甲醇合成的工艺流程
甲醇合成的工艺流程
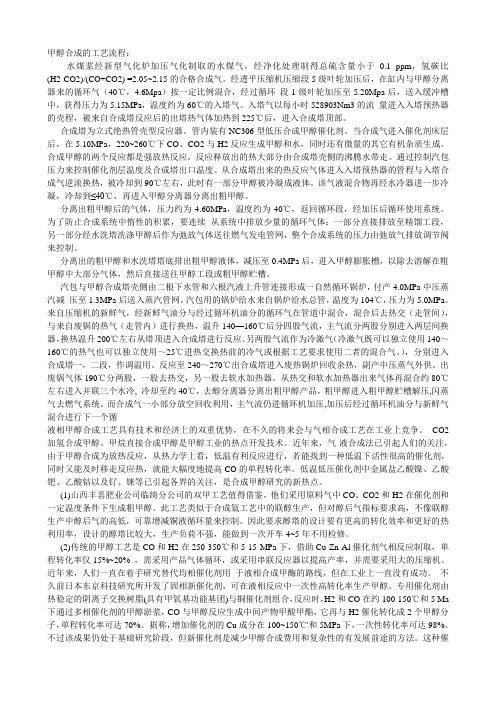
甲醇合成的工艺流程:水煤浆经新型气化炉加压气化制取的水煤气,经净化处理制得总硫含量小于0.1 ppm,氢碳比(H2-CO2)/(CO+CO2) =2.05~2.15的合格合成气。
经透平压缩机压缩段5级叶轮加压后,在缸内与甲醇分离器来的循环气(40℃,4.6Mpa)按一定比例混合,经过循环段1级叶轮加压至5.20Mpa后,送入缓冲槽中,获得压力为5.15MPa,温度约为60℃的入塔气。
入塔气以每小时528903Nm3的流量进入入塔预热器的壳程,被来自合成塔反应后的出塔热气体加热到225℃后,进入合成塔顶部。
合成塔为立式绝热管壳型反应器。
管内装有NC306型低压合成甲醇催化剂。
当合成气进入催化剂床层后,在5.10MPa,220~260℃下CO、CO2与H2反应生成甲醇和水,同时还有微量的其它有机杂质生成。
合成甲醇的两个反应都是强放热反应,反应释放出的热大部分由合成塔壳侧的沸腾水带走。
通过控制汽包压力来控制催化剂层温度及合成塔出口温度。
从合成塔出来的热反应气体进入入塔预热器的管程与入塔合成气逆流换热,被冷却到90℃左右,此时有一部分甲醇被冷凝成液体。
该气液混合物再经水冷器进一步冷凝,冷却到≤40℃,再进入甲醇分离器分离出粗甲醇。
分离出粗甲醇后的气体,压力约为4.60MPa,温度约为40℃,返回循环段,经加压后循环使用系统。
为了防止合成系统中惰性的积累,要连续从系统中排放少量的循环气体:一部分直接排放至精馏工段,另一部分经水洗塔洗涤甲醇后作为弛放气体送往燃气发电管网,整个合成系统的压力由弛放气排放调节阀来控制。
分离出的粗甲醇和水洗塔塔底排出粗甲醇液体,减压至0.4MPa后,进入甲醇膨胀槽,以除去溶解在粗甲醇中大部分气体,然后直接送往甲醇工段或粗甲醇贮槽。
汽包与甲醇合成塔壳侧由二根下水管和六根汽液上升管连接形成一自然循环锅炉,付产4.0MPa中压蒸汽减压至1.3MPa后送入蒸汽管网。
汽包用的锅炉给水来自锅炉给水总管,温度为104℃,压力为5.0MPa。
制甲醇工艺流程
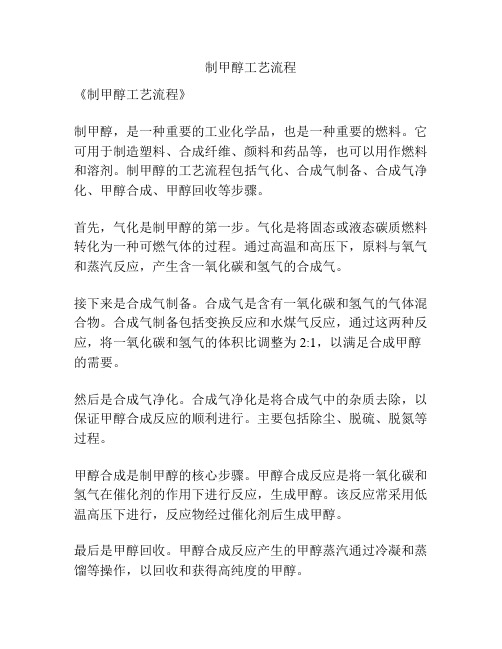
制甲醇工艺流程
《制甲醇工艺流程》
制甲醇,是一种重要的工业化学品,也是一种重要的燃料。
它可用于制造塑料、合成纤维、颜料和药品等,也可以用作燃料和溶剂。
制甲醇的工艺流程包括气化、合成气制备、合成气净化、甲醇合成、甲醇回收等步骤。
首先,气化是制甲醇的第一步。
气化是将固态或液态碳质燃料转化为一种可燃气体的过程。
通过高温和高压下,原料与氧气和蒸汽反应,产生含一氧化碳和氢气的合成气。
接下来是合成气制备。
合成气是含有一氧化碳和氢气的气体混合物。
合成气制备包括变换反应和水煤气反应,通过这两种反应,将一氧化碳和氢气的体积比调整为2:1,以满足合成甲醇的需要。
然后是合成气净化。
合成气净化是将合成气中的杂质去除,以保证甲醇合成反应的顺利进行。
主要包括除尘、脱硫、脱氮等过程。
甲醇合成是制甲醇的核心步骤。
甲醇合成反应是将一氧化碳和氢气在催化剂的作用下进行反应,生成甲醇。
该反应常采用低温高压下进行,反应物经过催化剂后生成甲醇。
最后是甲醇回收。
甲醇合成反应产生的甲醇蒸汽通过冷凝和蒸馏等操作,以回收和获得高纯度的甲醇。
总的来说,制甲醇的工艺流程是一个复杂的过程,需要多种反应和操作步骤。
这些步骤需要在严格的条件下进行,以保证甲醇质量和产量。
制甲醇的工艺流程不仅对设备要求高,还对操作者要求高,需要具备一定的专业知识和技能。
甲醇合成工艺流程

甲醇合成工艺流程甲醇合成是一种重要的化学工艺,用于生产甲醇这种重要的有机化合物。
下面将介绍甲醇合成的工艺流程。
首先,甲醇合成的原料主要包括一氧化碳和氢气。
一氧化碳可以通过化石燃料的气化或者过程废气的处理得到。
而氢气可以通过天然气重整反应或者通过电解水得到。
在甲醇合成过程中,首先需要对原料进行净化和预热。
一氧化碳和氢气通过净化装置,去除其中的杂质和有毒物质。
然后,原料进入加热器,通过加热提高其温度,为后续的反应做准备。
接下来,原料进入甲醇合成反应器。
在反应器中,一氧化碳和氢气发生甲醇合成反应,生成甲醇和水。
这个反应是一个高压、高温的反应,需要使用催化剂来提高反应速率和选择性。
常用的催化剂包括铜、锌、铝和锆等金属催化剂。
反应器内部可以采用固定床、流化床或者微管等不同形式。
在反应过程中,甲醇和水汽经过冷却装置,进行冷却,使其冷凝成液体。
然后,通过分离装置,将液体甲醇和水汽进行分离。
水汽可以再循环利用,或者通过进一步处理后排放。
甲醇分离纯化是甲醇合成工艺中的重要环节。
甲醇需经过除杂工艺,去除其中的杂质,如碱金属、杂质醇、酮和酚等。
常用的方法有萃取、析出、蒸馏等。
经过精馏、提纯等处理,最终得到纯度高的甲醇产品。
在甲醇合成工艺中,还需要对废气进行处理。
废气中一般含有甲烷、氢气、一氧化碳等有价值的成分,可以通过分离和净化技术进行回收利用。
同时,废气中也含有一些有害物质,如二氧化碳、氮氧化物等,需要经过净化和处理后排放。
总结起来,甲醇合成的工艺流程主要包括原料净化预热、甲醇合成反应、冷却分离、甲醇纯化和废气处理等步骤。
这些步骤的操作和控制都需要高度的工艺和技术要求,以确保甲醇的合成和生产过程稳定、高效并符合环保要求。
合成甲醇的工艺流程
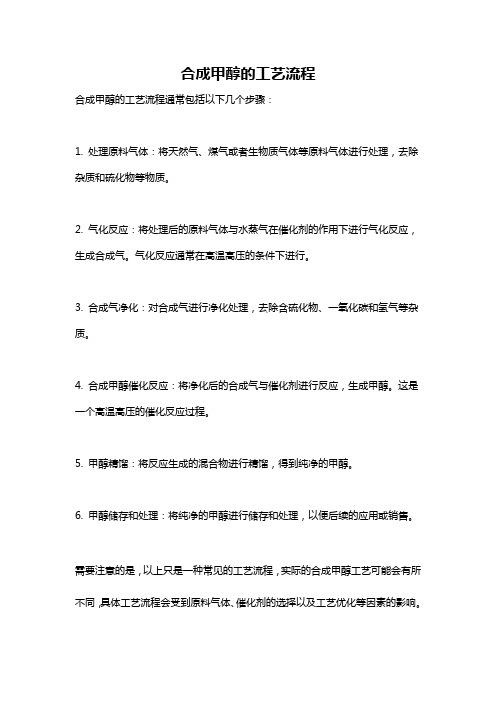
合成甲醇的工艺流程
合成甲醇的工艺流程通常包括以下几个步骤:
1. 处理原料气体:将天然气、煤气或者生物质气体等原料气体进行处理,去除杂质和硫化物等物质。
2. 气化反应:将处理后的原料气体与水蒸气在催化剂的作用下进行气化反应,生成合成气。
气化反应通常在高温高压的条件下进行。
3. 合成气净化:对合成气进行净化处理,去除含硫化物、一氧化碳和氢气等杂质。
4. 合成甲醇催化反应:将净化后的合成气与催化剂进行反应,生成甲醇。
这是一个高温高压的催化反应过程。
5. 甲醇精馏:将反应生成的混合物进行精馏,得到纯净的甲醇。
6. 甲醇储存和处理:将纯净的甲醇进行储存和处理,以便后续的应用或销售。
需要注意的是,以上只是一种常见的工艺流程,实际的合成甲醇工艺可能会有所不同,具体工艺流程会受到原料气体、催化剂的选择以及工艺优化等因素的影响。
甲醇生产—甲醇生产工艺流程
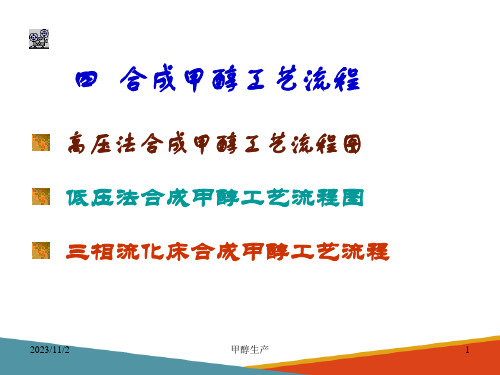
再见 反应器,冷激气在段间经喷嘴喷入,喷嘴分布于反应器的整
个截面上,以便冷激气与反应气混合均匀。混合的温度正好 是反应温度低限,混合气进入下一段床层进行反应。段中进 行的反应为绝热反应,释放的反应热使反应气体温度升高, 但未超过反应温度高限,于下一段间再与冷激气混合降温后 进入下段床层进行反应。冷激式绝热反应器在反应过程中流 量不断增大,各段反应条件略有差异,气体的组成和空速都 不同。
水
3
乙炔尾气
99..99%甲 醇
杂醇油
➢低压法合成甲醇工艺流程图
2023/11/2
甲醇生产
4
2 三相流化床合成甲醇工艺流程
工艺流程(图) 优点:单程转化率高,出口甲醇1520%(V);循环气量少;动力消耗低;反 应器结构简单;温度均匀易于控制。 缺点:三相互相夹带不易分离。
2023/11/2
甲醇生产
2023/11/2
甲醇生产
2
1.低压法合成甲醇流程示意图
O2 水汽
乙炔尾气
400
加热炉
2023/11/2
220000
KK2C2COO3 3
转转 化化 器器
脱脱硫硫塔塔 CCOO2空空 放空
99.85%
分分
脱脱
精甲醇
离离
烃烃 精
器器
塔塔
馏 塔 杂醇油
粗粗甲甲醇醇槽槽
(2) 列管式等温反应器 该类反应器类似于列管式换热器, 其结构示意如图5-10所示。 催化剂装填于列管中,壳程走冷却水(锅炉给水)。反应热 由管外锅炉给水带走,同时产生高压蒸汽。通过对蒸汽压力
甲醇合成的工艺流程和设备

甲醇合成的工艺流程和设备甲醇是一种重要的化工原料,广泛应用于化工、医药、食品等领域。
甲醇的合成工艺流程主要包括天然气制甲醇和煤制甲醇两种。
以下将以天然气制甲醇为例,介绍甲醇的合成工艺流程和设备。
1. 甲醇合成工艺流程甲醇的合成主要通过气相合成法进行,该方法通过一系列复杂的催化反应将一氧化碳和氢气合成甲醇。
具体的工艺流程如下:- 天然气→天然气净化→变化转换反应→合成气→合成气净化→合成气改质→甲醇合成→甲醇回收2. 甲醇合成设备甲醇合成设备主要包括催化反应器、冷凝器、分离塔等:- 催化反应器:将一氧化碳和氢气催化反应生成甲醇,需要具有较高的反应活性和选择性。
- 冷凝器:用于冷却和凝结合成气中的甲醇,使其形成液体甲醇。
- 分离塔:用于将液体甲醇从残余的气相中分离出来,保证甲醇的纯度和回收率。
3. 甲醇生产过程甲醇生产过程主要包括天然气的催化转变、合成气的制备、甲醇的合成和甲醇的回收等环节。
整个过程需要耗费大量的热能和电能,因此需要具备较为完备的能源设施和配套设备。
总的来说,甲醇的合成工艺流程较为复杂,需要涉及多个催化反应和分离过程,所需要的设备也比较繁杂。
企业在进行甲醇合成生产时,需要充分考虑到工艺流程和设备配置,确保生产过程的高效稳定。
甲醇是一种重要的化学品,其合成工艺的复杂性和对能源的依赖性使得甲醇工业在全球范围内备受关注。
天然气制甲醇是目前全球最为主流的甲醇生产工艺。
下面将详细介绍甲醇的合成工艺流程和设备,以及在甲醇生产过程中可能出现的关键技术和挑战。
4. 甲醇合成过程甲醇的合成工艺主要涉及以下几个过程:4.1 天然气制备合成气首先,天然气需要在天然气净化设备中进行净化处理,去除其中的硫化氢、二氧化碳和水等杂质。
通过石灰石和干燥剂的吸附、脱硫等处理,可使天然气达到合成气制备的要求。
然后,经催化转化反应,天然气中的甲烷和水蒸气进行高温反应,生成一氧化碳和氢气,形成合成气。
4.2 合成气的制备合成气是由一氧化碳和氢气所组成的气体混合物,它是甲醇合成的重要中间产物。
甲醇合成的工艺流程
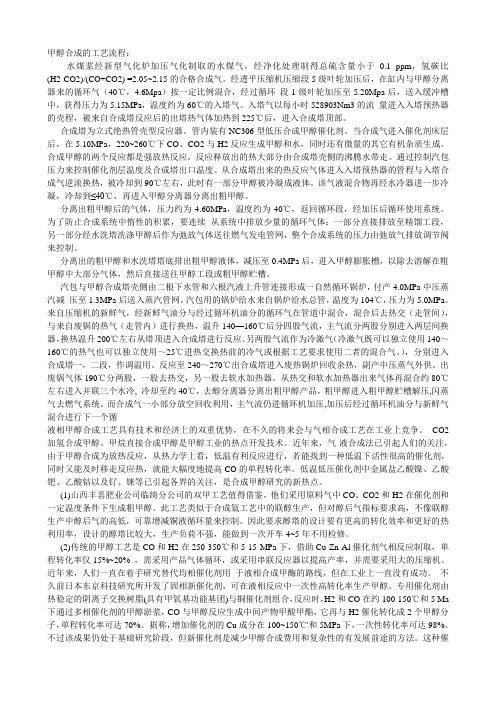
甲醇合成的工艺流程:水煤浆经新型气化炉加压气化制取的水煤气,经净化处理制得总硫含量小于0.1 ppm,氢碳比(H2-CO2)/(CO+CO2) =2.05~2.15的合格合成气。
经透平压缩机压缩段5级叶轮加压后,在缸内与甲醇分离器来的循环气(40℃,4.6Mpa)按一定比例混合,经过循环段1级叶轮加压至5.20Mpa后,送入缓冲槽中,获得压力为5.15MPa,温度约为60℃的入塔气。
入塔气以每小时528903Nm3的流量进入入塔预热器的壳程,被来自合成塔反应后的出塔热气体加热到225℃后,进入合成塔顶部。
合成塔为立式绝热管壳型反应器。
管内装有NC306型低压合成甲醇催化剂。
当合成气进入催化剂床层后,在5.10MPa,220~260℃下CO、CO2与H2反应生成甲醇和水,同时还有微量的其它有机杂质生成。
合成甲醇的两个反应都是强放热反应,反应释放出的热大部分由合成塔壳侧的沸腾水带走。
通过控制汽包压力来控制催化剂层温度及合成塔出口温度。
从合成塔出来的热反应气体进入入塔预热器的管程与入塔合成气逆流换热,被冷却到90℃左右,此时有一部分甲醇被冷凝成液体。
该气液混合物再经水冷器进一步冷凝,冷却到≤40℃,再进入甲醇分离器分离出粗甲醇。
分离出粗甲醇后的气体,压力约为4.60MPa,温度约为40℃,返回循环段,经加压后循环使用系统。
为了防止合成系统中惰性的积累,要连续从系统中排放少量的循环气体:一部分直接排放至精馏工段,另一部分经水洗塔洗涤甲醇后作为弛放气体送往燃气发电管网,整个合成系统的压力由弛放气排放调节阀来控制。
分离出的粗甲醇和水洗塔塔底排出粗甲醇液体,减压至0.4MPa后,进入甲醇膨胀槽,以除去溶解在粗甲醇中大部分气体,然后直接送往甲醇工段或粗甲醇贮槽。
汽包与甲醇合成塔壳侧由二根下水管和六根汽液上升管连接形成一自然循环锅炉,付产4.0MPa中压蒸汽减压至1.3MPa后送入蒸汽管网。
汽包用的锅炉给水来自锅炉给水总管,温度为104℃,压力为5.0MPa。
合成甲醇工艺流程
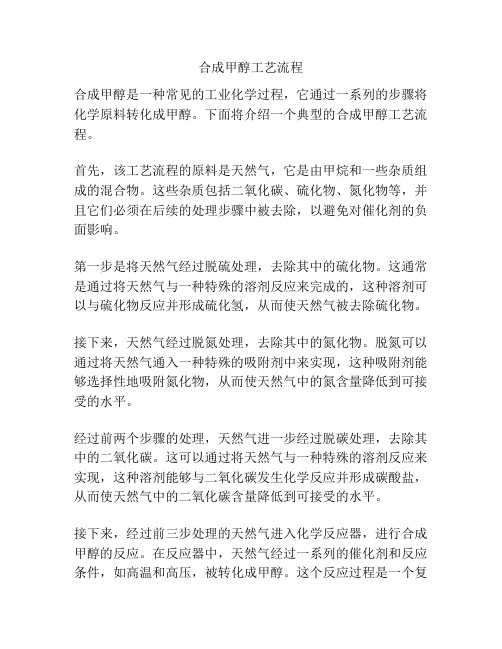
合成甲醇工艺流程合成甲醇是一种常见的工业化学过程,它通过一系列的步骤将化学原料转化成甲醇。
下面将介绍一个典型的合成甲醇工艺流程。
首先,该工艺流程的原料是天然气,它是由甲烷和一些杂质组成的混合物。
这些杂质包括二氧化碳、硫化物、氮化物等,并且它们必须在后续的处理步骤中被去除,以避免对催化剂的负面影响。
第一步是将天然气经过脱硫处理,去除其中的硫化物。
这通常是通过将天然气与一种特殊的溶剂反应来完成的,这种溶剂可以与硫化物反应并形成硫化氢,从而使天然气被去除硫化物。
接下来,天然气经过脱氮处理,去除其中的氮化物。
脱氮可以通过将天然气通入一种特殊的吸附剂中来实现,这种吸附剂能够选择性地吸附氮化物,从而使天然气中的氮含量降低到可接受的水平。
经过前两个步骤的处理,天然气进一步经过脱碳处理,去除其中的二氧化碳。
这可以通过将天然气与一种特殊的溶剂反应来实现,这种溶剂能够与二氧化碳发生化学反应并形成碳酸盐,从而使天然气中的二氧化碳含量降低到可接受的水平。
接下来,经过前三步处理的天然气进入化学反应器,进行合成甲醇的反应。
在反应器中,天然气经过一系列的催化剂和反应条件,如高温和高压,被转化成甲醇。
这个反应过程是一个复杂的化学过程,通过控制反应条件和催化剂的选择,可以提高甲醇的产率和纯度。
最后,合成的甲醇经过分离和净化步骤,得到高纯度的甲醇产品。
这通常涉及蒸馏、吸收、结晶等过程,以去除其中的杂质和不纯物。
这样,最终得到的甲醇可以应用于各种领域,如化学工业、能源行业和医药等。
总结起来,合成甲醇的工艺流程包括脱硫、脱氮、脱碳、合成反应和产品净化等步骤。
这些步骤确保天然气中的杂质被去除,并在化学反应过程中得到高产率和高纯度的甲醇产品。
这个工艺流程在甲醇生产中得到广泛应用,为相关行业提供了重要的化学原料。
- 1、下载文档前请自行甄别文档内容的完整性,平台不提供额外的编辑、内容补充、找答案等附加服务。
- 2、"仅部分预览"的文档,不可在线预览部分如存在完整性等问题,可反馈申请退款(可完整预览的文档不适用该条件!)。
- 3、如文档侵犯您的权益,请联系客服反馈,我们会尽快为您处理(人工客服工作时间:9:00-18:30)。
甲醇合成的工艺流程:水煤浆经新型气化炉加压气化制取的水煤气,经净化处理制得总硫含量小于0.1 ppm,氢碳比(H2-CO2)/(CO+CO2) =2.05~2.15的合格合成气。
经透平压缩机压缩段5级叶轮加压后,在缸内与甲醇分离器来的循环气(40℃,4.6Mpa)按一定比例混合,经过循环段1级叶轮加压至5.20Mpa后,送入缓冲槽中,获得压力为5.15MPa,温度约为60℃的入塔气。
入塔气以每小时528903Nm3的流量进入入塔预热器的壳程,被来自合成塔反应后的出塔热气体加热到225℃后,进入合成塔顶部。
合成塔为立式绝热管壳型反应器。
管内装有NC306型低压合成甲醇催化剂。
当合成气进入催化剂床层后,在5.10MPa,220~260℃下CO、CO2与H2反应生成甲醇和水,同时还有微量的其它有机杂质生成。
合成甲醇的两个反应都是强放热反应,反应释放出的热大部分由合成塔壳侧的沸腾水带走。
通过控制汽包压力来控制催化剂层温度及合成塔出口温度。
从合成塔出来的热反应气体进入入塔预热器的管程与入塔合成气逆流换热,被冷却到90℃左右,此时有一部分甲醇被冷凝成液体。
该气液混合物再经水冷器进一步冷凝,冷却到≤40℃,再进入甲醇分离器分离出粗甲醇。
分离出粗甲醇后的气体,压力约为4.60MPa,温度约为40℃,返回循环段,经加压后循环使用系统。
为了防止合成系统中惰性的积累,要连续从系统中排放少量的循环气体:一部分直接排放至精馏工段,另一部分经水洗塔洗涤甲醇后作为弛放气体送往燃气发电管网,整个合成系统的压力由弛放气排放调节阀来控制。
分离出的粗甲醇和水洗塔塔底排出粗甲醇液体,减压至0.4MPa后,进入甲醇膨胀槽,以除去溶解在粗甲醇中大部分气体,然后直接送往甲醇工段或粗甲醇贮槽。
汽包与甲醇合成塔壳侧由二根下水管和六根汽液上升管连接形成一自然循环锅炉,付产4.0MPa中压蒸汽减压至1.3MPa后送入蒸汽管网。
汽包用的锅炉给水来自锅炉给水总管,温度为104℃,压力为5.0MPa。
来自压缩机的新鲜气,经新鲜气油分与经过循环机油分的循环气在管道中混合,混合后去热交(走管间),与来自废锅的热气(走管内)进行换热,温升140—160℃后分四股气流,主气流分两股分别进入两层间换器,换热温升200℃左右从塔顶进入合成塔进行反应。
另两股气流作为冷激气(冷激气既可以独立使用140~160℃的热气也可以独立使用~25℃进热交换热前的冷气或根据工艺要求使用二者的混合气。
),分别进入合成塔一,二段,作调温用。
反应至240~270℃出合成塔进入废热锅炉回收余热,副产中压蒸气外供。
出废锅气体190℃分两股,一股去热交,另一股去软水加热器。
从热交和软水加热器出来气体再混合约80℃左右进入并联三个水冷, 冷却至约40℃,去醇分离器分离出粗甲醇产品,粗甲醇进入粗甲醇贮槽解压,闪蒸气去燃气系统。
而合成气一小部分放空回收利用,主气流仍进循环机加压,加压后经过循环机油分与新鲜气混合进行下一个循液相甲醇合成工艺具有技术和经济上的双重优势,在不久的将来会与气相合成工艺在工业上竞争。
CO2加氢合成甲醇、甲烷直接合成甲醇是甲醇工业的热点开发技术。
近年来,气-液合成法已引起人们的关注,由于甲醇合成为放热反应,从热力学上看,低温有利反应进行,若能找到一种低温下活性很高的催化剂,同时又能及时移走反应热,就能大幅度地提高CO的单程转化率。
低温低压催化剂中金属盐乙酸镍、乙酸钯、乙酸钴以及钌、铼等已引起各界的关注,是合成甲醇研究的新热点。
(1)山西丰喜肥业公司临绮分公司的双甲工艺值得借鉴,他们采用原料气中CO、CO2和H2在催化剂和一定温度条件下生成粗甲醇。
此工艺类似于合成氨工艺中的联醇生产,但对醇后气指标要求高,不像联醇生产中醇后气的高低,可靠增减铜液循环量来控制。
因此要求醇塔的设计要有更高的转化效率和更好的热利用率,设计的醇塔比较大,生产负荷不强,能做到一次开车4~5年不用检修。
(2)传统的甲醇工艺是CO和H2在250-350℃和5-15 MPa下,借助Cu-Zn-Al催化剂气相反应制取,单程转化率仅15%~20% ,需采用产品气体循环,或采用串联反应器以提高产率,并需要采用大的压缩机。
近年来,人们一直在着手研究替代均相催化剂用于液相合成甲酶的路线,但在工业上一直没有成功。
不久前日本东京科技研究所开发了固相新催化剂,可在液相反应中一次性高转化率生产甲醇。
专用催化剂由热稳定的阴离子交换树脂(具有甲氧基功能基团)与铜催化剂组合,反应时,H2和CO在约100-150℃和5 Ma 下通过多相催化剂的甲醇淤浆,CO与甲醇反应生成中间产物甲酸甲酯,它再与H2催化转化成2个甲醇分子,单程转化率可达70%。
据称,增加催化剂的Cu成分在100~150℃'和5MPa下,一次性转化率可达98%。
不过该成果仍处于基础研究阶段,但新催化剂是减少甲醇合成费用和复杂性的有发展前途的方法。
这种催化剂优于一些均相催化剂,因为它容易从液体产品中分离出来,在低压下的液相操作也使换热器和压缩机减少。
(3)一种由CO2生产甲醇的新工艺,已由韩国科技研究院(KIST)纳米技术研究中心正式开发。
现在1套为100 kg/ d的中试装置已经运转,在这种Camero工艺中,通过一种逆水-气转化反应,在600-700 ℃和大气压力下,采用ZnAl204催化剂,CO2与H2反应形成CO和H20。
在进入甲醇合成反应器之前,先将产物气体干燥除去H20。
在甲醇合成反应中,在250~300℃以及5~8 MPa下,采用CuO/ZnO/ZrO2/ Al2O3催化剂,CO和未反应的H2结合形成甲醇。
(4)为了克服传统甲醇合成工艺单程转化率低、循环比大、能耗高等缺点,日本东洋工程公司和三井东亚化学公司共同研发出一种新型节能降耗的多段内冷式径向流动甲醇合成塔,生产能力为2500 t/d,直径4700mm,高度为14100 mm,重量为420 t,压力降0.05 Ma,生产每t甲醇可回收热量2.5 GJ。
示范装置建成后,随后在特立尼达和多巴哥的1200 t/ d甲醇装置改造中,与原有的ICI冷塔平行安装了1台合成塔,完全达到了预期效果。
我国海南省海洋石油富岛化工公司60万吨/年甲醇装置中引进了该合成塔。
这种新型甲醇合成塔的优点是:(a)气体压力降小,压力降仅为普通轴向塔的1/10; (b)回收热量多;(c)温度控制合理,甲醇生产效率高,合成塔出口甲醇浓度高于8.5% ;(d)催化剂寿命长;(e)生产能力大。
(e)节能效果显著,由于降低了塔内压力降和气体循环速度,功率减少50%,从而节省了大量能量,合成循环系统的t甲醇热能耗从激塔的111.6 MJ降低到57.0MJ。
(5)粉煤气化制甲醇联产合成氨尿素的创新技术已经问世。
用纯氧加压气化生产甲醇,甲醇弛放气联产合成氨、尿素,是煤炭综合利用,转化为洁净能源和化肥产品的最有效途径之一,是一条节能、降耗、循环和环保的新型的氨醇生产工艺路线。
该工艺中,合成氨和甲醇生产用的CO+H2合成气由煤炭或烃类转化。
由于气化温度高达1400-1700℃,煤炭利用率可达99%,气体中仅含0.3%的CH4,而CO+H的产率达90%以上。
每t甲蹲在合成过程中产生弛放气282 m3,经变换后合成氨和尿素。
目前四川、山西、内蒙古、黑龙江、宁夏等许多地方都在兴建这种装置,此技术已呈现良好的发展势头。
(6)一种高效液相合成甲醇新工艺,已由空气产品和化学公司与伊斯曼化学公司合作成立的空气产品液相转换公司在最近获得成功。
该工艺实现了废物零排放,并可生产出高纯度的甲醇产品。
这种LPMEOH 工艺与传统工艺不同,使用的是由空气产品设计的淤浆泡罩塔反应器(SBCR) ,当合成气进入SBCR,粉末催化剂分散到惰性的矿物油中,在此环境中合成气在催化剂作用下生成甲醇。
LPMOH工艺可以处理来自煤气化的不同浓度的原料气体,可以吸收合成气中25%-50%的热值,并且不需要传统技术除去原料气中CO2的工艺步骤,可以生产出纯度99%的甲醇产品。
(7)美国商务部先进技术处(ATP)资助UOP公司开发甲烷液相制甲醇技术,在2005~2007年内该项目将耗资500万美元,其中A TP资助200万美元。
该项目将集中于甲烷低温工艺的开发。
UOP 称,如果该项目成功,将立即转入工业化生产。
预计该技术可将甲醇的生产成本从80美元/t下降至58美元/t,此外,投资费用、能耗和CO2副产也会分别下降50%、60%和33%。
据说该技术可以利用偏远地区的天然气建厂。
甲醇工区化工装置的目的和作用是:对煤气化装置来的粗煤气进行变换处理,以调整其氢气和一氧化碳的含量;通过低温甲醇洗装置对变换后的气体进行脱硫脱碳处理;然后再通过甲醇合成和精馏装置对净化后的气体进行甲醇合成和精制生产;最后对制得的精甲醇产品进行贮存及装车外运;同时,对低温甲醇洗脱除的克劳斯气进行硫磺回收;并对合成放出的弛放气进行氢回收,以达到节能降耗的目的。
氨压缩制冷装置是为低温甲醇洗装置配套的,其作用是为低温甲醇洗装置提供冷量,并在必要时为空分装置提供冷量支持。
第三节工艺原理及特点简介1、变换装置变换的原理是气体中的CO和水蒸汽在一定温度和压力条件下,在变换催化剂的作用下发生变换反应生成H2和CO2。
反应式如下:本变换装置采用的催化剂是宽温耐硫变换催化剂,采用的工艺是宽温耐硫部分变换工艺,这是根据粗煤气中:CO浓度高、含有硫化物和下游装置对原料气中CO浓度的要求来选取的。
该工艺的特点是:A、能抗原料气中硫化物。
对原料气中的硫化物只有下限规定,没有上限要求;B、采用粗煤气部分变换,操作灵活方便;C、蒸汽消耗低;D、热量回收利用率高。
(2)、低温甲醇洗其原理是以拉乌尔定律和亨利定律为基础,依据低温状态下的甲醇具有对H2S和CO2等酸性气体的溶解吸收性大、而对H2和CO溶解吸收性小的这种选择性,来脱除粗变换气中的H2S和CO2等酸性气体,从而达到净化粗变换气的目的。
低温甲醇洗工艺的特点是:A、工艺成熟,有多套大型装置长期稳定运行的经验;B、对原料气的净化程度较高;C、运行费用较低;D、洗涤用的甲醇溶剂容易获取。
(3)、硫回收装置硫回收装置采用的是三级克劳斯硫回收工艺,其原理是SO2和H2S在一定的温度下,在催化剂的作用下发生克劳斯反应生成单质硫和水,并放出热量。
其反应式如下:其特点是:A、工艺技术成熟;B、硫的回收率较高;C、操作方式灵活、操作弹性较大,可分别采用部分燃烧法和分流法来处理H2S含量高低不同的原料气。
(4)、氨压缩制冷制冷装置采用的是氨压缩制冷工艺,其制冷的原理是利用氨的压缩、冷凝、节流和蒸发形成循环来向外界提供冷量。
氨压缩制冷装置的特点是:A、设置有液氨深冷器,单位质量工质的制冷量增大,节省了气氨进入一级压缩的压缩功,达到了省功的目的;B、压缩机采用蒸汽透平驱动,提高蒸汽能量转换率,节省能耗;C、装置设备布置较紧凑,占地面积小。