面料及坯布疵点分析大全
坯布验布评分标准
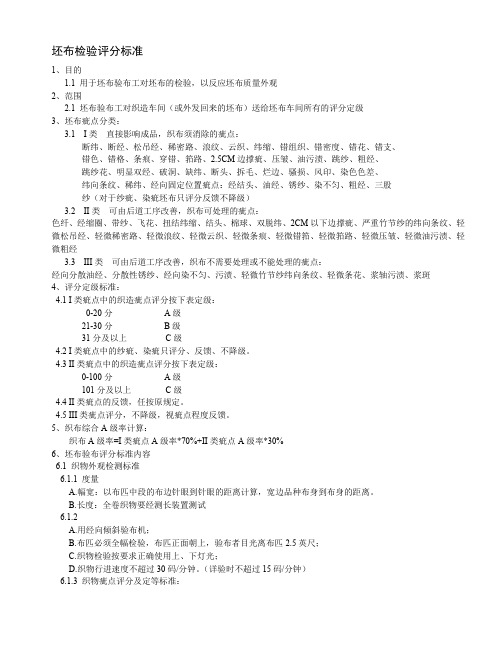
坯布检验评分标准1、目的1.1 用于坯布验布工对坯布的检验,以反应坯布质量外观2、范围2.1 坯布验布工对织造车间(或外发回来的坯布)送给坯布车间所有的评分定级3、坯布疵点分类:3.1 I类直接影响成品,织布须消除的疵点:断纬、断经、松吊经、稀密路、浪纹、云织、纬缩、错组织、错密度、错花、错支、错色、错格、条痕、穿错、筘路、2.5CM边撑疵、压皱、油污渍、跳纱、粗经、跳纱花、明显双经、破洞、缺纬、断头、拆毛、烂边、骚损、风印、染色色差、纬向条纹、稀纬、经向固定位置疵点:经结头、油经、锈纱、染不匀、粗经、三股纱(对于纱疵、染疵坯布只评分反馈不降级)3.2 II类可由后道工序改善,织布可处理的疵点:色纤、经缩圈、带纱、飞花、扭结纬缩、结头、棉球、双脱纬、2CM以下边撑疵、严重竹节纱的纬向条纹、轻微松吊经、轻微稀密路、轻微浪纹、轻微云织、轻微条痕、轻微错筘、轻微筘路、轻微压皱、轻微油污渍、轻微粗经3.3 III类可由后道工序改善,织布不需要处理或不能处理的疵点:经向分散油经、分散性锈纱、经向染不匀、污渍、轻微竹节纱纬向条纹、轻微条花、浆轴污渍、浆斑4、评分定级标准:4.1 I类疵点中的织造疵点评分按下表定级:0-20分A级21-30分B级31分及以上C级4.2 I类疵点中的纱疵、染疵只评分、反馈、不降级。
4.3 II类疵点中的织造疵点评分按下表定级:0-100分A级101分及以上C级4.4 II类疵点的反馈,任按原规定。
4.5 III类疵点评分,不降级,视疵点程度反馈。
5、织布综合A级率计算:织布A级率=I类疵点A级率*70%+II类疵点A级率*30%6、坯布验布评分标准内容6.1 织物外观检测标准6.1.1 度量A.幅宽:以布匹中段的布边针眼到针眼的距离计算,宽边品种布身到布身的距离。
B.长度:全卷织物要经测长装置测试6.1.2A.用经向倾斜验布机;B.布匹必须全幅检验,布匹正面朝上,验布者目光离布匹2.5英尺;C.织物检验按要求正确使用上、下灯光;D.织物行进速度不超过30码/分钟。
坯布布面常见疵点分析

坯布布面常见疵点分析1.密路:局部纬纱密度比布面正常情况大,表现为纬向出现一直横档,颜色偏向纬纱,透光性差。
2.稀路:局部纬纱密度比布面正常情况小,表现观看,出现纬向一条路,颜色偏向经纱,易透光。
3.双纬:一般正常品种,每一织口引入一根纬纱,双纬则引入两根纬纱在一起。
4.断纬:织入纬纱断一段或短一段,并未停车。
5.断经:经纱断裂,平纹有双经的外观,但在开下灯光时有透光现象。
6.纬缩:纬纱松驰,织入布面在布面凸出或起圈。
7.错综:没有按工艺规定穿综顺序进行穿综,布面显示组织有变化。
8.错筘:过筘时,没有按工艺规定,穿错筘,布面经向出现一稀密现象。
9.松吊经:在织物中,经纱张力一会儿紧,一会儿松,产生经向条痕,松经时经纱凸出布面,吊经时经纱凹入布面。
10.边撑疵:在织物布边,经纱或纬纱被边撑刺钩断,拉断或针孔过大。
11.跳纱、跳花:织物中,经纬纱没有按正常组织规律交织,单根成多根经(纬)纱浮在多根纬(经)纱上。
12.错支、错纱:织物中织入工艺要求外的纱,如颜色不对,纱支不对。
13.双经:织布时综眼里多穿了一根经纱,虽未组织错乱,但多穿部分已成为双经。
14.筘路:由于筘齿损伤、变形、发软松动等原因,使布面经向呈一直条疏密现象。
15.稀纬:纬纱比正常纱细一些,造成纬向一条痕,有有结和无结之分。
16.结头:打结纱尾过长(3MM以上)或因纱线太粗造成接头太大突出于布面。
17.油经、污经:经纱被油污沾上。
18.条花:布面出现颜色深浅程度相对比较明显的经向条形疵点。
19.纬向条纹:布面纬纱颜色不均匀,深浅不一,有时表现出为横向抛物线状条纹。
20.色差:由于纬纱颜色有深浅,在布面形成纬向横档。
21.轻浆棉球:由于经纱浆纱不当,经纱毛羽多,织布后布面出现许多棉球,轻浆棉球一般能沿经纱上下滑动。
22.云织:布面纬纱一段稀,一段密,稀密交替出现。
23.油污渍:布面上沾上三条纱及以上的一志块油污痕渍。
24.经缩圈:织物表面经纱呈起圈现象,多发生在泡泡布和提花布上。
(完整版)织布疵点大全

织造品质织疵成因一、经纱断头原因。
(不包括纱原纱品质及准备工用原因)1.综框过高低,左右不平。
2.开口过大过小,过早过迟。
3.经纱路线过短,(后梁过前),经纱张力太大4.后梁及停经架位置赤字高,上下层经不张力悬殊太大。
5.停经架与综框距离过远过低。
6.空气调节、湿度过高过低。
(尤其麻纱反应最大)7.剑颈、钢筘、综丝、停经片、剑带等毛糙。
8.过撑位置过高,应距最低位置1mm。
9.结头纱尾、飞花杂物搅入经纱。
10.值车对经纱倒断头、搅头处理不良,断经后接纱结头不良;如纱尾长。
二、断纬原因1.纬纱强力过低、松捻纱、大结头、棉籽屑、飞花回丝夹附。
2.络筒时强力过太、张力太大、成形不良。
3.边撑太前撞筘,距离钢筘到少要有1mm的间隙。
三、双纬1.纬纱断头为主要原因,首先须减少断纬线。
2.值车工不注意在断头后,未将织口内断纬拉清。
3.值车工在断纬后未将开开口顺序较主合适时开车。
4.纬纱断头后断纬运动未立即作用停车,而中间缺少数根或一根纬纱。
四、缩纬1.纬纱捻度过大。
2.纬纱太干或太湿。
3.开口不清。
4.开口时间过早或过迟。
5.纬纱引出张力太小。
6.经纱张力不足。
7.纬纱筒子有大结头、飞花、杂物附着、粗节纱造成部分开口不清。
五、小稀路1.筘座及卷取刺毛辊松动或腐蚀。
2.经纱张力过大或过小。
3.经纱上下两层纱张力相差悬殊。
4.停车过久后开车时梭口未较正。
5.停车后开车起动太缓慢影响打纬力。
(主电机皮带松驰无力)六、纬纱尾织入1.右测经纱距离顺风管太远,废边纱未能很好夹持纱尾。
2.纬纱张力太小,剑头开启时间太晚。
七、稀路1.起因均为断纬、首先须减少断纬。
2. 断纬卷取退卷绕装置不良。
八、跳花1、综框松动、不平或过低。
2、经纱张力上下两层相差悬殊。
3、浆纱过毛、开口粘滞、上浆不良引起绒球或毛羽。
4、经纱有飞毛、纱尾及大结头。
5、综丝头尾损断或综丝搅乱。
6、部分经纱松弛或张力过低。
7、开口时间不对。
(开口过小) 8、边撑高低不标准。
坯布布面常见疵点分析

1.密路:局部纬纱密度比布面正常情况大,表现为纬向出现一直横档,颜色偏向纬纱,透光性差。
2.稀路:局部纬纱密度比布面正常性情况小,表现观看,出现纬向一条路,颜色偏向经纱,易透光。
3.xx:一般正常品种,每一织口引入一根纬纱,双纬则引入两根纬纱在一起。
4.断纬:织入纬纱断一段或短一段,并未停车。
5.断经:经纱断裂,平纹有双经的外观,但在开下灯光时有透光现象。
6.纬缩:纬纱xx,织入布面在布面凸出或起圈。
7.错综:没有按工艺规定穿综顺序进行穿综,布面显示出组织有变化。
8.错筘:过筘时,没有按工艺规定,穿错筘,布面经向出现一稀密现象。
9.松吊经:在织物中,经纱张力一会儿紧,一会儿松,产生经向条痕,松经时经纱凸出布面,吊经时经纱凹入布面。
10.边撑疵:在织物布边,经纱或纬纱被边撑刺钩断、拉断或针孔过大。
11.跳纱、跳花:织物中,经纬纱没有按正常组织规律交织,单根成多根经(纬)纱浮在多根纬(经)纱上。
12.错支、错纱:织物中织入工艺要求外的纱,如颜色不对,纱支不对。
13.双经:织布时综眼里多穿了一根经纱,虽未组织错乱,但多穿部分已成为双经。
14.筘路:由于筘齿损伤、变形、发软松动等原因,使布面经向呈一直条疏密现象。
15.稀纬:纬纱比正常纱细一些,造成纬向一条痕,有有结和无结之分。
16.结头:打结纱尾过长(3mm以上)或因纱线太粗造成接头太大突出于布面。
17.油经、污经:经纱被油污沾上。
18.条花:布面出现颜色深浅程度相对比较明显的经向条形疵点。
19.纬向条纹:布面纬纱颜色不均匀,深浅不一,有时表现为横向抛物线状条纹。
20.色差:由于纬纱颜色有深浅,在布面形成纬向横档。
21.轻浆棉球:由于经纱浆纱不当,经纱毛羽多,织布后布面出现许多棉球,轻浆棉球一般能沿经纱上下滑动。
22.云织:布面纬纱一段稀,一段密,稀密交替出现。
23.油污渍:布面上沾上三条纱及以上的一块块油污痕渍。
24.经缩圈:织物表面经纱呈起圈现象,多发生在泡泡布和提花布上。
坯布疵点检测技术

坯布疵点检测技术前言坯布是制作纺织品的重要原材料,而对于制作出来的纺织品,品质的好坏直接影响到销售情况。
在坯布生产过程中,可能会存在疵点,因此需要进行疵点检测。
本文将介绍坯布疵点检测技术的相关内容。
一、坯布疵点的种类坯布的疵点种类很多,主要包括以下几种:1. 结痕:指纱线在织造过程中,受到长时间拉拽而产生的褶皱和织痕。
2. 炸纬:指纬线在织造过程中出现的断裂、起毛、飘边现象,使布面出现纬向的横向白线。
3. 破洞:指因纱线断裂或织造顺序错位而造成的正面或背面的孔洞。
4. 合股:指两股或多股纱线在织造过程中并合成一股,或在穿纬过程中被咬住所形成的缺口、断裂。
二、坯布疵点检测技术1. 人工检测传统的坯布疵点检测方式是人工检测,但是这种方法效率低、耗时长且人为因素较大,容易导致漏检和误判等情况。
2. 图像处理技术随着计算机技术的发展,图像处理技术逐渐应用到了坯布疵点检测中。
这种方法可以高效、快速地检测坯布疵点,并且减少人工因素的影响。
通过采集坯布表面图像,利用图像处理算法对坯布疵点进行分析与处理。
这种方法可以对坯布的疵点进行快速且准确的检测,具有高效、自动化等特点。
三、坯布疵点检测技术的局限性尽管现有的图像处理技术在检测坯布疵点方面已经取得了一定的进展,但是仍然存在以下局限性:1. 图像质量的不确定性为了获得准确的疵点检测结果,需要获取高质量的图像,但是由于各种原因(如纺织品表面凹凸不平、光照条件不佳等),获取高质量的图像是困难的。
2. 疵点形态的复杂性坯布疵点形态复杂,而且会随着生产线的不同而变长,这导致疵点检测算法难以适应所有情况,甚至可能会造成漏检。
3. 背景噪声的影响由于照片拍摄时环境不同,光线强度、噪声等情况也不相同,因此需要进行背景去除等操作,增加算法的复杂性和难度。
结语坯布疵点检测是现代纺织业生产过程中的重要一环,传统的人工检测方法效率低、耗时长且人为因素较大,容易导致漏检和误判等情况。
而图像处理技术,则可以高效、快速地检测坯布疵点,避免了人工因素的影响,具有高效、自动化等特点。
织布疵点大全

织造品质织疵成因一、经纱断头原因。
(不包括纱原纱品质及准备工用原因)1.综框过高低,左右不平。
2.开口过大过小,过早过迟。
3.经纱路线过短,(后梁过前),经纱张力太大4.后梁及停经架位置赤字高,上下层经不张力悬殊太大。
5.停经架与综框距离过远过低。
6.空气调节、湿度过高过低。
(尤其麻纱反应最大)7.剑颈、钢筘、综丝、停经片、剑带等毛糙。
8.过撑位置过高,应距最低位置1mm。
9.结头纱尾、飞花杂物搅入经纱。
10. 值车对经纱倒断头、搅头处理不良,断经后接纱结头不良;如纱尾长。
二、断纬原因1.纬纱强力过低、松捻纱、大结头、棉籽屑、飞花回丝夹附。
2.络筒时强力过太、张力太大、成形不良。
3.边撑太前撞筘,距离钢筘到少要有1mm的间隙。
三、双纬1.纬纱断头为主要原因,首先须减少断纬线。
2.值车工不注意在断头后,未将织口内断纬拉清。
3.值车工在断纬后未将开开口顺序较主合适时开车。
4. 纬纱断头后断纬运动未立即作用停车,而中间缺少数根或一根纬纱。
四、 缩纬1.纬纱捻度过大。
3.开口不清。
5.纬纱引出张力太小。
6.经纱张力不足。
7.纬纱筒子有大结头、飞花、杂物附着、粗节纱造成部分开口不清。
五、 小稀路1.筘座及卷取刺毛辊松动或腐蚀。
2.经纱张力过大或过小。
3.经纱上下两层纱张力相差悬殊。
4.停车过久后开车时梭口未较正。
5.停车后开车起动太缓慢影响打纬力。
(主电机皮带松驰无力)六、 纬纱尾织入1.右测经纱距离顺风管太远,废边纱未能很好夹持纱尾。
2.纬纱张力太小,剑头开启时间太晚。
七、 稀路1.起因均为断纬、首先须减少断纬。
2. 断纬卷取退卷绕装置不良。
八、 跳花1、综框松动、不平或过低。
2、 经纱张力上下两层相差悬殊。
3、浆纱过毛、开口粘滞、上浆不良引起绒球或毛羽。
2.纬纱太干或太湿。
4. 开口时间过早或过迟。
4、经纱有飞毛、纱尾及大结头。
5、综丝头尾损断或综丝搅乱。
6、部分经纱松弛或张力过低。
7、开口时间不对。
技术|粗细节、条干不匀等五大常见疵点的影响、成因及改善措施

技术|粗细节、条干不匀等五大常见疵点的影响、成因及改善措施对于纯棉精梳细号纱线,从危害程度和发生频次看影响布面质量的有害疵点主要是粗细节、条干不匀、飞花、棉结和异常疵点。
这些疵点对后工序有哪些影响?影响布面质量的有害疵点01粗细节粗节,布面表现为一个突出的粗节,影响织物外观,甚至造成布面降级。
布厂可以通过人工挑修改善外观,但是挑修操作困难、费时费工;细节,因为比正常纱细,就会形成纱线强力弱环,造成准备和织造过程的断头,影响准备和织造的效率,即使未发生断头在布面表现为细于正常纱的疵点,且无法修复,数量多时会造成布面降级。
02条干不匀影响织物外观,造成布面降级,特别严重时在织物布面表现为条影或木纹,较轻的情况下布面外观浑浊、不光洁似有云斑,条干不匀还会造成染色不匀。
03棉结布面表现为棉点或白星,星星点点分布在布面上,影响织物外观。
布厂可通过人工挑修来降低棉点,但数量过多时挑修不能达到良好的效果,而且费时费工。
此类疵点较多或较大时在准备、织造中纱线断头率会增加,影响准备织造效率,影响织物外观及平整,造成布面降级。
04飞花布面表现介于粗节和大棉结之间,比粗节短、纤维松散,影响布面光洁程度。
通过人工挑修可得到改善。
异常疵点多表现为长片段,发生频率低,如单纱中的双线纱,股线中的三股纱和四股纱等,以及长粗节、长细节。
此类疵点严重影响织物外观,造成布面降级,制衣厂一般都需要做避裁处理,会降低布的利用率。
更严重时甚至会延误订单的交期,赔偿客户的损失。
不同的布种对纱线的质量要求可以看出纱线疵点对后工序尤其是织物的布面效果有较大影响。
从布厂的产品种类看,不同的布种对纱线的质量要求也不同。
a)净色布种(经纬纱线同色或不同色的平纹织物):根据经纬颜色的反差大小,对纱线的棉结要求不同,经纬颜色反差越大,对棉结要求越高,尤其经特殊后整理的布种对粗节、棉结要求更高。
b)米通条布种(经向、纬向或经纬两方向相邻纱线颜色不同的织物):纱线颜色反差越大,对粗节、棉结和条干均匀度的要求越高。
干货纺织品62种瑕疵及成因汇总,如何帮客户解决?
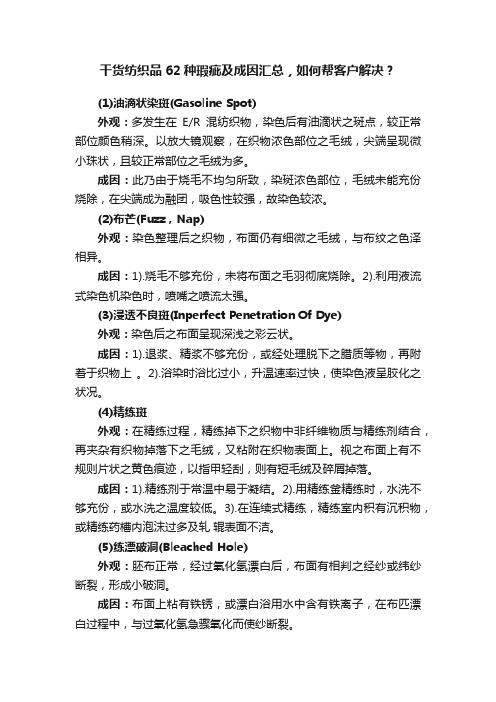
干货纺织品62种瑕疵及成因汇总,如何帮客户解决?(1)油滴状染斑(Gasoline Spot)外观:多发生在E/R混纺织物,染色后有油滴状之斑点,较正常部位颜色稍深。
以放大镜观察,在织物浓色部位之毛绒,尖端呈现微小珠状,且较正常部位之毛绒为多。
成因:此乃由于烧毛不均匀所致,染斑浓色部位,毛绒未能充份烧除,在尖端成为融团,吸色性较强,故染色较浓。
(2)布芒(Fuzz,Nap)外观:染色整理后之织物,布面仍有细微之毛绒,与布纹之色泽相异。
成因:1).烧毛不够充份,未将布面之毛羽彻底烧除。
2).利用液流式染色机染色时,喷嘴之喷流太强。
(3)浸透不良斑(Inperfect Penetration Of Dye)外观:染色后之布面呈现深浅之彩云状。
成因:1).退浆、精浆不够充份,或经处理脱下之腊质等物,再附着于织物上。
2).浴染时浴比过小,升温速率过快,使染色液呈胶化之状况。
(4)精练斑外观:在精练过程,精练掉下之织物中非纤维物质与精练剂结合,再夹杂有织物掉落下之毛绒,又粘附在织物表面上。
视之布面上有不规则片状之黄色痕迹,以指甲轻刮,则有短毛绒及碎屑掉落。
成因:1).精练剂于常温中易于凝结。
2).用精练釜精练时,水洗不够充份,或水洗之温度较低。
3).在连续式精练,精练室内积有沉积物,或精练药槽内泡沫过多及轧辊表面不洁。
(5)练漂破洞(Bleached Hole)外观:胚布正常,经过氧化氢漂白后,布面有相判之经纱或纬纱断裂,形成小破洞。
成因:布面上粘有铁锈,或漂白浴用水中含有铁离子,在布匹漂白过程中,与过氧化氢急骤氧化而使纱断裂。
(6)色花(Skilteriness)外观:布面有不规则片状之颜色深浅。
成因:前处理工程之退浆,精练未能彻底作好。
(7)雾斑(Mist)外观:片状之染斑,有深有浅,轮廓不明显,形状大小不一,发生之位置不集中,亦无一定之规则。
成因:1).待染之织物,被溅到污水或其它药品。
2).练漂后未立即烘干,长时间堆积在布车上,部份织物发生风干之水印。
- 1、下载文档前请自行甄别文档内容的完整性,平台不提供额外的编辑、内容补充、找答案等附加服务。
- 2、"仅部分预览"的文档,不可在线预览部分如存在完整性等问题,可反馈申请退款(可完整预览的文档不适用该条件!)。
- 3、如文档侵犯您的权益,请联系客服反馈,我们会尽快为您处理(人工客服工作时间:9:00-18:30)。
(4)飞花(Flyer)
外观:与粗结相似,但其较粗,不像粗结般之细长,纤维成团状。将纱略予退捻,可不致使纱断裂。
成因:细纱间内飘浮于空中之纤维团,或积集在机器喂入附近台面上之纤维 团,缠绕于纱上。
(8)纤维点(Fiber Spot)
外观:染色之织物,布面中有极少量之纤维不上色,或上色较浅,而呈现泛白色者。
成因:1).棉纤维中有死棉纤维。 2).在纺纱过程中,因疏忽或管制欠妥,混入极少量之聚酯纤维,于染 色时非使用分散性染料,及非高温施染,则聚酯纤维不上色。
(9)批号不同(Different Iots)
成因:多发生在中、下等级之棉质染色布,纱中死棉纤维所形成之棉粒,于 精练,丝光时未能清除。染色时因该种死棉纤维上色性甚差,故难以染着而呈现白点。近来20Ne以下之纯棉开端纺纱织成之织物,于染色时经常发生。
纺织品瑕疵——属于织造原因者
(1)异纱(Wrong Yarn)
外观:在针织物之毛中,横向连续之毛圈,由较规格用纱为粗或细之纱织造而成。一般多为单根,但偶亦有并列或间隔多根者。视之稀密、厚薄与正常者不同。
(5)节纱(Cockled Yarn)
外观:在约纤物幅宽长度之一段纱中,有间隔性之大粗结。纱之粗细变化似竹节状,一般在粗纱织物之纬纱较常见,故亦称竹节纬。
成因:精纺机之牵伸罗拉设定大紧,罗拉盖太松,喂入之粗纱中偶有异长之 纤维。
(6)纱支不均(Uneven Yarn)
外观:由织物长面观察,织入之纱有粗细不均匀之现象。一般多发生在纬纱。
面料及坯布疵点分析大全
(1)棉粒(Nep)
外观:布面呈现类似接头大小之棉纤维团,且系纺入纱中者。如将之拔下,则纱呈断裂或将至断裂之状态。低等级原棉纺成之粗纱,常有此种瑕疵。
成因:1).原棉中有死棉纤维团,于清花过程中未彻底除去。2).梳棉时锡林或针板之针不够尖锐,或两者间之隔距设定不当,未能 充份发挥梳理作用。
成因:1).整经牵纱时即疏忽将两根当作一根。 2).浆纱后分纱不清,两根粘在一起,形同一根。 3).穿综时两根穿入同一综丝。
(6)并纬(Mispick)
外观:纬纱两根织入同一织口内,偶亦有三根或更多根者。并纬之长度长短不等,以织物全幅宽者,与在近两布边10公分上下者较多。
成因:1).织物全幅长之并纬,系因停机排除故障后,未查对织口开车。或探纬针失效,断纬未自停。 2).非全幅长之并纬,经因保险纱之长度不够,边剪设定不当或不够锐利,及断纬后未将纱尾清除。
成因:在针织物织造时,操作人员误用非指定支数或丹尼规格之纱编织。误用较细之纱,则织物显得稀薄。误用较粗之纱,则织物显得密厚 。
(2)异经(Wrong End)
外观:梭织物之经纱有单独一根或并列数根非指定规格之粗细者。若为较细之纱,则称谓细经(Fine End)。若为较粗之纱,则称谓粗经(Coarse End) 。
成因:细纱机纺出之纱,由于牵伸机构故障,或性能不良,致纺出之纱在一 段间,时有略粗时有略细者。
(7)云织(Cloudd of Weaaving)
外观:纬纱之支数显著不均匀,织造时粗者或细者恰好集中排列在一起,形成片状,布面外观似片片浮云,故称云织。
成因:纬纱有规律性之不匀,于织造时纬纱之排列又恰好粗者或细者汇集在 一起。
(10)蒸纱不良:
外观:一疋E/C混纺布,经退浆、精练、漂白后,布幅有间隔性宽窄不同之变化。
成因:混纺纱于细纱落管后,需利用高压饱和蒸汽于密闭之容器内热蒸处理 ,以稳定纱之物性。如蒸纱温度或时间不足,未能使纱定型,则于练漂时蒸煮后,织物布面横向呈现一段紧,一段松之现象。
(11)白点:
外观:染色之织物,布面呈现未上色之纤维团,尤以染中深色者较为显著。
外观:化纤丝或化纤加工丝织物,混纺纱织物,支数粗细与密度均符合规定,但经染色后,经纱间或纬纱间有界限分明颜色深浅之不同。
成因:1).在织造时虽使用丹尼数相同之丝,但制造批号不同。由于吸色性不同,或伸缩性、膨松性不一致,在经染色后,则有颜色深浅之不同。 2).在织造时使用之混纺纱,虽支数与密度符合规定,但纱中纤维之混 纺率不同,在经染色后则有颜色深浅之差别。
(7)稀衖(Set Mark,Fine)
外观:布面上纬纱排列之密度较规定稀少。沿织物长度一段织入之纬纱,由正常密度逐渐变稀,再由最稀逐渐恢复至原来密度,形成一条等宽窄之稀疏布面。
成因:1).探纬针失灵,无纬纱时继续空转送经。 2).织造时经纱张力控制不当。 3).停机再开车前经纱张力调整太紧。
(8)密路(Set Mark,Coarse)
(2)棉籽皮(Seeds)
外观:纯棉或棉纤维混纺之胚布面,有甚小黑色或深色之非纤维纤碎片点。
成因:1).轧棉工程在将棉纤维与棉籽分离时,纤维根端带有棉籽皮,或棉籽 被碾碎而掺附于原棉中。 2).清花过程未能将棉籽皮彻底清除。
(3)粗结(Slub)
外观:织物之经纱或纬纱上,偶有一小段长约5至20mm较纱之正常直径为粗,较炒之正常捻数为少之簇状纤维。
成因:于整经时取用牵经之筒子纱支数错误,使用非指定规格之经纱。此种瑕疵经常为全匹性者。
(3)异纬(Wrong Pick)
外观:梭织物之纬物,有一根或连续多根非指定规格之粗细者。若为较细之纱,则称谓细纬(Fine Pick)。若为较粗之纱,则称谓粗纬(Coarse Pick)。
成因:于织造时,纬纱管之纬纱,或无梭织机喂入之筒子纱支数错误,使用非指定规格之纬纱。操作人员于发现后,多予以停机拆除。但自动换管之织机,则往往不易发现。
(4)组织错误(Wrong Weaving)
外观:即织法错误,布面之织纹与原设计成。其它如提花织物之纹板错误,多规格经纱织物之经纱排列错误等。
(5)并经(Wrong Draw)
外观:相邻之两根经纱并在一起,依织物组织当作一根织入布中者。视之,该根(实为两根)纱显得特别粗。此种瑕疵均为全匹性者,如在经轴初织时发现,剔除并列中之一根,则能完全避免。