基于Flotherm的某机载设备热仿真分析
Flotherm在某型设备的应用

图1 设备结构图
1.2 Flotherm分析模型
本文主要考虑设备后面机箱的热设计,模块1有独立散热方式,因此不考虑模块1的热功耗。
机箱结构对称,且热
图2 分析模型(隐藏上盖板)
图4 风道
利用Flotherm进行模拟仿真,可以快速准确获取风道的阻力特性。
模型周围环境的相对压力设定为0,在进风口放置一个固定流量式(Fixed Volume)风机,在模型内部进风口
图5 风机特性曲线和风道阻力特性曲线
重量随之增加,同时风道阻力也会增加。
选择合适的翅片数
量和间距,是模型热设计需要考虑的重要因素。
图9 模块5温度分布
图6 散热翅片示意图
翅片厚度选择为1mm,通过比较元器件A的温度(元
器件A为模块5上温度最高的元器件),确定翅片最优间距
和数目。
利用Flotherm软件进行仿真计算,得出如下结果如
表面通风量(m3/s)模块5重量(g)
720
736
736
746.5
750
753.5
757
760
图10 模型结构件温度分布
4 结 语
Flotherm软件仿真法避免了传统方法中因经验不足、数
据不充分所导致的误差以及繁琐的解析计算过程。
这种方法。
基于Flotherm的某机载设备热仿真分析

基于Flotherm的某机载设备热仿真分析摘要:热设计对提高电子设备运行的可靠性具有十分重要的意义,是电子设备结构设计中的重要环节。
本文首先简单介绍了电子设备传热类型,然后利用热分析软件Flotherm通过建立计算模型、边界条件、网格划分等,对某机载设备进行仿真分析,得到了温度分布,为该设备热设计提供理论参考,同时本文对于应用该软件分析其他电子设备热性能具有一定的参考意义。
关键词:电子设备;热仿真分析;Flotherm1引言随着电子技术的高速发展,电子设备朝着集成化、设备小型化等方向发展,由此使得电子设备过热的问题越来越突出[1]。
研究表明65%的电子设备失效是由温度过高引起的,过热是电子设备损坏的主要形式,严重限制了电子产品性能及可靠性的提高,降低了设备的工作寿命。
在产品设计阶段对其进行热仿真,能够确定模型中的温度分布,找出模型中温度最高点,从而改进结构设计,能够有效减少设计费用,缩短设计周期,提高产品的可靠性。
2 电子设备传热电子设备热传递主要有热传导、对流换热和辐射换热三种方式[2]。
热传导,是其于傅里叶定律,一般发生于同一种物质之中的传递;对流,可分为自然换热是流体流过某物体表面时所发生的热交换过程对流和强迫对流,对流一般发生于流体中。
辐射是物体以电磁波形式传递能量的过程。
3热仿真分析热仿真分析就是根据分析对象建立热分析模型,并设定模型各种属性、环境条件、功率大小等因素,模拟计算出温度场等数据,从而对其分析研究[3]。
该型设备工作温度为65℃,本文采用热分析软件Flotherm对该型电子设备高温工作时的温度场进行仿真分析。
3.1建模该机载设备为一密闭电子设备,包括一块PCB处理板及铝合金壳体。
PCB处理板上有诸多电子元器件,其中主要器件通过与壳体接触热传递,其余电子元器件通过壳体内空气对流换热将热量传递到铝合金壳体上,壳体再将热量散失到外部环境。
在建模过程中,由于PCB板上电子元器件多而密集,考虑到在保证结果精度的条件下减少计算量和运算时间,需要对印制电路板进行了适当简化,保留功耗和体积较大的元器件[4];简化后的主要发热器件有射频芯片、FPGA芯片、DSP、电源等,它们的功耗分别为0.8w、3w、1.5w、0.5w。
基于Flotherm分析的机柜热设计及仿真研究
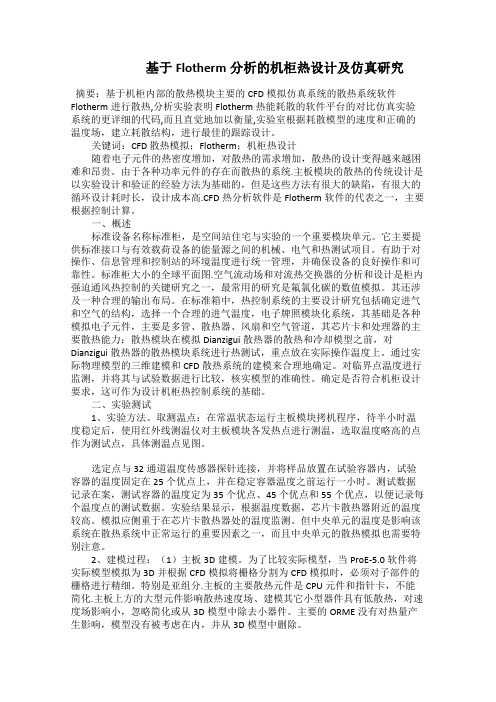
基于Flotherm分析的机柜热设计及仿真研究摘要:基于机柜内部的散热模块主要的CFD模拟仿真系统的散热系统软件Flotherm进行散热,分析实验表明Flotherm热能耗散的软件平台的对比仿真实验系统的更详细的代码,而且直觉地加以衡量,实验室根据耗散模型的速度和正确的温度场,建立耗散结构,进行最佳的跟踪设计。
关键词:CFD 散热模拟;Flotherm;机柜热设计随着电子元件的热密度增加,对散热的需求增加,散热的设计变得越来越困难和昂贵。
由于各种功率元件的存在而散热的系统.主板模块的散热的传统设计是以实验设计和验证的经验方法为基础的,但是这些方法有很大的缺陷,有很大的循环设计耗时长,设计成本高.CFD热分析软件是Flotherm软件的代表之一,主要根据控制计算。
一、概述标准设备名称标准柜,是空间站住宅与实验的一个重要模块单元。
它主要提供标准接口与有效载荷设备的能量源之间的机械、电气和热测试项目。
有助于对操作、信息管理和控制站的环境温度进行统一管理,并确保设备的良好操作和可靠性。
标准柜大小的全球平面图.空气流动场和对流热交换器的分析和设计是柜内强迫通风热控制的关键研究之一,最常用的研究是氟氯化碳的数值模拟。
其还涉及一种合理的输出布局。
在标准箱中,热控制系统的主要设计研究包括确定进气和空气的结构,选择一个合理的进气温度,电子牌照模块化系统,其基础是各种模拟电子元件,主要是多管、散热器、风扇和空气管道,其芯片卡和处理器的主要散热能力:散热模块在模拟Dianzigui散热器的散热和冷却模型之前,对Dianzigui散热器的散热模块系统进行热测试,重点放在实际操作温度上。
通过实际物理模型的三维建模和CFD散热系统的建模来合理地确定。
对临界点温度进行监测,并将其与试验数据进行比较,核实模型的准确性。
确定是否符合机柜设计要求,这可作为设计机柜热控制系统的基础。
二、实验测试1、实验方法。
取测温点:在常温状态运行主板模块拷机程序,待半小时温度稳定后,使用红外线测温仪对主板模块各发热点进行测温,选取温度略高的点作为测试点,具体测温点见图。
基于Flotherm的一种电源设备热仿真分析

2 1 年 8月 01
机
电
元
件
V0 . . 131 No 4 Au ,2 l g 01
ELECTRoM ECHANI CAL C0M PoNENTS
基 于 Foh r 的 一 种 电 源 设 备 热 仿 真 分 析 ltem
丁成 斌 王克成 张 文革 武 荣
联系 ,减小 电应 力 ( 额 ) 会 使 热 应 力 相应 的 降 降
低 ,从 而提 高电子元 器件 的可靠 性 。
对 于航天 器单 机 电子 设备 ,不能 够使用 自然对
流形式进 行冷 却 ,这是在 轨失 重状态 所致 。 因此 宇 航 电子设 备 只能依靠 传导 、辐射 ,或者 强迫 对流 的
机械应力 ) 。电应力 和热应 力 之 间存 在 紧 密 的 内在
冷却 方式 l 。 】 J
电子设备的可靠性在很大程度上取决于设备结构
设计的合理性和所采取散热措施 的有效性 。本文介绍 了一种航天器电源设备 的热设计 ,与其他的 电子设备 相 比,该设备功耗大 。由于高 温会对 电子元器件的性 能产生有害的影 响 ,为避免温度过 高形成机械应力 损 伤 、降低电子元器 件寿命 ,必须 进行合 理 的热设 计 , 给大功耗电子元器件建立有效的散热路径 。 由于设备 结构设 计 以及 元器件 的布 置安装 形式
Ab t a t Ac o d n o c a a t r t s o o r u i ,w i h a e ma e u fma y h g sr c : c r i g t h r c e si fp we n t h c r d p o n i h—p w rc mp n ns i c o e o o e t.
用flotherm对简单的封闭式设备进行热仿真]
![用flotherm对简单的封闭式设备进行热仿真]](https://img.taocdn.com/s3/m/011ea9a510661ed9ad51f3c1.png)
用flotherm4.2对简单的封闭式设备进行热仿真一设备介绍1.1设备概述该设备为一台工业级的电子设备,用途不祥,型号不祥。
1.2 设备特征图1.1 A型机外型图1)设备的大小为423mm(W)×88mm(h)×370mm(L);2)设备为密封式设备,密封程度防雨淋;3)机壳用铝合金(2A12)焊接而成,壳体和壳盖选择在整机的上部分分型,搭接面填充的非导热材料;4)机壳的两个侧板与盖板均铣有散热槽。
二设备组成与工作环境2.1 设备内部结构图图2.1 A型机内部构造图2.2 内部特征1)内部组成设备由三个模块组成,即主板、控制板、电源模块。
控制板通过板间连接器扣在主板的上方。
2)模块功耗设备的整机设计功耗为50W,实测功耗为35W,其中各个器件的设计功耗如下表所列:序号名称功耗所在位置数据来源1主板22实测值2控制板4实测值3电源10计算值4芯片11011主板中心,Top设计值5芯片11453主板右下角,Top设计值6芯片82453控制板中心,Top设计值7电源模块8电源中心,Bottom经验值表2.1 功耗列表2.3散热方法图2.2 A 型机内部散热图1) 用110导热板将芯片110的热量传导至机壳底板上; 2) 用8245导热板将芯片8245的热量传导至机壳侧壁上; 3) 在1145上放置一个铝材散热片;4) 电源模块直接贴在机壳底板上,通过机壳底板散热; 5) 导热板的材料采用合金铝(3A12),采用折弯成型方法;6) 铝表面之间采用厚度为1mm 的导热膜导热,接触压力由连接螺钉的紧固力产生; 7) 铝表面和芯片表面采用厚度为1mm 的导热膜导热,导热膜的变形量为0.7,从而产生接触压力;8) 除与接触接触位置的表面粗糙度为3.2外,其余均为12.5。
2.4 工作环境1) 设备的工作温度上限为55℃;2) 设备所处环境的空气会有不同程度的紊流。
三 仿真过程中的参数设置3.1 环境参数1) 求解范围:600mm (W )×200mm (h )×50mm (L )机箱尺寸,设备位于求解区中心;2)环境温度:55℃;3) 空气导热率:10 W/m^2K 【停滞空气的导热率为5 W/m^2K 】 3.2 建立模型图3.1 设备模型图1)假设设备外壳为壁厚为4mm的空心壳体,忽略盖板与侧壁上的散热槽,忽略其他结构要素;2)忽略设备内部线缆造成的阻尼;线缆阻尼3)忽略设备内部线缆在工作工程中的功耗;线缆功耗4)设备内部的大器件,如滤波器,在建模时设定为无热量、不导热的固体;5)设备内部的小器件,如磁环、走线板等,在建模时忽略。
基于FLOTHERM的固态功率放大器热设计

基于FLOTHERM的固态功率放大器热设计文章对L波段固态功率放大器整机结构热设计进行了研究,并结合L波段固态功率放大器设计实例,最后给出了整机的仿真及实物测试结果。
标签:热设计;固态功率放大器;热仿真;FLOTHERM引言固态功率放大器主要由功率放大模块、增益放大模块、合成模块、耦合模块和控制电路等组成,功率放大模块在大功率条件下工作时,器件发热量大,使器件处于高温状态下工作。
而高温会使元器件电性能恶化,引起失效,导致设备可靠性下降。
资料表明:单个半导体元件的温度升高10 ℃~12 ℃,其可靠性降低50%[1]。
随着器件的密集化,电子设备的功率密度增大,对热设计的需求也日益强烈。
1 整机结构设计主要设计指标如下:频率范围1GHz~2.5GHz,功率增益≥50dB,最大输入功率≤10dBm,最大输出功率≥50dBm,环境适应性满足GJB3947A-2009环境4级设备要求,另外还有输入端口驻波比、输出功率平坦度、1dB压缩点输出功率、3dB压缩点输出功率、噪声系数、谐波抑制等指标要求。
功率放大模块采用某型号功率芯片,单个芯片无论在输出功率或功率增益方面都无法达到设计要求,因此,本方案选用两极放大串联的方式满足功率增益的要求,其中前级作为推动级,末级作为功率输出级,末级使用4路放大并联的方式满足输出功率的要求,前后两个放大级中的各单管放大电路设计成完全相同的形式。
信号流图如图1所示。
功率放大模块中的功率芯片满载时功耗较高达到115瓦。
五个功率放大模块共有10个芯片,芯片总功耗高达1150瓦,并且该芯片面积小,热流密度高,散热难度很大。
综合整机内部信号流、模块的功能、可装配性和可维修性等,為了更好的散热,整机结构布局如图2所示。
散热器由上下基板和中间散热片组成,在机箱高度方向放置于机箱中部,上下基板可以贴附散热器件,可以最大限度的增加机箱散热性能。
电源自带散热风机,因此将电源单独放置于机箱左侧的电源仓,不仅有利于散热,更有利于屏蔽强电信号。
使用Flotherm和Expedition协同完成电子设备芯片级热仿真

(上 接第 44页 ) Use FIOtherm and Expedition to Com plete CChip Scale Thermal Sim ulation of Electronic Equipm ent M IA0 Li
(China Aviation Computing Technology Research Institute,Xi an shangxi 7 10068,China)
【7]鲁丽君 ,瞿伟廉 ,李 明.桅杆结 构脉 动风 速模拟 与风 荷载 计算叨.武汉理工大学学报:交通科学与工程版 ,2010,34(05):
1057-】060:
The W ind Vibration Response Analysis of the Integrated Com m unication Tower W EN Fang,CHEN ji—zhao,JIANG Yi,LIU W en-bin
连 折
《装备制造技术}2016年第 02期
6 结束语
综上 分 析 ,我们 得 出 以下 结论 : (1)设计一种新型的一体化通信塔 ,塔体和 机房 为一体 ,塔体 自身 、塔体和机房之间可 以通过 自行 叠 及 展开 实现 运输 及 运行 两种 方式 。 (2)选取一种 比较经济而且精度较高 的 ARMA 模型 ,在模拟出脉动风速时程后 ,将脉动风功率谱与 目标 谱 进行 对 比 ,得 出 ARMA法模 拟 的可 行 性 ,进 而 得 到 脉动 风 荷 载模 拟 ,其模 拟 结 果 与实 际 情 况 基本 符合 。 (3)利用 ANSYS的瞬态动力分析功能对通信塔 风振响应时程分析可知 ,一体化通信塔的结构可行。
参 考 文 献 : [1]王肇 民 ,马人乐.塔式结构 [M].北京:科学 出版社 ,2004. [2】王肇 民.高耸 结构 的发 展和展 望[J1.特种 结构 ,2000,17(1):
基于Flotherm的电子设备机箱热分析应用
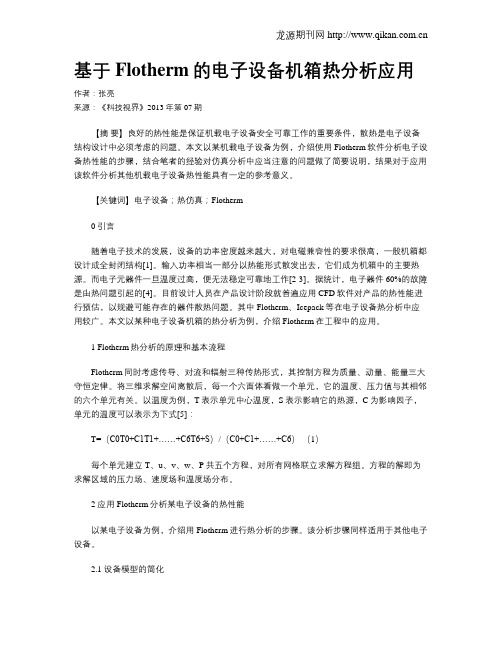
基于Flotherm的电子设备机箱热分析应用作者:张亮来源:《科技视界》2013年第07期【摘要】良好的热性能是保证机载电子设备安全可靠工作的重要条件,散热是电子设备结构设计中必须考虑的问题。
本文以某机载电子设备为例,介绍使用Flotherm软件分析电子设备热性能的步骤,结合笔者的经验对仿真分析中应当注意的问题做了简要说明,结果对于应用该软件分析其他机载电子设备热性能具有一定的参考意义。
【关键词】电子设备;热仿真;Flotherm0 引言随着电子技术的发展,设备的功率密度越来越大,对电磁兼容性的要求很高,一般机箱都设计成全封闭结构[1]。
输入功率相当一部分以热能形式散发出去,它们成为机箱中的主要热源。
而电子元器件一旦温度过高,便无法稳定可靠地工作[2-3]。
据统计,电子器件60%的故障是由热问题引起的[4]。
目前设计人员在产品设计阶段就普遍应用CFD软件对产品的热性能进行预估,以规避可能存在的器件散热问题。
其中Flotherm、Icepack等在电子设备热分析中应用较广。
本文以某种电子设备机箱的热分析为例,介绍Flotherm在工程中的应用。
1 Flotherm热分析的原理和基本流程Flotherm同时考虑传导、对流和辐射三种传热形式,其控制方程为质量、动量、能量三大守恒定律。
将三维求解空间离散后,每一个六面体看做一个单元,它的温度、压力值与其相邻的六个单元有关。
以温度为例,T表示单元中心温度,S表示影响它的热源,C为影响因子,单元的温度可以表示为下式[5]:T=(C0T0+C1T1+……+C6T6+S)/(C0+C1+……+C6)(1)每个单元建立T、u、v、w、P共五个方程,对所有网格联立求解方程组。
方程的解即为求解区域的压力场、速度场和温度场分布。
2 应用Flotherm分析某电子设备的热性能以某电子设备为例,介绍用Flotherm进行热分析的步骤。
该分析步骤同样适用于其他电子设备。
2.1 设备模型的简化图1 简化后设备的热仿真模型该设备包含17块PCB板,原始结构比较复杂,需要对其进行简化,包括CAD模型和PCB板的简化。
- 1、下载文档前请自行甄别文档内容的完整性,平台不提供额外的编辑、内容补充、找答案等附加服务。
- 2、"仅部分预览"的文档,不可在线预览部分如存在完整性等问题,可反馈申请退款(可完整预览的文档不适用该条件!)。
- 3、如文档侵犯您的权益,请联系客服反馈,我们会尽快为您处理(人工客服工作时间:9:00-18:30)。
基于Flotherm的某机载设备热仿真分析
发表时间:2017-08-08T17:51:37.010Z 来源:《电力设备》2017年第10期作者:李新亮
[导读] 摘要:热设计对提高电子设备运行的可靠性具有十分重要的意义,是电子设备结构设计中的重要环节。
(中国电子科技集团公司第二十研究所陕西西安 710068)
摘要:热设计对提高电子设备运行的可靠性具有十分重要的意义,是电子设备结构设计中的重要环节。
本文首先简单介绍了电子设备传热类型,然后利用热分析软件Flotherm通过建立计算模型、边界条件、网格划分等,对某机载设备进行仿真分析,得到了温度分布,为该设备热设计提供理论参考,同时本文对于应用该软件分析其他电子设备热性能具有一定的参考意义。
关键词:电子设备;热仿真分析;Flotherm
1引言
随着电子技术的高速发展,电子设备朝着集成化、设备小型化等方向发展,由此使得电子设备过热的问题越来越突出[1]。
研究表明65%的电子设备失效是由温度过高引起的,过热是电子设备损坏的主要形式,严重限制了电子产品性能及可靠性的提高,降低了设备的工作寿命。
在产品设计阶段对其进行热仿真,能够确定模型中的温度分布,找出模型中温度最高点,从而改进结构设计,能够有效减少设计费用,缩短设计周期,提高产品的可靠性。
2 电子设备传热
电子设备热传递主要有热传导、对流换热和辐射换热三种方式[2]。
热传导,是其于傅里叶定律,一般发生于同一种物质之中的传递;对流,可分为自然换热是流体流过某物体表面时所发生的热交换过程对流和强迫对流,对流一般发生于流体中。
辐射是物体以电磁波形式传递能量的过程。
3热仿真分析
热仿真分析就是根据分析对象建立热分析模型,并设定模型各种属性、环境条件、功率大小等因素,模拟计算出温度场等数据,从而对其分析研究[3]。
该型设备工作温度为65℃,本文采用热分析软件Flotherm对该型电子设备高温工作时的温度场进行仿真分析。
3.1建模
该机载设备为一密闭电子设备,包括一块PCB处理板及铝合金壳体。
PCB处理板上有诸多电子元器件,其中主要器件通过与壳体接触热传递,其余电子元器件通过壳体内空气对流换热将热量传递到铝合金壳体上,壳体再将热量散失到外部环境。
在建模过程中,由于PCB 板上电子元器件多而密集,考虑到在保证结果精度的条件下减少计算量和运算时间,需要对印制电路板进行了适当简化,保留功耗和体积较大的元器件[4];简化后的主要发热器件有射频芯片、FPGA芯片、DSP、电源等,它们的功耗分别为0.8w、3w、1.5w、0.5w。
在NX中按照实际物理模型创建机载设备简化三维模型,保存为STP格式;在flotherm中创建一新工程,将NX中的STP格式文件导入Flotherm中;随后设定求解域、湍流模型、环境条件、赋予发热器件的材料、功耗等属性;最后设置温度监测点。
图2 网格划分图
3.2网格划分
建模完成之后,对模型网格进行划分。
为了获得较好的模拟结果,应对大功率发热器件处网格进行局部加密[5]。
网格如下图所示:
3.3求解计算
在网格划分完成后就可以进行求解计算。
图3是压力、速度与温度收敛曲线。
由图可看出:一般压力、速度残差曲线收敛较快,温度残差曲线收敛速度较慢。
设备温度残差曲线降到10 以内并保持稳定[6],可近似为曲线收敛,表明该系统稳定。
计算完成后查看计算结果,PCB板上温度场如图4所示,金属壳体外表面温度场如图5所示。
结果显示,虽然FPGA和DSP功耗较大,但FPGA表面温度为79℃,DSP表面温度为78.9℃,这是因为PGA和DSP与金属壳体内表面相接处,散热较快,而最高温度点出现在RF表面达到81.2℃;金属壳体表面最高温度达到78.9℃,壳体表面温度最高点在与FPGA和DSP接触处,在靠近金属壳边缘的空气温度67.8℃,金属壳表面温度由最高点向四周逐渐降低。
电子元器件的极限高温工作温度一般情况下为:民用级70 ℃;工业级85 ℃;军用级125 ℃。
该型机载设备选用工业级芯片,而本文计算出最高温度为81.2℃,满足工作温度范围;经环境实验室测试,该型设备在65℃时可靠工作。
4 结论
本文采用热分析软件Flotherm对某机载设备进行了热仿真分析,获得了温度分布,结果显示最高温度为81.2℃,满足工程要求,为该设备热设计提供理论参考,减少设计费用,同时缩短设计周期;本文对于应用该软件分析其他电子设备热性能具有一定的参考意义。
参考文献:
[1]张瑜.电子设备热设计与分析[J].航空兵器,2011(2):57 -60.
[2]王秋旺,曾敏.传热学要点与解题.西安交通大学出版社,2006
[3]ZAM_ENGO A,RECCHIA M,KRAUS W,et a1. Electrical and thermal analyses for the radio⁃frequency circuit of ITERNBI ion source [J]. Fusion Engineering and Design,2009,84(9):2025⁃2030.
[4]张红根,郑欣燕.高热量机箱的热设计-Flotherm 建模[J].应用天地,2007,10(8):55-56.
[5]徐晓婷,朱敏波,杨艳妮.电子设备热仿真分析及软件应用[J].电子工艺技术,2006,27(5):265-268.
[6]朱金彪.一种星载电子设备散热结构的设计与优化[J].电子机械工程,2008,24(4):11 - 13.。