供应商品质管理规范
供应商品质奖罚管理规范

供应商品质奖罚管理规范一、引言供应商品质奖罚管理规范是为了提高供应商的产品质量,保障公司产品质量的稳定性和可靠性,确保客户满意度的提升而制定的。
本规范适用于公司与供应商之间的产品质量管理。
二、目的1. 确保供应商提供的产品符合公司的质量要求,达到预期的质量标准。
2. 建立奖罚机制,激励供应商提供高质量的产品,同时惩罚质量不达标的供应商,以保证供应链的稳定性和可靠性。
三、责任与义务1. 公司责任:a. 制定明确的产品质量标准和要求,提供给供应商,并确保供应商理解和遵守。
b. 定期对供应商进行质量评估,及时发现问题并采取相应的措施。
c. 建立健全的奖罚机制,对供应商的产品质量进行评价和奖罚。
d. 提供必要的培训和支持,帮助供应商提升产品质量。
2. 供应商责任:a. 理解并遵守公司的产品质量标准和要求。
b. 按时交付符合质量标准的产品。
c. 建立并执行质量管理体系,确保产品质量的稳定性和可靠性。
d. 及时处理客户的质量投诉,并采取纠正措施避免再次发生类似问题。
四、质量评估与奖罚机制1. 质量评估:a. 定期对供应商进行质量评估,包括产品质量、交货准时率、客户投诉率等指标。
b. 评估结果分为优秀、良好、一般和不合格四个等级,并给予相应的奖励或处罚。
2. 奖励机制:a. 优秀供应商:产品质量稳定且符合公司标准,交货准时率高,客户投诉率低。
可获得额外的订单、提前支付等优惠措施。
b. 良好供应商:产品质量基本符合公司标准,交货准时率较高,客户投诉率较低。
可获得订单优先处理等奖励。
3. 处罚机制:a. 一般供应商:产品质量不稳定或不完全符合公司标准,交货准时率一般,客户投诉率较高。
需进行整改,并限制其订单数量。
b. 不合格供应商:产品质量严重不符合公司标准,交货准时率低,客户投诉率高。
需立即停止合作,并追究其责任。
五、质量管理体系1. 供应商应建立完善的质量管理体系,包括以下方面:a. 产品设计与开发:确保产品符合公司的质量要求和客户需求。
供应商品质奖罚管理规范
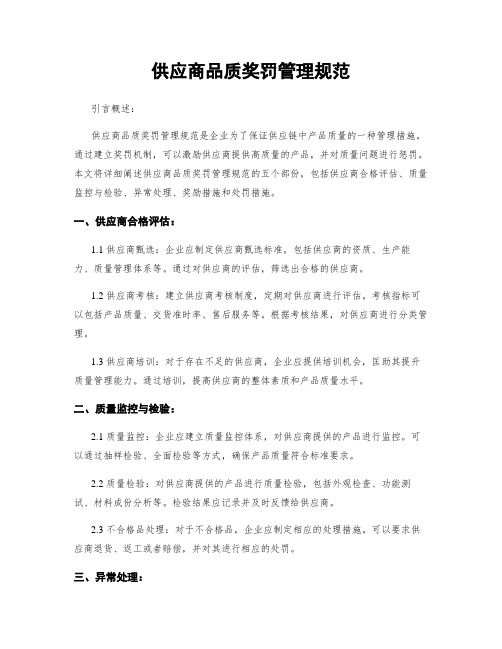
供应商品质奖罚管理规范引言概述:供应商品质奖罚管理规范是企业为了保证供应链中产品质量的一种管理措施。
通过建立奖罚机制,可以激励供应商提供高质量的产品,并对质量问题进行惩罚。
本文将详细阐述供应商品质奖罚管理规范的五个部份,包括供应商合格评估、质量监控与检验、异常处理、奖励措施和处罚措施。
一、供应商合格评估:1.1 供应商甄选:企业应制定供应商甄选标准,包括供应商的资质、生产能力、质量管理体系等。
通过对供应商的评估,筛选出合格的供应商。
1.2 供应商考核:建立供应商考核制度,定期对供应商进行评估。
考核指标可以包括产品质量、交货准时率、售后服务等。
根据考核结果,对供应商进行分类管理。
1.3 供应商培训:对于存在不足的供应商,企业应提供培训机会,匡助其提升质量管理能力。
通过培训,提高供应商的整体素质和产品质量水平。
二、质量监控与检验:2.1 质量监控:企业应建立质量监控体系,对供应商提供的产品进行监控。
可以通过抽样检验、全面检验等方式,确保产品质量符合标准要求。
2.2 质量检验:对供应商提供的产品进行质量检验,包括外观检查、功能测试、材料成份分析等。
检验结果应记录并及时反馈给供应商。
2.3 不合格品处理:对于不合格品,企业应制定相应的处理措施。
可以要求供应商退货、返工或者赔偿,并对其进行相应的处罚。
三、异常处理:3.1 异常情况记录:对于供应链中浮现的异常情况,企业应及时记录并进行分析。
异常情况可以包括产品质量问题、交货延迟等。
3.2 异常原因分析:对异常情况进行原因分析,找出问题的根源。
可以采用鱼骨图、5W1H等工具,匡助确定问题的原因。
3.3 异常处理措施:根据异常情况的分析结果,制定相应的处理措施。
可以与供应商进行沟通,共同解决问题,并采取措施避免类似问题再次发生。
四、奖励措施:4.1 奖励标准设定:企业应制定奖励标准,明确供应商可以获得奖励的条件和奖励的形式。
奖励可以是奖金、信誉度提升、定单优先等。
供应商品质管理规范
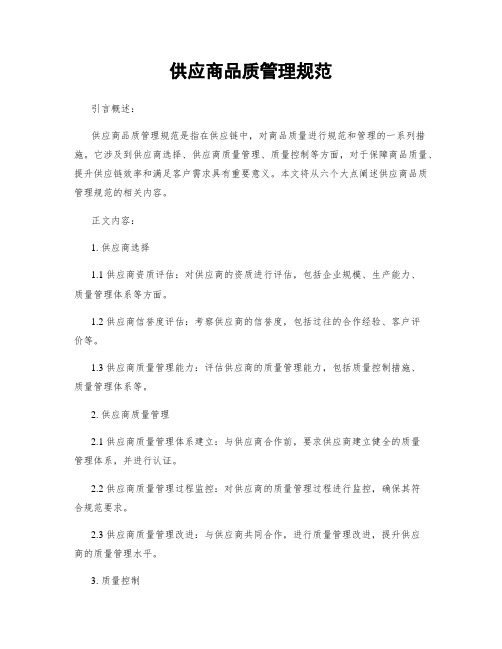
供应商品质管理规范引言概述:供应商品质管理规范是指在供应链中,对商品质量进行规范和管理的一系列措施。
它涉及到供应商选择、供应商质量管理、质量控制等方面,对于保障商品质量、提升供应链效率和满足客户需求具有重要意义。
本文将从六个大点阐述供应商品质管理规范的相关内容。
正文内容:1. 供应商选择1.1 供应商资质评估:对供应商的资质进行评估,包括企业规模、生产能力、质量管理体系等方面。
1.2 供应商信誉度评估:考察供应商的信誉度,包括过往的合作经验、客户评价等。
1.3 供应商质量管理能力:评估供应商的质量管理能力,包括质量控制措施、质量管理体系等。
2. 供应商质量管理2.1 供应商质量管理体系建立:与供应商合作前,要求供应商建立健全的质量管理体系,并进行认证。
2.2 供应商质量管理过程监控:对供应商的质量管理过程进行监控,确保其符合规范要求。
2.3 供应商质量管理改进:与供应商共同合作,进行质量管理改进,提升供应商的质量管理水平。
3. 质量控制3.1 原材料质量控制:对原材料进行严格的质量控制,确保其符合产品要求。
3.2 生产过程质量控制:对生产过程进行质量控制,包括工艺参数控制、检测设备使用等。
3.3 成品质量控制:对成品进行全面的质量控制,包括外观检查、功能性测试等。
4. 质量监测与检测4.1 质量监测计划制定:制定质量监测计划,明确监测的目标、内容和频率。
4.2 质量检测方法选择:选择适合的质量检测方法,包括物理检测、化学检测、微生物检测等。
4.3 质量检测结果分析:对质量检测结果进行分析,及时发现问题并采取相应的措施。
5. 不合格品处理5.1 不合格品分类:对不合格品进行分类,包括严重不合格品、可修复不合格品等。
5.2 不合格品处理流程:制定不合格品处理流程,明确责任人和处理方式。
5.3 不合格品追溯与反馈:追溯不合格品的原因,并及时向供应商反馈,以便供应商改进。
6. 持续改进6.1 质量管理体系改进:不断完善质量管理体系,提升整体质量管理水平。
供应商品质管理规范

供应商品质管理规范引言概述:供应商品质管理规范是企业为确保所供应的商品质量达到一定标准而采取的一系列管理措施。
有效的商品质管理规范可以提高企业的竞争力,增强消费者对商品的信任度。
本文将从五个方面详细阐述供应商品质管理规范的内容。
一、供应商选择与评估1.1 供应商背景调查:企业在选择供应商时,应对其进行背景调查,包括了解其企业规模、经营状况、资质认证等情况,以确保供应商具备合法合规的资质。
1.2 供应商质量管理体系:企业应评估供应商的质量管理体系,包括其质量控制流程、质量标准、质量检测设备等,以确保供应商能够提供符合要求的商品。
1.3 供应商绩效评估:企业应定期对供应商进行绩效评估,包括对其交货准时率、退货率、客户投诉率等进行考核,以确保供应商能够持续提供高质量的商品。
二、采购合同管理2.1 合同条款明确:企业在与供应商签订采购合同时,应明确商品质量要求、交货时间、售后服务等条款,以确保供应商清晰了解企业的要求。
2.2 合同履行监督:企业应建立合同履行监督机制,对供应商的合同履行情况进行监督,确保供应商按合同要求提供商品。
2.3 合同变更管理:如果需要对采购合同进行变更,企业应与供应商进行充分沟通,并确保变更事项符合法律法规和质量要求。
三、商品质量检验3.1 原材料检验:企业应对供应商提供的原材料进行检验,包括外观质量、物理性能、化学成份等方面,以确保原材料符合质量要求。
3.2 生产过程监控:企业应对商品生产过程进行监控,包括设定生产工艺参数、进行生产现场检查等,以确保商品生产过程符合质量标准。
3.3 成品检验:企业应对成品进行全面检验,包括功能性能、外观质量、安全性等方面,以确保成品符合质量要求。
四、供应链管理4.1 供应链透明化:企业应与供应商建立良好的合作关系,共享信息,确保供应链透明化,以便及时发现和解决质量问题。
4.2 供应商培训与支持:企业应提供供应商培训和技术支持,匡助供应商提升质量管理能力,确保供应商能够提供高质量的商品。
供应商品质奖罚管理规范

供应商品质奖罚管理规范一、引言供应商品质奖罚管理规范是为了提高供应商的产品质量,确保供应链的顺畅运作而制定的一套管理标准。
本文将详细介绍供应商品质奖罚管理规范的内容和要求。
二、背景良好的供应商品质是企业能否提供高质量产品的关键因素之一。
为了确保供应商能够持续提供符合标准的产品,我们制定了供应商品质奖罚管理规范,以激励供应商优化产品质量,同时对质量不达标的产品进行惩罚。
三、供应商资格要求1. 供应商必须具备合法的经营资质和相关认证,并能提供相关证明文件。
2. 供应商必须具备一定的生产能力和技术实力,能够满足定单的生产要求。
3. 供应商必须具备完善的质量管理体系,包括质量控制流程、检测设备等。
4. 供应商必须具备良好的信誉和服务意识,能够及时响应客户需求并提供有效的解决方案。
四、产品质量评估标准1. 产品质量评估标准将根据产品的特性和客户需求而定,包括外观、性能、可靠性等方面的指标。
2. 评估标准将采用定量和定性相结合的方式,通过实验室测试、样品检验等方法进行评估。
3. 评估结果将以合格、不合格和优良等级进行分类,供应商将根据评估结果获得相应的奖励或者惩罚。
五、奖励机制1. 供应商根据产品质量评估结果获得相应的奖励,包括财务奖励、合作机会优先等。
2. 奖励机制将根据供应商的质量表现进行定期评估和调整,以激励供应商不断提升产品质量。
六、惩罚机制1. 供应商如果产品质量不达标,将面临一系列的惩罚措施,包括罚款、降低合作机会等。
2. 惩罚机制将根据产品质量不达标的程度和频次进行评估和执行,以确保供应商能够及时改进产品质量。
七、质量改进要求1. 供应商在获得奖励或者惩罚后,应及时进行质量改进,并提供改进计划和措施。
2. 供应商应建立完善的质量管理体系,包括质量控制流程、培训计划等,以提升产品质量。
八、监督和评估1. 企业将建立供应商质量管理团队,负责监督和评估供应商的产品质量。
2. 监督和评估将采用定期抽样检验、现场考察等方式进行,以确保供应商的质量管理符合规范要求。
供应商品质管理规范
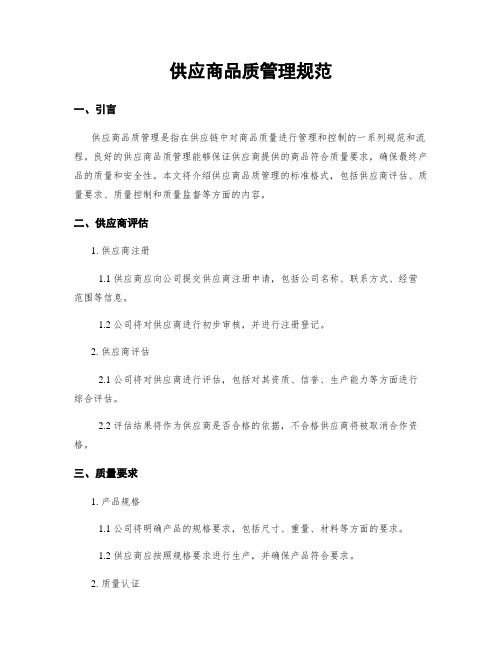
供应商品质管理规范一、引言供应商品质管理是指在供应链中对商品质量进行管理和控制的一系列规范和流程。
良好的供应商品质管理能够保证供应商提供的商品符合质量要求,确保最终产品的质量和安全性。
本文将介绍供应商品质管理的标准格式,包括供应商评估、质量要求、质量控制和质量监督等方面的内容。
二、供应商评估1. 供应商注册1.1 供应商应向公司提交供应商注册申请,包括公司名称、联系方式、经营范围等信息。
1.2 公司将对供应商进行初步审核,并进行注册登记。
2. 供应商评估2.1 公司将对供应商进行评估,包括对其资质、信誉、生产能力等方面进行综合评估。
2.2 评估结果将作为供应商是否合格的依据,不合格供应商将被取消合作资格。
三、质量要求1. 产品规格1.1 公司将明确产品的规格要求,包括尺寸、重量、材料等方面的要求。
1.2 供应商应按照规格要求进行生产,并确保产品符合要求。
2. 质量认证2.1 供应商应具备相应的质量认证,如ISO9001等。
2.2 公司将对供应商的质量认证进行核实,确保其有效性和合法性。
3. 检测要求3.1 公司将制定检测方案,包括抽样检验、检测方法和标准等。
3.2 供应商应按照检测要求进行产品检测,并提供检测报告。
四、质量控制1. 原材料采购1.1 供应商应从合法渠道采购原材料,并提供相关证明文件。
1.2 公司将对原材料进行抽样检验,确保其符合质量要求。
2. 生产过程控制2.1 供应商应建立完善的生产过程控制体系,包括设备维护、操作规范等。
2.2 公司将对供应商的生产过程进行监督和抽查,确保产品质量稳定。
3. 不良品处理3.1 供应商应建立不良品处理机制,包括不良品的分类、记录和处理方法等。
3.2 公司将对供应商的不良品处理进行监督和评估,确保处理措施的有效性。
五、质量监督1. 定期检查1.1 公司将定期对供应商进行质量监督检查,包括对产品、生产过程和管理体系的检查。
1.2 检查结果将作为供应商绩效评估的依据。
供应商品质管理规范

供应商品质管理规范一、引言供应商品质管理是指在供应链中,对商品质量进行有效管理和控制,以确保供应商提供的商品符合客户的要求和期望。
本文旨在制定一套供应商品质管理规范,以提高供应商的质量管理水平,确保所供商品的质量稳定可靠。
二、适用范围本规范适用于所有供应商提供的商品,包括但不限于原材料、零部件、成品等。
所有供应商必须遵守本规范的要求,并与采购方建立合作关系。
三、质量管理体系1. 质量方针供应商应制定明确的质量方针,并将其传达给所有员工。
质量方针应注重客户需求、持续改进和合规性要求。
2. 组织结构供应商应建立健全的质量管理组织结构,明确各级质量管理职责和权限。
质量管理部门应与其他部门保持紧密合作,确保质量管理工作的顺利进行。
3. 质量目标和指标供应商应设定合理的质量目标,并制定相应的质量指标进行评估和监控。
质量目标应具体、可衡量和可追踪,以确保质量管理工作的有效实施。
4. 流程控制供应商应建立完善的质量管理流程,包括但不限于供应商评估、原材料检验、生产过程控制、成品检验等。
流程应符合相关法规和标准要求,并持续改进。
四、供应商评估1. 评估标准采购方将根据一定的评估标准对供应商进行评估,评估标准包括但不限于质量管理体系、生产能力、技术能力、交货准时性、售后服务等。
2. 评估方法评估方法可以包括供应商自评、现场审核、样品检验等。
评估结果将作为供应商合作与否的决策依据。
3. 评估周期供应商评估应定期进行,评估周期根据供应商的实际情况和重要性确定。
评估结果将影响供应商在采购方供应商名单中的地位。
五、原材料检验1. 检验标准供应商应制定明确的原材料检验标准,确保所采购的原材料符合质量要求。
检验标准应包括外观、尺寸、性能等方面。
2. 检验方法供应商应采用适当的检验方法进行原材料检验,包括但不限于目视检查、物理性能测试、化学成分分析等。
3. 检验记录供应商应对原材料检验结果进行记录和保存,确保检验结果可追溯。
检验记录应包括检验日期、检验人员、检验结果等信息。
供应商品质管理规范

供应商品质管理规范一、引言供应商品质管理规范是为了确保所供应的商品符合一定的质量标准和要求,从而保证客户满意度和企业形象的提升。
本文将详细介绍供应商品质管理的标准格式和内容。
二、范围本规范适用于所有供应商,无论其规模大小和所供应的商品种类。
三、术语和定义1. 供应商:指向企业提供商品或服务的个人或组织。
2. 商品质量:指商品在设计、生产、包装、运输和销售等过程中所具备的特性和性能。
四、质量管理体系1. 质量目标:供应商应制定明确的质量目标,以确保所供应的商品符合客户要求和国家法规标准。
2. 组织结构:供应商应建立质量管理部门,并明确质量管理人员的职责和权限。
3. 质量文件:供应商应编制和维护相关的质量文件,包括质量手册、程序文件和记录文件等。
4. 培训和意识:供应商应定期组织培训,提高员工的质量意识和技能水平,确保他们能够正确执行质量管理要求。
五、质量控制1. 供应商选择:供应商应建立供应商评估和选择的程序,确保所选择的供应商具备满足质量要求的能力。
2. 进货检验:供应商应对所进货的商品进行检验,确保其质量符合要求。
3. 生产过程控制:供应商应建立生产过程控制的程序,包括原材料的选择和检验、生产工艺的控制和设备的维护等。
4. 检测和测试:供应商应建立检测和测试的程序,对所供应的商品进行质量检测和性能测试,确保其符合标准要求。
5. 不合格品处理:供应商应建立不合格品处理的程序,包括不合格品的隔离、返工和报废等。
六、质量改进1. 数据分析:供应商应定期分析质量数据,找出问题的根本原因,并采取相应的改进措施。
2. 客户投诉处理:供应商应建立客户投诉处理的程序,及时处理客户的投诉,并采取纠正措施,以避免类似问题再次发生。
3. 内部审核:供应商应定期进行内部审核,评估质量管理体系的有效性和符合性,并提出改进意见。
七、质量保证1. 认证和认可:供应商应根据需要,申请并通过相关的质量管理体系认证和认可。
2. 供应商评估:企业应定期对供应商进行评估,评估其质量管理能力和供应商品质量的稳定性。
- 1、下载文档前请自行甄别文档内容的完整性,平台不提供额外的编辑、内容补充、找答案等附加服务。
- 2、"仅部分预览"的文档,不可在线预览部分如存在完整性等问题,可反馈申请退款(可完整预览的文档不适用该条件!)。
- 3、如文档侵犯您的权益,请联系客服反馈,我们会尽快为您处理(人工客服工作时间:9:00-18:30)。
供应商品质管理规范
文件编号:
现行版本: A版
编制:
审核:
批准:
修改记录
1目的
对供应商进行定期评审及考核,对其现有体系保证能力进行测量、分析,以促进其不断加以改善,从而能够长期、稳定地供应公司要求的合格物料、适应公司的长期发展需要。
2 适应范围
适用于所有供应物料给XX 公司之供应商。
3 内容
3.1 评核评估表的适用分类:
I类供应商评核评估表—适用于电子料、五金件、INLAY物料的供应商的评核;
Ⅱ类供应商评核评估表—适用于包装材料、化工、耗用材料的供应商的评核;
Ⅲ类供应商评核评估表_适用于海外供应商的评核。
Ⅳ类供应商评核评估表—适用于模具供应商的评核;.
3.2新供应商评核
3.2.1SQE收到采购的评核联络书后,安排SQE工程师与采购、工程一同评核;
3.2.2评核结果
A级(得分≧85分)――优良供应商,优先采购;
B级(70≤得分<85)――合格供应商,正常采购;
C级(60≤得分<70)――限期改善之供应商,待复评合格后才可采购;
D级(得分<60分)――拒绝接受之供应商;
3.2.3 新供应商必须被评为B级时,才可下单采购;
3.3 年度评核
3.3.1 评核计划
3.3.1.1 SQE负责制订C类(省内)主要合格供应商年度评核计划:
a)评核的体系类别
——品质体系评核适用于所有C类主要合格供应商。
——环境体系评核适用于有《XX GREEN STANDARD》要求,需对来料进行环境管理物质监控的C类供应商主要合格供应商。
b)评核的周期
评核的周期根据供应商上一次的评核结果来确定。
——上一次评鉴得分在A级的供应商每两年评核一次。
——评核评分在B级的供应商一年评核一次。
——评核评分在C级的供应商半年评核一次。
——D级及以下的供应商,将根据“供应商评核不合格通知”中的总经理意见确定评核周期。
——当出现以下情况,SQE将临时安排供应商现场评核:
1)供应商的交货出现严重的品质缺陷;
2)供应商产品质量连续3个月明显下降。
3.3.1.2 当实际评核行动与计划有较大变动时,SQE对计划进行重新修订。
3.3.1.3 评核计划的编制和修订需经品质部经理的批准。
3.3.2 评核的实施
3.3.2.1按照评核计划,SQE在评核前一个工作周内向供应商发出“供应商评核联络书”,在与供应
商协调后,确定评核日期。
3.3.2.2 评核的主要依据为《供应商评核评估表》。
3.3.2.3 评核后一个星期内作出评核结论,如有需要则发出《供应商改善要求书》。
评核结果必须
反馈给供应商、采购部、物控部和公司领导层。
3.3.2.4 供应商在收到《供应商改善要求书》后半月内,必须反馈相关改善行动计划。
3.3.2.5 SQE针对供应商的改善计划,监督其实施情况,并根据实际需要确定是否复查。
3.3.3 评核不合格的处理
当SQE评核评定为不合格供应商时,将发出“供应商评核不合格通知”,要求采购部给予处理意见,并最终由总经理确认处理结果。
采购部在收到通知一个星期内如没有回应,将视为同意SQE评定结果。
3.4国内主要供应商的月度品质评价
3.4.1 评估对象为C类主要物料供应商
3.4.2评分内容
3.4.2.1来货品质状况
①批退率(不合格批次/来货批次*100%)25分
D、铝壳
备注:1)全检物料之供应商不作批退率评分,不良率评分以50分计。
2)如当月上货批数少于20批,每判退一批扣4分,直至扣完25分;
3)免检物料:每判退一批扣4分,直至扣完25分;
②不良率(抽检不良数/抽检总数*100%)
1)电子类(25分)
2)PCB类(25分)
5)五金类(25分)
备注:1)来错货之不良数不计入不良率数据中;
3.4.2.3品质改善(10分)
3.4.2.4配合程度(10分)
注:收到投诉报告或电话投诉1天内,及时向投诉人沟通并经其同意延时回复的不纳入评分范围
3.4.3评价等级
注:D 级发生一次时------一个月内必须改善不良点;
D 级发生二次时------限期整改,警告且通知相关部门;
D 级发生三次时------减少或暂停采购,须同相关部门重新评鉴供应商品质保证体系。
3.4.4按照评分内容作出评分后,须将结果记录于《供应商品质评价表》中,经主管审核后发放其它
相关部门。
3.5 海外供应商的质量管理
3.5.1每季度对海外供应商的来料质量状况进行统计,并发放采购部 3.5.2当出现如下质量异常时,须将如下结果通报公司领导层: a ) 来料批次小于10批时,批退率>50% b ) 来料批次大于10批时,批退率>20% c ) 来料出现重大质量异常时 3.6 来料质量异常的反馈及处理
3.6.1 SCAR 报告《Supplier Corrective Action Request Report 》 3.6.1.1发放条件:
a) 来料抽检时,功能不良超出AQL ;
b) 来料抽检时,尺寸不良影响装配,并且不良率超过3%; c) 来料抽检时,外观缺陷的不良率大于5%; d) 生产线投诉时,与a )、b )、c )相同; e) 客户投诉并要求书面回复时; 3.6.1.2 结案条件:
a) 来料连续3批无类似缺陷;
b) 一个月内只有一批来料,且该批来料无类似缺陷或不良率有明显降低; c) 一个半月内无上货,其他同类产品无类似缺陷或不良率有明显降低;
3.6.2 除3.5.1.1项之外发现的来料不良,SQE 都必须以电话或其它形式反馈给供应商改善、处理; 3.7 免检物料供应商
3.7.1当供应商满足以下条件时,可考虑将其纳入免检供应商: a)
交货品质良好且稳定,连续12个月内,无出现较大品质不良; b) 不良品在生产线上易发现,出现品质问题时易处理;
d)物料生产周期较短,出现不良退货时能较快补货;
e)供应商配合态度良好;
3.7.2当免检物料在生产线出现品质问题时,处理方法依照《供应商免检协议》。
4相关文件及记录
《XX GREEN STANDARD》 XX-01
《供应商评核评估表》 QR-06-01
《供应商改善要求书》Q R-06-03
《供应商评核联络书》 QR-06-08
《供应商评核不合格通知》 QR-06-09
《供应商月品质评价表》 QR-06-05。