塑料成型工艺
几种常用塑料的成型工艺
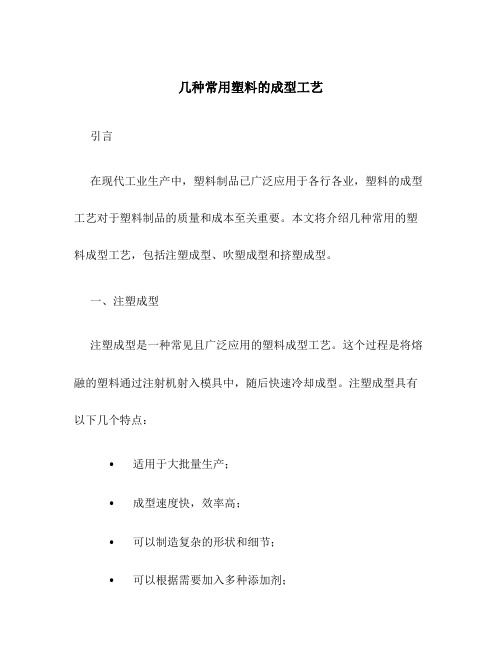
几种常用塑料的成型工艺引言在现代工业生产中,塑料制品已广泛应用于各行各业,塑料的成型工艺对于塑料制品的质量和成本至关重要。
本文将介绍几种常用的塑料成型工艺,包括注塑成型、吹塑成型和挤塑成型。
一、注塑成型注塑成型是一种常见且广泛应用的塑料成型工艺。
这个过程是将熔融的塑料通过注射机射入模具中,随后快速冷却成型。
注塑成型具有以下几个特点:•适用于大批量生产;•成型速度快,效率高;•可以制造复杂的形状和细节;•可以根据需要加入多种添加剂;•成本相对较低。
注塑成型主要有以下几个步骤:1.塑料原料进料:将塑料颗粒通过注塑机的料斗输送到加热筒中,进行熔融。
2.制作模具:根据产品的形状和尺寸,制作适当的模具。
3.射入模具:将熔融的塑料注入模具中。
4.冷却成型:通过冷却系统,使塑料迅速冷却成型。
5.取出成品:将成品从模具中取出。
注塑成型应用广泛,常见的产品包括塑料杯、塑料盒、零部件等。
二、吹塑成型吹塑成型是一种常用的塑料成型工艺,适用于制造中空物体,如瓶子、容器、玩具等。
吹塑成型具有以下几个特点:•适用于大中批量生产;•可以制造中空物体;•成型速度较快;•成本相对较低。
吹塑成型主要有以下几个步骤:1.塑料颗粒预热:将塑料颗粒通过加热系统进行预热,使其变软且易于塑性变形。
2.吹塑成型:将预热的塑料颗粒放入吹塑机中,通过高压气体将其吹塑成模具中的形状。
3.冷却固化:通过冷却系统,使塑料迅速冷却固化。
4.修整:将成品从模具中取出,并进行修整、修剪等处理。
吹塑成型广泛应用于食品包装、化妆品容器等领域。
三、挤塑成型挤塑成型是一种将熔融的塑料挤出成型的工艺,适用于制造具有恒定截面形状的长条状成品,如管道、线缆等。
挤塑成型具有以下几个特点:•适用于大批量生产;•可以制造长条状成品;•成型速度较快;•成本相对较低。
挤塑成型主要有以下几个步骤:1.塑料预处理:将塑料颗粒或粉末进行预处理,使其达到适合挤塑的熔融状态。
2.加热熔融:将预处理的塑料通过加热系统加热熔融。
塑胶成型工艺大全
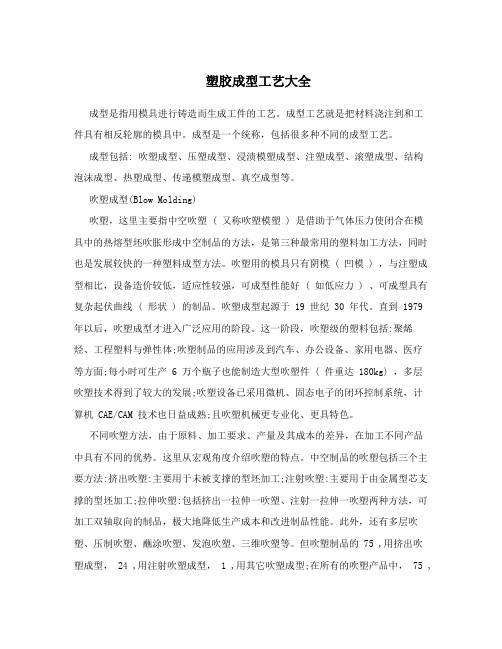
塑胶成型工艺大全成型是指用模具进行铸造而生成工件的工艺。
成型工艺就是把材料浇注到和工件具有相反轮廓的模具中。
成型是一个统称,包括很多种不同的成型工艺。
成型包括: 吹塑成型、压塑成型、浸渍模塑成型、注塑成型、滚塑成型、结构泡沫成型、热塑成型、传递模塑成型、真空成型等。
吹塑成型(Blow Molding)吹塑,这里主要指中空吹塑 ( 又称吹塑模塑 ) 是借助于气体压力使闭合在模具中的热熔型坯吹胀形成中空制品的方法,是第三种最常用的塑料加工方法,同时也是发展较快的一种塑料成型方法。
吹塑用的模具只有阴模 ( 凹模 ) ,与注塑成型相比,设备造价较低,适应性较强,可成型性能好 ( 如低应力 ) 、可成型具有复杂起伏曲线 ( 形状 ) 的制品。
吹塑成型起源于 19 世纪 30 年代。
直到 1979 年以后,吹塑成型才进入广泛应用的阶段。
这一阶段,吹塑级的塑料包括:聚烯烃、工程塑料与弹性体;吹塑制品的应用涉及到汽车、办公设备、家用电器、医疗等方面;每小时可生产 6 万个瓶子也能制造大型吹塑件 ( 件重达 180kg) ,多层吹塑技术得到了较大的发展;吹塑设备已采用微机、固态电子的闭环控制系统,计算机 CAE/CAM 技术也日益成熟;且吹塑机械更专业化、更具特色。
不同吹塑方法,由于原料、加工要求、产量及其成本的差异,在加工不同产品中具有不同的优势。
这里从宏观角度介绍吹塑的特点。
中空制品的吹塑包括三个主要方法:挤出吹塑:主要用于未被支撑的型坯加工;注射吹塑:主要用于由金属型芯支撑的型坯加工;拉伸吹塑:包括挤出一拉伸一吹塑、注射一拉伸一吹塑两种方法,可加工双轴取向的制品,极大地降低生产成本和改进制品性能。
此外,还有多层吹塑、压制吹塑、蘸涂吹塑、发泡吹塑、三维吹塑等。
但吹塑制品的 75 ,用挤出吹塑成型, 24 ,用注射吹塑成型, 1 ,用其它吹塑成型;在所有的吹塑产品中, 75 ,属于双向拉伸产品。
挤出吹塑的优点是生产效率高,设备成本低,模具和机械的选择范围广,缺点是废品率较高,废料的回收、利用差,制品的厚度控制、原料的分散性受限制,成型后必须进行修边操作。
塑胶成型工艺流程

塑胶成型工艺流程塑胶成型是一种常见的制造工艺,用于生产各种塑料制品,如塑料容器、零件、玩具等。
塑胶成型工艺流程通常包括原料准备、塑胶成型、冷却、脱模和后处理等步骤。
本文将详细介绍塑胶成型工艺的流程及各个步骤的具体操作。
1. 原料准备。
塑胶成型的第一步是原料准备。
塑胶原料通常以颗粒或粉末的形式存在,需要根据产品的要求选择合适的塑料原料。
在原料准备阶段,操作人员需要将塑料原料加入到注塑机的料斗中,并根据产品的要求设置好注塑机的参数,如温度、压力等。
2. 塑胶成型。
一旦原料准备就绪,接下来就是塑胶成型的阶段。
在注塑机中,塑料原料会被加热融化,然后通过射出系统注入到模具中。
模具通常由两个部分组成,分别是上模和下模。
当塑料原料进入模具后,会根据模具的形状和尺寸进行冷却,最终形成所需的产品。
3. 冷却。
在塑胶成型过程中,冷却是一个非常重要的步骤。
冷却的速度和方式会直接影响产品的质量和性能。
通常情况下,模具中的冷却系统会通过水或其他介质来降低模具的温度,以便快速固化塑料原料,确保产品的尺寸和形状稳定。
4. 脱模。
当产品完成冷却后,就需要进行脱模操作。
脱模是指将成型好的产品从模具中取出的过程。
通常情况下,脱模操作需要小心谨慎,以避免产品的损坏。
有些复杂的产品可能需要采用特殊的脱模工艺,如气动脱模、液压脱模等。
5. 后处理。
最后,成型好的产品通常还需要进行一些后处理工艺,如修边、去毛刺、喷漆等。
这些后处理工艺可以提高产品的外观和性能,使其更加符合市场需求。
总结。
塑胶成型工艺流程包括原料准备、塑胶成型、冷却、脱模和后处理等步骤。
每个步骤都需要严格控制和操作,以确保产品的质量和性能。
随着科技的不断进步,塑胶成型工艺也在不断创新和改进,为各行各业提供更高质量的塑料制品。
希望本文能够对塑胶成型工艺有所了解,并能够对相关行业的从业人员提供一定的参考和帮助。
塑料成型工艺流程
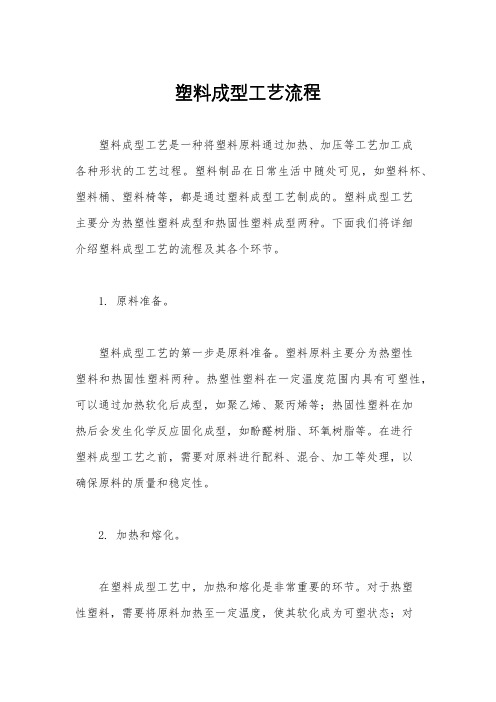
塑料成型工艺流程塑料成型工艺是一种将塑料原料通过加热、加压等工艺加工成各种形状的工艺过程。
塑料制品在日常生活中随处可见,如塑料杯、塑料桶、塑料椅等,都是通过塑料成型工艺制成的。
塑料成型工艺主要分为热塑性塑料成型和热固性塑料成型两种。
下面我们将详细介绍塑料成型工艺的流程及其各个环节。
1. 原料准备。
塑料成型工艺的第一步是原料准备。
塑料原料主要分为热塑性塑料和热固性塑料两种。
热塑性塑料在一定温度范围内具有可塑性,可以通过加热软化后成型,如聚乙烯、聚丙烯等;热固性塑料在加热后会发生化学反应固化成型,如酚醛树脂、环氧树脂等。
在进行塑料成型工艺之前,需要对原料进行配料、混合、加工等处理,以确保原料的质量和稳定性。
2. 加热和熔化。
在塑料成型工艺中,加热和熔化是非常重要的环节。
对于热塑性塑料,需要将原料加热至一定温度,使其软化成为可塑状态;对于热固性塑料,需要将原料加热至一定温度,使其发生化学反应固化成型。
在加热和熔化的过程中,需要控制加热温度、加热时间等参数,以确保原料能够达到适合成型的状态。
3. 成型。
成型是塑料成型工艺的核心环节。
在成型过程中,需要将熔化后的塑料原料注入模具中,并施加一定的压力,使其充分填充模具腔体,并形成所需的产品形状。
成型过程中需要控制注塑压力、注塑速度、注塑时间等参数,以确保成型品质量和生产效率。
4. 冷却。
在成型完成后,需要对产品进行冷却。
冷却过程中,需要控制冷却时间、冷却速度等参数,以确保产品能够充分冷却固化,并保持所需的形状和尺寸稳定。
5. 脱模。
脱模是将成型后的产品从模具中取出的过程。
在脱模过程中,需要注意产品与模具之间的脱模性能,以确保产品能够顺利脱模并保持完整的形状和表面质量。
6. 加工和表面处理。
在脱模后,还需要对产品进行加工和表面处理。
加工包括修整、打磨、去毛刺等工艺,以确保产品的尺寸和表面质量达到要求;表面处理包括喷漆、印刷、镀铬等工艺,以美化产品外观并提高产品的耐磨性和耐腐蚀性。
塑料的成型工艺
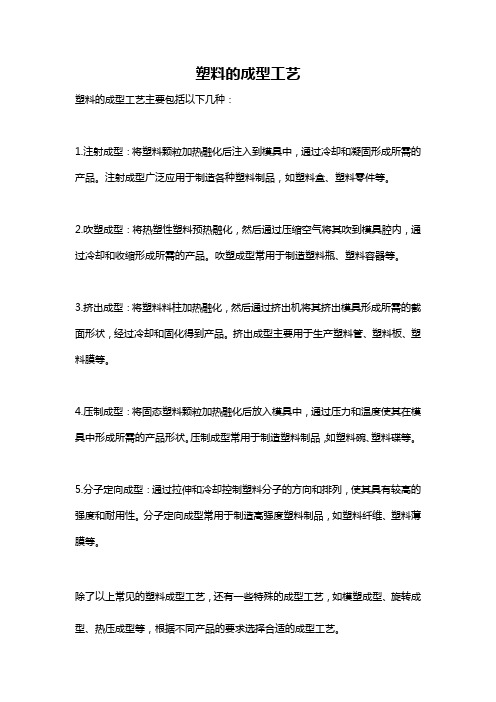
塑料的成型工艺
塑料的成型工艺主要包括以下几种:
1.注射成型:将塑料颗粒加热融化后注入到模具中,通过冷却和凝固形成所需的产品。
注射成型广泛应用于制造各种塑料制品,如塑料盒、塑料零件等。
2.吹塑成型:将热塑性塑料预热融化,然后通过压缩空气将其吹到模具腔内,通过冷却和收缩形成所需的产品。
吹塑成型常用于制造塑料瓶、塑料容器等。
3.挤出成型:将塑料料柱加热融化,然后通过挤出机将其挤出模具形成所需的截面形状,经过冷却和固化得到产品。
挤出成型主要用于生产塑料管、塑料板、塑料膜等。
4.压制成型:将固态塑料颗粒加热融化后放入模具中,通过压力和温度使其在模具中形成所需的产品形状。
压制成型常用于制造塑料制品,如塑料碗、塑料碟等。
5.分子定向成型:通过拉伸和冷却控制塑料分子的方向和排列,使其具有较高的强度和耐用性。
分子定向成型常用于制造高强度塑料制品,如塑料纤维、塑料薄膜等。
除了以上常见的塑料成型工艺,还有一些特殊的成型工艺,如模塑成型、旋转成型、热压成型等,根据不同产品的要求选择合适的成型工艺。
塑料成型工艺
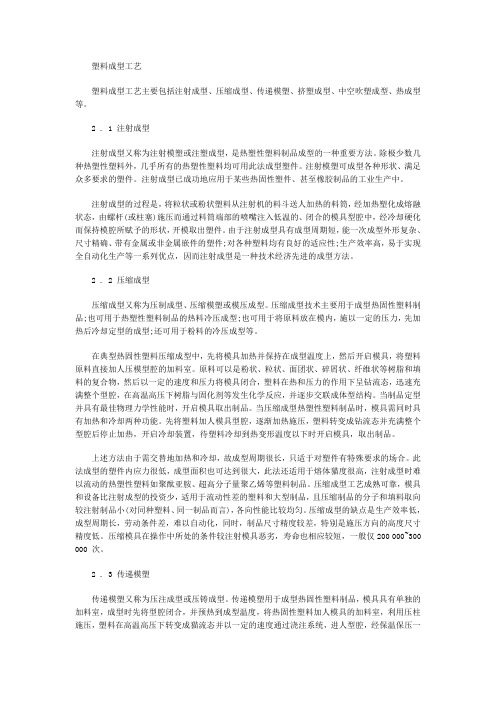
塑料成型工艺塑料成型工艺主要包括注射成型、压缩成型、传递模塑、挤塑成型、中空吹塑成型、热成型等。
2 . 1 注射成型注射成型又称为注射模塑或注塑成型,是热塑性塑料制品成型的一种重要方法。
除极少数几种热塑性塑料外,几乎所有的热塑性塑料均可用此法成型塑件。
注射模塑可成型各种形状、满足众多要求的塑件。
注射成型已成功地应用于某些热固性塑件、甚至橡胶制品的工业生产中。
注射成型的过程是,将粒状或粉状塑料从注射机的料斗送人加热的料筒,经加热塑化成熔融状态,由螺杆(或柱塞)施压而通过料筒端部的喷嘴注入低温的、闭合的模具型腔中,经冷却硬化而保持模腔所赋予的形状,开模取出塑件。
由于注射成型具有成型周期短,能一次成型外形复杂、尺寸精确、带有金属或非金属嵌件的塑件;对各种塑料均有良好的适应性;生产效率高,易于实现全自动化生产等一系列优点,因而注射成型是一种技术经济先进的成型方法。
2 . 2 压缩成型压缩成型又称为压制成型、压缩模塑或模压成型。
压缩成型技术主要用于成型热固性塑料制品;也可用于热塑性塑料制品的热料冷压成型;也可用于将原料放在模内,施以一定的压力,先加热后冷却定型的成型;还可用于粉料的冷压成型等。
在典型热固性塑料压缩成型中,先将模具加热并保持在成型温度上,然后开启模具,将塑料原料直接加人压模型腔的加料室。
原料可以是粉状、粒状、面团状、碎屑状、纤维状等树脂和填料的复合物,然后以一定的速度和压力将模具闭合,塑料在热和压力的作用下呈钻流态,迅速充满整个型腔,在高温高压下树脂与固化剂等发生化学反应,并逐步交联成体型结构。
当制品定型并具有最佳物理力学性能时,开启模具取出制品。
当压缩成型热塑性塑料制品时,模具需同时具有加热和冷却两种功能。
先将塑料加人模具型腔,逐渐加热施压,塑料转变成钻流态并充满整个型腔后停止加热,开启冷却装置,待塑料冷却到热变形温度以下时开启模具,取出制品。
上述方法由于需交替地加热和冷却,故成型周期很长,只适于对塑件有特殊要求的场合。
常用的十大塑料成型工艺(优缺点介绍)
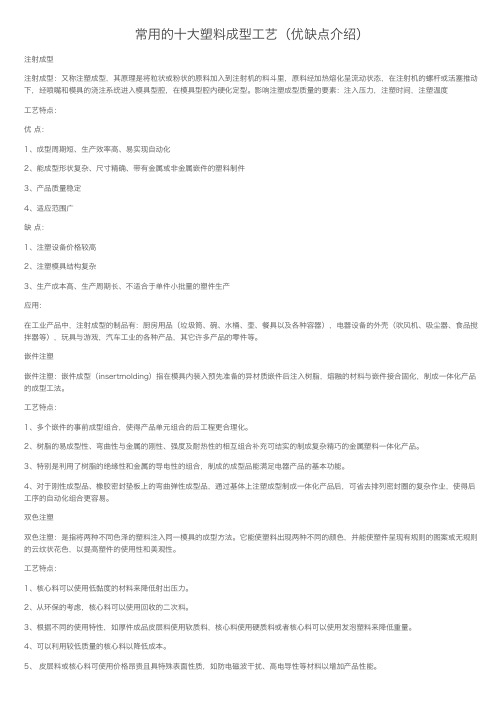
常⽤的⼗⼤塑料成型⼯艺(优缺点介绍)注射成型注射成型:⼜称注塑成型,其原理是将粒状或粉状的原料加⼊到注射机的料⽃⾥,原料经加热熔化呈流动状态,在注射机的螺杆或活塞推动下,经喷嘴和模具的浇注系统进⼊模具型腔,在模具型腔内硬化定型。
影响注塑成型质量的要素:注⼊压⼒,注塑时间,注塑温度⼯艺特点:优 点:1、成型周期短、⽣产效率⾼、易实现⾃动化2、能成型形状复杂、尺⼨精确、带有⾦属或⾮⾦属嵌件的塑料制件3、产品质量稳定4、适应范围⼴缺 点:1、注塑设备价格较⾼2、注塑模具结构复杂3、⽣产成本⾼、⽣产周期长、不适合于单件⼩批量的塑件⽣产应⽤:在⼯业产品中,注射成型的制品有:厨房⽤品(垃圾筒、碗、⽔桶、壶、餐具以及各种容器),电器设备的外壳(吹风机、吸尘器、⾷品搅拌器等),玩具与游戏,汽车⼯业的各种产品,其它许多产品的零件等。
嵌件注塑嵌件注塑:嵌件成型(insertmolding)指在模具内装⼊预先准备的异材质嵌件后注⼊树脂,熔融的材料与嵌件接合固化,制成⼀体化产品的成型⼯法。
⼯艺特点:1、多个嵌件的事前成型组合,使得产品单元组合的后⼯程更合理化。
2、树脂的易成型性、弯曲性与⾦属的刚性、强度及耐热性的相互组合补充可结实的制成复杂精巧的⾦属塑料⼀体化产品。
3、特别是利⽤了树脂的绝缘性和⾦属的导电性的组合,制成的成型品能满⾜电器产品的基本功能。
4、对于刚性成型品、橡胶密封垫板上的弯曲弹性成型品,通过基体上注塑成型制成⼀体化产品后,可省去排列密封圈的复杂作业,使得后⼯序的⾃动化组合更容易。
双⾊注塑双⾊注塑:是指将两种不同⾊泽的塑料注⼊同⼀模具的成型⽅法。
它能使塑料出现两种不同的颜⾊,并能使塑件呈现有规则的图案或⽆规则的云纹状花⾊,以提⾼塑件的使⽤性和美观性。
⼯艺特点:1、核⼼料可以使⽤低黏度的材料来降低射出压⼒。
2、从环保的考虑,核⼼料可以使⽤回收的⼆次料。
3、根据不同的使⽤特性,如厚件成品⽪层料使⽤软质料,核⼼料使⽤硬质料或者核⼼料可以使⽤发泡塑料来降低重量。
塑料成型工艺
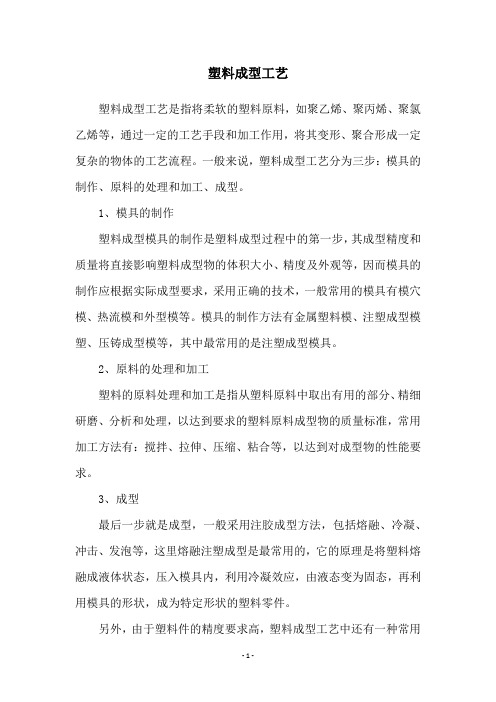
塑料成型工艺
塑料成型工艺是指将柔软的塑料原料,如聚乙烯、聚丙烯、聚氯乙烯等,通过一定的工艺手段和加工作用,将其变形、聚合形成一定复杂的物体的工艺流程。
一般来说,塑料成型工艺分为三步:模具的制作、原料的处理和加工、成型。
1、模具的制作
塑料成型模具的制作是塑料成型过程中的第一步,其成型精度和质量将直接影响塑料成型物的体积大小、精度及外观等,因而模具的制作应根据实际成型要求,采用正确的技术,一般常用的模具有模穴模、热流模和外型模等。
模具的制作方法有金属塑料模、注塑成型模塑、压铸成型模等,其中最常用的是注塑成型模具。
2、原料的处理和加工
塑料的原料处理和加工是指从塑料原料中取出有用的部分、精细研磨、分析和处理,以达到要求的塑料原料成型物的质量标准,常用加工方法有:搅拌、拉伸、压缩、粘合等,以达到对成型物的性能要求。
3、成型
最后一步就是成型,一般采用注胶成型方法,包括熔融、冷凝、冲击、发泡等,这里熔融注塑成型是最常用的,它的原理是将塑料熔融成液体状态,压入模具内,利用冷凝效应,由液态变为固态,再利用模具的形状,成为特定形状的塑料零件。
另外,由于塑料件的精度要求高,塑料成型工艺中还有一种常用
的加工方法,叫做机械加工,机械加工可以有效地提高塑料件的精度,以适应高精度的零部件制造。
总之,塑料成型工艺是一个复杂的流程,还需要考虑到其他材料的合成性能、工艺要求、工艺可行性以及部件的精度要求等,以保证产品的质量和可靠性。
- 1、下载文档前请自行甄别文档内容的完整性,平台不提供额外的编辑、内容补充、找答案等附加服务。
- 2、"仅部分预览"的文档,不可在线预览部分如存在完整性等问题,可反馈申请退款(可完整预览的文档不适用该条件!)。
- 3、如文档侵犯您的权益,请联系客服反馈,我们会尽快为您处理(人工客服工作时间:9:00-18:30)。
模压时间太长:生产效率↓;长时间高温将使树脂降解。
模压时间太短:硬化不足,外观无光,性能↓。 一般,PF、UF的模压时间为:1min / 1mm制品厚度。
第一章 模压成型工艺
第一章 模压成型工艺
第二章 注射成型工艺
配料 干燥 塑化 锁模 注塑 开模 保压 冷却 预塑
顶出取零件
模塑料 注塑机 注塑模
热固性压塑料在模腔内变化情况: 压塑料 → 软化、熔融 → 流动 → 充模 → 固化 → 制品
可溶
加料闭模 物理变化
模压 放气 保压 化学变化
不熔
第一章 模压成型工艺
实线:无支承面模具 虚线:有支承面模具
热固性塑料模压成型时的压力-温度-体积关系
第一章 模压成型工艺
1、 模压压力
压机对制品平面垂直方向施加的单位压力,生产上常用压机的
5、水份与挥发物的含量
游离水,以及受热受压时所释放出的氨、甲醛与结合水。
产生后果:
流动性太大,收缩率大,翘曲,无光泽,波纹。
解决方法:
预热。
6、细度与均匀度
细度:颗粒直径大小; 均匀度:颗粒间直径大小的差距。
第一章 模压成型工艺 三、模压成型工艺
模具清理和嵌件安放
压缩料
计量
预压或预热
加料
合模
排气
保压固化
第二章 注射成型工艺
保留一小段
螺杆向前一点
3.2、保压
• 在充填结束后到开模前的这段时间称为“后充填时间” • 充填结束后以某一压力维持住螺杆直到浇口冷却凝固所费的时间称为 “保压/维持时间”
• 弥补材料本身的可压缩性及冷却收缩
• 这段时间是由熔体填充模腔99%开始至浇口凝固为终止。保持压力时 亦要预先保留一小段的熔胶位置在螺杆前。这保压的一段就是防止熔
模压压力的选择与压塑料的工艺性能和制品的成 型条件有关:
流动性↓ 工艺性能 固化速度↑ 压缩率↑ 经过预热 模压温度↑ 成型条件 制品深度↑ 形状复杂 制品密度↑ → → → → → → → → 模压压力 模压压力 模压压力 模压压力 模压压力 模压压力 模压压力 模压压力 ↑ ↑ ↑
↑ ↑ ↑
第一章 模压成型工艺
未预热:25~35MPa
第一章 模压成型工艺
4、嵌件安放
嵌件通常是制品的导电部分,或使制品与其他物体结合用的,安放
要求:正确,平稳。
5、加料
加料量多,则制品毛边厚,难以脱模;少则制品不紧密,光泽差; 所以加料量要准确。
加料工序强调的是加料准确和合理堆放。一般应堆成“中间高,四
周低”的形式。原因:有利于排气;闭模中对模与物料接触时少冲料。
准备
温度 压力 时间
注射
后处理
第二章 注射成型工艺 一、成型过程
注射成型是一个循环的过程,每一周期主要包括: 定量加料—熔融塑化—施压注射—充模冷却—启
模取件。取出塑件后又再闭模,进行下一个循环。
第二章 注射成型工艺
1、成型三大过程
塑料熔体填模过程
充填阶段:刚注满模腔 增压阶段:模具承受一定压力 补偿阶段:收缩引起补缩。大部分残余应力在此 阶段产生。
第二章 注射成型工艺
熔体流动过程
凝固层 Frozen Layer 模具 Mold Wall
Melt
喷泉流区域 Fountain Flow Region
模具 Mold Wall
第二章 注射成型工艺
熔体正在冷却
模 具 壁
P
融体流动状态
波纤
第二章 注射成型工艺
2、注射成型周期
开模时间
填充时间
保压时间
第一章 模压成型工艺
第一章 模压成型工艺
2、模具
模具(钢制),有多种类型,结构形式通常较简单。模压成型用的 模具常用的有三种: 1)溢式模具;2)不溢式模具;3)半溢式模具
第一章 模压成型工艺
溢式模具示意图
1-上模板;2-组合式阳模;3-导柱;4-阴模;5-气孔;6-下模板; 7-顶杆;8-制品;9-溢料缝
第一章 模压成型工艺
不溢式模具示意图
1-阳模; 2-阴模; 3-制品;4-顶杆;5-定位下模板
第一章 模压成型工艺
半溢式模具示意图 (a)有支撑面(b)无支撑面
1-阳模;2-制品;3-阴模;4-溢料刻槽;5-支撑面
(A段为装料室,B段为平直段)
第一章 模压成型工艺 二、热固性模塑料的成型工艺性能
一定要对材料进行预处理,使得材料能保持合适的水分。
第二章 注射成型工艺
几种塑料的烘料条件及成型时所能允许的适当水分:
注: ※最佳;○可接受;□尽量避免;×不好
第二章 注射成型工艺
2、模温的设定
2.1、模温影响成型周期及成形品质,在实际操作 当中是由使用材质的最低适当模温 开始设定, 然后根据品质状况来适当调高。 2.2、正确的说法,模温是指在成形被进行时的模腔 表面的温度,在模具设计及成形工程的条件设 定上,重要的是不仅维持适当的温度,还要能 让其均匀的分布。 2.3、不均匀的模温分布,会导致不均匀的收缩和内 应力,因而使成型口易发生变形和翘曲。
9、 脱模
热固性塑料可趁热脱模,通常靠顶出杆来完成。(问题:热塑性塑 料呢?) 热脱模须注意两个问题:1)防止冷却翘曲;2)防止产生内应力
热处理——消除内应力;进一步固化,直至固化完全。(处理温度 比成型温度高10~50℃。) 整修——修边。
10、后处理
第一章 模压成型工艺
四、压模成型工艺条件及控制
发生交联,结构趋于紧密,加上低分子物挥发,体积必定收缩,尺寸变化
很大。一般高分子材料的SL在1~3%,是模具设计的重要指标。
产生收缩的基本原因:
化学结构的变化(交联)、热收缩、弹性回复、塑性形变。
影响收缩率的因素:
工艺条件、模具和制品的设计、塑料的性质。
产生的后果:制品翘曲、开裂。 解决的办法:预热、采用不溢式模具、严格工艺规程。
第二章 注射成型工艺
3.4、开模时间
• 整个行程包括公模后移,模具 打开,成品顶出及移出,模具关 闭等。
为下一阶段做好准备!
第二章 注射成型工艺 二、注射成型条件
1、成型前的物料干燥
成型加工前,塑胶必须被充分的干燥。含有水分的材料进入 模腔后,会使制件的表 面出现银绦状的瑕斑,甚至会在高温
时发生加水分解的现象,致使材质劣化。因此在成型加 工前
表压表示,可以换算。
压力的作用:
促进物料流动,充满型腔提高成型效率。 增大制品密度,提高制品的内在质量。 克服放出的低分子物及塑料中的挥发物所产生的压力,从而避免制品
出现气泡、肿胀或脱层。
闭合模具,赋予制品形状尺寸。 一般,热固性塑料如PF、UF:Pm =15~30 MPa
第一章 模压成型工艺
脱模
制品后处理
热固性塑料制品
第一章 模压成型工艺
1、计量
重量法:按质量加料,准确但麻烦;
容量法:按体积加料,方便但不及重量法准确。
记数法:按预压坯料计数,操作最快,但预先有预压计量操作。
2、预压
在室温下,把定量的料预先用冷压法压成一定形状大小的胚料。 影响预压料质量的因素主要有模塑料的水分,颗粒大小,压缩率,
1、流动性
热固性模塑料的流动性是指其在受热和受压情况下充满整个模具型腔 的能力。流动性即可塑性,对成型加工极为重要,直接影响热固性塑料成型 过程中的物理化学行为及制品的质量。
影响流动性的因素:
压模塑料的性能和组成(分子量、颗粒形状、小分子);
模具与成型条件(光洁度、流道形状、预热)。
流动性过大过小的后果:
体凝固收缩后的空洞,或浇口位置的弱处等导致模件强度不足的关键。
第二章 注射成型工艺
3.3、冷却时间
• 压力维持结束后压力开始释放,一直到 成品固化到足以顶出时所需的时间称 为冷却时间 • 也是一般所称的固化时间(Cure Time) • 当熔体进入模腔,碰到金属表面时, 熔体冷却的步骤就己经开始
开始储料
预压温度和压力等。
第一章 模压成型工艺
2.1、预压的优点:
加料快、准确、无粉尘; 降低压缩率,可减小模具装料室和模具高度;
预压料紧密,空气含量少,传热快,又可提高预热温度,从而缩短了
预热和固化的时间,制品也不易出现气泡; 便于成型较大或带有精细嵌件的制品。
2.2、预压的缺点:
如果预压生产效率低,则运营成本高;
4、能压制较大面积、形状复杂及厚度较大的制品;
5、制品成型后,可趁热脱模。
第一章 模压成型工艺 一、 模压成型的设备和模具
1、成型设备-压机
压机的作用:
通过模具对塑料传热和施加压力;
提供成型的必要条件:T,P; 开启模具和顶出制品。
压机——机械加压、液压(上压式、下压式) 压机的主要参数:公称压力、柱塞直径、压板尺寸和 工作行程。
塑料成型工艺
第一章、模压成型工艺
第二章、注射成型工艺 第三章、常见缺陷原因分析及对策 第四章、塑料制品检验
第一章 模压成型工艺
工艺特点:
1、成型工艺及设备成熟,是较老的成型工艺,设备和模具比 注射成型简单; 2、间歇成型,生产周期长,生产效率低,劳动强度大,难以 自动化;
3、制品质量好,不会产生内应力或分子取向;
排气的原因:热固性塑料在加工中因缩聚等化学反应会释放出小分子 物质,在成型温度下体积膨胀,形成气泡。 排气的作用:赶走气泡、水份、挥发物,缩短固化周期,避免制品内 部出现气泡或分层现象。 排气的方式:卸压,松模,时间很短即可(零点几秒~几秒),如此 连续几次(2~5次)。 排气的次数、间隔时间等,决定于所模压物料的性质。 何时排气:不能过早,也不能过迟。