LOI辊底式加热炉在济钢中厚板厂应用
7济钢中厚板调质生产线的开发与应用
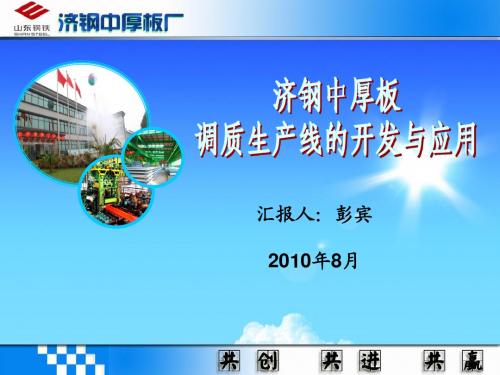
2.1 无氧化辊底式热处理炉
无氧化辊底式热处理炉在氮气保护下, 无氧化辊底式热处理炉在氮气保护下,由安装在辐射管内的自身预 热式烧嘴对钢板进行间接加热。允许(不推荐)最高炉温1000℃ 1000℃。 热式烧嘴对钢板进行间接加热。允许(不推荐)最高炉温1000℃。为保证 炉子的气密性,除采用钢结构加固外, 炉子的气密性,除采用钢结构加固外,在钢板入炉及出炉区各设计有带 门帘的门厅。炉内共布置154套烧嘴。为提高炉内温度控制精度, 154套烧嘴 门帘的门厅。炉内共布置154套烧嘴。为提高炉内温度控制精度,并降 低燃料消耗,将有效炉长分为20个温度控制区,并分别设检测热电耦。 20个温度控制区 低燃料消耗,将有效炉长分为20个温度控制区,并分别设检测热电耦。
钢板运行方向
图2:辊式淬火机淬火过程示意图
淬火机冷却系统设计为高、低压分段式喷水冷却。 淬火机冷却系统设计为高、低压分段式喷水冷却。高 压段喷水系统的喷嘴由三种形式,分别为水幕、 压段喷水系统的喷嘴由三种形式,分别为水幕、密集快速 冷却喷嘴和常规喷嘴,喷嘴布置方式为上下对称式。 冷却喷嘴和常规喷嘴,喷嘴布置方式为上下对称式。 1-6段为水幕喷嘴布置于淬火机辊道第3根后,喷水角 段为水幕喷嘴布置于淬火机辊道第3根后, 度和喷嘴距离钢板表面的距离可调节; 12段密集快速冷 度和喷嘴距离钢板表面的距离可调节;7-12段密集快速冷 却喷嘴设置在水幕喷嘴后,每组喷嘴各有3排高压喷水孔, 却喷嘴设置在水幕喷嘴后,每组喷嘴各有3排高压喷水孔, 以一定角度喷水;13、14段常规喷嘴设置在密集快速冷却 以一定角度喷水;13、14段常规喷嘴设置在密集快速冷却 喷嘴后,每组喷嘴各有1排高压喷水孔, 喷嘴后,每组喷嘴各有1排高压喷水孔,喷水孔倾斜角度 于密集喷嘴喷水孔倾斜角度一致;15-18段为低压段喷水 于密集喷嘴喷水孔倾斜角度一致;15-18段为低压段喷水 系统由38组低压喷嘴组成,每组喷嘴各有1排低压喷水孔。 38组低压喷嘴组成 系统由38组低压喷嘴组成,每组喷嘴各有1排低压喷水孔。 为了除去淬火后钢板表面残余冷却水, 为了除去淬火后钢板表面残余冷却水,淬火机出口安装有 吹扫装置。 吹扫装置。
LOI辊底式加热炉在济钢中厚板厂的应用

3 、钢板处理工序流程
3 . 1 上料 、对 中和长度及厚度测量 当新 板被送 到加热炉 的上料平 台上 后 , 板 的相关参数信 息通过操作 员输入控制 系统 或 是来三级 级 ME S ,一旦板 的相关参数信息 被 确认 ,板就 能被处理 了。首先钢板 移动到 热 处理炉前面 的对中装 置,在到对 中装 置 的 过 程中 ,板 的长度通过 两个光栅根据 辊道速 度 进行测量 。这样测得 的长度将会 与板的相 关参数信 息进 行 比较 ,如果有偏差 ,操作 员 需要再次确认 。板在上 料平 台上通 过对 中装 置进行调位 ,先用提升 轨道将板从 辊子平 台 上提起进 行中心对准调 位,然后 电机带着对 中凸轮装 置把钢板夹 正,当 凸轮缩 回后 ,板 又落到辊子上。 在热处理 炉的前面 安装一个刷 辊装置 , 当板通过 时,清洗板 的底部 以保证 没有任何 杂物黏附在热处理炉的辊子上。 这些工序 可 以在现 场手工启 动或在操 作
燃烧 系统包括烧 嘴、控制 阀、计量装 置 和关 闭系统 。烧 嘴与炉 内辐射 管是分开 的。 单只辐射 管是 由耐高温材料制 作成 的。烧 嘴 和辐 射管被安装在 炉壁 的左侧 和右侧 以及 炉 内辊 子的上面和 下面 。顶部 的辐射管装在 中 间,它们 的端部 用耐火支架悬 在炉顶上 ,底 部 的辐射管安在耐火砖制成的支座上面 。
应 用技 术
L O I 辊底式加热炉在济钢中厚板厂的应用
朱万 飞
济 南钢铁集 团检修公 司轧钢部 山东 济南 2 5 0 1 0 1
摘要 : 本文介绍 了辊底式炉的基本结构 ,工作流程 , 自 动化控制 ,燃烧控制以及二级模 型在加 热炉中应用,对 了解辊底 式加热炉有很大 帮助。 关键词 : 辊底武炉 淬火 燃烧控制 数学模型 热处理
宽厚板的加热、轧制和冷却技术

2一 0 取样贯 2 一扮线装! 2 一 1 2 冷娇机
图 3 德 国迪林根厚板厂工艺图
本也开始建立了发m优势。之后, 一些新工艺技 术、 控制系统和装备得到了开发与应用, 其中宽厚 板轧制新技术主要有 1高尺寸精度轧制技术。如r ) 射线测厚仪、 立 辊轧边机、 A 液压 WC系统、 工作辊移动( S + WR ) 强力弯辊( B 、 WR )成对交叉辊轧机(C 和连续可 P) 变凸度轧机(V ) 皮 C C等一术的应用, 提高了厚板尺寸 控制精度; 2平面形状控制伎术。如 M S ) A 平面形状控制 法、 狗骨轧制法及T P F 技术在日 芬兰、 本、 英国、 瑞 典等宽厚板轧机上得列了应用; 3控轧控冷技术。T C 工艺已成为宽厚板 ) MP 生产的主导工艺, 采用此技术生产的钢板已占3% 0 - 0 其板坯加热溢度为90 1 I, 5%, 5 一1 C 出炉温 5 0 度低于常规 轧制, 但混差小于 3'。此外, 0 C 宽厚板 生产品种多、 用途广、 现格大, 因而国外宽厚板生产 已 经普遍由 计算机进行 设定、 控制。
1 . x . 15 7 2 4
千叶厚板厂
全箱式炉型
8 3 0 3 . x . 5
加古川厚 h ’ / v
炉型
9 0 1 1 0 7 15 1
‘ ik声波探伤(/) _ 一 J 一 o A V_
热矫直、标记轧制批号 一 卜 一一
成检w 、扎,板志试打- , 品查 面尺 . 标 样印一 a r 品
L卜 部 查 试 打 冷 _外 松 、 样 印
一争 人工超声波探伤 ( , 供货状态) 一 1 一
最终检查伏 面、板形尺寸和标心
- il线装置 一 , - t ,
中厚板推钢式加热炉施工重点、难点及对策

中厚板推钢式加热炉施工重点、难点及对策步进梁式两大类。
根据燃料燃烧方式,又分为蓄热式和非蓄热式加热炉。
加热炉组成及施工的重点、难点通常的加热炉由炉膛、燃料输送和燃烧装置、供风系统、排风系统、排烟系统、冷却系统、热工检测与自动调节装置以及余热利用装置等组成。
炉膛、燃烧装置、冷却系统是推钢式加热炉施工中的重点,其中吊挂炉顶和全热滑块与纵水管的焊接是施工中的难点。
炉膛施工对策1 炉墙施工为了缩短烘炉时间,一种新型耐火材料防爆快干浇注料得到了广泛的应用。
(1) 浇注料的搅拌:在350搅拌机内每次投入200kg 防爆快干浇注料,干搅3~5min 使其充分搅匀,然后边搅拌边缓慢加入8%左右的水,待出浆后再搅拌2min ,即可进行浇注。
20min 内浇注并捣打完毕。
一般炉墙结构如图1 所示。
图1 炉墙结构示意图(2) 施工注意事项:①浇注料浇注施工前,为了减少轻质保温砖吸收防爆快干浇注料中的水分,通常在轻质保温砖外表面刷一遍防水沥青漆。
②浇注振动棒切勿碰锚固砖,以免使其折断。
(3) 膨胀缝作法:防爆快干浇注料炉墙膨胀缝分贯通缝和半贯通缝两种,一般每隔4. 2~4. 5 m留一个S型贯通缝,缝隙宽15mm 左右,采用20mm 厚氧化铝纤维毡填充;每隔1.2~1.5 m 留一个直线型半贯通缝(一般4 m2 左右应留一个半贯通缝) ,缝宽3mm ,采用PV 板作填料。
2 炉顶施工炉顶是加热炉最薄弱的地方,塌顶又是最常见的事故现象,因此炉顶施工要格外重视。
炉顶与炉墙是用20mm 厚氧化铝纤维毡隔开的,炉顶的重量完全由工字梁承担,并通过加热炉侧墙上的立柱传给设备基础。
炉顶结构见图2。
图2 炉顶结构示意图(1) 浇注防爆快干浇注料前,用木楔使挂钩与锚固砖紧密接触,并使其与炉顶保持垂直,但木楔不可楔得太紧,否则会使锚固砖吊耳处受力过大而折断。
浇注时应使用30 mm 振动棒并且放在两个锚固砖中间轻轻振动,振动时间要短,振动棒提出要缓慢。
大规格辊底式淬火炉设备在铝合金中厚板生产中的应用

大规格辊底式淬火炉设备在铝合金中厚板生产中的应用集团企业公司编码:(LL3698-KKI1269-TM2483-LUI12689-ITT289-大规格辊底式淬火炉设备在铝合金中厚板生产中的应用随着中国科技的进步,大飞机计划和强军战略的实施,高性能的铝合金中厚板材越来越多的被应用于航空、航天、舰船等高技术领域,辊底式淬火炉设备在铝合金中厚板生产过程中的重要性也越来越被众多铝加工企业所重视。
本文介绍了一台超大规格辊底式淬火炉在铝合金中厚板生产中的应用。
过去的几十年来,我国80%以上的铝合金中厚板都来自于进口,随着我国有色金属加工行业的快速发展,国内铝加工企业不断地更新设备和创新工艺,国产铝合金中厚板在航空航天、舰船、汽车和高速动车等领域得到了广泛的应用。
并随着我国经济转型升级节奏的不断加快,高性能的铝合金中厚板需求量也越来越大。
4000Mm宽幅、300000Mm长度以上的超大规格铝合金板材是我国目前可以生产的最大规格的中厚板,而超大规格的辊底式淬火炉设备是该材料生产过程中的关键设备,该机组的设计和建成将满足国内对高性能、大规格铝合金中厚板材产品的需求,可以更好地解决靠进口铝合金板材对我国航空、航天行业发展需要材料的制约问题。
辊底式淬火炉的工艺原理铝合金固溶处理的实质是将材料加热到特定温度使溶质充分地固溶在铝基体中,然后以最快的冷却速度冷却形成过饱和的固溶体,为随后的时效过程中获得最大的析出强化效果提供良好的条件。
辊底式淬火炉热处理机组就是借助辊底炉来实现多品种铝合金中厚板的固溶淬火处理。
辊底式淬火炉的设备组成和特性2.1来料品种及规格合金品种:2xxx、6xxx、7xxx系合金;厚度:6~250mm;宽度:1000~4350mm;长度:6000~38000mm;单板最大重量:20t;金属加热温度:200~580℃;炉气最高温度:600℃;板材冷却速度:≥20℃/s。
2.2设备组成和特性铝合金板材由天车吊至上料轨道,经轨道输送进入炉内加热区。
厚级别锅炉构建钢材的研发及运用

厚级别锅炉构建钢材的研发及运用1中厚板是济钢的主要产品三炼钢的中厚板生产线是我国先进的中厚板生产线之一,能够生产高纯净钢质、高强度、高韧性、焊接性能优良的高技术要求产品。
随着石油化工、大型电站的发展,锅炉用钢板的厚度、宽度不断提高,2005年济钢开始开发生产30~80 mm锅炉用厚规格20g钢板,开展了一系列工作,顺利取得了全国锅炉压力容器生产许可证,可批量供应厚规格20g钢板。
2厚规格的锅炉用钢板20g的研制2. 1技术要求20g钢板具有一定的强度,其塑性、韧性、成形和焊接工艺性能均很好,用于制造中、低压锅炉汽包和一些锅炉的大梁。
2. 1. 1化学成分20g钢板化学成分要求见1.120g钢板化学成分2. 1. 2力学性能20g钢板力学性能要求见2.2 20g钢板力学性能2. 2化学成分优化设计通过对济钢以前生产的30 mm以下的20g钢板的化学成分和力学性能进行统计分析,认真研究了微合金元素和生产工艺对性能的影响。
针对厚规格20g钢板时效、高温持久等性能要求,进行了如下主要成分设计。
1)Nb:钢中加入微量Nb、V、Ti等合金元素可明显细化晶粒,并产生强烈的沉淀强化作用,在厚规格20g的成分设计中采用Nb、Ti微合金元素,主要考虑这些元素在加热温度范围内具有足够的溶解度,而在钢材加工和冷却过程中又能产生特定大小的质点析出,从而使钢材性能发生变化。
其中Nb在钢中与C、N有极强的亲合力,形成稳定的化合物。
Nb相变时析出加速了γ-α转变行为,缩小了贝氏体、马氏体出现的几率,可形成稳定的F + P组织。
Nb在高温析出扩大了未再结晶区的范围,可实现严格的未再结晶区轧制,促进铁素体晶粒的细化。
含Nb钢在低温变形中延迟再结晶作用更大,但低温大压下量轧制的钢,Nb含量不需太高,半共格的NbCN析出可起到强烈的沉淀强化作用,有资料显示,0. 01%的Nb可提高强度50 MPa.在钢中加入微量的Nb,可以在保持同样的强度水平下降低碳当量,从而提高钢的可焊性和韧性。
济钢中板采用双倍R轧制工艺

济钢中板采用双倍R轧制工艺
孙浩;刘润坦
【期刊名称】《山东冶金》
【年(卷),期】1992(014)001
【总页数】3页(P33-35)
【作者】孙浩;刘润坦
【作者单位】不详;不详
【正文语种】中文
【中图分类】TG335.52
【相关文献】
1.济钢中板厂出口板轧制工艺改进 [J], 刘玉珍;董恩乐;程绍娟;冯旻;倪立森
2.济钢中板加热炉采用破号装炉工艺 [J], 孙浩
3.Q345B中板控制轧制工艺实践 [J], 陈润泽;陆淑娟
4.提高低碳微合金化中板延伸率的轧制工艺措施 [J], 彭正全
5.济钢中板厂Q460C板轧制工艺优化 [J], 刘玉珍;许方泉;董恩乐
因版权原因,仅展示原文概要,查看原文内容请购买。
2017

中国科技期刊数据库 工业C2015年42期 1272017合金淬火工艺的研究韩 明哈尔滨中飞新技术股份有限公司,黑龙江 哈尔滨 150060摘要:研究了2017T451状态合金板材经淬火、拉伸后的各项性能,通过改变辊底式淬火炉的淬火工艺参数等,改善产品的组织,使其得到最佳的性能,提高产品的实际质量。
关键词:辊底式淬火炉;2017合金;淬火 中图分类号:TG156.3,TG156.3 文献标识码:A 文章编号:1671-5810(2015)42-0127-022017合金属热处理可强化铝合金,是第一个获得工业应用的2×××系合金,主要品种有板材、挤压型材、冷加工棒材、冷加工线材、锻件等,Al-Cu-Mg 系合金是中等强度合金,其耐热性能和加工性能良好。
主要应用在通用机械零件、飞机、船舶、交通、建筑结构件、运输工具结构件、螺旋桨与配件等方面。
以往板材淬火用盐浴槽淬火,存在淬火板形无法控制、转移时间不规范、随机性大等问题。
而采用辊底式淬火炉淬火,很好地控制了淬火板形和淬火转移速度,但就目前来看,板材的力学性能有些偏下限。
本次工艺研究主要是为了解决2017合金20mm 厚度板材辊底炉淬火性能偏低的问题。
1 试验1.1 试验用料选用255×1500mm 规格半连续水冷铸造的2017合金铸锭,在现行工艺制度下热轧轧制成20mm 厚的板材,其化学成分(EN485标准)如表1所示:表1 化学成分(%)CuMgMnFeSiCrZnTi其他 Al 单个 合计4.09 0.61 0.61 0.7 0.62 0.10 0.20 0.10 0.05 0.15余量1.2 试验目标值淬火拉伸后板材的性能应满足EN485标准,其各项性能指标如下表2:表2 拉伸板材主要性能合金状态 厚度/mm Rm/MPa RP0.2/MPa 延伸率/% 不小于 不大于 最小 最小 最小 2017T4516 12.5 390 260 12 12.5 40 390 250 12 40100385240141.3 试验内容通过辊底式淬火炉对2017热轧板材进行淬火,同时分别从板材的固溶加热时间、淬火速度、试样送检间隔时间等因素进行试验,对板材的主要性能进行对比,选择较好的热处理制度。
- 1、下载文档前请自行甄别文档内容的完整性,平台不提供额外的编辑、内容补充、找答案等附加服务。
- 2、"仅部分预览"的文档,不可在线预览部分如存在完整性等问题,可反馈申请退款(可完整预览的文档不适用该条件!)。
- 3、如文档侵犯您的权益,请联系客服反馈,我们会尽快为您处理(人工客服工作时间:9:00-18:30)。
LOI辊底式加热炉在济钢中厚板厂的应用
摘要:本文介绍了辊底式炉的基本结构,工作流程,自动化控制,燃烧控制以及二级模型在加热炉中应用,对了解辊底式加热炉有很大帮助。
关键词:辊底式炉淬火燃烧控制数学模型热处理
1、引言
济钢于2007年建设一条厚板热处理生产线,该产线引进德国loi 公司技术,包括辊底式炉和连续淬火装置。
热处理炉将用于钢板的常化、奥氏体化和回火,在氮保护气氛下借助于辐射管通过间接加热对钢板进行热处理。
热处理炉全长59,74米,可对低合金结构钢、z型钢、船用钢、桥梁钢、管线钢、高强度钢等钢种进行处理,单个钢板最长可达15米,重量最大达14吨,温度最高至980℃,最大处理能为30吨/小时。
2、基本结构
我们的加热炉采用安装在顶部和底部的辐射管上的蓄热式烧嘴
对钢板进行加热、最高温度可以达到980℃。
2.1 炉壳
炉壳的设计各部分现场焊接在一起,炉壳的密封是用一块焊接钢板进行结构加固。
辊底式炉的入口和出口区域各有一个门廊(门帘)。
炉子中板子经过的直线区域上部和下部耐火的地方采用绝缘纤维阻塞。
炉壳还包括炉辊的支撑和带密封的烧嘴。
在炉子的每侧都有操作和维护平台,可以方便到达烧嘴区域、设备区域、观察孔
区域、传感器和热电偶等位置,方便维护。
在炉墙壁中,有维护通路门,以便进入炉内进行必要的清洁和修理操作。
这些门用带插销的钢板制作,方便拆装移动,并且用陶瓷纤维绝缘。
氮气入口沿着炉顶按固定的间距排列。
氮气在入口和出口门廊(门帘)处被排放。
为了减少氮气的消耗,炉子的上料和卸料将以最大速度进行,其它时间门关闭。
在上料和卸料区域,安装了2套用于对炉内的o2 含量检测的o2检测设备。
2.2炉内辊
炉内辊的尺寸根据处理钢板的最高温度980℃确定,能够承受炉内的热负荷及机械压力。
考虑上料的运输,炉内安装的109根辊的斜度是580mm。
辊子的壁厚是20mm,辊子的筒体离心浇注。
为了使炉内辊子达到好的密封效果,热处理炉的壁与辊子的两端端焊接在一起。
考虑辊子的密封和支撑,端部焊接在轴上。
为了防止热量从辊子中心向轴辐射,端部充填保温纤维。
在炉壳的外部,辊子的驱动端固定有轴承,当辊子受热膨胀时另一端可以通过轴承支座自由膨胀。
每个辊子都是通过传动电机和连接轴单独驱动,传动电机通过西门子m440变频机调速。
棍子以
0.3-20m/min的速度运行,在卸料区域,棍子能够以0.3-60m/min 的速度运行。
厚的板子需要不超过0.3m/min的速度移动。
钢板在炉内移动方式采用游荡的方式(例如,向前1.5m向后1m)。
在热处理炉无负荷时,棍子会前后摆动(大概1.5m左右),这样辊子始终来回移动不下垂。
2.3 燃烧系统
燃烧系统包括烧嘴、控制阀、计量装置和关闭系统。
烧嘴与炉内辐射管是分开的。
单只辐射管是由耐高温材料制作成的。
烧嘴和辐射管被安装在炉壁的左侧和右侧以及炉内辊子的上面和下面。
顶部的辐射管装在中间,它们的端部用耐火支架悬在炉顶上,底部的辐射管安在耐火砖制成的支座上面。
3、钢板处理工序流程
3.1上料、对中和长度及厚度测量
当新板被送到加热炉的上料平台上后,板的相关参数信息通过操作员输入控制系统或是来三级级mes,一旦板的相关参数信息被确认,板就能被处理了。
首先钢板移动到热处理炉前面的对中装置,在到对中装置的过程中,板的长度通过两个光栅根据辊道速度进行测量。
这样测得的长度将会与板的相关参数信息进行比较,如果有偏差,操作员需要再次确认。
板在上料平台上通过对中装置进行调位,先用提升轨道将板从辊子平台上提起进行中心对准调位,然后电机带着对中凸轮装置把钢板夹正,当凸轮缩回后,板又落到辊子上。
在热处理炉的前面安装一个刷辊装置,当板通过时,清洗板的底部以保证没有任何杂物黏附在热处理炉的辊子上。
这些工序可以在现场手工启动或在操作台启动。
3.2上料及在热处理炉内的运动
在跟踪系统确认出热处理炉上料区域有足够的空间时,炉门将会
被打开,板将以最大速度(20m/min)进行输送上料。
当板通过后炉门将会被关闭。
板在热处理炉内的通过时间取决于板的厚度、宽度、目标温度和保持时间,此时间由plc系统控制。
通过监视炉内辊道速度来跟踪钢板通过热处理炉的过程。
通过沿炉子长度方向安装的光栅装置周期性的对板子的位置进行校正。
板子不断的被移动,但是一旦回火板的厚度超过80mm时,板的移动将产生振荡现象。
3.3 热处理炉卸料并完成淬火
板子在炉内的停留时间是确定的情况下,每个板在经过热处理炉时都会被跟踪监视直到板到达靠近卸料端。
此时考虑是否进行淬火处理,如进行淬火,需要一定的准备工作,系统要确认卸料平台是否有空间接受钢板。
如果目标温度经测高温计测得已经达到目标温度,高温保持时间经计算已经足够,板子才允许离开热处理炉。
如果板子要进行淬火处理,水阀门打开(震荡情况除外),淬火机上面的辊子调整到一定高度。
一旦准备就绪,出炉门将打开,板子将离开热处理炉以一定的速度进行淬火处理。
如果板子不进行淬火处理(正火处理、回火处理),那么上面的淬火辊平台将会上升在最高位,板将以最快速度通过淬火。
4、温度控制
加热炉采用焦炉煤气通过蓄热式的烧嘴进行加热,炉子包括20
个温度控制区域。
烧嘴以脉冲循环模式进行操作。
烧嘴的开停时间比例调节根据不同区域的热量需求确定。
一个区域不是所有的烧嘴
都同时关闭和同时点燃,而是周期性的循环式的关闭和点燃,以增加燃烧效率和改善板子的温度均匀性。
每个区域都装有一个热电偶,如果炉顶热电偶故障时,那么底部区域的热电偶将负责两个区域的温度控制。
顶部设置一个热值测定仪,燃烧系统能够补偿和调节变化的煤气热值。
20个区域的温度调控主要依靠plc系统中的pid调控软件执行控制。
热电偶的值通过线形转化器输入plc系统中。
pid控制器的输出值送到烧嘴脉冲循环控制执行器(在plc系统中)进行处理。
单个烧嘴的点火是通过阀门控制煤气和助燃空气,同时开启点火电极进行点火。
点火之后,点火电极监视火焰的燃烧情况。
烧嘴的工作状态和关闭状态值通过通讯送到plc系统中,这些信号在hmi中显示。
加热炉采用在线计算热处理炉内钢板温度的数学模型,利用该数字模型,可以计算钢板沿厚度方向上三个点的温度,即头部、中部和尾部的温度。
当有待退火的钢板进入装料辊道时,或者是操作人员输入相关的数据:长度、宽度、厚度、等级、目标卸料温度、停留时间或者由l3传输这些数据。
当这些钢板进入炉子时,跟踪系统便开始控制并调节炉子的速度。
只要钢板的端部进入炉子,就开始进行温度的计算。
钢板内部的温度分布用傅里叶微分方程转换成差分来说明,每一个钢板的温度计算必须在一秒钟内完成。
在钢板经过炉子的过程之中,为计算钢板的温度,炉子实际热电偶的温度十秒钟采样一次,同时考虑炉腔和炉墙对钢板表面的对流和传导传热。
将实际计算的钢板温度值与钢板设定温度曲线进行对比,设定温度曲线是根据等级、目标温度和保温时间进行优化,并储存在计算机中的。
当实际温度与钢板的设定温度之间存在偏差时,就调节炉子相应部位的温度,以减少实际温度与设定温度之间的偏差。
例如,如果生产线上出现故障,计算机将自动降低炉子的温度,这样就可以节省能源及减少太长的停工时间,当没有达到目标温度和保温时间,计算机将拒绝让钢板卸料。
5、总结
自2007年热处理炉建成以来,设备运行稳定,加热能力充足,温度控制精确,一直运行良好,生产了多种高附加值钢板,为济钢创造了巨大的经济效益。