隧道窑余热锅炉技术
余热锅炉说明

窑炉的余热利用1、余热来源煤矸石多孔砖烧成温度最高可达1030℃,经过高温焙烧段后进入冷却段,砖体温度仍可达到900℃,此时多孔砖已烧结,但晶型转化尚未完成,所以冷却段需要一个较长的范围来满足产品生产的物化要求。
在热值适中、干燥和余热合理、焙烧操作正确的烧制过程中,冷却带从20#车位就开始了,温度可以保证在900℃左右。
进入冷却带的多孔砖带有大量热量,这部分热量通过热辐射的方式向窑顶、窑墙和窑车传递,致使窑体温度偏高,需要采取保温措施保护窑顶吊板及窑墙不受损失。
因为焙烧窑生产是连续性的,所以在冷却段每个位置的环境温度也是相对稳定,此时的热源洁净无烟尘,这就为余热利用提供了稳定的洁净热源。
2余热利用现状目前,煤矸石烧结多孔砖隧道窑余热利用已经在设计过程中得到广泛考虑并使用,其利用情况主要有以下几个方面:●干燥砖坯每条隧道式焙烧窑配套设计一条干燥室,用于干燥成型好的砖坯。
干燥热源取自焙烧窑冷却段的余热,热气体洁净无尘。
热源可使成型后湿砖坯进行烘烤,含水率由13%左右降至4%左右,以便使砖坯进入焙烧窑后易于燃烧。
干燥室废气经排潮风机排空。
这是余热的首先主要利用。
●厂内职工洗浴与采暖每条焙烧窑加设两台直径1400mm的换热器,取窑内热气与冷水进行热交换,经过换热器的热气重新回入抽气主管道,凉水变为热水进入热水管道送入浴室(一年四季)。
●职工饮用水换热器附近加茶水炉,热源采用窑内余热,生产热水可用于全厂职工饮用。
●8.2.4工人工作服烘干引抽余热管道一组制作成散热器状,把洗净后的湿工作服烘干,可满足1000余名工人工作服等物品的烘干,减少厂区再购置烘干机。
热水或蒸汽锅炉车间外加设锅炉房,利用窑内余热作为热源,热交换过程采用软化水,交换后得到热水(汽)产量大,温度高,可服务人数增加。
此种余热利用方式技术较先进,采用锅炉设备后热利用效率得到提高,效果明显,经济效益显著,可广泛推广。
目前余热利用方式—采用低压余热锅炉1安装位置的选择鉴于以上余热各种利用方式的利弊关系,必须研究更科学的利用方式,而采用低压余热锅炉应该是今后发展的方向。
隧道窑余热利用分析

符合 烧结 温度 曲线要求 , 要么 采不 到热要 么影响烧 砖 。
3 如何正确 利 用余热
生 产 区和 生活 区供 暖 、 洗 浴用 水 、 溴化 锂 空调 制冷 、 矿 工 工作服 烘 干 、 井 口采 暖 、 矿 区食堂 等 。
用途 , 才能确 定应该采 用 哪一种利 用方式 。 3 . 2 计 算余热 量
余 热利用 , 顾名 思 义是在满 足烧砖 的前提 下 , 对 窑
内多余 的热量进行利用。余热量多少受到很多因素影
响: 原 材料 的发热量 、 易烧 性 、 窑 墙窑顶 的保温性 能 、 窑 车 的密封性 、 抽风 系统 的合理性 等 。中 、 大 断面 的隧道 窑保 温材料要 求 比较严格 , 保温 性能 比较好 , 窑外墙 温 度基 本 为 常温 。窑 车加 工精 度也 比较高 , 密 封性 比较
高 的问题 。
个别企业不作调查研究 , 片面追求余热利用产生 的效 益 , 把 烧砖 的隧道 窑 当成 了锅 炉房 , 烧 出的砖 不是
欠 火 就是 过烧 , 完全 背离 了余 热 利用 的初 衷 。还 有企
业本来原料热值就不高 , 却为了利用余热而掺煤提高
窑 内热量 , 其 行 为令 人 啼笑 皆非 。有 的生产线 余 热采 集 量远远 达不 到系统 运行需 求 , 投 产 即停产 , 空 投几百
安装 余 热发 电 系统后 , 正常 工作 条 件下 每小 时 发 电量
不低 于 1 0 0 k WA。
首先要清楚开发余热干什么用 , 目前余热 主要用 途有 : 本 厂 的采 暖 、 洗浴 , 周 同 的生产 、 生 活 区供热 , 溴 化锂 空调制冷 , 食堂 用热 , 发 电等 。只有 明确 了余热 的
隧道窑余热利用方法

隧道窑余热利用方法
“隧道窑余热利用方法”是指利用隧道窑生产过程中产生的废热进行
再利用的方法。
这种方法既可以提高工厂的能源利用率,又可以减少
环境污染,受到了越来越多企业的欢迎。
下面就详细介绍一下隧道窑
余热利用的具体方法。
第一步:收集废热
隧道窑废热的收集一般是在窑的分解炉和头炉之间进行,这里需要设
置一个热交换器,将窑内高温的尾气传导到热交换器中,释放出的热
量被吸收,并传递给空气或水。
通过这种方式,废热就被成功地收集
到了一起。
第二步:通过蒸汽发电利用废热
利用废热进行蒸汽发电是其中非常重要的一种利用方式。
可以将收集
到的废热中的热量通过传热器传递给水,使水蒸发,产生蒸汽,并驱
动涡轮机产生电能。
通过这种方式发电产生的电力可以提供给工厂自用,也可以通过连接到电网上来获得一定的收益。
第三步:余热直接供暖
除了进行电力发电,隧道窑余热还可以通过直接供暖的方式进行利用。
由于余热温度较高,可以通过管道将其输送到生产场所或者员工休息
室等区域,为工厂内部带来一定的温暖。
第四步:生产热水
隧道窑生产中产生的热量还可以用来加热水,制造出热水供应给厂区内的生产、员工休息区域等需要的场所。
可以利用余热产生的热水进行加热,这种方式既可以提高工厂的能源利用率,还可以减少环境污染。
总之,“隧道窑余热利用方法”是一种非常重要的能源利用方式,能够提高工厂的能源利用率,达到节约能源、减少污染的目的。
通过以上四个步骤,我们可以成功地将利用隧道窑废热进行能源创造和环保循环利用。
隧道窑余热锅炉技术
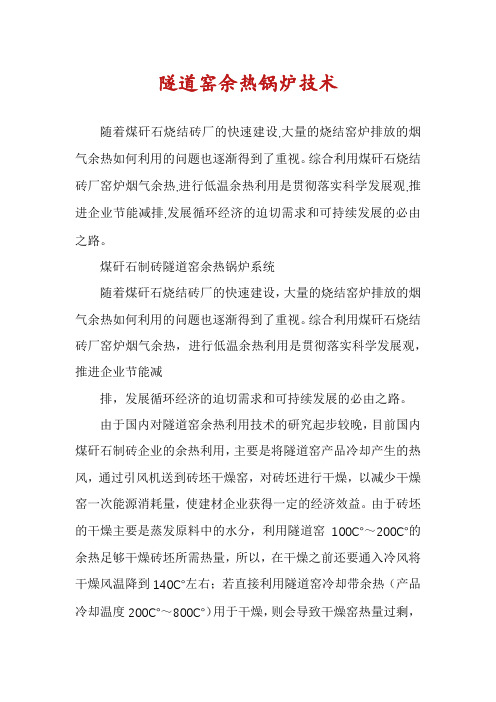
隧道窑余热锅炉技术随着煤矸石烧结砖厂的快速建设,大量的烧结窑炉排放的烟气余热如何利用的问题也逐渐得到了重视。
综合利用煤矸石烧结砖厂窑炉烟气余热,进行低温余热利用是贯彻落实科学发展观,推进企业节能减排,发展循环经济的迫切需求和可持续发展的必由之路。
煤矸石制砖隧道窑余热锅炉系统随着煤矸石烧结砖厂的快速建设,大量的烧结窑炉排放的烟气余热如何利用的问题也逐渐得到了重视。
综合利用煤矸石烧结砖厂窑炉烟气余热,进行低温余热利用是贯彻落实科学发展观,推进企业节能减排,发展循环经济的迫切需求和可持续发展的必由之路。
由于国内对隧道窑余热利用技术的研究起步较晚,目前国内煤矸石制砖企业的余热利用,主要是将隧道窑产品冷却产生的热风,通过引风机送到砖坯干燥窑,对砖坯进行干燥,以减少干燥窑一次能源消耗量,使建材企业获得一定的经济效益。
由于砖坯的干燥主要是蒸发原料中的水分,利用隧道窑100℃~200℃的余热足够干燥砖坯所需热量,所以,在干燥之前还要通入冷风将干燥风温降到140℃左右;若直接利用隧道窑冷却带余热(产品冷却温度200℃~800℃)用于干燥,则会导致干燥窑热量过剩,不仅影响制砖质量,同时能源损失量大,切大大地降低余热的利用价值。
2 隧道窑余热利用锅炉系统建造内容在保证煤矸石制砖窑炉烧结砖工艺的前提下,充分开发利用多余的窑炉烟气热量,是煤矸石砖厂余热锅炉开发与应用研究项目的重点。
其核心内容就是应用当前先进的低温余热锅炉技术,通过项目前期对现场相关参数的测试,将烧结窑炉排放的烟气余热,进行有效收集通过低温余热锅炉转化为中低压蒸汽,在保证隧道窑正常焙烧制砖的前提下,最大限度的收集转化利用窑炉余热,将蒸汽送往企业生产、生活场所,用于驱动设备做功(发电)及矿区职工洗浴、家属区和办公楼的集中供暖,使煤矸石热量得到充分的利用。
具体建设内容有:2.1 制砖隧道窑预热带及冷却带烟道的改造施工主要有隧道窑预热带和冷却带主烟道和分烟道的改造施工、阀门的制作加工、烟道内部的防腐施工以及仪表的安装等工作。
科技成果——烧结砖隧道窑辐射换热式余热利用技术

科技成果——烧结砖隧道窑辐射换热式余热利用技术适用范围建材行业烧结砖瓦隧道窑生产线行业现状目前隧道窑生产线消耗的一次能源(煤),除窑体散热、砖坯水分蒸发、烧结等必须消耗的能量外,约40%-45%的能量是随排烟热损失和产品冷却而浪费。
在这些浪费的热量(简称余热)中,采用余热干燥砖坯的方式,可利用余热的15%,另有25%-30%左右的余热还没有得到充分利用,采用制砖隧道窑辐射换热式余热利用技术,废弃的余热被用于发电或供汽。
砖瓦企业每生产一万块(折标)的用电量平均为350-500kWh,采用隧道窑余热利用(发电)技术后,每生产一万匹标砖可以下降到100kWh以下,节约二次能源;采用隧道窑余热产生蒸汽供热,每生产一万匹标砖可节约标煤390-500kg;降低企业的生产成本,减少二氧化碳气体排放。
目前该技术可实现节能量2万tce/a,减排约5万tCO2/a。
成果简介1、技术原理将隧道窑950-200℃砖坯余热通过辐射换热式余热锅炉产生2.45MPa、400℃蒸汽,余热锅炉利用后的200℃以下的低温烟气余热再用于砖坯干燥,在不影响原生产工艺、不增加燃料消耗和不影响砖坯质量的前提下,实现隧道窑余热的梯级利用。
产生的蒸汽直接用于生产、生活或推动汽轮机发电。
2、关键技术(1)隧道式窑炉余热发电装置技术;(2)隧道式窑炉余热锅炉;(3)超内燃烧结砖隧道窑余热锅炉;(4)满足隧道窑生产工艺需要的分段换热技术。
3、工艺流程烧结砖隧道窑辐射换热式余热利用技术流程图主要技术指标1、隧道窑余热利用率:>20%;2、每万匹标砖产汽量:4-5t蒸汽(参数2.45MPa、400℃);3、每万匹标砖发电量:680-860kW(凝汽式汽轮发电机组);4、单位节能量:供汽时每万标砖390-500kgce,发电时每万标砖210-300kgce。
技术水平项目技术已于2011年5月由农业部和联合国工业发展组织(UNIDO)组织工信部、国家发改委、中国砖瓦工业协会和西安墙体材料设计研究院等单位现场鉴定、验收。
高温隧道炉余热回收利用技术改进方案

高温隧道炉余热回收利用技术改进方案环境与化学工程学院过程装备与控制工程一、前言节能是我国经济和社会发展的一项长远战略方针,也是建设发展和谐社会的必要条件。
为推动全社会开展节能降耗,缓解能源紧张,建立节约型社会,促进社会可持续发展,实现和谐社会的目标,就要从日常生活、生产工作入手,加强能源节约建设。
高温隧道炉余热回收利用,就是秉承这一宗旨,把生产过程中产生的剩余能量进行回收利用,达到了“节约能源,造福社会”的目标。
在稀土加工中, 消耗尽量少的能源, 生产出更多的合格产品, 是高温隧道炉热工性能、技术水平的重要标志, 也是高温隧道炉设计工作者长期以来为之奋斗的目标。
无论引进国外先进窑炉,还是发展新型窑炉, 其目的都是为了改善窑炉的热工性能, 降低烧成能耗, 提高炉的热效率。
为了提高产品的产量和质量, 首先就要使高温隧道炉的热工性能符合产品的烧成工艺。
对高温隧道炉, 要求烧成( 温度、压力、气氛) 制度要稳定,温度要均匀, 燃料燃烧要完全, 热能的综合利用率要高等, 从而实现低耗、优质、高产的目的。
本文通过对高温隧道炉综合与分析, 探讨了降低能耗, 提高炉热效率的潜力的一些方法。
二现况分析在稀土生产过程中, 消耗尽量少的能源, 生产出更多的合格产品, 是衡量窑炉热工性能、技术水平的重要标志, 也是高温隧道炉设计工作者长期以来为之奋斗的目标。
无论引进国外先进窑炉,还是发展新型窑炉, 其目的都是为了改善高温隧道炉的热工性能, 降低烧成能耗, 提高炉的热效率。
为了提高稀土产品的产量和质量, 首先就要使高温隧道炉的热工性能符合产品的生产工艺。
对连续式的高温隧道炉—隧道, 要求温度、压力、气氛条件要稳定, 断面温度要均匀, 燃料燃烧要完全, 热能的综合利用率要高等, 从而达到快速烧成, 实现低耗、优质、高产的目的。
从以上数据表明,生产工艺中产品仅消耗5%的热量,95%的热量被散失,能源浪费严重。
可主要表现在几个方面:1)炉内热交换慢,生产周期长。
隧道窑辐射换热式余热利用(发电)技术在砖瓦行业的应用前景
成 , 合 了 两 大行 业 的 l 、 程 、 全 、 量 标 准 , 过 多 个 T 程项 目的 运 行 经 验 总结 而 成 目前 , 综 丁艺 流 安 质 经 四 川 围 立 能 源 科 技 有 限 公 司 已制 定 了企 业标 准 Q 7 5 8 2 — 隧道 窑余 热 利 用 一 电》 技 术 成 熟 , 1 /6 o 4 o x《 发 , 对 大 中 型砖 瓦 企业 的 隧道 窑 余 热 利 用 ( 电 、 暖 、 冷 、 燥 ) 较 好 的投 资 效 益 , 会 效 益 明 显 , 术 发 供 制 干 有 社 技 应 用 符 合 国家 相关 产 业 政 策 . 当前 我 国重 点 支持 的 “ 是 十大 重 点 节 能 T程 ” 一 . 之 . 【 键词 】 隧 道窑 ; 热 ; 机容 量 ; 能 ; 关 余 装 节 制砖
产生 1 7 a饱和蒸 汽 . 过膨胀 螺杆 机发 电。 . MP 2 通
( 1 北 中节 能新 型材 料有 限公 司安装 辐射 换 热 4河
2 1. 01 7墙材革新与建筑节能 21
新 型 墙 材
Ne W alMa e il w 24 MP 、0  ̄ x 热蒸 汽 , 产 . 5 a4 0C'  ̄ _ 通过 凝 汽
0
新 型 墙 材
Ne W a I t r l w lMa e i s a
隧道 窑烧结 制砖 工 艺 以产 量 大 、 能耗低 、 自动化 程度 高 、 量质量 稳 定 、 炉烧成 参数 可控 等特 产 窑
点, 已成为当今国际上最先进的制砖工艺之_ 。随着国家淘 汰 2 以 下轮窑生产线等政策和劳动力 4门 成本 的上升 , 未来将 有更 多的小砖 厂被 淘汰, 而代 之的是 大 中型 现代化 隧道 窑制砖 生产 线 。而 大力 取
隧道窑余热锅炉的设计结构合理及热效率
隧道窑余热锅炉的设计结构合理及热效率
隧道窑余热锅炉的设计结构合理及高热效率主要得益于以下因素:
1. 结构:该锅炉的结构设计紧凑、合理,能够化地利用空间,使传热面积不浪费,锅炉体积小,重量轻,安装方便。
同时,其受热面布置方式能有效应对烟气流动特性,确保烟气能够充分接触受热面,传热效率高。
炉内设置的多个烟气转弯处,使烟气能够均匀传热,避免局部过热现象。
2. 受热面:隧道窑余热锅炉的受热面较大,能够充分吸收高温烟气的热量。
同时,烟气-水换热充分,不会出现受热面堵塞现象,确保了锅炉的热效率。
3. 保温:锅炉的保温性能良好,能够减少热量散失,从而提高锅炉的热效率。
4. 运行环境:在隧道窑的运行过程中,窑炉产生的废气温度较高,热量利用价值高,为余热锅炉的设计提供了良好的工况条件。
总的来说,隧道窑余热锅炉的设计充分利用了隧道窑的高温废气,结构设计紧凑、合理,受热面布置及保温性能良好,都大大提高了余热锅炉的热效率。
此外,科学合理的结构设计、较高的换热效率以及良好的保温性能等因素也进一步保障了余热锅炉的热效率。
在实际使用中,该锅炉的热效率通常能达到85%以上。
隧道窑余热综合利用的工艺技术要求
科技 部联合 发 布新修 订 的 《 国节 能技 术政 策 大纲 》 中 (0 6 ,要求 在工业 节 能领 域推 广 生产 过程 余热 、 20 ) 余 压 、 能利 用技术 时 。 余 必须 遵循 “ 级利 用 、 梯 高质 高用 ” 的原则 。“ 优先 把高 品位 余热余 能用 于做功或发 电 , 低 温 余热 用 于空 气 、 料 及 物料 的预 热 。 外 热 回收用 燃 炉
1 烧 结 砖 生 产 中 隧 道 窑 余 热 的 综 合 利 用
生 产过 程 中隧道 窑 的余热 利用 是一 项 国家 积极鼓 励 、 大力 推 广 的节能 技术 .充 分利 用企 业现 有余 热 资源 . 把生 产 和节 能有机 地结 合起 来 . 为企 业 的长期 生 存奠
为推 动 节 能技 术 进 步 . 高 能 源利 用效 率 . 进 提 促 节 约能源 和优化 用 能结 构 ,国家 发展 和改革 委 员会 、
工作
道 窑冷 却段 安装余 热 锅炉换 热 装置 . 直接 利 用高 品位 余 热 (0 3 0℃~9 0o 的产 品 冷却 余热 ) 5 C 产生 的蒸 汽或 转 化为 价值更 高 的电力 能 源的技 术 。而将 品位 较 低 、 余 热锅 炉难 以利 用 的余 热 (0 10℃ ~3 0o 再用 于砖 0 C) 坯预热、 干燥 。 实现余 热 的梯 级利 用 , 降低 企业 的生 产
研究 设 计 院承 担 . 同时进行 了煤 矸石 制砖 行业 余 热 并
发 电 的可 行 性 评 估 .调 查 煤 矸石 制 砖 企 业 的企 业 生
产、 能源 利用 等情 况 根 据技术 数 据判定 该 企业 否
材厂 的隧道 窑余 热利 用率 较低 . 将低 品位 的余 热用 只 于砖 坯 干燥 和加 热 生 活用 水 、 暖及 洗 浴 等 . 用效 采 利 率 很低 . 而将 大 量高 品位 的余热 都 浪费掉 了 利 用 高 品位 的余 热发 电既符合 国家环保 节 能的要 求 . 又会 使 企业 的生 产成 本大 大地 降低 . 动砖 瓦企 业朝 着 资源 推 节约 型 、 境 友好 型 的方 向发 展 , 企 业 发 展步 入 良 环 使
砖瓦行业隧道窑余热发电
砖瓦行业煤矸石隧道窑余热发电发布日期:2011-05-24浏览次数:186导言:近年来,一方面,“限电停产”在一些省市和地区渐成常态,拉闸限电现象的加剧致使一些工厂陷入危机。
而对于今年,有关专家认为有可能是自2004年大缺电以来最困难的一年,目前煤炭涨价与电网建设滞后加剧“电荒困局”;另一方面,余热发电技术在水泥等建材行业发展迅猛,余热发电所产生的效益对企业的影响日益明显。
余热发电在砖瓦行业的应用发展虽然相对缓慢,但目前也取得了不错的成绩。
资料显示,“隧道窑余热发电装置”技术对煤矸石等原料热值较高的砖厂尤其适用,可有效地换取高温带多余的热量,对砖瓦企业提高产量有明显效果。
由于各企业的生产情况千差万别,若选用余热全部用于发电的方案,可满足砖厂70~100%的用电量。
煤矸石与隧道窑我国每年煤矸石的排放量相当于当年煤炭产量的10%-15%,煤矸石年产量已达到3亿多吨。
截止到2010年底,我国煤炭系统共有煤矸石砖厂近2000家。
除现已投产的煤矸石生产线以外,四川、山西、山东、河北等地还将陆续新建一批煤矸石空心砖生产线,新建的制砖厂规模比较大,在6000万块-16000万块之间,普遍采用了隧道窑生产技术。
隧道窑烧结制砖工艺以产量大、能耗低、自动化程度高、产量质量稳定、窑炉烧成参数可控等特点,已成为当今国际上最先进的制砖工艺之一。
世界各国对隧道窑余热利用技术的研究和应用主要是把少量余热用于砖坯干燥、加热空气用于助燃或加热成80℃左右热水供砖瓦企业内部冬季供暖和职工洗浴等用途,余热利用效率较低。
余热发电大背景最近十多年,政府加大了淘汰落后产能的力度,在钢铁、电力、冶金、化工、化肥、水泥等行业大规模的推广先进工艺和技术,淘汰中小规模的生产企业,使这些行业的能耗或经济指标达到或领先国际先进水平。
2010年,政府又把砖瓦行业淘汰落后产能工作提上了日程,将淘汰中小型轮窑等能耗高、自动化程度低的烧结砖生产企业,在全国范围内推广大中型隧道窑制砖生产技术,推动砖瓦行业的节能减排工作,提高砖瓦行业的技术水平。
- 1、下载文档前请自行甄别文档内容的完整性,平台不提供额外的编辑、内容补充、找答案等附加服务。
- 2、"仅部分预览"的文档,不可在线预览部分如存在完整性等问题,可反馈申请退款(可完整预览的文档不适用该条件!)。
- 3、如文档侵犯您的权益,请联系客服反馈,我们会尽快为您处理(人工客服工作时间:9:00-18:30)。
煤矸石制砖隧道窑余热锅炉系统
随着煤矸石烧结砖厂的快速建设,大量的烧结窑炉排放的烟气余热如何利用的问题也逐渐得到了重视。
综合利用煤矸石烧结砖厂窑炉烟气余热,进行低温余热利用是贯彻落实科学发展观,推进企业节能减排,发展循环经济的迫切需求和可持续发展的必由之路。
由于国内对隧道窑余热利用技术的研究起步较晚,目前国内煤矸石制砖企业的余热利用,主要是将隧道窑产品冷却产生的热风,通过引风机送到砖坯干燥窑,对砖坯进行干燥,以减少干燥窑一次能源消耗量,使建材企业获得一定的经济效益。
由于砖坯的干燥主要是蒸发原料中的水分,利用隧道窑100℃~200℃的余热足够干燥砖坯所需热量,所以,在干燥之前还要通入冷风将干燥风温降到140℃左右;若直接利用隧道窑冷却带余热(产品冷却温度200℃~800℃)用于干燥,则会导致干燥窑热量过剩,不仅影响制砖质量,同时能源损失量大,切大大地降低余热的利用价值。
2 隧道窑余热利用锅炉系统建造内容
在保证煤矸石制砖窑炉烧结砖工艺的前提下,充分开发利用多余的窑炉烟气热量,是煤矸石砖厂余热锅炉开发与应用研究项目的重点。
其核心内容就是应用当前先进的低温余热锅炉技术,通过项目前期对现场相关参数的测试,将烧结窑炉排放的烟气余热,进行有效收集通过低温余热锅炉转化为中低压蒸汽,在保证隧道窑正常焙烧制砖的前提下,最大限度的收集转化利用窑炉余热,将蒸汽送往企业生产、生活场所,用于驱动设备做功(发电)及矿区职工洗浴、家属区和办公楼的集中供暖,使煤矸石热量得到充分的
利用。
具体建设内容有:
2.1 制砖隧道窑预热带及冷却带烟道的改造施工
主要有隧道窑预热带和冷却带主烟道和分烟道的改造施工、阀门的制作加工、烟道内部的防腐施工
以及仪表的安装等工作。
2.2余热锅炉的研制和安装
通过项目前期对现场相关数据的调研测试,以及周围用热情况综合考虑,本着余热最大利用的原则,结合制砖工艺,对余热锅炉进行设计、制造及现场安装施工。
2.3 水处理设备的安装
通过项目前期对锅炉供水水质的化验分析,合理设计余热锅炉系统的水处理系统,使供水水质达到
国家相关标准要求。
2.4余热锅炉受热面防腐处理
通过项目前期对制砖原料的分析和隧道窑烟气成分的测试分析,对其SO2对锅炉系统的腐蚀情况进行标准评估,并选择相应的防腐材料用于锅炉受热面,延长锅炉使用寿命。
2.5 给水自动控制和检测系统设备安装
通过自动化设备及仪表的安装,提高给水系统自动化水平,避免锅炉缺水干锅事故的发生,通过监测系统自动化水平的提高可对相关参数进行实时监测分析,降低运行人员劳动强度(见图1)。
3 隧道窑余热利用锅炉系统技术要点
研究并调整窑炉制砖运行工艺,在不影响窑炉制砖工艺的情况下最大限度的将窑炉余热集中收集,通过余热锅炉转化成中低压蒸汽,直接应用于生产、生活用汽等。
其中研究并调整窑炉制砖运行的主要工
艺如下:
3.1 烟气回收系统
煤矸石多孔砖生产过程中,砖坯的烧成是烧结工艺中最为关键的一道工序,如果进入窑炉的冷却风量过大,烟气带走的热量较多,则会造成烧成后的制品出现严重的欠烧、过火和裂纹等质量问题,直接影响产品的合格率;而如果进入窑炉的冷却风量过小,烟气带走的热量也相应减少,造成煤矸石制砖过程中余热利用不充分,热量被白白排放,而且烧成后的制品表面温度过高,冷却时间长,卸砖困难,影响生产
产量。
3.2 砖坯干燥系统
砖坯干燥室煤矸石制砖烧成工序的前期准备阶段,其热源来自焙烧窑预热带或冷却带余热所形成的热烟气,一般会比较合适的温度是105℃~120℃,如果风温过高则会容易引起砖坯表面细微裂纹,当砖坯进入焙烧窑烧成时,裂纹将会继续扩大,从而造成制品裂纹。
我们通过对上述生产工艺的研究及调整,并对烟气相关参数进行在线检测,从而研究出了在不影响制砖工艺的情况下,达到余热利用最大化的生产模式,并将余热锅炉排出的烟气继续用于砖坯的干燥及物料的预热,形成能源的梯度利用,这也是该项目突出亮点。
4 高效余热锅炉
4.1 科学设计锅炉结构形式
在锅炉结构形式上,根据煤矸石制砖隧道窑焙烧窑烟气的性质、烟气入口位置、布置形式及清灰方式,确定选用多回程式自然循环型低温余热锅炉。
鉴于煤矸石制砖隧道焙烧窑炉烟气含有大量的SO2,但烟尘含量不高,烟气量和烟气温度波动较大,因此辐射冷却室宜采用II型——用扁钢焊接而成的翘片管结构(见图2),这样可防止炉内SO2的渗出或外面空气漏入,从而防止了低温硫腐蚀。
4.2合理确定锅炉的主要运行参数
针对煤矸石含硫特点,该项目设计余热锅炉蒸汽温度在250℃以上,余热锅炉炉膛内温度高于烟气露点温度,锅炉钢制炉管烟硫腐蚀非常轻微,锅炉大修周期长,大修费用低。
4.3 采取适宜的锅炉清灰、除尘方式
煤矸石砖厂焙烧窑烟气中烟尘含量虽然不高,但也必须考虑锅炉积灰问题。
因此,我们在高温区灰斗的四周应用水冷对流壁遮盖,使烟气与水冷对流壁管直接接触,并使烟尘在灰斗中得到进一步冷却,形成不粘结性积灰,另外,我们还采用较为先进的燃气电子振动式吹灰方式,经过现场应用清灰效果明显。
4.4 锅炉防腐
根据现场检测烟气的含硫情况,在余热锅炉相应部件采用耐腐蚀合金钢制造,或喷涂耐高温防腐材料,大大降低余热锅炉的检修率,延长锅炉使用寿命。
4.5 锅炉的自动化控制
采用较为先进的仪表设备,提高余热锅炉的自动化水平,锅炉控制柜设计有自动上水和高低水位报警功能,提醒司炉工向锅炉上水,有效控制锅炉缺水干锅事故的发生。
5 余热利用系统技术创新点
由于是利用煤矸石制砖隧道窑余热生产蒸汽,所以,该余热锅炉技术项目与其他蒸汽生产工艺相比
具有以下创新亮点:
5.1 余热锅炉设计合理,热效率高
该余热锅炉用于煤矸石制砖隧道窑烟气管道上,与传统锅炉相比,无机械不完全燃烧损失和化学不完全燃烧损失,锅炉设计合理,场内组装,保温性能良好,锅炉热效率较高,运行后经地方质量监督部门
检测,该余热锅炉热效率达到了58%。
5.2 系统设计合理,烟气余热回收率高
该余热锅炉系统是为煤矸石制砖隧道窑专门设计,符合煤矸石制砖的工艺要求,在锅炉设计和使用方面,由于充分利用制砖工艺中的烟气热量,与传统燃煤锅炉相比,无燃烧系统,仅有辐射换热装置,减少了磨损,延长了锅炉使用寿命。
余热锅炉所排放的烟气能够满足砖坯干燥的最低需求,达到了余热最大利用的目的,经测算,在余热锅炉系统应用前后,烟气余热回收率提高了60%。
5.3 体现了“梯级利用、高质高用”的余热利用
该项目较好的将制砖工艺与余热锅炉技术巧妙融合,在不影响制砖工艺的前提下,遵循生产过程中产生余热、余压、余能利用“梯级利用,高质高用”的原则,优先吧高热量余热余能用于做功、供暖,低热
量余热用于制砖物料的预热、干燥窑砖坯的烘干。
5.4 项目建设周期短、投资少,投资回收期短,经济效益明显
由于该余热锅炉系统有效地利用了煤矸石制砖所产生的余热,省去了锅炉的燃烧系统,不仅不产生粉尘污染和化学污染,而且由于不需要消耗一次能源,带来了直接的经济效益。
由于制砖工艺中热源稳定,并充分利用制砖设备原来的引风系统,不需要配备鼓风机和引风机,节约项目建设安装及运行费用,减少余热锅炉系统维护工作量。
据测算,仅电费一项每年就可节约30余万元。
若以某砖厂一台3t余热锅炉替代一台3t燃煤锅炉计算,每年减少向大气排放锅炉烟尘3.75t、SO21.42t、炉渣固体废弃物590t,年可节
约燃煤近3000t,价值150万元。
5.5 符合国家“节能减排,保护环境”的产业政策
由于该项目是利用煤矸石制砖隧道窑余热生产蒸汽,投资少,见效快,为企业增加了就业岗位,缓解了社会、企业的就业压力,符合国家产业经济发展政策,经济效益和社会效益显著。
而且该余热锅炉利用项目的开发,为制砖企业创造了稳定、廉价的生产、生活蒸汽供应,为延长企业产业链,促进企业生态
循环经济的发展奠定了良好的基础。