最新刀柄部分的结构图例
液压刀柄资料2017.12.12

浅谈刀柄的种类与特点伟泽作百家号06-2904:50刀柄作为连接机床和刃具的重要“桥梁”,关系着加工精度、刃具寿命、加工效率等的优劣,最终影响加工质量与加工成本。
因此,如何正确选择一把合适的刀柄就显得非常重要。
由于各种加工的要求不尽相同,与之相呼应是不同夹紧方式的刀柄。
在这里,对各种刀柄的普遍特点做简单介绍。
(一)弹簧刀柄工作原理:利用有锥度的弹簧夹套在轴向移动(锁紧)的过程中逐渐收缩,实现夹紧刃具。
适用范围:钻头、铰刀、精加工立铣刀等特点:夹持范围大;通用性好;精度高(仅限部分厂家)。
关键点:弹簧夹套是否能够完美均匀收缩是决定跳动精度的关键因素之一;轴承式螺母可大幅降低锁紧时对夹套的扭力。
弹簧夹套在4D处跳动精度级别代表20μm以内普通级普通ER夹套10μm以内精密级精密ER夹套5μm以内超精密少数厂家3μm以内顶级高精度NBC夹套(二)液压刀柄工作原理:利用液压使刀柄内径收缩实现夹紧刃具。
适用范围:立铣刀、硬质合金钻头、金刚石铰刀等的高精度加工。
特点:操作方便,只需1根T型扳手即可拧紧,属于所有刀柄中夹持方式最简单的;精度稳定,扭紧力不直接作用于夹持部分,即使新入职的操作人员也可以稳定装夹;完全防水、防尘;防干涉性能好,市面上部分细长型液压刀柄,已可媲美热缩刀柄的防干涉性能。
(三)热缩刀柄工作原理:利用刀柄和刃具的热膨胀系数之差,实现夹紧刃具。
适用范围:干涉条件要求较高的加工场合。
特点:防干涉性好;夹持范围小,只能夹持一个尺寸的刃具;初期跳动精度较好(随着加热次数的增加下降较快);需专门的加热冷却装置,安全性差,对操作人员要求高。
(四)强力铣刀柄工作原理:通过螺母压迫刀柄本体收缩,实现夹持刃具。
适用范围:立铣刀的重切削。
特点:高刚性;夹持力强,是所有夹持类刀柄中夹持力最大的。
防干涉性不好;(最近也有厂家推出了螺母外径仅为32mm的强力铣刀柄)跳动精度一般,普遍在0.02mm以下,但也有厂家做到了5~10μm。
高速刀柄及其工具系统的结构与性能

图 3 KM 刀柄的结构
KM 工具系统具有高刚度、高精度、快速装夹和 维护简 单等优点。试验证 实 KM 刀柄的动 刚度比 HSK 系统更高, 不过由于 KM 刀柄锥面上开有对称 的两个供夹紧用的圆弧凹槽, 通常需要较大的夹紧 力才能使其正常工作。
3. 4 NC5 刀柄及其工具系统 NC5 工具系统是日本株式会社日研工作所开发 的( 如图 4 所示) , 该刀柄采用 1: 10 锥度的实心短锥 结构, 锥柄外部套装有开轴向槽的锥套, 锥套和法兰 端面之间装有碟形弹簧。锥套在碟形弹簧的作用下 轴向移动, 实现和主轴锥面的配合, 同时也实现了端 面定位。
1 tan2b
接传递) cos( q+ 2 6385)
3. 5 ( 详 见 参考文献 [ 3] )
拉钉
后靠 传递
拉 锥
紧 套
1(拉 钉 接传递)
直
tana
冷却 形式
外部冷却 可以内冷
可以内冷 可以内冷 可以内冷
锥体 形式
实心锥体 空心薄壁
实 心 锥 体 实心 锥 体
空心薄壁 ( 带冷却孔 ( 带内部冷
* 十五 国家科技攻关项目( 项目编号: 2001BA205) 江苏省自然科学基金资助项目( 项目编号: BK2004027)
收稿日期: 2008 年 1 月
图 1 高速加工时 BT 刀柄工作示意图
3 高速刀柄及其工具系统
3. 1 高速加工对工具系统的基本要求 高速加工工具系统的基本功能是保证刀具在机 床中的准确定位, 同时传递加工所需的运动和动力。 为了实现其基本功能, 工具系统要具有高动平衡精
2008 年第 42 卷 10
31
高速刀柄及其工具系统的结构与性能*
薛宏丽1 王贵成1 刘 钢2
加工中心刀柄 (2)

加工中心刀柄介绍随着加工中心在零件机械加工中的运用越来越普遍,加工中心刀柄的使用也越来越多。
但是,刀柄的种类有很多,我们必须选择精度足够的、经济的、使用方便的刀柄用于零件的加工,这就要求我们对刀柄有全面的了解。
刀柄,用于连接加工中心主轴与切削刃具的装备。
这就如同人用手拿着笔写字,人是机床,笔是切削刃具,手就是刀柄。
如图1所示,由于刀柄是与主轴连接、与刀具连接,所以刀柄的分类也主要有两种分类。
按与加工中心主轴的连接方式分类:分为7:24锥度刀柄和1:10锥度刀柄;按刀柄与刀具的连接方式分类:分为侧固式刀柄、弹簧夹套式刀柄、液压刀柄、热涨刀柄等。
图1一、刀柄与主轴连接方式加工中心的主轴和刀柄之间通常采用锥度配合。
锥度配合特点是具有定心性好、间隙或过盈可以方便地调整等。
图2锥度C=(D-d)/L,如图2。
因此刀柄按锥度也分为7:24和1:10两大类。
(一)、7:24锥度刀柄定位原理及特点1、7:24锥度刀柄定位原理图3 图47:24锥度刀柄通过长锥面限制X、Y方向的移动及转动,Z方向的移动5个自由度,通过拉力F与锥面产生的摩擦力限制Z轴的转动(如图3、图4所示),从而实现刀柄的完全定位,此定位方式刀柄端面与主轴端面有间隙,如BT系列刀柄。
2、7:24锥度刀柄的特点优点:1)、不自锁,可以实现快速装卸刀具;2)、刀柄的锥体在拉杆轴向拉力的作用下,紧紧地与主轴的内锥面接触。
3)、7:24锥度的刀柄在制造时只要将锥角加工到高精度即可保证连接的精度,所以成本相应比较低,而且使用可靠。
缺点:1)、单独的锥面定位。
7:24锥度刀柄连接锥度较大,锥柄较长,导致a、换刀行程长,换刀时间慢;b、刀柄重量增加,机床损耗功率增加。
2)、在高速旋转时,由于离心力的作用,主轴前端锥孔会发生膨胀,膨胀量的大小随着旋转半径与转速的增大而增大,见图5,但是与之配合的7:24锥度刀柄由于是实心的所以膨胀量较小。
(如:在离主轴中心r=0.02m处,一质量为m=100g的质点,在机床主轴转速为n=12000r/min时,所受到的离心力为F=3158.3N,即为315.83Kg的力。
车刀图解要点

一般对切削刃上关键部位点的后角进行验算,避免过小。
第十二页,共21页。
成形车刀的轮廓设计
工件的轮廓是指工件轴向剖面上的形状和尺寸,包 括宽度、深度、圆弧半径等。
成形车刀轮廓在与后刀面垂直的剖面内表示,对圆体 成形车刀而言,就是它的轴向剖面。
➢轮廓设计的必要性
当 rf0、f 0时 ,刀具廓形等,于 但工 这件 种廓 成形意 车 ;义 刀 当 rf0、f0时 ,必须按工件修 的正 廓计 形算 深成 度 深 形 。 度 车刀
刀具廓形深度公差取工件相应公差的1/2~1/3;
刀具廓形宽度公差/8;
位置公差 棱体成形车刀后刀面对燕尾槽安装基面的平行度和两侧面对
燕尾槽安装基面的垂直度在100长度内均不超过0.02mm; 圆体成形车刀切削刃对内孔轴线的圆跳动公差为0.02~0.03mm,
✓断屑槽形式与宽度
目的:卷屑、断屑 形式:16种,按结构分为开口式封闭式两大类
开口式:(A、Y、H、K、J等)断屑槽一边或两边开通,前角大,刃口锋利, 切削力小,刀尖强度低,断屑范围窄。
封闭式:(V、M、W、G)断屑槽不开通,左、右切削刃角度相等, 可以通用,刀尖强度好,适应性广。
第八页,共21页。
第十三页,共21页。
➢轮廓设计的准备工作 1、理论上工件廓形各点均需修正计算,以便求出刀具廓形 上的对应点。通常选取工件形状与尺寸变化的各转折点作为 组成点,进行修正计算。
2、计算组成点尺寸 按平均值标注 3、根据工件材料性质和刀具类型,选取所需前、后角
4、圆体成形车刀,尚须确定外径D1
实际生产中,已知apmax,可参考资料选取相关尺寸。
可转位刀片的选择
可转位刀片的型号由代表一定意义的字母和数字代号 按一定顺序排列组成,共有十个号位。
数控加工工艺——第五章 数控机床刀具系统

第四节 数控机床刀具系统
一、数控刀具刀柄
刀柄是机床主轴和刀具之间的连接工具,是数控机床 工具系统的重要组成部分。
1.(JE)和锥柄(JT) 两种形式,如图5-20所示。加工中心上一般刀柄均采用 7∶24圆锥工具柄。
目前在我国多采用国际标准ISO7388-1983,中国标 准GB10944-1989,日本标准MAS404-1982,美国标 准ANSI/ASMB5.50-1985。
第四节 数控机床刀具系统
图5-20 刀柄结构示意图
第四节 数控机床刀具系统
2.常用数控刀具刀柄及拉钉结构
我国数控刀柄结构(GB10944-1989)如图 5-21所示。相应的拉钉国际标准GB10945-89包 括两种形式:A型用于不带钢球的拉紧装置,其 结构如图5-22(a)所示;B型用于带钢球的拉紧装 置,其结构如图5-22(b)所示。
2.镗铣类工具系统
镗铣类工具系统一般由与机床主轴连接的锥柄、延伸 部分的连杆和工作部分的刀具组成。镗铣类工具系统又分 整体式工具系统和模块式工具系统两大类。
第四节 数控机床刀具系统
(1)整体式工具系统。如图5-25所示为镗铣 类整体式工具系统。
图5-25 整体式工具系统的组成
第四节 数控机床刀具系统
XXB·X/X—X
其中,第1位X和第2位X所代表的内容与主柄模块前两 位表示的意义相同;第3位B表示此模块为中间模块;第4 位X表示靠近主柄模块一端的模块外径;第5位X表示靠近 工作模块一端的模块外径;第6位X表示中间模块的接长 长度L2值。
第四节 数控机床刀具系统
工作模块(工作头):
XXC (D)·X—XX—X
第四节数控机床刀具系统第四节数控机床刀具系统图521中国标准刀柄结构第四节数控机床刀具系统第四节数控机床刀具系统图522中国标准刀柄拉钉结构第四节数控机床刀具系统第四节数控机床刀具系统图523日本标准刀柄及拉钉结构第四节数控机床刀具系统图524美国标准刀柄及拉钉结构3
刀柄种类规格

加工中心的主轴锥孔通常分为两大类,即锥度为7:24的通用系统和1:10的HSK真空系统。
7:24锥度的通用刀柄锥度为7:24的通用刀柄通常有五种标准和规格,即NT(传统型)、DIN 69871(德国标准)、IS0 7388/1 (国际标准)、MAS BT(日本标准)以及ANSI/ASME(美国标准)。
NT型刀柄德国标准为DIN 2080,是在传统型机床上通过拉杆将刀柄拉紧,国内也称为ST;其它四种刀柄均是在加工中心上通过刀柄尾部的拉钉将刀柄拉紧。
目前国内使用最多的是DIN 69871型(即JT)和MAS BT 型两种刀柄。
DIN 69871型的刀柄可以安装在DIN 69871型和ANSI/ASME主轴锥孔的机床上, IS0 7388/1型的刀柄可以安装在DIN 69871型、IS0 7388/1 和ANSI/ASME主轴锥孔的机床上,所以就通用性而言,IS0 7388/1型的刀柄是最好的。
(1)DIN 2080型(简称 NT或ST)DIN 2080是德国标准,即国际标准ISO 2583 ,是我们通常所说NT型刀柄,不能用机床的机械手装刀而用手动装刀。
(2) DIN 69871 型(简称JT、 DIN、DAT或DV)DIN 69871 型分两种,即DIN 69871 A/AD型和 DIN 69871 B型,前者是中心内冷,后者是法兰盘内冷,其它尺寸相同。
(3) ISO 7388/1 型(简称 IV或IT)其刀柄安装尺寸与DIN 69871 型没有区别,但由于ISO 7388/1 型刀柄的D4值小于DIN 69871 型刀柄的D4值,所以将ISO 7388/1型刀柄安装在DIN 69871型锥孔的机床上是没有问题的,但将DIN 69871 型刀柄安装在ISO 7388/1型机床上则有可能会发生干涉。
(4) MAS BT 型(简称 BT)BT型是日本标准,安装尺寸与 DIN 69871、IS0 7388/1 及ANSI 完全不同,不能换用。
最新刀柄部分的结构图例

Taper:1/10 Angle: 2°51 47
4
4
刀柄系统 – 机床主轴的接口形式
Capto®接口
20000-40000转/分 钟的高速度
车刀和回转刀具 共用的主轴接口 形式
5
5
刀柄系统 – 机床主轴的接口形式
Capto®接口
+/- 0.002mm
6
6
刀柄系统 – 夹紧方式
• 利用差动螺钉和一 对锯齿形夹爪将刀 柄/刀具夹紧。
• 中心拉钉夹紧。
7
7
刀柄系统 – 刀具的接口形式
8
8
刀柄系统 – 刀具的接口形式
9
9
刀柄系统 – 刀具夹持
三爪夹头
10
10
刀柄系统 – 刀具夹持
侧压夹头
11
11
刀柄系统 – 组成
12
12
刀柄系统 – 模块化刀具
Modular
Solid
Total: 4+2+30+10 = 46 items
山特维克可乐满 大中华区效率中心
金属切削基础及刀具应用
--主轴接口形式
DIN69871-A/B ISO7388-1
MAS BT403
CAT -V
YAMAZAKI
2
DIN 2080
2
DIN 2079
刀柄系统 – 机床主轴的接口形式
BBT 接口
传统7:24接口
3
3
刀柄系统 – 机床主轴的接口形式
弹簧夹套 Runout 0.01-0.03mm
15
15
刀柄系统 – 刀具夹持
液压夹头CoroGrip
F
高速刀柄简介
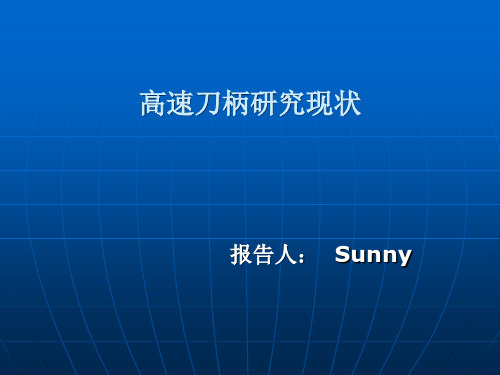
报告人: Sunny
目录
1.引言 2.各型刀柄 2.1 传统刀柄 2.2 新型刀柄 3.致谢
1. 引
言
在高速主轴的设计中,目前对刀柄和主轴
连接较成功的设计主要有两种:一种是为了降低
成本,仍然采用7:24锥度而进行改进的刀兵结
构如美国的WSU系列刀柄,日本的Big-Plus刀
柄等。另一种就是彻底改变7:24锥度标准采用
替代型结构,如德国的HKS系列,美国的KM系
列刀柄等。这些设计都各具特色但也存在一些问 题。
2. 各型刀柄
2.1 传统刀柄
2.1.1 BT工具系统
BT工具系统(7:24),常规机床广泛 采用的实心长刀柄,工作时仅靠锥面定位。 优点:结构简单,使用便利,成本低 缺点:不能用于高速加工
2.1.2 BIG-PLUS工具系统
HSK
2.2.2 KM工具系统
KM(1:10)空心短锥刀柄,锥面和端面双面 定位。 优点:双面定位,高速性能好,允许较大过盈量 缺点:与传统主轴兼容问题,大过盈量导致主轴 膨胀恶化,缩短轴承寿命
2.2.3 CAPTO工具系统
CAPTO(1:20),刀柄呈锥形三角体结构, 锥面和端面双面定位。 优点:无滑动的扭矩传递,动平衡性能好,位置 精度高 缺点:三角体加工困难,成本高
2.3 其他工具系统
a. H.F.C工具系统(日本)
b. SHOW D-F-C工具系统(日本) c. NC5刀柄(日本)
国外刀柄性能研究
在新型工具系统的性能研究方面,通用汽 车公司的Ihab M.Hanna、John S.Agapiou和David A.Stephenson利用 abaqus软件建立了HSK A-63型刀柄的有 限元模型,系统分析了锥面接触间隙和应 力分布以及不同过盈下弯矩载荷与接触刚 度的关系;分别讨论了外加载荷、夹紧力、 离心力对刀柄接触应力的影响规律,为了 解HSK工具系统接口性能提供了依据。
- 1、下载文档前请自行甄别文档内容的完整性,平台不提供额外的编辑、内容补充、找答案等附加服务。
- 2、"仅部分预览"的文档,不可在线预览部分如存在完整性等问题,可反馈申请退款(可完整预览的文档不适用该条件!)。
- 3、如文档侵犯您的权益,请联系客服反馈,我们会尽快为您处理(人工客服工作时间:9:00-18:30)。
13
13
Total 480 items
刀柄系统 – 刀具夹持
液压夹头CoroGrip
14
14
几种夹持方式测量径跳比
——长径比为3的验棒头部径跳
CoroGrip液压夹头 Runout 0.003-0.006mm
Hydro-Grip 精密夹头 Runout 0.003 - 0.006mm
Weldon/Whistle Notch 夹柄 Runout 0.01 - 0.03mm
山特维克可乐满 大中华区效率中心
金属切削基础及刀具应用
---刀柄系统
/1
1
刀柄系统 – 机床主轴接口形式
DIN69871-A/B ISO7388-1
MAS BT403
CAT -V
YAMAZAKI
2
DIN 2080
2
DIN 2079
刀柄系统 – 机床主轴的接口形式
BBT 接口
传统7:24接口
3
3
刀柄系统 – 机床主轴的接口形式
HSK接口
Taper:1/10 Angle: 2°51 47
4
4
刀柄系统 – 机床主轴的接口形式
Capto®接口
20000-40000转/分 钟的高速度
车刀和回转刀具 共用的主轴接口 形式
5
5
刀柄系统 – 机床主轴的接口形式
Capto®接口
+/- 0.002mm
6
6
刀柄系统 – 夹紧方式
• 利用差动螺钉和一 对锯齿形夹爪将刀 柄/刀具夹紧。
• 中心拉钉夹紧。
7
7
刀柄系统 – 刀具的接口形式
8
8
刀柄系统 – 刀具的接口形式
9
9
刀柄系统 – 刀具夹持
三爪夹头
10
10
刀柄系统 – 刀具夹持
侧压夹头
11
11
刀柄系统 – 组成
12
12
刀柄系统 – 模块化刀具
Modular
Solid
Total: 4+2+30+10 = 46 items
弹簧夹套 Runout 0.01-0.03mm
15
15
刀柄系统 – 刀具夹持
液压夹头CoroGrip
F
16
16
刀柄系统 – 刀具夹持
可调式刀柄
17
17
刀柄系统 – 组装工具
•用于装配和拆卸主 刀柄的装卸台 391.200
•模块化刀具的组装 工具
18
18