【精品课件】金属塑性成形
金属塑性成形优秀课件

概述
塑性成形又称压力加工。它是利用金属在外力作用下产生 的塑性变形.以获得具有一定形状、尺寸和力学性能的原材料 (如金属型材、板材、管材和线材等)、毛坯或零件的生产方法。
压力加工可生产出各种不同截面的型材(加板材、线材、 管材等)和各种机器零件的毛坯或成品(如轴、齿轮、汽车大梁、 连杆等)。
加工硬化是一种不稳定现象,具有自发地回复到稳定状 态的倾向。加工硬化的消除方法主要有回复和再结晶。
T回 = (0.25~0.3)T熔 T再 = (0.35~0.4)T熔
根据需要对冷变形金属进行回复处理与 再结晶退火,前者使冷变形金属保持力学 性能(如硬度、强度、塑性等)基本不变, 部分地消除残余应力;后者使冷变形金属 的强度、硬度显著下降,塑性和韧性显著 提高,内应力和加工硬化完全消除,金属 又恢复到冷变形之前的状态,再次获得良 好塑性。
实际金属的滑移是靠位错的移动来实现的。
τ
τ
9
2)孪生: 晶体的一部分相对一部分沿一定的晶面发生相对转动。
2. 多晶体的塑性变形
晶内变形
滑移 孪生
滑动 晶间变形
转动
多晶体塑性变形的实质:
晶粒内部发生滑移和孪生;同时晶 粒之间发生滑移和转动。
10
二、塑性变形后金属的组织和性能
• 金属塑性变形时,在改变其形状和尺寸 的同时,其内部组织结构以及各种性能 均发生变化。塑性变形时的温度不同, 金属变形后的组织和性能也有所不同。 因此,金属的塑性变形分为冷变形和热 变形两种。冷变形是指金属在再结晶温 度以下进行的塑性变形;热变形是指金 属在再结晶温度以上进行的塑性变形。
(2)在垂直于纤维组织的方向上:材料的塑性、韧性下 降,抗剪能力提高。
为了充分利用纤维组 织的性能.设计制造 零件应尽量使零件受 最大拉应力方向与纤 维方向一致.受最大 剪切应力方向与纤维 方向垂直,并使纤维 方向与零件的轮廓相 符合而不被切断。
金属塑性成形课件

2023-11-06•金属塑性成形概述•金属塑性成形工艺•金属塑性成形设备•金属塑性成形技术的发展趋势•金属塑性成形过程中的缺陷与质量控制目•金属塑性成形实例分析录01金属塑性成形概述金属塑性成形是一种使金属材料发生塑性变形,以获得所需形状、尺寸和性能的加工方法。
金属塑性成形广泛应用于机械制造、航空航天、汽车、电子等领域,是一种重要的材料加工技术。
金属塑性成形的定义金属塑性成形可以制造出复杂形状的零件,并且能够获得较高的精度和表面质量。
与切削加工相比,金属塑性成形具有更高的材料利用率和更低的能耗。
金属塑性成形过程中材料的变形是均匀的,因此可以避免应力集中和裂纹等缺陷。
金属塑性成形的特点03金属塑性成形的基本原理包括应力状态、屈服准则、塑性流动规律等。
金属塑性成形的基本原理01金属塑性成形的原理是基于金属的塑性变形规律,即在外力作用下,金属材料会发生形状和尺寸的变化。
02在金属塑性成形过程中,材料的变形受到应力状态、变形温度、变形速度等因素的影响。
02金属塑性成形工艺自由锻工艺自由锻是利用冲击力或静压力使金属坯料变形,并施加外力将其锻造成所需形状和尺寸的锻造方法。
定义特点流程应用自由锻具有较大的灵活性,可以生产形状各异的锻件,但生产效率较低,适用于单件或小批量生产。
自由锻的流程包括坯料准备、加热、变形和锻后冷却。
自由锻主要用于大型锻件和难变形材料的加工,如轴、轮毂、法兰等。
模锻工艺模锻是利用模具使金属坯料变形,并施加外力将其锻造成所需形状和尺寸的锻造方法。
定义模锻具有较高的生产效率,且能获得较为精确的形状和尺寸,但模具制造成本较高。
特点模锻的流程包括坯料准备、加热、放入模具、变形、锻后冷却和修整。
流程模锻广泛应用于中小型锻件的生产,如齿轮、轴套、法兰等。
应用板料冲压工艺板料冲压是利用冲压机将金属板料变形,并施加外力将其冲制成所需形状和尺寸的加工方法。
定义板料冲压具有较高的生产效率,且能获得较为精确的形状和尺寸,但模具对材料的厚度和硬度有一定要求。
金属塑性成形PPT课件

(Mg、Zn、Cd、α-Ti)
3.2塑性成 形机理
滑移
3 金属塑性 成形
滑移带 500倍
26
3.2塑性成 形机理 滑移
3 金属塑性 成形
27
3.2塑性成 形机理 滑
移
3 金属塑性 成形
28
3.2塑性成 形机理 滑移
3 金属塑性 成形
辊锻,楔横轧, 辗环,辊弯
7
3.1塑性成 形概述
塑性成形类型
3 金属塑性 成形
8
3.1塑性成 形概述
3 金属塑性 成形
体积成形
体积成形主要是指那些利用锻压设备和工、模具 ,对金属坯料(块料)进行体积重新分配的塑性 变形,得到所需形状、尺寸及性能的制件。
主要包括锻造(Forging)和挤压(Extrusion )两大类。
日 常 用 品
3
汽 车 覆 盖 件
飞
冲压成形产品示例—— 高科技产品
机 蒙 皮
4
5
6
3.1塑性成 形概述
3 金属塑性 成形
锻压3塑(性Met成al 形for分gin类g and stamping)
1.体积成形 (Bulk Metal Forming):
1.1 锻造 (Forging)
1.1.1自由锻造 1.1.2模锻
用伸长率δ、断面收缩率ψ表示:
δ= (L1-L0)/ L0 ×100% ψ=( S0-S1)/S0×100%
22
3.2塑性成
3 金属塑性
形机理
成形
2.金属塑性变形的实质
金 体—属——原—子显微组织——晶 典型晶格结构:
《金属塑性成形方法》课件
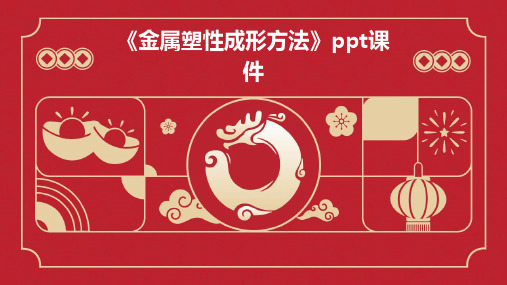
目录
CONTENTS
• 金属塑性成形方法简介 • 金属塑性成形的基本原理 • 金属塑性成形的主要方法 • 金属塑性成形的质量控制 • 金属塑性成形技术的发展趋势
01 金属塑性成形方法简介
CHAPTER
金属塑性成形的基本概念
金属塑性成形是一种通过施加外 力使金属材料发生塑性变形,从 而获得所需形状和性能的加工方
大型金属件和复杂形状的金属件制造,如轴、齿轮、连杆等。
模型锻造
要点一
总结词
通过将金属坯料放置在模具中,在高温和高压下使其发生 塑性变形,从而获得所需形状和尺寸的金属件。
要点二
详细描述
模型锻造是一种常见的金属塑性成形方法,通过将金属坯 料放置在模具中,在高温和高压下使其发生塑性变形,从 而获得所需形状和尺寸的金属件。模型锻造过程中,金属 坯料在高温和高压下发生变形,内部晶粒结构发生变化, 从而提高了金属的力学性能。模型锻造适用于中小型金属 件制造,如齿轮、轴承、气瓶等。
过程稳定可控。
在线检测
采用先进的在线检测技术,对成形 过程中的产品进行实时检测,及时 发现并处理问题。
成品检测
对成形后的产品进行全面的检测, 包括尺寸、外观、性能等,确保产 品质量符合要求。
05 金属塑性成形技术的发展趋势
CHAPTER
高性能金属材料的开发与应用
高强度钢
通过合金化、热处理等手段提高 钢材的强度和韧性,用于制造轻
流动法则与加工硬化
流动法则是描述金属在塑性成形过程中应力的分布规律。加工硬化是指 在塑性成形过程中,随着变形的进行,材料的强度和硬度逐渐提高的现 象。
金属塑性变形的工艺基础
塑性成形的基本方法
材料成型工艺基础-金属塑性成形课件
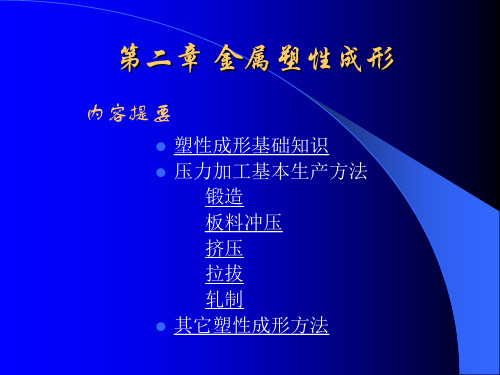
扩展市场,开发未来,实现现在。202 0年12 月8日星 期二上 午12时 44分36 秒00:4 4:3620. 12.8
做专业的企业,做专业的事情,让自 己专业 起来。2 020年1 2月上 午12时4 4分20. 12.800:44December 8, 2020
人生不是自发的自我发展,而是一长 串机缘 。事件 和决定 ,这些 机缘、 事件和 决定在 它们实 现的当 时是取 决于我 们的意 志的。2 020年1 2月8日 星期二 12时44 分36秒 Tuesday , December 08, 2020
感情上的亲密,发展友谊;钱财上的 亲密, 破坏友 谊。20. 12.8202 0年12 月8日星 期二12 时44分 36秒20 .12.8
4.冷镦
2.5其他成形
冷镦机
2.5其他成形
每一次的加油,每一次的努力都是为 了下一 次更好 的自己 。20.12. 820.12. 8Tuesd ay , December 08, 2020
天生我材必有用,千金散尽还复来。0 0:44:36 00:44:3 600:44 12/8/20 20 12:44:36 AM
五、锻件的结构工艺性
轴类零件 杆类零件 盘类零件
2.2自由锻
§3 模锻
一、模锻方式
锤上模锻 压力机上模锻 胎模锻
蒸汽 - 空气锤
锤上模锻
2.3模 锻
锻模结构
2.3模 锻
思考题
2.3模 锻
模锻能否直接锻出通孔?
二、模锻工序
2.3模 锻
形状简单的零件: 预锻→终锻→清理
形状较复杂或锻造比大的零件: 制坯→预锻→终锻→清理 连杆锻模 曲轴模锻
金属塑性成形课件
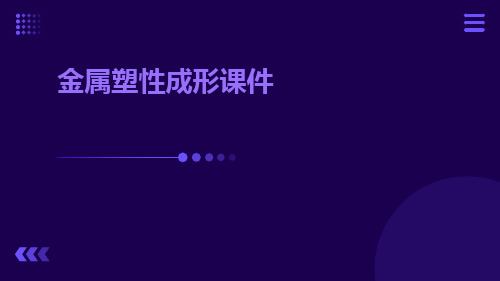
液压成形可以提高锻件精度、降低成本、减少模具制造时间,适用于生产大型、 复杂形状的锻件。但需要使用专门的液压设备和液态介质,成本较高。
粉末冶金
粉末冶金基本工艺
粉末冶金是将金属粉末作为原料,通过压制、烧结等工艺制 成具有一定形状和性能的制品。
粉末冶金特点
粉末冶金可以生产出高精度、高密度、高性能的制品,适用 于生产复杂形状的零件。但生产周期长、成本高,且对于大 型零件来说存在一定的局限性。
制品翘曲
优化坯料加热和模具设计,改善制品冷 却条件,减少翘曲变形。
工艺优化与改进方法
优化工艺参数
引进新工艺
通过试验和模拟等方法,确定最佳的工艺参 数组合,提高产品质量和生产效率。
积极推广新工艺,提高生产效率和产品质量 ,降低生产成本。
自动化与智能化
持续改进
引入自动化和智能化设备,提高生产过程的 稳定性和效率,降低人为因素对产品质量的 影响。
03
针对不同的产品要求,灵活调整工艺参数
模具设计
1
根据产品要求和工艺方案,进行模具设计计算
2
确定模具的结构形式、材料、尺寸和精度要求 等
3
对模具进行强度、刚度和稳定性等方面的校核
计算机辅助工艺设计
01
利用计算机辅助工艺设计软件,进行工艺模拟和优化
02
根据模拟结果,对工艺方案、工艺参数和模具等进行调整和优
3
非晶合金材料
具有高强度、高硬度、耐磨、耐蚀等优点,是 制造精密部件的理想材料。
高精度与高效率成形技术
精密塑性成形技术
采用高精度模具、精确控制成形工艺参数等方法,使金属坯料达到高精度、 高化工艺流程、采用多工位成形、高速压制等手段,提高生产效率,降 低生产成本。
- 1、下载文档前请自行甄别文档内容的完整性,平台不提供额外的编辑、内容补充、找答案等附加服务。
- 2、"仅部分预览"的文档,不可在线预览部分如存在完整性等问题,可反馈申请退款(可完整预览的文档不适用该条件!)。
- 3、如文档侵犯您的权益,请联系客服反馈,我们会尽快为您处理(人工客服工作时间:9:00-18:30)。
四、塑性成形的基本规律
1. 体积不变定律 指金属在塑性变形过程中,其体积保持不变。
2. 最小阻力定律 变形过程中,金属各质点将沿着阻力最小的方向流动。
1 . 可锻性的衡量指标
1)塑性: 材料的塑性越好,其可锻性越好。
2)变形抗力: 材料的变形抗力越小,其可锻性越好。
2 . 影响可锻性的因素 1)金属的化学成分及组织 ①化学成分: 含碳量低,则塑性较好,可锻性就好,一般 纯金属的可锻性好于合金;含有形成碳化物的元素(如W、 Cr等),则可锻性就差。 ②组织状态:单相固溶体具有良好的可锻性。
加工硬化是一种不稳定现象,具有自发地回复到稳定状 态的倾向。加工硬化的消除方法主要有回复和再结晶。
T回 = (0.25~0.3)T熔 T再 = (0.35~0.4)T熔
根据需要对冷变形金属进行回复处理与 再结晶退火,前者使冷变形金属保持力学 性能(如硬度、强度、塑性等)基本不变, 部分地消除残余应力;后者使冷变形金属 的强度、硬度显著下降,塑性和韧性显著 提高,内应力和加工硬化完全消除,金属 又恢复到冷变形之前的状态,再次获得良 好塑性。
τ
τ
2)孪生: 晶体的一部分相对一部分沿一定的晶面发生相对转动。
2. 多晶体的塑性变形
晶内变形
滑移 孪生
滑动 晶间变形
转动
多晶体塑性变形的实质:
晶粒内部发生滑移和孪生;同时晶 粒之间发生滑移和转动。
二、塑性变形后金属的组织和性能
• 金属塑性变形时,在改变其形状和尺寸 的同时,其内部组织结构以及各种性能 均发生变化。塑性变形时的温度不同, 金属变形后的组织和性能也有所不同。 因此,金属的塑性变形分为冷变形和热 变形两种。冷变形是指金属在再结晶温 度以下进行的塑性变形;热变形是指金 属在再结晶温度以上进行的塑性变形。
加工硬化在工业生产中很有实用意义。某些不能通过热 处理方法来强化的金属材料.如低碳钢、纯铜、防锈铝、镍 铬不锈钢等,可以通过冷轧、冷拔、冷挤压等工艺,使其产 生加工硬化.以此来提高其强度和硬度或提高其特殊性能。 加工硬化可用于金属强化,但对压力加工不利,使金属变形 抗力增加.继续变形困难。
3) 回复处理与再结晶退火
第二章 塑性成形-压力加工
概述
塑性成形又称压力加工。它是利用金属在外力作用下产生 的塑性变形.以获得具有一定形状、尺寸和力学性能的原材料 (如金属型材、板材、管材和线材等)、毛坯或零件的生产方法。
压力加工可生产出各种不同截面的型材(加板材、线材、 管材等)和各种机器零件的毛坯或成品(如轴、齿轮、汽车大梁、 连杆等)。
1.冷变形后金属的组织和性能
1)组织变化的特征:
①晶粒沿变形最大方向伸长;
②晶格与晶粒均发生畸变; ③晶粒间产生碎晶。
2)性能变化的特征:
加工硬化:
原因
随着变形程度的增加,其强度和硬度不断提高,塑性和韧性不 断下降。
单晶体发生晶内 滑移,使晶格扭曲, 内应力增大,即滑移 阻力增大;晶粒间有 碎晶.使品粒滑动阻 力增大.结果使得进 一步变形困难,
1)零件大小不受限制;2)生产批量不受限制。的实质
各种压力加工方法,都是通过对金属材料施加外力,使 之产生塑性变形来实现的。单晶体的塑性变形形式主要 有滑移和孪生两种。
1.单晶体的塑性变形
1)滑移:
晶体的一部分τ相对一部分沿一τ定的晶面发生相对滑动。但
实际金属的滑移是靠位错的移动来实现的。
2)工艺条件
①变形温度: T温越高,材料的可锻性越好。
②变形速度: V变越小,材料的可锻性越好。
③应力状态:
塑
性、
三向压应力—
变
形
塑性最好、变形抗
抗
力最大。
力
变形抗力
三向拉应力—
塑性最差、变形抗 力最大。
塑性
vc v
锻造温度范围
始锻温度: 过热、过烧 缺陷 终锻温度: 加工硬化
45: 1200℃~800℃
1)不产生加工硬化
2)使组织得到改善,提高了力学性能
① 细化晶粒; ② 压合了铸造缺陷; ③ 组织致密。 3)形成纤维组织
钢锭是压力加工中的原始毛坯,其 内部存在着不溶于基体金属的非金属 夹杂物。这些夹杂物在热变形中,将 随金属品粒的变形方向被拉长或压 扁.呈纤维状。当金属再结品时.被 压碎的晶粒恢复为等轴细晶粒.而纤 维状夹杂物无再结晶能力.仍然沿被 拉长方向保留下来,形成纤维组织。
造
下砥 铁
模 锻
➢板料冲压(又称薄板冲压和冷冲压)
➢ 轧制、挤压
➢拉拔和冷镦
塑性成形(压力加工)的特点
1.力学性能高 1)组织致密; 2)晶粒细化; 3)压合铸造缺陷; 4)使纤维组织合理分布。
2.节约材料 1)力学性能高,承载能力提高; 2)减少零件制造中的金属消耗(与切削加工相比)。
3.生产率高 4.适用范围广
纤维组织的稳定性很高, 靠通常的热处理无法消除。 只有经过锻压使金属变形, 才能变其方向和形状。因 此,在设计和制造零件时, 为使零件具有良好的力学 性能,应根据零件的工作 条件,正确控制金属的变 形流动和流线在锻件中的 分布。
纤维组织具有各向异性的特点:
(1)在平行于纤维组织的方向上:材料的塑性、韧性提 高,抗拉强度增加。
用于压力加工的金属必须具有良好的塑性。各种钢 材与大多数有色金属及其合金都具有—定程度的塑 性.可以在不同温度下进行压力加工。但铸铁等脆性 材料,以及形状复杂特别是具有形状复杂内腔的零件 或毛坯(如箱体),难以用压力加工方法制造。
塑性成形加工的方法有:
➢锻造加工: 自由锻造和模锻
上砥 铁
自
由坯
锻料
(2)在垂直于纤维组织的方向上:材料的塑性、韧性下 降,抗剪能力提高。
为了充分利用纤维组 织的性能.设计制造 零件应尽量使零件受 最大拉应力方向与纤 维方向一致.受最大 剪切应力方向与纤维 方向垂直,并使纤维 方向与零件的轮廓相 符合而不被切断。
三、金属的可锻性
是金属材料在压力加工时成形的难易程度。
塑性变形后金属被拉长了的晶粒重新生核、结品,变为等轴品粒,这一过程 称为再结品。即温度再增加.金属原子获得更多能量,则以碎晶和杂质为结 鼎核重新结品成新的晶粒,从而完全消除加工硬化。
部分原子回复到正常排列位置、减轻了晶格 扭曲,消除了部分加工硬化。即强度、硕度 略有下降,塑性、韧性略有提高
2.热变形后金属的组织和性能