厚度自动控制(AGC)资料
冷轧控制AGC简介

FB AGC FF AGC
FB AGC FF AGC
FB AGC
H2
h5D
COMPEN
MFG5 CALCULATION
h4X MFG4
||||||
CALCULATION
||||||
hm3
MFG3 CALCULATION
hm2 MFG2
||||||
CALCULATION
H5
H4
H3
V5D V4D
V4D V3D COMPEN
传统. AGC
高级 AGC
h≦0.3 96.5
98.4
0.3<h≦0.5 96.6
98.3
0.5<h
96.9
98.4
1.0%
传统. AGC
高级 AGC
98.9 99.8 99.0 99.9
99.1 99.9
超差最小化的方法 (厚度控制)
问题
设定值的精度 FGC 部分误差 (1)热卷厚度
/硬度变化 (2)轧制期间摩擦力的变化
轧制计划 2.3mm→0.233mm× 905mm 100
2.4%
(μm)
(μm)
-100 20 -20
2000
高级 AGC
± 0.75 μm (0.32%)
Conventional AGC
± 1.5μm (0.64%)
(P Company)
(mpm)
0
成品厚差合格率(%)
精度
(mm)
厚度
0.45%
厚度 偏差(p-p)
16.0μm
12.0μm
加减速部分 厚差
8.0μm 4.0μm
入口热卷 厚差
轧辊偏心对 厚差影响
轧机厚度自动控制AGC系统说明

轧机厚度自动控制AGC系统使 用 说 明 书中色科技股份有限公司装备所自动化室二零零九年八月二十五日目 录第一篇 软件使用说明书第一章 操作软件功能简介第二章 操作界面区简介第三章 操作使用说明第二篇 硬件使用说明书第一章 接口板、计算机板跨接配置图 第三篇 维护与检修第一章 系统维护简介及维护注意事项第二章 工程师站使用说明第三章 检测程序的使用第四章 常见故障判定方法第四篇 泵站触摸屏操作说明第五篇 常见故障的判定方法附录:第一章 目录第二章 系统内部接线表第三章 系统外部接线表第四章 系统接线原理图第五章 系统接口电路单元图第一篇软 件 说 明 书第一章 操作软件功能简介.设定系统轧制参数;.选择系统工作方式;.系统调零;.显示时实参数的棒棒图、馅饼图、动态曲线;.显示系统的工作方式、状态和报警。
以下就各功能进行分述:1、在轧机靠零前操作手需根据轧制工艺,设定每道次的入口厚度、出口厚度和轧制力等参数。
也可以在轧制表里事先输入,换道次时按下道次按钮,再按发送即可。
2、操作手根据不同的轧制出口厚度,设定机架控制器和厚度控制器的工作方式,与轧制参数配合以得到较理想的厚差控制效果。
3、在泄油状态下,操作手通过在规定状态下对调零键的操作,最终实现系统的调零或叫靠零,以便厚调系统正常工作。
4、在轧制过程中,以棒棒图、馅饼图和动态曲线显示厚调系统的轧制速度、轧制压力、开卷张力、卷取张力、操作侧油缸位置、传动侧油缸位置、压力差和厚差等实时值。
(注意:轧机压靠前操作侧油缸位置、传动侧油缸位置显示为油缸实际移动位置。
轧机压靠后操作侧油缸位置、传动侧油缸位置显示的是辊缝值。
)5、显示系统的工作方式、系统状态和系统报警。
6、系统有两种与传动和测厚仪协调工作模式A.常用数据由厚控AGC发送到传动及测厚仪。
如人口厚度、出口厚度、轧制速度及张力等等。
传动以此为基准值,如调整需通过把手或其他方式加到此基准值上,然后返送回AGC。
厚度控制-AGC

AGC控制系统的原理数学模型及应用综述摘要:本文介绍了AGC在上生产过程中的控制原理,AGC的分类及数学模型,AGC控制系统在生产中的应用和AGC控制技术的发展过程及趋势。
关键词:AGC;控制原理;数学模型;监控1 概述AGC是Automatic Gauge Control System的简称,即所谓的轧机自动厚度控制系统。
是轧机自动化系统中不可缺少的一部分,它控制金属带材厚度精度,使金属带材厚差在限定的标准内,提高金属带材的成品率。
AGC系统的作用有两个:一是辊缝的计算,二是根据产品尺寸结合机架的形变量来调整实际的辊缝值,使之轧制的产品尺寸符合既定要求[1]。
1.1 我国厚度控制技术的发展概况目前我国已经应用的厚度控制系统,可大致分为3种基本类型[2]。
(1) 用测厚仪信号反馈控制轧机压下或轧机入口侧带钢张力的AGC(Automatic Gauge Control)系统。
上个世纪70年代,厚度控制系统大多是这类系统,而且是模拟线路。
按轧机出口侧测厚仪测出的带钢实际偏差信号反馈控制,大偏差或被轧带钢厚度大于0.4mm时,按偏差信号大小去移动压下位置,改变辊缝间距,以减小厚度偏差,即所谓粗调;在小偏差或被轧带钢厚度小于0.4mm时,则调节轧机入口侧带钢张力,进一步减小厚度偏差,即所谓精调。
我国早期的AGC系统调节压下装置的执行机构是电动的,因电动压下响应慢和非线性的缺点,逐渐被液压压下机构代替睁[3]。
(2) 采用前馈控制和测厚仪信号反馈控制轧机压下或轧机入口侧带钢张力的AGC系统。
将上述AGC系统数字化,并增加前馈控制回路就构成这类AGC系统。
前馈控制是当轧机入口侧有厚度偏差的带钢进入轧辊时,立即调节被控机架压下位置,将入口带钢厚度偏差消除的一种控制策略。
方法是将轧机入口侧测厚仪至轧辊中心的距离分成若干整数段,把经过入口侧测厚仪的每段带钢厚度顺序存入移位寄存器中,寄存器按FIFO方式工作,当寄存器输出的带钢段进入轧辊时,系统按该段厚度偏差值调整压下,以消除进入轧机的带钢厚度偏差。
厚度自动控制系统概述

厚度自动控制系统概述概述厚度自动控制系统(agc),是英国钢铁协会于20世纪40年代末50年代初发明的,该方法称之谓biraagc。
之后日本、德国、美国等发明了测厚计型agc,称之谓gmagc。
bisraagc控制模型中只有轧机参数m,没有轧件参数q,从理论上讲是不完备的。
采用传统轧制力预报模型计算,最大偏差多在20%以上,所以传统的常规的数学模型不能提供足够精确的近似值。
即使采用自适应技术,利用实测数据重新计算模型参数,但由于模型本身结构的限制,也难于适应实际生产过程。
随着钢铁产品应用领域的激增,对钢铁板拎产品的规格和质量都明确提出了更高建议,而合金钢设备的自动化掌控水平就是关键,它的性能影响产品的精度和生产率。
现代化轧机的水平主要彰显在高速、高效率、高精度等方面,厚度精度就是板材最重要的技术指标。
根据建议的板材厚度,设计最合适的掌控方案,去同时实现厚度自动控制(automaticgaugecontrol)。
目前,板厚自动控制技术(agc)已日益成熟,纵向厚差的控制精度基本得到了解决。
现代控制理论及智能控制理论与技术也被广泛地应用于轧制过程中的厚度控制。
己经取得了巨大成果和经济效益。
为了同时实现轧件的自动厚度掌控,在现代板带轧机上,通常装有液压甩下装置。
使用液压压下的自动厚度控制系统通常称作液压agc。
agc系统包含三个主要部分:1测量薄部分:主要就是检测得到的轧件实际厚度;2厚度比较和调节部分,主要是将检测得到的轧件实际厚度与给定厚度比较,得出厚差,此外,根据具体情况和要求,转换和输出辊缝调节量讯号;3辊缝调节部分:主要是根据辊缝调节讯号,通过压下装置对辊缝进行相应的调节,以减少或消除轧件的厚差基本概念1自动化:主要就是指用无人化成目标的自动化技术。
它就是在生产现场为并使生产合理化而展开的自动操作方式和自动化技术的缩写2耦合刚度:实际工程中联接件或车轴的刚度值随输出功率的变化,它就是激振频率的函数.通常在转子动力学分析中,滚动轴承的刚度值使用统计数据,其范围为1×106~1×109nm,或使用某些经验公式并作估计3压下有效系数:空载辊缝该变量与它所引起的带钢实际轧出厚度的变化量比值4弹跳方程轧件出口厚度与完整辊缝及轧机跳跃量之间的关系,5:秒流量控制:利用轧机入口和出口带材长度及带材入口厚度几个测量结果,计算出轧出的带材厚度6相对值agc:挑质软头某一实际合金钢厚度值做为目标厚度,然后在合金钢掌控过程中,已检测出来的出口辊缝值和合金钢压力的增量信号去掌控厚度,并使质软的厚度都被掌控在改为目标厚度范围之内,从而并使时程质软达至掌控同板差目的控制系统7板带材钢卷包装对冷轧生产效率和产品质量的影响冷轧薄板(包括:电工钢板、不锈钢板、彩板和镀锌板等)通常的供货状态或是按一定规格剪成的板材,或是成卷的带材(统称为板带材)原理厚度自动控制就是通过测厚仪或传感器对质软轧出厚度展开已连续的测量,并根据实测值与取值值相比较后的偏差编号,借助掌控电路和装置或计算机的功能程序,发生改变甩下边线,合金钢压力,张力,合金钢速度等,把厚度掌控在容许偏差范围内的方法。
液压AGC自动厚度控制系统介绍

一、液压AGC自动厚度控制系统简介液压AGC自动厚度控制系统是现代化轧机提高轧制精度必不可少的技术装备,是生产厂家在未来激烈市场竞争中取得优势的重要保证。
公司致力于液压AGC成套技术与装备的研发、推广。
公司建立了多学科相配套的AGC专业体系,可以集液压AGC自动厚度控制系统的设计、开发、制造、安装、调试于一体,为用户提供优质服务。
目前为止,本公司所推出的液压AGC自动厚度控制系统已经应用在国内外上百条冷轧、热轧带钢生产线上,完全可以满足带钢产品厚度的精确控制。
为了保证带钢产品的厚度精度和良好板型,本系统具有液压压下辊缝控制(AGC)、恒轧制压力控制(AFC)、测厚仪监控,对薄规格产品还可采用张力厚度控制等功能。
本系统工作可靠、操作方便、自我保护功能完备,并具有轧制工艺数据库,在轧制不同规格的带材时,只需要调出相应的轧制工艺即可在每次开始轧制以前设置轧制状态。
应用该系统后,冷轧带钢的厚控精度可以达到:0.15±0.003mm、0.3±0.006mm(纵向厚度偏差)二、系统主要控制功能1、辊缝位置闭环控制(APC);2、带钢厚度闭环控制(监控AGC、张力AGC、秒流量AGC、予控AGC);3、辊缝压靠压力设定及辊缝拨零操作;4、轧辊两侧压/抬同步控制;5、辊缝差设定与钢带纠偏控制;6、轧制力设定与报警;7、各项轧制工艺参数的采集、记录、显示和打印为轧制规程的优化提供参数。
三、主要技术性能指标1、辊缝(厚度)设定精度优于0.001mm2、带材厚度控制精度:±1.5~3%h(带钢厚度)本指标与测厚仪以及来料和轧机精度水平有关。
3、系统响应时间: 30-50 ms四、主要设备介绍1、液压泵站液压泵站主要由主液压泵、蓄能器、油箱,司服阀组,减压稳压阀组、循环过滤机构等组成。
2、压下油缸压下油缸采用优质锻造合金钢制作,经过三次无损探伤,以保证缸体的质量;结构采用特殊设计,油封采用进口产品;装有高分辨率的位移传感器以检测油缸的位移。
4 厚度自动控制——AGC

(3)实际轧出厚度随来料厚度H而变化 的规律 当来料厚度H 发生变化时,便会 使B曲线的相对位 置和斜率都发生变 化 ⇒ h,即有: H ↑ ⇒h↑
(4)实际轧出厚度随润滑条件、轧制速
度而变化的规律 ① 当减小摩擦 系数时,轧制压 力会降低,可以 使得带钢轧得更 薄,即: f↓ ⇒ h↓。
② 轧制速度对实际轧出厚度的影响, 主要是通过对摩擦系数的影响来起 作用的,当轧制速度增高时,摩擦 系数减小,则实际轧出厚度也减 小,反之则增厚。
0 F m
4. 活套补偿系统 (压下补偿系统、速
度补偿系统) (1)原因:当AGC系统移动压下而改 变辊缝进行调厚(即调压下厚控)时, 必然使压下率变化,从而影响前 滑和后滑,改变带钢出口和入口速度。 这种现象将干扰活套的工作,而活套 的动态调节又将反过来影响调厚效果 ⇒ h波动
三、P-h 图的用途 1. 分析轧机刚度对轧件厚度的影响 2. 分析各种轧制工艺条件对轧件厚度的 影响 3. 可作为对轧机辊缝预设定的工具 4. 是板带材厚度控制的基础和依据
厚控的基本思想——通过采用合 适的厚控方法,使线A与线B的交点始 终落在一条垂直线上,这条垂线称为 等厚轧制线。因此,板带厚度控制实 质就是不管轧制条件如何变化,总要 使线A与线B交到等厚轧制线上,这样 就可得到恒定厚度(高精度)的板带 材。
实现厚度自动控制的系统——AGC。 根据轧制过程中对厚度的控制方式不 同,AGC的基本形式有:反馈式、厚度 计式、前馈式、监控式、张力式、金属 秒流量式 、相对值式、绝对值式 、动态 设定式和各种补偿系统等十种。
一、反馈式厚度自动控制的基本原理 1. 控制原理 2. 数学模型
∆S 0 = (1 + M / K m )∆h
四、监控式厚度自动控制的基本原理 1. 使用意义:对于采用P-AGC、张力式、液 压式的轧机或机组,由于轧机方面的原因可 能导致误操作而进行弥补,以保证厚度精度。 2. 控制原理:用设置在出口侧的高精度X-射线 测厚仪或同位素测厚仪所测得的厚度实测值 与设定值进行比较∆hX ,按照金属秒流量相 等的原则推算出各个机架的轧出厚度偏差, 作适当的压下或张力调节,对各机架的 AGC系统进行监控修正,来提高成品带钢 的厚度。
AGC

新型轧机系统是机、电、液、气、仪一体化的大型复杂系统,其结构与功能的复杂性决定了故障机理的复杂性以及故障诊断的困难度。轧机系统高精度与高可靠性要求使故障诊断任务更加艰巨。
这一章根据作者在轧机液压系统设计分析、故障诊断与维修领域的长期实践与积累,对现代新型轧机液压故障的症状、原因,以及故障分析的过程和方法等进行总结与提炼。主要是概括轧机控制系统(AGC系统、CVC系统、弯辊系统、活套系统)的常见故障,整理故障分析的基本思路与程序、列出故障树,并总结出故障症状与原因的关系。同时,也对轧机液压控制故障与产品质量的关系进行分析。上述内容是轧机智能诊断与监测系统的主要专家知识。
4、油缸卡死,驱动电流不为零
5、电气断线,驱动电流为零
3.2 CVC液压故障与分析
3.2.1 CVC液压故障概述
CVC主要故障有:
1) 位置传感器故障。BA给定位置设定信号,CVC油缸位移不到位,主要有:单个位置传感器测量值>极限位,或控制过程中位置传感器输出信号不变,即可能位置传感器故障;同一个辊两个位置传感器位置差|E-A|>5mm,报警;上、下两辊||UP|-|DOWN||>2mm,封锁。可能故障:液压伺服系统零点漂移、油缸卡滞等。分析位移偏差量的变化趋势。
伺服阀寿命性故障 伺服阀零偏电流趋势增大,对零偏电流I趋势分析
伺服阀突发性故障 油缸位置无法控制或偏向某一端,零偏电流突然增大
溢流阀调压力过高 当伺服系统发生故障时,可能引起油缸压力过高
溢流阀调压力过低 当伺服系统发生故障时,可能引起油缸压力过低
溢流阀损坏 压力建立不起,或起不到溢流作用
机械与电气零点不一致 伺服系统驱动零偏电流增大
6) 调节器封锁:系统应符合CVC功能投入条件,如:硬件好,传感器没有故障;开关自动状态;BA硬件好(油库准备好)等。否则调节器封锁。
AGC控制
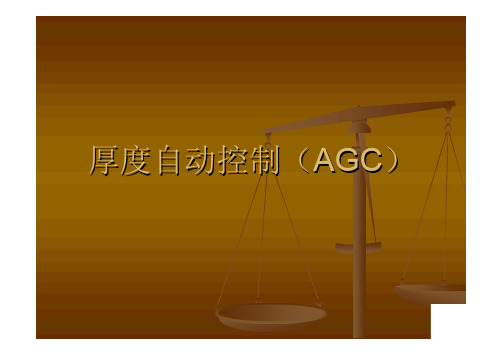
1、厚度自动控制基础
1.1P-h图的建立和运用 板带轧制过程既是轧件产生塑性变形的
过程,也是轧机产生弹性变形(即所谓弹 跳)的过程。由于轧机的弹跳,使轧出的 带材厚度h等于轧辊的理论空载S’0缝加轧机 的弹跳值。按照虎克定律,轧机弹性变形 与应力成正比,则弹跳值为P/CP
1.2冷轧带钢厚差产生的原因
位置内环、厚度外环和轧制力内环、厚度外环 的控制算法不同,将在下面分别叙述。位置内环、 厚度外环是根据厚差控制轧辊的位置到一定的目标 值;而轧制力内环、厚度外环是根据厚差控制轧制 压力到一定的目标值。
4.张力AGC
上述几种AGC均为压下AGC,但轧制薄而硬 的带材时(M很大),压下调节效率不高,这时 需采用张力AGC进行 厚度控制。
LRU2 F2 event
LRU3 F3 event
LRU4 F4 event
LRU5
F5 event
Old product
U NCOILER - STD1 INTERSTAND 1-2 INTERSTAND 2-3 INTERSTAND 3-4 INTERSTAND 4-5 STD5 - CO ILER
心的影响,为了进一步消除偏心往往在第一机架 或第一、二机架加上偏心控制。由于压下效率随 着带钢厚度减薄,硬度变硬而急剧变小,后面机 架一般不加偏心补偿。
A--幅值 ω--频率 ψ--初相角
从正弦波特性可知,只有两个幅值相等但反 相,频率相等且初相角相同的两个信号相加才能 完全互相抵消,否则:
1)频率不同的正弦信号无法相加,但由于频率与轧 辊转速有关,容易找准;
采用C方式,因为第五机架变形量很 小,轧制力也小,如果用低粗糙度的磨削 辊,就可能会产生打滑现象。所以第五机 架的工作辊应采用粗糙 高的毛化辊。C方 式可以充分满足后道机组对产品表面高粗 糙度的要求,由于第五机架作为平整机使 用,因而可在成品带钢上获得良好的板形。
- 1、下载文档前请自行甄别文档内容的完整性,平台不提供额外的编辑、内容补充、找答案等附加服务。
- 2、"仅部分预览"的文档,不可在线预览部分如存在完整性等问题,可反馈申请退款(可完整预览的文档不适用该条件!)。
- 3、如文档侵犯您的权益,请联系客服反馈,我们会尽快为您处理(人工客服工作时间:9:00-18:30)。
a-上支承辊轴承座; b-下支承辊轴承座; c-上下工作辊; d-机架; e-油压缸; f-位置传感器; g-压头; h-伺服阀; i-控制装置。
液压式厚度自动控制系统结构图
图 3-20
假设预调辊缝值为S0,轧机的刚度系数为 K,来料厚度为H0,此时轧制压力为P1,则实 际轧出厚度h1应为:
h1 S 0 P1 K
克服反馈式AGC的检测滞后; 特点 可以消除轧件及工艺方面等多种原因造成的厚差;
控制精度较低。
(5)液压式厚度自动控制系统
原理:液压AGC是按照轧机刚性可变控制的原理来实现 厚度的控制。
控制原理:液压AGC就是借助于轧机的液压 系统,通过液压伺服阀(能根据位置检测和压力检 测所发出的微弱电信号,精确地控制流入油缸的流 量)调节液压缸的油量和压力来控制轧辊的位置, 对带钢进行厚度自动控制的系统。
(2)前馈式厚度自动控制系统(前馈式AGC)
前馈式厚度自动控制
控制原理:轧机入口侧,测量出其入口厚度H,并与给 定厚度值H0相比较,当有厚度偏差ΔH时,便预先估计出 可能产生的轧出厚度偏差Δh,确定为消除此Δh值所需的 辊缝调节量ΔS ,当执行机构完成调节时,检测点正好到 达辊缝处,厚差消失。
特点
影响板带厚度变化的因素: 1、轧件温度、成分和组织性能不均匀的影响 温度↑→变形抗力↓→轧制压力↓→轧机弹跳↓→板厚度变薄↓
变形抗力 对轧出厚 度的影响
2、来料厚度不均匀的影响
来料厚度↓→压下量↓→轧制压力↓→轧机弹跳↓→板厚度变薄↓
来料厚度 对轧出厚 度的影响
3、张力变化的影响
张力↑→变形抗力↓→轧制压力↓→轧机弹跳↓→板厚度变薄↓
ΔS0 tanα=ΔH tanβ ΔS0=ΔH tanβ/ tanα ΔS0 =ΔH M/K M-轧件的塑性刚度系(M=tanβ) K-轧机的刚度系数 (K= tanα)
ΔS0与出口厚度偏差Δh的关系
Δh tanβ=tanα(ΔS0-Δh) 整理后得:Δh/ΔS0=K/(M+K) ΔS0=Δh(M+K)/ K
由p-h图看出:无论A线、B线发生变化,实际厚度都要 发生变化。
保证实际厚度不变就要进行调整。
例如:B线发生变化(变为B‘),为保持厚度不变,A线 移值A',是交点的坐标不变。
C线――等厚轧制线
板带厚度控制的实质:不管轧制条件如何变化,总要使A 线和B线交到C线上。
p-h图
二、板带厚度变化的原因和特点
张力对轧 出厚度的 影响
4、轧制速度变化的影响
通过影响摩擦系数和变形抗力来改变轧制压力。
摩擦系数↓→变形抗力↓→轧制压力↓→轧机弹跳↓→板厚度变薄↓
摩擦系数 对轧出厚 度的影响
5、对轧出厚 度的影响
三、压下调整量ΔS0 与入口出口厚度变化量的关系
A
(2)轧件的塑性曲线 根据轧制压力与压下量的关系绘制出的曲线――轧件塑性变形曲线,
用B表示。
B
(3)弹塑性曲线的建立 将轧机弹性变形曲线与轧件塑性变形曲线绘制在一个坐标
系中,称为弹塑性曲线,简称P-h图。
注 A线与 B线交点的纵坐标为轧制力 意 A线与 B线交点的横坐标为板带实际轧出厚度
2. p-h图的运用
当来料厚度因某种原因有变化时,由H0变为,其厚 度差为ΔH,因而在轧制过程中必然会引起轧制压力和 轧出厚度的变化
当压力由P1变为P2时,轧出厚度为 :
h2 S0 P2 K
当轧制压力由P1变为P2时,则其轧出厚度的厚度偏差Δh正 好等于压力差所引起的弹跳量为:
Δh=h2h1=
1
1
(P2 P1) P
(1)绝对AGC
当轧件轧出后,根据S0,P等反馈实测信号间接计算 实测厚度后,与此目标值相比较,如不同,就进行调 厚,直到δh=0为止。这种方法要求将整个带钢的厚 度都调到目标值—设定值。但如果由于空载辊缝设定 不当,轧件头部的厚度已经与设定值差得较多的情况 下,若一定要求压下系统将带钢厚度调到设定值势必 会造成压下系统负荷过大,同时亦将把带钢调成楔形 厚差。
3. 厚度自动控制系统的基本型式
(1)反馈式厚度自动控制系统(反馈式AGC)
反馈式厚度自动控制 控制原理: 测厚仪安装在轧机出口侧,测量出实际轧出
厚度,并与给定厚度值相比较,当有厚度偏差时,便计算出 所需的辊缝调节量ΔS,然后由执行机构作相应的调节,以 消除厚度偏差。
特点 滞后的调节手段; 调整的精确度高。
3.监控AGC 精轧机组厚度自动控制主要以厚度计-AGC为主,
厚度自动控制
2009.02
一、厚度自动控制的工艺基础
1.p-h图的建立
(1)轧制时的弹性曲线 轧出的带材厚度等于理论空载辊缝加弹跳值。 轧出厚度:h=S0 +P/K―――轧机的弹跳方程
S0 ――空载辊缝 P――轧制压力 K――轧机的刚度系数
根据弹跳方程绘制成的曲线(近似一条直线)――轧机弹性变形曲 线,用A 表示。09年2月MMT测试\FM1轧机刚度.xls
(2)相对AGC
不论带钢头部是否符合设定值,厚度控制系统以头 部的实际厚度为标准,即用头部的实测厚度作为目标 值。
2. 自动控制:几种方法相结合。
在精轧机各机架上采用GAUGE METER AGC来 控制轧件的波动,可以根据轧制力的实测值对本机 架进行反馈控制,还可以对后面的机架进行预控。 依靠精轧机最终机架后设置的板厚仪信号、反馈控 制板厚以消除产品厚度偏离。
K
K
为了消除此厚度偏差,可以通过调节液压缸的流量来控 制轧辊位置,补偿因来料厚度差所引起的轧机弹跳变化量, 此时液压缸所产生的轧辊位置修正量,应与此弹跳变化量 成正比,方向相反,为:
x C 1 P K
C——轧辊位置补偿系数;
四、热轧板带钢的厚度控制(精轧机控制) 1. 厚度锁定(设定)(两种方法)
超前的控制手段 用来控制入口厚度波动引起的轧出厚度波动。
(与反馈式配合使用)
(3)厚度计式厚度自动控制系统(厚度计AGC或P-AGC)
控制原理:实际的轧制压力由压头检测,辊缝S0与轧机的 弹跳值相加便得实际轧出厚度h(gaugemeter thickness)。 比较与设定厚度的偏差Δh,计算所需的辊缝调节量ΔS,调节 辊缝来消除此时的厚度偏差Δh。