培养基模拟灌装试验管理规
培养基模拟灌装试验方案

培养基模拟灌装试验方案(无菌粉末分装粉针剂)目录1.目的 (3)2.范围 (3)3.验证组织及职责 (3)4.方案说明 (4)5.工艺概述 (4)6.验证前检查 (5)7.验证内容 (6)8.验证周期 (13)9.验证总结、评价与建议 (14)10.验证报告的审核批准 (14)11.验证合格证 (14)1.目的对于无菌生产来说,即使所有与产品无菌性有关的设备部件、容器以及原料都经过有效地灭菌处理,但当这些生产要素在实际工艺条件下组合在一起时,仍有可能因各种原因导致产品被污染。
对于非最终灭菌的无菌生产工艺必须进行培养基灌装来验证。
培养基灌装是用于评估整个无菌工艺过程,用于表明如果严格按照工艺要求生产,产品的无菌性有可靠保证。
2.范围本验证方案适用于无菌粉末分装粉针剂生产线的培养基模拟灌装试验。
3.验证组织及职责3.1验证职责3.2验证方案的培训验证实施前,QA部门对验证相关人员培训,填写《员工培训记录表》。
4.方案说明4.1验证过程中偏差处理的要求执行《偏差管理规程》4.2验证过程中变更的要求执行《变更管理规程》4.3验证过程中记录填写的要求执行《记录管理规程》4.4其他要求5.工艺概述5.1产品:5.1.1性状:白色结晶或结晶性粉末。
5.1.2规格:0.25g/瓶。
5.1.3包装:10ml西林瓶。
5.1.4批量:24000瓶。
5.2胶塞处理:纯化水清洗、硅化、注射用水清洗、灭菌。
(121℃,20分钟)5.3西林瓶处理:纯化水清洗、注射用水清洗、压缩空气吹干、隧道烘箱灭菌。
(灭菌段温度320℃≥5分钟,冷却温度﹤40℃)5.4铝盖干热灭菌。
(180℃,120分钟)5.5无菌药粉通过分装机充填到西林瓶中,盖胶塞、轧铝盖、灯检、贴签、包装。
5.6工艺流程图如下:6.验证前检查6.1人员的确认确认参与验证人员均接受过微生物知识、更无菌衣、无菌操作、培养基模拟灌装试验方案的培训,同时确认参与验证人员的健康体检情况,详见附件1《员工体检和培训确认表》。
培养基模拟灌装验证

一、目的建立培养基模拟灌装验证的管理规程,确保培养基模拟灌装验证符合生产工艺及GMP要求。
二、适用范围适用于制剂车间生产的产品需要培养基模拟灌装验证的整个工艺过程,包括从部件、材料的灭菌准备,一直到完成灌装和容器密封的整个过程。
三、责任者制剂车间、生产部、公用事业部、质量控制部、物流部、质量保证部及验证部遵照执行。
四、缩写与定义1. 最差条件(worst case)在SOP范围内(或超出),由工艺参数的上、下限和相关因素组成的一个或一系列条件。
与理想条件相比时,最差条件使产品或者生产工艺失败的几率为最大,这样的条件不一定导致产品或生产工艺的失败。
2. 干预(Intervention)操作人员在无菌操作区域内的操作活动。
3. 正常干预(Inherent Interventions)在无菌工艺灌装过程中发生的正常的在计划中的活动(例如,设备安装、装量调节、胶塞的再补给、灌装容器的再补给、环境监测、取样等等)。
4. 纠正干预(Corrective Interventions)在无菌工艺灌装过程中的纠正或调整的活动,其不属于计划性。
(例如,灌装容器的破损、倒瓶、掉塞、更换灌装针、灌装设备维修)五、健康、安全和环境无六、程序1. 验证小组职责:1.1 验证部1.1.1 负责编制培养基模拟灌装验证管理规程。
1.1.2 协助起草并审核培养基模拟灌装验证方案及培养基模拟灌装验证报告。
1.1.3 验证工作的组织与协调,参与并监督培养基模拟灌装验证的实施,模拟灌装样品的接收、培养及结果观察。
1.1.4 对验证过程中偏差、变更处理过程追踪。
1.2 质量保证部1.2.1 审核培养基模拟灌装验证方案及培养基模拟灌装验证报告。
1.2.2 验证工作的组织与协调,参与并监督培养基模拟灌装验证的实施,负责验证过程中取样。
1.2.3 负责培养基模拟灌装验证环境监控,参与模拟灌装样品的接收、培养及结果观察。
1.2.4 参与验证过程中偏差、变更处理。
培养基模拟灌装管理..

使用自动粒子计数法测试洁净室中的粒子。按悬浮状态连续计数的方法,空气采样量为28.3L/分,每个采样点测试3次,采样过程应覆盖培养基模拟灌装全过程,最少采样点的数目参考GB/T16292-2010《医药工业洁净室(区)悬浮粒子测试方法》制定。
3)检测点分布:根据实际情况参考GB/T16292-2010《医药工业洁净室(区)悬浮粒子测试方法》设置
QC经理
签名
日期(年/月/日)
审核
QA经理
签名
日期(年/月日)
审核
技术科科长
签名
日期(年/月/日)
批准
质量受权人
签名
日期(年/月/日)
培养基模拟灌装验证
1.验证项目概述
培养基模拟灌装验证,是在与培养基模拟灌装生产过程有关的其他验证,如:洁净厂房、公用系统、灭菌设备(包括蒸汽灭菌柜、隧道式干燥灭菌器、热循环烘箱等)、制剂设备(包括分装机及灌装机、洗瓶机、冻干机、轧盖机等)、容器具清洁验证合格后,且操作人员熟练掌握了岗位SOP后进行的。
负责监督测试现场严格按本方案实施
负责相关SOP文件的制定和审核
质量控制(QC)的职责包括以下:
负责完成所有测试内容和出具完整的检验报告
设动科的职责包括以下:
负责完成最初的生产设备安装、校验和确认
负责对所有仪器仪表进行校验
负责对验证仪器进行校验
验证参与人员与职责
姓名
部门
职务
分工
质量管理部
总监
最终批准验证文件
3.人员与职责
技术科的职责包括以下:
负责计划、组织、协调本方案的实施
负责本方案的评估并将其提交各部门批复
负责对验证结果作出正确的评估并出具完整的验证文件
培养基无菌灌装模拟试验方案

培养基⽆菌灌装模拟试验⽅案XXXXX制药有限公司培养基⽆菌灌装模拟试验再验证⽅案⽂件编号: YZML101P -09所在车间:冻⼲粉针车间起草⼈:⽇期: 2009年6⽉25⽇审核⼈:⽇期:2009年7⽉04⽇批准⼈:⽇期: 2009年7⽉05⽇验证⽅案的起草与审批验证⽅案的起草验证⽅案的审批验证进度计划提出完整的验证计划,经验证⼩组批准后实施,整个验证活动分三个阶段完成。
验证⽅案⽬录第⼀部分:概述 (4)1、验证⽬的 (4)2、验证概述 (4)3、验证领导⼩组分⼯及职责 (4)4、被模拟⼯艺 (5)5、模拟试验中使⽤的设备设施 (6)6、培养基的选择 (6)7、微⽣物培养条件 (7)8、⼯艺模拟的批量,批次 (7)9、灌装体积、灌装速度及灌装⽤容器的确定 (7)10、验证最差条件 (7)11、可接受的合格标准 (8)第⼆部分:试验实施 (9)1、试验实施前的准备⼯作 (9)1.1 培养基⽆菌性试验 (9)1.2 培养基促⽣长试验 (9)1.3 ⽆菌环境控制与监测 (9)2、试验实施过程 (11)2.1⼚房、空间清洁 (11)2.2试验相关⼯序准备 (12)2.3培养基配置、除菌过滤过程 (12)2.4模拟灌装 (12)2.5模拟冻⼲ (13)2.6轧盖 (13)2.7微⽣物培养 (13)3、盖胶塞密闭系统挑战试验 (15)4、偏差的处理 (15)5、试验结果分析与评估 (16)6、验证的维护 (17)第⼀部分:概述1、验证⽬的评价⼀个⽆菌⼯艺操作能⼒的最有⽤的⽅法之⼀是⼯艺模拟,其提供了⼀个可能影响最终产品⽆菌的⽆菌⼯艺操作变更进⾏评价的⽅法,它可以⽤于鉴别⽆菌操作⼯艺中,可以导致产品微⽣物污染的潜在缺陷,通过模拟⽆菌冻⼲粉针的灌装试验,证明冻⼲粉针灌装过程中所采⽤的⽆菌灌装⼯艺参数和相关的SOP对于防⽌微⽣物污染⽔平达到可接受的合格标准,或提供保证所⽣产产品的⽆菌性的可信限度达到可接受的合格标准的证据。
培养基模拟灌装试验(07.7.7)
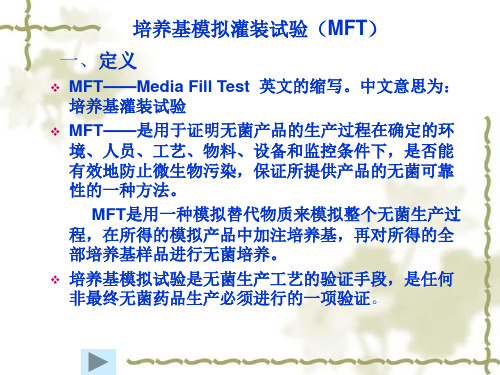
生产环境变更 生产工艺变更 主要设备变更 主要关键岗位生产人员变更 阳性试验变更 阳性试验变更
培养基模拟灌装试验( 培养基模拟灌装试验(MFT) ) 无菌原料药和无菌制剂(非最终灭菌制剂) 无菌原料药和无菌制剂(非最终灭菌制剂) 生产出现如下情况
培养基模拟灌装试验( 培养基模拟灌装试验(MFT) )
(7)人员 ) 更衣? 更衣 消毒? 消毒 操作过程? 操作过程 操作人员? 操作人员? QC人员 人员? 人员 管理人员? 管理人员 其它人员?(如外来参观人员等 如外来参观人员等) 其它人员 如外来参观人员等
A. B. C. D. E. F. G.
四、MFT的前期工作 的前期工作
模拟灌装试验人员的培训 (1)模拟灌装试验人员无菌操作知识培训 ) (2)模拟灌装试验人员无菌检验知识培训 ) (3)模拟灌装装备检修人员的无菌设备维修 ) 知识培训 培训( (4)模拟灌装试验 )模拟灌装试验SOP培训(含生产、QC、 培训 含生产、 、 计量、装备) 计量、装备) 培训( (5)模拟灌装试验 )模拟灌装试验SOR培训(含生产、 培训 含生产、 QC、计量、装备) 、计量、装备)
培养基模拟灌装试验( 培养基模拟灌装试验(MFT) )
结果的分析
对微生物污染的样品应进行鉴别试验, 对微生物污染的样品应进行鉴别试验,鉴别的内容 至少应包括菌落、细胞形态学及革兰染色特性等。 至少应包括菌落、细胞形态学及革兰染色特性等。 不成功(染菌) 不成功(染菌)原因 ?(生产 (1)环境?(生产?检验?储存?) )环境?(生产?检验?储存?) (2)设备? )设备? (3)物料? )物料? (4)转移过程的容器? )转移过程的容器? (5)水? ) (6)检测 )检测?
4、培养基模拟灌装试验

3
法规及相关指南(二)
药品GMP指南•无菌药品:12 无菌工艺模拟试验
PDA technical report NO.22 Process simulation testing for aseptically filled products, 2011
7
培养基模拟灌装流程-方案
培养基的选择
一般原则:选择适合绝大多数微生物生长的 胰蛋白大豆肉汤培养基(TSB);
2015-06-24 特殊情况:硫乙醇酸流体培养基(FTM)
(1)无菌工艺需要在一个严格无氧环境中进行; (2)环境监测或无菌检查中发现厌氧菌的存在; (3)厌氧环境和FTM促生长的研究。
鉴定
试验
调查
微生物 限度
无菌 检查
溯源
环境 监测
24
45
40 39
35
34
32
30
25
24
菌种统计
20
15 12 10 10
10 7 6
2015-06-24
5
4 33
2222 2
11111 111111 111111 111
0
系列1
藤黄 微球
菌
科式 葡萄 球菌
人葡 萄球
菌
克氏 葡萄 球菌
萎缩 芽孢 杆菌
H
48h
48h
H
20人
20人
M
150-400
视情况 设置
M
16h
16h
12
培养基模拟灌装流程-方案
干扰动作的设计原则: 识别干扰-干扰汇总表 干扰分类:计划性干预和非计划性干预
培养基模拟灌装试验管理规

1 主题内容与适用范围本文件规定了培养基模拟灌装试验的程序和要求。
本文件适用于培养基模拟灌装试验的管理。
2 引用标准《药品生产质量管理规范》2010年修订3 术语培养基模拟灌装试验(以下简称试验):英文名称MFT——Media Fill Test的英文缩写,是用一种模拟替代物质来模拟整个无菌生产过程,在所得的模拟产品中加注培养基,再对所得的全部培养基样品进行无菌培养。
培养基模拟试验是无菌生产工艺的验证手段,是任何非最终无菌药品生产必须进行的一项验证。
最差条件:导致工艺及产品失败的概率高于正常工艺的条件或状态,即标准操作规程范围以内工艺的上限和下限。
但这类最差条件不一定必然导致产品或工艺的不合格。
4 职责4.1 生产部门负责试验方案的制定、组织实施、试验报告的撰写、偏差的报告等。
4.2 质监中心负责试验培养基的促生长试验、灌装物的培养等。
4.3 质量保证部负责试验过程的监督管理。
5 管理规定5.1 试验目的:规范公司培养基模拟灌装试验,评估无菌原料药和无菌制剂的生产工艺,为所生产产品无菌性的可信限度达到可接受的合格标准提供证据,证明其具有生产无菌原料药和无菌制剂的能力并具有可重现性,符合现行GMP要求和相关技术指南要求。
5.2 试验要求5.2.1 试验频次培养基模拟灌装试验的首次验证,每班次应当连续进行3次合格试验。
培养基模拟灌装试验按照生产工艺每班次半年进行1次,每次至少一批。
单一规格品种再验证周期为半年,正常生产的多规格品种每一规格再验证周期为一年。
每位无菌操作人员每年至少参加一次成功的培养基模拟灌装试验。
空气净化系统、设备、生产工艺及人员重大变更后,应当重复进行培养基模拟灌装试验。
5.2.2 试验批量及容器的数量、装量培养基灌装批量及容器的数量、装量应当足以保证评价的有效性。
批量较小的产品,培养基灌装的数量应当至少等于产品的批量。
无菌原料药容器数量不少于被模拟产品的实际包装量,模拟物装量尽量接近实际值,不超过容器体积的70%,培养基装量应能满足微生物的生长;粉针制剂灌装数量每种规格不少于5000支。
培养基模拟灌装试验方案

培养基模拟灌装试验方案(无菌粉末分装粉针剂)目录1.目的 (3)2.范围 (3)3.验证组织及职责 (3)4.方案说明 (4)5.工艺概述 (4)6.验证前检查 (5)7.验证内容 (6)8.验证周期 (13)9.验证总结、评价与建议 (14)10.验证报告的审核批准 (14)11.验证合格证 (14)1.目的对于无菌生产来说,即使所有与产品无菌性有关的设备部件、容器以及原料都经过有效地灭菌处理,但当这些生产要素在实际工艺条件下组合在一起时,仍有可能因各种原因导致产品被污染。
对于非最终灭菌的无菌生产工艺必须进行培养基灌装来验证。
培养基灌装是用于评估整个无菌工艺过程,用于表明如果严格按照工艺要求生产,产品的无菌性有可靠保证。
2.范围本验证方案适用于无菌粉末分装粉针剂生产线的培养基模拟灌装试验。
3.验证组织及职责3.1验证职责3.2验证方案的培训验证实施前,QA部门对验证相关人员培训,填写《员工培训记录表》。
4.方案说明4.1验证过程中偏差处理的要求执行《偏差管理规程》4.2验证过程中变更的要求执行《变更管理规程》4.3验证过程中记录填写的要求执行《记录管理规程》4.4其他要求5.工艺概述5.1产品:5.1.1性状:白色结晶或结晶性粉末。
5.1.2规格:0.25g/瓶。
5.1.3包装:10ml西林瓶。
5.1.4批量:24000瓶。
5.2胶塞处理:纯化水清洗、硅化、注射用水清洗、灭菌。
(121℃,20分钟)5.3西林瓶处理:纯化水清洗、注射用水清洗、压缩空气吹干、隧道烘箱灭菌。
(灭菌段温度320℃≥5分钟,冷却温度﹤40℃)5.4铝盖干热灭菌。
(180℃,120分钟)5.5无菌药粉通过分装机充填到西林瓶中,盖胶塞、轧铝盖、灯检、贴签、包装。
5.6工艺流程图如下:6.验证前检查6.1人员的确认确认参与验证人员均接受过微生物知识、更无菌衣、无菌操作、培养基模拟灌装试验方案的培训,同时确认参与验证人员的健康体检情况,详见附件1《员工体检和培训确认表》。
- 1、下载文档前请自行甄别文档内容的完整性,平台不提供额外的编辑、内容补充、找答案等附加服务。
- 2、"仅部分预览"的文档,不可在线预览部分如存在完整性等问题,可反馈申请退款(可完整预览的文档不适用该条件!)。
- 3、如文档侵犯您的权益,请联系客服反馈,我们会尽快为您处理(人工客服工作时间:9:00-18:30)。
1 主题内容与适用范围本文件规定了培养基模拟灌装试验的程序和要求。
本文件适用于培养基模拟灌装试验的管理。
2 引用标准《药品生产质量管理规范》2010年修订3 术语培养基模拟灌装试验(以下简称试验):英文名称MFT——Media Fill Test的英文缩写,是用一种模拟替代物质来模拟整个无菌生产过程,在所得的模拟产品中加注培养基,再对所得的全部培养基样品进行无菌培养。
培养基模拟试验是无菌生产工艺的验证手段,是任何非最终无菌药品生产必须进行的一项验证。
最差条件:导致工艺及产品失败的概率高于正常工艺的条件或状态,即标准操作规程范围以内工艺的上限和下限。
但这类最差条件不一定必然导致产品或工艺的不合格。
4 职责4.1 生产部门负责试验方案的制定、组织实施、试验报告的撰写、偏差的报告等。
4.2 质监中心负责试验培养基的促生长试验、灌装物的培养等。
4.3 质量保证部负责试验过程的监督管理。
5 管理规定5.1 试验目的:规范公司培养基模拟灌装试验,评估无菌原料药和无菌制剂的生产工艺,为所生产产品无菌性的可信限度达到可接受的合格标准提供证据,证明其具有生产无菌原料药和无菌制剂的能力并具有可重现性,符合现行GMP要求和相关技术指南要求。
5.2 试验要求5.2.1 试验频次培养基模拟灌装试验的首次验证,每班次应当连续进行3次合格试验。
培养基模拟灌装试验按照生产工艺每班次半年进行1次,每次至少一批。
单一规格品种再验证周期为半年,正常生产的多规格品种每一规格再验证周期为一年。
每位无菌操作人员每年至少参加一次成功的培养基模拟灌装试验。
空气净化系统、设备、生产工艺及人员重大变更后,应当重复进行培养基模拟灌装试验。
5.2.2 试验批量及容器的数量、装量培养基灌装批量及容器的数量、装量应当足以保证评价的有效性。
批量较小的产品,培养基灌装的数量应当至少等于产品的批量。
无菌原料药容器数量不少于被模拟产品的实际包装量,模拟物装量尽量接近实际值,不超过容器体积的70%,培养基装量应能满足微生物的生长;粉针制剂灌装数量每种规格不少于5000支。
培养基装量不小于容器体积的10%,模拟物不少于10mg/1ml培养基,具体加量根据溶解性试验确定。
灌装体积的多少,应充分考虑容器倒转或旋转时,培养基能充分地接触到容器和密封件的内表面,不能达到此要求时应适当增加灌装体积。
5.2.3 试验染菌率的可接受度培养基模拟灌装试验的目标是零污染,发生任何微生物污染时,均应当进行调查。
应当遵循以下要求:(一)灌装数量少于5000时,不得检出污染品。
(二)灌装数量在5000至10000时:1.有1支污染,需调查,可考虑重复试验;2.有2支污染,需调查后,进行再验证。
(三)灌装数量超过10000时:1.有1支污染,需调查;2.有2支污染,需调查后,进行再验证。
5.3 试验准备5.3.1 试验开始前,除工艺验证、本验证外的其它验证已完成且验证合格。
需完成的验证主要有:a 厂房设施、设备、空调系统、水系统需经过确认和验证;b 灭菌设备、除菌过滤器、直接接触无菌药品的设备、容器、管道、人员及无菌服的除菌灭菌效果经过验证;c 清洁方法、检验方法等经过验证。
5.3.2 试验开始前,应确保环境已消毒、设备已清洁并灭菌,设施、设备、空调净化系统已经在预期的状态中受控运行。
需建立的程序及无菌准备至少包括:a 人流、物流、设备使用要求和参数的确定,无菌室消毒和维护的要求;b 粒子和微生物监控的要求和频率:包括悬浮粒子、沉降菌、浮游菌、厂房、设备表面、人员洁净服外表面擦拭菌的采样点、采样频次;c 直接接触无菌药品的内包材灭菌:铝桶、塑料袋、西林瓶、胶塞等;装载容器、用品及用具灭菌;无菌物料检测仪器、物品灭菌;蠕动泵、管道输送灭菌等。
5.3.3 试验开始前,明确对人员的要求,至少应包括:a 参与试验的相关人员应进行培训,培训内容根据实际需要确定:更衣和无菌操作知识培训;取样和无菌检验知识培训;生产、检验、计量、设备等操作规程培训;相关设备检修人员的无菌设备维修知识培训等;b 应把所有参与试验的操作者和主管人的姓名、员工参与次数以及相关事项记录在批生产记录里,包括进出次数等。
操作者的操作任务应与正常灌装实施期间的任务相同。
c 试验期间所有进入生产区域的人员(包含执行环境监控人员在内)都必须正确着装。
d 试验的员工数量不得小于正常生产条件下该区域允许的最大员工数量。
5.3.4 培养基和模拟培养物5.3.4.1 培养基的准备:胰蛋白酶酪胨大豆培养基(TSB)。
a 培养基的消毒:过滤灭菌 (0.2um filter)或蒸汽灭菌;b 培养基的测试:促生长性能测试合格、无菌性测试合格;灭菌后的培养基在百级层流下用西林瓶进行取样分装,共分装30支:促生长性能试验:取10支分装好培养基的西林瓶接种枯草杆菌,接种量<100CFU,接种后盖塞、封口,在30~35℃培养7天;另取10支接种白色念珠菌,接种量<100CFU,接种后盖塞、封口,在23~28℃培养7天;7天内至少50%上述接种的西林瓶中出现明显的所接种微生物的生长。
无菌性试验:取10支分装好培养基的西林瓶分别加5ml符合无菌要求的水,盖塞、封口后先在23~28℃培养7天,然后在30~35℃培养7天,应无任何微生物生长。
5.3.4.2 模拟替代物的准备:惰性粉末a 惰性粉末的选择选材要求:无活性、易灭菌、易溶解、对培养基促进生长作用无副作用,易灌装,流动性要好;种类:聚乙二醇系列(PEG 6000,PEG 8000), 甘露醇,乳糖,碳酸钠等;b 惰性粉末灭菌:伽马辐照灭菌(钴60辐照灭菌,用量15~25kGy)或干热灭菌;c 惰性粉末测试:无菌性测试合格、无抑菌性测试合格,进行溶解性试验。
无菌性试验:用无菌操作方式取样,并按药典规定的无菌检验法检验其无菌性。
无抑菌性试验:将惰性粉末按无菌操作方式分别取样,用无菌蒸馏水制备成混悬液,加入培养基形成浓度分别为1.0%、2.5%、5.0%、10%(W/V)的样品液,将不同浓度的各种样品液分装于4个试管中,在其中2支试管内接种<100CFU的枯草杆菌,在另2支试管内接种<100CFU的白色念珠菌,对照品为空白培养基接种相同的枯草杆菌和白色念珠菌,全部样品、对照品在相适应的温度下培养7天。
7天内所有样品、对照品试管内均应有明显的微生物生长。
可证明所使用惰性粉末对枯草杆菌和白色念珠菌均无抑制作用。
溶解性试验:惰性粉末在一定浓度时,在轻微的搅拌下应能溶解于温度与培养温度相当的培养基中,若不能溶解则应在略低于该浓度下重新试验。
一般使用浓度为5.0%~10%。
5.3.5 试验工艺范围及步骤根据无菌产品的生产工艺,画出工艺流程图,选择恰当的试验范围。
通常情况下,无菌原料药的无菌工艺模拟以物料溶解开始进行模拟,主要模拟溶解、过滤、结晶、过滤、洗涤、干燥、无菌物料的转移(必要时)、粉碎(颗粒)、微粉(必要时)、分装、密封(轧盖或热合,根据工艺定)。
粉针制剂主要模拟西林瓶、胶塞的洗涤、灭菌、分装、加塞、压盖等工艺步骤。
在无菌模拟过程中,可能需要对实际操作进行一些变更,这些变更应基于风险分析的原则,相对于正常的操作,这些变更不应对模拟的结果造成影响。
方案的变更参见《变更管理程序》。
5.3.6 最差条件设计5.3.6.1 模拟正常生产最差条件a 灌装运行速度:最低灌装速度或½的最低灌装速度;b 手工灌装;c 最长时间的确认:培养基的灌装时间一般要大于等于最长的生产时间;延长完成灭菌至开始过程模拟的时间;灌装的设备,储罐,灭菌后原料,胶塞等储存的最长时间;使用最长时间间隔的容量、设备、取样工具;d 模拟日常班次轮换,暂停/休息和更衣过程:2班或3班的变化,中午/晚饭的休息时间,进出的更衣等;模拟员工最疲备时的操作;对无菌人员连续工作强度进行模拟;e 设备的安装和连接:培养基灌装时设备的安装和连接应和日常时设备的安装连接一致;f 更换气体。
5.3.6.2 模拟常规干预操作:装量的核对、装量的调节、物料的添加(橡塞,粉子等);瓶子堵塞,橡塞堵塞,粉子堵塞等的操作;5.3.6.3 模拟非常规干预操作:断电、设备维修等情况;更换灌装头,更换或调节剂量盘,修理传送带等;5.3.6.4 验证设计时,应综合考虑生产线可能造成污染的各种因素,尽量模拟这些可能的情况,尽可能模拟生产时的无菌操作;在无菌工艺模拟试验中,每一次干扰都要记录在批生产记录里,指明干扰时间。
5.4 试验程序5.4.1 试验方案根据确定的工艺范围及步骤,在分装模拟替代物后、密封或加塞前灌装培养基,形成培养基模拟灌装试验方案。
方案经审核批准后由生产单位组织实施。
过程中如实记录各步骤及产生的偏差,并形成培养基模拟灌装试验批生产记录。
5.4.2 取样在方案中应明确规定无菌模拟灌装试验实施过程中的取样方法及取样量;在包装后,应由取样人员根据实际取样原则按无菌操作方式模拟取样,并进行同条件培养。
5.4.3 培养基灌装产品的培养和测试5.4.3.1 所有密闭性完整的容器都应进行培养并检查。
5.4.3.2 培养条件:第一阶段: 23~28℃, 7天培养;第二阶段: 30~35℃, 7天培养;培养箱要进行温度分布的验证;5.4.3.3 培养基的检查:a 严格控制丢弃任何已经灌装的培养基,任何丢弃都应有充分的理由并做好记录。
例如,在灌装过程中正常产品的灌装量控制精度需要很高,但培养基灌装时,只要符合最低灌装量,而不应该丢弃。
但如果是胶塞上位不正确的培养基,由于密闭系统不完整,必须进行丢弃。
b 一般在第三,七和十四天进行检查,检查人员应进行专门的培训;c 检查的要求:明亮的灯光、慢慢地旋转、阳性容器必须主管进行复核;5.4.4 灌装试验后培养基生长试验:a 必须在产品培养结束(14天)后进行;b 测试所用的菌为:常规菌(药典要求):枯草芽孢杆菌、白色念珠球菌;非常规菌:生产现场中经常发现的菌、对该产品比较敏感的标准菌;c 接种的浓度:小于100 CFU/瓶。
5.4.5 失败调查工艺模拟试验中如果出现阳性结果,应对其开展调查,确定失败的最可能的原因。
必须对调查进行记录,至少包括对以下内容的检查:a 空气监测结果:沉降菌、浮游菌、悬浮粒子监测数据;表面擦拭菌监控数据;b 过滤前后完整性测试数据;使用的设备、物品、组件的灭菌数据及储存条件;c 评估人员是否遵循操作规程和检验操作规程(如:若培养基灌装被视频记录下来了,检查视频);若全部按规定操作,评估现有工艺及操作规程是否适用;调查结果和纠正措施应以报告的形式记录在文件中,报告经过审核批准后,重新开展模拟灌装试验。
5.4.6 再验证要求出现下列情况之一时,应至少进行一次再验证:a 设备、人员、工艺等发生重大变更时;b 产品出现无菌检测失败或无菌原因的投诉,但未查清具体原因时;c 无菌生产设备出现3个月以下停产时;d 连续生产半年时。