分度盘零件加工工艺及夹具设计
机械毕业设计-法兰盘加工工艺及夹具设计-钻四孔分度夹具

Title The flange plate processing technology and fixture designAbstractThe design is based on the body parts of the processing order of the processes and some special fixture design. Body parts of the main plane of the surface and pore system. In general, the plane guarantee processing precision than that of holes machining precision easy. Therefore, this design follows the surface after the first hole principle. Plane with holes and the processing clearly divided into roughing and finishing stages of holes to ensure machining accuracy. Datum selection box input shaft and the output shaft of the supporting hole as a rough benchmark, with top with two holes as a precision technology reference. Main processes arrangements to support holes for positioning and processing the top plane, and then the top plane and the supporting hole location hole processing technology. In addition to the follow-up processes individual processes are made of the top plane and technological hole location hole and plane processing. Supported hole processing using the method of coordinate boring. The whole process of processing machine combinations were selected. Selection of special fixture fixture, clamping means more choice of pneumatic clamping, clamping reliable, institutions can not be locked, so the production efficiency is high, suitable for large batch, line processing, can meet the design requirements.Keywords Frange plate; fixture;, design1 (1)1.1 (2)1.1.1 (2)1.1.2 (2)1.2 (3)1.3 (3)1.3.1 (3)1.3.2 (3)1.4 (3)1.5 (5)1.6 (6)1.7 (6)2 4- 10 (16)2.1 (16)2.2 (17)2.2.1 (17)2.2.2 (17)2.3 (18)2.4 (19)2.5 (19) (21) (22) (24)11.11.1.111.1.21 42 mRa2.32 10 4- 10 mRa2.31.21.31.3.1121.3.21.4c 9080 0.4%—1.1% 0.25%—0.5% mg 20010203040 87506070 82804- 10 90 100102030 4- 10 4050 87607080 829010010203040 87506070 8280 4- 10901001.5(1)HT200(2)2.2-5 HT200 HB 170—24121 3.2.23mm 4.3~7.1 mm 0.2 3.2.27 mm 28.02.3.59 mm 1 CT7 2.3.9 mm 6.11.6mm 1000mm [2] 6—7 CA6140 [2] 4—3 [2]1.71020.HT200 CA6140YG61.1 CA6140 200mm 1.30 H B =mm mm 2516 mm 5.4 0V =012 0 =06 v K =090 'v K =010 s =00 s r =mm 8.0pa mm 2f1.4mm 16mm 25 p a mm 4 100 400 f =0.5 1.0r mmCA6140 4.2—9f =0.7rmm 1—30 CA6140 max F =3530N1.21 174 207HBS p a mm 4 f 75.0 r mm r K =045 R F =950Nf F roFf K =1.0 sFf K =1.0 krFf K =1.17 1.29—2f F =95017.1 =1111.5N1-2f =r mm 7.01.9mm 5.1 T =min 60V1.11 6YG 200 219HBS p a mm 4 f r mm 75.0 V =min 63mtv K =1.0 mv K =0.92 sv K 0.8 Tv K =1.0 Kv K =1.0 1.28'0V =t V v K =63 0.10.184.092.00.10.1 1-3min48m n =D V c '1000=127481000 =120min r 1-4 CA61400n =125minr c VcV =1000c Dn =1000125127 min50m 1-51.25 HBS =160 245 p a mm 3 f r mm 75.0 min 50m VC P =KW7.1 krPc k =0.73 Pc r K 0=0.9CP =1.773.0 =1.2KW 1-61.30 n =min 125r E P =KW 9.5 C P E P C620—1p a =3.75mm f =r mm 7.0 n =min 125r =s r 08.2 V =min 50m 30 87YG61.1 C6140 200mm 1.30 H B =mm mm 2516 mm 5.4 0V =012 0 =06 v K =090 'v K =010 s =00 s r =mm 8.0pa mm 5.2p a =25.2=mm 25.1 f1.4mm 16mm 25 p a mm 4 100 400 f =0.5 1.0rmm CA6140 4.2—9f =0.7rmm1—30 CA6140 max F =3530N1.21 174 207HBS p a mm 4 f 75.0 r mm r K =045 R F =950Nf F roFf K =1.0 sFf K =1.0 krFf K =1.17 1.29—2f F =95017.1 =1111.5Nf =r mm 7.01.9mm 5.1 T =min 60V1.11 15YT 200 219HBS p a mm 4 f r mm 75.0 V =min 63mtv K =1.0 mv K =0.92 sv K 0.8 Tv K =1.0 Kv K =1.0 1.28'0V =t V v K =63 0.10.184.092.00.10.1 3-12min 48m n =D V c '1000=127100048 =120minr 3-13 CA61400n =125minr c VcV =1000c Dn =1000125127 min50m 3-141.25 HBS =160 245 p a mm 3 f r mm 75.0 min 50m VC P =kw7.1 krPc k =0.73 Pc r K 0=0.9C P =1.773.0 =1.2kw1.30 n =min 125r E P =kw 9.5 C P E P CA6140p a =1.25mm f =r mm 7.0 n =min 125r =s r 08.2 V =min 50m .nfl t3-15 L =l +y + l =mm127 1.26 y + =mm 1 L =126+1=mm128m t =7.0125127 =min 4.1 40YG61.1 C6140 200mm 1.30 H B =mm mm 2516 mm 5.4 0V =012 0 =06 v K =090 'v K =010 s =00 s r =mm 8.0pa mm 5.2p a =25.2=mm 25.1 f1.4mm 16mm 25 p a mm 4 100 400 f =0.5 1.0rmm CA6140 4.2—9f =0.7rmm 1—30 CA6140 max F =3530N1.21 174 207HBS p a mm 4 f 75.0 r mm r K =045 R F =950Nf F roFf K =1.0 sFf K =1.0 krFf K =1.17 1.29—2f F =95017.1 =1111.5Nf =r mm 7.01.9mm 5.1 T =min 60V1.11 15YT 200 219HBS p a mm 4 f r mm 75.0 V =min 63mtv K =1.0 mv K =0.92 sv K 0.8 Tv K =1.0 Kv K =1.0 1.28'0V =t V v K =63 0.10.184.092.00.10.1 3-12min 48m n =D V c '1000=127100048 =120minr 3-13 CA61400n =125minr c VcV =1000c Dn =1000125127 min50m 3-141.25 HBS =160 245 p a mm 3 f r mm 75.0 min 50m VC P =kw7.1 krPc k =0.73 Pc r K 0=0.9C P =1.773.0 =1.2kw1.30 n =min 125r E P =kw 9.5 C P E P CA6140p a =1.25mm f =r mm 7.0 n =min 125r =s r 08.2 V =min 50m .nfl t3-15 L =l +y + l =mm127 1.26 y + =mm 1 L =126+1=mm128m t =7.0125127 =min 4.1 502040 82YG61.1 C6140 200mm 1.30 H B =mm mm 2516 mm 5.40V =012 0 =06 v K =090 'v K =010 s =00 s r =mm 8.0pa mm 5.2p a =25.2=mm 25.1 f1.4mm 16mm 25 p a mm 4 100 400 f =0.5 1.0rmm CA6140 4.2—9f =0.7rmm 1—30 CA6140 max F =3530N1.21 174 207HBS p a mm 4 f 75.0 r mm r K =045 R F =950Nf F roFf K =1.0 sFf K =1.0 krFf K =1.17 1.29—2f F =95017.1 =1111.5Nf =r mm 7.01.9mm 5.1 T =min 60V1.11 15YT 200 219HBS p a mm 4 f r mm 75.0 V =min 63mtv K =1.0 mv K =0.92 sv K 0.8 Tv K =1.0 Kv K =1.0 1.28'0V =t V v K =63 0.10.184.092.00.10.13-12min 48m n =D V c '1000=127100048 =120minr 3-13 CA61400n =125minr c VcV =1000c Dn =1000125127 min 50m 3-141.25 HBS =160 245 p a mm 3 f r mm 75.0 min 50m VC P =kw7.1 krPc k =0.73 Pc r K 0=0.9C P =1.773.0 =1.2kw1.30 n =min 125r E P =kw 9.5 C P E P CA6140p a =1.25mm f =r mm 7.0 n =min 125r =s r 08.2 V =min 50m .nfl t3-15 L =l +y + l =mm127 1.26 y + =mm 1 L =126+1=mm128m t =7.0125127 =min 4.180 4- 10Z525 GB1436-85 22 10.4-2 10mm 0.20 0.35r mm rmm f 30.0 2 10.4-9min0m k f a T d c v v y x p m z v v v v3-20 125.0,55.0,0,25.0,1.8 m y x z c v v v v T=35minv =55.00125.025.03.053571.8 =1.6minmn =714.36.11000 =72min r min120r n 1000714.3120 v =2.64minmt =s 203.022282 4- 102.14- 10 Z525”2.22.2.182 822.2.210 D=1028.4F=C F d 0F z f F y k F ……………………………………3.1C F =420 Z F =1.0, y F =0.8, f=0.35k F =(07.1)190200()1903.1 F n HB F=420 1.00.8300.35 1.072123()NT=C T d 0T Z f T y k T: C T =0.206, Z T =2.0, y T =0.8T=0.206 2.00.8300.35 1.0717.34()N M P m =KW d T V 726.083095.1634.17300K=K 1K 2K 3K 4K 1 1.5;K 2 1.1;K 3 , 1.1;K 4 , 1.1F /=KF=1.5)(423921231.11.11.1N T=17.34 N M:F 1=N L T 267106534.173 1.0 f F f =4416)(6.4411.0N F f > F 12.3ZZmm 05.0~03.02 . mm 04.02 .P297mm008.03 mmDW 142.016.005.008.004.0125.022222252423222 .533.032142.0.2.43.13.22.51234[1] 1982. (1)[2] [M] 1984 20-23[3] [M] 1983 42-50[4] [ ] 1992[5] 1 [M] 1991[6] [M] 1979[7] [M] 1990[8] [M] 1994[9] [M] 1984[10] [M] 2002[11] , ( ) [M], ,2003.1[12] [M] 1995[13] [M] 1980[14] [M] 1991[15] [M] 2000 9-19[16] , , , ,1979.12[17] 2005 4-17[18] Machine Tools N.chernor 1984.[19] Machine Tool Metalworking John L.Feirer 1973.[20] Handbook of Machine Tools Manfred weck 1984 .[21] Sors l.fatigue design of machine components.oxford:pergramon press.1971!。
分度盘钻孔夹具课程设计说明书
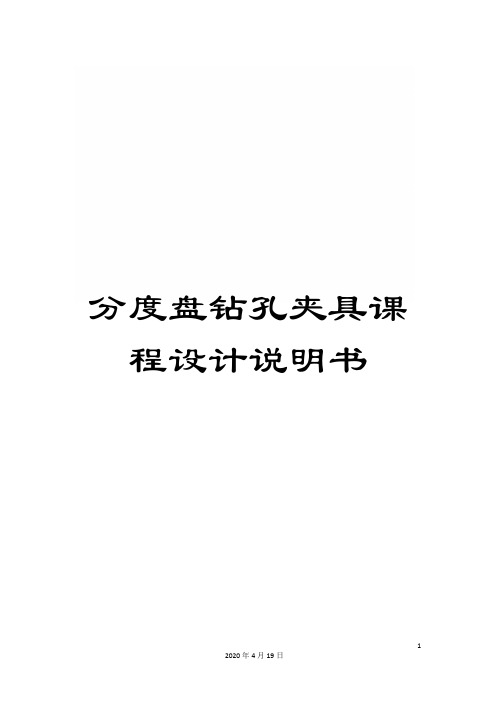
分度盘钻孔夹具课程设计说明书有全套1零件的工艺性分析1)该工件锻造比比较大,很容易造成应力的分布不均。
因此,锻造后进行正火处理,粗加工后进行调质处理,以改进材料的切削性能。
2)工序安排以台阶面和Φ100g6的外圆表面定位,装夹工件,达到了设计基准,工艺基准的统一。
3)分度盘大端面对Φ35H7mm孔中心线有垂直度要求;外圆台阶面对Φ100g6mm外圆轴心线有垂直度要求;Φ100g6mm外圆与Φ35H7mm孔有同轴度要求;6×M12螺纹与和6×Φ32mm孔对100g6mm外圆轴心线有位置度要求,可在偏摆仪上用百分表检查同轴度及垂直度。
12机械加工工艺规程设计2.1分度盘的工艺分析及生产类型的确定2.1.1分度盘的用途分度盘是一种高精度的分度定位元件。
主要用于需要高精度分度定位的金属切削机床和专用夹具上。
2.1.2分度盘的主要技术要求按表1-1形式将该分度盘的主要技术要求列于表6-1中。
表2-1 分度盘零件的主要技术要求26×Φ32孔6×Φ32H7 IT7 12.5Φ0.25 D○M Φ35孔Φ35H7 IT7 3.2Φ36孔Φ36 IT13 12.5Φ21孔Φ21 IT13 12.5螺纹孔6×M12-6H IT6 3.2Φ0.25 D○M6×Φ12孔6×Φ12±0.05IT10 3.2Φ0.1 DΦ10销孔Φ10H7 IT7 3.2Φ12孔底面10 IT13 3.2Φ32孔底面20 IT13 12.5弧形槽底面10 IT13 3.232.1.3审查分度盘的工艺性1)零件材料45钢,切削加工性良好。
2)分度盘Φ100g6mm外圆与Φ35H7mm孔有同轴度要求,为保证加工精度,工艺安排应粗、精加工分开。
3)主要表面虽然加工精度较高,但能够在正常的生产条件下,采用较经济的方法保证质量地加工出来。
2.1.4确定分度盘的生产类型依设计题目可知生产类型为:大批大量生产2.2确定毛坯绘制毛胚图2.2.1毛坯选择根据材料45钢,生产类型为大批大量生产及零件形状要求,可选择模锻件。
机床夹具设计与实践- 分度装置及夹具体设计

• 分度盘本身的误差 • 分度盘相对于回转轴线的径向圆跳动所造成的附加误差
• 对定误差和有关元件的误差等。
机床夹具设计与实践
分度精度的等级 (1)超精密级 分度误差≦0.1″~0.5″ (2)精密级 分度误差≦1″~10″ (3)普通级 分度误差≦1′~10′
分度误差: (1)单个分度误差:
再把捏手反转90°,在弹簧作用下,使分度定位器插入下一个分度孔,完成分度。
分度对定的操纵机构 1—对定销;2—衬套;3—导套;4—横销;5—捏手;
机床夹具设计与实践
(2)枪柱式控制机构 :逆转动手柄7,在螺钉与螺旋槽作用下拔出定位销,转动分度盘分
度,遇到下一分度孔在弹簧作用下,分度削插入分度孔,完成分度。
加工过程中,夹具体要承受较大的切削力和夹紧力。为保证夹具体不产 生不允许的变形和振动,夹具体应有足够的强度和刚度,因此夹具体需有一 定的壁厚。铸造和焊接夹具体常设置加强肋,或在不影响工件装卸的情况下 采用框架式夹具体。
(3) 结构工艺性好。 夹具体应便于制造、装配和检验。铸造夹具体上安装各种元件的表面应铸 出3~5mm高的凸面,以减少加工面积。铸造夹具体壁厚要均匀,转角外应有 R3~R5mm的圆角。
机床夹具设计与实践
5.1.2 任务分析
1. 生产纲领:年产量2000件。 2. 毛坯:毛坯为锻件,材料为45钢。外 圆和端面等其他表面在前面工序中已加工 完成。 3. 加工要求: (1) 保证一次装夹工件车削加工7φ24mm±0.1 mm孔。 (2) 保证7-φ24mm±0.1 mm孔轴线在直 径为φ75mm±0.1 mm的圆周上均匀分布。 (3) 保证7-φ24mm±0.1 mm各相邻两孔 轴线的夹角为51°25′±10′。
分度盘数控加工工艺及编程设计说明书

毕业设计(论文)设计题目:分度盘数控加工工艺及编程专业:数控技术班级:学号:姓名:指导老师:起讫日期年月日~年月日摘要本篇毕业设计主要有数控机床和编程的介绍,对分度盘零件的工艺性分析工艺参数的选择刀具的选择,零件的程序的手工编制,程序的仿真。
文章的主要内容为零件的工艺分析,工艺路线的制定,各工序的切削力及切削工时的计算以及零件的手工程序的编制和各主要工序的程序清单。
在零件的手工编程中用到了G02/G03圆弧插补指令;G81钻孔;M98调用子程序指令。
关键词:分度盘,手工编程,圆弧插补指令,钻孔,子程序目录1绪论 (5)1.1 数控机床的组成 (6)2数控加工工艺设计 (7)2.1 分度盘零件的工艺分析 (8)2.2 刀具、量具的选择 (9)2.3确定毛坯的制作形式 (10)2.4 编制加工工艺 (10)2.5工艺规程的设计 (11)2.6确定切削用量及基本工时 (11)2.6.1夹左端,粗车外圆φ80、φ77.4及端面 (11)2.6.2调头装夹,粗车外圆φ35.5,φ85,30度倒角端面 (12)2.6.3精车外圆φ35.5,φ85 (12)2.6.4调头装夹,精车外圆φ80、φ77.4及端面 (12)2.6.5钻内孔φ16 (12)2.6.6粗镗、精镗内孔φ20 (12)2.6.7粗镗、精镗内孔φ75 (12)2.6.8粗铣、精铣分度盘上12等分槽 (12)2.6.9钻φ6.8底孔,攻M8螺纹孔 (12)2.6.10钻φ6.5孔 (12)3工件的手动编程 (12)3.1 数控编程的定义及分类 (14)3.1.1数控编程的定义................................... 错误!未定义书签。
3.1.2数控编程的分类................................... 错误!未定义书签。
3.1.3编程方法的选择................................... 错误!未定义书签。
分度头锥套夹具及工艺设计

分度头锥套夹具及工艺设计分度头锥套夹具是一种常用于加工旋转对称零件的夹具,它具有结构简单、操作方便、稳定性好等特点,广泛应用于机械加工领域。
下面将介绍分度头锥套夹具的设计工艺以及相关注意事项。
首先,分度头锥套夹具的设计工艺包括以下几个方面:1. 选择合适的夹具材料:分度头锥套夹具通常由高强度合金钢或不锈钢制成,以确保夹具具有足够的强度和刚度。
2. 设计夹具结构:夹具的结构设计要根据加工零件的形状和尺寸,采用合理的夹持方式和夹具形式。
一般情况下,分度头锥套夹具采用中心夹持的形式,即将零件的中心固定在夹具的中央,并通过锥套夹具来实现夹持。
3. 确定夹具定位方式:分度头锥套夹具需要具备良好的定位精度,以确保零件在加工过程中的位置准确。
常用的定位方式有基准面定位、内外圆定位等,根据具体情况选择合适的定位方式。
4. 设计夹具压紧机构:夹具的压紧机构是夹紧零件的关键部分,需要保证夹具能够稳定地夹持零件,同时不会对零件造成过大的变形或损伤。
一般来说,分度头锥套夹具采用螺旋压力机构,在夹具中心的锥套处施加适当的压力以夹持零件。
此外,还需注意以下几点:1. 夹具的加工精度要求高,特别是夹具的内表面和锥套的加工精度,以确保夹具的匹配度和夹持稳定性。
2. 夹具的刚性要足够好,以避免夹具变形或发生震动影响加工质量。
3. 在夹具的选择上要根据具体的加工要求来确定夹具的尺寸和型号。
不同规格的分度头锥套夹具适用于不同大小范围的零件加工。
4. 需要注意的是,夹具在使用过程中需要注意保持清洁和定期维护,以保证夹具的性能和使用寿命。
综上所述,分度头锥套夹具的设计工艺包括材料选择、结构设计、定位方式和压紧机构的确定。
在设计和使用过程中需要注意相关的要点和注意事项,以确保夹具的性能和加工质量。
继续写相关内容:5. 夹具的稳定性要得到充分考虑,特别是在高速加工和重切削条件下。
需要设计适当的支撑系统,以确保夹具在加工过程中不产生晃动或位移,保证加工精度和安全性。
分度盘加工工艺范文

分度盘加工工艺范文分度盘加工工艺是一种用于制作分度盘的工艺过程。
分度盘是一种用于测量和刻度旋转角度的工具。
分度盘通常由金属材料制成,具有一系列刻度和指针,可以精确地测量和调整物体的位置。
下面是一个分度盘加工工艺的范文,详细介绍了每个步骤和注意事项。
一、制备原材料分度盘通常使用钢材作为制作材料,可以选择合适的钢材进行制备。
首先需要确定分度盘的尺寸和形状,根据要求选择厚度和直径适宜的钢材。
然后,将原材料锯切成所需的尺寸,确保切口平整,不产生明显的毛刺。
二、磨削平整将切割好的原材料放入磨床中,进行平整磨削。
通过旋转盘磨的方法,使得材料表面达到光滑,去除切割时产生的毛刺,保证材料表面平整度。
三、切割齿形准备好切割刀具,使用车削或铣削的方法将分度盘上的齿形进行切割。
根据设计图纸上的要求,选择合适的切割工艺参数,如切削转速、进给速度等,保证切削质量。
在切割过程中要注意保持切削刀具和工件的刚性,以避免切削过程中的振动和误差。
四、刻划刻度将已经切割好齿形的分度盘固定到机床上,使用刻度刀具进行刻度。
根据设计要求,在分度盘的外圆表面上进行划线,以表示角度的刻度。
刻度刀具应选择合适的形状和尺寸,保证刻度的清晰和准确性。
在刻划过程中,要注意保持刀具的锋利,并进行适当的润滑和冷却。
五、表面处理分度盘的表面可以进行各种处理,如磨光、镀铬等,以增强分度盘的耐腐蚀性和美观度。
根据实际要求选择合适的表面处理方法,并进行相应的操作。
六、质量检验制作完成的分度盘需要经过质量检验,以保证其质量和精度。
对分度盘的尺寸、形状和刻度等进行检查,确保其满足设计要求。
可以使用量具、显微镜等工具进行检测。
检测结果应与设计要求进行比对,并进行相应的记录和处理。
总结:通过以上的加工工艺,可以制作出精确度高、刻度清晰的分度盘。
在加工过程中,需要注意选择合适的材料、切割工艺和表面处理方法,保证分度盘的质量和精度。
此外,加工过程中要严格按照工艺要求进行操作,并进行必要的质量检验,以确保制作出符合设计要求的分度盘。
简析盘类零件分度夹具设计

简析盘类零件分度夹具设计作者:张伟南来源:《新教育时代》2014年第25期摘要:夹具是一种装夹工件的工艺装备。
它的主要功用是实现工件的定位和夹紧,使工件加工时相对于机床、刀具有正确的位置,以保证加工精度。
本文通过对斜盘的结构特点进行加工工艺分析,并对几种加工方法进行比较,提出采用专用夹具加工平面斜交小孔,同时设计出一套适用性较强的三轴立式加工中心分度钻孔夹具,用于批量生产。
该夹具的结构简单,制造容易,经济实用,安装操作方便,极大提高了加工精度和加工效率。
经在生产实践中使用后证明,该夹具除了很好的保证加工精度、提高生产效率,同时也降低劳动强度、改善工作环境上取得了很好的效果。
关键词:三轴立式加工中心斜交小孔分度钻孔夹具引言盘套类零件是很常见的机械零件,但随着科技的进步,在盘类零件上出现了许多各种各样的轮廓形状和加工要求,因而对如何来完成其加工提出了更大挑战。
在实现过程中有时由于受到设备的条件限制,此时就必须结合实际采取有效的方法来解决问题。
本文主要通过对斜盘零件的结构特点进行加工工艺分析,并结合现有条件,决定采用三轴立式加工中心来进行加工,为了保证加工质量,零件装夹采用设计的专用夹具来进行装夹加工。
一、加工分析和加工方法比较本文所要加工的零件由(如图1所示),在A侧的两个φ5mm斜孔对称分布于零件两侧,它们分别以角度为33°20′与φ10mm孔相贯通,孔的深度尺寸为84mm,加工时要求两φ5细孔终端与零件圆弧中心对称的两个孔相交,而位于B处的另一个φ5mm孔需与另一端φ10mm孔相垂直贯通。
如果工艺方法选择不当,会导致两深孔不能与零件圆弧中心对称的两个孔相交及钻头折断等现象。
图1 斜盘零件简图目前对零件常用几种装夹加工方法有如下[2]:1.划线找正加工:该方法运用工具先在零件上划加工位置刻线,加工时对住所划位置进行加工。
但由于划线误差大以及对刀误差大,加工过程有定位偏移现象,比较难保证斜孔加工尺寸和精度要求。
毕业论文(设计)-盘类零件加工工艺及其夹具的设计

毕业论文(设计)-盘类零件加工工艺及其夹具的设计一、研究背景与意义盘类零件广泛应用于制造业,适用于飞机、汽车和机械等领域。
盘类零件具有高精度、高强度、重负荷承载等特点,其的制造工艺和夹具设计对产品质量和成本控制等方面都具有重要影响。
因此,本研究旨在研究盘类零件加工工艺及夹具的设计,探究其中的关键技术和原理,并通过实验验证其可行性,为工业生产提供有价值的参考和借鉴。
二、加工工艺研究1. 盘类零件加工的基本工艺流程盘类零件加工的基本工艺流程包括铣削、车削、钻孔等工序。
铣削工序:选择合适的铣刀和主轴转速,将盘形零件加固在工作台上,并设置削进量和切削参数。
在切削过程中,要注意切削力的控制、冷却液的喷洒和刀具的清洁,以保证加工精度和表面质量。
车削工序:选择合适的车刀和主轴转速,将盘形零件放置在支座上,并设置逐步切削的深度和切削参数。
在切削过程中,要注意切削区域的冷却液喷射、车床速度的控制、车刀的磨损以及工件翘曲、振动等现象的预防和解决。
钻孔工序:选择合适的钻头和主轴转速,将盘形零件固定在工作台上,并设置钻孔深度和切削参数。
在切削过程中,要注意刀具的静止和动态平衡、冷却液的喷洒和去除,以保证加工质量和效率。
2. 加工中的关键技术(1)工件夹紧技术在盘类零件的制造过程中,工件夹紧技术是关键技术之一。
传统的工件夹紧方式包括:机械夹紧、真空吸附、电磁吸盘等。
为了提高加工质量和效率,近年来采用多点分布式夹紧、多面器夹紧等新型夹紧技术,可以有效减小加工误差和提高精度。
(2)切削刃量和切削传动技术盘类零件加工中,选取合适的切削刃量和切削传动技术,能够减小切削面积和降低切削力。
采用高速切削技术,可以提高生产效率和加工质量。
(3)刀具磨损与刀具寿命管理技术刀具磨损是影响盘类零件加工质量和效率的重要因素之一。
采用合适的刀具与切削速度,加强刀具的管理维护,可以延长刀具使用寿命,优化生产成本。
三、夹具设计研究1. 夹具选择与设计盘类零件夹具的选择要考虑到工件的形状、大小、加工要求和制造工艺等多方面因素。
- 1、下载文档前请自行甄别文档内容的完整性,平台不提供额外的编辑、内容补充、找答案等附加服务。
- 2、"仅部分预览"的文档,不可在线预览部分如存在完整性等问题,可反馈申请退款(可完整预览的文档不适用该条件!)。
- 3、如文档侵犯您的权益,请联系客服反馈,我们会尽快为您处理(人工客服工作时间:9:00-18:30)。
1零件的工艺性分析1)该工件锻造比比较大,很容易造成应力的分布不均。
因此,锻造后进行正火处理,粗加工后进行调质处理,以改善材料的切削性能。
2)工序安排以台阶面和Φ100g6的外圆表面定位,装夹工件,达到了设计基准,工艺基准的统一。
3)分度盘大端面对Φ35H7mm孔中心线有垂直度要求;外圆台阶面对Φ100g6mm外圆轴心线有垂直度要求;Φ100g6mm外圆与Φ35H7mm 孔有同轴度要求;6×M12螺纹与和6×Φ32mm孔对100g6mm外圆轴心线有位置度要求,可在偏摆仪上用百分表检查同轴度及垂直度。
2机械加工工艺规程设计2.1分度盘的工艺分析及生产类型的确定2.1.1分度盘的用途分度盘是一种高精度的分度定位元件。
主要用于需要高精度分度定位的金属切削机床和专用夹具上。
2.1.2分度盘的主要技术要求按表1-1形式将该分度盘的主要技术要求列于表6-1中。
表2-1 分度盘零件的主要技术要求加工表面尺寸及偏差/mm公差及精度等级表面粗糙度Ra/μm形位公差/mm大端面Φ180 IT12 12.5⊥0.02 C 外圆台阶面 1.6⊥0.01 D 小端面Φ100g6 IT6 12.5大外圆Φ180 IT12 12.5小外圆Φ100g6 IT6 1.6◎Φ0.01○M C○M 6×Φ32孔6×Φ32H7 IT7 12.5Φ0.25 D○M Φ35孔Φ35H7 IT7 3.2Φ36孔Φ36 IT13 12.5Φ21孔Φ21 IT13 12.5螺纹孔6×M12-6H IT6 3.2Φ0.25 D○M6×Φ12孔6×Φ12±0.05IT10 3.2Φ0.1 DΦ10销孔Φ10H7 IT7 3.2Φ12孔底面10 IT13 3.2Φ32孔底面20 IT13 12.5弧形槽底面10 IT13 3.22.1.3审查分度盘的工艺性1)零件材料45钢,切削加工性良好。
2)分度盘Φ100g6mm外圆与Φ35H7mm孔有同轴度要求,为保证加工精度,工艺安排应粗、精加工分开。
3)主要表面虽然加工精度较高,但可以在正常的生产条件下,采用较经济的方法保证质量地加工出来。
2.1.4确定分度盘的生产类型依设计题目可知生产类型为:大批大量生产2.2确定毛坯绘制毛胚图2.2.1毛坯选择根据材料45钢,生产类型为大批大量生产及零件形状要求,可选择模锻件。
毛坯的拔模斜度5°。
2.2.2确定毛坯的尺寸公差和机械加工余量1)公差等级由分度盘零件的功用和技术要求,确定该零件的公差等级为普通级。
2)锻件重量根据机械加工后零件的形状及零件材料,估算锻件毛坯重量为m=7.50kg。
t3)锻件复杂系数对分度盘零件图进行分析计算,可大致确定锻件外廓包容体的直径d=Φ180mm,高H=60mm。
由公式S=N mm t/=7.50kg/12.0kg≈0.63。
由此可确定该分度盘零件的复杂系数为2S级。
4)锻件材质系数由于该分度盘零件材料为45钢,是碳的质量分数小于0.65%的碳素钢,故该锻件的材质系数为1M级。
5)锻件分模线形状与零件表面粗糙度根据该分度盘零件的形位特点,采用平直分模面。
由零件图可知,该分度盘零件各加工表面的粗糙度Ra均大于等于1.6μm 。
根据上述诸因素,可查表确定该锻件的尺寸公差和机械加工余量,所得结果列于表2-2中。
表2-2 分度盘锻造毛坯尺寸公差及机械加工余量锻件重量/kg 包容体重量/kg形状复杂系数材质系数公差等级7.3 11.9 2S1M普通级项目/mm 机械加工余量/mm 尺寸公差/mm 备注Φ180外圆1.21.12.3+-表2-14 2.0 表2-10Φ100外圆9.19.08.2+-表2-14 2.6 表2-10高度607.18.05.2+-表2-11 2.0 表2-13高度25(台阶面)5.17.02.2+-表2-11 2.0 表2-13注:根据表2-10的表注,将此表中所有公差按±1/2分配。
2.2.3绘制分度盘锻造毛坯简图由表2-2所得结果,绘制毛坯简图如图2-1所示。
图2-12.3 拟定分度盘工艺路线2.3.1定位基准的选择3.1.1精基准的选择根据该分度盘零件的技术要求和装配要求,选择分度盘大端面为精基准,零件上的很多表面都可以采用它们作为基准进行加工,即遵循了“基准统一”原则。
分度盘∅35H7mm的轴线是设计基准,选用其作为精基准定位加工分度盘∅100g6mm外圆柱面和台阶面,实现了设计基准和工艺基准的重合,保证了被加工表面的垂直度和同轴度要求。
在钻削均布圆周孔时采用∅100g6mm的轴心线作为精基准,做到了设计基准与工艺基准的统一。
3.1.2粗基准的选择作为粗基准的表面应平整,没有飞边、毛刺或其他表面缺欠。
此处选择分度盘∅100g6mm轴线作为粗基准,可以为后续工序准备好精基准。
2.3.2表面加工方法的确定根据分度盘零件图上个加工表面的尺寸精度和表面粗糙度,确定加工工件各表面的加工方法,如表2-3所示。
表2-3 分度盘零件各表面加工方案加工表面尺寸精度等级表面粗糙度Ra/μm加工方案备注大端面IT11 12.5 粗车表1-8外圆台阶面IT6 1.6 粗车—半精车—精车表1-8小端面IT11 12.5 粗车表1-8 大外圆IT10 12.5 粗车—半精车表1-6小外圆IT6 1.6 粗车—半精车—精车表1-86×Φ32孔IT13 12.5 钻—扩表1-7Φ35孔IT7 3.2钻—粗镗—半精镗—精镗表1-8Φ36孔IT13 12.5 粗车表1-8 Φ21孔IT13 12.5 钻表1-7 螺纹孔(6个)IT6 3.2 钻—攻螺纹表2-39 6×Φ12孔IT9 3.2 钻—铰表1-7 Φ10销孔IT7 3.2 钻—粗铰—精铰表1-7 弧形槽底面IT13 3.2 铣Φ10圆锥形孔IT12 12.5钻表1-7 2.3.3加工阶段划分该分度盘加工质量要求较高,可将加工阶段划分成粗加工、半精加工和精加工几个阶段。
2.3.4 工序集中与分散采用工序集中原则,尽可能在一次安装中加工许多表面,或尽量在同一台设备上连续完成较多的加工要求。
2.3.5工序顺序的安排1)机械加工工序遵循”先基准后其他“、“先粗后精”、“先主后次”、“先面后孔”的原则。
2)热处理工序因模锻件的表面层有硬皮,会加速刀具磨损和钝化,为改善切削加工性,模锻后对毛坯进行正火处理,软化硬皮;零件Φ100g6mm外圆面和台阶面需进行淬火,由于零件壁厚小,易变形,加之加工精度要求高,为尽量控制淬火变形,在零件粗加工后安排调质处理作预处理。
3)辅助工序在粗加工和半精加工后各安排一次中间检验,精加工后安排去毛刺、清洗和终检工序。
2.3.6确定工艺路线在综合考虑上述工序安排原则基础上,表2-4列出了分度盘的工艺路线。
表2-4 分度盘工艺路线及设备、工装的选用工序号工序名称机床设备刀具量具1 正火2 粗车大端面C620︒90偏刀游标卡尺3 粗车大外圆C620︒90偏刀游标卡尺4 钻大端孔立式钻床Z550麻花钻游标卡尺5 粗车小端面C620︒90偏刀游标卡尺6 粗车小外圆C620︒90偏刀游标卡尺7 粗车台阶面C620︒90偏刀游标卡尺8 钻Φ21孔立式钻床Z550麻花钻卡尺、塞规9 中间检验塞规、百分表、卡尺等10 调质处理硬度230~250HB11 半精车大端面C620︒90偏刀游标卡尺12 粗镗—半精镗—精镗卧式镗床镗刀内径千分尺、塞规13 车内槽C620 内槽车刀游标卡尺14 半精车小外圆C620︒90偏刀游标卡尺15 半精车台阶面C620︒90偏刀游标卡尺16 车削退刀槽C620 切槽刀游标卡尺17 钻—铰6×Φ12孔立式钻床Z550钻头复合铰刀卡尺、塞规18 铣弧形槽立式铣床X51 键槽铣刀游标卡尺19 钻—粗铰—精铰Φ10销孔立式钻床Z550麻花钻、铰刀内径千分尺20 中间检验塞规、百分表、卡尺等21 热处理—淬硬40~45HRC淬火机等22 精车小外圆C620︒90偏刀外径千分尺23 精车台阶面C620︒90偏刀外径千分尺24 钻—攻螺纹孔立式钻床Z550麻花钻、丝锥卡尺、塞规25 钻—扩孔6×Φ32孔立式钻床Z550麻花钻、扩孔钻卡尺、塞规26 去毛刺钳工台平锉27 清洗清洗机28 终检塞规、百分表、卡尺等2.4工序25—加工余量、工序尺寸和公差的确定1)钻孔余量钻Z=10.0mm2)由于需要保证Φ10圆锥形孔的尺寸要求,所以不能继续使用麻花钻进行扩孔,而采用多次扩孔的方法达到Φ32mm孔的尺寸要求。
查表2.5-48(《机械加工工艺手册》 李洪)可得扩孔工步余量:1Z =1.5mm 2Z =1.5mm 3Z =1.5mm 4Z =1.5mm 5Z =1.5mm 6Z =1.5mm 7Z =2.0mm ;8Z =2.0mm ;9Z =2.0mm ;10Z =2.0mm ;11Z =2.0mm ;12Z =2.0mm ;13Z =1.0mm 。
3)查表1-20可确定各工序尺寸的加工经济精度等级分别为:IT12、IT11、IT11、IT11、IT11、IT11、IT11、IT11、IT11、IT11、IT11、IT11、IT11。
根据以上结果,再查标准公差数值表可确定各工步的公差值分别为:0.15mm 、0.11mm 、0.11mm 、0.11mm 、0.11mm 、0.11mm 、0.13mm 、0.13mm 、0.13mm 、0.13mm 、0.13mm 、0.13mm 、0.13mm 、0.16mm 。
综上所述,该工序各工步的工序尺寸及公差分别为,钻孔:15.0010+∅mm :扩孔:11.005.11+∅mm 、11.0013+∅mm 、11.005.14+∅mm 、11.0016+∅mm 、11.005.17+∅mm 、13.0019+∅mm 、13.0021+∅mm 、13.0023+∅mm 、13.0025+∅mm 、13.0027+∅、13.0029+∅mm 、13.0031+∅mm 、16.0032+∅mm 。
2.5 切削用量、时间定额的计算由于孔的加工精度和表面粗糙度要求不高,所以在刀具强度允许的情况下,选择较大的切削用量和进给量。
2.5.1切削用量的计算 1)钻孔工步背吃刀量的确定 取p a =10.0mm 。
进给量的确定 由表5-21,选取该工步的每转进给量 f=0.2mm/r 。
切削速度的计算 由表5-21,按工件材料为45钢的条件选取,切削速度v 可取为20m/min 。
由公式(5-1) n=1000v/π d 可求得该工序钻头转速n=636.9r/min ,参照表4-9所列Z550立式钻床主轴转速,取转速n=735r/min 。