混铁炉耐火材料炉衬蚀损的调查与分析
八钢300t混铁炉炉衬侵蚀原因分析及材质选择

停 炉后 转炉 炼钢 厂工 程技术 人 员和耐 火材料 供
货方 技术 人 员共 同检 查3 0  ̄ 炉炉 衬各 部位 的侵 0Q 铁
蚀 情况 , 衬各 部位 的侵 蚀情况 见表 1 炉 。
30混铁 炉炉 衬侵 蚀原 因进行 分 析 , 新建 60 混 0t 为 0t
表 I 3 0混 铁 炉 炉衬 各 部 位 的 侵蚀 情 况 0t
新疆 钢 铁
9 期 7
4 . O . i 3 . 2 , 2 1 和 Fe 2 4 S 2 5 1 % A 1O . 3 O 3 2 2 3 O
CO( 十 Si s 一 — g) C( ) +Si) ( ) C( ) (,1 十 s
1. 0 , 2 8 使用 的渣 剂量 2 g 因 为该 3 0混铁 炉保 温 0。 0t 铁 水 温 度 一般 为 I5 ~ 1 0 采 用 焦炉 煤 气混 合 0 0C, 2 4
3 1 试验 方法 及条件 .
试 验 采 用坩 埚 侵 渣 法 , 选取 高 铝 砖 、 油 刚 玉 浸
砖 、 碳 化 硅 砖 和镁 铬 砖各 一 块按 照取 样 要 求切 取 铝
6 ×6 ×6 ( m) 立方 体 , 其 中心部 位 钻成 5 0 0 5r 的 a 在 3
x4 ( m) 0 r 的洞 穴 , a 凿成试 验 用坩 埚 。
维普资讯
2 0 年第 l 06 期
新疆 钢 铁
9 期 7
八 钢 3 0混 铁 炉 炉 衬侵 蚀 原 因分 析 及 材 质 选 择 0t
阿 不 力 克 木
( 疆 八 一钢 铁 股 份 有 限 公 司 ) 新 摘 要 : 针对 八钢 3 0 0 吨混 铁 炉 采 用 的 炉 衬 耐 火材 料 结 构 , 炉 衬 侵 蚀 原 因进 行 抗 渣 性 试验 分 析 , 60 对 为 0 吨混 铁
浅谈600t混铁炉内衬耐火材料的资源优化配置

浅谈600t混铁炉内衬耐火材料的资源优化配置本文通过对略钢600t混铁炉内衬耐火材料损毁原因的分析,制定几点优化混铁炉内衬耐火材料资源配置措施,有利于提高混铁炉的使用寿命,希望能对钢铁企业加强冶炼工艺,稳定生产节奏、降本增效带来一些帮助。
标签:混铁炉;内衬;耐火材料1 混铁炉简介混铁炉是转炉炼钢的重要辅助设备之一,起着均匀铁水成份、稳定铁水温度和贮存铁水保证铁水持续供应的功能。
近些年随着我国经济的发展,钢铁产量持续增长,钢铁的种类日益繁多,混铁炉的使用条件更加苛刻,加之混铁炉长期贮存铁水并频繁受铁和出铁,炉衬受到铁、渣以及重力冲刷和化学侵蚀作用,使得混铁炉的寿命出现缩短趋势。
提高混铁炉使用寿命,对保证铁水的正常供应,稳定转炉的正常生产节奏有着重要意义。
我国的混铁炉一般有300吨、600吨、900吨和1300吨几个类型,按照冶钢企业规模的不同而装备不同类型的混铁炉。
混铁炉炉体是由可以拆分的侧面凸起端盖和设有铁水输入口、铁水输出口的圆筒组成筒体装置。
炉体内部铺砌有高温耐火材料层,高温耐火材料层与炉体外壳之间的空隙填有主要成分为硅藻土料的隔热层,通过隔热层达到对炉体内衬高温耐热材料受热膨胀对炉壳产生压力的缓冲和阻止热传导,避免炉体材料的受热变形。
隔热层向里硅藻土砖层,硅藻土砖层向里是粘土砖层,与粘土砖层紧挨的是直接与铁水接触的混铁炉工作层,工作层大多数是用耐高温腐蚀的镁砖砌筑而成。
略钢炼钢分厂现有600吨混铁炉1座,60吨氧气顶吹转炉2座,配有六机六流150mm×150mm方坯连铸机一台,年吞吐铁水90多万吨,产钢100万吨左右。
铁水温度为1200℃~1350℃,铁水化学成分如下:燃气条件,略钢600吨混铁炉保温使用的燃气为高炉煤气,发热值较低,只有3000-3800KJ/Nm3。
为提高高炉煤气的燃烧温度,在煤气燃烧时配入适量的富氧,以此提高燃烧温度。
2 混铁炉内衬耐火材料损毁原因混铁炉整体性能以及使用寿命如何对钢铁冶炼有着重要意义,我国研究技术人员以及工程技术人员对混铁炉的建造和维护技术进行了艰苦的探索,并且取得了不少成果。
高炉炉衬侵蚀机理的研究

Ku n mi n g 6 5 0 0 9 3, C h i n a)
ABSTRA CT : Us s i n g t h e me t h o d s o f S EM , XRD a n d EDS a n a l y s i s, t he l i n i n g d a ma g e o f KI SCO ’ S No .6 b l a究
袁 国翠 丁跃 华 代 林 晴
( 昆明理工 大学冶 金 与能源 工程 学院 , 昆明 6 5 0 0 9 3 )
摘 要 : 采用 S E M、 X R D 、 E D S 等显微分析方法 , 对某公司 6号高炉炉缸和炉底砖衬进行 了侵蚀 机理的
研究 。6号 高 炉 长 寿 主要 原 因是 炉 衬 良好 的 导 热性 和 T i ( C N) 的保 护 , 而 导 致 炉 衬 破 损 的 主要 原 因 是 热 应力作用 , 以及 铁 水 、 钾、 钠 和 锌 对碳 砖 的侵 蚀 , 且 钾 的 侵 蚀 比钠 的更 严 重 。金 属 铅 主 要 以 气态 和液 态 的
t h e r ma l c o n d u c t i v i t y a n d T i ( C N)p r o t e c t i o n ,w h i l e t h e ma i n r e a s o n o f r f u r n a c e l i n i n g d a m a g e l i e s i n t h e t h e r ma l
电炉维修:中频炉炉衬损毁的原因及解决方案
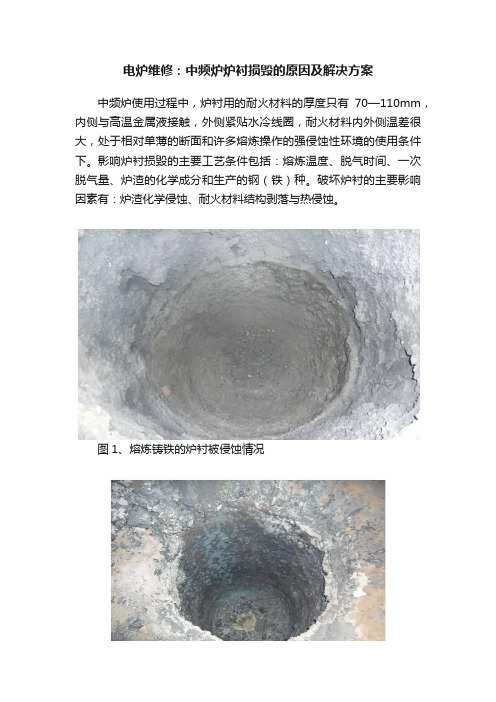
电炉维修:中频炉炉衬损毁的原因及解决方案中频炉使用过程中,炉衬用的耐火材料的厚度只有70—110mm,内侧与高温金属液接触,外侧紧贴水冷线圈,耐火材料内外侧温差很大,处于相对单薄的断面和许多熔炼操作的强侵蚀性环境的使用条件下。
影响炉衬损毁的主要工艺条件包括:熔炼温度、脱气时间、一次脱气量、炉渣的化学成分和生产的钢(铁)种。
破坏炉衬的主要影响因素有:炉渣化学侵蚀、耐火材料结构剥落与热侵蚀。
图1、熔炼铸铁的炉衬被侵蚀情况图2、熔炼铸钢的炉衬被侵蚀情况1.中频炉的炉衬中频炉的炉衬通常是用各种规格粒度组成的耐火材料打结而制成(常用的耐火材料主要有镁质、石英质、铝质及复合材料四大类)。
其特点是:直接结合。
因而抗侵蚀性能高、力学强度高、抗热震性能良好。
图3、严格按打结工艺打结出的炉衬2、镁质炉衬材料的损毁机理以镁质耐火材料为例,阐述一下镁质材料的损毁机理:镁质材料损毁的主要表现是:流动钢液造成的热侵蚀和炉渣成分渗透进入材料中引起的化学侵蚀。
熔炼过程中溶液会通过耐火材料基体中的毛细孔道渗入到耐火材料基体内部侵蚀炉衬。
渗入到耐火材料基体内部的成分包括;渣中的CaO、SiO2、FeO; 钢液中的Fe、Si、Ai、Mn、C,甚至还包括金属蒸汽,CO气体等。
这些渗入成分沉积在耐火材料毛细孔道中,造成耐火材料工作面的物理化学性能与原耐火材料基体的不连续性,在操作温度急变下将出现裂纹、剥落和结构疏松,严格的说这个损毁过程比溶解损毁过程严重得多。
加入炉内的金属材料会带入各种不同的氧化物,不同材质、不同炉次的炉渣成份也不尽相同。
炉渣中存在的各种氧化物、碳化物、硫化物及各种形态的复合化合物,大部分都会和炉衬发生化学反应,生成不同熔点的新的化合物。
反应中生成的一些低熔点氧化物如铁橄榄石(FeOSiO2)、锰橄榄石(MnOSiO2)等熔点一般在1200℃左右范围内。
低熔点渣具有极好的流动性,可能会形成助熔剂作用,对炉衬产生剧烈的化学侵蚀,从而降低炉衬的使用寿命。
混铁炉用耐材的现状和前景

混铁炉用耐火材料的发展和现状摘要:本文主要介绍了混铁炉的结构以及针对不同部位不同工作要求提出综合砌筑方案,炉顶、炉底和炉墙整体浇注, 并在不同部位选用不同的优质炉衬耐火材料, 能使混铁炉炉衬实现均匀侵蚀,既降低了成本,又节约了耐材。
关键词:混铁炉; 炉衬;综合砌筑前言混铁炉是炼钢车间贮存铁水的热工设备。
它的用途除了贮存铁水外, 还有混匀铁水成分和保持铁水温度的作用, 另外它在协调炼铁、炼钢生产过程及调节铁水的供需平衡方面也起着非常重要的作用。
由于它长期储存高温铁水, 受铁水、渣的长时间的冲刷和侵蚀, 其炉衬材料的抗冲刷性、耐侵蚀性及抗热震稳定性等性能的优劣, 对混铁炉的使用寿命起着关键性的作用。
1概述混铁炉由炉体; 支撑底座; 倾动装置;气动松闸机构; 炉顶平台; 煤气、空气管道; 炉门升降卷扬; 鼓风装置; 干油润滑系统; 电控系统等组成( 见图1)2混铁炉内衬材料的损毁传统的混铁炉内衬全部使用砖砌形式, 主要材料有高铝砖、镁砖、铝碳化硅炭砖、硅砖及镁铝砖等,也有的厂家针对砖砌出铁嘴损毁较快的现状, 对出铁嘴材料进行了改进, 用浇注料对出铁嘴进行整体浇注。
近年来国内出现了整体浇注的混铁炉内衬,其材料包括低水泥高铝浇注料、刚玉- 莫来石- 碳化硅浇注料及Al2O3- SiO2 质微膨胀浇注料。
混铁炉使用时和铁水罐相似,都是不直接接触铁水,铁水和炉壁有一层耐火材料,大概工作温度在1350~1450之间,它的用途除了贮存铁水外, 还有混匀铁水成分和保持铁水温度的作用, 另外它在协调炼铁、炼钢生产过程及调节铁水的供需平衡方面也起着非常重要的作用。
由于它长期储存高温铁水, 受铁水、渣的长时间的冲刷和侵蚀, 其炉衬材料的抗冲刷性、耐侵蚀性及抗热震稳定性等性能的优劣, 对混铁炉的使用寿命起着关键性的作用。
常见的混铁炉损毁状况有:炉底耐火材料承受高温铁水的渗透; 不规则操作引起渣线上下浮动, 渣线区域面积增大; 铁口拐角处的墙体及沟口受铁水的频繁冲刷和侵蚀; 因化学侵蚀导致的掉砖、砖层变薄甚至炉衬穿漏和出铁口渣封。
钢铁行业耐火材料应用与管理中存在的问题探究与讨论

I ndustry development行业发展钢铁行业耐火材料应用与管理中存在的问题探究与讨论张 岭摘要:我国耐火材料技术的发展主要体现在耐火材料的研发和制造上。
然而,在应用方面,钢铁行业的冶金耐火材料技术差距不断扩大。
与此同时,由于资源、能源和环境等因素的影响,耐火材料产业的发展离不开节能环保等技术的操作水平。
因此,中国耐火材料产业的发展需要进行深入和系统的思考。
本文对国内外耐火材料的生产与应用现状进行了探讨。
关键词:钢铁行业;耐火材料;应用;管理在工业窑炉中,耐火材料是炉窑衬里结构中最为重要的一种材料,其性能的好坏直接影响着衬里的使用时限和使用效果。
目前,国内的耐火材料已经由最初的冶金辅助材料向主体冶金原材料过渡,许多新的冶金产品、新材料的开发,都需要高质量的耐火材料。
近几年,随着对国外耐火材料的分析,国内耐火材料产业发展迅速,已接近国际先进水平,有些产品已达国际先进水平。
1 吨钢耐火材料应用分析1.1 耐火材料应用成本控制狭义上来讲,这指的是耐火材料的生产成本;广义上来看,它不仅包括耐火材料本身的成本,还包括物流、施工和耐火材料质量等方面的成本。
吨钢的耐火材料消耗量是指制造1吨钢材所需的耐火材料重量。
事实上,吨钢和电钢的耐火材料消耗不是相互对立的,而是一个有机的整体。
降低吨钢的耐火材料生产成本有两个主要途径。
一是选择质量较差但价格低廉的耐火材料,虽然耐火材料用量较大,但可以实现电钢耐火材料的低成本;二是采用优质的耐火材料,尽管价格较高,但可以显著延长耐火材料的使用寿命,减少单耗。
这同时可以降低由于耐火材料污染引起的钢液净化费用,并降低吨钢的生产成本。
吨钢的耐火材料成本和耐火材料消耗量是衡量钢铁行业使用耐火材料的重要指标。
由于不同公司有不同的想法和出发点,对这个指标的定义也不尽相同。
观念上,国内大部分的钢铁企业采取了耐火材料区域整体承包方式。
这种方式只考虑到耐火材料的成本,所以大多数企业只计算了每吨耐火材料的成本,而对于电钢的耐火材料消耗量没有进行控制。
浅谈600t混铁炉内衬耐火材料的资源优化配置

达到对各个高炉输入混铁炉的不同成分铁水的均匀混合以及温度的调 匀。 有时由于误操作或其他原因可能会导致混铁炉转速不均, 造成内部 铁水对混铁炉内衬耐火材料冲刷力矩产生变化 ,造成混铁炉内衬耐火 材料受 损。主要集 中在 出铁 口、 炉底铁水 冲击 区。 2 . 4操 作不当 迫于生产任务紧急 , 一些钢铁冶炼企业尤其是在一些中小钢铁冶 炼工 厂 , 混铁炉 经常 出现不恰 当 的操 作 , 加剧 了混铁 炉 内衬 耐火材 料 的 损毁状 况。 2 . 4 . 1 煤气供应不合理。 为了节省能源, 部分钢铁冶炼企业及工厂对 混铁炉的煤气供应停送频繁。转炉需要铁水供应时,给混铁炉输入煤 气, 升高混铁炉内部温度 ; 而转炉不需要铁水供应时, 就停止向混铁炉 输如煤气, 降低混铁炉内部温度 , 加之高炉煤气质量较差 , 发热值不高 等原 因造 成混铁 炉 内部 温度 波动频 繁 ,超 过了混铁 炉 内衬 耐火材 料 的 热胀冷缩恢 复系数 , 造成 内衬耐火 材料损伤 。 2 . 4 . 2铁水成分控制不当。由于对高炉输入混铁炉的铁水成分分析 不当, 或铁水质量成分较差, 造成混铁炉内部各高炉铁水成分之间的不 稳定 , 甚 至发生化 学反应 , 造成 对混铁 炉内衬耐火 材料 的不 均衡腐蚀 。 2 . 5炉砖材料 与砌筑技 术 产钢 1 0 0 万 吨左右 。 建 设混铁炉 所采用 的炉砖 材料 以及使用 的砌筑 技术 ,也是影 响混 铁炉 内衬耐 火材料性能 的主要 因素之一 。 铁 水温度为 1 2 0 0  ̄ C ~ 1 3 5 0 c C , 铁水化 学成分 如下 : 2 5 . 1炉砖材料。混铁炉炉砖材料应当依据混铁炉的操作条件和工 l c ( % ) S i ( % ) t C t n ( % ) P( % ) S ( % ) 作环境进行分析、 选择 。混铁炉内铁水矿渣呈碱性渣时 , 应当采用镁质 l 3 . 4 5 — 4 . 4 0 0 . 3 3 - 0 . 9 7 0 . 1 1 - 0 . 4 0 O . 1 4 1 - 0 . 2 5 0 0 . 0 2 2 — 0 . 0 7 0 耐火 材料 ;而当铁水 矿渣 呈酸性渣 时 ,则 采用硅 酸铝质 耐火材 料更 适 合, 要防止铁水矿渣以及铁水成分与混铁炉炉砖产生化学反应 , 破坏混 燃气条件, 略钢 6 0 0吨混铁炉保温使用的燃气为高炉煤气, 发热值 铁炉 内衬 内火材 料 。 较低 , 只有 3 0 0 0 - 3 8 0 0 K J / N m 。 为提高高炉煤 气的燃烧 温度 , 在煤气燃 烧 2 5 _ 2砌筑技术。混铁炉的砌筑技术也是影响混铁炉内衬耐火材料 时配 ^ 适量的富氧, 以此提高燃烧温度。 整体 眭能的关 键。能否在混 铁炉 的关键 部位使 用高档 的内衬耐火 材料 , 2混铁炉 内衬耐火材料 损毁原 因 决定 了混铁 炉内衬 耐火材 料的使用 时 间 ,以及 能够承 受的铁水 温度 和 混铁炉整体性能以及使用寿命如何对钢铁冶炼有着重要意义 , 我 化学成 分腐 蚀 的极 限 。 国研究技术人员 以及工程技术人员对混铁炉的建造和维护技术进行了 3混铁炉内衬耐火材料的资源优化配置 艰 苦 的探 索 , 并且取得 了不少成 果。可是 随着 我国一些列 改革措施 的实 综合以上论述我们知道混铁炉在现代钢铁冶炼领域有着很重要的 行, 我 国的各项工 程建 陕速发 展 , 对钢材 的需求 从钢材 的种类 到钢 材 意义 ,以及造 成混铁 炉 内衬 耐火材 料损毁 的几种 原 因 ,我们可 以 了解 的质量都提高了要求 , 由于缺乏技术上更新, 以及为了高产一些钢铁冶 到,对混铁炉内衬耐火材料资源进行优化配置是钢铁冶炼企业现在面 炼企业出现了违规操作、 延误设备维护时间等不恰当的生产方式, 导致 临的—个重要问题 , 同时我们也知道, 要对混铁炉内衬耐火材料进行资 源优化配置需要从整体上来把握, 从各个方面加强措施。 我国钢铁冶炼企业的混铁炉经常出现内衬损毁的现象。 2 . 1化学 侵蚀作用 3 . 1完善 的 寸 . 力案 根据钢铁冶炼企业的冶炼技术和冶炼环境 ,对混铁炉进行完善的 化学侵蚀是指由于对钢铁冶炼采用的铁矿石成分缺乏详细了解, 造成高炉输入混铁炉的铁水中含有对混铁炉内衬耐火材料产生化学腐 设计 , 包括混铁炉吨位、 炉砖材料 、 砌筑技术、 混铁炉炉形等 , 从整体上把 蚀作用的化学成分 , 其与混铁炉内衬耐火材料发生化学反应 , 造成混铁 握混铁炉的各个细节 ,以及可能产生的各种损毁混铁炉内衬内火材料 炉 内衬 耐火材 料损毁 。主要是铁 矿石 冶炼设备 产生 的矿物残 渣混 于铁 的问题 , 并 制定相应 的应对措施 。 水 中形成 的。 3 . 2研发 新型冶炼 工艺 2 2 热应 力损毁 钢铁冶炼企业应当加强对新型冶炼工艺的研发 ,提高铁矿石的开 热应力损毁是指由高炉输入混铁炉的铁水成分温度过高,超过了 发利用率, 降低矿物残渣, 净化铁水成分 , 从而避免铁水混入矿物残渣 混 铁炉 内衬耐火 材料 的温度 和膨 胀 系数 承受极 限 ,造 成混铁 炉 内衬 耐 对 混铁炉 内衬耐火材 料造成 的各种损毁 。 火 材料不 同程度 的损毁 。或生产 中, 当铁水 供应 紧张时 , 混 铁炉 内铁水 3 _ 3专业 的混铁炉操作 维护人 员 液 面较低 , 有 时甚至将铁 水倒空 , 导致 渣线 区域加 宽 , 易损 面积增 大 。 培养专业的混铁操作炉维护人员 , 依照操作规范正确操作混铁炉 , 2 . 3机械 冲刷 及时地对混铁炉进行矿物残渣清理 , 以及及时对混铁炉炉砖进行修补 , 机械冲刷是造成混铁炉内衬耐火材料损毁最常见原因, 包含以下 避免混铁 炉 内衬耐 火材料发 生损毁 。 两 种 因素 。 混铁炉内衬耐火材料资源的优化配置是一个复杂的系统化工程 , 2 . 3 . 1 矿石 残渣 。 主要 是 由于对铁 矿石 的选矿 不准 , 导致 有高炉冶炼 需 要 内衬 耐火 材料开发 人员 、混铁炉 结构设 计 人员以及 混铁炉操 作维 出来输入混铁炉的铁水很有矿石残渣超量,或是混铁炉内矿石残渣清 护人员的通力合作 , 因此在做好技术上的措施外, 还要加强各部门间的 理不及时, 导致矿石残渣刮伤混铁炉内衬耐火材料 ; 或是附着在内衬材 管理措施实施 , 协调各部门的高效运作 , 这样才能做到混铁炉 内衬耐火 料上, 降低了内衬材料的受热膨胀系数, 造成混铁炉 内衬耐火材料的损 材料资源的全面优化配置。 伤; 亦或混铁炉长时间没有进行清理 , 导致铁水中混入的矿石残渣大量 参考 文献 堆积在混铁炉内, 造成炉压上升 , 导致混铁炉内衬耐火材料损坏 , 集中 [ 1 】 朱波. 莱钢混铁炉长寿技术的应用Ⅲ. 耐火材料, 2 0 1 1 , 4 5 ( 1 ) : 6 7 _ 6 8 . 在前后墙渣线部位。 [ 2 ] 张兴业. 我国连铸 中间包内衬 耐火材料 的发展及应用叨_ 山东冶金 , 2 3 - 2混铁炉转速。 一般的混铁炉都有固定的转速, 通过平稳的转动 2 0 0 9 , 3 1 (  ̄, - 2 9 . 混铁炉是转炉炼钢的重要辅助设备之一 , 起着均匀铁水成份 、 稳定 铁水温度和贮存铁水保证铁水持续供应的功能。近些年随着我国经济 的发展 , 钢铁产量持续增长 , 钢铁的种类 E t 益繁多, 混铁炉的使用条件 更加苛刻, 加之混铁炉长期贮存铁水并频繁受铁和出铁 , 炉衬受到铁、 渣以及重力冲刷和化学侵蚀作用 , 使得混铁炉的寿命出现缩短趋势。提 高混铁炉使用寿命, 对保证铁水的正常供应, 稳定转炉的正常生产节奏 有 着重要 意义 。我 国的混铁炉~ 般有 3 0 0 吨、 6 0 0吨 、 9 0 0吨和 1 3 0 0吨 几个类型 , 按照冶钢企业规模的不同而装备不同类型的混铁炉。 混铁炉 炉体是由可以拆分的侧面凸起端盖和设有铁水输入 口、铁水输 出口的 圆筒组成简体装置。 炉体内部铺砌有高温耐火材料层 , 高温耐火材料层 与炉体外壳之间的空隙填有主要成分为硅藻土料的隔热层,通过隔热 层达到对炉体内衬高温耐热材料受热膨胀对炉壳产�
高炉耐火材料磨损机理及对策

1简介高炉耐火材料的磨损对高炉炉龄有决定性作用。
高炉炉役期间,可以在生产时,对炉衬材料进行几次维修。
然而,炉膛区的修理工作需要停止生产。
因此,高炉炉膛是非常关键的部分。
高炉炉龄不仅取决于耐火材料及其性能,还取决于设计标准(冷却设备设计,电气机械设计)和操作标准。
所以,规定了碳块的要求。
耐火材料的磨损决定高炉炉龄。
由于在高炉上部区已制定了现代修补技术,只有风口以下接触炉渣和铁水的下炉膛和炉底区在中间不能进行修补。
因此,这个区的炉衬需要高质量炉衬材料。
最重要的磨损参数之一是铁水阻力,本文解释了标准和微气孔碳的测量。
另外,比较了微气孔族中的不同材料。
2热化学磨损所有磨损机理都是联合起作用的。
为更好地理解,下面分别说明不同的磨损机理。
(1)铁水中碳溶解造成的磨损这是难熔碳的溶解,在高炉下部不同温度和流动条件下碳块中的碳溶解在铁水中,类似于炉料中焦炭溶解。
(2)铁水渗透造成的磨损这个渗透过程更适宜在高炉下部铁水池的高铁水静压力下进行。
由于碳块的多孔性,最初溶解后开始渗透,同时材料性能开始变化。
在铁渗透后,织构破裂,线裂纹形成。
连同铁水的永久侵蚀和温度变化,导致碳块碎裂。
在有碱金属和锌的情况下,它促使脆层形成。
(3)碱金属循环造成的磨损碱金属以氧化物和硫酸盐形式与炉料、焦炭一起进入高炉,并发生反应。
它们在三个可能的反应中产生碳料:渗透的碱金属氧化;把碱金属蒸汽添入碳结构,导致局部容积增加;碱金属与添加剂或杂质在炉衬中产生反应。
(4)氧化造成的磨损立式冷却壁漏水或有缺陷的风口会出现碳衬氧化。
来自冷却系统的热鼓风或水蒸汽能导致多孔粘结基体加速磨损。
因此,碳的耐磨组分将溶解,并受到铁水冲洗。
(5)CO分解造成的磨损按照布氏反应,另一个磨损因素与CO分解有关。
在一定的温度条件下,将出现碳沉积,并由此造成裂纹。
3热机械磨损(1)热应力造成的磨损热面处的炉衬暴露于高温之下,温度达到1150℃。
这个区的磨损受到温度分布和合成压缩应力控制,它取决于炉衬的机械物理性能。
- 1、下载文档前请自行甄别文档内容的完整性,平台不提供额外的编辑、内容补充、找答案等附加服务。
- 2、"仅部分预览"的文档,不可在线预览部分如存在完整性等问题,可反馈申请退款(可完整预览的文档不适用该条件!)。
- 3、如文档侵犯您的权益,请联系客服反馈,我们会尽快为您处理(人工客服工作时间:9:00-18:30)。
混铁炉耐火材料炉衬蚀损的调查与分析徐国涛徐静波杜鹤桂摘要进行了600t混铁炉的耐火材料蚀损调查与分析,认为Al2O3-SiC-C砖的蚀损出铁口以亚铁渣氧化熔蚀为主,前墙以渣蚀渗透这主。
关键词混铁炉耐火材料蚀损INVESTIGATION AND ANALYSIS ON WRECKAGE OF REFRACTORY LINING IN HOT METAL MIXERXu Guotao XuJingboWuhan Iron & Steel Corp.Du HeguiNortheastern UniversitySynopsis Causes for wreckimg of the refractory lining in 600 ton hot metal mixer have been investigated and analyzed. Results show that the wrecckage of Al2O3-SiC-C bricks used in the lining of taphole is primarily due to oxidation-melting of FeO slag and wrecking of bricks in the front wall is out of the slag penetration reaction.Keywords Hot metal mixer refractroy wreck1 前言混铁炉的功能在于混匀铁水,均温提质。
目前,国内武钢、首钢、太钢、包钢、重钢等厂由于各种原因,仍然使用600t混铁炉,其使用寿命在1~2年,维修任务比较频繁,成本也较高。
由于不定时的高温回炉钢水的影响,以及KR法脱硫后铁水的温度变化难以控制,造成混铁炉的温度波动较大,炉衬的热应力破坏严重,加之高炉渣碱度为1.0~1.03左右,酸性渣对耐火材料的侵蚀较大,总体上讲混铁炉寿命较低。
实际操作中,常通过修补料修补出铁口及炉底,但因粘附能力差,砖衬变质层氧化而形成裂纹,造成粘附层易起拱上浮,效果差,材料消耗量大,生产成本增高。
为了弄清混铁炉内耐火材料的侵蚀状况,在武钢二炼钢厂600t混铁炉2号炉大修期间,对炉衬的蚀损进行了调查,分析了残砖的结构与性能,以探讨其侵蚀机理,改进耐火材料的品质及砌筑维护工艺水平,以提高混铁炉的使用寿命与工作效率。
2 混铁炉残砖状况及分析混铁炉内砌砖大致可分为工作层与保温层,蚀损取样主要在工作层。
炉顶为高铝砖干砌;出铁口使用了镁砖及Al2O3-SiC-C砖,湿砌;前墙使用了不烧铝碳化硅碳砖,湿砌;后墙用镁砖干砌;炉底用镁砖干砌。
干砌的砖缝一般不大于1.5~2mm,湿砌的砖缝一般不大于2mm。
1998年2月二炼钢厂2号混铁炉大修,拆出铁口时,发现使用的不烧铝碳化硅炭砖残砖砖质轻,砖中粗颗粒大,外观呈黑色,不耐磨不耐蚀,平砌砖345mm的长度蚀损掉1/3至2/3,表面挂铁渣层厚5~16mm。
工作层疏松、多孔,砖背热面有氧化现象,表层泛红白色、厚3~5mm,残砖气孔率19%,体积密度2.52g/cm3。
拱顶3环高铝砖仅热面一环有20~36mm的变质层,为铁系粘附物及少量的低熔点出物。
炉前墙铝碳化硅炭砖的渣反应层厚度约15~32mm,变质层厚达48~60mm,切割残砖,发现沿砖缝铁水渗入深度在50~140mm,并横向渗入砖中的孔隙内,形成0.2~1mm宽、长不等的铁相弥散状分布带,少量铁粒可达2×5mm,残砖的气孔率17%,体积密度为2.76g/cm3。
炉底镁砖侵蚀均匀,工作层及变质层的厚度约3~5mm,且结构致密。
对残砖进行了化学分析,C1为出铁口用铝碳化硅炭砖,Cq为前墙用铝碳化硅炭砖,以1号表示近热面30mm以内的样品成分,2号表示近热面30~60mm以内的样品成分,结果如表1示。
表1 混铁炉炉衬残砖的化学成分/%(wt)3 镁砖残砖3.1 镁砖残砖镁砖残砖显微镜下呈桔黄色,工作层厚度2~3mm。
从蚀损状况看可分成四个层带。
未变带:矿物以方镁石为主,其间有少量橄榄石与硅酸盐相充填,晶粒尺寸在0.02~0.26mm,一般为0.088mm;白色过渡带:(厚0.08~0.56mm)方镁石晶粒长大,橄榄石及玻璃相较少;棕褐色已变带:(厚0.08~0.4mm)方镁石晶间有大量铁酸镁生成,呈细小柱状、粒状,少量硅酸盐及零星气孔分布其间;灰黑色工作带:(厚1~2mm)矿物以橄榄石为主,呈板柱状、粒状,均匀密集分布,其次为RO相(FeO>MgO)和氧化铁,氧化铁呈大块熔蚀状,弥散分布,局部富集,气孔变大。
3.2 铝碳化硅砖残砖3.2.1 原砖原砖含骨料和细粉。
骨料为板状,、粒状及桶状刚玉,含少量铝矾土及莫来石与玻璃相。
细粉以石墨为主,有少量细晶刚玉与碳化硅。
刚玉晶粒尺寸为0.008~0.08mm,一般为0.036mm,铝矾土呈半晶质、隐晶质。
莫来石呈细小针状、柱状,在玻璃相中析出,局部富集。
石墨呈板片状、条带状,均匀分布在细粉中,粒径在0.025~0.225mm,一般在0.0625mm,碳化硅呈板状、四方粒状,在细粉中零散分布,晶粒尺寸一般为0.0625~0.095mm(如图1示)。
图1 反光160×1.石墨(灰白色)2.刚玉(白色)3.碳化硅(亮白色)3.2.2 出铁口处残砖从蚀损样看残砖可分为未变带、过渡带与工作带。
未变带组成与原砖类似,不同之处在于刚玉颗粒中微气孔较多,细粉中碳化硅极少,局部见硅酸盐玻璃相零星分布,裂纹在颗粒边缘明显可见。
过渡带(厚1.5~2mm)呈棕黄色,矿物以长石为主,均匀密集分布;其次为少量橄榄石呈板柱状、圆粒状,少量RO相呈四方粒状,零星分布;局部见刚玉颗粒周围有微量尖晶石呈六边形、三角形、棱角状分布。
工作带(厚约2mm)呈褐黑色,矿物以橄榄石为主,呈板柱状、粒状均匀密集分布;其次为少量的黄长石呈针状、短柱状与树枝状;少量磁铁矿填充其间,呈自形半形晶零星分布,局部富集。
残留石英呈粒状,晶面有裂纹,局部较多,气孔多以黑色封闭气孔为主,不规则分布。
(图2~3示)图2 正交光25×长石呈聚片双晶(灰白色)图3 正交光100×残留石英(白色)图4 反光160×1.橄榄石(灰色)2.磁铁矿(白色)3.黄长石(深灰色)3.2.3 前墙处残砖侵蚀状况大致可分为两个层带,即原砖带与工作带。
原砖带矿物与出铁口处铝碳化硅砖类似,不同之处在于有微量黄铁矿在刚玉颗粒与细粉间零星分布,且局部残留石英。
工作带呈棕黄带褐色,矿物以黄长石为主,呈针状、细条状、粒状,形成梳状、编织席状结构,均匀密集分布;其次为少量玻璃相呈棕褐色在晶间充填;微量的赤铁矿呈粒状、半自形晶状局部富集,气孔比出铁口处残砖内要小,呈弥散分布。
(图5~图6)。
图5 透光100×1.黄长石(针状、细条状)2.玻璃相(黑色)3.气孔(白色)图6 反光160×注:局部赤铁矿富集(亮白色)4 蚀损的原因与讨论4.1 矿物的变化影响混铁炉内镁砖的蚀损比较均匀,从未变带。
到工作带,矿物变化主要因含铁相的渗透及与渣中SiO2、CaO、MgO等成分反应而来,镁砖本身抗碱性渣的能力较强。
但在渣碱度C/S=1.0左右时,工作层内MgO与渣铁相反应生成橄榄石,2FeO*SiO2熔点仅1205℃,而2FeO*SiO2熔点为1890℃,两者之间可以形成完全固熔体,共熔温度在上述两矿物熔点之间变化。
渣中FeO、SiO2含量越大,与镁砖反应生成的矿物熔点也越低,当其熔点低于铁水处理温度(1320~1400℃间变化)时,工作面出现熔损,低熔物进入渣中。
变质层中含铁酸镁,MgO与FeO可形成连续固熔体,且熔点较高,如砖结构致密,高粘滞的变质层矿物对耐蚀性有益。
铝碳化硅炭砖含有石墨,所用部位不同,氧化程度不一,出铁口与前墙处残砖的未变带含石墨各为9.32%及13.03%。
加入石墨,因其高温下不与铁水浸润可防止渣铁的渗透,耐蚀性好,且压砖易于结构致密,抗热震性好。
铁水预脱硫使用了CaO-CaF2系或CaC2系脱硫剂,增加了铁渣的CaO 含量,渣相仍以黄长石为主,进入混铁炉后,当铁水兑出时,渣粘挂于炉衬上。
前墙及出铁口部位的铝碳化硅炭中石墨氧化形成脱碳层,渣渗透入砖中,并与其中的Al2O3、SiO2反应,形成钙长石或橄榄石。
从过渡带到工作带,出铁口残砖内黄长石减少,橄榄石增多,与其工作状态有关,出铁后,金属铁及少量渣粘附于炉衬,铁相氧化生成氧化亚铁或氧化铁,化学分析表明铁渣中含铁系氧化物达84.74%,另外SiO2含量达7.22%,铁橄榄石熔点低,渗透力也强,FeO对石墨碳的氧化能力也强,石墨氧化,结构疏松,耐火材料的侵蚀也加快了。
有人[1]研究了铝炭砖及铝碳化硅炭砖在高FeO渣中的侵蚀性能,侵蚀速度前者可达5.88mm/h,后者可达0.78mm/h,这也验证了FeO对石墨有较强的侵蚀能力。
钙铁橄榄石与钙镁橄榄石、钙锰橄榄石可形成连续固熔体,黄长石也可形成固熔体,其熔点都较低,这就引起出铁口处的熔损较大。
前墙处铝碳化硅炭砖因使用中砖面被铁水覆盖,出铁水后,渣层均匀覆盖砖表面,石墨的被氧化脱碳能力弱一些,且渣相中FeO含量不高,矿物以黄长石为主,黄长石熔点为1550℃,相对而言,耐蚀能力要强些。
实际破损调查前墙铝碳化硅炭砖侵蚀较严重,主要可能还有两方面因素:砖自身抗氧化能力差,存在背热面脱碳层,热面及变质层结构疏松;砖缝泥浆质量差,与砖不配套,铁渣从砖缝渗入的深度可达140mm,并横向渗入砖中孔隙形成铁相的弥散分布。
4.2 铝碳化硅炭砖的抗氧化性不烧铝碳化硅炭砖性能优良,有一个前提:高温下石墨不被氧化,砖结构致密。
混铁炉内存在氧化气氛,如果砖的高温抗氧化性不好,使用性能也不佳。
对铝碳砖系列产品进行脱硫脱磷剂的侵蚀试验表明,抗氧化性好的不烧铝碳化硅炭砖耐侵蚀性好,表面存在釉状保护膜,内层石墨未氧化。
反之,即使砖常规性能好,耐侵蚀性也差。
从热力学角度看:碳、石墨、碳化硅、硅、氧化亚铁的氧化还原都各有一定的温度条件。
2C+O2=2CO ΔG°=-223426-175.31TC+CO2=2CO ΔG°=169452-172.69TT反≥708℃SiC+O2=SiO2+CΔG°=-818097+174.25TFeO+C=Fe+CO ΔG°=147904-150.2TT反≥712℃Si+O2=SiO2ΔG°=-871527+181.2T热力学数据[3]的计算表明:硅、碳化硅的氧化均优先于碳的氧化,当Si、SiC的氧化物对砖内变质层的石墨形成有效的保护膜时,砖衬热面氧化物才可能具备抗渣蚀的能力。