铝合金液态模锻成型过程的可视化【文献综述】
液态模锻工艺介绍资料
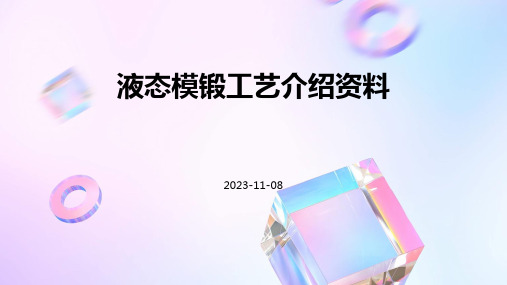
产,以满足不同客户的需求。
技术挑战与难点
模具设计与制造
液态模锻工艺的模具设计与制造是技术难点之一,需要具备高精 度、高强度、高耐热性能等要求。
液态金属流动控制
在液态模锻过程中,液态金属的流动控制是关键技术之一,需要掌 握金属的流动规律和模具填充技巧。
设备投资大
液态模锻工艺需要使用专门的设备 和生产线,相较于传统锻造工艺, 设备投资较大。
液态模锻工艺的改进方向
01
02
03
提高成型精度
通过改进模具设计和制造 工艺,提高液态模锻工艺 的成型精度。
开发新型设备
研发新型的液态模锻设备 和工艺,提高生产效率和 产品质量。
优化生产流程
通过对生产流程进行优化 ,提高生产效率,降低生 产成本。
特点
高生产效率:液态模 锻工艺可以实现批量 生产,提高生产效率 。
制品质量高:液态模 锻工艺可以获得高精 度、高表面质量的金 属制品。
节约材料:液态模锻 工艺采用模具成型, 可以减少材料浪费, 降低成本。
液态模锻工艺的起源与发展
起源
液态模锻工艺起源于20世纪初,最初用于铝合金制品的生产 。
发展
随着科技的不断进步,液态模锻工艺逐渐完善,应用范围也 不断扩大,现在已经成为金属加工领域的重要技术之一。
液态模锻工艺的应用范围
航空航天领域
液态模锻工艺可以用于制造航空航天 领域的铝合金、镁合金等高性能金属 制品。
汽车制造领域
液态模锻工艺可以用于制造汽车车身 、发动机部件等高性能金属制品。
电子通讯领域
液态模锻工艺可以用于制造电子通讯 领域的金属壳体、连接器等精密金属 制品。
铝合金薄壁壳体件液态模锻成形工艺研究

第22卷第11期Voa.22No.11黄河科技学院学报JOURNALOFHUANGHES&TCOLLEGE2020年11月Nev.2020铝合金薄壁壳体件液态模锻成形工艺研究牛海侠%朱松波2张琼%(1.安徽三联学院机械工程学院,安徽合肥230601;2.天津津航计算技术研究所,天津300000)摘要:铝合金薄壁壳体件在航空航天和高速列车上有广泛的应用,是较为重要的受力构件。
这类零件壁厚较薄,普通的生产成形工艺很难实现其性能的要求。
以某火箭发动机阀门壳体件为研究对象,采用液态模锻成形工艺,通过模具设计和改变成形工艺参数进行液态模锻成形实验,研究了零件的最佳成形方案和合理工艺参数,为铝合金薄壁壳体件的液态模锻成形提供参考。
关键词:薄壁壳体件;液态模锻;模具设计;工艺参数中图分类号:TG146.3文献标识码:A文章编号:2096-790X(2020)11-0038-06DOI:10.19576/j.issn.2096-790X.2020.11.008Research on Liquid Din Forging Forming Procest ofAluminum Alloy Thid-Walled Shell PartsNou Haotoa1.Zhu Songbo2.ZhangQoong1(1.Anhut Sanlan University,School of Mechanical Engineering,Hefee COy,Anhui Province230601;2.Tianjm Tianjm Instituty O computing technology,Tianjm City300000)Abstraci:Aluminum toy thin-walled shell pc S s are impoaant forco-beaang components that widely used in aerospaco and high-speed trains The wai thickness of such pafs is relativeay thin,and d is didicult for ordinary production and forming processes to meet their paformanco requiements.Theefore,this artide takes a rocket engine valvv shell as the research object,adopts liquid die forging forming process,conducts liquid die forging foaning experiment through die design and changing forming process parameters,and studies the optiml forming scheme and reasonable process parameters of the parts.Moreover, this paper provides a reference for thaiquid die forging of aaumonum a a oython-wa a d sh=a paets.Key woris:thin-walled shell parts;liquid die forging;mold design;process parameters0前言铝合金件在机械加工时存在刚性和硬度不足、锻后易变形等问题,普通的铸造、锻造已逐渐不能满足高性能铝合金件的需求[1]"采用液态模锻加工,充分利用该工艺低压充型及高压迅速补缩凝固的特点,获得性能较好的模锻件[2-4]"由于液态模锻成型充填过程平稳,且在高压下凝固成形,得到的产品内部组织均匀、致密[5]"不用浇冒口系统,金属的利用率可以达到100%"液态模锻工艺能够成形重要的结构件,且零件的性能能够满足使用要求,这方面的研究受到越来越多的关注"鉴于模锻成形铝合金件存在浇注不足、缩孔、疏松等缺陷,本文以某火箭发动机阀门壳体为例,研究零件的液态模锻成形工艺,为铝合金薄壁壳体件的成形研究拓宽思路"1实验1.1壳体件介绍某火箭发动机的阀门壳体件如图1和图2所收稿日期:2020-07-24基金项目:安徽省教育厅高校自然科学重点项目(KJ2019A0892);安徽省高校优秀拔尖人才培育资助项目(GXGNFX2019071)(安徽三联学院科研基金重点课题(KJJD2018007)作者简介:牛海侠(1979-),女,山东菏泽人,副教授,硕士,主要从事铝合金半固态成形技术方面的研究。
哈尔滨工业大学科技成果——大型铝合金制件液态模锻精密成形技术

哈尔滨工业大学科技成果——大型铝合金制件液态
模锻精密成形技术
项目简介
随着我国交通运输业,武器装备向现代化、高速化方向发展,轻量化要求日趋强烈,特别是轻量化程度要求高的飞机、航天器、高速列车、汽车、舰艇、火炮、坦克以及机械设备等重要受力部件和结构件,需要大量使用铝合金锻件和模锻件以替代原来的钢结构件。
而传统的铸造和模锻技术已不能完全满足这些铝合金关键零部件的制造需求和使用性能,正是这种需求使得大型铝合金制件液态模锻精密成形技术的研究。
成型制件
2000年哈尔滨工业大学液态模锻课题组开展了大型铝合金负重轮液态模锻精密成形技术的研究工作,2003年成功地实现了铝合金负重轮本体与局部(钢质材料或复合材料)耐磨增强一体化精密成形,各项静态和里程试验性能指标均达到设计要求,与钢制轮盘相比,质
量减轻了40%,经检验后取得成功应用。
该成形技术操作方便,成本低,产品综合性能良好,填补了国内液态模锻生产铝合金负重轮的空白。
成形技术的推广应用。
ZL102合金液态模锻工艺的研究

考察指标
拉伸强度 布氏硬度 断后伸长率 断面收缩率 干摩擦磨损率 油摩擦磨损率
RA
8.768 426 4.367 5 0.008 391 2.417 112 0.012 987 0.002 906
RB
13.706 39 3.357 5 0.044 274 2.557 998 0.019 819 0.003 608
!b / MPa HB # ( %) " ( %) r 干 ( %) r 油 ( ‰)
液锻前 158.454 7 46.25 2.80 9.73 0.082 617 0.021 4 液锻后 182.326 0 60.10 4.72 9.16 0.070 610 0.019 2
各种缺陷, 而且还使组织得到细化。 晶粒越细, 晶界所占的比例越大, 位错运动的
一次枝晶臂间距减小为 62.0 μm, 二次枝晶臂间
距为 46.6 μm, 可见, 液态模锻使组织明显得到细
化, 从而明显改善合金的力学性能。
( a) 压力 0KN
(b) 压力 60 kN
( a) 压力 0KN
(b) 压力 60 kN
50 "m
100 "m
图 3 不同工艺条件下 α-Al 的拉伸断口形貌( 模具预热 温度: 380 ℃, 合金浇注温度: 660 ℃)
图 2 不同工艺条件下 α-Al 的形貌 (模具预热温度 380 ℃, 合金浇注温度 660 ℃) ×70
Fig.2 Appearances ofα-Al at different process ( pouring temperature at 660 ℃, die preheat temperature
在铝合金铸件生产中, 普通的砂型铸造、压力 铸造、金属型铸造等工艺应用较多, 生产成本较 低, 但容易产生缩孔、疏松等铸造缺陷, 力学性能 较低, 达不到质量要求。液态模锻是一项先进的 加工工艺, 属于一种铸锻交叉的精密成形制造技 术。通过液态模锻不仅可以消除铸造组织中的缩 孔、疏松等缺陷, 还可以改善制件的微观组织和力 学性能, 同时还可以降低制件、尤其是复杂形状制 件的制造成本, 在国内外得到广泛应用[1-3]。本文通 过正交试验和极差分析方法设计试验, 探索液态 模锻工艺对铝合金微观组织和力学性能的影响。
铝合金薄壁壳体件液态模锻塑性变形过程的数值模拟

f s = mk = m σ / 3
(2)
式中ꎬm 为剪切摩擦系数ꎻk 为材料的剪切屈服
强度ꎮ
为了简化计算并得到一般规律ꎬ模拟中将壳体
件抽象为筒形件ꎬ对简单筒形零件进行反向挤压ꎬ
研究零件在不同的成形压力下致密度变化的一般
规律ꎬ再通过规律对壳体件进行验证ꎮ
1. 2 初始条件的设置
创建了材料的流动应力模型和剪切模型ꎬ在模
应用最广ꎮ 液态模锻的成形原理是将熔融的液态
合金浇注入模具型腔ꎬ通过上模施加一定的压力ꎬ
促进合金液体的充填ꎬ在一定的压力下合金凝固ꎬ
图 1 薄壁壳体示意图
产生 塑 性 变 形ꎬ 得 到 组 织 结 构 致 密 的 产 品 的 过
程 [5] ꎮ 由于液态合金在高压下凝固产生变形ꎬ因
①
收稿日期:2020 - 08 - 27
第 38 卷 第 5 期 佳 木 斯 大 学 学 报 ( 自rnal of Jiamusi University ( Natural Science Edition)
Vol. 38
Sep.
No. 5
工艺却不够成熟稳定ꎮ 为研究液态模锻过程中铝合金薄壁壳体件的塑性变形过程ꎬ应用有限元
分析分析软件 DEFORMꎬ对零件塑性变形阶段进行了仿真计算ꎬ针对模拟问题进行了零件质量
均匀化改进ꎬ采用复合加载工艺保证了零件使用性能上的要求ꎮ
关键词: 薄壁类零件ꎻ液态模锻ꎻ有限元分析ꎻ致密度
中图分类号: TG146. 3 文献标识码: A
拟软件的前处理器中ꎬ还要对液态模锻的温度、材
料的参数以及边界条件等进行设定ꎮ 主要设置如
下:
(1 ) 坯 料 的 温 度 设 定 为 500℃ ꎬ 模 具 温 度
铝合金的液态模锻成形
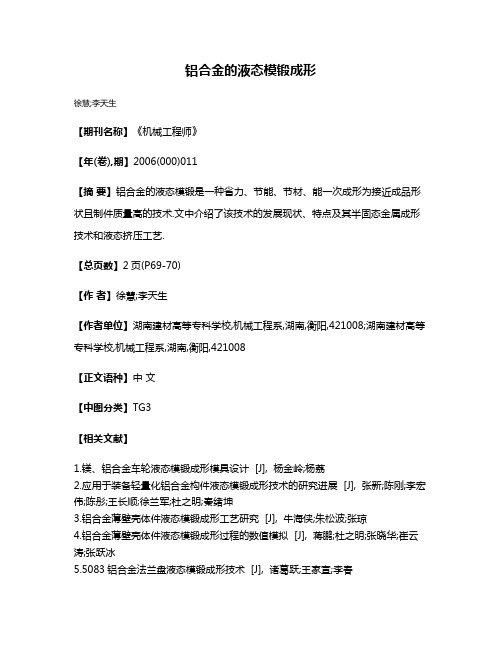
铝合金的液态模锻成形
徐慧;李天生
【期刊名称】《机械工程师》
【年(卷),期】2006(000)011
【摘要】铝合金的液态模锻是一种省力、节能、节材、能一次成形为接近成品形状且制件质量高的技术.文中介绍了该技术的发展现状、特点及其半固态金属成形技术和液态挤压工艺.
【总页数】2页(P69-70)
【作者】徐慧;李天生
【作者单位】湖南建材高等专科学校,机械工程系,湖南,衡阳,421008;湖南建材高等专科学校,机械工程系,湖南,衡阳,421008
【正文语种】中文
【中图分类】TG3
【相关文献】
1.镁、铝合金车轮液态模锻成形模具设计 [J], 杨金岭;杨荔
2.应用于装备轻量化铝合金构件液态模锻成形技术的研究进展 [J], 张新;陈刚;李宏伟;陈彤;王长顺;徐兰军;杜之明;秦绪坤
3.铝合金薄壁壳体件液态模锻成形工艺研究 [J], 牛海侠;朱松波;张琼
4.铝合金薄壁壳体件液态模锻成形过程的数值模拟 [J], 蒋鹏;杜之明;张晓华;崔云涛;张跃冰
5.5083铝合金法兰盘液态模锻成形技术 [J], 诸葛跃;王家宣;李春
因版权原因,仅展示原文概要,查看原文内容请购买。
铝合金的液态模锻成形
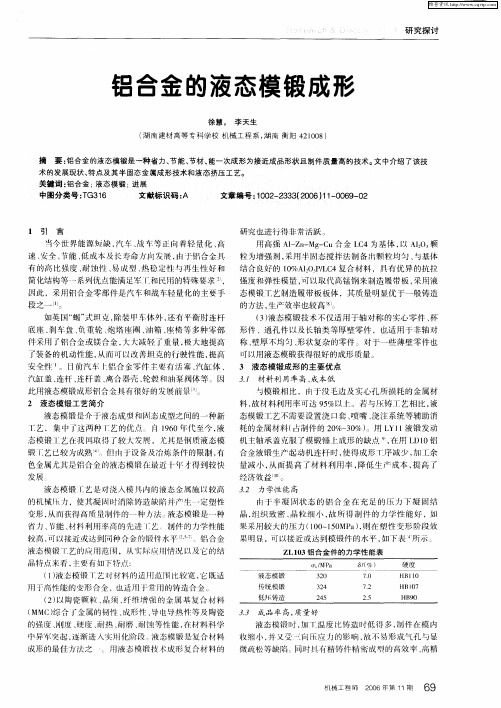
速、 安全 、 节能 、 低成本及长寿命 厅向发展 , 由于锌 合金具 粒为增强剂 , 1 采用半固态搅拌法制备 颗粒均匀 、 与基体
简化结构等 一 系列优点能满 足军 I 和民用的特殊要求 2 l ,
因此 ,采 用钒 合 金零 部 件 是 汽 车和 战 车轻 量化 的主要 手
段 之一 …。
如英国“ ” 坦 兜, 蝎 式 除装 甲车体 外 , 还有 平 衡肘 连 杆 底 座 、 车 盘 、 蕈轮 、 塔 座 圈 、 箱 、 椅 等 多种 零 部 刹 负 炮 { 南 座 件 采用 钒 合金 或镁 合 金 , 大减轻 重 最 , 大 地 提 高 大 极
Z 0 L1 3铝 合 金 件 的 力 学 性 能 表
较高, 可以接近或达到同种 合金的锻件水平I。.铝合金 .
液态 模锻 ] 艺的 用 范 隔 ,从 实际 J 川情 况 以及它 的结 一 | f
晶特 点来 看 , 要有 如 下特 点 : 主 ( ) 念模 锻 _艺 对 材 料 的适 川 范 闹 比较 宽 , 既 通 1液 『 它
的强 度 、 度 、 度 、 刚 硬 耐热 、 磨 、 蚀 等性 能 , 材料 科 学 耐 耐 在 中异 车突 起 , 进 入实 化阶段 液 态模 锻是 复 合材 料 逐渐 成形 的最 佳 方法 之 ・ 液 态模 锻 技 术 成形 复 合材 料 的 。用 液态 模 锻 时 , T温 度 比铸 造 时 低 得 多 , 件 住模 内 加 制 收缩 小 , 又受 _ 甸压应 力 的 影响 , 不 易 形成 气 孔 与 并 故
的方法 , 生产 效 率也 较 高 - s ] 。 () 3 液态 模 锻技 术 不 仅适 用 于 轴 对 称 的实 心 零 件 、 杯 形 件 、通 孔件 以及 长轴 类 等 厚 壁零 件 ,也 适 用 于 非 轴 对 称、 壁厚 不 均 匀 、 状 复杂 的零 件 。对 于 一 些 薄壁 零 件 也 形 叮以用 液 态模 锻 获得 很好 的成形 质量 。
文献综述——铝挤压

基于数值模拟研究铝合金管材挤压过程中的金属流动规律及模具优化设计文献综述1.铝合金分类及铝合金挤压现状纯铝的密度为ρ=2.7g/cm3,约是铁的1/3,熔点为660℃,铝是面心立方结构,故具有很高的塑性(δ:32~40%,ψ:70~90%),易于加工,可制成各种型材、板材,并且具有极好的抗腐蚀性能;但是纯铝的强度很低,退火状态σb 值约为8kgf/mm2,故不宜作结构材料。
通过长期的生产实践和科学实验,人们逐渐以加入合金元素及运用热处理等方法来强化铝,这就得到了一系列的铝合金。
添加一定元素形成的合金在保持纯铝质轻等优点的同时还能具有较高的强度,σb 值分别可达24~60kgf/mm2。
这样使得其“比强度”(强度与比重的比值σb/ρ)胜过很多合金钢,成为理想的结构材料,铝合金密度低,但强度比较高,接近或超过优质钢,塑性好,可加工成各种型材,具有优良的导电性、导热性和抗蚀性。
近几十年来发展十分迅速,在国民经济和人民生活各领域获得了十分广泛的应用,成为仅次于钢材的第二大金属材料。
2002~2010年间,全国铝合金产量如表1所示。
表1 2002-2010年中国铝合金产量及增长速度统计从表中可以看出,2002-2010年间,全国的铝合金产量呈上升趋势。
随着加工技术,产品性能的提高,铝合金的产量将继续增大,其应用必定会更加广泛。
1.1铝合金的分类铝合金分两大类:铸造铝合金,在铸态下使用;变形铝合金,能承受压力加工。
可加工成各种形态、规格的铝合金材。
主要用于制造航空器材、建筑用门窗等。
铝合金挤压所用的材料一般均为变形铝合金。
1.1.1铸造铝合金铸造铝合金(cast aluminium alloy)是指适于熔融状态下充填铸型获得一定形状和尺寸铸件毛坯的铝合金,可按成分中铝以外的主要元素硅、铜、镁、锌分为四类,代号编码分别为100、200、300、400。
(1)铝硅系合金,也叫“硅铝明”或“矽铝明”。
有良好铸造性能和耐磨性能,热胀系数小,在铸造铝合金中品种最多,用量最大的合金,含硅量在10%~25%。
- 1、下载文档前请自行甄别文档内容的完整性,平台不提供额外的编辑、内容补充、找答案等附加服务。
- 2、"仅部分预览"的文档,不可在线预览部分如存在完整性等问题,可反馈申请退款(可完整预览的文档不适用该条件!)。
- 3、如文档侵犯您的权益,请联系客服反馈,我们会尽快为您处理(人工客服工作时间:9:00-18:30)。
毕业论文文献综述
机械设计制造及其自动化
铝合金液态模锻成型过程的可视化
1 铝合金液态模锻成型过程的可视化的意义
当今世界能源短缺,汽车、战车等正朝着轻量化、高速、安全、节能、低成本及长寿命方向发展,采用轻合金是汽车和兵器轻量化的主要手段之一。
铝合金具有高比强度、耐锈蚀、热稳定性好、易成型、再生性好和简化结构等一系列优点,能满足汽车工业的特殊要求。
目前汽车上铝合金零件主要有活塞、汽缸体、汽缸盖、连杆、连杆盖、离合器壳、车轮、油泵阀体等。
这些铝合金零件的生产方法多采用压力铸造、低压铸造及普通模锻等常规工艺,它具有材料及燃料消耗较高、设备投资大、劳动强度大、制作成本高等缺点。
零件成型的常规方法有两种:(l)液态成型即各种铸造工艺,如金属铸造、压力铸造、低压铸造等;(2)固态成型即用固体坯料通过诸如模锻、压力加工、切削加工等工艺加工成所需形状的零件。
液态模锻则是介于这两种工艺之间的一种崭新的工艺,集中了它们的优点[2]。
铝合金液态模锻成型过程的可视化可以帮助我们更好的了解不同参数对模锻成型过程的影响,熟悉液态模锻的工作原理以及掌握一些基本的可视化软件的操作,并且为计算机模拟液态模锻实验提供依据。
2 铝合金液态模锻成型过程及可视化的研究现状
2.1 铝合金液态模锻的基本原理
液态模锻工艺其实质是把液态金属直接浇入模具型腔内,然后在一定时间内以一定的压力作用于半熔融或半凝固的金属上,使之成形,并在此压力下结晶私塑性流动,从而获得毛坯或零件的一种金属加工方法[13]。
铝合金液态模锻工艺的应用范围,从国内外实际应用情况以及它的结晶特点来看,主要有如下特点:
(1)液态模锻工艺对材料选择范围较宽。
它既适用于铸造合金,也适用于变形合金。
(2)纤维强化金属具有质量轻、强度高、耐磨、耐高温等特点。
现在已经进行了包含碳、碳化硅、氧化铝等高强度长短纤维铝合金的汽车零件研究开发工作。
作为铝合金强化材料很有发展前途。
(3)液态模锻技术不仅适用于轴对称的实心零件、杯形件、通孔件以及长轴类等厚
壁零件,也适用于非轴对称、壁厚不均匀、形状复杂的零件[2-3]。
4.2 铝合金液态模锻成型的研究情况
(1)工艺简介
液态模锻是介于液态成型和固态成型之间的一种新工艺,集中了这两种工艺的优点。
之前,铝合金管的通常是运用落后的热铸造技术成型的[12]。
自1960年代至今,液态模锻工艺在我国取得了较大发展,尤其是钢质液态模锻工艺已较为成熟。
但由于设备及冶炼条件的限制,有色金属尤其是铝合金的液态模锻在最近一年才得到较快发展[4]。
液态模锻工艺是对浇入模具内的液态金属施以较高的机械压力,使其凝固时消除铸造缺陷并产生一定塑性变形,从而获得高质量制件的一种方法。
液态模锻是一种省力、节能、材料利用率高的先进工艺。
制件的力学性能较高,可以接近或达到同种合金的锻件水平[5-8]。
(2)半固态金属成形技术
半固态金属成形技术作为一种新兴复合材料加工技术引起了广泛的关注[9,10],它的研究起源于1970年代。
一般而言,金属在静止状态下结晶时,最先凝固的部分是树枝状长大,形成网状结构,残余液态金属分布于树枝结晶体之间,这种半固态金属的流动性差,对成形不利。
1970年代初,麻省理工学院的研究人员发现,在金属凝固时加以搅拌,可以将产生的树枝状初晶破碎并分散到未凝固的残余液体金属中去,凝固组织山通常的树枝状晶体变成球状的等轴晶体,成为变形抗力较低、具有良好流动性的金属糊状物,并可以很方便地施以各种后续成形加工。
半固态成形技术有如下特点:显微组织细化,大大减轻了内部缺陷和偏析等;半固态金属变形抗力大大降低,并可以制造出近净成形制品;利用半固态糊状金属的高粘性,可以容易并且均匀地混入异种材料和比重差大的金属,从而制造新型复合材料和新成分合金。
(3)液态挤压工艺
液态挤压是在液态模锻研究的基础上,结合热挤压变形的特点而发展起来的一种液态金属成形工艺。
其成形过程为:将液态金属直接浇入挤压桶内,借助挤压冲头对未凝固的或准凝固金属施以高压,使其在压力下发生流动、结晶、凝固过程,随后,挤压成形模口处的准凝固金属经受断面缩减的大塑性变形,一次成形出管、棒、型材类制品。
利用液态挤压工艺也可以直接制备金属基复合材料管、棒、型材类制件,由此突破了现有复合材料成形方法均需二次变形,即先成形出复合材料坯体,再经挤、轧等工艺制成管、棒型材的限制,可以减少成形工序,降低成本,有望成为成形高性能复合材料管、棒、
型材的一条新途径[11]。
3.可视化的研究介绍
数据可视化(Data Visualization)的概念首先来自科学计算可视化,科学家们不仅需要通过图形图像分析计算机算出的数据,而且需要了解计算过程中数据的变化。
随着计算机技术的发展,数据可视化的概念已大大扩展,不仅包括科学计算数据的可视化,而且包括工程数据和测量数据的可视化。
现代的数据可视化技术指的是运用计算机图形学和图像处理技术,将数据转换为图形或图像在屏幕上显示出来,并进行交互处理的理论、方法和技术。
它涉及到计算机图形学、图像处理、计算机辅助设计、计算机视觉及人机交互技术等多个领域[1]。
3 铝合金液态模锻成型的发展趋势
目前,汽车、摩托车等的零件向轻量化方向发展,世界各国逐渐用铝合金代替钢质材料的系统工程研究是今后长时间需要解决的问题。
铸造技术和模锻技术有机结合成先进的液态模锻成形工艺.简化了生产工序、提高了产品质量和合格率、减少了设备投资,降低了产品成本,特别适合于形状复杂、带有多孔或台阶形状制件的成形,是一种具有较广的适用性、较大推广价值的很有发展前途的新工艺。
参考文献
[1] 赵国庆, 黄荣怀, 陆志坚. 知识可视化的理论与方法[J]. 开放教育研究, 2005, 11
(1): 23-27 .
[2]洪慎章, 曾振鹏. 国内外铝合金液态模锻的发展与展望[J]. 机械制造, 1999 (3): 12-13.
[3] 韦丽君, 马风雷,李任江. 液态模锻在铸铝合金中的应用研究[J].材料工程,2003(7).
[4]徐慧, 李天生. 铝合金的液态模锻成形[J]. 机械工程师, 2006, (17).
[5] 洪慎章,曾振鹏.国内外铝合金液态模锻的发展与展望「J].机械制造,1999 (3) :12- 13.
[6]罗守靖,何绍元,王尔德,等.钢质液态模锻[M].哈尔滨:哈尔滨工业大学出版社.
1990:4-25.
[7]上海交通大学锻压教研组.液态模锻[M].北京:国防工业出版社,1981.
[8]齐丕襄.挤压铸造[M].北京:国防工业出版社,1984.
[9]蒋鹏,贺小毛,张秀峰.半固态金属成形技术的研究概况[J].塑性工程学报,1998. 5
(3) :1-7.
[10]蒋鹏,贺小毛,张秀峰.半固态成形在工业生产中的应用现状与前景[J].模具技术,
1998 (5) : I S- 23.
[11]Qi Le- Hua, Hou Jun- Jie, Cui Pei- Ling, He- Jun Li. Research on Prediction of the
Processing Parameters of Liquid Extrusion by BP Network [J]. Journal of Material Processing Technology, 1999 (95) :232- 237.
[12]Yin F, Wang G.X, Hong S Z et al. Technological study of liquid die forging for the
aluminum alloy connecting rod of an air compressor. [J]. Journal of Material Processing Technology, 2003, 139(1-3) :462-464.
[13]Murali S, Yong M S. Liquid forging of thin Al-Si structures [J]. Journal of Materials
Processing Technology, 2010, 210(10): 1276~1281.。