常见双金属复合管及生产方法
双金属复合管制作工艺
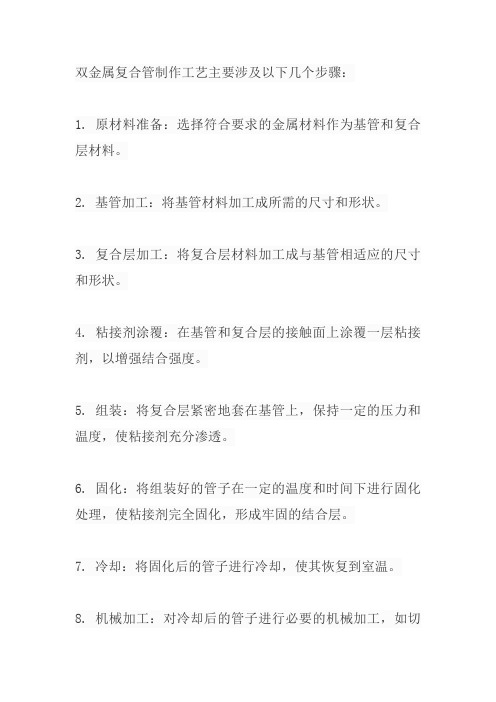
双金属复合管制作工艺主要涉及以下几个步骤:
1. 原材料准备:选择符合要求的金属材料作为基管和复合层材料。
2. 基管加工:将基管材料加工成所需的尺寸和形状。
3. 复合层加工:将复合层材料加工成与基管相适应的尺寸和形状。
4. 粘接剂涂覆:在基管和复合层的接触面上涂覆一层粘接剂,以增强结合强度。
5. 组装:将复合层紧密地套在基管上,保持一定的压力和温度,使粘接剂充分渗透。
6. 固化:将组装好的管子在一定的温度和时间下进行固化处理,使粘接剂完全固化,形成牢固的结合层。
7. 冷却:将固化后的管子进行冷却,使其恢复到室温。
8. 机械加工:对冷却后的管子进行必要的机械加工,如切
削、磨削等,以达到最终的尺寸和形状要求。
9. 检验:对成品管子进行外观、尺寸、结合强度等方面的检验,确保产品质量。
通过以上工艺流程,可以制得具有优良性能的双金属复合管,广泛应用于各种工程领域。
复合管生产工艺和方法介绍

复合管主要的生产工艺方法有热轧复合方法、热挤压复合法、铸造复合方法、爆炸焊接复合方法、组合式双金属复合管生产方法、激光包覆法等。
复合管已经在腐蚀性较强的石油、石化企业、核工业以及医药、食品加工等领域获得广泛认同。
复合管是近10年发展较快的一种工程管道,品种、功能繁多,性能优越,形成了比较成熟的工艺技术,并且已经投产。
接下来,我们来了解一下复合管产品性能以及如何制备。
复合管管层之间通过各种变形和连接技术形成紧密结合,从而使两种材料结合成一体而制成的一种新型金属复合管材。
其一般设计原则是基材满足管道设计许用应力,复层抵抗腐蚀或磨损等。
复合管兼有基层和复层的所有优点,相对于整体合金管能有效降低成本,而且在对整体合金管具有应力腐蚀开裂敏感性的氯化物和(或)酸性环境中复合管可以提高安全性和可靠性。
随着工业技术的发展,环境介质的复杂化,以及竞争的加剧,许多行业对金属管材综合性能的要求越来越高,因而复合管及其生产技术得到迅速发展。
对于强腐蚀、高磨损、高工作压力环境下使用的流体管道,通常采用高品质的不锈钢或高合金含量的无缝钢管,这类管材由于大量添加合金元素,其价格是一般普通无缝钢管的几倍或几十倍。
多年来,管材用户和生产商一直在努力寻求通过不同金属的复合,从而获得一种既能满足苛刻的使用环境,又价廉物美的高性能复合管材。
复合管能实现材料的优势互补,节省合金元素,降低工程费用,在保证原基管各项性能的基础上,提高了管道的耐腐蚀性、耐磨性,延长了管道的使用寿命,是纯不锈钢管、铜管或其他耐腐蚀性合金管的替代产品。
目前双金属复合管的生产方法主要包括冷成型法、热成型法、离心铸造法、离心铝热剂法、爆炸焊成型法、电磁成型法等等。
离心铸造+热挤压(热挤压+冷轧)法“离心铸造+热挤压”是一种新的复合管短流程制备方法,通过离心铸造生产空心复合管坯,然后加热、热挤压或热挤压冷轧,以及后续热处理等工序,获得成品复合管。
它有效整合了离心铸造和热挤压两种方法的优点,缩短了生产工序,并实现了复合界面的完全冶金结合。
双金属复合管技术
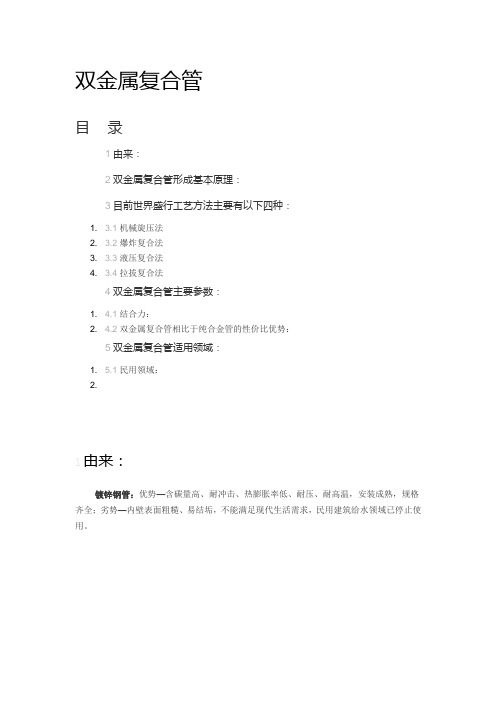
双金属复合管目录1由来:2双金属复合管形成基本原理:3目前世界盛行工艺方法主要有以下四种:1. 3.1 机械旋压法2. 3.2 爆炸复合法3. 3.3 液压复合法4. 3.4 拉拔复合法4双金属复合管主要参数:1. 4.1 结合力:2. 4.2 双金属复合管相比于纯合金管的性价比优势:5双金属复合管适用领域:1. 5.1 民用领域:2.1由来:镀锌钢管:优势—含碳量高、耐冲击、热膨胀率低、耐压、耐高温,安装成熟,规格齐全;劣势—内壁表面粗糙、易结垢,不能满足现代生活需求,民用建筑给水领域已停止使用。
薄壁不锈钢管:优势—304不锈钢制成,耐腐蚀、表面光滑不结垢,综合性能优越,但价格昂贵;双金属复合钢管:是将镀锌钢管或焊管、无缝钢管和壁厚更薄的不锈钢管强力嵌合在一起的新型复合给水管材,也是一种更理想的管道升级换代产品。
它保留了两种不同材料内在的优点,互补了它们内在的不足,并且沿用了镀锌钢管传统成熟的安装方式和工艺,因此在使用中方便、可靠、卫生、安全。
跟据基管与内衬管选材的不同,以及制造工艺的提升,已有不少厂家生产的双金属复合管广泛应用于油田、化工、电力等工业领域,其适用范围越来越广泛,带来的经济、环境、社会效益也更加明显。
双金属复合管内外层的的结构说明2双金属复合管形成基本原理:双金属复合钢管基本原理:外基管负责承压和管道刚性支撑的作用,内衬管承担耐腐蚀的作用。
外基管可以根据输送介质的流量和压力要求,选用不同通径和壁厚的碳钢管材。
热镀锌钢管、直缝焊管、螺旋管、低中压流体输送用无缝钢管、高压锅炉、石油裂化用无缝管钢管、管线管等。
直径可从φ20-φ1020mm,壁厚可从2.5-50mm。
内衬管可以根据输送介质化学成分,选用不同的耐腐蚀合金。
可以是奥氏体不锈钢304、304L、316、316L、铜基合金、镍基合金、哈氏合金、钛、钛合金、双相不锈钢等新型高耐腐蚀合金材料。
内衬管壁厚可以根据使用寿命和焊接工艺的要求从0.3-4mm。
双金属复合管复合工艺
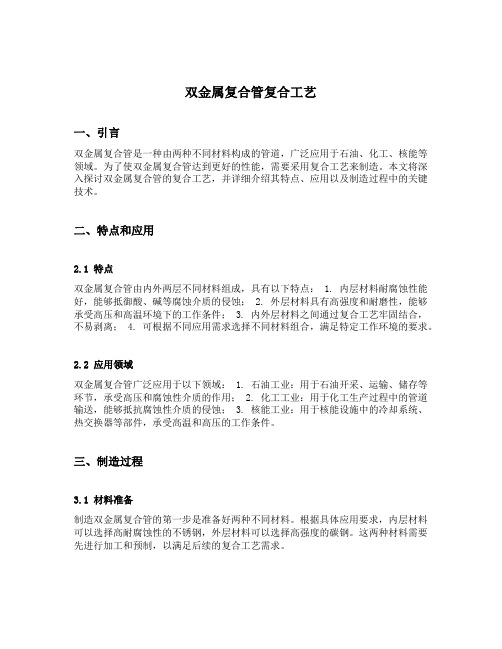
双金属复合管复合工艺一、引言双金属复合管是一种由两种不同材料构成的管道,广泛应用于石油、化工、核能等领域。
为了使双金属复合管达到更好的性能,需要采用复合工艺来制造。
本文将深入探讨双金属复合管的复合工艺,并详细介绍其特点、应用以及制造过程中的关键技术。
二、特点和应用2.1 特点双金属复合管由内外两层不同材料组成,具有以下特点: 1. 内层材料耐腐蚀性能好,能够抵御酸、碱等腐蚀介质的侵蚀; 2. 外层材料具有高强度和耐磨性,能够承受高压和高温环境下的工作条件; 3. 内外层材料之间通过复合工艺牢固结合,不易剥离; 4. 可根据不同应用需求选择不同材料组合,满足特定工作环境的要求。
2.2 应用领域双金属复合管广泛应用于以下领域: 1. 石油工业:用于石油开采、运输、储存等环节,承受高压和腐蚀性介质的作用; 2. 化工工业:用于化工生产过程中的管道输送,能够抵抗腐蚀性介质的侵蚀; 3. 核能工业:用于核能设施中的冷却系统、热交换器等部件,承受高温和高压的工作条件。
三、制造过程3.1 材料准备制造双金属复合管的第一步是准备好两种不同材料。
根据具体应用要求,内层材料可以选择高耐腐蚀性的不锈钢,外层材料可以选择高强度的碳钢。
这两种材料需要先进行加工和预制,以满足后续的复合工艺需求。
3.2 复合工艺双金属复合管的复合工艺一般包括以下几个步骤: 1. 清洁处理:将内外层材料进行表面清洁处理,以去除油污和氧化物等杂质,保证复合牢固性。
2. 巨型焊接:采用巨型焊接设备,将内层材料与外层材料进行焊接,形成初始复合管。
3. 冷拔工艺:将初始复合管进行冷拔加工,通过拉伸和压缩等力学变形,使复合管形成完整且均匀的形态。
4. 热轧工艺:对冷拔加工后的复合管进行热轧处理,以进一步提高其机械性能和表面质量。
5. 热处理:将热轧后的复合管进行热处理,消除内应力,提高材料的结构和性能。
3.3 表面处理和测试制造完成的双金属复合管需要进行表面处理,以防止腐蚀和氧化。
复合管生产工艺和方法介绍

复合管主要的生产工艺方法有热轧复合方法、热挤压复合法、铸造复合方法、爆炸焊接复合方法、组合式双金属复合管生产方法、激光包覆法等。
复合管已经在腐蚀性较强的石油、石化企业、核工业以及医药、食品加工等领域获得广泛认同。
复合管是近10年发展较快的一种工程管道,品种、功能繁多,性能优越,形成了比较成熟的工艺技术,并且已经投产。
接下来,我们来了解一下复合管产品性能以及如何制备。
复合管管层之间通过各种变形和连接技术形成紧密结合,从而使两种材料结合成一体而制成的一种新型金属复合管材。
其一般设计原则是基材满足管道设计许用应力,复层抵抗腐蚀或磨损等。
复合管兼有基层和复层的所有优点,相对于整体合金管能有效降低成本,而且在对整体合金管具有应力腐蚀开裂敏感性的氯化物和(或)酸性环境中复合管可以提高安全性和可靠性。
随着工业技术的发展,环境介质的复杂化,以及竞争的加剧,许多行业对金属管材综合性能的要求越来越高,因而复合管及其生产技术得到迅速发展。
对于强腐蚀、高磨损、高工作压力环境下使用的流体管道,通常采用高品质的不锈钢或高合金含量的无缝钢管,这类管材由于大量添加合金元素,其价格是一般普通无缝钢管的几倍或几十倍。
多年来,管材用户和生产商一直在努力寻求通过不同金属的复合,从而获得一种既能满足苛刻的使用环境,又价廉物美的高性能复合管材。
复合管能实现材料的优势互补,节省合金元素,降低工程费用,在保证原基管各项性能的基础上,提高了管道的耐腐蚀性、耐磨性,延长了管道的使用寿命,是纯不锈钢管、铜管或其他耐腐蚀性合金管的替代产品。
目前双金属复合管的生产方法主要包括冷成型法、热成型法、离心铸造法、离心铝热剂法、爆炸焊成型法、电磁成型法等等。
离心铸造+热挤压(热挤压+冷轧)法“离心铸造+热挤压”是一种新的复合管短流程制备方法,通过离心铸造生产空心复合管坯,然后加热、热挤压或热挤压冷轧,以及后续热处理等工序,获得成品复合管。
它有效整合了离心铸造和热挤压两种方法的优点,缩短了生产工序,并实现了复合界面的完全冶金结合。
常见双金属复合管及生产方法
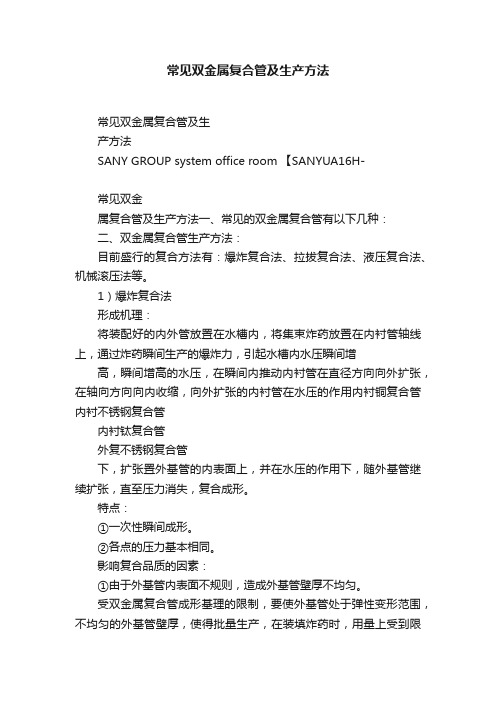
常见双金属复合管及生产方法常见双金属复合管及生产方法SANY GROUP system office room 【SANYUA16H-常见双金属复合管及生产方法一、常见的双金属复合管有以下几种:二、双金属复合管生产方法:目前盛行的复合方法有:爆炸复合法、拉拔复合法、液压复合法、机械滚压法等。
1)爆炸复合法形成机理:将装配好的内外管放置在水槽内,将集束炸药放置在内衬管轴线上,通过炸药瞬间生产的爆炸力,引起水槽内水压瞬间增高,瞬间增高的水压,在瞬间内推动内衬管在直径方向向外扩张,在轴向方向向内收缩,向外扩张的内衬管在水压的作用内衬铜复合管内衬不锈钢复合管内衬钛复合管外复不锈钢复合管下,扩张置外基管的内表面上,并在水压的作用下,随外基管继续扩张,直至压力消失,复合成形。
特点:①一次性瞬间成形。
②各点的压力基本相同。
影响复合品质的因素:①由于外基管内表面不规则,造成外基管壁厚不均匀。
受双金属复合管成形基理的限制,要使外基管处于弹性变形范围,不均匀的外基管壁厚,使得批量生产,在装填炸药时,用量上受到限制。
药量大了,瞬间冲击波大,外基管易发生永久变形,甚至不安全,使得结合力反而下降;药量小了,冲击力小,内衬管达不到一次性充分塑性变形,导致双金属复合管结合力小。
通常为0.5MPa左右。
由于爆炸成形工艺的特点,导致内衬管轴向方向向内收缩。
为了保证管口整圆,不得不进行二次校正。
②由于结合力小,使得内外管环状结合面间隙大,内衬管在管端焊接处,将反复承受介质输送过程中,压力交替变化的扭动、折弯,致使连接处出现材料疲劳、开裂,导致耐腐蚀性能下降—(折翘现象)。
③由于装填炸药用量上受到限制,内衬管达不到充分的塑性变形。
由于冲击波产生的反作用力小,内衬管内表面压应力达不到充分的体现,内衬管直缝焊接处仍处于拉应力状态。
致使内衬管表面整体,尤其是直缝焊接处,抗热应力腐蚀的能力下降。
2)拉拔复合法形成机理:将装配好的内外管,通过一个带有锥度的(通常锥度为1:25、1:50),最大轮廓外圆尺寸固定的模具,沿内衬管轴线拉拔前行。
双金属复合管复合工艺
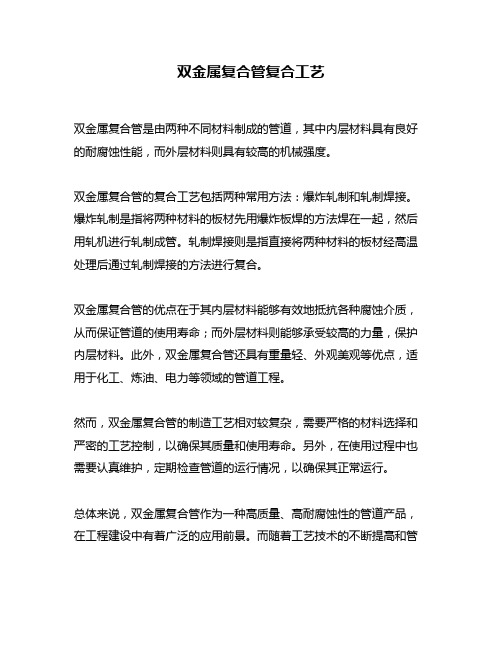
双金属复合管复合工艺
双金属复合管是由两种不同材料制成的管道,其中内层材料具有良好的耐腐蚀性能,而外层材料则具有较高的机械强度。
双金属复合管的复合工艺包括两种常用方法:爆炸轧制和轧制焊接。
爆炸轧制是指将两种材料的板材先用爆炸板焊的方法焊在一起,然后用轧机进行轧制成管。
轧制焊接则是指直接将两种材料的板材经高温处理后通过轧制焊接的方法进行复合。
双金属复合管的优点在于其内层材料能够有效地抵抗各种腐蚀介质,从而保证管道的使用寿命;而外层材料则能够承受较高的力量,保护内层材料。
此外,双金属复合管还具有重量轻、外观美观等优点,适用于化工、炼油、电力等领域的管道工程。
然而,双金属复合管的制造工艺相对较复杂,需要严格的材料选择和严密的工艺控制,以确保其质量和使用寿命。
另外,在使用过程中也需要认真维护,定期检查管道的运行情况,以确保其正常运行。
总体来说,双金属复合管作为一种高质量、高耐腐蚀性的管道产品,在工程建设中有着广泛的应用前景。
而随着工艺技术的不断提高和管
道材料的不断创新,双金属复合管的制造和应用也将得到更进一步的推广和应用。
双金属不锈钢复合管的生产工艺汇总

双金属不锈钢复合管的生产工艺汇总双金属不锈钢复合管是一种由两种不同金属制成的管材,具有不锈钢外层和内层。
它结合了不锈钢的耐腐蚀性和强度以及其他金属的导热性和导电性能,可以广泛应用于石化、化工、船舶、核电站等行业。
以下是关于双金属不锈钢复合管的生产工艺的汇总。
1.材料准备:2.钢管制备:首先需要将不锈钢以及其他金属制成管材。
制备钢管的工艺通常包括热轧、冷拉或焊接等工序,根据不同的材料和要求选择合适的加工方式。
在制备的过程中需要控制好管材的尺寸、表面质量和机械性能等指标。
3.内外钢管的清洗:由于双金属复合管的内外层由不同材料组成,为了保证内外界面的粘接质量,需要对内外钢管进行清洗。
清洗一般使用酸洗、碱洗或电解清洗等方法,以去除管材表面的氧化皮、油污和其他杂质,为后续的粘接工艺做好准备。
4.内外管的粘接:将清洗过的钢管进行内外粘接。
粘接工艺通常采用高温焊接或物理粘接的方式。
高温焊接可以将内外层金属材料熔融并形成强力的粘接。
物理粘接包括滚压法、滚焊法和镶嵌法等,将内层金属塞入外层金属管中,通过一定的力量和变形将两者粘接在一起。
5.精整加工:粘接后的双金属复合管具有一定的粘接接头,需要进行进一步的精整加工。
精整加工可以采用机械加工、切割或抛光等方法。
目的是去除管材表面的凸凹、毛刺和瑕疵等缺陷,获得光滑的表面和合适的尺寸,确保管材的质量和使用性能。
6.性能测试:制备完成的双金属不锈钢复合管需要进行性能测试。
性能测试包括力学性能、耐腐蚀性能、密封性能等方面的测试。
通过对复合管的性能测试可以验证其质量是否符合要求,并对管材进行分类和检验。
7.表面处理:最后对复合管进行表面处理,以提高其耐腐蚀性和装饰性。
表面处理可以采用喷涂、镀锌、抛光等方法。
根据具体的使用要求和环境条件选择合适的表面处理方式。
双金属不锈钢复合管的生产工艺需要进行多个环节的操作和控制,确保制备出质量优良的管材。
生产工艺的每一个环节都需要严格控制,保证各种加工参数、设备、工艺和材料的符合要求。
- 1、下载文档前请自行甄别文档内容的完整性,平台不提供额外的编辑、内容补充、找答案等附加服务。
- 2、"仅部分预览"的文档,不可在线预览部分如存在完整性等问题,可反馈申请退款(可完整预览的文档不适用该条件!)。
- 3、如文档侵犯您的权益,请联系客服反馈,我们会尽快为您处理(人工客服工作时间:9:00-18:30)。
常见双金属复合管及生产方法 一、常见的
双金属复合管
有以下几种:
二、双金属复合管生产方法:
目前盛行的复合方法有:爆炸复合法、拉拔复合法、液压复合法、机械滚压法等。
1)爆炸复合法
形成机理:
将装配好的内外管放置在水槽内,将集束炸药放置在内衬管轴线上,通过炸药瞬间生产的爆炸力,引起水槽内水压瞬间增高,瞬间增高的水压,在瞬间内推动内衬管在直径方向向外扩张,在轴向方向向内收缩,向外扩张的内衬管在水压的作用下,扩内衬铜复合管 内衬不锈钢复合管 内衬钛复合管 外复不锈钢复合管
张置外基管的内表面上,并在水压的作用下,随外基管继续扩
张,直至压力消失,复合成形。
特点:
①一次性瞬间成形。
②各点的压力基本相同。
影响复合品质的因素:
①由于外基管内表面不规则,造成外基管壁厚不均匀。
受双金属复合管成形基理的限制,要使外基管处于弹性变形范围,不均匀的外基管壁厚,使得批量生产,在装填炸药时,用
量上受到限制。
药量大了,瞬间冲击波大,外基管易发生永久
变形,甚至不安全,使得结合力反而下降;药量小了,冲击力
小,内衬管达不到一次性充分塑性变形,导致双金属复合管结
合力小。
通常为0.5MPa左右。
由于爆炸成形工艺的特点,导
致内衬管轴向方向向内收缩。
为了保证管口整圆,不得不进行
二次校正。
②由于结合力小,使得内外管环状结合面间隙大,内衬管在管
端焊接处,将反复承受介质输送过程中,压力交替变化的扭动、折弯,致使连接处出现材料疲劳、开裂,导致耐腐蚀性能下降
—(折翘现象)。
③由于装填炸药用量上受到限制,内衬管达不到充分的塑性变
形。
由于冲击波产生的反作用力小,内衬管内表面压应力达不
到充分的体现,内衬管直缝焊接处仍处于拉应力状态。
致使内
衬管表面整体,尤其是直缝焊接处,抗热应力腐蚀的能力下降。
2)拉拔复合法
形成机理:
将装配好的内外管,通过一个带有锥度的(通常锥度为1:25、1:50),最大轮廓外圆尺寸固定的模具,沿内衬管轴线拉拔前
行。
通过拉拔模具挤压、扩张的方式,将内衬管在直径方向复
合到外基管的内表面上,并通过继续扩张使外基管也处于弹性
变形的范围内。
当外力去除后,内衬管呈塑性变形无法收缩,
外基管处于弹性变形呈收缩趋势,但受内衬管的限制,外基管
内表面强力的嵌合在内衬管的外表面上,复合成形。
特点:
①生产工艺比较简单,价格较便宜。
②复合管内表面圆整度好。
影响品质的因素:
①由于外基管内表面形状不规则,不平高度影响了模具轮廓最
大外圆尺寸全行程的通过。
①拉拔模具最大轮廓是机械加工的整圆,必须沿轴心线平行前
行。
模具与内衬管的材质为硬钢于软钢,在拉拔扩张过程中,
模具嵌入在内衬管内表面中。
当外基管不规则的内表面影响拉
拔模具通过时,会造成拉拔模具轴线与内衬管轴线形成夹角,
扩大了模具最大轮廓直径。
当出现对称的不平高度时,由于作
用在拉拔模具上的力,在360度方向上是对称的,这样就会造成拉拔模具无法避让。
两种现象都会使内衬管受挤压处弯曲变形加大,造成拉拔模具最大轮廓处,切削内衬管表面,引起表面光洁度的破坏,甚至无法通过。
这种状况在复合较大直径的双金属复合管时更为明显。
为了保证表面品质和功效,通常采用减小拉拔模具最大轮廓尺寸,因此复合后的双金属复合管结合力小。
通常仅为0.2~0.3MPa之间。
②由于结合力低使得内外管环状结合面间隙大,内衬管在管端
焊接处将反复承受介质输送过程中,压力交变的扭动、折弯,致使连接处出现材料疲劳、开裂,导致耐腐蚀性能下降—(折翘现象)。
③由于内衬管没有达到充分的塑性变形,内衬管内表面由作用
力与反作用力产生的表面压应力,达不到充分的体现,表面压应力几乎没有反映。
此时,内衬管中直缝焊接处仍处于拉应力状态,因此内衬管表面整体,尤其是直缝焊接处,抗热应力腐蚀能力下降。
另外,采用拉拔工艺,拉拔模具呈直线运动,内衬管表面始终处于拉应力状态,界面非扩散结合,只是依靠对外层进行的冷加工来获得紧配合。
因此冷加工复合管如果遭遇高温就有分层倾向,复合管会因应力释放而失效,这就限制了该冷加工管只能在较低温度的环境中使用。
3)水压复合法
形成机理:
将装配好的内外管完全密封—呈密闭长筒,再将液体注入筒内,逐步加压筒内的液体,使得内衬管逐步的在直径方向向外扩张,在轴向方向向内收缩。
通过连续逐步施压,使得内衬管最终达到塑性变形,外基管仍处于弹性变形范围内,当通过压力表判定内外管已达到塑性变形,外基管处于弹性变形要求时,施放压力,复合形式。
特点:
①逐步加压成形。
②密闭长筒内各点压力相同。
影响复合品质的因素:
①外基管内表面不规则,造成外基管壁厚不均匀。
由于在批量生产过程中,对密闭长筒内的液体作微量调压,控制其最大压力则成为生产过程中的“瓶颈”。
由于液体在微量调节时受调节“滞后特性”以及压力“超调特性”的影响,为了保证外基管不至于产生塑性变形,甚至破裂,
调节时不得不降低施加的压力,尽量避免微量调节。
致使内衬
管达不到充分塑性变形—导致双金属复合管结合力小。
通常
〈0.5Mpa。
由于液压成形工艺的特点,导致内衬管轴向方向向
内收缩。
为了保证管口整圆,不得不进行二次校正。
②由于结合力小,使得内外管环状结合面间隙大,内衬管在管
端焊接处,将反复承受介质输送过程中,压力交替变化的扭动、折弯,致使连接处出现材料疲劳、开裂,导致耐腐蚀性能下降
—(折翘现象)。
4)机械滚压法
形成机理:
内衬不锈钢复合管材的复合技术是根据金属材料的弹塑性变形特性复合而成的。
即利用外基管(碳钢管)弹性变形范围大,利用内衬管(不锈钢管)屈服强度低的特性。
在旋压机具螺旋
进给的挤压下,使内衬管连续局部塑性变形,外基管始终保持
在弹性变形范围之内。
当外力去除后,外基管弹性收缩,内衬
管由于已呈塑性变形无法收缩。
从而达到内衬管外表面强力的
嵌合在外基管的内表面中,复合成型。
滚压复合的优点:
经过螺旋滚压技术对管材内壁进行了滚压,冷作硬化提高了内层金属材料的硬度,从而提高了管材的耐磨性流体的畅通性。
由于滚压模具直径调节为大于基管内径0.3-0.5mm,使内层金属管产生较大的
塑性变形,而外管弹性变形,使内管紧密地贴合在外层管的内壁上,压力消失后基管恢复使基管与内衬管能够以较高的强度结合在一起。