轿车地毯总成技术条件
轿车地毯成型机功能及技术指标
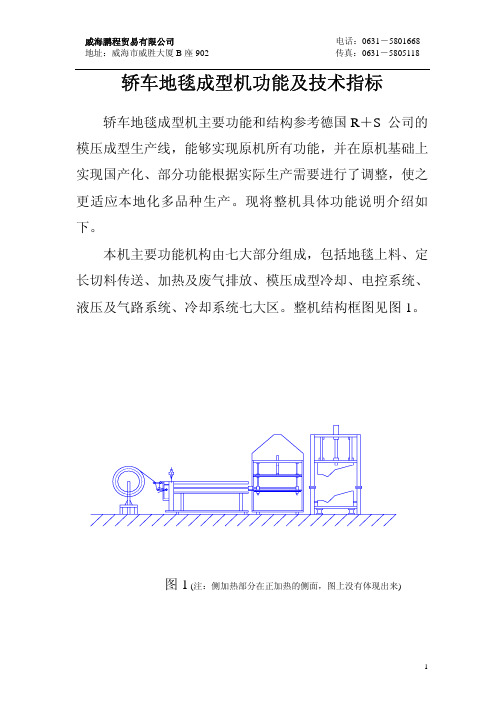
轿车地毯成型机功能及技术指标轿车地毯成型机主要功能和结构参考德国R+S 公司的模压成型生产线,能够实现原机所有功能,并在原机基础上实现国产化、部分功能根据实际生产需要进行了调整,使之更适应本地化多品种生产。
现将整机具体功能说明介绍如下。
本机主要功能机构由七大部分组成,包括地毯上料、定长切料传送、加热及废气排放、模压成型冷却、电控系统、液压及气路系统、冷却系统七大区。
整机结构框图见图1。
图1 (注:侧加热部分在正加热的侧面,图上没有体现出来)主要功能介绍:1、上料部分:该部分完成生产地毯进料切边功能。
由于地毯浸胶或复合过程中收缩不均匀,存在卷绕不齐或有多余的毛边,特设有进料调整功能,以保证地毯进料准确到位,两个边切刀自动切除多余的边料。
一卷地毯用完后,压完最后一件设备自动停机。
该部分包括料架、纠偏电机、切边电机、压料辊、传感器、支架等。
2、切料传送部分:该部分完成生产原料的定长和切断及传送。
长度由设在支架上的高灵敏光电传感器完成控制,操作人员只需根据每种产品的不同长度自行设定。
当地毯从进料辊进到指定位置,横切刀动作切断地毯,由传送带将地毯传送至预加热位置。
关键部件为气囊高温切刀、光电定位。
还包括传送带、进料电机、送料电机、支架以及配套的气动元件。
3、加热及废气排放部分:该部分正侧两套加热装置,采用PID温度控制,加热温度、时间均可以根据工艺要求自行设定,加热板根据用料幅宽可以调整。
该部分地毯传送采用直线导轨加旋转夹具方式传送。
加热板上部装有自动定时排风装置,保证车间空气清洁。
正加热采用单面加热,主要为面料加热。
侧加热采用上下双面加热,主要为辅助基材加热。
两种材料加热完毕后,辅助基材自动传送至正加热板下,与面料复合,然后送至模压成型区。
该部分由料夹、加热板、温控系统、传感器及相关液压电气系统组成。
4、模压成型部分:该部分目前采用上下模均动的工作方式,合模时间等工艺参数由工作人员自己设定。
合模开模均设有快慢速控制过程,可根据工艺要求随意调整。
轿车地毯总成技术条件
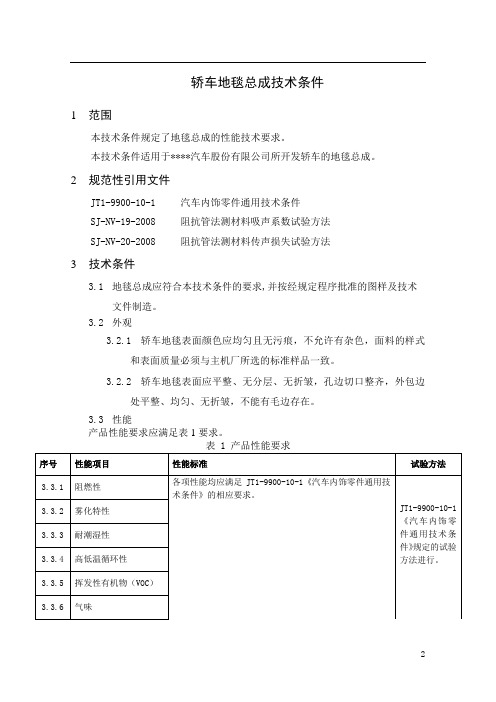
轿车地毯总成技术条件1范围本技术条件规定了地毯总成的性能技术要求。
本技术条件适用于****汽车股份有限公司所开发轿车的地毯总成。
2规范性引用文件JT1-9900-10-1 汽车内饰零件通用技术条件SJ-NV-19-2008 阻抗管法测材料吸声系数试验方法SJ-NV-20-2008 阻抗管法测材料传声损失试验方法3技术条件3.1地毯总成应符合本技术条件的要求,并按经规定程序批准的图样及技术文件制造。
3.2外观3.2.1轿车地毯表面颜色应均匀且无污痕,不允许有杂色,面料的样式和表面质量必须与主机厂所选的标准样品一致。
3.2.2轿车地毯表面应平整、无分层、无折皱,孔边切口整齐,外包边处平整、均匀、无折皱,不能有毛边存在。
3.3性能产品性能要求应满足表1要求。
4.1 压缩百分率及压缩弹性率试验方法取宽50mm、长50mm试样三块。
以1.96kPa压30s测量试样厚度t(mm)。
在不移动试样的情况下以98kPa压5min,再测该块试样的厚度t1(mm)。
然后不移动试样,卸去负载,让试样松弛5min后再在该块试样上在1.96kPa下压30s后测量该块试样的厚度t2;(mm)。
用以下公式分别计算每块试样的压缩百分率和压缩弹性率。
并用三块试样的平均值表示。
t= (t0-t1)/t×100%,t:压缩百分率;t p =(t2-t1)/(t-t1)×100%,tp:压缩弹性率;4.2耐水色牢度试验方法取宽度40mm、长度50mm试样和白布各三块。
把试样和白布放置在盛有蒸馏水烧杯里保持1h,然后把试样和白布同时取出放在70℃±2℃中干燥1h,并在室温下冷却,比较试验后的试样和白布与原试样和白布的褪色和沾色的级数。
用GB 250和GB 251评定试样褪色和白布沾色的级数。
以三块试样的平均值表示。
4.3 抗起毛性试验方法按照SAE J1530-A 进行试验H-18 砂轮, 500 g负荷,按照要求进行循环,观察外观变化。
【汽车行业类】汽车用地毯的性能要求及试验方法

(汽车行业)汽车用地毯的性能要求及试验方法前言本标准是根据全国汽车标准化技术委员会汽车行业标准制、修订计划制定的。
本标准由机械工业部提出。
本标准由全国汽车标准化技术委员会归口。
本标准由上海纺织科学研究院、上海汽车地毯总厂、长春汽车材料研究所负责起草。
本标准主要起草人:周叶芳、朱守恒、陈浩、徐巧华。
中华人民共和国汽车行业标准QC/T216壹1996汽车用地毯的性能要求及试验方法1范围本标准规定了汽车内饰用未成型的针刺地毯的技术要求及试验方法。
本标准适用于各种汽车内饰未成型的针刺地毯。
2引用标准下列标准包含的条文,通过在本标准中引用而构成为本标准的条文。
在本标准出版时,所系版本均为有效。
所有标准都会被修改,使用本标准的各方应探讨使用下列标准最新版本的可能性。
GB250壹84评定变色用灰色样卡GB251壹84评定沾色用灰色样卡GB6529壹86纺织品调湿和试验用标准大气GB8170壹87数值修约规则GB8410壹94汽车内饰材料的燃烧特性3定义本标准采用下列定义:3.1非织造布凡不是用传统织、编方法制造出来的布。
3.2针刺地毯采用梳毛机将纤维梳成网状后,且用针刺机使纤维缠成非织造布,再用塑料或橡胶等涂于背面而成的地毯。
3.3纵向卷起的方向。
3.4横向垂直于卷起的方向。
4技术要求4.1外观地毯不应有沾污,色泽不匀、裂缝、破洞、经纬条痕明显等疵点,表面要平整。
地毯不应散发出任何使人难受的气味,也不应含有任何有毒或不利于健康的物质。
4.2性能要求汽车用地毯的性能要求应符合表1的规定。
5试验总条件5.1试验室标准大气条件温度20℃±2℃,相对湿度(65±5)%。
如试验在其它条件下进行,应注明试验时大气条件。
5.2取样方法样品应从成卷的地毯中裁取。
在距纵向俩头1m的范围内取整幅和必须的长度。
5.3试样的制备方法从样品中取样,要离开幅度宽俩边各150mm。
纵向试样不应从同壹纵向延伸线裁取。
横向试样不应从同壹横向延伸线裁取。
汽车用成型地毯

试验速度100±10mm/min;
试验次数:经向、纬向各5块。
5.5.3试验步骤
5.5.3.1从5.2条准备的试验室样品中随机取经向样品5块(经向×纬向=50mm×200mm),纬向样品5块(纬向×经向=50mm×200mm)。
5.5.3.2将试样一端夹入拉力试验机夹持器中,另一端夹入下夹器,启动拉力试验试验机至试样断裂,记录断裂时的强度值(N)和伸长值(mm)。
5.5.4结果计算
按下式分别计算经向和纬向的断裂强力及断裂伸长率:
断裂强力=
各试样强力值总和
………………………..(2)
试样数
5.6湿断裂强力试验
湿断裂强力试验同断裂强力,其中试样需在水中浸渍2h后,取出并晾至不滴水再进行拉伸试验。
5.7撕破强力试验
5.7.1仪器和工具
拉力试验机0~200N,最小分度值0.04N,带自动记录装置。
1
本标准规定了奇瑞汽车有限公司车用成型地毯的性能要求、试验方法、检验规则、标识、包装及储存等。
此次修订对成型地毯的试验方法和检验规则进行了重新规定。
本企业标准由范围、规范性引用文件、术语、技术要求、试验方法、检验规则、包装储存等部分组成。
本标准由奇瑞汽车有限公司乘用车工程研究院提出。
本标准由奇瑞汽车有限公司乘用车工程研究院归口。
70℃
──
──
──
──
──
≤12
──
12
气味试验
≤4.0(C3)
≤4.0(C3)
≤4.0(C3)
≤4.0(C3)
3.5(C3)
3.5(C3)
3.0(C2C3)
5.15
序号
项目
地毯(含隔音垫)设计规范
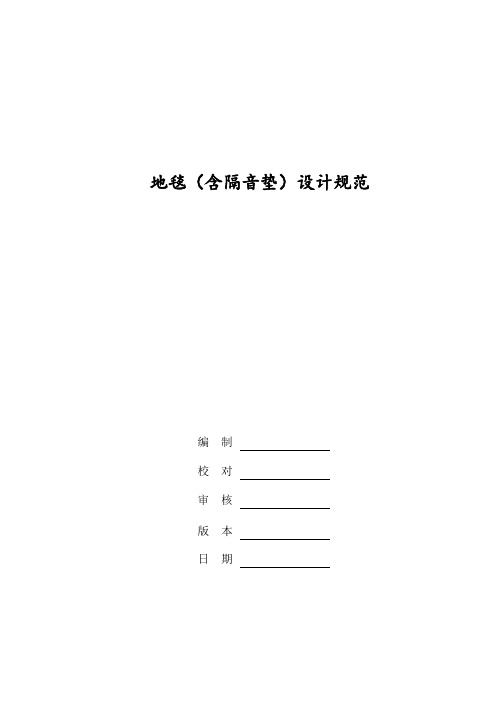
地毯(含隔音垫)设计规范编制校对审核版本日期目录1.适用范围 (1)2.满足标准 (1)2.1阻燃实验 (1)2.2成分 (1)3.流程图 (2)4.各阶段详细工作 (3)4.1概念阶段 (3)4.2设计阶段 (5)1.适用范围本规范描述了地毯设计开发规范,适用于乘用车地毯开发设计流程。
2.满足标准2.1阻燃实验1.国内标准 GB 84102.美国标准 FMVSS3023.欧盟标准 EEC95/282.2 成分欧盟标准:2000/53/EC主要检测气味、甲醛含量、有机物散发、冷凝组分等项目。
具体指标按各企业标执行。
4.各阶段详细工作4.1 概念阶段1.概述汽车地毯通常由织物及PVC等材料复合而成,铺于汽车地板或减振垫上,起装饰及隔音隔热作用,对汽车的美观及舒适性上有很大影响。
2.人机要求地毯设计应符合人机工程学原理,满足乘用舒适性要求,美观大方,材料对人体没有伤害。
3.零件材料与料厚地毯一般分为前地板地毯与行李箱地毯,部分车型有行李箱装饰板是由地毯材质制成的,驾驶员侧脚踏板与前地毯的配合关系较密切。
行李箱地毯由于需要承载行李,所以下方加有木粉板,一般厚度为5mm,为了减少振动时发出的声音,在木粉板四周粘有减震垫。
前地板地毯考虑到工艺性,一般建议采用复合方法将地毯与减震垫复合在一起,这样在装配时减少一道工序,考虑到原材料的可回收性以及成本因素,一般采用双面胶将减震垫与地毯粘在一块,也可以减震垫与地毯分开装配。
3.生产工艺地毯的成型方法为热压成型。
根据不同地毯的不同要求,将地毯整体加热到某个温度,然后整体热压成型,所以这种加工方法需要考虑以下几个问题:1)加热装置的大小。
2)热压方向。
在热压方向上不能出现负角。
3)不同材料的伸缩率不同,局部拉深也会不一样,这项需要和厂家讨论决定。
4)脱模方向一般为z向,设计脱模角度最好大于10度。
4.2设计阶段1.地毯边界1)内饰:仪表板、副仪表板、立柱下护板、座椅、安全带、脚踏板等。
汽车地毯工艺技术
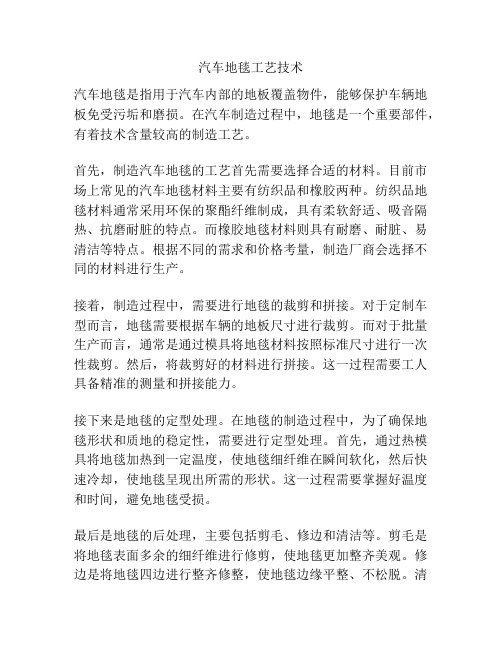
汽车地毯工艺技术汽车地毯是指用于汽车内部的地板覆盖物件,能够保护车辆地板免受污垢和磨损。
在汽车制造过程中,地毯是一个重要部件,有着技术含量较高的制造工艺。
首先,制造汽车地毯的工艺首先需要选择合适的材料。
目前市场上常见的汽车地毯材料主要有纺织品和橡胶两种。
纺织品地毯材料通常采用环保的聚酯纤维制成,具有柔软舒适、吸音隔热、抗磨耐脏的特点。
而橡胶地毯材料则具有耐磨、耐脏、易清洁等特点。
根据不同的需求和价格考量,制造厂商会选择不同的材料进行生产。
接着,制造过程中,需要进行地毯的裁剪和拼接。
对于定制车型而言,地毯需要根据车辆的地板尺寸进行裁剪。
而对于批量生产而言,通常是通过模具将地毯材料按照标准尺寸进行一次性裁剪。
然后,将裁剪好的材料进行拼接。
这一过程需要工人具备精准的测量和拼接能力。
接下来是地毯的定型处理。
在地毯的制造过程中,为了确保地毯形状和质地的稳定性,需要进行定型处理。
首先,通过热模具将地毯加热到一定温度,使地毯细纤维在瞬间软化,然后快速冷却,使地毯呈现出所需的形状。
这一过程需要掌握好温度和时间,避免地毯受损。
最后是地毯的后处理,主要包括剪毛、修边和清洁等。
剪毛是将地毯表面多余的细纤维进行修剪,使地毯更加整齐美观。
修边是将地毯四边进行整齐修整,使地毯边缘平整、不松脱。
清洁是将地毯进行清洗、烘干等处理,确保地毯干净无尘。
在整个汽车地毯的制造过程中,需要员工具备一定的技术和经验。
尤其是在裁剪、拼接和定型等环节,需要严密的操作和精细的观察,以确保地毯的质量和效果。
同时,地毯的选材、设计和款式也是考量的因素,需要根据市场需求和车辆的特点进行合理选择。
总之,汽车地毯的制造工艺涉及材料选择、裁剪拼接、定型处理和后处理等多个环节。
这些工艺技术的良好运用,可以为汽车地毯的质量和效果提供保证,满足消费者对于舒适、美观和耐用性的需求。
汽车地毯行业将继续推动技术创新和提升,不断适应市场的需求和变化。
cab 1011-2012《汽车地毯的技术要求》

cab 1011-2012《汽车地毯的技术要求》
《汽车地毯的技术要求》是一份关于汽车地毯制造和使用的标准文件。
这份文件主要规定了汽车地毯的各种技术参数和性能要求,以确保汽车地毯的质量和安全性。
1. 材料:汽车地毯通常由尼龙、聚酯或其他合成纤维制成,这些材料具有良好的耐磨性、耐脏性和防火性。
2. 尺寸:汽车地毯的尺寸需要精确到毫米,以确保与汽车地板的完美匹配。
3. 颜色:汽车地毯的颜色应均匀一致,无明显色差。
同时,为了易于清洁和维护,一般选择深色或中性色。
4. 表面处理:汽车地毯的表面应平整,无破损、污渍和异味。
同时,为了提高防滑性,地毯表面通常会进行特殊处理。
5. 耐磨性:汽车地毯需要具有良好的耐磨性,以抵抗日常使用中的磨损。
6. 耐脏性:汽车地毯需要具有良好的耐脏性,以便在车辆使用过程中能够保持清洁。
7. 防火性:汽车地毯需要具有良好的防火性,以防止火灾的发生。
8. 环保性:汽车地毯在生产和使用过程中,需要符合环保标准,不产生有害物质。
乘用车内饰设计规范参考-经验整理

地毯设计规范参考1.1 地毯总成与A/B/C柱下护板及前/后门槛装饰板之间的搭接量一般在10mm以上,过盈量一般在(0~2.0)mm之间(因地毯材料不同而有所不同)1.2 地毯总成与副仪表板之间的搭接量一般在10mm以上,过盈量一般在(0~2.0)mm之间(因地毯材料不同而有所不同)1.3 地毯与加速踏板间隙一般在(40~60)mm1.4 地毯垫脚板与水平面成角度一般在40°~60°1.5 踏板周边与地毯间距---奥迪参考如下顶棚设计规范参考2.1 顶棚与A/B/C柱上护板之间的搭接量一般为8~10mm2.2 顶棚总成与遮阳板之间的间隙:A一般为5mm,B根据人机工程需要,手部操作位置一般为10mm左右,其他位置根据造型需要确定2.3 顶棚与前后风窗间隙最小为3mm2.4 顶棚与天窗的搭接方式有两种:天窗框固定方式、T型环固定方式2.5 顶棚与门洞密封条及顶棚拉手搭接方式3.1 顶棚拉手固定座与顶棚之间的搭接量A≥4mm3.2 顶棚拉手固定座与顶棚上安装孔配合间隙:在满足3.1要求的前提下,为保证顶棚拉手装配方便性,一般情况下间隙B=1mm(建议值,可根据顶棚上顶棚拉手安装孔成型工艺及顶棚拉手上定位销的位置进行调整)3.3 折叠式顶棚拉手本体与顶棚的位置关系:一般情况下间隙C≥5mm(建议值,可根据顶棚拉手与顶棚配合处造型风格进行调整),间隙D=0mm(顶棚拉手处于自然状态时与顶棚表面贴合即可)3.4 顶棚拉手手握区域范围:一般情况下尺寸E≥40mm,尺寸F≥80mm(下图阴隐部分为顶棚拉手手握区域)4.1 化妆镜灯开启点位参考4.2 遮阳板轴拔出力参考4.3 遮阳板折叠/侧翻力矩参考侧围护板设计规范参考5.1 A柱上护板与前风窗玻璃之间的间隙一般为3mm5.2 A柱上护板表面与前风窗黑带之间的间隙一般最小为5mm5.3 A柱上护板与仪表板之间的间隙一般为1mm;如果仪表板或A柱上护板为软化件时,此间隙一般为0mm5.4 B柱上护板与安全带总成沿X向的间隙最小2.5mm,一般≥3mm5.5 B柱上护板与安全带总成最高或最低的间隙一般≥5mm5.6 B柱下护板与门护板之间的间隙一般最小为7mm5.7 C柱上护板与后风窗玻璃之间的间隙一般为3mm;C柱上护板表面与后风窗玻璃黑带之间的间隙最小为5mm5.8 C柱上护板表面与包裹架护板本体之间的间隙一般为0.5mm或1mm;如果C柱上护板为软化件时,此间隙一般为0mm5.9 A/B/C柱上护板与顶棚的搭接量一般最小为10mm5.10 门槛装饰板与门护板总成之间的间隙一般≥7mm门护板设计规范参考6.1 门护板总成与高音扬声器格栅之间的间隙一般为2mm6.2 门护板总成与仪表板之间的间隙一般为6~8mm6.3 门护板总成与门槛装饰板、B/C柱下护板的间隙最小为7mm6.4 门护板总成与座椅操作手柄的间隙最小为35mm6.5 门护板总成与开关的间隙一般为1mm6.6 门护板总成与内开手柄的间隙一般为1.5mm6.7 门护板杂物斗内物品取放性检查:要求杂物斗内物品在取放时空间足够6.8 门护板与烟灰盒的间隙一般为1.5mm6.9 门护板总成与杂物箱开启时的间隙最小为10mm副仪表板设计规范参考7.1 副仪表板总成与驻车制动操纵机构之间的间隙一般为3mm~4mm7.2 副仪表板总成与换挡机构之间的间隙一般最小为5mm7.3 副仪表板总成与座椅滑轨之间的间隙一般最小为10mm(注:一般情况下,座椅调整到最前位置时,可接受坐垫与副仪表板总成轻微的干涉)7.4 副仪表板总成与踏板总成之间的间隙一般最小为30mm7.5 副仪表板总成与地毯之间的过盈量一般为1mm~2mm7.6 副仪表板总成杯架大小:一般底部直径最小为65mm7.7 扶手设计要点:1)扶手Z向高度应在座椅R点以上140mm到170mm,与门护板上扶手高度差不应过大;2)扶手长度一般应在260mm以上,最低可接受的长度为210mm,扶手前端与换挡器最后的距离应该在100mm以上3)扶手的开启角度,一般应使扶手重心的旋转角度超过90°,即扶手可以通过自重实现开启后不自动关闭。
- 1、下载文档前请自行甄别文档内容的完整性,平台不提供额外的编辑、内容补充、找答案等附加服务。
- 2、"仅部分预览"的文档,不可在线预览部分如存在完整性等问题,可反馈申请退款(可完整预览的文档不适用该条件!)。
- 3、如文档侵犯您的权益,请联系客服反馈,我们会尽快为您处理(人工客服工作时间:9:00-18:30)。
轿车地毯总成技术条件
1范围
本技术条件规定了地毯总成的性能技术要求。
本技术条件适用于****汽车股份有限公司所开发轿车的地毯总成。
2规范性引用文件
JT1-9900-10-1 汽车内饰零件通用技术条件
SJ-NV-19-2008 阻抗管法测材料吸声系数试验方法
SJ-NV-20-2008 阻抗管法测材料传声损失试验方法
3技术条件
3.1地毯总成应符合本技术条件的要求,并按经规定程序批准的图样及技术
文件制造。
3.2外观
3.2.1轿车地毯表面颜色应均匀且无污痕,不允许有杂色,面料的样式
和表面质量必须与主机厂所选的标准样品一致。
3.2.2轿车地毯表面应平整、无分层、无折皱,孔边切口整齐,外包边
处平整、均匀、无折皱,不能有毛边存在。
3.3性能
产品性能要求应满足表1要求。
4.1 压缩百分率及压缩弹性率试验方法
取宽50mm、长50mm试样三块。
以1.96kPa压30s测量试样厚度t
(mm)。
在不移动试样的情况下以98kPa压5min,再测该块试样的厚度t1(mm)。
然后不移动试样,卸去负载,让试样松弛5min后再在该块试样上在1.96kPa下压30s后测量该块试样的厚度t2;(mm)。
用以下公式分别计算每块试样的压缩百分率和压缩弹性率。
并用三块试样的平均值表示。
t= (t
0-t
1
)/t
×100%,t:压缩百分率;
t p =(t
2
-t
1
)/(t
-t
1
)×100%,t
p
:压缩弹性率;
4.2耐水色牢度试验方法
取宽度40mm、长度50mm试样和白布各三块。
把试样和白布放置在盛有蒸馏水烧杯里保持1h,然后把试样和白布同时取出放在70℃±2℃中干燥1h,并在室
温下冷却,比较试验后的试样和白布与原试样和白布的褪色和沾色的级数。
用GB 250和GB 251评定试样褪色和白布沾色的级数。
以三块试样的平均值表示。
4.3 抗起毛性试验方法
按照SAE J1530-A 进行试验H-18 砂轮, 500 g负荷,按照要求进行循环,观察外观变化。
4.4 摩擦失重性试验方法
按照SAE J1530-B, 方法A, 进行试验H-18 砂轮,1000 g 负荷, 按照要求进行循环,测量。
4.5 耐磨损性试验方法
按照SAE J1530-A 进行试验,用1000g负荷,H18砂轮,按照要求进行循环,观察外观变化。
4.6、吸声性能试验方法
吸声性能试验方法按照**技术规范SJ-NV-19-2008《阻抗管法测材料吸声系数试验方法》执行。
4.7、隔声性能试验方法
隔声性能试验方法按照**技术规范SJ-NV-20-2008《阻抗管法测材料传声损失试验方法》执行。
5检验规则
5.1基本要求
产品须经制造厂质量检验部门检验合格,并附有检验合格证后方能出厂。
5.2出厂检验
出厂检验必须检验第3.2条的内容。
5.3型式检验
5.3.1有下列情况之一时,应进行型式检验
a) 新产品定型或老产品转厂生产的试制定型鉴定时;
b) 正式生产后,如结构、材料、工艺有较大改变,有可能影响产品性能时;
c) 正常生产时,每2年不少于一次;;
d) 停产一年以上,恢复生产时;
e) 出厂检验结果与上次型式检验有较大差异时;
f) 国家质量监督机构提出进行型式检验的要求时。
5.3.2型式检验项目是第3章的全部内容。
5.3.3型式检验的抽样是从出厂检验合格的产品中随机抽取(必须根据
实际情况规定抽样数量)。
检验项目中,如燃烧特性不合格,不允许
复查,判该次型式检验不合格。
其他型式检验项目中如有一项不合格,
允许加倍抽取对该不合格项进行复验,如仍不合格,则该产品不合格。
6标识、包装、运输及储存
6.1标识
6.1.1产品标识:
a)需标识的零部件,统一确定为01状态的零部件。
b)产品上需要有**注册商标(“*****”)+供应商(生产厂家)代码(标识中商标与供应商代码的排列为并排结构或上下结构)、材料、生产日期标
识,有环保和3C要求的零件还应有相应的环保和3C标识,左右对称的产
品应有“L、R”标识。
c)标识的字体为宋体,字号的大小应视零部件的大小确定。
6.1.2包装箱标识:
a)制造厂名称、地址及厂标;
b) 产品名称及型号;
c) 产品数量及总质量;
d) "防火"、"防潮"、"勿重压"等字样及符号;
e) 包装箱外形尺寸(长X宽X高);
f) 出厂年、月、日、批号。
6.2包装
6.2.1产品应经制造厂质检部门检验合格后方可包装。
6.2.2外包装箱应保证在正常运输中不被损坏,产品应用防潮材料包装后再放
入包装箱中。
6.2.3箱内零件应放置可靠。
6.2.4每箱产品应附有合格证。
6.3 运输和贮存
6.3.1输过程中应防火、防潮、防重压。
6.3.2产品应放在通风干燥且无有害气体的仓库内,且不得与化学药品、酸碱等腐蚀性物质一同存放。
7质量保证
产品随整车从经销部门销售之日起,在正常使用条件下使用时间不满一年,且行驶里程不超过25000 km时,如确因制造质量不良而造成损坏,制造厂应免费维修或更换。
附件1:参照样本
5级4级3级2级1级
5级
4级3级2级1级
5级
4级3级2级
1级
5级
4级3级
2级
1级。