束丝机、绞线的工艺要点及质量标准
束绞工序检验指导书

束绞工序检验指导书工序名称:导电线芯束绞工序生产设备:束线机、绞线机用于检验站名称:工序检验员检验受检特质量特检验项序性重要检验方法性值手段号性区别除实心导体外,各种导体应绞合或束合,绞束合用的单线表面质量应1 束绞线B 目测符合工艺卡片的规定,绞束合后线芯表面要求光滑、紧密、圆整、节距均芯外观匀,无松股、跳股、缺根、挂伤、拉细、氧化及油污等缺陷,排线整齐,工序工作人员要做好首件检验、中间控制和完工检验。
指导书有效日期:注意频次事项1.自检: 100% 检查,开车过程中自检。
结构尺寸单线外径2绞束合节距及方向焊接要3求4收排线5合格证6摆放外径按 GB4909.2 规定测量。
绞合或束绞线芯的单线应均有相同的标称直B 千分径,单线外径,根数应符合相应产品标准的规定。
尺绞束合导体的节距和绞向应符合工艺卡片规定,相邻层的绞向应相反。
C一米节距是指被绞合体沿绞合中心旋转一圈沿产品轴向前进的距离(即绞线中卷尺任意一根单线形成的一个完整螺旋轴向长度),节距比是长度与被绞合的产品外径之比,绞束合节距应采用退扭法或划印法测量。
B 目测对束绞导电线芯的焊接,应按工艺卡片的规定要求进行巡回检验和自检。
绞束线不允许整根焊接。
收排线应整齐、平服、不粘线、不松散不超满。
按照 GB/T3048.4 进行检验,由试验室检验人员按抽样规定进行检验,不合格产品应及时通知车间及有关部门进行处理。
所有绞束制品,应按品种、规定分类进行堆放,并在线盘上挂上标签,注明:品种、型号、规格、重量kg、生产人员、检验人员、日期。
不合格产品应及时隔离处理,经检验合格的导电线芯并挂上合格证,方能流入2.互检:操作工人对上一工序流入的线芯进行检查。
3.工序检验人员专检:(1)首检;(2)巡回检查;(3)成盘 100% 检查。
操作工自检,工序检验员巡回检验。
操作工自检,工序检验员每盘检验由理化试验员按每批不少于1%抽检。
100%检验。
束丝工序操作规程

7、每束完一盘丝材后,应测量一次束丝节距,确保束丝节距一致性。
三、操作要点及注意事项:
1、开机后要加强巡检,看是否有断根、缺根,注意丝材涨力大小和排线情况。
2、收线盘不宜装的过满,一般是外层距侧板边缘至少有5cm,束丝表面不应有油污、毛刺、碰伤、松散、跳股等现象。
4、准备好收线盘及其它工具,裸丝要分规格堆放整齐,做到先领先用,防止氧化。
5、按生产工艺要求,将丝材盘子放到放线架上。
6、根据工艺要求可调配齿轮,符合束丝节距的要求(具体见下表1),绞向一律左向。
表1:高速φ500束丝机齿轮配比表
截面(mm2)
齿轮配比
截面(mቤተ መጻሕፍቲ ባይዱ2)
齿轮配比
0.3
25:38
1.5
32:31
3.2准备好工量具,适用于束线机所用的线盘,并检查单线质量。
4.操作规程
一、开机之前:
1、检查电器设备、电源开关、自动停机等各个部位完好状态,检查操作安全装置是否良好,各传动部分、排线器及滑轮都要加油保养。
2、调整好收线盘及计米装置。
3、用精度为0.001mm千分尺测量裸丝直径及公差(0.15—0.4mm其公差+0.004、0.401—14.00mm,其公差+1%d)严防规格混淆。
束丝机
操作规程
文件编号:LS-JS-04
执行时间:2008年01月01日
1.适用范围
本操作规程适用于在束线机上把根数较多、线径较细的相同线径的圆单线按照同一方向,一次绞合成截面较大的特别柔软的导电线芯的工艺过程。
2.生产范围
标称截面:0.3~6mm2
绞线工序质量控制要求
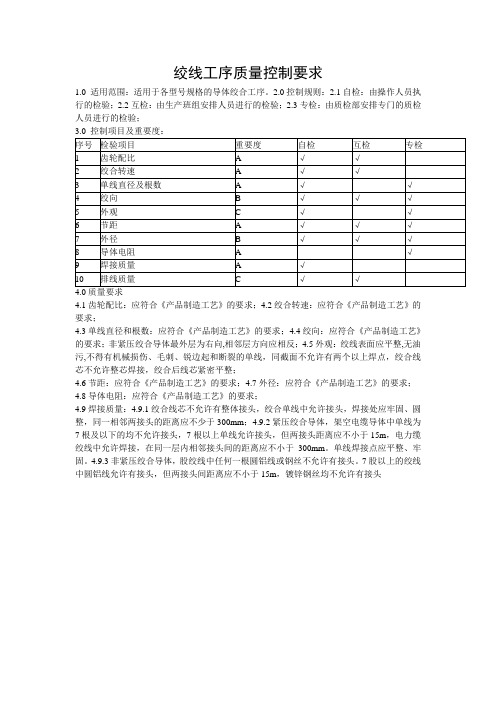
绞线工序质量控制要求
1.0 适用范围:适用于各型号规格的导体绞合工序。
2.0控制规则:2.1自检:由操作人员执行的检验;2.2互检:由生产班组安排人员进行的检验;2.3专检:由质检部安排专门的质检人员进行的检验;
4.1齿轮配比:应符合《产品制造工艺》的要求;4.2绞合转速:应符合《产品制造工艺》的要求;
4.3单线直径和根数:应符合《产品制造工艺》的要求;4.4绞向:应符合《产品制造工艺》的要求;非紧压绞合导体最外层为右向,相邻层方向应相反;4.5外观:绞线表面应平整,无油污,不得有机械损伤、毛刺、锐边起和断裂的单线,同截面不允许有两个以上焊点,绞合线芯不允许整芯焊接,绞合后线芯紧密平整;
4.6节距:应符合《产品制造工艺》的要求;4.7外径:应符合《产品制造工艺》的要求;
4.8导体电阻:应符合《产品制造工艺》的要求;
4.9焊接质量:4.9.1绞合线芯不允许有整体接头,绞合单线中允许接头,焊接处应牢固、圆整,同一相邻两接头的距离应不少于300mm;4.9.2紧压绞合导体,架空电缆导体中单线为7根及以下的均不允许接头,7根以上单线允许接头,但两接头距离应不小于15m,电力缆绞线中允许焊接,在同一层内相邻接头间的距离应不小于300mm。
单线焊接点应平整、牢固。
4.9.3非紧压绞合导体,股绞线中任何一根圆铝线或钢丝不允许有接头。
7股以上的绞线中圆铝线允许有接头,但两接头间距离应不小于15m,镀锌钢丝均不允许有接头。
束丝工艺的要求
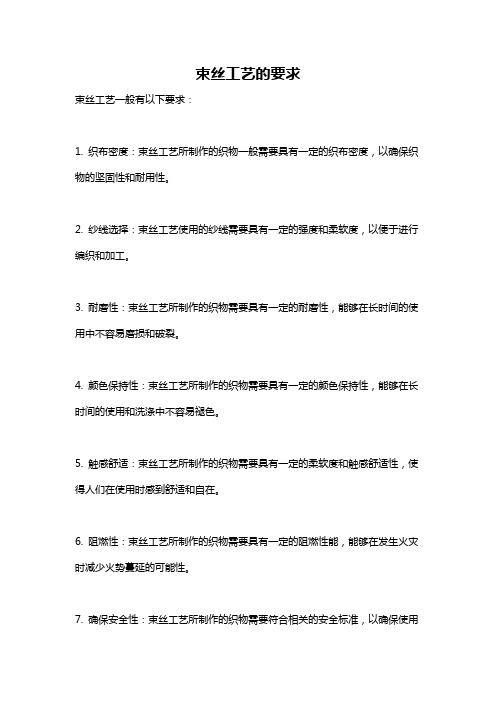
束丝工艺的要求
束丝工艺一般有以下要求:
1. 织布密度:束丝工艺所制作的织物一般需要具有一定的织布密度,以确保织物的坚固性和耐用性。
2. 纱线选择:束丝工艺使用的纱线需要具有一定的强度和柔软度,以便于进行编织和加工。
3. 耐磨性:束丝工艺所制作的织物需要具有一定的耐磨性,能够在长时间的使用中不容易磨损和破裂。
4. 颜色保持性:束丝工艺所制作的织物需要具有一定的颜色保持性,能够在长时间的使用和洗涤中不容易褪色。
5. 触感舒适:束丝工艺所制作的织物需要具有一定的柔软度和触感舒适性,使得人们在使用时感到舒适和自在。
6. 阻燃性:束丝工艺所制作的织物需要具有一定的阻燃性能,能够在发生火灾时减少火势蔓延的可能性。
7. 确保安全性:束丝工艺所制作的织物需要符合相关的安全标准,以确保使用
者的安全。
以上是一些常见的束丝工艺的要求,具体要求会根据不同的应用和需求有所差异。
线束生产各工序注意要点及品质要求

3.1、设备的安装和调试有无问题,这是直接影响端子压接质量的好坏。(例如:模具有没 有松动,端子有没有到位,模具里面有没有杂质等等)
3.2、员工手势的摆放,不正确的手势会造成各种不同的不良品。 3.3、注意安全,压接作业时切勿将手伸入刀模内。
线束生产的工序及品质要求
4、端子各部位名称及功能说明
4.2、在装配时,左手拿起胶壳,右手取一条相配的端子线,在确认端子弹片正常和插入方向后,右手大拇 指及食指固定好端子的和角度和方向,轻力匀速地直接推进胶壳的穴位底部,直到端子弹片钩住胶壳内 的卡点(正常情况下都能听到咔嚓一声,手上有感感觉)方可为插到位。如图1、图2:
图1
图2
线束生产的工序及品质要求 HHCCBB
8、压接不良图解
NO.1外皮压接过度
Science And Technology
原因:压接手势不正确或挡板调试不当导致芯线压接部位压进外皮, 造成外皮压接过度,产生不良。 后果:直接影响导体的压接,造成电流流通不顺或直接断路。
Science And Technology
线束生产的工序及品质要求 HHCCBB
3.3、产品不需要扎胶或扎带时,装配时要注意不能绞线。 3.4、复杂装配时,先装配孔位少的再装配到多孔位塑件中。
Science And Technology
线束生产的工序及品质要求 HHCCBB
4、装配过程及质量控制点
4.1、在装配作业时,首先应确认材料(线材,胶壳)型号、颜色使用是否正确,是否与相应的图纸和作业指 导书相一致,如不能确认,需向班长或巡检员报告帮忙确认无误后方可正式作业
原因:模具调试,上下模配合不好,或者刀片粘端子。(端子湾的角度在15 以 内是可以接受的)
束丝成缆工序质量控制

LOGO
绞线工作流程图
设备点检
按照检点表内容检查设备状况,填写设备点检表.
领取生产工单、工艺卡
核对工单产品编码是否与工艺卡一致.
领取原材料、半成品、模具
重新
确认所领原材料、半成品、模具的规格 尺寸是否与工艺卡及工单一致. 确认导体直径或芯线根数、颜色、穿线 结构、节距、排列顺序是否符合工艺. 自主进行首检:检验试产产品质量是否达到合格 要求, 进行调节,直到良好. 5分钟以内进行中间检验,观察质量是否达到合格 要求,经常巡检:芯线根数,排序、排线是否正 常,有无背股、跳丝,做到提前发现问题,迅速 解决问题. 报表及流水卡的填写要求:规范,工整、整洁.
☆设备操作-束丝机
束丝机也叫高速绞线机,其型号主要以收线盘的尺寸来命名,公司现用 的高速绞线机有:保龙650、富川650两种,根据导线进入机器方向可 分左手机(从机器右边进入)和右手机(从机器左边进入)。 主要参数
FC650P BL650P
1600RPM(3200扭/分)
机器最高转速 单丝线径
2000RPM(4000扭/分)
保龙束丝机收线张力调节
每周定期检查张力调节螺母,有无灰尘 积累,图示方面位置少量注油 每月检查张力弹簧是否缺失,手压弹簧 顶盘无倾斜,如有请更换弹簧
手调张力调节螺母,顺时针方向张力增大、 逆时针方向减小,开机后手压收线盘内 导体,无明显凹坑。 首检产品导体拉伸小于0.002mm
Φ 0.08~0.45mm
Φ 0.08~0.40mm
绞合截面积
绞距 绞向 收线轴
张力控制 升降台
0.35~1. 5mm2
4.22~39.64mm 左右均可 Φ 630
电动调节 电动升降
束丝机、绞线的工艺要点及质量标准

束丝机、绞线的工艺要点及质量标准一、绞合工艺的工艺要点1、准备阶段的质量控制1)在未装夹单线或股线前,应根据设备检查的要求,检查设备情况。
必要时启动设备进行试运行,检查各相关部件的运行情况,各类保护开关是否有效。
绞线机2)检查各类领用材料是否符合工艺指导卡规定和生产令的要求,如单线的规格长度、各类包带的规格等等。
3)按工艺要求将将单线或股线安置到放线架上,注意内外层绞向、排列等应与工艺要求一致。
预调好放线张力以及收线张力等。
4)根据生产指令和工艺要求选配并安装好各类摸具,如并线模、紧压模等,必要是根据实际情况进行适当调整.5)收线盘的容量应与生产长度和规格相适应,装夹时应按设备的操作规程进行.2、绞线运行阶段的质量控制1)设定好绞合节距和绞合方向,将单线或股线逐步穿好并与导引绳连接引入到收线盘。
2)低速启动设备,运行一定长度,停车后检查节距、绞向等。
同时对设备的运行情况再作一检查,以确定完好。
3)待确认符合要求后再正常开车运行,在运行过程中,不得私自离岗,因巡回检查绞线外径、查看绞线是否有缺股、断丝、外观等并按半成品检验规范要求记录。
4)检查绕包质量情况,包括搭盖、接头、外形等。
5)0.3mm以下单线允许接头,但相邻两接头必须大于300mm,0。
3mm以上单线必须焊接,接头应修平。
不得有2根以上单线一起扭接。
6)排线的节距应与绞线尺寸和收线速度相适应,严禁严重的交叉排列。
线盘不能装得过满,一般应低于盘边5~10mm为宜,卸盘时应注意防止碰伤线芯.3、绞线完工阶段的质量控制1)对每盘下机后的线芯应认真填写流水卡及各类报表,以确保半制品流转质量。
2)对每盘线芯下车后应再次核实是否符合要求,并按指定地点堆放提交仓库称检重量。
3)工作结束后应关闭电源,以防止他人误操作引起设备故障。
二、束线、绞线的质量标准1、束线的质量标准l)外观绞合后的束线,单线表面应光洁,无明显的机械损伤,不得有氧化变色现象,不得有明显的松股和背股。
束丝工艺
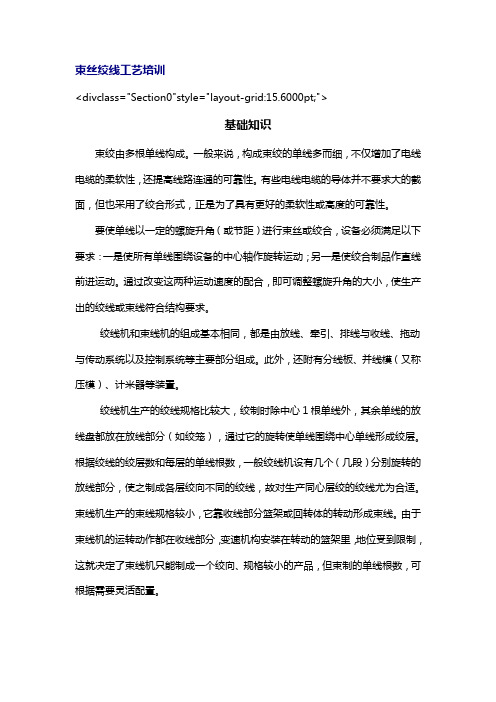
束丝绞线工艺培训<divclass="Section0"style="layout-grid:15.6000pt;">基础知识束绞由多根单线构成。
一般来说,构成束绞的单线多而细,不仅增加了电线电缆的柔软性,还提高线路连通的可靠性。
有些电线电缆的导体并不要求大的截面,但也采用了绞合形式,正是为了具有更好的柔软性或高度的可靠性。
要使单线以一定的螺旋升角(或节距)进行束丝或绞合,设备必须满足以下要求:一是使所有单线围绕设备的中心轴作旋转运动;另一是使绞合制品作直线前进运动。
通过改变这两种运动速度的配合,即可调整螺旋升角的大小,使生产出的绞线或束线符合结构要求。
绞线机和束线机的组成基本相同,都是由放线、牵引、排线与收线、拖动与传动系统以及控制系统等主要部分组成。
此外,还附有分线板、并线模(又称压模)、计米器等装置。
绞线机生产的绞线规格比较大,绞制时除中心1根单线外,其余单线的放线盘都放在放线部分(如绞笼),通过它的旋转使单线围绕中心单线形成绞层。
根据绞线的绞层数和每层的单线根数,一般绞线机设有几个(几段)分别旋转的放线部分,使之制成各层绞向不同的绞线,故对生产同心层绞的绞线尤为合适。
束线机生产的束线规格较小,它靠收线部分篮架或回转体的转动形成束线。
由于束线机的运转动作都在收线部分,变速机构安装在转动的篮架里,地位受到限制,这就决定了束线机只能制成一个绞向、规格较小的产品,但束制的单线根数,可根据需要灵活配置。
绞线或束线质量,一方面取决于单线材料及附加材料的本身质量,另一方面也取决于绞制或束制工艺。
选用何种绞合设备与绞制品的结构,截面和外径大小、单线根数、单线粗细以及绞制品的制造长度有直接的关系。
如果是同心层绞的绞线,应首先考虑绞线机放线盘的盘数和大小是否与之适应,然后再考虑绞合方向、节距长度和要不要退扭等。
若为复绞线,还需考虑股线变形,这就需要分析绞线结构、规格、材料,确定工艺数据,最后选择适合的绞线机。
- 1、下载文档前请自行甄别文档内容的完整性,平台不提供额外的编辑、内容补充、找答案等附加服务。
- 2、"仅部分预览"的文档,不可在线预览部分如存在完整性等问题,可反馈申请退款(可完整预览的文档不适用该条件!)。
- 3、如文档侵犯您的权益,请联系客服反馈,我们会尽快为您处理(人工客服工作时间:9:00-18:30)。
束丝机、绞线的工艺要点及质量标准
一、绞合工艺的工艺要点
1、准备阶段的质量控制
1)在未装夹单线或股线前,应根据设备检查的要求,检查设备情况。
必要时启动设备进行试运行,检查各相关部件的运行情况,各类保护开关是否有效。
绞线机2)检查各类领用材料是否符合工艺指导卡规定和生产令的要求,如单线的规格长度、各类包带的规格等等。
3)按工艺要求将将单线或股线安置到放线架上,注意内外层绞向、排列等应与工艺要求一致。
预调好放线张力以及收线张力等。
4)根据生产指令和工艺要求选配并安装好各类摸具,如并线模、紧压模等,必要是根据实际情况进行适当调整。
5)收线盘的容量应与生产长度和规格相适应,装夹时应按设备的操作规程进行。
2、绞线运行阶段的质量控制
1)设定好绞合节距和绞合方向,将单线或股线逐步穿好并与导引绳连接引入到收线盘。
2)低速启动设备,运行一定长度,停车后检查节距、绞向等。
同时对设备的运行情况再作一检查,以确定完好。
3)待确认符合要求后再正常开车运行,在运行过程中,不得私自离岗,因巡回检查绞线外径、查看绞线是否有缺股、断丝、外观等并按半成品检验规范要求记录。
4)检查绕包质量情况,包括搭盖、接头、外形等。
5)0.3mm以下单线允许接头,但相邻两接头必须大于300mm,0.3mm以上单线必须焊接,接头应修平。
不得有2根以上单线一起扭接。
6)排线的节距应与绞线尺寸和收线速度相适应,严禁严重的交叉排列。
线盘不能装得过满,一般应低于盘边5~10mm为宜,卸盘时应注意防止碰伤线芯。
3、绞线完工阶段的质量控制
1)对每盘下机后的线芯应认真填写流水卡及各类报表,以确保半制品流转质量。
2)对每盘线芯下车后应再次核实是否符合要求,并按指定地点堆放提交仓库称检重量。
3)工作结束后应关闭电源,以防止他人误操作引起设备故障。
二、束线、绞线的质量标准
1、束线的质量标准
l)外观
绞合后的束线,单线表面应光洁,无明显的机械损伤,不得有氧化变色现象,不得有明显的松股和背股。
对于镀锡线芯,表面要求色泽均匀、光滑,不能有黑斑,镀锡层均匀,不应有漏镀等。
2)尺寸
单线应圆整,不应有明显的拉细现象,拉细必须在标准规定的范围内,束线外径应在工艺要求以内。
3)结构与组成
束线不得有缺根、断根、松股,搭股、束线表面如有轻微擦毛,仍可作合格品。
结构与组成必须符合工艺规定。
4)束线的节距比和束制方向应符合规定。
5)焊接
一次束合导体,不允许整芯焊接,但单线允许焊接,焊头距离不小于300mm,焊头外经不超过公差绝对值的2倍,复绞线用的股线允许焊接,焊头距离不小于1m,焊头应修
光、锉圆,其焊头直径不能超过标称直径的0.2mm及以下,第6种束线的单线允许扭接,但不允许有毛头,线芯应平滑。
绞线机
6)装盘
成盘导电线芯排线整齐,平整,不得有腰鼓形和线芯互相压叠现象。
2、绞线的质量标准
l)、外观
绞线外观应光洁,不得有三角口、裂纹、斑疤及夹杂物,节距均匀整齐,不得有明显的机械损伤,对于铜绞合导体不得有氧化变色现象和黑斑。
对于镀锡线芯要求色泽均匀,光亮,不得有黑斑和漏镀。
2)、尺寸
组成绞线的单线的挣细量,必须在规定范围内,绞线外径应符合工艺规定。
3)、结构与组成
绞线的结构与组成,及成品直流电阻值应符合GB/T3956—1997电缆导体)的规定。
不能缺根,少股、断股、压叠,对扇形线芯压型的偏心度不能超过10%。
4)、节距和绞向应符合工艺要求。
5)、状态,除架空绝缘线用硬铜导体外,其余铜导体必须是退火状态。
绞线机
6)多层绞线由内至外节距比逐渐缩小,且同层节距保持一致,绞合各层应相反。
7)第2种合第5、6种导体不允许整芯焊接,单单线或股线允许焊接,焊接处的直径应不大于偏差绝对值的2倍,束线焊头外径不大于标称直径0.2mm,同层或相邻层的焊头距离不小于300mm。
束丝机、绞线机产品的质量缺陷和预防
束丝、绞线产品的质量缺陷主要有以下几种:
1、绞线表面擦伤,刮伤线芯
产生原因:通常一是分线盘上的线嘴磨损,二是单线跳出滑轮,三是穿线用木管或塑料管磨通,四是牵引设备推线板上的定位销损坏,五是压模中有异物等原因。
消除的办法:更换分线盘上的穿线嘴和穿线用的木管、塑料管,检查线芯的走向是否正常,保护线芯不与设备直接磨损,并随时检查压模是否完好,并注意操作方法。
2、单线在绞合时断线,缺股单线断线产生的原因:
l)由于放线张力过大拉断线芯。
2)单线在拉制时松乱、排线不好、压线跨线,造成线芯挣断。
3)单线本身材质有裂纹,机械性能不好脆断。
4)放线盘安装位置不当,轴向晃动,造成断线。
5)单线跳出滑轮槽,机械卡断。
排除方法①调整放线张力,使之适当。
②注意选择进线,发现拉线时有松乱现象,必须经过复绕后方可上机。
③注意操作方法,仔细检查放线盘的位置,使放出的线不摆不跳,检查单线经过的地方,有没有跳出导轮槽的现象。
④要检查线芯表面质量,看是否有裂纹、夹渣、斑疤等缺陷。
如果断线发生在内层,而断头已经走得过长,就无法修理,只有剪去这段缺股线芯,如果断线发生在外层,应把线修复后再开机。
3、过扭
过扭是指绞合过程中,扭绞过度呈麻花形现象。
产生的原因:一是绞线在牵引轮上绕的圈数不够,一般少于4圈,摩擦力过小而打滑,造成扭绞过度。
二是收线张力松或收线盘不转,而转体仍在旋转,而造成扭绞过度。
排除方法:如果外层单线已经剧烈变形,损伤严重,已无修复的可能,只有剪断。
如果单线不受严重损伤,可将设备转体部分和牵引部分分开,将其朝绞合相反方向转动,使局部扭绞部分退回,再用手把线芯修好,并把多余的单线再绕到收线盘上,把设备和转体牵引合一,较松的过压线模后,用力压线,另用模具手动修复,这样就可重新开机生产。
4、束线、绞线中单线背股、松股
产生原因:一是放线张力不均匀,松松紧紧,张力松的线芯走得多、造成背股,二是压模孔型太大,起不到适当调节张力的作用,三是压模位置不当,绞合角不合理,四是节距比较大等。
束线机束制19股及以上的单线芯,由于束线没有方向的区别,只能同向束制,所以线芯结合呈不规则状态,目前生产厂家大都采用双节距束制,因此束线束制19股以上的线芯,背股,松股现象比绞线严重。
排除方法:对束线(l股以上的束制品)一是改进束线的放线装置,采用较先进的单线张力放线器,使每根单线的张力都可以调整、控制。
二是采用导向模,导向模的孔径为束线计算外径叨97%%。
这样导向模可以适当调节张力。
三是改用单节距的束线机,这种束线机的束制产品,可以达到绞线的水平。
四是对背股,松股严重的束线芯,用过模复绕修复的办法,也能达到使用的要求。
五是适当调整节距比。
对于绞线产品背股,松股的排除方法:一是调整放线张力,使之均匀。
二是改换压模,便线芯在模孔中不要松动,注意压模的喇叭口,如果喇叭口已经损坏,也不能使。
三是调整压模座的位置,使绞线的绞入角合理。
四是如果绞合节距较大,应适当减小。
5、排线混乱、压线
产生的原因:绞合产品一般都是成盘供应。
大截面,要一根根的排好,尤其是底层线要特别注意排整齐,在排线调头时,由于有一个停留,应特别注意,上下层之间不能留有太大间隙,排距要适当,过大容易造成压线。
排除的办法:首先要调整收线张力,当手动排线时,一能够排得动为宜,第二根据线芯直径大小更换排线节距,排好第一层是关键,一定要排整齐;排第二层,在调层时,要进行人工排线,确保排线质量。
三是加强操作责任心随时观察排线质量,发现问题要及时调整,注意固定好两个线头和留边距离。
6、单线线径忽大、忽小或掺错线芯
产生原因:绞合中发现单线线径超差或掺错线芯,主要原因是没有认真执行工艺规定,另一个原因是管理上存在一定的问题。
消除方法:掺错线芯如果长度不长,可以扒下,重新换线,按编线修理法修复。
如果长度太长,就无法修理,只有下机,另行处理。
因此上机前,操作者应认真检查和测量。
当然管理者也应该提供一个保证办法,比如线规是否偏多,公差是否合理,生产调度是否安排得当,按PDCA原则认真思考管理上存在的问题,避免人为的不良品和废品的产生。
7、绞合线芯松股
产生的原因:(l)节距过大,造成绞合线芯不坚实。
(2)压模孔型过大,起不到压实和调节作用。
线模喇叭口过大或被磨损,损坏。
(3)放线张力不均匀,松松紧紧。
(4)各层节距比配合不好。
(5)线芯状态不符合工艺规定,尤其是铝线芯。
(6)分线器和压模座的位置不当等。
排除方法:首先严格工艺纪律,执行工艺操作规程,适当减少过大的节距,调节好放线张力和压模。
分线器到压模座的位置,根据不同的结构,一般调到200~250mm为宜。
对于绞。