常用加工设备的技术参数
hec1600卧式加工中心技术参数

hec1600卧式加工中心技术参数HEC1600卧式加工中心技术参数HEC1600卧式加工中心是一种高精度、高效率的机床设备,广泛应用于航空航天、汽车制造、模具加工等领域。
下面我们将详细介绍该设备的技术参数。
1. 机床主轴HEC1600卧式加工中心采用的主轴为高速电主轴,最高转速可达15000转/分钟。
主轴具有较高的刚性和稳定性,能够满足各种加工要求。
2. 行程范围HEC1600卧式加工中心的X轴行程为1600mm,Y轴行程为1300mm,Z轴行程为1000mm。
这一行程范围足够大,能够满足大型工件的加工需求。
3. 工作台HEC1600卧式加工中心的工作台尺寸为1600mm×1300mm,承载能力为4000kg。
工作台采用T型槽设计,方便夹紧工件,确保加工稳定性。
4. 刀库HEC1600卧式加工中心配备了24个刀位的刀库,可以实现多刀具的自动换刀。
刀库采用伺服驱动,刀具换位快速准确,提高了生产效率。
5. 控制系统HEC1600卧式加工中心采用的是先进的数控系统,具有高度灵活性和稳定性。
该系统支持G代码和M代码编程,能够实现复杂零件的加工。
6. 快速移动速度HEC1600卧式加工中心的快速移动速度为30m/min,加工速度为15m/min。
快速移动速度的提高,能够显著提高加工效率,缩短生产周期。
7. 加工精度HEC1600卧式加工中心的定位精度为0.008mm,重复定位精度为0.005mm。
高精度的加工精度可以满足对零件精度要求较高的加工任务。
8. 冷却系统HEC1600卧式加工中心配备了冷却系统,能够及时降低机床温度,保证加工过程中的稳定性和精度。
9. 自动润滑系统HEC1600卧式加工中心自带自动润滑系统,能够对机床的各个润滑点进行定期润滑,保证机床的正常运行和寿命。
10. 外形尺寸HEC1600卧式加工中心的外形尺寸为4200mm×6200mm×3600mm,整机重量约为15吨。
平面磨床的加工参数
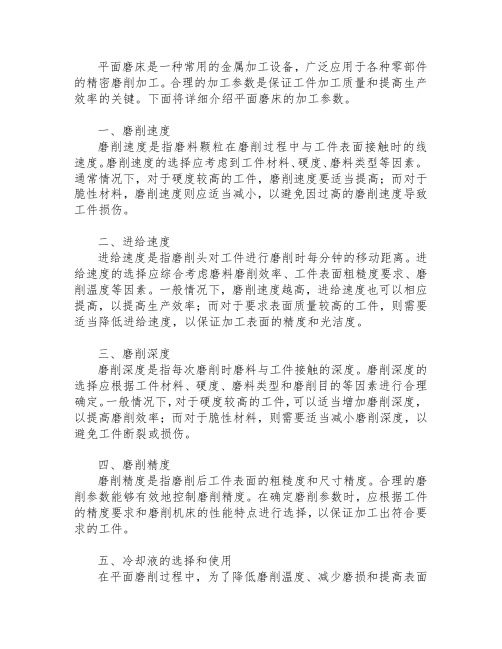
平面磨床是一种常用的金属加工设备,广泛应用于各种零部件的精密磨削加工。
合理的加工参数是保证工件加工质量和提高生产效率的关键。
下面将详细介绍平面磨床的加工参数。
一、磨削速度磨削速度是指磨料颗粒在磨削过程中与工件表面接触时的线速度。
磨削速度的选择应考虑到工件材料、硬度、磨料类型等因素。
通常情况下,对于硬度较高的工件,磨削速度要适当提高;而对于脆性材料,磨削速度则应适当减小,以避免因过高的磨削速度导致工件损伤。
二、进给速度进给速度是指磨削头对工件进行磨削时每分钟的移动距离。
进给速度的选择应综合考虑磨料磨削效率、工件表面粗糙度要求、磨削温度等因素。
一般情况下,磨削速度越高,进给速度也可以相应提高,以提高生产效率;而对于要求表面质量较高的工件,则需要适当降低进给速度,以保证加工表面的精度和光洁度。
三、磨削深度磨削深度是指每次磨削时磨料与工件接触的深度。
磨削深度的选择应根据工件材料、硬度、磨料类型和磨削目的等因素进行合理确定。
一般情况下,对于硬度较高的工件,可以适当增加磨削深度,以提高磨削效率;而对于脆性材料,则需要适当减小磨削深度,以避免工件断裂或损伤。
四、磨削精度磨削精度是指磨削后工件表面的粗糙度和尺寸精度。
合理的磨削参数能够有效地控制磨削精度。
在确定磨削参数时,应根据工件的精度要求和磨削机床的性能特点进行选择,以保证加工出符合要求的工件。
五、冷却液的选择和使用在平面磨削过程中,为了降低磨削温度、减少磨损和提高表面质量,通常需要使用冷却液。
不同的工件材料和磨削条件需要选择不同类型的冷却液,并合理控制冷却液的流量和温度,以达到最佳的磨削效果。
六、磨削轮修整磨削轮的修整对于平面磨床的加工效率和加工质量至关重要。
合理的修整参数能够保持磨削轮的良好状态,延长使用寿命,提高磨削精度和表面质量。
总之,平面磨床的加工参数对于磨削效率、加工质量和工件表面质量都有着重要的影响。
在实际加工中,操作人员需要根据具体的工件材料、形状和加工要求,合理选择和调整磨削参数,以确保磨削过程稳定、高效、精确,从而满足客户对工件加工质量的需求。
龙门常用加工参数

龙门常用加工参数1. 引言龙门加工是一种常见的数控加工方式,广泛应用于金属加工、木工加工等领域。
在进行龙门加工时,合理设置加工参数对于保证加工质量、提高生产效率至关重要。
本文将介绍龙门常用加工参数的相关知识,包括进给速度、主轴转速、进给倍率、切削深度等。
2. 进给速度进给速度是指工件在加工过程中的移动速度,通常用毫米/分钟(mm/min)来表示。
进给速度的选择要根据具体的工件材料、刀具类型和切削条件来确定。
一般来说,对于硬度较高的材料,进给速度应较低,以保证加工质量;而对于较软的材料,则可以适当提高进给速度,提高生产效率。
3. 主轴转速主轴转速是指刀具在加工过程中的转速,通常用转/分钟(rpm)来表示。
主轴转速的选择要根据刀具材料、刀具直径、切削深度等因素来确定。
一般来说,对于硬度较高的材料,主轴转速应较低,以防止刀具磨损过快;而对于较软的材料,则可以适当提高主轴转速,提高加工效率。
4. 进给倍率进给倍率是指实际进给速度与设定进给速度之间的比值。
进给倍率的选择要根据具体的加工要求和设备性能来确定。
一般来说,进给倍率为1时,实际进给速度与设定进给速度相等;而进给倍率小于1时,则表示实际进给速度小于设定进给速度,可以用于调整加工速度。
5. 切削深度切削深度是指刀具在一次切削中所能切掉的工件材料的厚度。
切削深度的选择要根据刀具的刀尖半径、刀具材料、工件材料等因素来确定。
一般来说,切削深度应适中,过大会增加切削力,导致刀具磨损过快;过小则会降低加工效率。
6. 切削速度切削速度是指切削过程中切削点的线速度,通常用米/分钟(m/min)来表示。
切削速度的选择要根据刀具材料、工件材料、切削深度等因素来确定。
一般来说,对于硬度较高的材料,切削速度应较低,以保证刀具寿命;而对于较软的材料,则可以适当提高切削速度,提高加工效率。
7. 刀具进给量刀具进给量是指刀具在单位时间内所移动的距离,通常用毫米/转(mm/rev)来表示。
加工中心的主要技术参数

加工中心的主要技术参数
加工中心是一种精密加工设备,可以完成多种复杂的加工操作。
在选择加工中心时,需要了解其主要技术参数,以便对设备进行有效的比较和选择。
以下是加工中心的主要技术参数:
一、加工尺寸
加工尺寸是指加工中心能够加工的最大工件尺寸,它通常由
X,Y,Z三轴行程限制。
在选择加工中心时,需要根据加工件的尺寸要求来选择合适的加工中心。
二、精度和稳定性
加工中心的精度和稳定性包括加工精度、定位精度、重复定位精度、表面光洁度等指标。
这些指标直接影响到加工件的质量和加工效率。
三、主轴转速
主轴转速是指加工中心主轴的最高转速,它决定了加工中心能够加工的材料种类和加工效率。
在选择加工中心时,需要根据加工件的材料要求来选择主轴转速。
四、进给速度
进给速度是指加工中心在加工过程中工具的移动速度,它决定了加工中心的加工效率。
在选择加工中心时,需要根据加工件的材料要求来选择适当的进给速度。
五、刀库容量
刀库容量是指加工中心刀具的存放数量,它决定了加工中心的加工灵活性和自动化程度。
在选择加工中心时,需要根据加工件的加工要求来选择合适的刀库容量。
六、控制系统
加工中心的控制系统决定了其加工精度和加工效率。
常见的控制系统有普通数控系统、高级数控系统等。
在选择加工中心时,需要选择控制系统与加工件要求相匹配的加工中心。
综上所述,加工中心的主要技术参数包括加工尺寸、精度与稳定性、主轴转速、进给速度、刀库容量和控制系统等方面。
在选择加工中心时,需要根据加工件的要求来确定各项技术参数,以获得最佳的加工效果和经济效益。
2.5m立车粗加工参数

2.5m立车粗加工参数1.引言本文将为您介绍2.5m立车粗加工参数的相关信息。
立车是一种常用的金属加工设备,用于加工大型工件和零件。
了解正确的粗加工参数对于保证加工效果和提高生产效率至关重要。
本文将讨论立车的切削速度、进给速度和切削深度等关键参数。
2.切削速度切削速度是指立车车刀在加工过程中切削过工件表面的速度。
切削速度的选择与工件材料的硬度、车刀材料和车刀尺寸等因素有关。
一般来说,硬度高的工件,切削速度应适当降低,以避免车刀过热和磨损过快。
切削速度的单位通常是米每分钟(m/mi n)。
3.进给速度进给速度指的是立车车刀在单位时间内移动的距离。
进给速度的选择与工件的尺寸和要求的加工精度有关。
一般来说,对于大型工件,进给速度应适当降低,以确保加工精度和安全性。
进给速度的单位通常是毫米每转(mm/r ev)。
4.切削深度切削深度是指立车车刀在一次切削中进入工件的深度。
切削深度的选择应根据工件的材料性质、切削效果和机床刚性等因素进行合理调整。
一般来说,切削深度不宜过大,以避免车刀过载和工件变形。
切削深度的单位通常是毫米(m m)。
5.切削力切削力是指立车车刀在切削过程中对工件施加的力。
切削力的大小直接影响到设备的稳定性和加工质量。
为了保证加工效果和设备安全,需要控制切削力在合理范围内。
切削力的单位通常是牛顿(N)。
6.补偿及调整在实际加工过程中,根据加工效果和工件要求可能需要进行补偿和调整。
例如,根据加工后的尺寸偏差情况,可以进行工件尺寸的微调。
此外,根据机床刚性和切削力的变化,可能需要调整切削参数以提高生产效率和加工质量。
7.粗加工参数的优化为了获得更好的加工效果和提高生产效率,需要进行粗加工参数的优化。
通过合理选择切削速度、进给速度和切削深度等参数,可以最大程度地发挥设备的性能和加工能力。
同时,合适的切削参数还可以降低工具磨损和工件变形的风险。
8.总结本文简要介绍了2.5m立车粗加工参数的相关内容,包括切削速度、进给速度、切削深度和切削力等关键参数。
6140车床参数
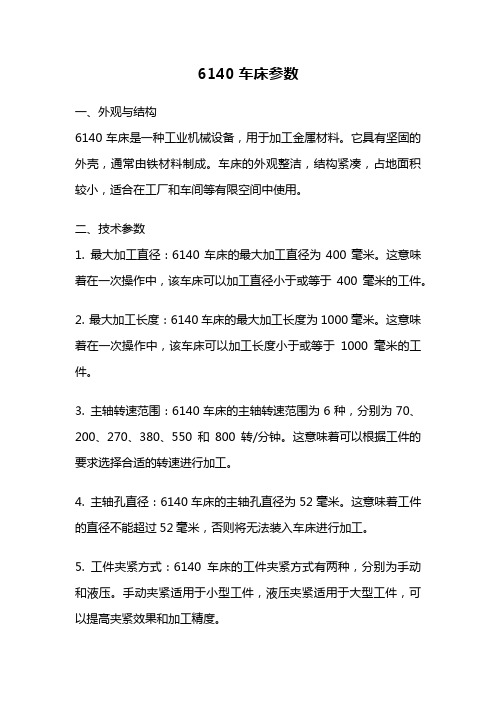
6140车床参数一、外观与结构6140车床是一种工业机械设备,用于加工金属材料。
它具有坚固的外壳,通常由铁材料制成。
车床的外观整洁,结构紧凑,占地面积较小,适合在工厂和车间等有限空间中使用。
二、技术参数1. 最大加工直径:6140车床的最大加工直径为400毫米。
这意味着在一次操作中,该车床可以加工直径小于或等于400毫米的工件。
2. 最大加工长度:6140车床的最大加工长度为1000毫米。
这意味着在一次操作中,该车床可以加工长度小于或等于1000毫米的工件。
3. 主轴转速范围:6140车床的主轴转速范围为6种,分别为70、200、270、380、550和800转/分钟。
这意味着可以根据工件的要求选择合适的转速进行加工。
4. 主轴孔直径:6140车床的主轴孔直径为52毫米。
这意味着工件的直径不能超过52毫米,否则将无法装入车床进行加工。
5. 工件夹紧方式:6140车床的工件夹紧方式有两种,分别为手动和液压。
手动夹紧适用于小型工件,液压夹紧适用于大型工件,可以提高夹紧效果和加工精度。
6. X轴移动范围:6140车床的X轴移动范围为220毫米。
这意味着工件可以在X轴上最大移动220毫米,以便进行不同位置的加工。
7. Z轴移动范围:6140车床的Z轴移动范围为1000毫米。
这意味着工件可以在Z轴上最大移动1000毫米,以便进行不同长度的加工。
8. 刀架数量:6140车床配备了两个刀架。
这意味着可以同时安装两种不同的刀具,以提高加工效率和灵活性。
9. 刀架行程:6140车床的刀架行程为X轴为220毫米,Z轴为1000毫米。
这意味着刀架可以在X轴和Z轴上进行相应的行程移动,以便进行不同位置和长度的加工。
三、应用领域6140车床广泛应用于机械加工行业。
它可以加工各种不同形状和尺寸的零件,如轴类、套类、齿轮类、螺纹类等。
该车床适用于批量生产和单件加工,在汽车制造、航空航天、电子设备等领域都有广泛的应用。
四、优势和特点1. 灵活性高:6140车床配备了两个刀架,可以同时安装两种不同的刀具,提高加工效率和灵活性。
立式和面机 技术参数

立式和面机技术参数立式和面机是两种常见的加工设备,它们在工业生产中起着重要的作用。
下面将分别介绍它们的技术参数和特点。
立式机床是一种将工件固定在工作台上,刀具在垂直方向上进行切削的机床。
它具有以下技术参数和特点:1. 主轴转速:立式机床的主轴转速通常较高,可以达到几千转每分钟。
高速转动的主轴可以提高切削效率和加工精度。
2. 功率:立式机床通常配备有较大功率的电机,以满足切削各种材料的需要。
高功率的电机可以提供足够的切削力和稳定的切削过程。
3. 行程:立式机床的行程较大,可以适应不同尺寸的工件加工。
行程的调节范围通常在数十毫米到数米之间。
4. 精度:立式机床具有较高的加工精度,其精度可达到亚毫米级别。
这得益于机床的稳定性和刚性,以及高精度的控制系统。
5. 自动化程度:立式机床通常配备有数字控制系统,可以实现自动化加工。
通过预先编写加工程序,可以实现工件的自动定位、自动换刀和自动加工等功能。
面机是一种将工件固定在工作台上,刀具在水平方向上进行切削的机床。
它具有以下技术参数和特点:1. 主轴转速:面机的主轴转速通常较低,一般在几百转每分钟。
较低的转速可以提供足够的切削力,并减少刀具磨损。
2. 功率:面机通常配备有适中功率的电机,以满足不同材料的切削要求。
适中的功率可以在保证切削效率的同时,避免过度热量和刀具磨损。
3. 行程:面机的行程较小,一般在数十毫米到数百毫米之间。
较小的行程适合加工较小尺寸的工件。
4. 精度:面机的加工精度通常较高,可以达到亚毫米级别。
这得益于机床的稳定性和刚性,以及高精度的控制系统。
5. 自动化程度:面机通常配备有数字控制系统,可以实现自动化加工。
通过预先编写加工程序,可以实现工件的自动定位、自动换刀和自动加工等功能。
立式机床和面机是两种常见的加工设备,它们在工业生产中具有重要的作用。
通过合理选择和使用这些设备,可以提高加工效率和加工精度,满足不同材料的加工需求。
加工中心常用参数

加工中心常用参数加工中心是一种高精度的金属加工设备,广泛应用于机械制造、航空航天、汽车制造等领域。
以下是加工中心常用的参数介绍。
1. 主轴转速:是指加工中心主轴的旋转速度,通常以转/分钟(rpm)来表示。
主轴转速与加工速度和切削速度有关,可以通过调整主轴转速来控制切削速度,以适应不同材料和加工任务的要求。
2. 进给速度:是指工件和刀具之间的相对运动速度。
进给速度通常以毫米/分钟(mm/min)或英寸/分钟(ipm)来表示。
进给速度与加工中心控制系统的指令速度有关,可以通过调整进给速度来控制切削速度和加工效率。
3. 刀具转速:是指刀具在切削中转动的速度。
刀具转速可以根据加工任务和材料特性来选择,通常以转/分钟(rpm)来表示。
4. 进给率:是指切削刀具每分钟被进给的距离。
进给率通常以毫米/转(mm/rev)或英寸/转(in/rev)来表示。
进给率与进给速度和主轴转速有关,可以通过调整进给率来控制切削速度和加工效率。
5. 切削深度:是指刀具在一次切削中每次接触工件的深度。
切削深度通常以毫米(mm)或英寸(in)来表示,可以通过调整进给速度和刀具转速来控制。
6. 切削速度:是指刀具在切削中与工件相对运动的速度。
切削速度通常以米/分钟(m/min)或英寸/分钟(ipm)来表示。
切削速度与主轴转速和刀具直径有关,可以通过调整主轴转速来控制。
7.加工精度:是指加工中心在加工过程中所能达到的精度水平。
加工精度可以通过加工中心的结构设计、传动系统、控制系统和加工工艺来保证。
8.加工面积:是指加工中心所能加工的最大工件尺寸。
加工面积通常以长、宽和高的尺寸范围来表示,可以通过加工中心的工作台尺寸来确定。
9.主轴功率:是指加工中心主轴所能输出的功率。
主轴功率通常以千瓦(kW)来表示,可以通过主轴的设计和驱动系统来确定。
10.刀库容量:是指加工中心所能容纳的刀具数量。
刀库容量可以根据加工需要和刀具的种类来选择,可以通过刀库的设计和布局来确定。