盲埋孔板工艺流程
盲埋孔技术
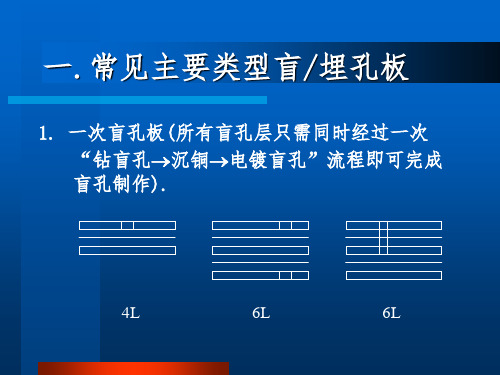
b.L1L5- 盲孔电镀: b.L1-2 & L5-6盲孔电镀: 根据lot卡及MI要求,选择电镀盲孔方法( lot卡及MI要求 根据lot卡及MI要求,选择电镀盲孔方法(lot 卡及MI会指明),根据板厚及盲孔孔径一般有 卡及MI会指明),根据板厚及盲孔孔径一般有 MI会指明),根据板厚及盲孔孔径 三种方法可选择: 三种方法可选择: - L1-2 & L5-6全铜面与盲孔一起板电. L1L5- 全铜面与盲孔一起板电. L1,L6面贴膜 整面干膜曝光(不用菲林), 面贴膜, - L1,L6面贴膜,整面干膜曝光(不用菲林), L2,L5大铜面与盲孔一起板电 大铜面与盲孔一起板电. L2,L5大铜面与盲孔一起板电. L1,L6贴干膜 用盲孔开窗点菲林曝光, 贴干膜, - L1,L6贴干膜,用盲孔开窗点菲林曝光,冲 影后,L2,L5大铜面与盲孔一起板电 大铜面与盲孔一起板电. 影后,L2,L5大铜面与盲孔一起板电.
一.常见主要类型盲/埋孔板 常见主要类型盲/
1. 一次盲孔板(所有盲孔层只需同时经过一次 一次盲孔板( 钻盲孔→沉铜→电镀盲孔” “钻盲孔→沉铜→电镀盲孔”流程即可完成 盲孔制作). 盲孔制作).
4L
6L
6L
二次盲孔板(需经过两次“钻盲孔→沉铜→ 2. 二次盲孔板(需经过两次“钻盲孔→沉铜→ 电镀盲孔”流程才可以完成盲孔制作). 电镀盲孔”流程才可以完成盲孔制作).
(3).流程解析: (3).流程解析: 流程解析 a.钻L1-2&L7- 盲孔: a.钻L1-2&L7-8盲孔: L1-2&L7- 盲孔钻带须加补偿. - L1-2&L7-8盲孔钻带须加补偿. 板边须有层数标志. - 板边须有层数标志. b.L1-2&L7-8盲孔电镀: b.L1-2&L7- 盲孔电镀: 与正常图电要求可能不一样,须依lot lot卡 - 与正常图电要求可能不一样,须依lot卡 MI要求做 要求做. 及MI要求做.
制作HDI盲埋孔板的基本流程

制作HDI盲埋孔板的基本流程一.概述:HDI板,是指High Density Interconnect,即高密度互连板,是PCB行业在20世纪末发展起来的一门较新的技术。
传统的PCB板的钻孔由于受到钻刀影响,当钻孔孔径达到0.15mm时,成本已经非常高,且很难再次改进。
而HDI板的钻孔不再依赖于传统的机械钻孔,而是利用激光钻孔技术。
(所以有时又被称为镭射板。
)HDI板的钻孔孔径一般为3-5mil(0.076-0.127mm),线路宽度一般为3-4mil(0.076-0.10mm),焊盘的尺寸可以大幅度的减小所以单位面积内可以得到更多的线路分布,高密度互连由此而来。
HDI技术的出现,适应并推进了PCB行业的发展。
使得在HDI板内可以排列上更加密集的BGA、QFP等。
目前HDI技术已经得到广泛地运用,其中1阶的HDI已经广泛运用于拥有0.5PITCH的BGA的PCB制作中。
HDI技术的发展推动着芯片技术的发展,芯片技术的发展也反过来推动HDI技术的提高与进步。
目前0.5PITCH的BGA芯片已经逐渐被设计工程师们所大量采用,BGA的焊角也由中心挖空的形式或中心接地的形式逐渐变为中心有信号输入输出需要走线的形式。
所以现在1阶的HDI已经无法完全满足设计人员的需要,因此2阶的HDI开始成为研发工程师和PCB制板厂共同关注的目标。
1阶的HDI技术是指激光盲孔仅仅连通表层及与其相邻的次层的成孔技术,2阶的HDI技术是在1阶的HDI技术上的提高,它包含激光盲孔直接由表层钻到第三层,和表层钻到第二层再由第二层钻到第三层两种形式,其难度远远大于1阶的HDI技术。
二.材料:1、材料的分类a.铜箔:导电图形构成的基本材料b.芯板(CORE):线路板的骨架,双面覆铜的板子,即可用于内层制作的双面板。
盲埋孔技术

埋盲孔技术
工艺能力 层次:18层max 最小孔径:0.10mm(激光钻孔) 0.15mm(机械钻孔) 厚径比:<12:1(机械钻孔),>0.75:1(激光钻孔)
埋盲孔技术
•埋盲孔设计建议
制作难度与成本,HDI激光埋盲孔板均高与多次层压埋盲孔 板.尽量避免设计交叠埋盲孔.
多次层压盲孔板
HDI激光孔板
埋盲孔技术
•埋盲孔板设计建议
1、金属化孔与线的连接 金属化孔通过焊盘与线连接: 设计焊环宽度=最小完成焊环宽度+孔位公差+蚀刻公差 焊盘直径=钻刀直径+2 x 最小完成焊环宽度+孔位公差+蚀刻公差 最小完成焊环宽度:0.025mm (IPC二级标准) 孔位公差:+/-0.075mm 蚀刻公差:+/-0.025mm 当间距允许时常以加泪滴盘的 方式保证焊盘与线的安全电气 连接。
埋盲孔技术
•埋盲孔板设计建议
空白区设计要点 –内层不要留大面积的基材区,否则板内应 力不均匀,易翘曲,压板时铜箔易起皱; –外层线路要尽量均匀,不要留大面积的基 材区(可用铺辅助无功能的方盘填充), 否则电镀不均,PTH孔径、线路铜厚会相差 较大。
大面积基材,NG
设置铜皮,OK
埋盲孔技术
•埋盲孔板设计建议
1、层结构最好为中心对称以防止因涨缩不一致导致PCB板严重翘曲。 2、尽量使用一种芯板厚度。 3、内层尽量使用一种铜厚,芯板两面铜厚尽量一致。 4、芯板与半固化片尽量使用常用规格。 5、埋孔孔径,建议0.30mm-0.50mm,过大或过小都不利于树脂塞孔; 6、埋盲孔最小焊环0.15mm,激光盲孔,最小焊环0.10mm
埋盲孔技术
•埋盲孔板设计建议
1、层结构最好为中心对称以防止因涨缩不一致导致PCB板严重翘曲。 2、尽量使用一种芯板厚度。 3、内层尽量使用一种铜厚,芯板两面铜厚尽量一致。 4、芯板与半固化片尽量使用常用规格。 5、埋孔孔径,建议0.30mm-0.50mm,过大或过小都不利于树脂塞孔; 6、埋盲孔最小焊环0.15mm,激光盲孔,最小焊环0.10mm
《盲埋孔制作工艺》课件

盲埋孔的加工
材料准备
选择合适的材料,如混凝土、钢筋等。
施工工艺
采用钻孔、浇筑等工艺进行盲埋孔的加工。
安全注意事项
提醒施工人员注意安全措施,如佩戴安全帽、保护眼睛等。
质量检验与验收
介绍盲埋孔制作完成后进行的质量检验和验收标准,确保孔位准确、结构牢 固。
案例展示及总结
成功案例展示
展示盲埋孔制作成功应用的实 际案例。
制作流程步骤
1
准备工作
清理施工区域,检查工具和材料。
孔位测量与标注
2
使用仪器测量孔位和确定标注点。
3
盲埋孔的加工
采用钻孔等工艺制作盲埋孔。
质量检验与验收
4
对制作的盲埋孔进行质量检验和最终 的验收。
孔位测量与标注
详细介绍盲埋孔的孔位测量方法和标注的重要性,包括使用仪器、计算孔位 坐标、标记工艺等。
经验总结
总结盲埋孔制作工艺中的关键 点和经验教训。
发展前景
展望盲埋孔制作工艺在未来的 发展前景和应用领域。
《盲埋孔制作工艺》
本PPT课件介绍了盲埋孔制作的工艺、需求分析、制作流程步骤、孔位测量 与标注、盲埋孔的加工、质量检验与验收、以及案例展示及总结。
工艺介绍
深入探讨盲埋孔制作的相关技术和方法,包括选材、孔位规划、施工原理等。
制作需求分析
详细分析盲埋孔的制作需求,包括孔径尺寸、深度要求、孔位布置等。
盲埋孔PCB的制作细节描述
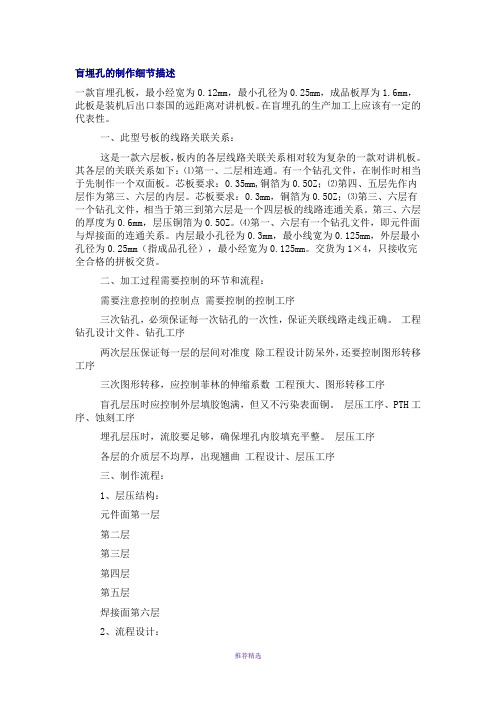
盲埋孔的制作细节描述一款盲埋孔板,最小经宽为0.12mm,最小孔径为0.25mm,成品板厚为1.6mm,此板是装机后出口泰国的远距离对讲机板。
在盲埋孔的生产加工上应该有一定的代表性。
一、此型号板的线路关联关系:这是一款六层板,板内的各层线路关联关系相对较为复杂的一款对讲机板。
其各层的关联关系如下:⑴第一、二层相连通。
有一个钻孔文件,在制作时相当于先制作一个双面板。
芯板要求:0.35mm,铜箔为0.5OZ;⑵第四、五层先作内层作为第三、六层的内层。
芯板要求:0.3mm,铜箔为0.5OZ;⑶第三、六层有一个钻孔文件,相当于第三到第六层是一个四层板的线路连通关系。
第三、六层的厚度为0.6mm,层压铜箔为0.5OZ。
⑷第一、六层有一个钻孔文件,即元件面与焊接面的连通关系。
内层最小孔径为0.3mm,最小线宽为0.125mm,外层最小孔径为0.25mm(指成品孔径),最小经宽为0.125mm。
交货为1×4,只接收完全合格的拼板交货。
二、加工过程需要控制的环节和流程:需要注意控制的控制点需要控制的控制工序三次钻孔,必须保证每一次钻孔的一次性,保证关联线路走线正确。
工程钻孔设计文件、钻孔工序两次层压保证每一层的层间对准度除工程设计防呆外,还要控制图形转移工序三次图形转移,应控制菲林的伸缩系数工程预大、图形转移工序盲孔层压时应控制外层填胶饱满,但又不污染表面铜。
层压工序、PTH工序、蚀刻工序埋孔层压时,流胶要足够,确保埋孔内胶填充平整。
层压工序各层的介质层不均厚,出现翘曲工程设计、层压工序三、制作流程:1、层压结构:元件面第一层第二层第三层第四层第五层焊接面第六层2、流程设计:工程设计时先开两个芯板,第一个芯板是1-2层,按第一个钻孔文件进行钻孔盲孔。
并按普通双面板的工艺流程制作到中检经过AOI存放;第二芯板是4-5层,开好一个芯板,按普通四层板的芯板制作工艺制作到中检经过AOI。
先将第二个芯板进行层压后,再按第二个钻孔文件钻埋孔,制作第3-6层的通孔和线路,此时按普通四层板的工艺经过除胶渣,制作3-6层的线路,到中检AOI。
多层盲埋孔板制作流程

3
東莞生益電子有限公司
二.材料:
1、材料的分类
1.铜箔:导电图形构成的基本材料 2.芯板(CORE):线路板的骨架,双面覆铜的板子,即可用 于内层制作的双面板。 3.半固化片(Prepreg):多层板制作不可缺少的材料,芯板 与芯板之间的粘合剂,同时起到绝缘的作用。 4.阻焊油墨:对板子起到防焊、绝缘、防腐蚀等作用。 5.字符油墨:标示作用。 6.表面处理材料:包括铅锡合金、镍金合金、银、OSP等等。
材料
5
東莞生益電子有限公司
2.2
最常用的FR-4半固化片材料的各种类型
材料名称 FR4
材料类型 7628 2116 3313 1080
原始介质厚 度(um) 193 122 99 74
材料
6
東莞生益電子有限公司
下图是SYE 制作的一个16层板的切面结构
材料
7
東莞生益電子有限公司
三.能力
SYE多层板的基本制程能力
内层线路做好的板子必须要经过黑化或棕化后才能进行层压。它是 对内层板子的线路铜表面进行氧化处理。一般生成的Cu2O为红色、 CuO为黑色,所以氧化层中Cu2O为主称为棕化、CuO为主的称为黑化。
流程
17
東莞生益電子有限公司
3. 黑化和棕化:
棕
流程
化
线
18
黑
化
线
東莞生益電子有限公司
4.层压:(PRESSING)
流程
23
東莞生益電子有限公司
5.钻盲埋孔:(DRILLING)
印制板上孔的加工形成有多种方式,目前使用最多的是 机械钻孔。机械钻孔就是利用钻刀高速切割的方式,在板子 (母板或子板)上形成上下贯通的穿孔。对于成品孔径在 8MIL及以上的穿孔,我们都可以采用机械钻孔的形式来加工。 目前来说,机械孔的孔径必须在8mil以上。 机械钻孔的形式决定了盲埋孔的非交叉性。就以我们这 块八层板而言,我们可以同时加工3 — 6层的埋孔、1—2层 的盲孔和7 — 8层的盲孔等等形式。但如果设计的是既有35层的埋孔,又有4-6层的埋孔,这样的设计在生产上将无法 实现。另外,从前面的层压我们可以了解到对称的必要性, 如果此时不是3-6层的埋孔而是3-5层或4-6层的埋孔,制作 难度与报废率将大幅提高,其成本将是3-6层埋孔的6倍以上。
盲孔、埋孔制造技术
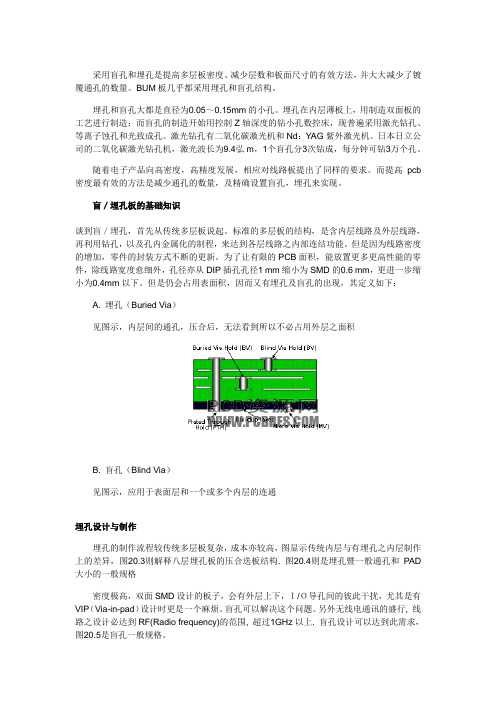
采用盲孔和埋孔是提高多层板密度、减少层数和板面尺寸的有效方法,并大大减少了镀覆通孔的数量。
BUM板几乎都采用埋孔和盲孔结构。
埋孔和盲孔大都是直径为0.05~0.15mm的小孔。
埋孔在内层薄板上,用制造双面板的工艺进行制造;而盲孔的制造开始用控制Z轴深度的钻小孔数控床,现普遍采用激光钻孔、等离子蚀孔和光致成孔。
激光钻孔有二氧化碳激光机和Nd:YAG紫外激光机。
日本日立公司的二氧化碳激光钻孔机,激光波长为9.4弘m,1个盲孔分3次钻成,每分钟可钻3万个孔。
随着电子产品向高密度,高精度发展,相应对线路板提出了同样的要求。
而提高pcb 密度最有效的方法是减少通孔的数量,及精确设置盲孔,埋孔来实现。
盲/埋孔板的基础知识谈到盲/埋孔,首先从传统多层板说起。
标准的多层板的结构,是含内层线路及外层线路,再利用钻孔,以及孔内金属化的制程,来达到各层线路之内部连结功能。
但是因为线路密度的增加,零件的封装方式不断的更新。
为了让有限的PCB面积,能放置更多更高性能的零件,除线路宽度愈细外,孔径亦从DIP插孔孔径1 mm缩小为SMD的0.6 mm,更进一步缩小为0.4mm以下。
但是仍会占用表面积,因而又有埋孔及盲孔的出现,其定义如下:A. 埋孔(Buried Via)见图示,内层间的通孔,压合后,无法看到所以不必占用外层之面积B. 盲孔(Blind Via)见图示,应用于表面层和一个或多个内层的连通埋孔设计与制作埋孔的制作流程较传统多层板复杂,成本亦较高,图显示传统内层与有埋孔之内层制作上的差异,图20.3则解释八层埋孔板的压合迭板结构. 图20.4则是埋孔暨一般通孔和PAD 大小的一般规格密度极高,双面SMD设计的板子,会有外层上下,I/O导孔间的彼此干扰,尤其是有VIP(Via-in-pad)设计时更是一个麻烦。
盲孔可以解决这个问题。
另外无线电通讯的盛行, 线路之设计必达到RF(Radio frequency)的范围, 超过1GHz以上. 盲孔设计可以达到此需求,图20.5是盲孔一般规格。
有关盲孔埋孔制作工艺
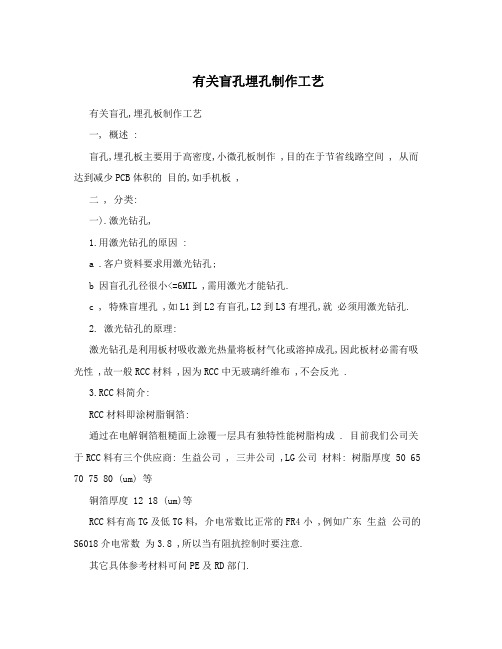
有关盲孔埋孔制作工艺有关盲孔,埋孔板制作工艺一, 概述 :盲孔,埋孔板主要用于高密度,小微孔板制作 ,目的在于节省线路空间 , 从而达到减少PCB体积的目的,如手机板 ,二 , 分类:一).激光钻孔,1.用激光钻孔的原因 :a .客户资料要求用激光钻孔;b 因盲孔孔径很小<=6MIL ,需用激光才能钻孔.c , 特殊盲埋孔 ,如L1到L2有盲孔,L2到L3有埋孔,就必须用激光钻孔.2. 激光钻孔的原理:激光钻孔是利用板材吸收激光热量将板材气化或溶掉成孔,因此板材必需有吸光性 ,故一般RCC材料 ,因为RCC中无玻璃纤维布 ,不会反光 .3.RCC料简介:RCC材料即涂树脂铜箔:通过在电解铜箔粗糙面上涂覆一层具有独特性能树脂构成 . 目前我们公司关于RCC料有三个供应商: 生益公司 , 三井公司 ,LG公司材料: 树脂厚度 50 65 70 75 80 (um) 等铜箔厚度 12 18 (um)等RCC料有高TG及低TG料, 介电常数比正常的FR4小 ,例如广东生益公司的S6018介电常数为3.8 ,所以当有阻抗控制时要注意.其它具体参考材料可问PE及RD部门.4. 激光钻孔的工具制作要求:A).激光很难烧穿铜皮,故在激光钻孔前要在盲孔位蚀出跟完成孔径等大的Cu Clearance .B). 激光钻孔的定位标记加在L2/LN-1层,要在MI菲林修改页注明。
C).蚀盲孔点菲林必须用LDI制作,开料要用LDI板材尺寸。
5.生产流程特点:A). 当线路总层数为N , L2—Ln-1 层先按正常板流程制作完毕, B). 压完板,锣完外围后流程改为:--->钻LDI定位孔--->干膜--->蚀盲孔点--->激光钻孔--->钻通孔 --->沉铜----(正常工序)。
6.其他注意事项:A).由于RCC料都未通过UL认证,故此类板暂不加UL标记. B).关于MI上的排板结构, 为避免把此类含RCC料排板当假层板排板(因为菲林房制做菲林假层板和正常板有别) ,我们在画排板结构时,要注意RCC料与L2或Ln-1层分开,例如SR2711/01排板:C).IPC-6016是HDI板标准:激光盲孔孔壁铜厚:0.4mil(min).焊锡圈要求 :允许相切如果PAD尺寸比孔径大5mil以下,要建议加TEARDROPD).板边>=0.8”二).机械钻盲/埋孔:1.适用范围:钻嘴尺寸>=0.20mm时可考虑用机械钻孔;2.关于盲埋孔的电镀方法(参照RD通告TSFMRD-113): A).正常情况下,任何层线路铜面只可1次板电镀+1次图形电镀; B). 正常情况下,全压板流程完成后,板厚>=80MIL ,通孔需板电镀+图形电镀,因此, 盲孔电镀时外层板面不能板电镀.C).满足上述两条件后,盲孔的电镀按如下方法进行:I).外层线路线宽度大于6MIL ,且通孔板厚小于80MIL时,在盲孔电镀中外层板面可整板电镀II).外层线路线宽大于6MIL , 但通孔板厚大于80MIL时,在盲孔电镀中外层板面需贴膜保护板面;III).外层线路线宽小于6MIL , 且通孔板厚>=80MIL时,在盲孔电镀中外层板面需贴膜保护板面;3. 贴膜的方式:1) 盲孔纵横比<=0.8 (L/D)时,外层板面贴干膜整板曝光,内层盲孔板面整板电镀 , 2) 盲孔纵横比>0.8时(L/D) 时,外层板面贴干膜盲孔曝光, 需制作电镀曝点菲林或LDI曝光 ,内层盲孔板面整板电镀.4. 盲孔曝点的方法:1) 盲孔<=0.4MM (16MIL)时,用LDI曝盲孔,2) 盲孔>0.4MM (16MIL)时,用菲林曝盲孔,5. 埋孔贴膜方式 :1) 当埋孔面的线宽<=4MIL时,埋孔板面需贴膜曝点,2) 当埋孔面的线宽>4MIL时 , 埋孔板面直接板电镀 ,6. 注意事项 :1) 纵横比中 L/D : L=介质厚+铜厚 , D=盲孔/埋孔直径 .2) 盲孔/埋孔电镀菲林 : * 曝光点的直径D=D-6 (MIL) .*曝光点菲林加对位点 , 其坐标与外围参考孔一致 . 3) 需贴膜的盲孔在电镀时一般使用脉冲电流 (AC) .三.盲孔板需注意的一些特别要求 :1.树脂塞盲孔: 当埋孔尺寸较大时并且孔数较多, 压板时, 填满埋孔需要很多树脂, 为防止其影响压板厚度, 经R&D要求时, 可在压板前用树脂将埋孔预先塞住, 塞孔方式应可参照绿油塞孔.2. 外层有盲孔时 ,a. 因压板时外层会有胶流出 ,所以在压板后需要有一除胶工序;b. 因外层干膜前会清洁板面,有一磨板工序,化学沉铜很薄,仅 0.05MIL 到0.1MI 故很容易在磨板时磨掉, 所以我们会加一板电镀工序,加厚铜.其相关工序如 : 压板除胶钻孔沉铜板电镀干膜图形电镀 .3. 另外在做层数高的盲孔板时可能会到用PIN-LAM压板,但要注意只有 CORE 的厚度小于30MIL时, 我们的机器才能打PIN-LAM孔 , 例如 : PR4726010 ,我们用的就是普通压板 .4. 关于盲孔板板边 ,考虑有多次压板 ,及工艺孔较多 ,所以尽量把板边留到0.8”以上.5. 在写LOT卡时 ,关于副流程 ,即要写单个副流程的排板结构 ,还要在特别要求里写上主流程的排板结构 ,为的是方便下面工序.6. 在写LOT卡时 , 在有盲孔干膜是放在内层做或外层做,举例说明一下 :L 1L 2A如CORE的A厚度大于12MIL(不含铜厚) , 就放到外层做 , 如CORE的A厚度小于12MIL(不含铜厚) , 就放到内层做 ,。
- 1、下载文档前请自行甄别文档内容的完整性,平台不提供额外的编辑、内容补充、找答案等附加服务。
- 2、"仅部分预览"的文档,不可在线预览部分如存在完整性等问题,可反馈申请退款(可完整预览的文档不适用该条件!)。
- 3、如文档侵犯您的权益,请联系客服反馈,我们会尽快为您处理(人工客服工作时间:9:00-18:30)。
常规盲埋孔板示意图 12 • 6+2盲埋孔板示意图:
L4-5层 L6-7层
板件工艺流程12
• 1/2层:开料、钻机械盲埋孔、去毛刺、沉铜、板镀、 内层镀孔菲林、电镀镀孔、内层图形、内层蚀刻、内 层AOI、棕化、层压(与L5-8层压合)、钻孔、正常流 程(如1/2层没有盲孔,板件钻完LDI孔后转往内层图 形)
L2-3层 L5-6层
板件工艺流程8
• 1/4层:开料、钻LDI孔、内层图形、内层蚀刻 、内层AOI、棕化、层压(压制1/4层)、钻孔 (钻1/3、4/6层的盲孔)、去毛刺、沉铜、板 镀、内层镀孔菲林、电镀镀孔、内层图形、内 层蚀刻、内层AOI、棕化、层压(与L5-6层压 合)、除胶、钻孔、正常流程
常规盲埋孔板示意图 11
• 8层2阶盲埋孔板示意图:
L1层RCC L2层RCC
L4-5层
L7层RCC L8层RCC
板件工艺流程11
• 开料(4/5层)、钻LDI孔、内层图形、内层 蚀刻、内层AOI、棕化、层压(压制成3/6 层)、钻孔(钻2/6层埋孔)、沉铜、板镀 、内层镀孔菲林、电镀镀孔、内层图形、内 层蚀刻、内层AOI、棕化、层压(压制RCC 2/7 层)、钻孔、激光钻孔、沉铜、板镀、 内层镀孔菲林、电镀镀孔、内层图形、内层 蚀刻、内层AOI、棕化、层压(压制RCC 1/8 层)、钻孔、激光钻孔、正常流程(如 3/6层没有埋孔,板件钻完LDI孔后转往内层
板件工艺流程4
• 开料(2/3层)、钻LDI孔、内层图 形、内层蚀刻、内层AOI、棕化、层 压(压制RCC 层)、钻孔、激光钻 孔、正常流程
常规盲埋孔板示意图 5 6层HDI盲埋孔板示意图:
L1层RCC
L3-4层
L6层RCC
板件工艺流程5
• 开料(3/4层)、钻LDI孔、内层图形、 内层蚀刻、内层AOI、棕化、层压(压制 成2/5 层)、钻孔(钻2/5层埋孔)、沉 铜、板镀、内层镀孔菲林、电镀镀孔、 内层图形、内层蚀刻、内层AOI、棕化、 层压(压制RCC 层)、钻孔、激光钻孔 、正常流程(如2/5层没有埋孔,板件钻 完LDI孔后转往内层图形)
常规盲埋孔板示意图 7 3+3(RCC)盲埋孔板示意图:
2-3层 4-5层
板件工艺流程7
• 钻LDI孔、内层图形、内层蚀刻、内层AOI、棕化、层压(压制 RCC成1/3层与4/6层)、钻孔(钻1/3、4/6层的盲孔)、去毛刺 、沉铜、板镀、内层镀孔菲林、电镀镀孔、内层图形、内层蚀刻 、内层AOI、棕化、层压、除胶、钻孔、激光钻孔、正常流程
常规盲埋孔板示意图 3 2+2盲孔板示意图
L 1-2层
L 3-4层
板件工艺流程3
• 开料、钻盲孔、去毛刺、沉铜、板 镀、内层镀孔菲林、电镀镀孔、内 层图形、内层蚀刻、内层AOI、棕化 、层压、除胶、钻孔、正常流程
常规盲埋孔板示意图 4
• 4层HDI盲埋孔板示意图:
L1层RCC
L 2-3层
L4层RCC
• 开料(2/3层)、钻孔(2/3层盲孔 )、去毛刺、沉铜、板镀、内层镀 孔菲林、电镀镀孔、内层图形2/3层 线路、内层蚀刻、内层AOI、棕化、 层压1/3层、除胶、钻孔(1/3层通孔 )、正常流程
常规盲埋孔板示意图 2
3层板RCC压合盲孔示意图
RCC层
L2/3层
板件工艺流程2
• 开料(2/3层)、钻LDI孔、内层图 形、内层蚀刻、内层AOI、棕化、层 压(压制RCC 1/3层)、钻孔、激光 钻孔、正常流程
• 板件工艺流程2:( 无1-2层、5-6层盲孔) • 钻LDI孔、内层图形、内层蚀刻、内层AOI、棕化、层压(压1/3
层与4/6层)、钻孔(钻1/3、4/6层的盲孔)、去毛刺、沉铜、板 镀、内层镀孔菲林、电镀镀孔、内层图形、内层蚀刻、内层AOI 、棕化、层压、除胶、钻孔、正常流程
常规盲埋孔板示意图 8 • 4+2盲埋孔板示意图:
常规盲埋孔板示意图 6 • 6层盲埋孔板示意图:
L1-2层 L3-4层 L5-6层
板件工艺流程6
• 开料、钻机械盲埋孔、去毛刺、沉 铜、板镀、内层镀孔菲林、电镀镀 孔、内层图形、内层蚀刻、内层AOI 、棕化、层压、除胶、钻孔、正常 流程(如3/4层没有埋孔,内层芯板 在钻LDI孔后转往内层图形)
L2-3 L4-5 L8-9 L10-11
工程设计原则
1、对于孔径≤ 0.13mm,且介质层厚度≤ 100um的板件 采用激光钻孔的工艺进行制作。
2、对于HDI板,激光钻孔的焊盘应保证单边最小3.5mil 焊环 。
3、目前公司RCC规格:100um、65um 铜厚全为12um。 4、孔到导体最小距离:一次压合:9mil 、 二次或三次
盲埋孔板工艺流程
盲埋孔的结构
盲 孔
埋 孔
盲埋孔板件的特点
特点: 1. 消除大量通孔设计,提高布线密度和封装密度; 2. 使多层板内部互连结构设计多样化和复杂化; 3. 明显提高了多层板的可靠性及电子产品的电气性
能。
常规盲埋孔板示意图 1
1、层板一次压合盲孔示意图
L1层
L2/3层
板件工艺流程1
压合:10mil 5、激光钻孔孔径与介质层厚度:0.1mm激光孔径可加工
≤ 65T RCC、0.13mm激光孔径可加工≤100T RCC
• 开料(2/3、6/7层)、钻LDI孔、内层图 形、内层蚀刻、内层AOI、棕化、层压( 压制成1/4、5/8 层)、钻孔(钻1/4、 5/8层盲孔)、沉铜、板镀、内层镀孔菲 林、电镀镀孔、内层图形、内层蚀刻、 内层AOI、棕化、层压(压制1/8 层)、 除胶、钻孔、正常流程(如1/4或5/8层 没有盲孔,板件钻完LDI孔后转往内层图 形)
• 5/6层:开料、钻机械盲埋孔、去毛刺、沉铜 、板镀、内层镀孔菲林、电镀镀孔、内层图形 、内层蚀刻、内层AOI、棕化、层压(与L1-4 层压合)、除胶、钻孔、正常流程(如5/6层 没有盲孔,板件钻完LDI孔后转往内层图形)
常规盲埋孔板示意图 9 • 4+4盲埋孔板示意图:
L2-3层
L6-7层
板件工艺流程9
大于8层盲埋孔板的工程叠层设计
板件设计参照以上叠层设计与工 艺流程,板件在设计叠层结构时尽 量避免采用两张芯板直接压合,而 需采用芯板
尽量避免采用:
L1-2层 L3-4层 L5-6层 L7-8层 L9-10层 L11-12层
芯板+PP压合的方式:
常规盲埋孔板示意图 10 • 8层2阶HDI盲埋孔板示意图:
板件工艺流程10
• 开料(3/4、5/6层)、钻LDI孔、内层图 形、内层蚀刻、内层AOI、棕化、层压( 压制成2/7 层)、钻孔(钻2/7层埋孔) 、沉铜、板镀、内层镀孔菲林、电镀镀 孔、内层图形、内层蚀刻、内层AOI、棕 化、层压(压制RCC 层)、钻孔、激光 钻孔(1-2、1-3、7-8、6-8)、正常流程( 如2/7层没有埋孔,板件钻完LDI孔后转 往内层图形)
• 5/8层:开料(4/5、6/7层)、钻LDI孔、内层图形、 内层蚀刻、内层AOI、棕化、层压(压制5/8层)、钻 孔(钻5/8层的盲孔)、去毛刺、沉铜、板镀、内层镀 孔菲林、电镀镀孔、内层图形、内层蚀刻、内层AOI 、棕化、层压(与L1-2层压合)、除胶、钻孔、正常流 程(如5/8层没有盲孔,板件钻完LDI孔后转往内层图 形)