 插入型处理。可见,对各种直线、圆弧间的连接过渡方式 都可通过数控系统,按上述规律作伸长缩短等处理,彻底 解决了数控加工中两程序段转接过程中的过渡问题。
数控机床刀具补偿原理
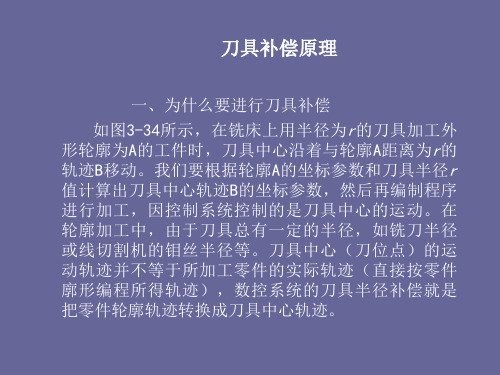
A
r1 N11 r2 P Q N12
G42
B r2 G41
N
M
r1
图3-43 刀补方向改变的切削实例
图3-44 刀补半径改变的实例
2. 改变刀具半径值 在零件切削过程中刀具半径值改变了,则新的补偿 值在下个程序段中产生影响。如图3-44所示,N10段补 偿用刀具半径r1 ,N11段变为r2 后,则开始建立新的刀 补,进入N12段后即按新刀补r2进行补偿。刀具半径的 改变可通过改变刀具号或通过操作面板等方法来实现。 3. 过切问题 (1)刀具半径补偿可使刀具中心轨迹在走刀平面 (如xy面)内偏移零件轮廓一个刀具半径值。在刀补 建立后的刀补进行中,如果存在有二段以上没有移动 指令或存在非指定平面轴的移动指令段,则可能产生 过切。 如图3-45所示,设刀具开始位置距工件 表面上方50mm, 切削深度为8mm。z轴垂直于走刀平 面(xy面),则按下述方法编程,会产生过切。
y A(X,Y) ΔY α K A′(X′,Y′) r K ΔX x
y
B′(Xb′,Yb′)
O
α O′
ΔY B(Xb,Yb) K ΔX R r A′(Xa′,Ya′) A(Xa,Ya) x
β O
图3-37 直线刀具补偿
图3-38 圆弧刀具半径补偿
2. 圆弧刀具半径补偿计算 对于圆弧而言,刀具补偿后的刀具中心轨迹是一个 与圆弧同心的一段圆弧。只需计算刀补后圆弧的起点 坐标和终点坐标值。如图3-38所示,被加工圆弧的圆 心坐标在坐标原点O,圆弧半径为R,圆弧起点A,终 点B,刀具半径为r。 假定上一个程序段加工结束后刀具中心为A′,其坐 标已知。那么圆弧刀具半径补偿计算的目的,就是计 算出刀具中心轨迹的终点坐标B′ X b ,Y。设BB′在两个坐 b X 为则 , Y 标上的投影 X b X b X Yb Yb Y (3-49)
数控刀补原理

数控刀补原理数控刀补原理数控刀补是指通过计算机控制的方式在数控加工中对刀具进行调整的技术。
在数控加工中,刀具的误差和磨损是不可避免的,使用刀补技术可以使加工精度得到提高。
一、数控刀补的作用数控刀补的作用是对加工中刀具的误差进行补偿,使得机床可以更准确的加工出零件。
在数控加工中,通过预设刀具的补偿值,来将刀具的实际指向达到理想的指向,从而减少工件的误差。
二、刀补方式数控刀补主要有刀尖补偿、刀具半径补偿、刀具长度补偿三种方式:1. 刀尖补偿刀尖补偿是指在加工过程中,刀具的转角密切影响着切削力和精度,通过调整刀尖的位置,来补偿误差的影响。
刀尖补偿一般适用于小浅孔加工或槽加工,由于加工深度不深,所以误差主要由刀尖位置引起。
2. 刀具半径补偿刀具半径补偿是指在加工中,由于刀具磨损或工艺要求,在刀具半径方向上进行误差补偿。
该补偿方式适用于不同直径的切削,例如加工槽、棱形或外形时,由于直径大小不一致,需要进行调整。
3. 刀具长度补偿刀具长度补偿是指在加工过程中,由于刀具长度的问题出现误差,该方式适用于龙门加工、雕刻等加工过程中。
龙门加工中,由于刀具长度不同,所以需要进行补偿。
在雕刻中,刀具长度与加工精度非常相近,刀具长度补偿就显得尤为重要。
三、刀补预设置刀补预设置是指在数控机床上,将刀补参数设置到系统中。
在预设时,需要考虑刀具的特性,如其长度、直径、材质等,还需要考虑加工的精度要求,适当的工艺参数以及被加工物料的特性等等,从而预设出合适的刀补参数。
四、刀补误差的影响因素刀补误差是影响加工精度的重要因素,在预设参数时,需要考虑各种因素。
1. 刀具自身的误差:由于刀具的加工、装夹等问题,也会对加工误差产生一定贡献。
2. 工作零件的误差:由于被加工零件的材料、尺寸等因素,对加工误差也有一定影响。
3. 工艺参数的选择:加工中,选择合适的工艺参数也是减少误差的重要措施,比如进给速度、切削深度等。
4. 加工过程中的其他因素:例如润滑、温度等因素也会对误差产生影响。
数控刀具补偿原理

3.3 刀具补偿原理刀具补偿(又称偏置),在20世纪60~70年代的数控加工中没有补偿的概念,所以编程人员不得不围绕刀具的理论路线和实际路线的相对关系来进行编程,容易产生错误。
补偿的概念出现以后很大地提高了编程的效率。
具有刀具补偿功能,在编制加工程序时,可以按零件实际轮廓编程,加工前测量实际的刀具半径、长度等,作为刀具补偿参数输入数控系统,可以加工出合乎尺寸要求的零件轮廓。
刀具补偿功能还可以满足加工工艺等其他一些要求,可以通过逐次改变刀具半径补偿值大小的办法,调整每次进给量,以达到利用同一程序实现粗、精加工循环。
另外,因刀具磨损、重磨而使刀具尺寸变化时,若仍用原程序,势必造成加工误差,用刀具长度补偿可以解决这个问题。
刀具补偿分为2种:☆刀具长度补偿;☆刀具半径补偿。
文献《刀具补偿在数控加工中的应用》(工具技术,2OO4年第38卷No7,徐伟,广东技术师范学院)中提到在数控加工中有4种补偿:☆刀具长度补偿;☆刀具半径补偿;☆夹具补偿;☆夹角补偿(G39)。
这四种补偿基本上能解决在加工中因刀具形状而产生的轨迹问题。
3.3.1 刀具长度补偿1.刀具长度的概念刀具长度是一个很重要的概念。
我们在对一个零件编程的时候,首先要指定零件的编程中心,然后才能建立工件编程坐标系,而此坐标系只是一个工件坐标系,零点一般在工件上。
长度补偿只是和Z坐标有关,它不象X、Y平面内的编程零点,因为刀具是由主轴锥孔定位而不改变,对于Z坐标的零点就不一样了。
每一把刀的长度都是不同的,例如,我们要钻一个深为50mm的孔,然后攻丝深为45mm,分别用一把长为250mm的钻头和一把长为350mm的丝锥。
先用钻头钻孔深50mm,此时机床已经设定工件零点,当换上丝锥攻丝时,如果两把刀都从设定零点开始加工,丝锥因为比钻头长而攻丝过长,损坏刀具和工件。
此时如果设定刀具补偿,把丝锥和钻头的长度进行补偿,此时机床零点设定之后,即使丝锥和钻头长度不同,因补偿的存在,在调用丝锥工作时,零点Z坐标已经自动向Z+(或Z)补偿了丝锥的长度,保证了加工零点的正确。
刀具半径补偿原理及补偿规则

刀具半径补偿原理及补偿规则在加工过程中,刀具的磨损、实际刀具尺寸与编程时规定的刀具尺寸不一致以及更换刀具等原因,都会直接影响最终加工尺寸,造成误差。
为了最大限度的减少因刀具尺寸变化等原因造成的加工误差,数控系统通常都具备有刀具误差补偿功能。
通过刀具补偿功能指令,CNC系统可以根据输入补偿量或者实际的刀具尺寸,使机床自动加工出符合程序要求的零件。
1.刀具半径补偿原理(1)刀具半径补偿的概念用铣刀铣削工件的轮廓时,刀具中心的运动轨迹并不是加工工件的实际轮廓。
如图所示,加工内轮廓时,刀具中心要向工件的内侧偏移一定距离;而加工外轮廓时,同样刀具中心也要向工件的外侧偏移一定距离。
由于数控系统控制的是刀心轨迹,因此编程时要根据零件轮廓尺寸计算出刀心轨迹。
零件轮廓可能需要粗铣、半精铣和精铣三个工步,由于每个工步加工余量不同,因此它们都有相应的刀心轨迹。
另外刀具磨损后,也需要重新计算刀心轨迹,这样势必增加编程的复杂性。
为了解决这个问题,数控系统中专门设计了若干存储单元,存放各个工步的加工余量及刀具磨损量。
数控编程时,只需依照刀具半径值编写公称刀心轨迹。
加工余量和刀具磨损引起的刀心轨迹变化,由系统自动计算,进而生成数控程序。
进一步地,如果将刀具半径值也寄存在存储单元中,就可使编程工作简化成只按零件尺寸编程。
这样既简化了编程计算,又增加了程序的可读性。
刀具半径补偿原理(2)刀具半径补偿的数学处理①基本轮廓处理要根据轮廓尺寸进行刀具半径补偿,必需计算刀具中心的运动轨迹,一般数控系统的轮廓控制通常仅限于直线和圆弧。
对于直线而言,刀补后的刀具中心轨迹为平行于轮廓直线的一条直线,因此,只要计算出刀具中心轨迹的起点和终点坐标,刀具中心轨迹即可确定;对于圆弧而言,刀补后的刀具中心轨迹为与指定轮廓圆弧同心的一段圆弧,因此,圆弧的刀具半径补偿,需要计算出刀具中心轨迹圆弧的起点、终点和圆心坐标。
②尖角处理在普通的CNC装置中,所能控制的轮廓轨迹只有直线和圆弧,其连接方式有:直线与直线连接、直线与圆弧连接、圆弧与圆弧连接。
- 1、下载文档前请自行甄别文档内容的完整性,平台不提供额外的编辑、内容补充、找答案等附加服务。
- 2、"仅部分预览"的文档,不可在线预览部分如存在完整性等问题,可反馈申请退款(可完整预览的文档不适用该条件!)。
- 3、如文档侵犯您的权益,请联系客服反馈,我们会尽快为您处理(人工客服工作时间:9:00-18:30)。
3.3 刀具补偿原理刀具补偿(又称偏置),在20世纪60~70年代的数控加工中没有补偿的概念,所以编程人员不得不围绕刀具的理论路线和实际路线的相对关系来进行编程,容易产生错误。
补偿的概念出现以后很大地提高了编程的效率。
具有刀具补偿功能,在编制加工程序时,可以按零件实际轮廓编程,加工前测量实际的刀具半径、长度等,作为刀具补偿参数输入数控系统,可以加工出合乎尺寸要求的零件轮廓。
刀具补偿功能还可以满足加工工艺等其他一些要求,可以通过逐次改变刀具半径补偿值大小的办法,调整每次进给量,以达到利用同一程序实现粗、精加工循环。
另外,因刀具磨损、重磨而使刀具尺寸变化时,若仍用原程序,势必造成加工误差,用刀具长度补偿可以解决这个问题。
刀具补偿分为2种:☆刀具长度补偿;☆刀具半径补偿。
文献《刀具补偿在数控加工中的应用》(工具技术,2OO4年第38卷No7,徐伟,广东技术师范学院)中提到在数控加工中有4种补偿:☆刀具长度补偿;☆刀具半径补偿;☆夹具补偿;☆夹角补偿(G39)。
这四种补偿基本上能解决在加工中因刀具形状而产生的轨迹问题。
3.3.1 刀具长度补偿1.刀具长度的概念刀具长度是一个很重要的概念。
我们在对一个零件编程的时候,首先要指定零件的编程中心,然后才能建立工件编程坐标系,而此坐标系只是一个工件坐标系,零点一般在工件上。
长度补偿只是和Z坐标有关,它不象X、Y平面内的编程零点,因为刀具是由主轴锥孔定位而不改变,对于Z坐标的零点就不一样了。
每一把刀的长度都是不同的,例如,我们要钻一个深为50mm的孔,然后攻丝深为45mm,分别用一把长为250mm的钻头和一把长为350mm的丝锥。
先用钻头钻孔深50mm,此时机床已经设定工件零点,当换上丝锥攻丝时,如果两把刀都从设定零点开始加工,丝锥因为比钻头长而攻丝过长,损坏刀具和工件。
此时如果设定刀具补偿,把丝锥和钻头的长度进行补偿,此时机床零点设定之后,即使丝锥和钻头长度不同,因补偿的存在,在调用丝锥工作时,零点Z坐标已经自动向Z+(或Z)补偿了丝锥的长度,保证了加工零点的正确。
2.刀具长度补偿指令通过执行含有G43(G44)和H指令来实现刀具长度补偿,同时我们给出一个Z坐标值,这样刀具在补偿之后移动到离工件表面距离为Z的地方。
另外一个指令G49是取消G43(G44)指令的,其实我们不必使用这个指令,因为每把刀具都有自己的长度补偿,当换刀时,利用G43(G44)H指令赋予了自己的刀长补偿而自动取消了前一把刀具的长度补偿。
G43表示存储器中补偿量与程序指令的终点坐标值相加,G44表示相减,取消刀具长度偏置可用G49指令或H00指令。
程序段N80 G43 Z56 H05与中,假如05存储器中值为16,则表示终点坐标值为72mm。
3.刀具长度补偿的两种方式(1)用刀具的实际长度作为刀长的补偿(推荐使用这种方式)。
使用刀长作为补偿就是使用对刀仪测量刀具的长度,然后把这个数值输入到刀具长度补偿寄存器中,作为刀长补偿。
使用刀具长度作为刀长补偿的理由如下:首先,使用刀具长度作为刀长补偿,可以避免在不同的工件加工中不断地修改刀长偏置。
这样一把刀具用在不同的工件上也不用修改刀长偏置。
在这种情况下,可以按照一定的刀具编号规则,给每一把刀具作档案,用一个小标牌写上每把刀具的相关参数,包括刀具的长度、半径等资料,事实上许多大型的机械加工型企业对数控加工设备的刀具管理都采用这种办法。
这对于那些专门设有刀具管理部门的公司来说,就用不着和操作工面对面地告诉刀具的参数了,同时即使因刀库容量原因把刀具取下来等下次重新装上时,只需根据标牌上的刀长数值作为刀具长度补偿而不需再进行测量。
其次,使用刀具长度作为刀长补偿,可以让机床一边进行加工运行,一边在对刀仪上进行其他刀具的长度测量,而不必因为在机床上对刀而占用机床运行时间,这样可以充分发挥加工中心的效率。
这样主轴移动到编程Z坐标点时,就是主轴坐标加上(或减去)刀具长度补偿后的Z坐标数值。
(2)利用刀尖在Z方向上与编程零点的距离值(有正负之分)作为补偿值。
这种方法适用于机床只有一个人操作而没有足够的时间来利用对刀仪测量刀具的长度时使用。
这样做当用一把刀加工另外的工件时就要重新进行刀长补偿的设置。
使用这种方法进行刀长补偿时,补偿值就是主轴从机床Z坐标零点移动到工件编程零点时的刀尖移动距离,因此此补偿值总是负值而且很大。
3.3.2 刀具半径补偿1.刀具半径补偿概念在轮廓加工时,刀具中心运动轨迹(刀具中心或金属丝中心的运动轨迹)与被加工零件的实际轮廓要偏移一定距离,这种偏移称为刀具半径补偿,又称刀具中心偏移。
如图3-1所示,在加工内轮廓时,刀具中心向工件轮廓的内部偏移一个距离;而加工外轮廓时,刀具中心向工件的外侧偏移一个距离,这个偏移,就是所谓的刀具半径补偿。
图中,粗实线为工件轮廓,虚线为刀具中心轨迹。
本图中的偏移量为刀具半径值。
而在粗加工和半精加工时,偏移量为刀具半径和加工余量之和。
图3-1 B功能刀具补偿的交叉点和间断点由于数控系统控制的是刀具中心轨迹,因此数控系统要根据输入的零件轮廓尺寸及刀具半径补偿值计算出刀心轨迹。
由此可见,刀具半径补偿在数控加工有着非常重要的作用,根据刀具补偿指令,数控加工机床可自动进行刀具半径补偿。
特别是在手工编程时,刀具半径补偿尤为重要。
手工编程时,运用刀具半径补偿指令,就可以根据零件的轮廓值编程,不需计算刀心轨迹编程,这样就大大减少了计算量和出错率。
虽然利用CAD/CAM自动编程,手工计算量小,生成程序的速度快,但当刀具有少量磨损或加工轮廓尺寸与设计尺寸稍有偏差时或者在粗铣、半精铣和精铣的各工步加工余量变化时,仍需作适当调整,而运用了刀具半径补偿后,不需修改刀具尺寸或建模尺寸而重新生成程序,只需要在数控机床上对刀具补偿参数做适当修改即可。
既简化了编程计算,又增加了程序的可读性。
刀具半径补偿有B功能(Basic)和C功能(Complete)两种补偿形式。
由于B功能刀具半径补偿只根据本段程序进行刀补计算,不能解决程序段之间的过渡问题,要求将工件轮廓处理成圆角过渡如图3-1所示,因此工件尖角处工艺性不好。
而且编程人员必须事先估计出刀补后可能出现的间断点和交叉点,并进行人为处理,显然增加编程的难度;而C功能刀具半径补偿能自动处理两程序段刀具中心轨迹的转接,可完全按照工件轮廓来编程,因此现代CNC数控机床几乎都采用C功能刀具半径补偿。
这时要求建立刀具半径补偿程序段的后续至少两个程序段必须有指定补偿平面的位移指令(G00、G01,G02、G03等),否则无法建立正确的刀具补偿。
2.刀具半径补偿指令根据ISO规定,当刀具中心轨迹在程序规定的前进方向的右边时称为右刀补,用G42表示;反之称为左刀补,用G41表示。
G41是刀具左补偿指令(左刀补),即顺着刀具前进方向看(假定工件不动),刀具中心轨迹位于工件轮廓的左边,称左刀补。
如图3.2(a)所示。
G42是刀具右补偿指令(右刀补),即顺着刀具前进方向看(假定工件不动),刀具中心轨迹位于工件轮廓的右边,称右刀补。
如图3.2(b)所示。
G40是为取消刀具半径补偿指令。
使用该指令后,G41、G42指令无效。
在使用G41、G42进行半径补偿时应采取以下步骤:(1)设置刀具半径补偿值:程序启动前,在刀具补偿参数区内设置补偿值。
(2)刀补的建立:刀具从起刀点接近工件,刀具中心轨迹的终点不在下一个程序段指定的轮廓起点,而是在法线方向上偏移一个刀具补偿的距离。
在该段程序中,动作指令只能用G00或G01。
(3)刀补进行:在刀具补偿进行期间,刀具中心轨迹始终偏离编程轨迹一个刀具半径的偏移值。
在此状态下,G00、G01、G02、G03都可以使用。
(4)刀补的取消:在刀具撤离工件、返回原点的过程中取消刀补。
此时只能用G00、G01。
3.B 功能刀具半径补偿对直线而言,刀具补偿后的轨迹是与原直线平行的直线,只需要计算出刀具中心轨迹的起点和终点坐标值。
如图3-3所示,被加工直线段的起点在坐标原点,终点坐标为A 。
假定上一程序段加工完后,刀具中心在O ′点坐标已知。
刀具半径为r ,现要计算刀具右补偿后直线段O ′A ′的终点坐标A ′。
设刀具补偿矢量AA ′的投影坐标为,则图3-2刀具半径的左右补偿 (a) 外轮廓补偿 (b) 内轮廓补偿 X X X Y Y Y '=+∆'=+∆xOA A AK α'∠=∠=22sin X r r X Y α∆==+22cos Y r r X Y α∆=-=-+22X X X Y'=++对于圆弧而言,刀具补偿后的刀具中心轨迹是一个与圆弧同心的一段圆弧。
只需计算刀补后圆弧的起点坐标和终点坐标值。
如图3-4所示,被加工圆弧的圆心坐标在坐标原点O ,圆弧半径为R ,圆弧起点A ,终点B ,刀具半径为r 。
假定上一个程序段加工结束后刀具中心为A ′,其坐标已知。
那么圆弧刀具半径补偿计算的目的,就是计算出刀具中心轨迹的终点坐标B ′。
设BB ′在两个坐标上的投影 为,X Y ∆∆,则以图3-1的加工外轮廓为例,采用B 功能刀具半径补偿方法,加工完第一个程序段,刀具中心落在B /、点上,而第二个程序段的起点为A /,两个程序段之间出现了断点,只有刀具中心走一个从B /、至A /的附加程序,即在两个间断点之间增加一个半径为刀具半径的过渡圆弧B 1B 2,才能正确加工出整个零件轮廓。
可见,B 刀补采用了读一段,算一段,再走一段的控制方法,,无法预计到由于刀具半径所造成的下一段加工轨迹对本程序段加工轨迹的影响,相邻两程序段的刀具中心轨迹之间可能出现间断点或交叉点。
为解决下一段加工轨迹对本段加工轨迹的影响,在计算本程序段轨迹后,提前将下一段程序读入,然后根据它们之间转接的具体情况,再对本段的轨迹作适Y Y '=x y ′,Y ′) ) (X a ′,Y a ′) 图3-3 直线刀具补偿 图3-4 圆弧刀具补偿/b b X X X =+∆b b Y Y Y '=+∆BOx B BK β'∠=∠=cos sin b b X X r r R Y Y r r R ββ∆==∆==b b b b b b rX X X R rY Y Y R'=+'=+当修正,得到本段正确加工轨迹,这就是C功能刀具补偿。
C功能刀补更为完善,这种方法能根据相邻轮廓段的信息自动处理两个程序段刀具中心轨迹的转换,并自动在转接点处插入过渡圆弧或直线从而避免刀具干涉和断点情况。
4.C功能刀具半径补偿目前,通常的CNC系统中,实际所能控制的轮廓只有直线和圆弧,相应的有如下转接线形:直线与直线转接、直线与圆弧转接、圆弧与圆弧转接、圆弧与直线转接。