基于ANSyS的汽车轮胎有限元分析
汽车轮胎的有限元阐述

汽车轮胎的有限元阐述有限元分析法在对汽车轮胎力学结构进行分析之时,使研究工作达到了巅峰的阶段,这一分析方法在应用之时把汽车轮胎看作各向异性连接体,轮胎的构造与材质得到了简易的分析,同时能够将与轮胎相关的信息整体地呈现出来,进而完成对起初轮胎性能推测的目标。
目前有限元分析法在轮胎的充气形状和应力、载荷—位移曲线、接地面积和形状、轮胎的滚动阻力以及侧偏特性等方面都得到了广泛的应用,且取得了良好的应用效果。
1 汽车轮胎结构力学非线性有限元分析1.1 建设有限元汽车轮胎模型众所周知,汽车轮胎在地面运行的状态为滚动,在计算量上应用初始构形会产生很多弊端。
而有限元分析法的使用对轮胎模型进行建设之时有效地应用轮胎滚动构性这一参考构形,此时三维实体单元模拟的组成元素为以下种类:轮胎、轮惘及刚性路面;汽车有限元模型的建立健全,把轮胎运动的形式细化为刚体滚动和纯变形两类;而接触单元模拟成为表示轮胎与地面之间的相互作用的效果;胎面花纹沟被省略的同时细化网络将汽车轮胎接触区域周边的面貌呈现出来;三维超弹性模拟应用在轮胎胎面橡胶上;使用三维复合材料单元模拟的对象主要是胎体帘布层、带束层和冠带层;六面体八节点等参元模拟用于建设汽车轮胎结构;对于以上一切的单元,其均具有变形能力强、高硬度的特征。
1.2 对汽车轮胎承载部件受力情况的分析应用有限元分析法对195/651R489H型号的高速轿车子午线轮胎垂直加载这一工作状况下的结构进行分析。
因为汽车轮胎在垂直载荷的作用下,此时轮胎自体与地表接触时不是轴对称这是必然的结果,那么此时与轮胎相接触的地面区域势必会产生复杂多变的应力,且发生无规则的形变。
有限分析法在应用之时发现在接触底的中心轮胎胎体帘布层无应力产生,而当汽车轮胎与接地中心背离之时胎体帘布层受到了拉应力的作用,并且在接触区域的始末端拉应力的数值是最大的;有限元分析法在对汽车轮胎的带束层进行分析之时,发现其并不是在轮胎接地内、外区域均受到拉应力的作用,在接地区域内部其只受压应力,而产生压应力最大的位置依然是汽车轮胎接地区域的中心,并且轮胎第一带束层接地中心的压应力远远小于第二带束层,在接地区域的其他范围内第一、二带束层所受的压应力值基本一致。
基于ANSYS14.0汽车充气轮胎与地面接触的有限元分析
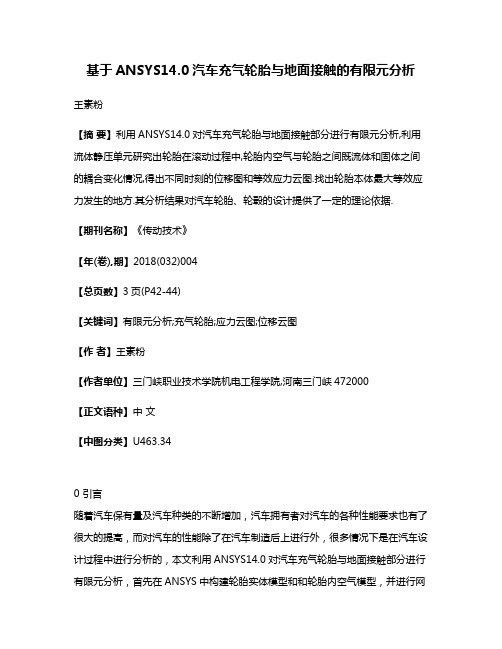
基于ANSYS14.0汽车充气轮胎与地面接触的有限元分析王素粉【摘要】利用ANSYS14.0对汽车充气轮胎与地面接触部分进行有限元分析,利用流体静压单元研究出轮胎在滚动过程中,轮胎内空气与轮胎之间既流体和固体之间的耦合变化情况,得出不同时刻的位移图和等效应力云图.找出轮胎本体最大等效应力发生的地方.其分析结果对汽车轮胎、轮毂的设计提供了一定的理论依据.【期刊名称】《传动技术》【年(卷),期】2018(032)004【总页数】3页(P42-44)【关键词】有限元分析;充气轮胎;应力云图;位移云图【作者】王素粉【作者单位】三门峡职业技术学院机电工程学院,河南三门峡472000【正文语种】中文【中图分类】U463.340 引言随着汽车保有量及汽车种类的不断增加,汽车拥有者对汽车的各种性能要求也有了很大的提高,而对汽车的性能除了在汽车制造后上进行外,很多情况下是在汽车设计过程中进行分析的,本文利用ANSYS14.0对汽车充气轮胎与地面接触部分进行有限元分析,首先在ANSYS中构建轮胎实体模型和和轮胎内空气模型,并进行网格划分,创建流体静压单元,定义带控制点的接触对,主要为轮胎底面与路面的刚—柔接触。
施加载荷后求解,利用流体静压单元研究出轮胎在滚动过程中轮胎内空气与轮胎之间的流体和固体之间的耦合变化情况[1],得出不同时刻的位移图和等效应力云图。
找出轮胎本体最大等效应力发生的地方。
其分析结果对汽车轮胎、轮毂的设计提供了一定的理论依据。
1 轮胎模型建立及网格划分本文所分析的对象是轮胎和道路之间的接触,在有限元分析软件ANSYS14.0中首先直接建立轮胎本体模型,所建立的几何模型尺寸为:轮胎厚度为5 mm,内半径为85 mm,整个轮胎的内半径为335 mm。
由于轮胎内的强化纤维为钢材料,假设轮胎内的空气为可压缩空气,使用HSFLD242单元模拟轮胎内的空气,因此选用PLANE183单元和SOLID186单元联合模拟轮胎。
基于ANSYS的火车车轮热应力有限元分析

基于ANSYS的火车车轮热应力有限元分析童乐1’2钟斌1’2陈刚1’2茆勇1’2邹强1’2高伟1’2(1.高性能轨道交通新材料及安全控制安徽省重点实验室;2.马鞍山钢铁股份有限公司)摘要火车刹车制动过程极易引发车轮热损伤,有必要对新设计车轮进行刹车制动过程的热应力分析。
利用AN SYS软件对新设计车轮进行热应力有限元分析,得出车轮在热载荷和静力载荷下的温度分布及应力分布情况,指导车轮的进一步优化设计。
关键词 热应力分析 A N S Y S溫度分布应力分布Finite Element Analysis of the Thermal Stress of Train Wheels Based on ANSYS Tong Le1,2Zhong Bin1,2Chen Gang1,2Mao Yong1,2Zou Qiang1,2Gao Wei1,2(1. Anhui Key Laboratory of High-performance Rail Transportation New Materials and Safety Control;2. Maanshan Iron & Steel Co. , Ltd.)Abstract The braking process of the train is very easy to cause the thermal damage of wheels. It is necessary to analyze the thermal stress of the newly designed wheels in the braking process. The thermal stress finite element analysis of the new designed wheels was carried out by ANSYS software, the temperature distribution and stress distribution of the wheels under heat load and static load were obtained* which guides the further optimum design of the wheels.Keywords thermal stress analysis ANSYS temperature distribution stress distribution〇前言目前,随着轨道车辆的运行速度及轴重的不断 增加,轨道车辆在高速行驶过程中所产生的动能也 在不断加大,这导致了在刹车制动过程中因闸瓦和 车轮踏面部位的机械摩擦而产生的热负荷引起的车 轮热损伤加剧[>4]。
基于ansys workbench的胎面花纹的结构优化设计

胎面花纹有限元分析及其优化设计摘要:随着科技的日新月异,汽车工业得到了迅速发展。
汽车工业的发展预示着对汽车上相关部件的要求也越来越高,而轮胎是汽车与路面直接接触的部件,研究轮胎结构特性对研究汽车行驶安全性,以及轮胎的使用寿命都非常有必要。
现代社会的发展主题是节能、环保。
现代环保标准对轮胎的使用寿命的要求也越来越高,轮胎胎面磨损将导致轮胎提前报废,同时改变轮胎诸多的使用性能,因此胎面磨损越来越引起轮胎制造商和使用者的关注。
此文章基于Ansys Workbench软件,对轮胎胎面花纹进行结构优化设计,减轻轮胎质量,增加热流量速率,同时使得胎面应力分布更加均匀、合理,从而节省了材料,延长轮胎的使用寿命,降低轮胎的制造成本,具有很好的实用价值。
关键词:胎面花纹;磨损;有限元分析;优化随着经济的不断发展和科学技术的日新月异,社会对产品的要求越来越高。
相同,汽车工业的飞速发展也给汽车上相关零部件提出了更高的要求。
而轮胎与路面直接接触,是汽车中最重要的部件之一。
轮胎性能的优劣直接影响着汽车的驾驶性、透过性、舒适性和安全性。
然而车轮表面形状,即轮胎胎面花纹又与轮胎性能直接相关,在车轮设计的四大要素中胎面花纹是最复杂,也是最重要的。
它决定了车轮的抓地力、排水性以及噪声。
因此,改进胎面花纹的设计是提高轮胎质量的重要途径之一。
轮胎设计技术经历了从经验设计阶段、半定量设计阶段到现代设计阶段的发展历程。
目前而言,就胎面花纹结构对轮胎的磨损的影响的研究还是挺多的,大部分还是以经验公式作为轮胎磨损的评价指标。
本文是建立在Ansys Workbench有限元分析的基础上,以胎面花纹为研究对象,对轮胎结构进行有限元分析,达到优化胎面结构,在保证胎面压力均布的同时降低胎面温度。
借助前辈的经验得出轮胎磨损与胎面花纹结构、胎面温度以及压力分布之间的关系,从而在保证轮胎结构安全的前提下,减小轮胎胎面磨损,达到延长轮胎使用寿命的目的,具有很好的研究价值。
基于ANSYSWorkbench的轮毂轴承法兰盘轮毂有限元分析_卢小辉
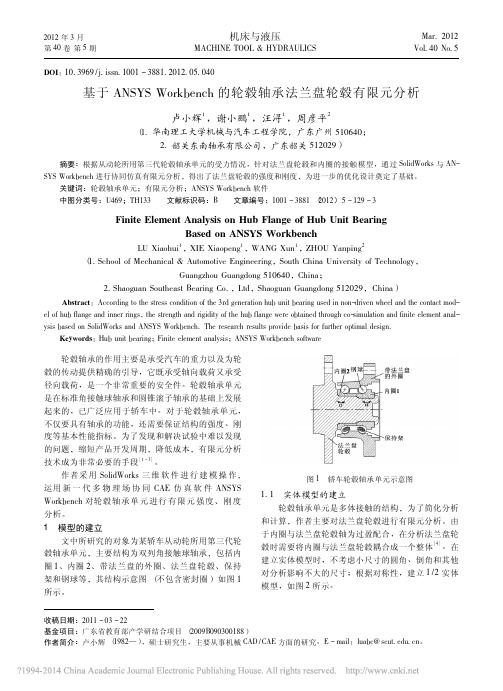
( ) Fz
=
mg 2
1 +2
H ·ag Tg
( 1)
Fy
=
-
F
z
·
ag g
( 2)
式中: Fz 为径向载荷 ( N) ,方向垂直向上; Fy 为轴 向载荷 ( N) ,负号表示方向由轮胎的外侧指向内测;
m 为 满 载 时 后 轴 质 量 ( kg ) ; H 为 轿 车 质 心 高 度
( mm) ; T 为后轴轮距 ( mm) ; g 为重力加速度,取 为 9. 81 m / s2 ; ag 为侧向加速度,取最大值为 0. 55g。 某轿车的整车参数见表 2 所示。
图 1 轿车轮毂轴承单元示意图
1. 1 实体模型的建立 轮毂轴承单元是多体接触的结构,为了简化分析
和计算,作者主要对法兰盘轮毂进行有限元分析。由 于内圈与法兰盘轮毂轴为过盈配合,在分析法兰盘轮 毂时需要将内圈与法兰盘轮毂耦合成一个整体[4]。在 建立实体模型时,不考虑小尺寸的圆角、倒角和其他 对分析影响不大的尺寸; 根据对称性,建立 1 /2 实体 模型,如图 2 所示。
表 2 某轿车的整车参数
满载时后轴质量 m / kg
1 200
质心高度 H / mm
600
后轴轮距 T / mm 轮胎滚动半径 Rs / mm
1 550 324
2. 2 确定边界条件
对于模型载荷与约束,主要参考文献 [8] 提供 的加载及约束方式,将法兰盘轮毂的 5 个螺栓孔面进 行全约束,对称面采用对称约束[3]。在约束了法兰盘 轮毂螺栓孔面的情况下,模型在内圈滚道上受到来自 钢球的作用,将径向载荷、轴向载荷以及所形成的力 矩作用在两个内圈滚道上。载荷与约束如图 4 所示。
基于ANSYS的火车车轮静强度及疲劳强度有限元分析

2019年14期创新前沿科技创新与应用Technology Innovation and Application基于ANSYS 的火车车轮静强度及疲劳强度有限元分析童乐,刘学华,张艳,钟斌(马鞍山钢铁股份有限公司技术中心,安徽马鞍山243000)前言车轮是轨道交通车辆走行部分中关键零部件之一,承受着来自多方面的复杂的应力作用,例如,车轮、车轴是通过过盈配合的方式压装成轮对,轮轴装配部位不可避免的会产生应力作用,形成轮轴装配应力,在轨道交通车辆实际运行过程中,由于运行线路地形复杂,车轮承受着不同工况下轨道对其赋予的不同形式的动态载荷,形成复杂的动态应力。
不仅如此,车辆频繁的启动、刹车制动、拐弯、上坡等行为也对车轮所受到的应力作用产生很大影响。
当前,高速度、大载重是轨道交通车辆快速发展的方向,轮轨之间的作用力也随之不断增长[1-2],因此车轮承受的应力作用变得更加复杂,车轮的设计强度很可能无法满足实际使用要求,车轮疲劳损伤等运行可靠性问题日益凸显。
因此,车轮在最初的轮型设计阶段有必要开展结构适用性分析,对车轮的设计强度进行校核[3-4]。
文献[5]仅对车轮的静强度做了分析,且其车轮为直辐板,本文研究的车轮采用的是S 型辐板。
目前,车轮强度校核主要是指依据UIC5l0-5标准和BS EN 13979-1标准进行车轮静强度和疲劳强度的校核分析,标准主要内容大致相同,对车轮在实际运行线路中普遍存在的直线工况、曲线工况和道岔工况进行了相关描述,并给出了对应不同工况所施加载荷大小的计算方法以及施加位置,同时对车轮有限元分析结果评价准则和方法也做出了规定[5-6]。
本文以典型的货运铁路车辆非动力整体车轮为研究对象,应用有限元仿真软件ANSYS 建立磨耗到限车轮的有限元模型,依据相关标准给出的载荷计算方法、施加位置和计算结果评定准则,建立车轮的静强度和疲劳强度校核有限元计算模型,获得不同工况下车轮的应力分布情况,对静强度和疲劳强度进行校核分析,为轮型设计提供依据。
基于ANSYS的载重车辆轮胎失效仿真研究[1]
2008年第4期车辆与动力技术Vehicle &Power Technol ogy总第112期文章编号:1009-4687(2008)04-0058-05基于ANS YS 的载重车辆轮胎失效仿真研究齐晓杰1,2, 于建国1(11东北林业大学交通学院,哈尔滨 150050;21黑龙江工程学院汽车工程系,哈尔滨 150050)摘 要:针对轮胎的主要失效形式,利用有限元法进行了失效仿真研究,主要进行了应力、应变及位移状况的分析,并对轮胎的寿命进行了预测.关键词:载重车辆轮胎;有限元分析;失效仿真;寿命预测中图分类号:U4631341+3 文献标识码:ASi m ul ati on Research on the Heavy 2duty Vehi cleTyre Fa ilure Based on ANS YSQ I Xiao 2jie1,2, Y U J ian 2guo1(11The Traffic College,Northeast Forestry University,Haerbin 150050,China;21The Aut omobile Engineering Depart m ent,Hei L ongjiang I nstitute of Technol ogy,Haerbin 150050,China )Abstract:The finite ele ment failure si m ulati on research of tyres is achived t o their main failure f or m.The stress,strain and the dis p lace ment in the tyres are analyzed ,and the seruice life of the Tyres is f orecasted .Key words:heavy 2duty vehicle tyres;finite ele ment analysis;failure si m ulati on;life p redicti on收稿日期:2008-09-01作者简介:齐晓杰(1960-),男,在读博士,教授. 随着汽车技术水平的不断提高,载重车辆行驶的速度越来越快,交通越来越便捷,但同时道路交通事故给人民带来的伤害也越来越大.其中,一部分道路交通事故是由于载重车辆轮胎在高速重载情况下突然失效造成的.因此,研究载重车辆轮胎的力学特性,进行有限元失效仿真研究对提高交通安全具有重要意义.作者主要针对载重车辆轮胎在高速和重载条件下出现的失效形式,研究载重车辆轮胎的力学特性并进行有限元失效仿真研究与分析,获得载重车辆轮胎在不同压力场和温度场下的应力、应变分布状况,最后对轮胎的综合应力、应变分布状况进行了较为深入的分析研究,并对轮胎的寿命进行了预测,为进一步进行子午线轮胎的动态接触分析和结构优化设计奠定了理论基础[1,2].1 载重车辆轮胎主要失效形式载重车辆轮胎大部分用于专业运输系统,承载重,经常在较差路面上行驶.在高速和重载的工况下,常见的失效形式有:①轮胎胎面磨损,包括正常和异常磨损;②轮胎结构性损坏,包括因轮胎使用不当造成的结构性损坏和因车辆底盘技术状况不良造成的结构性损坏.前者表现为轮胎胎体断线穿洞破裂、帘线松散脱胶、线层与面胶脱离等失效形式;后者表现为极度异常磨损、机械擦伤或划伤等失效形式.损坏原因主要有:①当载重车辆速度过高或第4期齐晓杰等:基于ANSYS 的载重车辆轮胎失效仿真研究负荷过大时,轮胎所受载荷也急剧增大,致使轮胎内帘布层之间、帘布层与橡胶之间、内胎和外胎之间的磨损加剧,热量增多,温度升高.而橡胶在高温下的抗拉强度、耐磨性和粘结力均显著降低,最终造成轮胎的结构性损坏;②载重车辆轮胎运营里程过长又没有及时进行换位保养,轮胎经常处以单方向与路面摩擦,极易造成轮胎的不均匀磨损.2 载重车辆轮胎失效仿真研究与分析1)轮胎三维实体模型的建立及模型导入选用典型规格的10100R20载重子午线轮胎作为载体进行建模分析.构建轮胎模型主要使用拉伸、实体化、阵列、环形折弯、镜像、复制特征等工具,轮胎与地面装配模型如图1所示.ANSYS 在默认的情况下是不能直接对Pr o /E 中的pat 及as m 文件进行直接转换的,必须通过以下对ANSYS 设置连接过程进行激活模块:鼠标点击“开始→程序→ANSYS8.0→U tilities →ANS_ADM I N ”,选择configurati on op ti ons →OK,接下来的对话框顺序选取.Configurati on Connecti on f or Pr o /E →OK,AN 2SYSMulti physics &W I N 32→OK,完成后ANSYS 提示已在自己的安装目录中成功生成config anscon 文件,记下config anscon 的路径.在接下来出现的对话框中“Pr o /Engireer I nstallati on path ”选项后输入Pr o /E 的起始安装路径如“C:\Pr o -gra m Files \p r oe W ildfire 3.0”,“Language used with Pr o /Engi 2neer ”选项用默认的usascii,点击OK .出现对话框提示在Pr o /E 目录下建立了一个p r otk .dat 文件,点击确定完成配置.然后将config anscon 拷贝到Pr o /E 的安装路径.最后,将ANSYS 的路径追加到path,如“C:\Pr ogra mFiles \Ansys I nc \Shared Files \bin \intel ”运行Pr o /E,在Pr o /E 软件的工具菜单后面出现了ANSYS8.0,点击Pr o /E 中的ANSYS8.0按钮(如图2所示),子午线轮胎便导入ANSYS 中[3~6].图1 子午线轮胎三维模型图2 将子午线轮胎模型导入ANSYS 软件2)子午线轮胎的有限元失效仿真研究1)网格划分为精确分析接触区域的应力-应变场,对可能接触的胎圈区域进行网格细分,并且接地部分的网格划分得更细,划分密度为10.由平面网格旋转拉伸生成3/4三维模型,如图3所示.图3 网格划分2)模型特殊处理轮辋与胎圈的过盈配合:轮辋与胎圈是过盈配合,考虑到轮辋定位后的实际位置与定位前的胎圈是相交的,本模型先将轮辋沿轮胎轴线移动-40mm ,使轮辋与胎圈有一定间隙,再给轮辋定义一个沿轴向的位移(40mm ),通过定义接触边界条件来真实地模拟轮辋与胎圈的配合.在考虑轮辋的约束时,通过将钢丝圈上所有节点的6个自由度全部约束;当考虑路面对轮胎的约束时,将模型中的目标面(即地面)的所有自由度约束.试验中的下沉量从轮胎充气后的胎面位置开始计算,即充气过程中路面对轮胎没有约束.由于预先不知道充气后胎面的位置,为了真实地模拟试验,本模型将路面从胎面的初始位置沿径向向外移动(大于估计的胎面径向位移量),保证充气过程中路面对轮胎没有约束.3)边界条件的设定通过直接约束法解决接触问题.将轮辋和路面定义为刚体,给定轮辋沿轴向的位移和路面移向轴心的位移,将可能与轮辋、路面发生接触的单元定义为可变形体.・95・车辆与动力技术2008年4)载荷工况的设定对模型先后施加下述5种载荷:①轮辋定位载荷:通过轮辋沿轴向(X方向)的位移来实现;②充气压力:施加在轮胎的内表面;③静负荷:通过路面相对于轮胎轴心的下沉量来实现;④自由滚动:通过轮胎的扭矩控制;⑤稳态滚动:通过轮胎的转速控制.模拟的试验条件:充气压力为0184MPa、静负荷为25000kg(对应路面的下沉量为28mm),充气压力为0125MPa、静负荷为2940kg(对应路面的下沉量为10mm)两种情况.静负荷是充气后加上去的,即路面的下沉量是从轮胎充气后的位置计算的.滚动工况通过施加转矩来实现,在轮胎的中心轴处左右两侧端面约束X方向位移为0,对地面施加固定约束.在轮胎上施加实际工作时承载的重量40kg,在轮心处内表面节点施加恒定转速1313rad/s.考虑到轮胎与地面的摩擦作用,静摩擦系数取为0.7[7,8].首先建立起轮胎与地面的接触模型,定义接触对过程如图4所示.约束的建立及加载过程如图5、6所示.施加对称载荷的过程如图7所示.轮胎与轮辋间的接触换热用热-耦合分析方法来完成,热-耦合分析方法通过施加速度边界条件和施加热边界条件来实现.设置过程如下图8所示.图4 接触对的建立图5 建立约束(左)和施加均布载荷(右)图6 施加静载荷(左)施加扭矩(右)图7 施加对称载荷图8 施加速度(左)和热(右)边界条件3 仿真结论分析1)不同压力场下应力和应变静止工况下不同压力场的变形如图9所示,自由滚动工况下不同压力场的变形如图10所示,静止工况下不同压力场的应力如图11所示,自由滚动工况下不同压力场的应力如图12所示,轮胎不同层之间的应力关系如图13所示.图9 静止工况下的轮胎变形・6・第4期齐晓杰等:基于ANSYS的载重车辆轮胎失效仿真研究图10 自由滚动工况下的轮胎变形图11 静止工况下的接触应力图12 自由滚动工况下的接触应力图13 轮胎不同层间的应力 2)轮胎的应力关系分析由图可以分析出,在胎冠部中央张力最大,当胎体的约束程度提高时,胎体内的张力逐渐减小,而带束内的帘线所承受的力不断增大.分析结果表明,带束层受力的基本状况主要取决于充气压力,静负荷的作用主要在接地区里影响带束层的受力状况,而钢丝圈的应力几乎不受影响.3)整体分析由分析得到的结果可以发现施加静态载荷后,轮胎接地面内最大值并不出现在接地面中心,而是偏离中心节点.通过胎面位移随充气压力的变化关系可以看出,充气开始阶段胎面位移有波动,随着充气压力增大,胎面位移量增大,且与充气压力基本呈线性关系.4)接地区域分析由图可以看出,垂直位移主要集中在与地面接触的节点上,随着下沉量的增大,接地区域扩大,接触压力增大,并且接地区域近似为1/4椭圆形.随着下沉量增大,接触反力增大,并与下沉量近似呈线性关系.在一定下沉量条件下,随着充气压力提高,路面接触反力增大,并且两者基本呈线性关系.从轮胎断面变形前后的对照图中,可以看到带束层及胎体帘线产生了变形.接地区域轮胎中应变分布图显示了在带束层边缘和胎圈外侧应变较大,由此可以预测轮胎的滚动过程中,由于橡胶存在滞后损失,使这两个部位容易生热,并且散热较困难,致使温度较高.这与轮胎在实际工作过程中,经常出现肩空、肩裂和胎圈爆破是一致的.4 子午线轮胎的疲劳寿命预测通过以上有限元分析得到的变化规律,可以直观的观察与轮胎寿命相关的负荷、压力、速度和温度的变化趋势,从而可以预测出轮胎的使用寿命.当轮胎受随机载荷作用时,其疲劳寿命不能是各循环应力对应寿命的简单迭加,而需要运用一定的累积损伤法则将各应力引起的损伤累加起来,进行寿命计算.本研究采用M iner 线性累积损伤法则计算累积损伤寿命N ,其具体形式如下:N =∑mi =1n i /∑mi =1n iN i,(1)式中 n i 为每次运行中某种循环的循环次数;N i 为根据该循环的应力幅值考虑平均应力的影响,m 为统计出的应力循环种类数.汽车轮胎行驶过程中承受多种载荷的作用,但总的说来可以分为径向载荷和弯曲载荷两种,根据以往的轮胎试验,轮胎因弯曲疲劳造成破坏的比例很高,并且大多数同类型轮胎的疲劳裂纹都产生在轮辐螺母座附近,而径向疲劳造成破坏的比例相对较低,所以选择轮辐螺母座处在弯曲工况下进行寿命计算.在轮胎疲劳试验中,每个循环的最大主应力及最小主应力都分别有它们的最大值和最小值,利用公式(2)可求出当量应力在一个循环周期的幅值σra 和平均值σr m .σra =σ21a +σ22a -σ1a σ2a ,σr m =σ21m +σ22m -σ1m σ2m ,(2)式中 σ1a 为最大主应力在一个循环周期内的幅值;σ2a 为最小主应力在一个循环周期内的幅值;σ1m・16・车辆与动力技术2008年为最大主应力在一个循环周期内的平均值;σ2m为最小主应力在一个循环周期内的平均值.本研究通过对子午线轮胎进行了有限元失效仿真分析,当给轮胎施加25000N垂直载荷和8232 N侧向载荷时,得最大主应力平均值σ1m=35413 MPa,最大主应力幅值σ1a=63183MPa,最小主应力平均值σ2m=186164MPa,最小主应力幅值σ2a =86164MPa.将这些数据代入公式(2),可求当量应力幅值σra=77179MPa,当量应力平均值σ= 306198Mpa.5 结束语利用Pr o/E的强大建模功能建立了载重车辆轮胎三维模型,通过专用的模型数据接口技术将模型导入到ANSYS软件中进行有限元研究与分析,模拟了轮胎模型的受力特点并对轮胎的使用寿命预测进行了探讨,为进一步进行轮胎动态分析和结构优化设计制造奠定了理论基础.由于研究部分相关参数是参考典型规格的轮胎取得的,研究结论在实际应用过程中可能会有所偏差,应根据实际情况详加考虑.参考文献:[1] 崔慧萍,陈 丽.载重汽车轮胎的使用现状及今后的发展[J].橡胶科技市场,2006(22):4-5.[2] 王洪礼,任 炜,乔 宇.汽车轮胎动力学特性研究[J].机械强度,2004(3):345-348.[3] 李 科,傅洪芳.改进花纹设计轻型载重轮胎高速性能[J].轮胎工业,2001(3):131-134.[4] 恒盛杰资讯.Pr o/E NGI N EER中文野火版从入门到精通[M].北京:中国青年出版社,2007.[5] 张许红,赵 红,景世庭.7.50_1614PR混合花纹轻载轮胎的结构设计[J].轮胎工业,2005(4):206-208.[6] 吴小国,秦东晨.Pr o/E与ANSYS接口[J].现代制造技术与装备,2007(1):19-20.[7] 俞 淇,戴元坎,张 凯.静负荷下轮胎接地压力分布测试的研究[J].轮胎工业,1999,20(1):47-49.[8] 闫相桥.轮胎结构有限元分析应用于载重子午胎胎体反包高度的优选[J].复合材料学报,2001,15(4):4-9.(上接第53页)通过表2可知,有限元分析结果与试验分析能很好的对应,该有限元模型的建立具有一定的精度,有限元模型能很好的模拟白车身进行理论分析,模拟分析的结果能较为精确的反映白车身的结构特性.4 结 论白车身的一阶扭转频率值为2919Hz,一阶弯曲模态频率值为4615Hz,一般同类车一阶扭转频率值为25Hz左右,一阶弯曲频率为40Hz左右,因此可以认为该车具有较好的刚度性能,同时具有一定的优化设计空间.所建立的模态试验方法对同类车的开发具有实际价值和指导意义.参考文献:[1] 高云凯.汽车车身结构分析[M].北京:北京理工大学出版社,2006.[2] 蓝晓理.轿车车身的低阶模态分析[D].长春:吉林工业大学,2000.[3] 师汉民,谌 刚,吴 雅.机械振动系统[M].武汉:华中理工大学出版社,1992.[4] 刘生涛,杨凤鹏.精通Ansys[M].北京:清华大学出版社,2002.[5] 李 昊,陈 剑,赵旭东,等.商务车车身地板动态特性的试验研究[J].合肥工业大学学报,2004,27(11):1460-1463.[6] 刘焕广.轿车白车身结构有限元及其试验分析[J].合肥工业大学学报,2007,30(12):1615-1619. [7] 曹树谦,张文德,萧龙翔.振动结构模态分析[M].天津:天津大学出版社,2001.・26・。
基于ANSYS汽车铝合金轮毂的有限元分析
10.16638/ki.1671-7988.2020.23.044基于ANSYS汽车铝合金轮毂的有限元分析张舵,迟瑞娟*(中国农业大学工学院,北京100083)摘要:轮毂作为支撑汽车重量并保证汽车顺利行驶的重要零部件,其结构强度和振动特性对于汽车安全性至关重要。
文章以17英寸汽车铝合金轮毂为研究对象,根据国家标准GB/T 3487-2005《汽车轮辋规格系列》利用Solidworks 对其三维建模,并通过有限元分析软件ANSYS进行了静力分析,验证了其结构强度的合理性,在此基础上进行了有预应力的模态分析,并通过和外界激振频率的对比,结果表明可以避免共振的发生,为轮毂的优化设计提供了理论依据。
关键词:轮毂;静力分析;模态分析中图分类号:U463.343 文献标识码:B 文章编号:1671-7988(2020)23-139-05Finite Element Analysis of Aluminum Alloy Wheel Hub based on ANSYSZhang Duo, Chi Ruijuan*(College of Engineering, China Agricultural University, Beijing 100083)Abstract: As an important part to support the weight of the automobile and ensure the smooth running of the automobile, the structural strength and vibration characteristics of the hub are very important for the safety of the automobile. In this paper, according to the national standard GB / T 3487-2005 "specification series of automobile rims", the 3D modeling of 17 inch automobile aluminum alloy wheel hub is carried out by SolidWorks, and the static analysis is carried out by ANSYS, The rationality of its structural strength is verified, on this basis, the modal analysis with prestress is done, and the comparison with the external excitation frequency proves that resonance can be avoided, which provides a theoretical basis for the optimal design of wheel hub.Keywords: Automobile hub; Static analysis; Modal analysisCLC NO.: U463.343 Document Code: B Article ID: 1671-7988(2020)23-139-05前言轮毂是汽车不可或缺的零部件,不仅要支撑汽车的整车重量,而且在汽车行驶过程中,还要受到路面和转向时的不同大小、方向的作用力,对汽车的顺利行驶和车内人员的乘坐舒适度起到了重要作用,故研究轮毂的应力和振动特性意义重大。
基于ANSYS Workbench的轮毂弯曲疲劳分析
10.16638/ki.1671-7988.2021.012.027基于ANSYS Workbench的轮毂弯曲疲劳分析胡裕超,杨辉(桂林理工大学机械与控制工程学院,广西桂林541006)摘要:轮毂是汽车运行时的主要承载部件,对于汽车安全行驶和可靠运行起着重要作用。
特别对于设计者而言,其各方面的性能都应得到重视。
文章以家用汽车轮胎的轮毂(18×7.5J)为研究对象,利用通用设计软件SolidWorks 建立轮毂仿真模型,而后将轮毂仿真模型导入ANSYS19.2中的geometry模块中进行分析,并且参考国标,在材料库输入铝合金A356的相关参数,得到铝合金A356的S-N曲线,最后求解得到轮毂在周期性弯曲载荷下的安全系数和使用寿命分布云图,根据以上仿真结果,判断轮毂是否符合使用要求,对设计人员具有指导作用。
关键词:轮毂;铝合金;弯曲疲劳;ANSYS workbench中图分类号:U463.343 文献标志码:A 文章编号:1671-7988(2021)12-90-03Bending Fatigue Analysis of Wheel Hub Based on ANSYS WorkbenchHU Yuchao, YANG Hui( College of Mechanical and Control Engineering, Guilin University of Technology, Guangxi Guilin 541006 )Abstract: As an important part of the car wheel, the wheel hub has a significant impact on the safety and reliability of the car. Especially for designers, all aspects of its performance should be paid attention to. This paper takes the wheel hub (18×7.5J ) of the family car tire as the research object, establishes the 3D model of the wheel hub through the 3D software SolidWorks, imports it into the simulation software for simulation analysis, and establishes the fatigue life curve (S-N curve) of aluminum alloy (A356), through the analysis to obtain the safety factor and fatigue life cloud diagram of the hub, according to the above simulation results, determine whether the hub meets the requirements of use, which has a guiding role for the designer. Keywords: Wheel hub; Aluminum alloy; Bending fatigue; ANSYS workbenchCLC NO.: U463.343 Document Code: A Article ID: 1671-7988(2021)12-90-03引言传统的轮毂设计必须要通过实验法测定轮毂的各项结构性能以及疲劳使用寿命,极其耗费成本[1]。
ANSYS做的轮胎模型
ANSYS做的轮胎模型fini/cle/prep7/title,wheel-3!_____________________________________定义单元类型__________________________________________________et,1,45 !用来给土层,轮辋以及基层来分网格et,2,181!_____________________________________________________________ _______________________________________!____________________________________定义轮胎材料参数_________________________________________________!___________________________定义超弹材料,用9常数模型(单位为MPa)___________________mp,ex,1,8000e6mp,prxy,1,0.4!____________________________定义正交弹性材料(单位为MPa)___________________________mp,ex,2,1.03e10mp,prxy,2,0.33mp,ex,3,2.1e11mp,prxy,3,0.3save,material4,db/prep7!_______________________________________定义道路几何参数___________________________________________areaload=0.557800e6 !单位mpaarearadiu=0.1066 !单位mtop=0.5493thick1=0.04+top !单位mthick2=0.06thick3=0.07thick4=0.25thick5=0.27thick6=3.5distanceofaxie=1.5*arearadiu !两轮中心距rightb=1.50leftb=-1.50frontb=1.50backb=-1.50depthb=-(thick1+thick2+thick3+thick4+thick5+thick6)!_____________________________________________________________ ______________________________________!______________________________________定义道路材料参数_____________________________________________ex1=1200e6 !单位MPaprxy1=0.35dens1=2.509e-03 !单位kg/m3ex2=1000e6prxy2=0.35dens2=2.447e-03ex3=1000e6prxy3=0.35dens3=2.432e-03ex4=1400e6prxy4=0.2dens4=2e-03ex5=800e6prxy5=0.2dens5=1.800e-03ex6=35e6prxy6=0.4dens6=1.900e-03!_____________________________________________________________ ______________________________________!________________________________定义道路材料参数__________________________________________________mp,ex,4, ex1 !定义道路第一层材料参数mp,PRXY,4,prxy1mp,dens,4,dens1mp,ex,5, ex2mp,PRXY,5,prxy2mp,dens,5,dens2mp,ex,6, ex3mp,PRXY,6,prxy3mp,dens,6,dens3mp,ex,7, ex4mp,PRXY,7,prxy4mp,dens,7,dens4mp,ex,8, ex5mp,PRXY,8,prxy5mp,dens,8,dens5mp,ex,9, ex6mp,PRXY,9,prxy6mp,dens,9,dens6!_____________________________________________________________ _____________________________________/prep7!______________________________建立轮胎模型_________________________________________________________k,1,0,0,0k,2,0,0,0.03k,3,0,0.01,0k,4,0.297,0,0k,5,0.297,0,0.2k,6,0.297,0,-0.2k,7,0.297,0,0.01k,8,0.297,0,-0.01k,9,2,0,0.01k,10,0,0,-0.005k,11,0,0,0.005k,12,0.4028,0,0k,13,0.5425,0,0k,14,0.4028,0.01,0circle,1,0.297,2,4,360,1l,5,6LGEN,2,4,,1,0.01l,6,19l,5,18lsel,s,,,4,7,1al,alllsel,allVDRAG,1,,,,,,1,2,3vsel,s,,,1,3,1vadd,all !4torus,0.4028,0.1362,0.1422 !1torus,0.4028,0.1422,0.1465 !2vsbv,2,4,sepo,dele,keep !3,5vdele,3vsbv,1,4,sepo,dele,keep !2,3vdele,2wpoffs,,, 0.110836 WPSTYLE,,,,,,,,1wpstyle,0.05,0.1,-1,1,0.003,0,0,,5 vsbw,4,speo,delevdele,2wpoffs,,, -0.110836*2vsbw,1,speo,dele !轮辋宽0.11085 vdele,4l,11,10 !40circle,11,0.297,2,7,360,1lsel,s,,,41,43,2lsel,a,,,56al,all !11lsel,allvdrag,11,,,,,,40 !1vsel,s,,,1,2vadd,all !4vsel,allvglue,3,4,5 !1内胎,2外胎,6轮辋!分网格HPTCREATE,area,11,, coord,0,0,0.005HPTCREATE,area,73,, coord,0,0,-0.005 vsel,s,,,6type,1mat,3mshape,1,3Dmshkey,0esize,0.04!要粗化vmesh,allvsel,all !1336,1178csys,0!给外轮胎分网格!HPTCREATE,area,21,, coord,0,0.5493,0 vsel,s,,,2type,2mat,1mshape,1,3D !定义单元形状mshkey,0esize,0.02 !定义为自由网格!可能要局部粗化vmesh,allvsel,all!给轮胎束带层分网格vsel,s,,,1type,2mat,2mshape,1,3Dmshkey,0esize,0.02!可能要局部粗化vmesh,all!在内胎的内面上施加面荷载!13,14,67-70asel,s,,,13,14asel,a,,,67,70,1nsla,sSF,all,pres,0.63e6 !压力单位为Pa csys,0save,finimodel,db/prep7!____________________________________________________定义路面_______________________________________________block,rightb,leftb,-top,-thick1,frontb,backb !3block,rightb,leftb,-thick1,-(thick1+thick2),frontb,backb !4block,rightb,leftb,-(thick1+thick2),-(thick1+thick2+thick3),frontb,backb !5 block,rightb,leftb,-(thick1+thick2+thick3),-(thick1+thick2+thick3+thick4),frontb, backb!7block,rightb,leftb,-(thick1+thick2+thick3+thick4),-(thick1+thick2+thick3+thick4+ thick5),frontb,backb!8block,rightb,leftb,-(thick1+thick2+thick3+thick4+thick5),depthb,frontb,backb!9 vglue,3,4,5,7,8,9 !3,10,11,12,13,14vsel,s,,,3type,1mat,4mshape,1,3D !定义单元形状mshkey,0esize,0.0.5 !定义为自由网格vmesh,allvsel,s,,,10type,1mat,5mshape,1,3D !定义单元形状mshkey,0esize,0.15 !定义为自由网格vmesh,allvsel,s,,,11type,1mat,6mshape,1,3D !定义单元形状mshkey,0esize,0.18 !定义为自由网vmesh,allvsel,s,,,12type,1mat,7mshape,1,3D !定义单元形状mshkey,0esize,0.2 !定义为自由网格vmesh,allvsel,s,,,13type,1mat,8mshape,1,3D !定义单元形状mshkey,0esize,0.3 !定义为自由网格vmesh,allvsel,s,,,14type,1mat,9mshape,1,3D !定义单元形状mshkey,0esize,0.5 !定义为自由网格vmesh,allnsel,allvsel,allasel,allfini/solu!__________________________________给道路加约束_______________________________________________csys,0nsel,allnsel,r,loc,y,depthbd,all,all,0nsel,allnsel,r,loc,x,rightbnsel,a,loc,x,leftbd,all,ux,0nsel,allnsel,r,loc,z,frontbnsel,a,loc,z,backbd,all,uz,0save,pavemodel,dbfini/prep7!______________________________加接触对_________________________________________r,1001et,11,targe170et,12,conta174KEYOPT, 12,2,1 !定义使用罚函数KEYOPT, 12,12,1 !定义为无限大,忽略滑动KEYOPT, 12,7,3 !对下一个子步预测一个最小的时间增量asel,s,,,22asel,a,,,100,101nsla,s!nsel,r,loc,y,-0.4,-0.5493,0.0001cm,_contact12,nodetype,12real,1001esurf,,buttomasel,s,,,9 !目标面,选择较为粗的网格nsla,s!nsel,r,loc,x,-0.8,0.8,0.0001!nsel,r,loc,z,-0.7,0.7,0.0001cm,_target12,nodetype,11real,1001esurf,,topsave,contact,dbfinifini/solunsel,s,,,206nsel,a,,,412d,all,all,0!d,all,uy,0vsel,s,,,1,2nsel,r,loc,x,0d,all,ux,0vsel,s,,,1,2vsel,a,,,6nsel,r,loc,z,0d,all,uz,0antype,staticasel,allnsel,alltime,1solve但是其接触部分的UY,UX方向位移明显错误(问题1)当我把材料一改为超弹材料mp,ex,1,9000mp,prxy,1,0.49MPTEMP,,,,,,,,MPTEMP,1,0MPDATA,DENS,1,,1150TB,mooney,1,1,9,MOONTBTEMP,0TBDATA,,0.770,,0.0671,,,0.0955 TBDATA,,,,,,,MPTEMP,,,,,,,,MPTEMP,1,0。