换热器折流板各种型式的讨论
管壳式换热器中折流板的作用
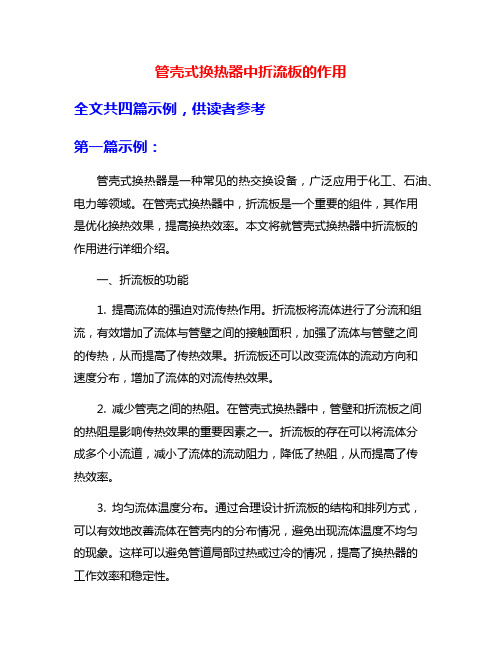
管壳式换热器中折流板的作用全文共四篇示例,供读者参考第一篇示例:管壳式换热器是一种常见的热交换设备,广泛应用于化工、石油、电力等领域。
在管壳式换热器中,折流板是一个重要的组件,其作用是优化换热效果,提高换热效率。
本文将就管壳式换热器中折流板的作用进行详细介绍。
一、折流板的功能1. 提高流体的强迫对流传热作用。
折流板将流体进行了分流和组流,有效增加了流体与管壁之间的接触面积,加强了流体与管壁之间的传热,从而提高了传热效果。
折流板还可以改变流体的流动方向和速度分布,增加了流体的对流传热效果。
2. 减少管壳之间的热阻。
在管壳式换热器中,管壁和折流板之间的热阻是影响传热效果的重要因素之一。
折流板的存在可以将流体分成多个小流道,减小了流体的流动阻力,降低了热阻,从而提高了传热效率。
3. 均匀流体温度分布。
通过合理设计折流板的结构和排列方式,可以有效地改善流体在管壳内的分布情况,避免出现流体温度不均匀的现象。
这样可以避免管道局部过热或过冷的情况,提高了换热器的工作效率和稳定性。
1. 弯曲型折流板。
弯曲型折流板通常采用波纹状或波形状的设计,能够有效地增加传热面积,同时还可以引起流体的湍流运动,增强了传热效果。
2. 梯形折流板。
梯形折流板的结构呈梯形状,能够有效地将流体进行分流和导流,提高了传热效率。
梯形折流板还可以根据需要调整板片的倾角和间距,以适应不同的换热条件。
3. 放置型折流板。
放置型折流板通常安装在换热器的内壳内侧,起到导流和分流的作用,能够有效地提高传热效率。
放置型折流板的结构简单,安装方便,适用于各种规格的换热器。
三、折流板的设计要点1. 考虑流体介质的性质。
在设计折流板时,需要考虑流体的性质,包括流速、温度、压力等因素,以确保折流板的结构能够适应流体的特点,提高传热效率。
2. 合理设计折流板的结构和排列方式。
折流板的结构和排列方式直接影响传热效果,需要根据具体的换热要求和工况条件,合理设计折流板的形状、尺寸和间距,以提高传热效率。
换热器-折流板结构形式

折流板
一、折流板概述
折流板是设置在壳体内与管束垂直的弓形或圆盘-圆环形平板。
安装折流板迫使壳程流体按照规定的路径多次横向穿过管束,既提高了流速又增加了湍流速度,改善了传热效果,在卧式换热器中折流板还可起到支撑管束的作用。
折流板的固定是通过拉杆和定距管来实现的。
二、折流板的分类及结构
常用的折流挡板有单弓形、双弓形、三弓形和盘—圆环形。
三、折流板作用
(1)提高壳程内流体的流速。
(2)加强湍流强度。
(3)提高传热效率。
(4)支撑换热管。
弓形折流板与盘环折流板对管壳式热交换器特性的影响研究

Value Engineering———————————————————————作者简介:胡悦(1991-),女,湖南涟源人,硕士,工程师,研究方向为发动机滑油系统设计。
0引言目前航空发动机上常用的管壳式热交换器属于小型管壳式热交换器[1],在结构设计上主要包括壳侧结构设计和管侧结构设计,例如某型燃油-滑油热交换器、某型燃油-液压油散热器和某型飞机交流发电机燃滑油散热器等,受限于发动机和飞机对热沉的使用,该类热交换器通常使用燃油做为热沉冷却其它介质,鉴于燃油的工作压力较高,同时为了有利于散热性能提高,燃油通常在管内流动,其它介质在壳侧流动,而发动机上燃油流量通常较大(飞行包线内个别低流量点不予讨论),其它介质的流量较小,这就造成管侧Re 数和换热系数较大,而壳侧的Re 数和换热系数较小[2]。
通过计算、仿真和试验等经验总结可知,目前影响该类热交换器性能的主要因素就在于壳侧流动不充分、换热系数小,通过改变折流板结构对壳侧结构设计进行调整,增加该侧的换热系数是提升该类散热器散热性能的有效途径[3]。
弓形折流板是指将折流板切除一定弦高,以一定距离对头布置在壳侧内[4]。
盘环折流板是指将折流板中心切除一定直径圆孔的环式折流板,配合将外环切除一定直径外环的盘式折流板,以一定距离布置在壳侧内[5]。
1技术分析1.1应用分析弓形折流板和盘环折流板管壳式热交换器在管壳式热交换器领域早有应用[6]。
通过改变折流板形状增加壳侧换热系数的方法也较多,例如螺旋折流板、折流棒等,鉴于上述结构在小型密集型散热管布置工艺不成熟(或者说目前发动机和飞机应用较少)本文不予讨论,但是近几年对于盘环式折流板应用较多,例如某型飞机交流发电机燃滑油散热器、某型燃滑油散热器以及最新研制的某型主/辅助燃滑油散热器等,通过计算分析和实际使用总结了一定的经验。
资料文献以及教科书对于盘环式管壳式热交换器均有一定的介绍,但是对其实际使用以及在使用过程中出现的问题和优点未做详细的评述,本文根据实际设计、计算和试验经验,针对两类热交换器进行特性分析。
螺旋折流板管壳式换热器结构特点剖析

【 关键词 】 化工机械 ; 换热器 ; 传热面积 ; ; 能耗 适应性 ; 环经济: 循 节能减排 : 热传递
2 连续与非连续螺旋折流板 . 1 要使 壳程工质形成理想的连续螺旋流动 . 折流板应 该是 一系列 连 在工业生产 中, 换热器 的主要作用是使热量 由温度较高的流体传 续 的螺旋曲面 . 可称之 为连续 型螺旋折 流板 . 其结构类似于常见 的输 递 给温度较低 的流体 . 使流体 温度达到工艺 流程规定 的指标 . 以满 足 送 固相介质 的搅龙 过程工 艺条件 的需要 , 也是余热 、 废热 回收利用 的有效装置 。 换热器作 连续螺旋折 流板可使壳程流体形 成相对 连续平稳 的螺旋 流动 . 但 为一种 通用的热工过程设备 在炼油 、 工 、 化 环保 、 发电 、 制冷 、 品 、 食 新 受 螺旋结构的限制 , 壳体中心 区域需要加装 假管 . 其 从而降低 了壳体 能源利用等许多工业部 门中广泛使用 。以石油化工 厂为例 . 换热器 占 空间的利用率 , 换热器紧凑性下降。 此外 . 连续螺旋折流板换热器的加 建厂总投 资的 2%左右 , 0 在全厂化工设备总重量中约 占4 %。鉴于换 0 工 制造 安装也 比较复 杂 .给产品 的进一步 大型化和推广应用带来 困 热器在工业生产 中的重要作用 . 改进典 陛能和提 高其效 率成为节能减 难。 排 的重要途径 , 将产生显著 的社会和经济效益 。 目 应用中的螺旋折流 板换 热器大多采用一 系列法向与换热管 前 轴 向成 一定夹 角的扇形平 面板进 行搭接 . 形成 近似 螺旋面 . 可称之为 1 管壳式换热器综述 非连续螺旋折流板。 相邻两块折流板间会形成一个三角区 . 导致漏 流. 1 横 向流支撑结构 . 1 壳程流体进行的是“ 伪螺旋状流动 最有代表性 的横 向流支撑结构是单 弓形折流板 . 结构简单 . 其 制 22 螺旋角 . 造安 装方便 . 因而 目前应用 最广泛 . 发展最成 熟 , 计资 料也较 为完 设 螺旋角又称折流板倾角 . 连续螺旋折 流板螺旋角 的定义为折流板 备 在单 弓形折流板管壳式换热器 内, 壳程流体经过折 流板的圆缺部 在壳体上形成的螺旋曲线切线与壳体横截面间的夹角 口 。非连续螺旋 分后垂直掠过管束 . 并在折流板的作用下进行“ ” z 字形流 动 . 流体湍流 折流板螺旋角的定义为折流板 法线方 向与换热管轴心的夹角 。 程度强 . 传热效率高 . 但缺点也较明显 : 2 螺旋折流板裁剪方式 - 3 () 1流体反复横 向冲刷换热管束并不断剧烈改变流 动方 向会产生 非连 续螺旋折流板按照裁剪 方式还可 以分 为四分之一椭圆和 四 较大的形体阻力 . 壳程压降往往超出允许值。 分之一扇形两种形式 四分之一椭 圆螺旋折流板的长短边分别 为折流 () 2 在折流板与壳体相连处存在流动死区 , 结垢严重需 经常清理 , 板所在椭 圆的长短轴 . 四分之一扇形螺旋折流板左右对称 。每片椭 圆 停工检修频繁 : 型钢板采用 四分之一椭圆裁剪 方式可 以裁 出四块折流板 , 采用 四分之 ・3流动死 区同时也是传热死 区, () 降低了壳程换 热系数 ; 扇形裁剪方式可以裁出两块 折流板 . 前者材料利用率更高不 留边角 () 4 壳程 流体剧烈 冲刷 换热管束 . 而窗 口区管束无 支撑跨距是 折 料 。 流板间距 的两倍 . 易产生流体诱导振动 . 导致换热管磨损甚 至断裂 , 缩 2 相邻折流板搭接方式 . 4 短 了换热器寿命 相邻 非连续螺旋折流板 之间有外围点接触 的连续 搭接和直边交 1 纵 向流支撑结构 . 2 叉点接触 的交错搭接两种布置方式 采用交错搭接布置可以在其他结 最有代表 性 的纵 向流换热器是 上世 纪 7 年代美 国 P ii 石 油 构参数不变的情况下减小螺距 。 0 hn s P 增加折流板数量。 搭接量 e 的定 义为 : 公司为解 决传统 弓形 折流板支撑结构 中换热管 与折流板的切 割破坏 2 0 % l xl 0 e = 和流体诱导振动而开发的折流杆管壳式换热器 . 其壳程支撑结 构为管 间排布的支撑杆组成的折流栅 。相关研究表 明, 折流杆壳程 支撑结构 式 中:为相邻折流板搭接点到壳体 内壁 的距离 。D 为壳体 内径 。 f 拥有诸多优点 : 连续搭接时可认为搭接量 e 0 = ( ) 先它 的轴 向流动方 式 , 少 了壳程 流体 的滞 流 、 1首 减 回流和 死 交错搭 接后相邻折流板 间除靠 近壳体 中心 的三角区外还会形成 区. 提高了佩克莱常数 P 值 . 了壳程 压降和污垢沉 积; e 减少 个靠近壳体内壁的搭 接区 . 两处漏流均会对壳程流动产生影响 。 ( )折流杆后的卡 门涡街脱落效应在传热管子表 面产 生湍流 , 2 提 25 螺 距 . 高了壳程单位压降下的对流换热系数 ; 连续螺旋折流板一个螺旋 周期在轴 向的长度称为螺距 。 于非连 对 () 3 折流 杆的夹持作用 能够抑制换 热管束 的破坏 性振动 , 使冷 换 续螺旋折流板相邻的两个相 同位 置折流板的轴向间距 称为螺距 。 每个 设备大型化成为可能 。 螺距 内所有螺旋折流板在管板 方向投影拼接为一个整圆。 一个 螺距 内 13 螺旋流支撑结构 . 折 流板 的数量越多 . 壳程流动越 接近连续螺旋流动。 一般来说, 出于加 螺旋流是介于横 向流和纵向流之间的一种壳程流体流 动形 态 . 兼 工方面的考虑 . 一个螺距 内为 2 4块折 流板 。有文献给 出了不 同形式 _ 有横向流和纵 向流的优点 , 可大体概括为换热效果好 、 壳程压 降小 、 管 螺旋折流板换热器螺旋角 口与螺距 B的通用计算公式 : 柬不易结垢以及能防止管束流体诱导振动等。 借助螺旋折流板可实现 日 (一 )D s t ,n 20 ) : 1e r , n a ( I ,≤ t i > 壳程工质的螺旋或近似螺旋流动 螺旋折流板 管壳式换热器 由前捷 克
曲面弓形折流板换热器壳程流体流动与传热
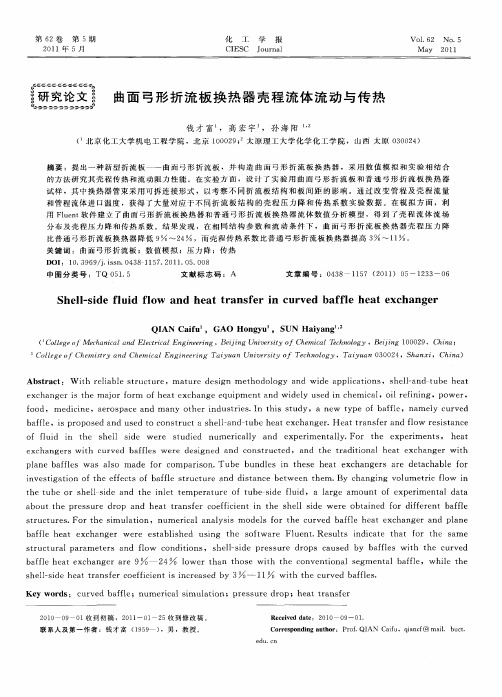
中 图 分 类 号 :TQ O 1 5 5 .
文献 标 志 码 :A
文 章 编 号 :0 3 —1 5 ( 0 1 0 — 1 3 —0 4 8 17 2 1 ) 5 2 3 6
S e lsde f u d fo a e tt a f r i u v d b f l e te c a g r h l- i l i l w nd h a r ns e n c r e a f e h a x h n e
比普 通 弓形 折 流 板 换 热 器 降 低 9 ~ 2 ,而 壳 程 传 热 系 数 比普 通 弓形 折 流 板 换 热 器 提 高 3 ~ 1 。 4 1 关 键 词 :曲 面 弓形 折 流 板 ;数 值 模 拟 ;压 力 降 ;传 热
DOI 1 . 9 9 j is . 4 8 l 5 . 0 1 0 . 0 : 0 3 6 /.s n 0 3 1 7 2 1 . 5 0 8
QI AN a f GAO n y 。 S C iu , Ho g u , UN ia g , Hay n
(C le eo M eh nc la d Elcrc l gn eig,Be igUnv riyo h mia eh oo y,Bejn 0 0 9 C ia olg c a i n etia a En iern i n iest f C e c lTc n lg j iig 1 0 2 , h n ; C le eo e sr n e c giern i u n Un v riy o c n lg olg f Ch mity a d Ch mial En n e i g Ta y a ie st f Teh oo y,Ta y a 3 0 4 h n , Chn ) i u n0 0 2 ,S a xi i a
换热器折流板各型式讨论
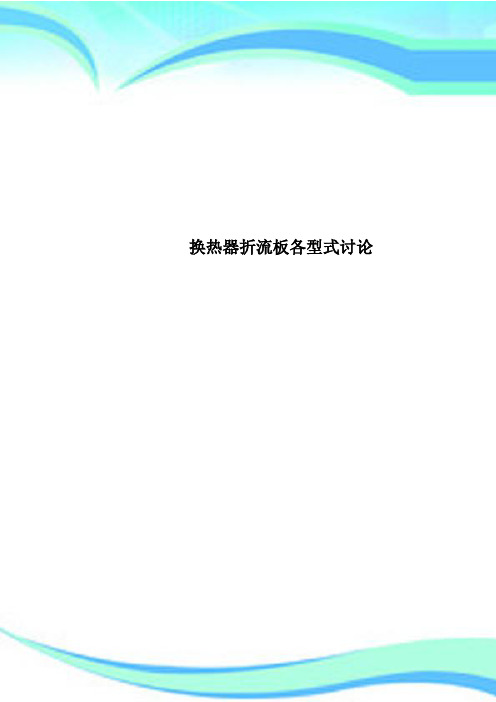
换热器折流板各型式讨论————————————————————————————————作者:————————————————————————————————日期:换热器折流板各种型式的讨论兰州四方容器设备有限责任公司李建仓摘要:本文介绍了换热器所用折流板的几种型式,对其结构及工作形式作了阐述,并将其优点及缺点进行了说明和总结,从而为折流板换热器的设计选型及制造提供了依据和指导。
折流板顾名思义是用来改变流体流向的板,常用于管壳式换热器设计壳程介质流道,根据介质性质和流量以及换热器大小确定折流板的多少。
折流板是列管式换热器中的一个零件可用以起到提高传热系数和支承管束的作用;但由于它结构简单所以往往被设计者所忽视。
现实的情况可以证实到目前为止无论是我国自行设计还是国外引进的设备折流板的结构常是五花八门,其中有些结构既制造复杂又不利于提高传热系数。
其原因在于设计者没有根据具体的传热性质来认真地对它进行分析后再确定具体的结构和尺寸。
本文拟对各种型式折流板的优缺点一一列出并进行对比,提出换热器在什么情况下所适用哪种折流板的一些个人意见和有关同志进行商榷。
折流板有常用折流板和异形折流板之分。
常用折流板主要有弓形和圆盘-圆环折流板,其中弓形又分为单弓形、双弓形和三弓形,如图一:图一异形折流板有:矩形折流板、折流杆型折流板和格栅折流板等,如图二~四:矩形折流板(图二)折流杆换热器示意图(图三)格栅折流板(图四)这些折流板都有各自的优缺点,逐一说明如下;一、弓形折流板。
大部分换热器都采用弓形折流板。
弓形折流板在壳程内的放置形式上下方向排列的形式,用以造成液体剧烈扰动以增大传热系数;左右方向排列的,多数用于卧式换热器,设备中都伴随着有气相的吸收冷凝,以利于冷凝液和气体的流动,当列管是正方形排列时,为了使介质形成湍流以提高换热效果,则采用转角切口。
单弓形折流板主要是为了提高整体的壳程的错流程度,切口的百分数一般为20%~49%;通常为20%~25%,最佳大小为20%,此时单位压降下传热膜系数最高,小于20%(缺口处不布管除外)压降较大;切口超过20%,导致形成流体流速的滞留区,切口过大或过小,都会降低管束的传热性能;为了减小振动,亦可采用缺口处不布管,缺口可减小到15%或者25%左右,其压降只有单弓形的1/3左右。
螺旋折流板换热器传热和流动性能分析

94在化工装置中管壳式换热器型式众多,当壳侧流体流量大且压降限制严格时,通常会采用双弓形折流板形式。
但是双弓形折流板在支撑结构和流动方式上存在诸多缺陷:壳侧流动存在冲刷不充分的流动死区、死区内局部换热系数低,壳侧整体换热不均匀,同时死区容易结垢,威胁换热设备的安全运行[1]。
为了提高壳侧单位压降下传热和避免壳侧由于沉积污垢造成的腐蚀泄漏,工业应用中越来越多的采用螺旋折流板代替壳侧弓形折流板,使壳侧在螺旋折流板引导下形成复杂的螺旋流形态,提高管束间的流速、实现壳体横向截面流体充分混合同时壳侧压降不增加,从而达到强化传热的目的[2]。
工程应用中最多采用的为四片式螺旋折流板结构,见图1,螺旋折流板一个螺旋节距的长度上是由四片式扇形板片按一定的安装倾角上、下、左、右交错排列而成,再用定距管将其定位,使其形成螺旋状[3]。
但是四片式螺旋折流板结构为非连续螺旋折流,中间相邻板片间会出现三角形的漏流区,严重削弱了传热能力[4]。
针对四片式螺旋折流板三角区短路漏流的缺点,中国石化工程建设公司联合抚顺化工机械设备制造有限公司和辽宁石油大学提出了一种新型的六片式螺旋折流板换热器型式,并获得专利授权[5]。
图1 四片式螺旋折流板 图2 六片式螺旋折流板1 模型设置1.1 几何模型三维数值模拟用SolidWorks分别建立尺寸180x1200mm下六片式螺旋折流板、四片式螺旋折流板和双弓折流板结构,设备型式BEM,水平安装,10mm换热管,正方形布管,换热管间距13mm,布108根换热管,换热器所有材质均采用碳钢。
双弓折流板结构采用16块折流板,间距60mm。
六片式螺旋折流板和四片式螺旋折流板都采用10度螺旋角,搭接度42%[6]。
由于管束元件较多,内部结构复杂,本文对换热器的结构进行适当简化如下:(1)认为换热管与折流板、筒体与折流板和管束与壳体都为紧密切合,忽略流体通过缝隙渗螺旋折流板换热器传热和流动性能分析宁静 中国石化工程建设有限公司 北京 100101 摘要:利用CFD分析软件FLUENT,研究10度螺旋角条件下,六片式螺旋折流板换热器和常见四片式螺旋折流板换热器传热和流动特性,并与双弓形折流板换热器进行对比。
四种换热器的结构特点及优缺点

四种换热器的结构特点及优缺点3、四种换热器的结构特点及优缺点。
(1)固定管板式换热器组成:管箱、管板、换热管、壳体、折流板或支撑板、拉杆、定距管等。
结构特点:管板与壳体之间采用焊接连接。
两端管板均固定,可以是单管程或多管箱,管束不可拆,管板可延长兼作法兰。
优点:结构简单,制造方便,在相同管束情况下其壳体内径最小,管程分程较方便。
缺点:壳程无法进行机械清洗,壳程检查困难,壳体与管子之间无温差补偿元件时会产生较大的温差应力,即温差较大时需采用膨胀节或波纹管等补偿元件以减小温差应力。
(2)浮头式换热器组成:管箱、管板、换热管、壳体、折流板或支撑板、拉杆、定距管、钩圈、浮头盖等。
结构特点:一端管板与壳体固定,另一端管板(浮动管板)与壳体之间没有约束,可在壳体内自由浮动。
只能为多管程,布管区域小于固定管板式换热器,管板不能兼作法兰,一般有管束滑道。
优点:不会产生温差应力,浮头可拆分,管束易于抽出或插入,便于检修和清洗。
缺点:结构较复杂,操作时浮头盖的密封情况检查困难。
(3)U形管式换热器组成:管箱、管板、U形换热管、壳体、折流板或支撑板、拉杆、定距管等。
结构特点:只有一个管板和一个管箱,壳体与换热管之间不相连,管束能从壳体中抽出或插入。
只能为多管程,管板不能兼作法兰,一般有管束滑道。
总重轻于固定管板式换热器。
优点:结构简单,造价较低,不会产生温差应力,外层管清洗方便。
缺点:管内清洗因管子成U形而较困难,管束内围换热管的更换较困难,管束的固有频率较低易激起振动。
(4)填料函式换热器组成:管箱、管板、管束、壳体、折流板或支撑板、拉杆、定距管、填料函等。
结构特点:一侧管箱可以滑动,壳体与滑动管箱之间采用填料密封。
管束可抽出,管板不兼作法兰。
优点:填料函结构较浮头简单,检修清洗方便;无温差应力,(具备浮头式换热器的优点,消除了固定管板式换热器的缺点)。
缺点:密封性能较差,不适用于易挥发、易燃、易爆和有毒介质。
- 1、下载文档前请自行甄别文档内容的完整性,平台不提供额外的编辑、内容补充、找答案等附加服务。
- 2、"仅部分预览"的文档,不可在线预览部分如存在完整性等问题,可反馈申请退款(可完整预览的文档不适用该条件!)。
- 3、如文档侵犯您的权益,请联系客服反馈,我们会尽快为您处理(人工客服工作时间:9:00-18:30)。
换热器折流板各种型式的讨论
兰州四方容器设备有限责任公司李建仓
摘要:本文介绍了换热器所用折流板的几种型式,对其结构及工作形式作了阐述,并将其优点及缺点进行了说明和总结,从而为折流板换热器的设计选型及制造提供了依据和指导。
折流板顾名思义是用来改变流体流向的板,常用于管壳式换热器设计壳程介质流道,根据介质性质和流量以及换热器大小确定折流板的多少。
折流板是列管式换热器中的一个零件可用以起到提高传热系数和支承管束的作用;但由于它结构简单所以往往被设计者所忽视。
现实的情况可以证实到目前为止无论是我国自行设计还是国外引进的设备折流板的结构常是五花八门,其中有些结构既制造复杂又不利于提高传热系数。
其原因在于设计者没有根据具体的传热性质来认真地对它进行分析后再确定具体的结构和尺寸。
本文拟对各种型式折流板的优缺点一一列出并进行对比,提出换热器在什么情况下所适用哪种折流板的一些个人意见和有关同志进行商榷。
折流板有常用折流板和异形折流板之分。
常用折流板主要有弓形和圆盘-圆环折流板,其中弓形又分为单弓形、双弓形和三弓形,如图一:
图一
异形折流板有:矩形折流板、折流杆型折流板和格栅折流板等,如图二~四:
矩形折流板(图二)
折流杆换热器示意图(图三)
格栅折流板(图四)
这些折流板都有各自的优缺点,逐一说明如下;
一、弓形折流板。
大部分换热器都采用弓形折流板。
弓形折流板在壳程内的放置形式上下方向排列的形式,用以造成液体剧烈扰动以增大传热系数;左右方
向排列的,多数用于卧式换热器,设备中都伴随着有气相的吸收冷凝,以利于冷凝液和气体的流动,当列管是正方形排列时,为了使介质形成湍流以提高换热效果,则采用转角切口。
单弓形折流板主要是为了提高整体的壳程的错流程度,切口的百分数一般为20%~49%;通常为20%~25%,最佳大小为20%,此时单位压降下传热膜系数最高,小于20%(缺口处不布管除外)压降较大;切口超过20%,导致形成流体流速的滞留区,切口过大或过小,都会降低管束的传热性能;为了减小振动,亦可采用缺口处不布管,缺口可减小到15%或者25%左右,其压降只有单弓形的1/3左右。
双弓形折流板:当采用单弓形阻力过高,可改为双弓形折流板。
双弓形折流板可以将通过壳程侧的流段分为两股,以此达到降低压降的目的,减小折流板间距,降低错流程度,其特点是有较大开口区域,允许与管子近乎平行的流动,所以流动诱发振动的几率较小。
多弓形折流板保留了单弓的优点,有些尺寸的多弓形可以使流体的流动和管子接近平行,压降更低,降低振动可能性。
双弓形和三弓形折流板能使两种换热介质良好的进行接触,消除换热器的死角,以提高换热目的,一般用于于大直径和大流量场合。
二、圆盘-圆环形折流板。
圆盘-圆环形折流板是由大直径的开口圆板即圆环板(也称环板)和小直径的盘板交错排列组成。
介质流动的特征是与轴心对称,流动多为与管束相向的平行流,因此,流动阻力较单弓形折流板小,由与管子垂直的横流引起的振动较小,但壳程传热膜系数增加比单弓形的小。
圆盘-圆环形折流板一般用于大直径和大流量场合。
三、矩形折流板—在大圆盘上开设矩形孔和矩形挡板交错排列。
矩形折流板有竖放和横放两种形式,竖放用于壳程介质是液相或有冷凝夜的情况;横放用于壳程是气相。
其多用于大直径和大流量场合。
四、折流杆式换热器。
这种换热器的主要结构主要是由折流网络和换热管组成的,折流网络是由很多个折流圈相隔一定距离焊接或用普通的定距管固定于拉杆上形成的。
而每一个折流圈又是由很多根折流杆相互平行通过一定的间距焊接在外环上形成的。
这些折流网络和换热管进行热交换就达到换热器的换热目的。
这种换热器能够改善常规的板式折流板换热器的流体诱导振动。
在这种结构中,支撑管子的折流杆与管子几乎不存在间隙,管束中每根传热管的上、下、左、右都得到了可靠的支撑,而且从根本上改变了流体的流动状况,变折流板换热器的
横向流动为平行于管子的轴向流动,从而消除了产生液体诱导振动的根源,增加了传热效率,减小了压力降。
另外折流杆换热器不易结垢,流体在经过折流杆时产生文丘里效应对管壁有强烈的冲刷作用,而且由于平行流动,避免了死区,也使得污垢难以形成。
五、格栅折流板。
格栅折流板是将上面的折流杆式换热器中的折流杆换成钢板条,排列方式与换热管相同。
格栅折流板完全用于管子的支承,不起折流作用,但它有较大的间隙,流体很容易从间隙中沿管束轴向通过,阻力小。
它的优点是栅形板与换热管表面的接触面积大,增加了换热管受弯曲应力时的稳定性,格栅折流板刚性好,但制作比较麻烦。
格栅折流板多为2层结构, 3层和四层结构较少。
六、其它折流板,如螺旋折流板。
其基本设计思想是:在壳程采用沿壳体轴线展开的螺旋形折流板结构,使换热器中的壳侧流体呈连续的螺旋状流动,可以消除壳程流体的流动死区,降低壳程流动压力损失,减小换热器能耗,并且强化壳程传热。
目前国内螺旋折流板列管式换热器结构样式繁多,但大体上分成连续螺旋折流板结构和非连续螺旋折流板结构(如图五)两大类。
图五
目前对连续型的研究较少,非连续型螺旋折流板换热器的结构由2~4块1/4椭圆(以椭圆长、短轴为边)或1/4扇形(以椭圆短边为对称线截取)自壳程进口处向出口处呈螺旋状首尾相接组装形成。
壳程流体围绕换热器中心轴呈近似螺旋状向前连续平稳流动。
螺旋折流板换热器由于其近似螺旋状的介质流动通道相比于弓形折流板换热器具有换热性能好、压降小的特点,并且具有良好的抗振性能和防
垢性能,特别适用于易结垢、高黏度的介质,如原油、渣油等的强化传热。
由于螺旋折流板换热器结构的原因,其制造加工比较复杂,成本高,制约了它的大规模推广。
从以上内容可以看出,换热器折流板型式是多种多样的。
折流板的型式对换热器的换热效率、压降及换热管的振动均有很大影响,选型的正确与否及合理性就对该台换热器起到关键作用,希望我上面所提到的一些内容对折流板的选型有所帮助。
传统的弓形折流板管壳式换热器具有结构简单、适用性广、制造成本低等优点,这种换热器的主要缺点是换热效率较低,壳程压力损失较大,存在流动死区,容易结构等。
近年来人们进行了许多研究和改进,上面所说的几种结构就在其中。
在改进、研究和选型中管壳式换热器折流板的布置还应遵循以下几点原则:
1.折流板的布置必须符合工艺设计条件的要求。
特别是对折流板的形式、折流板的间距、靠近壳程物料进出口的折流板位置等必须尽可能满足工艺设计条件。
2.在工艺设计条件没有特别要求的情况下,折流板一般应按等间距布置,管束两端的折流板尽可能靠近壳程进、出口接管。
3.卧式换热器的壳程为单相清洁流体时,折流板缺口应水平上下布置,若气体中含有少量液体时,则应在缺口朝上的折流板的最低处开通液口;若液体中含有少量气体时,则应在缺口朝下的折流板的最高处开通气口。
4.卧式换热器、冷凝器和重沸器的壳程介质为气、液相共存或液体中含有固体物料时,折流板缺口应垂直左右布置,并在折流板最低处开通液口。
参考文献
1、GB151-1999 《管壳式换热器》
2、化工设备设计全书—换热器
3、压力容器设计指导手册
4、折流杆换热器的设计北京沃利帕森工程技术有限公司康丽媛
中图分类号TQ051文献标识码A 文章编号1674-6708(2012)69-0132-02 5、螺旋折流板换热器研究进展太原科技大学化学与生物工程学院宋素芳
中图分类号TQ[文献标识码] A [文章编号] 1007-1865(2010)04-0020-02。