塔式鼓泡反应器混合法
塔式反应器选择与操作
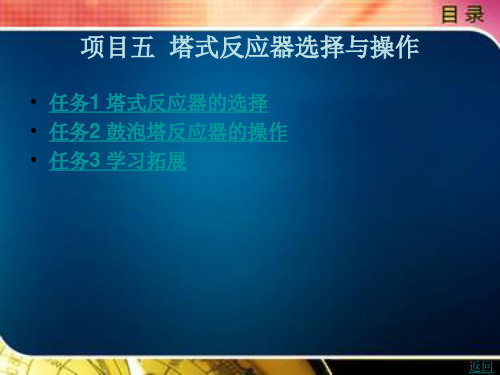
Hale Waihona Puke 上一页 下一页 返回任务1 塔式反应器的选择
• (1)塔底部的气体分布器。 • 分布器的结构要求使气体均匀分布在液层中;分布器鼓气管端的直径
项目五 塔式反应器选择与操作
• 任务1 塔式反应器的选择 • 任务2 鼓泡塔反应器的操作 • 任务3 学习拓展
返回
任务1 塔式反应器的选择
• 一、气液相反应动力学基础
• 在反应过程中至少有一种反应物在气相,另一些物质在液相,气相中 的反应物必须传递到液相中,然后在液相中发生化学反应,这种类型 的反应称为气液相反应。
上一页 下一页 返回
任务1 塔式反应器的选择
• 对塔设备的基本要求有以下几点: • (1)气液两相充分接触,相际间传热面积大。 • (2)生产能力大,即气液处理量大。 • (3)操作稳定,操作弹性大。 • (4)阻力小。 • (5)结构简单,制造、安装、维修方便,设备的投资及操作费用低。 • (6)耐腐蚀,不易堵塞。
上一页 下一页 返回
任务1 塔式反应器的选择
• 2.填料塔反应器结构 • 填料塔是以塔内装有大量的填料为相接触构件的气液传质设备。填料 • 塔的结构比较简单,如图5 -6所示。它由塔体、液体分布器、填料压
紧装置、填料层、液体收集与再分配装置和支撑栅板组成。 • 六、板式塔反应器特点与结构 • 1.板式塔反应器特点 • 板式塔反应器内部装有多块塔板,塔板的形式多为泡罩塔或筛板,液
上一页 下一页 返回
任务2 鼓泡塔反应器的操作
• (10)在确认工艺、设备等各种条件具备后方可开车。 • 2.正常开车 • (1)关闭所有入鼓泡塔的阀门,关闭各设备排污阀、去事故槽阀、烃
鼓泡塔反应器的特点结构、传质、工艺计算
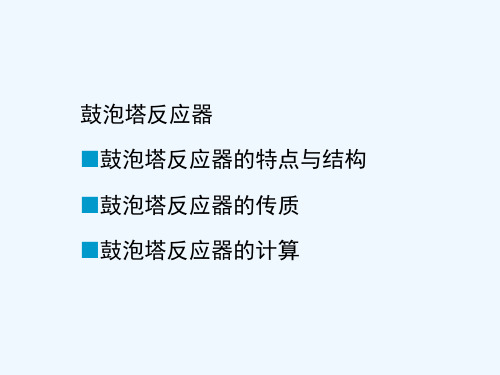
VOL
C AO x A rA
其中:(-rA)':实测的宏观速度。
VG:
VL G VG 1 G
VR: G 1 G
4、VE:
当液滴移动速度小于0.0001m/s HE=αED 当D<1.2m HE≥1m D≥1.2m αE=0.75
Re0 d0u0 G
G
<200
气泡群的直径的计算
a.当量比表面直径dVS:
b.体积平均直径dV:
c.几何平均直径dg:
含气率:
单位体积充气层内气体所点的体积分率。
εOG:静态气含率。液体不流动时的气含率。 εG:动态气含率。液体连续流动时的气含率。
比相界面a:
单位反应器有效体积气泡的表面积。m2/m3
计算液膜传质过程可用以下公式:
sh
k LA d b D LA
SCL
L DLA
L
Re b
dbuOGL
L
.072 1 0 bg3 0 .484 0 .339d Sh 2 .0 C Re S b CL 2/3 D LA
鼓泡塔的气体压降ΔP: ΔP=分布板小孔压降+鼓泡塔静压降 =
3 2 u 10 0 G H g R R 2 C 2
kpa
式中 C2=0.8 (小孔阻力系数) u0:小孔气速,m/s 鼓泡层密度,kg/m3
鼓泡塔的传质 一般气膜传质阻力较小,可以忽略,液膜传质阻力的大小决定了
传质速率的快慢。
鼓泡塔反应器
鼓泡塔反应器的特点与结构
鼓泡塔反应器的传质
鼓泡塔反应器的计算
鼓泡塔反应器鼓泡塔反应器的特点与结构 特点: 塔内充满液体,气体从反应器底部通入,分散成气泡沿着液体上升, 既与液相接触进行反应同时搅动液体以增加传质速率。 这类反应器适用于液体相也参与反应的中速、慢速反应和放热量大的 反应。 鼓泡塔反应器结构简单、造价低、易控制、易维修、防腐问题易解决, 用于高压时也无困难。 鼓泡塔内液体返混严重,气泡易产生聚并,故效率较低。
塔式反应器
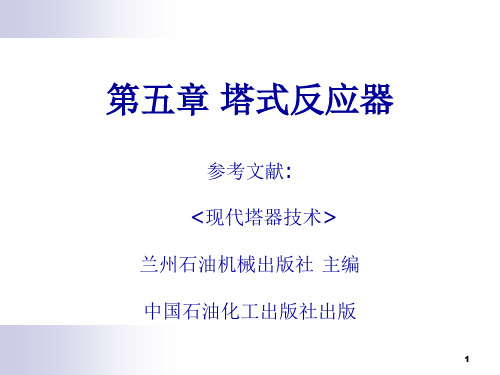
52
流向:液体在重力作用下自上而
下通过各层塔板后由塔底排出;
气体在压差推动下,经均布在塔 板上的开孔由下而上穿过各层塔 板后由塔顶排出;在每块塔板上 皆贮有一定的液体,气体穿过板 上液层时,两相接触进行传质。
板式塔的结构 1.塔壳体 2.塔板 3.溢流堰 4.变液盘 5.降液管
53
板式塔的结构
31
填料塔逆流操作时的持液量
1.动持液量:在填料塔正常操作时突然停止喷淋液体和输 入气体,由填料层流出的液体体积与填料层体积之比。
2.静持液量:当停止喷淋液体和输入气体后经过一段时间
仍然滞留在填料层内的液体体积与填料层体积之比。
Ht H0 H s
静持液量Hs、动持液量Ho 总持液量Ht 适当的持液量对填料塔操作的稳定性和传质是有益。
23
填料塔适用于:
1. 真空操作的精馏,产生泡沫的物料。
填料对泡沫有限制和破碎的作用。
2. 对于超小型的塔填料塔更有优势,塔径在2.5以下。
对于塔径在2.5以上,一般选择板式塔。
3. 对于高腐蚀性的物料精馏。
但冷却移除反应热或溶解热时,结构复杂化。
比较:高效填料材料的使用,使填料塔相对于板式塔的 效率可以以10倍计。
(1) 鲍尔环填料具有低压降、通量大、效率高的特点。
应用: 适用于各种分离、吸收、脱吸装置、常减压装
置、合成胺脱碳、脱硫系统、乙苯分离、异辛烷、甲
苯分离。
(2) 改型鲍尔环:高径比为0.2-0.4,取消了阶梯环的翻
边,采用内弯弧形筋片来提高填料强度,在乱堆时有
序排列,流道结构合理,压降低,在处理能力和传质
4月1日单元3任务2鼓泡塔式反应器仿真操作
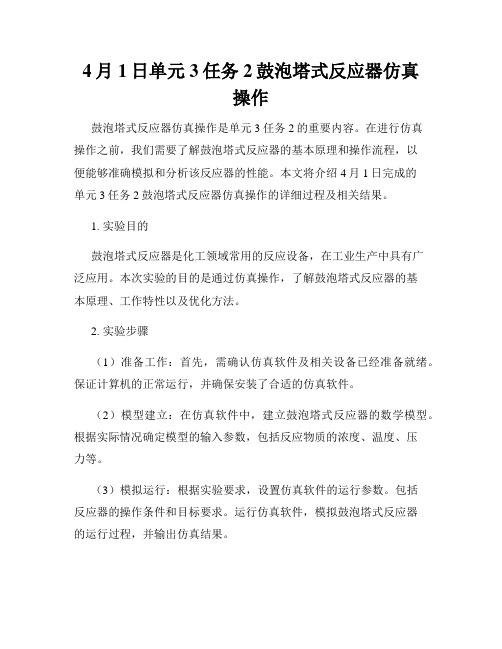
4月1日单元3任务2鼓泡塔式反应器仿真操作鼓泡塔式反应器仿真操作是单元3任务2的重要内容。
在进行仿真操作之前,我们需要了解鼓泡塔式反应器的基本原理和操作流程,以便能够准确模拟和分析该反应器的性能。
本文将介绍4月1日完成的单元3任务2鼓泡塔式反应器仿真操作的详细过程及相关结果。
1. 实验目的鼓泡塔式反应器是化工领域常用的反应设备,在工业生产中具有广泛应用。
本次实验的目的是通过仿真操作,了解鼓泡塔式反应器的基本原理、工作特性以及优化方法。
2. 实验步骤(1)准备工作:首先,需确认仿真软件及相关设备已经准备就绪。
保证计算机的正常运行,并确保安装了合适的仿真软件。
(2)模型建立:在仿真软件中,建立鼓泡塔式反应器的数学模型。
根据实际情况确定模型的输入参数,包括反应物质的浓度、温度、压力等。
(3)模拟运行:根据实验要求,设置仿真软件的运行参数。
包括反应器的操作条件和目标要求。
运行仿真软件,模拟鼓泡塔式反应器的运行过程,并输出仿真结果。
(4)结果分析:对仿真结果进行分析和评估。
包括反应物质的转化率、反应速率等指标的计算和比较。
观察反应器的温度、压力和流体分布等变化情况。
(5)参数调整:根据分析结果,对反应器的相关参数进行调整。
可以改变反应物质的初始浓度、温度和流速等参数,以获得更好的反应效果。
(6)结果验证:对调整后的参数进行仿真运行,并观察结果的变化。
通过与实际操作的对比,验证仿真结果的准确性和可靠性。
3. 实验结果根据仿真操作和分析,得到了鼓泡塔式反应器的相关结果:(1)反应物质的转化率随时间的变化曲线;(2)反应物质的浓度随反应器高度的变化曲线;(3)反应器中温度和压力的变化曲线;(4)气液两相混合的程度及流体的流动情况。
4. 结果分析根据仿真结果的分析,可以得到以下结论:(1)反应物质的转化率随时间的增加而逐渐增加,并趋于稳定;(2)反应物质的浓度随着反应器高度的增加而逐渐减小,且呈现非线性变化;(3)反应器中的温度随着反应进行而升高,压力也随之增加;(4)气液两相的混合程度在鼓泡塔内较好,流体的流动呈现较好的均匀性。
臭氧反应装置介绍
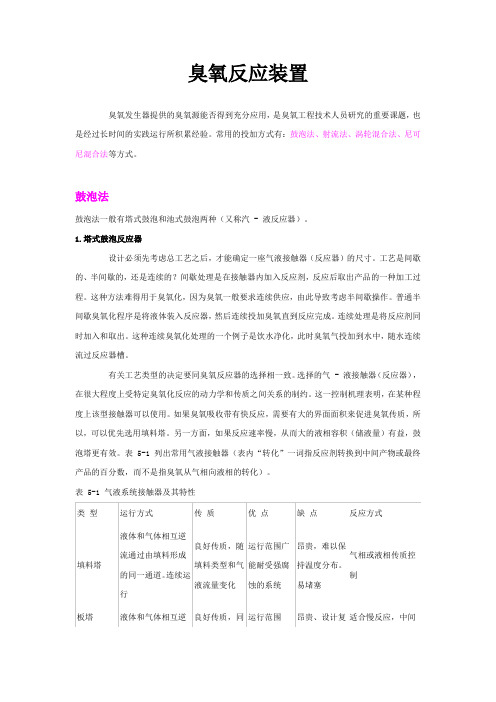
臭氧反应装置臭氧发生器提供的臭氧源能否得到充分应用,是臭氧工程技术人员研究的重要课题,也是经过长时间的实践运行所积累经验。
常用的投加方式有:鼓泡法、射流法、涡轮混合法、尼可尼混合法等方式。
鼓泡法鼓泡法一般有塔式鼓泡和池式鼓泡两种(又称汽 - 液反应器)。
1.塔式鼓泡反应器设计必须先考虑总工艺之后,才能确定一座气液接触器(反应器)的尺寸。
工艺是间歇的、半间歇的,还是连续的?间歇处理是在接触器内加入反应剂,反应后取出产品的一种加工过程。
这种方法难得用于臭氧化,因为臭氧一般要求连续供应,由此导致考虑半间歇操作。
普通半间歇臭氧化程序是将液体装入反应器,然后连续投加臭氧直到反应完成。
连续处理是将反应剂同时加入和取出。
这种连续臭氧化处理的一个例子是饮水净化,此时臭氧气投加到水中,随水连续流过反应器槽。
有关工艺类型的决定要同臭氧反应器的选择相一致。
选择的气 - 液接触器(反应器),在很大程度上受特定臭氧化反应的动力学和传质之间关系的制约。
这一控制机理表明,在某种程度上该型接触器可以使用。
如果臭氧吸收带有快反应,需要有大的界面面积来促进臭氧传质,所以,可以优先选用填料塔。
另一方面,如果反应速率慢,从而大的液相容积(储液量)有益,鼓泡塔更有效。
表 5-1 列出常用气液接触器(表内“转化”一词指反应剂转换到中间产物或最终产品的百分数,而不是指臭氧从气相向液相的转化)。
表 5-1 气液系统接触器及其特性流通过板塔,连续运行依气体质量而定的界面面积成比例广,易清洗杂、易堵塞停留容积和大液体容积鼓泡塔气体扩散成气泡,上升穿过液柱,能连续顺流或逆流,交替逆流,或反复逆流或顺流运行,可以是半批量的低传质,依界面面积而定,后者是气体流量的函数低能耗喷头可能堵塞,引起气泡的不均匀分布,混合差。
接触时间长要求大液体容积受反应速率控制的系统喷淋塔流体扩散到含 O 3的气体内借助大的界面面积有中等传质气相均匀高能耗,固体物能堵塞喷嘴适合小储液量的快反应搅拌塔能连续,半批量或批量运行,使用带机械搅拌的罐由于界面面积和气体储量可有中等到良好传质,前者依气体流量及搅拌而定高度灵活性,能处理固体,传热特性好搅拌需要能量,为获得所需转化,搅拌反应器需要最大理论容积受传质控制的反应喷射器和涡轮气体和液体被加压或抽吸顺流通过小孔隙传质和界面面积大混合好,接触时间短,接触室小耗能适合短暂液体滞留,传质限制的反应管道接触器可顺流(通常可用立管)或逆流运行如水流量高,在高气体流速下可得高传质易控温,低造价,易操作需要能量,为促进气液接触需要用固定混合器适合短暂液体滞留,传质限制反应当设计一座气液系统时,设计者必须做多种考虑。
塔式反应器结构和工作原理
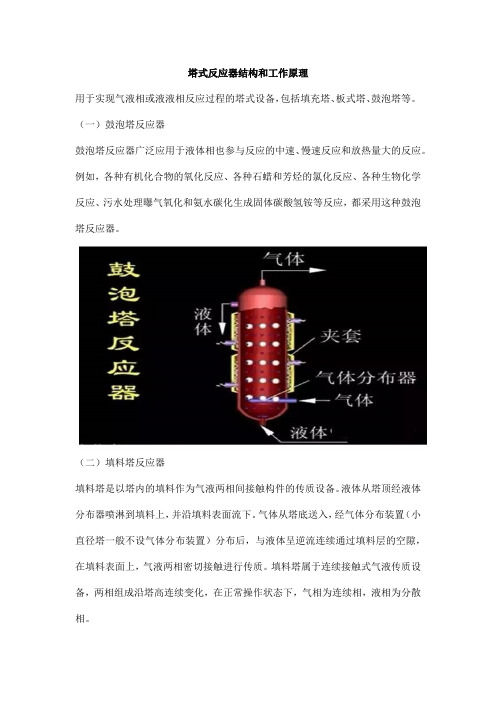
塔式反应器结构和工作原理用于实现气液相或液液相反应过程的塔式设备,包括填充塔、板式塔、鼓泡塔等。
(一)鼓泡塔反应器鼓泡塔反应器广泛应用于液体相也参与反应的中速、慢速反应和放热量大的反应。
例如,各种有机化合物的氧化反应、各种石蜡和芳烃的氯化反应、各种生物化学反应、污水处理曝气氧化和氨水碳化生成固体碳酸氢铵等反应,都采用这种鼓泡塔反应器。
(二)填料塔反应器填料塔是以塔内的填料作为气液两相间接触构件的传质设备。
液体从塔顶经液体分布器喷淋到填料上,并沿填料表面流下。
气体从塔底送入,经气体分布装置(小直径塔一般不设气体分布装置)分布后,与液体呈逆流连续通过填料层的空隙,在填料表面上,气液两相密切接触进行传质。
填料塔属于连续接触式气液传质设备,两相组成沿塔高连续变化,在正常操作状态下,气相为连续相,液相为分散相。
(三)板式塔反应器板式塔反应器的液体是连续相而气体是分散相,借助于气相通过塔板分散成小气泡而与板上液体相接触进行化学反应。
板式塔反应器适用于快速及中速反应。
采用多板可以将轴向返混降低至最小程度,并且它可以在很小的液体流速下进行操作,从而能在单塔中直接获得极高的液相转化率。
同时,板式塔反应器的气液传质系数较大,可以在板上安置冷却或加热元件,以适应维持所需温度的要求。
但是板式塔反应器具有气相流动压降较大和传质表面较小等缺点。
(四)喷淋塔反应器喷淋塔反应器结构较为简单,液体以细小液滴的方式分散于气体中,气体为连续相,液体为分散相,具有相接触面积大和气相压降小等优点。
适用于瞬间、界面和快速反应,也适用于生成固体的反应。
喷淋塔反应器具有持液量小和液侧传质系数过小,气相和液相返混较为严重的缺点。
鼓泡塔反应器设计 ppt课件
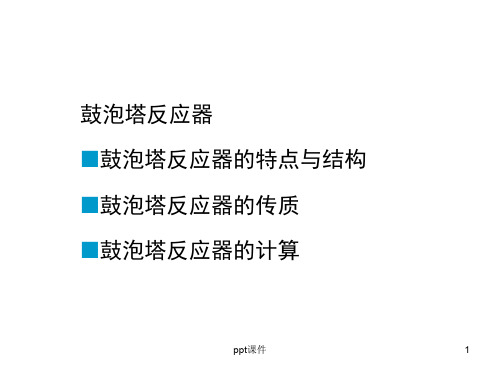
散系数。 扩散系数不仅与液体物理性质有关,而且还与反应温度、气体反
应物的分压或液体浓度有关。当鼓泡塔在安静区操作时,影响液相传质 系数的因素主要是气泡大小、空塔气速、液体性质和扩散系数等;而在 湍动区操作时,液体的扩散系数、液体性质、气泡当量比表面积以及气 体表面张力等,成为影响传质系数的主要因素。
条件:
Re 0
d0u0 G G
<200
ppt课件
6
气泡群的直径的计算
a.当量比表面直径dVS: b.体积平均直径dV: c.几何平均直径dg:
ppt课件
7
含气率: 单位体积充气层内气体所点的体积分率。 ε:动态气含率。液体连续流动时的气含率。
鼓泡塔反应器 鼓泡塔反应器的特点与结构 鼓泡塔反应器的传质 鼓泡塔反应器的计算
ppt课件
1
鼓泡塔反应器鼓泡塔反应器的特点与结构
特点: 塔内充满液体,气体从反应器底部通入,分散成气泡沿着液体上升,
既与液相接触进行反应同时搅动液体以增加传质速率。 这类反应器适用于液体相也参与反应的中速、慢速反应和放热量大的
当D<1.2m HE≥1m D≥1.2m αE=0.75
ppt课件
16
VC:
VC
D 3 12
式中 :形状系数,球盖: =1
标准椭圆形封头: =2
ppt课件
17
反应器直径和高度的计算
D
D
4VG
3600uOG
m
H H=HR+HE+HC
3 H 12 D
ppt课件
18
反应。 鼓泡塔反应器结构简单、造价低、易控制、易维修、防腐问题易解决,
鼓泡塔反应器设计[荟萃知识]
![鼓泡塔反应器设计[荟萃知识]](https://img.taocdn.com/s3/m/573b0a3eb0717fd5370cdc61.png)
行业知识
1
鼓泡塔反应器鼓泡塔反应器的特点与结构
特点: ➢ 塔内充满液体,气体从反应器底部通入,分散成气泡沿着液体上升,
既与液相接触进行反应同时搅动液体以增加传质速率。 ➢ 这类反应器适用于液体相也参与反应的中速、慢速反应和放热量大的
行业知识
12
鼓泡塔反应器的计算 反应器体积 充气层的体积:VR=VG+VL 分离空间体积:VE 顶盖死区体积:VC
行业知识
13
➢ VL: 半连续操作时:VL=VOL(τ+τ')
连续操作时:VL=VOL
VOL
C AO xA
rA
其中:(-rA)':实测的宏观速度。
行业知识
14
➢ VG:
VG
行业知识
5
➢ 气泡尺寸
a. 气泡的形成:
uOG较低时:气体分布器 uOG中等时:气体分布器加液体湍动 uOG较高时:液体湍动使气流破碎成气泡。
b.单个气泡的形状和直径 形状:db<0.2cm 垂直上升的坚实圆球. 0.2≤db≤1.0cm 螺旋式摆动上升的椭圆球 db>1.0cm 垂直上升的菌帽状
传质速率的快慢。 欲提高单位相界面的传质速率,即提高传质系数,则必须提高扩
散系数。 扩散系数不仅与液体物理性质有关,而且还与反应温度、气体反
应物的分压或液体浓度有关。当鼓泡塔在安静区操作时,影响液相传质 系数的因素主要是气泡大小、空塔气速、液体性质和扩散系数等;而在 湍动区操作时,液体的扩散系数、液体性质、气泡当量比表面积以及气 体表面张力等,成为影响传质系数的主要因素。
条件:
- 1、下载文档前请自行甄别文档内容的完整性,平台不提供额外的编辑、内容补充、找答案等附加服务。
- 2、"仅部分预览"的文档,不可在线预览部分如存在完整性等问题,可反馈申请退款(可完整预览的文档不适用该条件!)。
- 3、如文档侵犯您的权益,请联系客服反馈,我们会尽快为您处理(人工客服工作时间:9:00-18:30)。
臭氧发生器提供的臭氧源能否得到充分应用,是臭氧工程技术人员研究的重要课题,也是经过长时间的实践运行所积累经验。
常用的投加方式有:鼓泡法、射流法、涡轮混合法、尼可尼混合法等方式。
鼓泡法鼓泡法一般有塔式鼓泡和池式鼓泡两种(又称汽- 液反应器)。
1.塔式鼓泡反应器设计必须先考虑总工艺之后,才能确定一座气液接触器(反应器)的尺寸。
工艺是间歇的、半间歇的,还是连续的?间歇处理是在接触器内加入反应剂,反应后取出产品的一种加工过程。
这种方法难得用于臭氧化,因为臭氧一般要求连续供应,由此导致考虑半间歇操作。
普通半间歇臭氧化程序是将液体装入反应器,然后连续投加臭氧直到反应完成。
连续处理是将反应剂同时加入和取出。
这种连续臭氧化处理的一个例子是饮水净化,此时臭氧气投加到水中,随水连续流过反应器槽。
有关工艺类型的决定要同臭氧反应器的选择相一致。
选择的气- 液接触器(反应器),在很大程度上受特定臭氧化反应的动力学和传质之间关系的制约。
这一控制机理表明,在某种程度上该型接触器可以使用。
如果臭氧吸收带有快反应,需要有大的界面面积来促进臭氧传质,所以,可以优先选用填料塔。
另一方面,如果反应速率慢,从而大的液相容积(储液量)有益,鼓泡塔更有效。
表5-1 列出常用气液接触器(表内“转化”一词指反应剂转换到中间产物或最终产品的百分数,而不是指臭氧从气相向液相的转化)。
表5-1 气液系统接触器及其特性类型运行方式传质优点缺点反应方式填料塔液体和气体相互逆流通过由填料形成的同一通道。
连续运行良好传质,随填料类型和气液流量变化运行范围广能耐受强腐蚀的系统昂贵,难以保持温度分布。
易堵塞气相或液相传质控制板塔液体和气体相互逆流通过板塔,连续运行良好传质,同依气体质量而定的界面面积成比例运行范围广,易清洗昂贵、设计复杂、易堵塞适合慢反应,中间停留容积和大液体容积鼓泡塔气体扩散成气泡,上升穿过液柱,能连续顺流或逆流,交替逆流,或反复逆流或顺流运行,可以是半批量的低传质,依界面面积而定,后者是气体流量的函数低能耗喷头可能堵塞,引起气泡的不均匀分布,混合差。
接触时间长要求大液体容积受反应速率控制的系统喷淋塔流体扩散到含 O 3 的气体内借助大的界面面积有中等传质气相均匀高能耗,固体物能堵塞喷嘴适合小储液量的快反应搅拌塔能连续,半批量或批量运行,使用带机械搅拌的罐由于界面面积和气体储量可有中等到良好传质,前者依气体流量及搅拌而定高度灵活性,能处理固体,传热特性好搅拌需要能量,为获得所需转化,搅拌反应器需要最大理论容积受传质控制的反应喷射器和涡轮气体和液体被加压或抽吸顺流通过小孔隙传质和界面面积大混合好,接触时间短,接触室小耗能适合短暂液体滞留,传质限制的反应管道接触器可顺流(通常可用立管)或逆流运行如水流量高,在高气体流速下可得高传质易控温,低造价,易操作需要能量,为促进气液接触需要用固定混合器适合短暂液体滞留,传质限制反应当设计一座气液系统时,设计者必须做多种考虑。
这些要考虑的问题包括:气体和液体流量要满足生产规程、传质和化学反应关系;最后,选定一种将以最经济方式进行的气液接触器和操作方法。
在选择气液接触器过程中,需要考察以下一些参数对传质的影响:比界面面积a ,传质系数k L ,分散相的溶解度,溶质的扩散系数和分散相储存量。
其他间接影响传质的因素有:分散相表面速度,气泡直径和速度。
一些研究者还逐一评述了为臭氧使用的各种接触器。
这些参考文献可用来查阅设计公式。
下面将对表5-1 所列的接触器给以讨论,并将提出一般设计构想。
填料塔填料塔是立罐内装以填料,来分散气流和水流,并促进混合。
用于气体净化的填料塔,通常称作吸收塔,一般以气液逆流方式运行。
从乙醇胺液中吸收二氧化碳和硫化氢便是一例。
某些填料也可以起催化剂作用来促进反应。
当三氧化二铁催化剂用于填料塔内,同惰性填料相比,提高了臭氧氧化酚水溶液的臭氧利用率。
填料塔采用逆流运行,但是带催化的填料塔逆流顺流操作都可以。
在后一种情况下同向升流和同向降流操作都能遇到。
升流可提供较好的气液混合,但会碰到压降较高和流量限制问题。
同向降流以连续气相和分散液相方式通过催化填料,通常称作“滴滤床反应器”。
填料塔可提供大的界面面积,因此,它们适用于受传质控制的反应。
它们不需要大的压降,但在运行范围方面多少有些受限制。
因为液体和气体基本上在同一通道内通过塔填料,对于有效运行来说,液体和气体负荷的范围较窄。
塔内可能发生孤立温度偏离。
新型塑料填料可降低填料塔的费用,并可暴露于腐蚀性气体之中。
现有多种填料型号可从中选择,填料公司在提供K a G 及其他设计数据方面是有帮助的。
不过,应该认识到臭氧同多种增塑剂反应,推荐的塑料材料在它们确定使用之前,应在有臭氧存在情况下加以试验。
板式塔板式塔比填料塔更贵,但可提供较宽广的运行范围。
气液逆流,同时液体在每层塔板是重新分配的,由于水流在整个塔高度方向均匀地分布,因此,高通水量时可使用大直径塔。
塔板可设计为保证慢反应所需要的储液量,同时可为传质提供大界面面积。
当寻求一座有广泛运行灵活性的板式塔时,阀板——可变孔径的穿孔塔板,是供吸收塔使用的理想塔板型式。
鼓泡塔鼓泡塔向装满液体的塔内鼓气泡,是饮水消毒最常用的臭氧反应器,混合的程度依气泡大小和表面气体流速而定。
鼓泡塔运行简单经济,极适用于高压臭氧化。
为了控制温度,塔内可安装热交换器。
鼓泡塔也适用于化学反应速率控制的臭氧化反应,气体接触时间主要通过气泡上升速度和液柱高度予以控制。
在气- 液接触系统中,鼓泡塔传质效率所受压力的影响,不像它在气- 气接触系统中那么大。
在某些化学反应情况下,能投加催化剂颗粒构成一种絮体反应器。
催化剂颗粒因气泡运动被保持在悬浮状态,但是,催化剂颗粒也能引起喷头堵塞问题,特别是如果气流变成间歇的,或者如果气泡上升速度太慢不足以保持催化剂颗粒的悬浮。
喷淋塔在喷淋塔内液体被喷洒到大量含臭氧的气体中。
这种方法抽水费用很高,可产生很大的界面面积。
喷淋塔,由于短接触时间和高界面面积对瞬时或快速反应适用。
它们为一些欧洲的处理厂大批使用,而且在试验室试验中还发现它们有破坏氰化物的能力。
搅拌槽搅拌槽(搅拌反应槽)可用于其间传质速率和化学反应速率为同一数量级的中速反应方式。
搅拌槽为高气液储量提供一种经济的方法,所以,三种运行方式(间歇、半间歇和连续)都可使用搅拌槽。
连续向固定容积废水供臭氧气的半间歇运行,已成功地用于处理某些难降解工业废水。
以连续方式运行的搅拌槽,一般又称作返混反应器。
假设是完全混合,它将使整个反应器内成分均匀,从而,出流成分与反应器内相同。
对化学反应速率限制的反应方式来说,其内的传质效果不明显,返混反应器设计用公式表明,它们需要最大的理论容积,以获得所需的化学转化程度。
搅拌速度对气液平衡的主要作用是改变界面面积。
通过使用强力搅拌,搅拌槽能接近填料塔的界面面积,并能近似无搅拌鼓泡塔的界面面积。
改变搅拌速度的方法,常用于验证反应方式。
当反应机理随增加搅拌作用(界面面积)从一种受传质限制的,转变到另一种受反应速率限制的时候,将可得到一条类似图 1 的中速反应曲线。
因搅拌器消耗电能明显增加其运行费用是一缺点。
不过,当气体被扩散到液体内以后,降低了混合体的密度,所需搅拌电能也降低。
混合用功率需要值最好使用未加气的液体来测定。
搅拌槽的优点是混合及传热效果好。
机械搅拌作用能使投加的催化剂保持悬浮状态,从而改善絮体反应器的运行。
由于搅拌作用极好的传热速率是可能的,无论夹套式或是嵌管式热交换器均可使用,用后者可提供更好的传热效果。
韦斯特普(Weserterp )等以及普林格尔和巴罗那(Frengle 和Barona ),根据传质研究为搅拌反应槽设计了标准构造形式。
标准图型中常用反应槽尺寸与直径的不同比例关系。
这些比例可很容易地将反应槽的规模从半生产性放大到生产性装置。
图2 给出标准搅拌反应槽构造图。
当需要高度混合时可用喷射器和涡轮,可获得中到高度界面面积,而且在短接触时间内就能完成快速反应。
水泵可提供1~10s 的停留时间。
为了更高程度的混合或充分剪切以产生界面面积,可以使用轴向混合器(管道混合器)。
为将臭氧化气吸入到流体内,也常用文丘里反应器。
它的主要优点是易安装,但会产生堵塞问题。
管道反应管道反应器可以用单根连续管道制成,也可用几根并联运行的管道制成,大多数采用同向流通过管道以获得活塞流。
活塞流反应器的特征假定在直径方向完全混合,而在流动方向无扩散可利用。
这就使得在垂直于流线的任一断面面积上的流速、温度和浓度分布都是相等的,惟独组成成分沿流程变化。
对于受化学反应速率控制的反应方式来说,其内传质效果是不重要的,活塞流反应器设计公式表明,为获得所希望的化学转换程度,它们需要的理论值最小。
由于要确定气- 液流线图型是很复杂的,管道反应器很难设计用于气液反应。
西奇(Cichy )等及雷斯(Rase )给出管道反应器25 种可能流动方式的讨论,利用巴克尔(Baker )和戈维尔(Gorier )图来预计流线图型已取得某些成功。
气液管道反应器主要由于它们的费用低、易扩建和优良的传热特性而被采用。
在卧式管道反应器中常用紊流促进混合并给出活塞流状态。
在这种环境下,为重新往液体内分配气体,轴向固定混合器正在变得流行起来。
这种装置是将一些固定构造装在管道内,它们迫使同向流的气体和液体通过迂回通道,从而不断增加两流体间的表面相互作用。
既然这些嵌装的元件在管内是固定不动的,它们保证混合程度并传质增强到这种地步,都是由于受通过管道两种流体流速的影响。
如果液体流速很慢,达到的传质量接近用两相同向流运行的管道接触器内可能得到的传质量。
理查兹(Richards )等用固定混合器研究了臭氧向水中的传质,并报道改善后的传质超过一般的管道反应器。
化学工业中最常用的立式管道反应器是湿壁塔,在塔内,液相沿塔内壁向下流动,在塔中心,气体可以同向或逆向流动。
这些反应器用于特殊发热化学反应极好,但由于有限的界面面积而仅限于瞬时反应使用。
湿壁塔极少用于臭氧反应,因为仅仅少数臭氧反应是高发热的。
这是由于臭氧反应往往是处在低浓度下并且是被稀释到某种溶剂内的缘故。
在这些初步试验中含臭氧空气是循环通过试验装置的,而且一部分未经通过多孔扩散元件即被分解。
这是由于几种因素包括光的影响的气流的搅动造成的。
所以,考虑到为浓度比较用,在通过扩散器或未通过扩散器的出口处所量测到的那些浓度必须是精确的。