FQC检验规范.doc
FQC检验作业规范

3. 表單﹕《成品檢驗記錄
表》《不合格品處理單》 《品質異常改善追蹤 單》
核准
審核
製作
製作日期
SMD 系列外 PIN 的吃錫性檢驗用 20X 顯微鏡視檢。 6.2 尺寸﹕以遊標卡尺﹑萬分尺﹑塞規﹑模具等量治具檢驗確認。 6.3 電氣(功能)﹕依據《测试规格书》所規定的檢驗项目和檢驗設備。 七﹑檢驗設備 7.1 外观:目视、CCD 放大镜、显微镜、点规等。 7.2 尺寸:遊標卡尺﹑萬分尺﹑塞規﹑模具等。 7.3 电气功能:耐压测试机、数字万用表、电源供应器、电子负载、示波器等。 7.4 平整度检验:主要用光学分析仪。
4.3.1 根據控制計畫的要求,品保课策劃對產品實施全尺寸檢驗與功能試驗,並保持核對總和試 驗記錄 AC=0﹐RE=1。全尺寸检验的频率按顾客要求执行。无客户特殊要求则一年检验一次。 五﹑檢驗依據 5.1 抽樣依據《抽樣檢驗作業指導書》。 5.2 外觀檢驗依據《卷装沾異物檢驗標準》﹑《成品外觀檢驗標準》及”比對樣品”。 5.3 尺寸檢驗依據《尺寸檢驗標準規範》和《外观尺寸通用》。 5.4 電氣檢驗依據《測試規格書》。 5.5 包裝檢驗依據《包裝作業標準規範》﹑《產品包裝數量標准規範》﹑《產品包裝作業規範》。 5.6 平整度检验依據《成品外觀檢驗標準》。 六﹑檢驗方法 6.1 外觀﹕以距離 30cm 目視檢驗具體參照《成品外觀檢驗標準》﹐以及放大鏡﹑20~40X 顯微鏡確認。
文件編號
版本/次
A0
頁次 第 1 頁 共 4 頁
FQC 檢驗作業規範
一﹑ 目的﹕為確保產品最終檢驗規範化﹑標準化﹐以滿足客戶品質要求。 二﹑ 範圍﹕凡本公司制程完成之所有產品的入庫前檢驗。 三.﹑抽樣計畫 3.1 非汽车行业产品采用 ANSI-ASQZ1.4 一般檢驗水準 II 級 (適用於外觀﹑電氣功能項目)。
FQC检验规范

FQC检验规范流程1. 最终检验程序(FQC)1.1 目的:对产品出厂前检验/试验,确保产品质量满足客户要求。
1.2范围:产品检验和试验。
1.3责任:除已指定之外,品质主管负责以下程序中的所有运作。
1.4最终检验流程图:(见下页)1.5最终检验员(FQC)须具备资格条件:1.5.1 高中、中专或以上文化程度;1.5.2 熟悉产品装配工艺及客户品质要求;1.5.3 受过3C及有关成品检验培训并考核合格。
1.6FQC职责和权限:1.6.1 按《FQC检验规范流程》对成品进行检验;1.6.2 记录和保存检验数据;1.6.3 对检验过程中发生批量性品质问题,按《不合格品评审程序》处理;1.6.4 对质量记录做统计分析,用以指导生产,稳定和提高产品质量;1.6.5 受理客户投诉,调查不合格原因,跟踪纠正和预防措施,及时答复客户改善情况。
1.7FQC运作程序:1.7.1 FQC检验员按《作业指导书》对产品进行检验;1.7.2 FQC员每2小时对生产线上的材料、工位操作及治具确认一次,并填写《2小时生产部品确认表》,由品质主管审核;1.7.3 FQC按客户品质要求对产品进行抽样检验:对符合要求的产品,填写《FQC报告》并在现品票上贴上“合格”标签,标明机种、检验日期及检验员签名;1.7.4 FQC抽样不良缺陷超过客户要求AQL标准,即产品质量不符合客户要求时,填写《FQC报告》并在每栈板的现品票上贴上“不合格”标签,标明机种、不良原因、不良数量、检验日期及检验员签名,同时填写《重流通知单》,写明不良原因及数量,经品质主管审核后,并经公司领导确认后,发给生产;1.7.5 制造接到《重流通知单》后,安排时间重流,PQC重点对不良项目进行全检,检验结果记录在《重流通知单》上;1.7.6 FQC对重流过的成品重新进行抽检,合格后进仓;如重流二次均不符客户要求,则应组织有关人员进行评审,执行《不合格批评审程序》;1.7.7 FQC巡拉发现生产线员工违反《作业指导书》操作或引起品质异常时,必须通知生产部,要求制生产主管即时纠正员工操作,同时发出《纠正行动通知单》给制造,限其在8小时内将问题的原因及改善措施书面回复FQC,FQC不定期跟踪问题改善情况并将跟进结果记录于《品质问题跟踪表》中;1.7.8 在仓库存货交货前,仓库成品管理员应核查成品储存期,如超期,应书面通知FQC,FQC检验员将采取以下行动。
FQC全检检验作业指导书

MI(轻微缺陷):不影响产品性能,但影响产品外观,如色差、杂质、积油、残缺、烂牙、毛刺、碰划伤不良等。
4. 职责:
全检QC负责对成品包装前玻璃表面处理过程中所有产品实施外观全检作业,对上工序流出或表面处理过程造成不良进行剔除,将全检过程中发现品质问题及时反馈上工序,并要求生产性人员(作业员、组长、领班、技术员等)作出改善并跟踪问题的改善效果。全检QC将检验结果真实记录在《FQC检验记录表》上。
QC组长(品质技术员)以上人员负责掌握各客户产品的品质标准,对QC反映的品质问题进行处理,对产品的加工方法进行可行性判定。
5. 作业内容:
准备工作:
“6S”工作。
操作步骤:
戴上作业手套拿起流水线上已表面处理干净的成品逐个进行全面外观/尺寸检查,检查的内容包括:产品不良、(如:磕伤、划伤、毛刺、加工不良等)。
在全检时发现不良品后用白板笔或不良品打上标识摆放于不良品放置区进行标识隔离,并将重点不良立即和低级不良错误(如加工尺寸不符、严重磕碰伤等...)反馈相关人员进行改善。
不良品数量及其缺陷要记录在《FQC检验记录表》上,以便组长统计分析。
全检过程中,当遇到自己不能判断的缺陷时应立即问组长避免误判。
工作完成后清理不良品,对不能返工的报废品进行分类,记录数据交组长签字并整理、清洁工作岗位。
注意事项:
在产品表面处理过程中,应注意产品的放置及操作方法,轻拿轻放避免造成人为不良品的产生。
FQC全检检验作业指导书
1目的
规范包装前的全检作业,将产品按合格品,返修品,报废品区分,隔离,标示。对产品表面处理和包装过程进行有效的品质控制,杜绝不良品流出,确保产品品质能够满足客户需求;
FQC检验作业规范 (1)解析

主要缺陷:印字不清晰(或无印字) 、模糊、变形 2.方法[目视] 严重缺陷:表面是否破胶、露铜
主要缺陷:a.线身刮伤、污脏、起粒 b.印字内容错误 c.色差、杂色、混色、错色、不对板 次要缺陷:扎伤线、扎痕印深
C.注塑: 方法[目视]
主要缺陷:a.PVC颜料与线材统一 b.注塑类型 c.是否有冲胶、缺料、毛边等不良现象 3.规格: 方法[卷尺] 主要缺陷:总长 4.包装: 方法[目视] 主要缺陷:a.包装方式是否与生产计划单及作业指 导书规定相符
4.适用产品:V7类
1.检验项目 【外观】 2.合格判定基准:依生产计划单及作业指导书规定为基 准 A.水晶头: 方法[目视] 严重缺陷:水晶头卡位断裂或变形 主要缺点: a.水晶头线口为弧形或方口形 b.水晶头未压到位或压太深 B.线材:1.方法[擦试目视] 主要缺陷:印字不清晰(或无印字) 、模糊、变形 2.方法[目视] 严重缺陷:表面是否破胶、露铜
主要缺陷:a.线身刮伤、污脏、起粒 b.印字内容无“BELKIN”字样 c.色差、杂色、混色、错色、不对板 次要缺陷:扎伤线、扎痕印深
C.注塑: 方法[目视] 主要缺陷:a.PVC颜料与线材统一 b.注塑类型 c.是否有冲胶、缺料、毛边等不良现象 3.规格: 方法[卷尺] 主要缺陷:总长 4.包装: 方法[目视]
FQC成品检验作业规范
1.目 的:为确保成品出货质量,并降低检查费用而执行抽样检验,并使成 品检验有依可循。 2.定 义: 2.1.成品检验是指判定成品是否已完成客户订单之要求规范。 2.2.抽样检验是指送样批中,抽取若干样试验之,并将其结果与规范比较,以判断该批应 合收或拒收。 2.3.成品之抽检批量,经出货之数量为一批量,当FQC收到每批送检的成品时,按送检 的批量数进行抽检,所抽检出的成品检查数中,除各类产品的成品总长尺寸按每批 抽5PCS记录3PCS外,其它项目按抽查的成品数量进行全检,对所有抽检的成品, FQC记录时,尺寸项目记录3PCS数据,如有超出尺寸公差的,则必须记录超出公 差尺寸的数据,其它检验项目记录“OK”或“合格”字样即可,环保要求方面,依 客户环保要求及SGS核对,记录“OK”或“合格”字样即可。 2.4.每月初,品管部将对上个月FQC检验出的不良品项目,用《检查表》及《柏拉图》 形式统计出,并对柏拉图中前三项不良率最高项提交给责任单位作原因分析及改善 对策。 3.抽样标准 依据“GB/T2828.1-2003 正常检验一次抽样方案,一般Ⅱ级水平检验。
FQC入库出货检验规范

操作文件文件编号WI-FC-02 版次 1.0机密等级一般页次1/4FQC/OQC入库出货检验规范制定日期2014-11-17实施日期2014-11-17版本修订日期修订页次修订内容修订者1.02014-11-17 4 新版制作Wayne核准/日期审核/日期制定/日期Wayne 2014-11-17操作文件文件编号WI-FC-02 版次 1.0机密等级一般页次2/4FQC/OQC入库出货检验规范制定日期2014-11-17 实施日期2014-11-171.目的检查生产的成品是否符合规定要求,确保不合格品不得入库,防止不合格品流到顾客处。
2.适用范围适用于本公司入库前的成品及库存成品的检验。
3.定义FQC:Final Quality Control 最终成品检验OQC:Outgoing Quality Control 出货成品检验4.职责4.1 FQC负责成品入库前的检验;4.2品保主管/工程师负责对不合格品的分析并协助纠正预防措施的提出和验证。
5 内容5.1成品包装前,FQC应执行首件检查,检查项目包括各种标贴是否正确,成品实物与产品名称是否一致,及外观、尺寸、性能及包装材料等应满足相关《FQC/OQC检验规范》要求,并将检验结果记录在《出货检验记录表》中。
5.2若首件检查不合格,FQC应立即通知生产部并开出品质异常联络单,同时立即停止包装作业,待查明不良原因并消除原因后方能继续作业,不合格处理具体依《不合格品及纠正管理流程》执行。
5.3首件检查合格后,生产部开始执行包装作业。
FQC将巡检结果记录在《出货检验记录表》上,发生不合格时依《不合格品及纠正管理流程》执行。
操作文件文件编号WI-FC-02 版次 1.0机密等级一般页次3/4FQC/OQC入库出货检验规范制定日期2014-11-17 实施日期2014-11-175.4入库前生产部开出《成品入库单》交FQC检验,FQC依《BOM》图纸对该批成品进行抽样检验,检验结果记录在《FQC检验报告》上,若检验结果合格,FQC应在在入库单上签字,反之若检验不合格,FQC开出《品质异常联络单》交责任部门主管要求返工,返工结果应记录在《成品检验日报表内》,生产返工OK后,FQC执行再次成品检验,直至合格为止.5.5若同一不良品质问题多次发生且无改善动机及效果时,FQC应开出《品质异常联络单》给责任部门,并要求在限定时间内完成拟订及实施纠正及预防措施,FQC应跟踪纠正与预防措施的时限性与有效性。
FQC和OQC检验规范
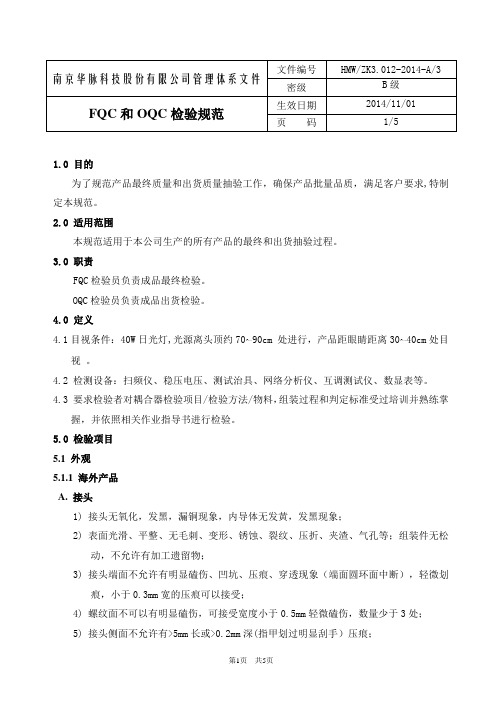
1.0 目的为了规范产品最终质量和出货质量抽验工作,确保产品批量品质,满足客户要求,特制定本规范。
2.0 适用范围本规范适用于本公司生产的所有产品的最终和出货抽验过程。
3.0 职责FQC检验员负责成品最终检验。
OQC检验员负责成品出货检验。
4.0 定义4.1目视条件:40W日光灯,光源离头顶约70~90cm 处进行,产品距眼睛距离30~40cm处目视。
4.2 检测设备:扫频仪、稳压电压、测试治具、网络分析仪、互调测试仪、数显表等。
4.3 要求检验者对耦合器检验项目/检验方法/物料,组装过程和判定标准受过培训并熟练掌握,并依照相关作业指导书进行检验。
5.0 检验项目5.1 外观5.1.1 海外产品A. 接头1)接头无氧化,发黑,漏铜现象,内导体无发黄,发黑现象;2)表面光滑、平整、无毛刺、变形、锈蚀、裂纹、压折、夹渣、气孔等;组装件无松动,不允许有加工遗留物;3)接头端面不允许有明显磕伤、凹坑、压痕、穿透现象(端面圆环面中断),轻微划痕,小于0.3mm宽的压痕可以接受;4)螺纹面不可以有明显磕伤,可接受宽度小于0.5mm轻微磕伤,数量少于3处;5)接头侧面不允许有>5mm长或>0.2mm深(指甲划过明显刮手)压痕;B. 腔体外观1)喷涂层均匀、完整,同批产品的光泽、纹理一致,颜色符合图纸要求;2)腔体表面不允许有碰伤露底,露白现象;3)腔体表面不允许有露底划痕,无感划痕可接受,单面不可以超过3处,长度不超过20mm,喷漆前有感划痕单面不可以超过1处,长度不超过9mm,宽度不超过1mm;4)腔体表面单面可以接受1处凹坑,长条状长度不超过6mm,宽度不超过2mm,块状面积不可超过9mm2,棱角不能有锯齿状凹坑,个别凹坑不会导致掉漆允许接受;5)腔体表面不允许有麻点群,影响光泽度;6)腔体表面有个别凸点但不会导致掉漆现象的可接受,单面不可以超过2个凸点,单个面积不可超过5mm2;7)腔体表面不允许有气泡,挂漆现象;8)腔体表面有个别杂质但不会导致掉漆现象的可接受,单面不可以超过1条,长度不超过9mm,宽度不超过1mm;9)腔体不允许有因抛光导致直角边缘的严重缺损,盖板接触侧小于<3*3mm的缺损可以接受,非盖板接触侧<5*5mm的缺损可以允收;5.1.2 国内产品A. 接头标准与出口产品一致B. 腔体外观1)检测面积按照每100mm*100mm(100cm²)区域进行划分,以下所述单位面积的缺陷数均以此为准。
一次性使用医用口罩IQC、IPQC、FQC及OQC检验规范

一次性使用医用口罩IQC、IPQC、FQC及OQC检验规范IQC进料检验规范1.目的和范围1.1目的规范一次性使用医用口罩的原材料进货检验操作,确保原材料符合规定要求,保证产品质量。
1.2范围适用于本公司一次性使用医用口罩产品的原材料进货检验。
2.工作程序2.1原材料进厂后应放原材料仓库待检区,由仓库填写请检单,送交质量部,质量部收到请检单后派员到现场进行检验或取样。
2.2质量部收集产品质量证明书。
3检验项目、要求、方法及抽样方案3.1熔喷布3.1.1外观质量3.1.2理化性能3.1.3徼生物3.2鼻夹3.3口罩带3.4包装袋IPQC过程检验1.目的规范一次性使用医用口罩产品生产过程中的检验项目、检验方法与检具、抽样方案及判定准则的要求,确保产品在生产过程中的质量要求。
2.范围适用于本公司一次性使用医用口罩生产过程检验。
3.检验项目、要求、检验方法、检验规则见下表FQC及OQC成品检验1.目的规范一次性使用医用口罩产品岀厂前检验项目、检验内容与要求、检验方法、抽样方案判定准则及检验记录的要求,桷保出厂成品符合注册标准要求。
2.范围适用于本公司一次性使用医用口罩成品出厂前检验。
3.检验依据3.1一次性使用医用口罩技术要求4.检测项目、质量要求、检验方法检测包括出厂检验和型式检验。
出厂检验项目项目:4.1外观、4.2结构与尺寸、4.3鼻夹、4.4口罩带、4.7微生物指标。
其中4.7为委托第三方检测项目,每批原材料送检一次。
型式检验应为产品标准的全性能检验。
4.1外观4.1.1口罩外观应整洁、形状完好,表面不得有破损、污渍。
4.1.2口罩的超声波复合应均匀、平直、牢固、无明显皱折。
4.1.3口罩超声波复合处粘合应牢固。
检验方法:随机抽取3个样品进行试验。
目视检查,结果应符合要求。
4.2结构与尺寸口罩佩戴好后,应能罩住佩戴者的口、鼻至下颌。
应符合表1的规定尺寸,最大偏差应不超过士5%表1口罩规格型号和基本尺寸单位:mm检验方法:随机抽取3个样品进行试验。
FQC检验规范830

厦门汉纳森汽车电子有限公司FQC检验规范HNSWI- QQ-065实施日期: 2012年月日受控状态:分发号:654321序号更改日期更改章节号更改审批单号更改人版本批准审核编制1 目的为确保公司产品质量符合合约规定之要求,防止不合格品流入客户,让客户满意。
2 范围适用于本公司成品入库前的检验活动。
3 职责3.1外协厂商管理人员负责对产成品的过程标识及通知检验。
3.2 质量管理人员负责产成品质量的检验、记录、判定、标识,报主管确认。
3.3 质量管理负责人依产品质量标准,对检验结果之核准。
4 检验指导书依照已经发布的检验指导书操作。
5 判定方法为使产品缺点的严重性做出明确的区分,以使检验人员能根据不同的缺点做出准确而迅速的判断。
5.1硬件(特性)/软件问题一般为重缺点;5.2结构产品特性不能实现或是对产品品位有大影响的判为重缺点,(如部件坏等),品位有影响,但不引起顾客投诉的判轻缺点;5.3包装未按指示包装,影响顾客使用或对产品造成损伤的判为重缺点(如漏装/错装/装箱方式错误);5.4可靠性问题一般为重缺点;6 成品检验成品检验是产成品在入库前,质管部所做的检验。
6.1为了确保产成品的品质,确认目前生产制程的作业及检查方法是否正确,以抽样检查的方法来确保不良品不会流出;6.2对生产的最终产品,以批为区分,实施抽样检查,对检查结果进行判定,并对产品进行合格与否的标识,不合格时要发行[不良/委托检讨书]给责任部门对策;6.3异常确认:当发生工程不良率高或出货检查及其他部门发现品质不安定等问题时,质管部经理认为必要时,出货检查要对已完成品进行相关确认,确认台数及项目由经理决定;6.4再检确认:对返工、再检及品质问题再确认时,出货检查要进行确认;确认方法:产品有拆开时作一般检查;产品未拆开时针对再检项目检查。
有开箱再检时要确认包装是否正确;确认数量:依生产再检数量的不同进行抽样,如下表:工程再检数量质管检验数量有拆台未拆台1000台以上10台20台100~1000台5台10台100台以下2台5台7 记录标识质管部应将检验结果记录于[出货(入库)检验报告]上,作出初步判定,报质管部主管确认。
- 1、下载文档前请自行甄别文档内容的完整性,平台不提供额外的编辑、内容补充、找答案等附加服务。
- 2、"仅部分预览"的文档,不可在线预览部分如存在完整性等问题,可反馈申请退款(可完整预览的文档不适用该条件!)。
- 3、如文档侵犯您的权益,请联系客服反馈,我们会尽快为您处理(人工客服工作时间:9:00-18:30)。
FQC检验规范流程
1. 最终检验程序(FQC)
1.1 目的:对产品出厂前检验/试验,确保产品质量满足客户要求。
1.2范围:产品检验和试验。
1.3责任:除已指定之外,品质主管负责以下程序中的所有运作。
1.4最终检验流程图:(见下页)
1.5最终检验员(FQC)须具备资格条件:
1.5.1 高中、中专或以上文化程度;
1.5.2 熟悉产品装配工艺及客户品质要求;
1.5.3 受过3C及有关成品检验培训并考核合格。
1.6FQC职责和权限:
1.6.1 按《FQC检验规范流程》对成品进行检验;
1.6.2 记录和保存检验数据;
1.6.3 对检验过程中发生批量性品质问题,按《不合格品评审程序》处理;
1.6.4 对质量记录做统计分析,用以指导生产,稳定和提高产品质量;
1.6.5 受理客户投诉,调查不合格原因,跟踪纠正和预防措施,及时答复客户改善情况。
1.7FQC运作程序:
1.7.1 FQC检验员按《作业指导书》对产品进行检验;
1.7.2 FQC员每2小时对生产线上的材料、工位操作及治具确认一次,并填写《2小时生产部品确认表》,由
品质主管审核;
1.7.3 FQC按客户品质要求对产品进行抽样检验:对符合要求的产品,填写《FQC报告》并在现品票上贴上
“合格”标签,标明机种、检验日期及检验员签名;
1.7.4 FQC抽样不良缺陷超过客户要求AQL标准,即产品质量不符合客户要求时,填写《FQC报告》并在
每栈板的现品票上贴上“不合格”标签,标明机种、不良原因、不良数量、检验日期及检验员签名,同
时填写《重流通知单》,写明不良原因及数量,经品质主管审核后,并经公司领导确认后,发给生产;
1.7.5 制造接到《重流通知单》后,安排时间重流,PQC重点对不良项目进行全检,检验结果记录在《重流
通知单》上;
1.7.6 FQC对重流过的成品重新进行抽检,合格后进仓;如重流二次均不符客户要求,则应组织有关人员进
行评审,执行《不合格批评审程序》;
1.7.7 FQC巡拉发现生产线员工违反《作业指导书》操作或引起品质异常时,必须通知生产部,要求制生产
主管即时纠正员工操作,同时发出《纠正行动通知单》给制造,限其在8小时内将问题的原因及改善措施书面回复FQC,FQC不定期跟踪问题改善情况并将跟进结果记录于《品质问题跟踪表》中;
1.7.8 在仓库存货交货前,仓库成品管理员应核查成品储存期,如超期,应书面通知FQC,FQC检验员将采
取以下行动。
a. 存货超过3个月,FQC需随机抽样10%检查;
b. 存货超过6个月,FQC需随机抽样20%检查;
1.7.9 超储存期成品经FQC再次检验确认合格后,应重新贴“合格”标签,注明机种、抽检日期和检验员签
名。
FQC检验流程图。