钢铁材料的表面处理
钢铁防锈有哪些方法
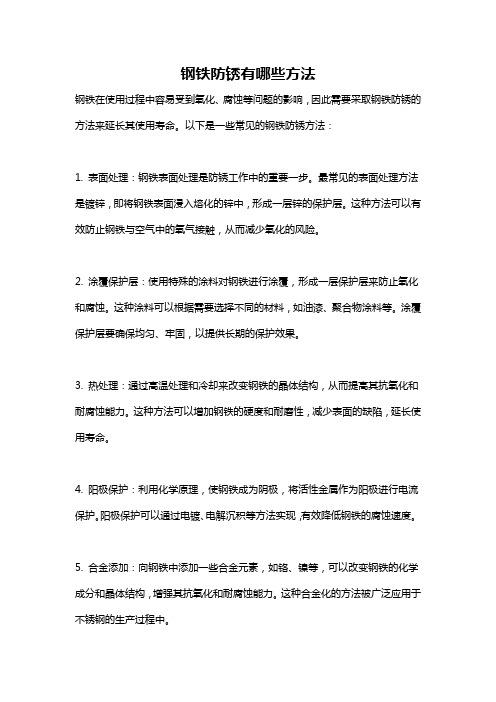
钢铁防锈有哪些方法钢铁在使用过程中容易受到氧化、腐蚀等问题的影响,因此需要采取钢铁防锈的方法来延长其使用寿命。
以下是一些常见的钢铁防锈方法:1. 表面处理:钢铁表面处理是防锈工作中的重要一步。
最常见的表面处理方法是镀锌,即将钢铁表面浸入熔化的锌中,形成一层锌的保护层。
这种方法可以有效防止钢铁与空气中的氧气接触,从而减少氧化的风险。
2. 涂覆保护层:使用特殊的涂料对钢铁进行涂覆,形成一层保护层来防止氧化和腐蚀。
这种涂料可以根据需要选择不同的材料,如油漆、聚合物涂料等。
涂覆保护层要确保均匀、牢固,以提供长期的保护效果。
3. 热处理:通过高温处理和冷却来改变钢铁的晶体结构,从而提高其抗氧化和耐腐蚀能力。
这种方法可以增加钢铁的硬度和耐磨性,减少表面的缺陷,延长使用寿命。
4. 阳极保护:利用化学原理,使钢铁成为阴极,将活性金属作为阳极进行电流保护。
阳极保护可以通过电镀、电解沉积等方法实现,有效降低钢铁的腐蚀速度。
5. 合金添加:向钢铁中添加一些合金元素,如铬、镍等,可以改变钢铁的化学成分和晶体结构,增强其抗氧化和耐腐蚀能力。
这种合金化的方法被广泛应用于不锈钢的生产过程中。
6. 环境控制:钢铁的环境条件对防锈效果有着重要影响。
控制温度、湿度、气体成分等因素可以减少钢铁的氧化和腐蚀速度。
例如,在潮湿的环境中,可以通过保持适当的通风和加湿控制来降低钢铁的腐蚀。
7. 定期维护:定期检查和维护钢铁制品,及时清除表面污垢和氧化物。
对于有损伤的涂层和保护层,及时修复或更换,以保持钢铁的防锈效果。
总结起来,钢铁防锈的方法包括表面处理、涂覆保护层、热处理、阳极保护、合金添加、环境控制和定期维护等。
这些方法可以综合运用,根据具体情况选择合适的防锈措施,以延长钢铁的使用寿命。
钢铁表面处理﹑粗糙度及判别标准

钢铁表面处理﹑粗糙度及判别标准钢铁表面处理)粗糙度及判别标准钢铁表面主要表面处理标准: GB8923-88 中国国家标准ISO8501-1:1988 国际标准化组织标准SIS055900-1967 瑞典标准SSPC-SP2,3,5,6,7和10 美国钢结构涂装协会表面处理标准BS4232 英国标准DIN55928 德国标准JSRA SPSS 日本造船研究协会标准国标GB8923-88 对除锈等级描述:喷射或抛射除锈以字母“Sa”表示。
本标准订有四个除锈等级: Sa1 轻度的喷射或抛射除锈钢材表面应无可见的油脂和污垢,并且没有附着不牢的氧化皮,铁锈和油漆涂层等附着物。
Sa2 彻底的喷射或抛射除锈钢材表面应无可见的油脂和污垢,并且氧化皮,铁锈和油漆涂层等附着物已基本清除,其残留物应该是附着牢固的。
Sa2.5 非常彻底的喷射或抛射除锈钢材表面应无可见的油脂,污垢,氧化皮,铁锈和油漆涂层等附着物,任何残留的痕迹应仅是点状或条纹状的轻微色斑。
Sa3 钢材表面外观洁净的喷射或抛射除锈钢材表面应无可见的油脂,污垢,氧化皮,铁锈和油漆涂层等附着物,该表面应显示均匀的金属色泽。
手工和动力工具除锈以字母“St”表示。
本标准订有二个除锈等级:St2 彻底的手工和动力工具除锈钢材表面应无可见的油脂和污垢,并且没有附着不牢的氧化皮、铁锈和油漆涂层等附着物。
St3 非常彻底的手工和动力工具除锈钢材表面应无可见的油脂和污垢,并且没有附着不牢的氧化皮、铁锈和油漆涂层等附着物。
除锈应比St2更为彻底,底材显露部分的表面应具有金属光泽。
我国的除锈标准与相当的国外除锈标准对照表:日本中国国际标准瑞典德国美国英国JSRA GB8923 ISO8501-1 SIS055900 DIN55928 SSPC BS4232SPSS Sa1 Sa1 Sa1 Sa1 Sp7 ---- ----Sd1 Sa2 Sa2 Sa2 Sa2 Sp6 3级Sh1Sd2 Sa2.5 Sa2.5 Sa2.5 Sa2.5 Sp10 2级Sh2Sd3 Sa3 Sa3 Sa3 Sa3 Sp5 1级Sh3 St2 St2 St2 St2 Sp2 ---- Pt2 St3 St3 St3 St3 SP3 ---- Pt3注:SSPC中的Sp6比Sa2.5 略为严格,Sp2为人工钢丝刷除锈,Sp3为动力除锈。
钢材的表面处理
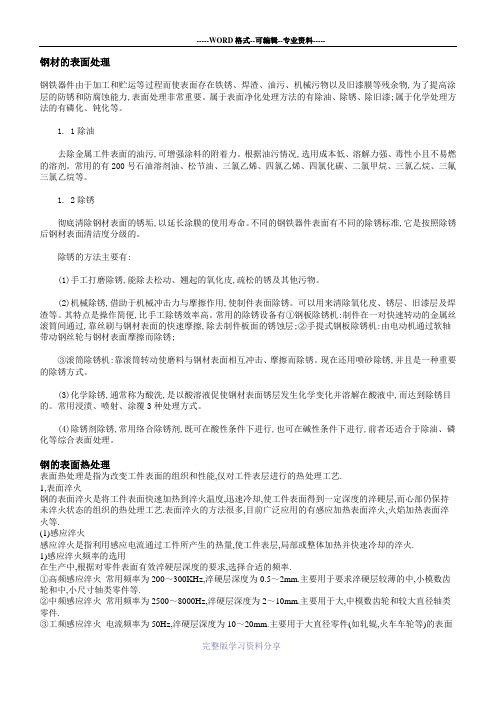
钢材的表面处理钢铁器件由于加工和贮运等过程而使表面存在铁锈、焊渣、油污、机械污物以及旧漆膜等残余物,为了提高涂层的防锈和防腐蚀能力,表面处理非常重要。
属于表面净化处理方法的有除油、除锈、除旧漆;属于化学处理方法的有磷化、钝化等。
1. 1除油去除金属工件表面的油污,可增强涂料的附着力。
根据油污情况,选用成本低、溶解力强、毒性小且不易燃的溶剂。
常用的有200号石油溶剂油、松节油、三氯乙烯、四氯乙烯、四氯化碳、二氯甲烷、三氯乙烷、三氟三氯乙烷等。
1. 2除锈彻底清除钢材表面的锈垢,以延长涂膜的使用寿命。
不同的钢铁器件表面有不同的除锈标准,它是按照除锈后钢材表面清洁度分级的。
除锈的方法主要有:(1)手工打磨除锈,能除去松动、翘起的氧化皮,疏松的锈及其他污物。
(2)机械除锈,借助于机械冲击力与摩擦作用,使制件表面除锈。
可以用来清除氧化皮、锈层、旧漆层及焊渣等。
其特点是操作简便,比手工除锈效率高。
常用的除锈设备有①钢板除锈机:制件在一对快速转动的金属丝滚筒间通过,靠丝刷与钢材表面的快速摩擦,除去制件板面的锈蚀层;②手提式钢板除锈机:由电动机通过软轴带动钢丝轮与钢材表面摩擦而除锈;③滚筒除锈机:靠滚筒转动使磨料与钢材表面相互冲击、摩擦而除锈。
现在还用喷砂除锈,并且是一种重要的除锈方式。
(3)化学除锈,通常称为酸洗,是以酸溶液促使钢材表面锈层发生化学变化并溶解在酸液中,而达到除锈目的。
常用浸渍、喷射、涂覆3种处理方式。
(4)除锈剂除锈,常用络合除锈剂,既可在酸性条件下进行,也可在碱性条件下进行,前者还适合于除油、磷化等综合表面处理。
钢的表面热处理表面热处理是指为改变工件表面的组织和性能,仅对工件表层进行的热处理工艺.1,表面淬火钢的表面淬火是将工件表面快速加热到淬火温度,迅速冷却,使工件表面得到一定深度的淬硬层,而心部仍保持未淬火状态的组织的热处理工艺.表面淬火的方法很多,目前广泛应用的有感应加热表面淬火,火焰加热表面淬火等.(1)感应淬火感应淬火是指利用感应电流通过工件所产生的热量,使工件表层,局部或整体加热并快速冷却的淬火.1)感应淬火频率的选用在生产中,根据对零件表面有效淬硬层深度的要求,选择合适的频率.①高频感应淬火常用频率为200~300KHz,淬硬层深度为0.5~2mm.主要用于要求淬硬层较薄的中,小模数齿轮和中,小尺寸轴类零件等.②中频感应淬火常用频率为2500~8000Hz,淬硬层深度为2~10mm.主要用于大,中模数齿轮和较大直径轴类零件.③工频感应淬火电流频率为50Hz,淬硬层深度为10~20mm.主要用于大直径零件(如轧辊,火车车轮等)的表面淬火和直径较大钢件的穿透加热.④超高频感应淬火电流频率一般为20~40KHz,它兼有高,中频加热的优点,淬硬层深度略高于高频,而且沿零件轮廓均匀分布.所以,它对用高,中频感应加热难以实现表面淬火的零件有着重要作用,适用于中小模数齿轮,花键轴,链轮等.2)感应淬火加热的特点与普通加热淬火相比,感应加热表面淬火有以下特点:①感应加热速度极快一般只需要几秒至几十秒时间就可以达到淬火温度.②工件表层获得极细小的马氏体组织,使工件表层具有比普通淬火稍高的硬度(高2~3HRC)和疲劳强度,且脆性较低.③工件表面质量好由于快速加热,工件表面不易氧化,脱碳,且淬火时工件变形小.④生产效率高便于实现机械化,自动化,淬硬层深度也易控制.上述特点使感应加热表面淬火得到广泛应用,但其工艺设备较贵,维修调整困难,不易处理形状复杂的零件.感应淬火最适宜的钢种是中碳钢(如40钢,45钢)和中碳合金钢(如40Cr钢,40MnB钢等),也可用于高碳工具钢,含合金元素较少的合金工具钢及铸铁等.一般表面淬火前应对工件正火或调质,以保证心部有良好的力学性能,并为表层加热作好组织准备.表面淬火后应进行低温回火,以降低淬火应力和脆性.(2)火焰淬火(见书)2,钢的化学热处理化学热处理是指将工件置于适当的活性介质中加热,保温,使一种或几种元素渗入其表层,以改变化学成分,组织和性能的热处理工艺.化学热处理的基本过程是:活性介质在一定温度下通过化学反应进行分解,形成渗入元素的活性原子;活性原子被工件表面吸收,即活性原子溶入铁的晶格形成固溶体或与钢中某种元素形成化合物;被吸收的活性原子由工件表面逐渐向内部扩散,形成一定深度的渗层.目前常用的化学热处理有:渗碳,渗氮,碳氮共渗等.(1)渗碳所谓渗碳是将工件放入渗碳气氛中,并在900~950℃的温度下加热,保温,以提高工件表层碳的质量分数并在其中形成一定的碳的质量分数梯度的化学热处理工艺.其目的是使工件表面具有高的硬度和耐磨性,而心部仍保持一定强度和较高的韧性.齿轮,活塞销等零件常采用渗碳处理.1)渗碳的方法渗碳所用介质称为渗碳剂,根据渗碳剂的不同,渗碳的方法分为固体渗碳,气体渗碳,真空渗碳和液体渗碳等.2) 渗碳用钢,渗碳后组织及热处理渗碳用钢为低碳钢和低碳合金钢,碳的质量分数一般为0.1%~0.25%.碳的质量分数提高,将降低工件心部的韧性.工件渗碳后其表层碳的质量分数通常为0.85%~1.05%范围.渗碳缓冷后,表层为过共析组织,与其相邻为共析组织,再向里为亚共析组织的过渡层,心部为原低碳钢组织.一般规定,从渗碳工件表面向内至碳的质量分数为规定值处(一般Wc=0.4%)的垂直距离为渗碳层深度.工件的渗碳层深度取决于工件尺寸和工作条件,一般为0.5~2.5mm.工件渗碳后必须进行适当的热处理,即淬火并低温回火,才能达到性能要求.渗碳件的热处理工艺有三种,如图3-35所示.①直接淬火法先将渗碳件自渗碳温度预冷至某一温度(一般为850~880℃),立即淬入水或油中,然后再进行低温回火.预冷是为了减少淬火应力和变形.直接淬火法操作简便,不需重新加热,生产率高,成本低,脱碳倾向小.但由于渗碳温度高,奥氏体晶粒易长大,淬火后马氏体粗大,残留奥氏体也较多,所以工件耐磨性较低,变形较大.此法适用于本质细晶粒钢或受力不大,耐磨性要求不高的零件.②一次淬火法工件渗碳后出炉缓冷,然后再重新加热进行淬火,低温回火.由于工件在重新加热时奥氏体晶粒得到细化,因而可提高钢的力学性能.此法应用比较广泛.③二次淬火法第一次淬火是为了改善心部组织和消除表面网状二次渗碳体,加热温度为Ac3以上30~50℃.第二次淬火是为细化工件表层组织,获得细马氏体和均匀分布的粒状二次渗碳体,( a)直接淬火(b) 一次淬火( c)二次淬火图3-35 渗碳体常用的热处理方法加热温度为Ac1以上30~50℃.二次淬火法工艺复杂,生产周期长,成本高,变形大,只适用于表面耐磨性和心部韧性要求高的零件或本质粗晶粒钢.渗碳件淬火后应进行低温回火(一般150~200℃).直接淬火和一次淬火经低温回火后,表层组织为回火马氏体和少量渗碳体,二次淬火表层组织为回火马氏体和粒状渗碳体.渗碳,淬火回火后的表面硬度均为58~64HRC,耐磨性好,心部组织取决于钢的淬透性,低碳钢一般为铁素体和珠光体,硬度137~183HBS.低碳合金钢一般为回火低碳马氏体,铁素体和托氏体,硬度35~45HRC,并具有较高的强度,韧性和一定的塑性.(2)钢的氮化(渗氮)它是指在一定温度下(一般在Ac1)以下,使活性氮原子渗入钢件表面的化学热处理工艺.其目的是使工件表面获得高硬度,高耐磨性,高疲劳强度和高热硬性和良好耐蚀性,因氮化温度低,变形小,应用广泛.常用的氮化方法有:气体渗氮和离子渗氮.①气体渗氮它是利用氨气在加热时分解产生的活性氮原子渗入工件表面形成氮化层,同时向心部扩散的热处理工艺.常用方法是将工件放人通有氨气的井式渗氮炉中,加热到500~570℃℃左右时,硬度无明显下降,热硬性高.渗氮前零件须经调质处理,以保证心部的强度和韧性.对于形状复杂或精度要求较高的零件,在渗氮前精加工后还要进行消除应力的退火,以减少渗氮时的变形.渗氮主要用于耐磨性和精度要求很高的精密零件或承受交变载荷的重要零件,以及要求耐热,耐蚀,耐磨的零件,如精密机床的主轴,蜗杆,发动机曲轴,高速精密齿轮等.但由于氮化温度低,所需时间特别长,一般氮化30~60h,才能获得0.2~0.5mm的氮化层,因此限制了它的应用.②离子氮化它是一种较先进的工艺,是指在低真空的容器内,保持氮气的压强为133.32~1333.32Pa,在400~700V的直流电压作用下,迫使电离后的氮离子高速冲击工件(阴极),被工件表面吸收,并逐渐向内部扩散形成渗氮层.离子氮化的特点是:渗氮速度快,时间短(仅为气体渗氮的1/5~1/2);渗碳层质量好,对材料的适应性强.目前离子氮化已广泛应用于机床零件(如主轴,精密丝杠,传动齿轮等),汽车发动机零件(如活塞销,曲轴等)及成型刀模具等.但对形状复杂或截面相差悬殊的零件,渗氮后很难同时达到相同的硬度和渗氮层深度.③碳氮共渗是指在工件表面同时渗入碳和氮,并以渗碳为主的化学热处理工艺.其主要目的是提高工件表面的硬度和耐磨性.常用的是气体碳氮共渗.碳氮共渗后要进行淬火,低温回火.共渗层表面组织为回火马氏体,粒状碳氮化合物和少量残留奥氏体,渗层深度一般为0.3~0.8mm.气体碳氮共渗用钢,大多为低碳或中碳的碳钢,低合金钢及合金钢.。
涂装前钢材表面处理规范
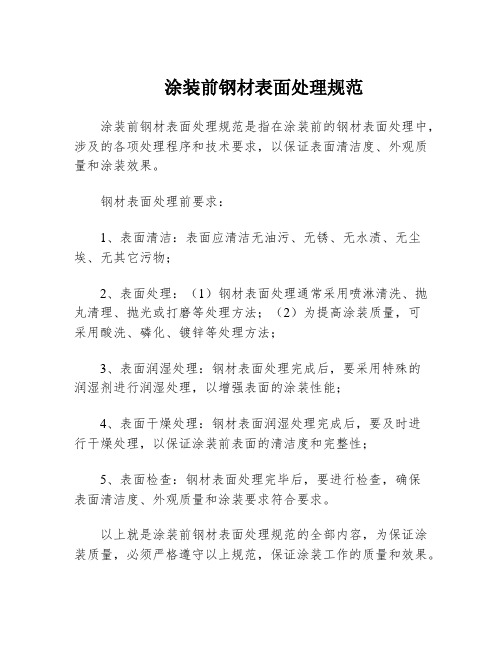
涂装前钢材表面处理规范
涂装前钢材表面处理规范是指在涂装前的钢材表面处理中,涉及的各项处理程序和技术要求,以保证表面清洁度、外观质量和涂装效果。
钢材表面处理前要求:
1、表面清洁:表面应清洁无油污、无锈、无水渍、无尘埃、无其它污物;
2、表面处理:(1)钢材表面处理通常采用喷淋清洗、抛丸清理、抛光或打磨等处理方法;(2)为提高涂装质量,可
采用酸洗、磷化、镀锌等处理方法;
3、表面润湿处理:钢材表面处理完成后,要采用特殊的
润湿剂进行润湿处理,以增强表面的涂装性能;
4、表面干燥处理:钢材表面润湿处理完成后,要及时进
行干燥处理,以保证涂装前表面的清洁度和完整性;
5、表面检查:钢材表面处理完毕后,要进行检查,确保
表面清洁度、外观质量和涂装要求符合要求。
以上就是涂装前钢材表面处理规范的全部内容,为保证涂装质量,必须严格遵守以上规范,保证涂装工作的质量和效果。
涂装前钢材表面处理是涂装质量的关键,只有表面处理做好,涂装才能达到质量要求,确保涂装质量合格。
因此,涂装前钢材表面处理规范一定要严格遵守,以保证涂装工作的质量和效果。
钢材料硬化处理及表面处理的种类
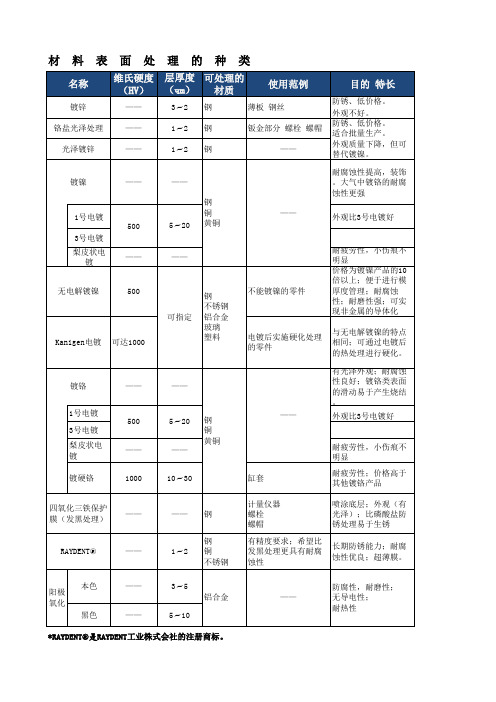
2.洛氏硬度 3.肖氏硬度 4.维氏硬度
1:短时间内即可求得
硬度值。
淬火 回火件
2:适用于对 实物进
表面氮化
行的中间检查。
利用金刚石压头或球形压头,施加标 表面氧化
3 :种类较多,许特
准负载,实验负载,从实验机的指使 铜 黄铜 青铜薄板 别注意。 *洛氏硬度
装置中显示的硬度值中求得。
*洛氏C标度硬度计 (HRC)不使用于细销 薄板等。
材料-梨皮表面处理-电镀
材料-电镀(3号电镀)
形成四氧化三铁保护膜(黑 色)
由于采用低温处理,因此材 料不受热的影响,塑料橡胶 等连接零件也可直接加工。
表面形成坚固的氧化保护 膜,并利用氧化保护膜的细 孔进行着色阳极氧化处理。
备注
为了使铜硬化处理或作;不 适用于主轴等较长的物体和 精密零件上。
属于低温退火。 消除成形时的内部应力提高 弹性。
备注
JIS Z2243
JIS Z2245 6JIS Z2245 JIS Z2244
计有A 标度(HRA)、 B标度(HRB)、C标度 (HRC)、D标度
(1:HR操D作)及等其多简种单类,。短
淬火 回火件 以一定的高度始锤落到试料的实验面 氮化处理 上,从其反弹的高度求得硬度。 经过渗碳处理等的大
型零件
时间内可获得数据。 2:适用大型零件。 3:凹坑浅不醒目,因 此适用于产品。 4:型小质轻,可携带
耐疲劳性;价格高于 其他镀铬产品
四氧化三铁保护 膜(发黑处理)
——
RAYDENT®
——
—— 钢
1~2
钢 铜 不锈钢
计量仪器 螺栓 螺帽
喷涂底层;外观(有 光泽);比磷酸盐防 锈处理易于生锈
钢铁防锈处理工艺流程

钢铁防锈处理工艺流程一、概述钢铁防锈处理是指为了延长钢铁材料的使用寿命,防止钢铁材料遭受腐蚀和氧化而采取的一系列技术措施。
防锈处理工艺可以分为物理方法和化学方法两大类。
物理方法主要包括喷涂、热浸镀、电镀、机械处理等;化学方法主要包括化学涂层、阴极保护、阳极保护等。
二、钢铁防锈处理工艺流程1. 表面处理钢铁材料在进行防锈处理之前,首先需要进行表面处理。
表面处理的目的是去除钢铁表面的油脂、尘土、氧化皮等杂质,以便后续的防锈处理能够更好地进行。
常用的表面处理方法有酸洗、喷砂、喷丸等。
2. 化学涂层化学涂层是一种常见的钢铁防锈处理方法。
在表面处理完成后,可以将钢铁材料浸入具有防锈效果的化学液中,使其表面形成一层防锈膜。
这层膜可以有效地隔绝钢铁与外界环境的接触,从而起到防止腐蚀和氧化的作用。
3. 热浸镀热浸镀是一种常用的物理防锈处理方法。
它的原理是将钢铁材料浸入熔化的金属中,使金属与钢铁表面发生化学反应,形成一层金属镀层。
这层镀层能够有效地隔绝钢铁与外界环境的接触,防止钢铁材料遭受腐蚀和氧化。
4. 电镀电镀是一种常用的物理防锈处理方法。
电镀的原理是利用电解作用,在钢铁表面镀上一层金属。
这层金属镀层能够有效地隔绝钢铁与外界环境的接触,防止钢铁材料遭受腐蚀和氧化。
5. 机械处理机械处理是一种常用的物理防锈处理方法。
它通过机械切削、磨削等方法,将钢铁表面的氧化皮和锈层去除,使其表面恢复光洁。
这样可以防止钢铁材料进一步氧化和腐蚀。
6. 阴极保护阴极保护是一种常用的化学防锈处理方法。
它利用电化学原理,在钢铁表面形成一层保护性的电位差,使钢铁处于保护性的电位。
这样可以防止钢铁材料遭受腐蚀和氧化。
7. 阳极保护阳极保护是一种常用的化学防锈处理方法。
它利用电化学原理,在钢铁表面形成一层保护性的电位差,使钢铁处于保护性的电位。
这样可以防止钢铁材料遭受腐蚀和氧化。
三、总结钢铁防锈处理工艺流程包括表面处理、化学涂层、热浸镀、电镀、机械处理、阴极保护和阳极保护等步骤。
钢筋表面处理方法及其应用
钢筋表面处理方法及其应用
增强钢筋与混凝土之间粘结力的关键在于提高钢筋表面的粗糙度,增加其与混凝土的接触面积。
以下是几种常用的钢筋表面处理方法:
1.喷砂处理:通过压缩空气将砂粒高速喷射到钢筋表面,去除表面的锈迹、
油脂和污染物,增加粗糙度。
2.酸洗处理:使用酸溶液去除钢筋表面的氧化膜,使其呈现活性状态,能够
更好地与混凝土粘结。
3.机械处理:利用砂轮机、喷丸等机械手段对钢筋表面进行磨削或抛丸,使
其变得粗糙,增加混凝土的附着力。
4.激光处理:使用激光对钢筋表面进行照射,使表面局部熔化再凝结,形成
具有粗糙表面的硬化层,提高与混凝土的粘结力。
5.涂层处理:在钢筋表面涂覆界面剂或环氧树脂等涂层材料,这些材料能够
填充钢筋和混凝土之间的微小空隙,提高粘结力。
在选择合适的表面处理方法时,需要考虑钢筋材料的类型、表面状况以及施工环境等因素。
处理后的钢筋应妥善保管,避免再次生锈或污染,以保证其与混凝土的粘结力。
钢材表面处理的6种方式
钢材表面处理的6种方式钢材是一种广泛应用于建筑、制造、交通等领域的材料,其表面处理是保证其性能和寿命的重要环节。
钢材表面处理的方式有很多种,本文将介绍6种常见的方式。
1. 酸洗酸洗是一种将钢材表面的氧化物和脏污物质去除的方法。
常用的酸洗液有硫酸、盐酸、氢氟酸等。
酸洗可以有效去除钢材表面的氧化皮和锈蚀物,提高钢材表面的光亮度和清洁度,为后续的表面处理提供良好的基础。
但酸洗会对环境造成一定的污染,需要注意安全操作。
2. 砂抛砂抛是一种用砂轮将钢材表面的氧化皮和锈蚀物去除的方法。
砂抛可以去除较重的氧化皮和锈蚀物,使钢材表面变得光滑,但会留下一定的砂痕和划痕,需要进行后续的打磨和抛光。
3. 喷丸喷丸是一种用高速喷射金属颗粒或矿物颗粒将钢材表面的氧化皮和锈蚀物去除的方法。
喷丸可以去除较重的氧化皮和锈蚀物,且可以改善钢材表面的粗糙度,提高其耐腐蚀性能。
但喷丸会产生噪音和粉尘,需要进行适当的防护措施。
4. 镀锌镀锌是一种将钢材表面涂上一层锌的方法。
锌具有很好的防腐蚀性能,能够有效地保护钢材表面不受氧化和锈蚀的侵害。
镀锌可以采用热镀锌和电镀锌两种方式,其中热镀锌的防腐蚀性能更好,但成本更高。
5. 涂层涂层是一种将钢材表面涂上一层保护层的方法。
涂层可以采用涂料、喷漆、粉末涂料等方式进行,不同的涂层具有不同的性能特点,如耐腐蚀性、耐磨性、耐高温性等。
涂层可以提高钢材表面的美观度和耐用性,但需要注意涂层的质量和厚度,以免影响钢材的使用寿命。
6. 氧化处理氧化处理是一种将钢材表面形成一层氧化膜的方法。
氧化膜具有很好的耐腐蚀性能,能够有效地保护钢材表面不受氧化和锈蚀的侵害。
氧化处理可以采用化学氧化和电化学氧化两种方式,其中电化学氧化的氧化膜质量更好,但成本更高。
总之,钢材表面处理是保证其性能和寿命的重要环节,需要根据不同的使用要求选择合适的处理方式。
以上介绍的6种方式都具有一定的优缺点,需要根据具体情况进行选择。
同时,钢材表面处理也需要注意环保和安全问题,避免对环境和人体造成不良影响。
表面钝化处理方法
表面钝化处理方法
表面钝化处理是一种常见的材料表面处理方法,旨在提高材料的耐腐蚀能力、防止氧化、增加材料的使用寿命。
表面钝化处理方法主要有以下几种:
一、镀锌
镀锌是将锌层成功地附着于金属表面,从而延长材料的使用寿命。
这种表面处理方法广泛应用于建筑、制造业和农业的领域。
镀锌分为电镀和热浸镀两种。
二、电泳涂层
电泳涂层是一种将液体涂料加入导电池内,然后在一定的电流下使材料表面均匀涂上一层漆膜。
电泳涂层工艺简单,且涂膜均匀,使用寿命较长。
三、磷酸钝化
磷酸钝化作为一种常用的钢铁材料表面处理方法,可以显著提高钢铁材料的耐腐蚀性能,增加材料使用寿命。
此外,磷酸钝化的涂层也具有良好的建筑性和装饰性。
四、阳极氧化
阳极氧化是一种将铝等金属材料暴露在含有硫酸等电解液中,然后在一定的电压下进行氧化。
这种表面处理方法可以生成一层坚硬的氧化膜,有效地提高金属材料的耐腐蚀性和硬度。
五、喷涂
喷涂是将带有颜料的液体喷在工件表面上,干燥后形成涂层。
这种表面处理方法工艺简单,成本较低,适用于大批量生产。
通过以上的介绍,我们可以看出不同的表面处理方法各有优缺点,需要根据实际需求选择合适的处理方法。
作为材料行业的从业者,我们应该熟悉不同的处理方法,以技术专业、质量保证的态度满足客户的需求。
钢铁表面处理技术的应用和研究
钢铁表面处理技术的应用和研究钢铁是一种广泛应用的金属材料,其表面处理技术对其性能和用途起着至关重要的作用。
钢铁表面处理技术主要包括防腐蚀处理、涂层技术和表面改性技术等方面,这些技术的应用和研究对于延长钢铁产品的使用寿命、提高其性能和功能、满足不同领域的需求等方面都具有重要意义。
本文将就钢铁表面处理技术的应用和研究进行探讨,以期对相关领域的专业人士和学生有所帮助。
防腐蚀处理是钢铁表面处理技术中的重要内容之一。
钢铁产品常常需要在恶劣的环境条件下使用,如高温、高湿度、酸碱腐蚀等,因此其表面的抗腐蚀能力就显得尤为重要。
防腐蚀处理的方法主要包括镀锌、喷涂涂料、热浸镀铝等。
这些方法可以有效地提高钢铁产品的抗腐蚀能力,延长其使用寿命。
在未来的研究中,可以在材料的选取、处理工艺、环保性等方面进行更深入的探讨和研究,以提高防腐蚀处理技术的效率和可持续性。
涂层技术是另一个钢铁表面处理技术中的重要内容。
涂层可以提高钢铁产品的耐磨性、耐腐蚀性、美观性等,使其更适用于不同的场合和环境。
目前,常用的涂层技术包括喷涂、电镀、热浸涂覆等。
此外,随着纳米技术的发展,纳米涂层技术在钢铁表面处理中也有着广阔的应用前景。
未来的研究可以着重探讨涂层材料的选择、涂层工艺的优化、涂层性能的测试等方面,以提高涂层技术在钢铁表面处理中的应用效果。
表面改性技术是钢铁表面处理技术中的又一重要内容。
表面改性技术可以改善钢铁产品的表面性能和功能,如增加其耐磨性、耐腐蚀性、附着力等,使其更适用于不同的工程应用。
目前,常用的表面改性技术包括表面喷丸处理、表面化学处理、表面机械加工等。
未来的研究可以针对不同的表面改性技术进行深入的探讨和比较研究,以找到更加适用于钢铁产品的新型表面改性技术。
总之,钢铁表面处理技术的应用和研究对于提高钢铁产品的性能和功能、延长其使用寿命、满足不同需求等方面具有重要意义。
未来的研究可以从材料的选择、工艺的优化、环保性等方面进行更深入的探讨,以提高钢铁表面处理技术的效率和可持续性。
- 1、下载文档前请自行甄别文档内容的完整性,平台不提供额外的编辑、内容补充、找答案等附加服务。
- 2、"仅部分预览"的文档,不可在线预览部分如存在完整性等问题,可反馈申请退款(可完整预览的文档不适用该条件!)。
- 3、如文档侵犯您的权益,请联系客服反馈,我们会尽快为您处理(人工客服工作时间:9:00-18:30)。
材的表面预处理按照顺序在氧化炉和还原炉中完成。
1.2.热浸镀分类
(2)保护气体还原法特点
:
缺:
设备比较复杂, 投资大,技术 难度大,适 合单一产品 的批量生产。
优:生产速度快
效率高、镀层结 合力好、无污染。 另外,还原型生 产线高温辐射加 热温度高,退火 时间长,产品性 能好。
现代带钢连续热浸镀采用的 最普遍和最广泛的一种工艺。
(1)溶剂法热浸镀的工艺流程为:
镀前检查一碱液除油一水清洗一酸洗一水清洗一
溶剂处理→烘干预热(湿式法无此程序)
一热浸镀锌一冷却一干燥一检验一成品
(1)溶剂法热浸镀特点:
溶剂法热浸镀特点: 溶剂法热浸镀特点:
1.2.热浸镀分类
(2)保护气体还原法(氢还原法)热浸镀:
该法主要采用保护气体还原法为前处理方式。钢
化学镀镍的装置示意图
化学镀镍及其原理
表一、镀液
成分 镍盐 还原剂 络合剂 稳定剂 缓冲剂 作用 提供被沉积的金属离子 化学镀镍的驱动力(次磷酸盐) 防止产生沉淀、控制反应速度等 防止分解 防止 PH 值波动
化学镀镍特点
镀层性能(Ni-P)
厚度均匀、表面光滑
硬度高、附着力好 抗腐蚀性好
钎焊
镀镍产品
镀镍产品
电镀及原理
在盛有电镀液的镀 槽中,经过清理和特殊预 处理的待镀件作为阴极, 用镀覆金属制成阳极,两 极分别与直流电源的负极 和正极联接。电镀液由含 有镀覆金属的化合物、导 电的盐类、缓冲剂、pH调 节剂和添加剂等水溶液组 成。通电后,阳极的金属 会氧化(失去电子),电 镀液中的金属离子,在电 位差的作用下移动到阴极 上形成镀层。
ห้องสมุดไป่ตู้
电镀的缺点
电镀的缺点首先是是污染问题:当镀液加温较高时, 镀液会加速蒸发和分解,气 雾中有高浓度的溶质成 分。这时会严重污染环境,尤其是酸、碱气雾,氰化 物和铬雾对环境的影响和人体危害会更大;镀液处理 过程中若不加以注意,则镀液的损耗量是相当大的; 电镀槽或加温(冷却)管渗漏往往也会造成严重污染。 另外,电镀过程中常常会造成不连续水膜(表面 被污染所引起的不均匀润湿性,使表面上的水膜变的 不连续)、孔隙、针孔、起皮、剥离、海绵状镀层、 烧焦镀层、麻点(在电镀或腐蚀中,与金属表面上形 成的小坑或小孔)等。
电镀要素
材料要求:镀层大多是单一金属或合金,
如钛、锌、镉、金或黄铜、青铜等;也
有弥散层,如镍-碳化硅、镍-氟化石墨等;
还有覆合层,如钢上的铜-镍-铬层、钢上
的银-铟层等。电镀的基体材料除铁基的
铸铁、钢和不锈钢等金属外,还有非铁 金属或ABS塑料、聚丙烯、聚砜和酚醛塑 料,但塑料电镀前,必须经过特殊的活 化和敏化处理。
发物或其反应产物蒸镀在基片上。
离子镀原理
离子镀的特点
离子镀特点如下: 一、优点 (1)膜层附着力强。 (2)膜层组织致密,耐蚀性好。 (3)具有绕镀性能,能够在形状复杂的零件表面
镀膜。
离子镀的特点
(4)可用来制备各种材料的薄膜,特别是可采用反
应离子镀制备各种化合物薄膜。
(5) 成膜速率高,可与蒸发镀膜的速率相当;且可 镀厚膜(达30m)。
电镀工艺一般包括电镀前预处理,电镀及 镀后处理三个阶段。基本工艺流程图如下所示:
工件
除油 清洗
清洗
电解除油 清洗
电镀 清洗
酸浸 产品
处理/烘干
电镀种类
镀锌 镀镍 镀铜
镀金
镀锡
种类
镀铬
镀银 复合电镀
合金电镀
电镀的优缺点
电镀的优点 电镀最大的优点是成本较低、使用的靶材 少。利用电解作用在机械制品上沉积出附着良 好的、但性能和基体材料不同的金属覆层的技 术,电镀层比热浸层均匀,一般都较薄,从几 个微米到几十微米不等。通过电镀,可以在机 械制品上获得装饰保护性和各种功能性的表面 层,还可以修复磨损和加工失误的工件。
钢铁材料的表面处理
《材料成型基础》
化学镀
定义:在经活化处理的基体表面上,镀液中 金属离子被催化还原形成金属镀层的过程。 原理:依据氧化还原反应原理,利用强还原 剂在含有金属离子的溶液中,将金属离子还
原成金属而沉积在各种材料表面形成致密镀
层的方法。
化学镀镍及其原理
定义:利用化学镀的原理,在镀件表面镀上 一层致密的金属镍层的方法。也叫Ni-P化学 镀。
• 电镀要素:电镀的要素: • 1.阴极:被镀物,指各种接插件端子 • 2.阳极:若是可溶性阳极,则为欲镀金属。 若是不可溶性阳极,大部分为贵金属(白 金,氧化铱) • 3.电镀液:含有欲镀金属离子的电镀液 • 4.电镀槽:可承受,储存电镀药水的槽体, 一般考虑强度,耐蚀,耐温等因素 • 5.整流器:提供直流电源的设备
1.1
热浸镀定义
热浸镀简称热镀,是把被镀金属件浸入到熔 融的金属或合金液体中使其表面形成金属镀层的一 种工艺方法。 镀层材料的金属或合金的熔点要比基体金属低 得多,故热镀层金属都采用低熔点的金属及其合金, 如锡(231.9℃)、铅(327.4℃)、锌 (419.5℃)、铝(658.7℃)及它们的合金,被镀 金属材料一般为钢、铸铁及不锈钢等。
热浸镀基本工艺流程
基本 工艺 流程 前处 理 热浸 镀 后处 理
清洗除 油
酸洗除 锈
水洗
熔剂处 理
1.
热浸镀分类
(1)按镀层类别分类:
热浸镀锌 热浸镀铝
热浸镀锡
热浸镀铅
1.2.热浸镀分类
(2)按前处理方法分类: 按前处理方法不同
溶剂法
干式 湿式
保护气体还原法
1.2.热浸镀分类
1.3.热浸镀的性能与应用
热浸镀的金属层一般较厚,因此能在某些 腐蚀环境中长期使用。或作为抗特种介质腐 蚀的防蚀镀层。
(1)抗大气腐蚀环境条件下应用 (2)抗高温、抗氧化和耐蚀条件下应用
离子镀
离子镀膜技术(简称离子镀),是在真空蒸发 和真空溅射技术基础上发展起来的一种新的镀 膜技术。在真空条件下,应用气体放电实现镀 膜,即在真空室中使气体或被蒸发物质电离, 在气体离子或被蒸发物质离子的轰击下,将蒸
原理(原子氢态理论)
H2PO2-+ H2O = HPO32-+ H++ 2[H] (次磷酸根) (亚磷酸根) Ni2+ +2[H] = Ni + 2H+ H2PO2-+ [H] = P + H2O + OH-
化学镀镍及其原理
1—水浴 2—烧杯 3—试样 4—温度计 5—化学镀液 6—电阻加热器