车身涂装工艺设计方案研究(九院盖东辉)
工程车辆喷涂方案设计
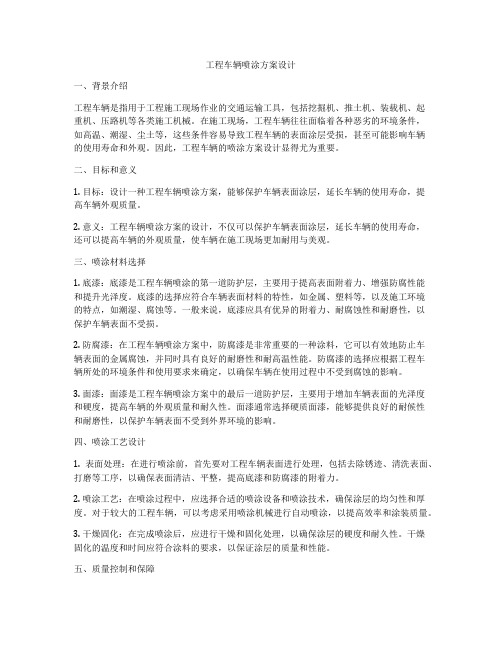
工程车辆喷涂方案设计一、背景介绍工程车辆是指用于工程施工现场作业的交通运输工具,包括挖掘机、推土机、装载机、起重机、压路机等各类施工机械。
在施工现场,工程车辆往往面临着各种恶劣的环境条件,如高温、潮湿、尘土等,这些条件容易导致工程车辆的表面涂层受损,甚至可能影响车辆的使用寿命和外观。
因此,工程车辆的喷涂方案设计显得尤为重要。
二、目标和意义1. 目标:设计一种工程车辆喷涂方案,能够保护车辆表面涂层,延长车辆的使用寿命,提高车辆外观质量。
2. 意义:工程车辆喷涂方案的设计,不仅可以保护车辆表面涂层,延长车辆的使用寿命,还可以提高车辆的外观质量,使车辆在施工现场更加耐用与美观。
三、喷涂材料选择1. 底漆:底漆是工程车辆喷涂的第一道防护层,主要用于提高表面附着力、增强防腐性能和提升光泽度。
底漆的选择应符合车辆表面材料的特性,如金属、塑料等,以及施工环境的特点,如潮湿、腐蚀等。
一般来说,底漆应具有优异的附着力、耐腐蚀性和耐磨性,以保护车辆表面不受损。
2. 防腐漆:在工程车辆喷涂方案中,防腐漆是非常重要的一种涂料,它可以有效地防止车辆表面的金属腐蚀,并同时具有良好的耐磨性和耐高温性能。
防腐漆的选择应根据工程车辆所处的环境条件和使用要求来确定,以确保车辆在使用过程中不受到腐蚀的影响。
3. 面漆:面漆是工程车辆喷涂方案中的最后一道防护层,主要用于增加车辆表面的光泽度和硬度,提高车辆的外观质量和耐久性。
面漆通常选择硬质面漆,能够提供良好的耐候性和耐磨性,以保护车辆表面不受到外界环境的影响。
四、喷涂工艺设计1. 表面处理:在进行喷涂前,首先要对工程车辆表面进行处理,包括去除锈迹、清洗表面、打磨等工序,以确保表面清洁、平整,提高底漆和防腐漆的附着力。
2. 喷涂工艺:在喷涂过程中,应选择合适的喷涂设备和喷涂技术,确保涂层的均匀性和厚度。
对于较大的工程车辆,可以考虑采用喷涂机械进行自动喷涂,以提高效率和涂装质量。
3. 干燥固化:在完成喷涂后,应进行干燥和固化处理,以确保涂层的硬度和耐久性。
工程车辆喷涂方案模板范文

工程车辆喷涂方案模板范文本文旨在提供一份工程车辆喷涂方案模板范文,供工程车辆喷涂相关人员参考。
本文仅为范例,具体方案根据实际需求作出调整。
1.背景和目的[公司名称]拟对[车辆数量]辆工程车辆进行喷涂,提升车辆外观美观度,增强公司品牌形象。
喷涂方案应考虑外观效果、涂装材料质量和费用等方面因素,确保符合公司定位和需求。
2.需求概述2.1 车辆型号与数量具体车型包括XXXX,XXX等等,需求数量为XXXX。
2.2 涂装颜色与效果涂装车辆颜色为公司主色系,应用喷涂技术以达到如下效果:•喷涂色面光滑平整,不得出现色差、流挂等•喷涂图案清晰鲜明,不得模糊、虚浮或变形•喷涂有一定的耐候性和耐磨性,维持时间应不少于2年3.方案设计设计方案应基于公司品牌形象与要求,针对车辆型号、相应面积进行量身设计。
3.1 喷漆采用的主要材料及规格•涂料品牌:XXXX•涂料颜色:XXXX•涂料规格:XXX•研磨材料:XXX3.2 喷涂工艺•涂料前处理:车体表面打磨,去除旧漆和其他杂质•喷涂过程:工程车辆进行VIP处理,涂装前最好采用静电除尘设备除尘,下面是参考的工艺:步骤工序备注1 底漆2 中涂层3 刻画logo和其他图案4 透明层增加耐候性,防止褪色5 定型后喷涂的干涂不会剥落6 处理瑕疵,修整边缘在定型前完成7 检查,验证每个车辆的品质被实现8 深度检测以质量为导向]检查检查是否有残漆、下垂9 定期皮肤深度抛光定期涂层更新让车体恢复光亮。
3.3 喷涂颜色与图案根据公司品牌要求,车身颜色应为XXXX。
图案的设计包括XXX和XXXX等等。
需要在搭配方案中约定使用RGB或PMS颜色编号。
TIF、EPS或AI形式的高分辨率格式的文件应当用于印刷制品。
4.费用估算及支付4.1费用总计根据方案设计和涂装车辆的具体数量,涂装总费用估计为XXXX元。
4.2货款支付方式•5000元定金•开始喷涂当车辆50%时支付50%的款项•全部喷涂完成后支付剩余的50%货款。
汽车涂装中的涂装工艺创新和创新技术
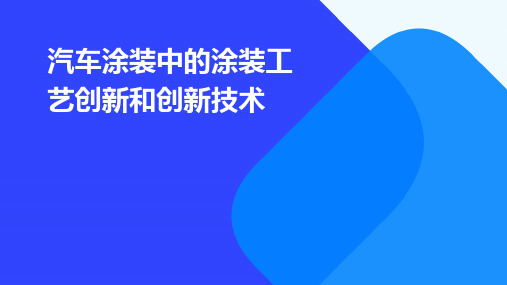
2
对于小批量生产或定制化生产,3D打印技术可以 快速、灵活地满足生产需求,降低生产成本。
3
3D打印技术还可以用于制造难以通过传统加工工 艺制造的复杂形状和结构,提高产品的设计自由 度。
05
未来展望
涂装工艺和技术的未来发展方向
高效能涂料
随着环保法规的日益严格,高效能涂料的需求将不断增加 ,如高耐候性、高防腐性、低VOC含量的涂料。
纳米涂层具有优异的耐磨性和 耐化学腐蚀性,能够更好地保 护汽车表面免受划痕和腐蚀。
纳米涂层还具有优异的透明度 和色彩稳定性,能够提供更好 的外观效果,并且不会影响汽 车的原漆颜色。
3D打印技术在复杂零部件和小批量生产方面的优势
1
3D打印技术可以快速制造出复杂的零部件,减少 传统加工工艺中的模具制造和切削加工等环节, 缩短产品开发周期。
汽车涂装工艺的发展历程
01
02
03
04
传统涂装工艺
以手工操作为主,生产效率较 低,但适合小批量生产。
半自动化涂装工艺
采用机械手、自动化设备等辅 助手段,提高了生产效率和涂
装质量。
自动化涂装工艺
通过机器人、自动化生产线等 高度自动化设备,实现大规模
、高效的生产。
环保型涂装工艺
随着环保意识的提高,无尘化 、水性化等环保型涂装工艺逐
渐成为主流。
02
涂装工艺创新
新型涂装材料
新型涂装材料
采用高分子材料、纳米材料等新型材料,提高涂层的耐磨性、耐候性和抗腐蚀 性,延长汽车使用寿命。
环保涂装材料
研发低挥发性有机化合物(VOC)排放的涂装材料,降低对环境和人体的危害 。
环保涂装技术
高效涂装前处理技术
工程车车身喷涂设计方案

工程车车身喷涂设计方案一、绪论工程车是工地施工必不可少的重要工具,其车身喷涂设计不仅仅是为了美观,更是为了提高其辨识度和安全性。
因此,对工程车的车身喷涂设计方案进行合理的规划和设计是至关重要的。
本文将从工程车车身喷涂设计的背景、流程、要求以及具体设计方案等方面展开讨论,为工程车的车身喷涂设计提供一些建议。
二、背景分析1. 工程车身喷涂的重要性工程车在施工现场扮演着重要的作用,除了承担特定的施工任务外,还承担着辨识度和安全性的责任。
良好的车身喷涂设计可以让工程车在施工现场更加显眼和易于识别,有效提高了施工效率。
另外,良好的车身喷涂设计还可以提高工程车的品牌形象和企业形象,为企业赢得更多的认可和信任。
2. 工程车身喷涂的现状目前,对于工程车的车身喷涂设计并没有统一的标准和规范,导致工程车的车身喷涂设计五花八门,缺乏统一性和规范性。
甚至一些小型施工企业对车身喷涂设计并不够重视,这导致了在施工现场工程车辨识度不高,存在安全隐患。
因此,有必要对工程车的车身喷涂设计进行规范和完善,提高其辨识度和安全性。
三、工程车车身喷涂设计流程1.需求调研对于工程车车身喷涂设计,首先需要对市场需求进行充分调研,了解市场上的同类产品的车身喷涂设计特点,以及用户的喜好和需求。
只有充分了解市场需求,才能进行合理的设计。
2. 设计规划在充分了解市场需求的基础上,进行合理的设计规划。
根据市场需求和用户需求进行整体设计规划,确定车身喷涂设计的整体风格和主题。
设计规划需要考虑到车身尺寸、颜色搭配、标识标识等方面,形成初步的设计方案。
3. 设计方案确定在设计规划的基础上,确定最终的设计方案。
设计方案需要考虑到施工企业的品牌形象和企业文化,同时也需要考虑到施工现场的实际环境和需求。
设计方案的确定需要经过多方沟通和讨论,确保设计方案合理和实用。
4. 生产实施设计方案确定后,进行生产实施。
生产实施需要选择合适的喷涂技术和材料,确保车身喷涂质量。
高品质汽车涂装工艺及装备关键技术研究

高品质汽车涂装工艺及装备关键技术研究发布时间:2022-08-24T01:33:57.410Z 来源:《新型城镇化》2022年17期作者:刘磊卢志业[导读] 基于传统的汽车喷涂工艺和环节,高品质的汽车涂装不仅仅局限于对高级轿车的而言,它应涵盖所有汽车车身涂装的几个要素体现:使用高性能的汽车涂料,采用可靠的自动喷涂设备及合理的工艺参数设计和控制,所获得的多涂层体系的涂膜具有高防腐性?高装饰性?中汽昌兴(洛阳)机电设备工程有限公司河南省洛阳市 471003摘要:汽车生产的主要能耗和环境控制的关键工序中,汽车涂装线是其中非常重要的一道工序,能直接决定汽车企业的制造成本情况和环保情况?通过介绍汽车涂装生产线的主要工艺手段引出涂装生产线优化与成本控制之间的因果关系,并据此针对性地提出完善汽车涂装生产线的优化方案?另外,本文就汽车装备的关键技术展开分析,希望可以给从事汽车制造的相关人员一定的技术支持?关键词:汽车涂装工艺;装备技术;技术节能1高品质涂装工艺的内涵基于传统的汽车喷涂工艺和环节,高品质的汽车涂装不仅仅局限于对高级轿车的而言,它应涵盖所有汽车车身涂装的几个要素体现:使用高性能的汽车涂料,采用可靠的自动喷涂设备及合理的工艺参数设计和控制,所获得的多涂层体系的涂膜具有高防腐性?高装饰性?汽车车身对色彩的运用十分重要,它会给人以强烈的精神感染?视觉震撼?一款汽车的不仅要具有清新流畅的外形,更要具有鲜明的色彩,从而实现完美的技术与艺术结合?在最近的十年来,业内对于汽车面漆涂装的高装饰性的要求越来越高,主要体现在高鲜映性?高闪光?高亮度,因而对金属漆的使用越来越多,不仅轿车80%以上采用金属闪光漆,而且商用车(重型卡车)驾驶室也采用金属高品质涂装的重要内容是金属漆喷涂工艺,缘于金属漆自身成分的特殊性,因此对喷涂工艺的设计要求很高?金属感光漆的喷涂技术的关键是保证铝粉的平行排列?只有涂料中铝粉的到平行排列,涂层正面反射光的量增加,才能展示出金属光泽的效果?刚涂装完毕的漆膜中铝粉排列是随机的,随着时间推移溶剂逐渐挥发使涂层体积收缩,进而促使铝粉平行排列?传统喷涂金属漆采用空气喷枪,但油漆利用率低?采用静电喷涂金属漆可以提高油漆利用率,但是由于静电的作用造成铝粉呈定向垂直排列,对光反射有损失,而且涂膜的外观不良?随着金属闪光漆专用旋杯的出现,这一问题得到解决?据相关资料介绍,采用旋杯喷涂时由于静电场和成形空气的作用涂料粒子的飞行速度达到12m/s,是铝粉的到较好的排列?在一般情况下,采用旋杯静电喷涂第一遍金属底色漆,涂膜在10μm左右,主要作用是用70%膜厚的完成对底材的遮盖;采用空气喷枪或空气静电喷枪喷涂第二遍金属底色漆,涂膜厚度厚度在3-5μm,主要作用是调整底色漆外观?由于商用车采用金属漆喷涂驾驶室的需求增长,相关企业对采用旋杯喷涂金属漆需要日益突出,以实现商用车由普通涂装向高品质涂装的转变?2汽车涂装生产线的优化方案和建议2.1涂装生产线生产节拍和生产效率的优化涂装生产线本身就是一个兼容性较强的生产线,但其通过性会受到车型大小的影响,因此在进行涂装线设计之前需要将规划中最大车型的产品数据考虑在内,甚至将其作为涂装线建设或改进的基础数据依据,因此涂装生产线生产节拍的优化方向需要进行以下三个方面的评估:1)机运以及工艺设备系统的能力是否能满足要求;2)手工操作区域的操作速度?节距是不是可以调整,应该如何调整,调整的难度如何;3)不同工序的节拍在做相应调整的时候应该如何做?2.2涂装生产线节能降耗?降低运行成本的优化改进涂装车间是四大工艺车间消耗资源?能源和成本最大的车间,若其能节能减成,对整个涂装线降低运行成本的贡献最大,所以如何改进涂装车间和涂装线一直以来都是汽车企业制造体系重点关注的方向之一,能降低涂装生产线能耗的方式有:1)改进设备工艺能降低成本;2)改进工艺技术能提升产品质量,降低返修率和报废率;3)降低颗粒控制的难度能有效帮助减少返修率,节约返修成本?3.3涂装生产线的生产物流的优化改进涂装生产线的质量控制可通过物料规划以及改善运行方式的方法实现,除此之外,物流的通道规划?周转控制和库存控制,也会直接影响到涂装的成本控制和质量控制?本论文简述了涂装物料的分类,然后通过两个比较有代表性的例子以点带面地研究了物流优化的具体方式,辅助生产线达到降低劳动强度?提高物流效率?减少质量问题?降低安全隐患的目的,提升整个生产线的生产水平和工作效率?2.3涂装生产线过程质量信息管理优化涂装生产线的基础统计工具和分析工具是各类不同质量?工艺报表,能有效帮助促进涂装生产线及相关系统的进一步完善,其中质量信息管理系统主要负责采集生产线的相关数据,若采集到的数据不准确,不完整,那么质量管理信息系统建设的再好,也没有了存在的意义?因为不完整的数据不能为生产质量以及生产效率的改进提供任何的有效支持,所以能够采集有效?完整的数据是质量信息管理系统完善的必要条件?3涂装设备关键技术分析自动喷涂机以其结构简洁?易于维护?造价相对低(相比较于喷涂机器人)的优点,在一些汽车制造厂广泛使用使用?在吸收引进自动喷涂机技术基础上,国内也开展自主研发制造自动喷涂机的工作?3.1喷涂机轨迹规划与结构设计3.1.1自动喷涂机的仿形运动商用车车身部分主要是驾驶室,重卡车型驾驶室多呈近似的方形结构。
乘用车的涂装及其工艺方法_文学艺术论文

乘用车的涂装及其工艺方法_文学艺术论文论文导读::乘用车的涂装及其工艺方法,文学艺术论文。
论文关键词:乘用车的涂装及其工艺方法现代乘用车与衣服一样,对可见部位用户的要求特别高,车身式样和涂装则是其中最重要的。
纵然这与实用性完全无关,但涂装表面外观性差,使汽车特别是现代乘用车的商品价值大大下降。
为此,生产厂家对车身的防锈、涂料的退色、调色、光泽度等非常重视,对涂装给予特别的关注。
1.现代乘用车的涂装工序现代乘用车的涂装工序一般分为三个步骤:以防锈为目的底涂、为保证面涂精度的中涂和为形成色彩和平滑涂装表面的面涂。
底漆的涂装从最早的刷漆、喷涂发展到电泳涂装,电泳涂装则由阴离子型变为涂层密实性更好的阳离子型。
目前,日本的轿车几乎完全采用阳离子涂装。
中涂和面涂一般是自动静电涂装后用手动静电涂装喷枪再进行补喷。
今后将广泛采用机器人涂装。
乘用车涂装工艺过程一般是,以油漆为原料的采购控制、原料的配料控制,然后在封闭的生产线内进行前处理工序(预清洗、脱脂、磷化和吹净),之后转到电泳涂装工序(电泳、后冲洗、烘干),再在流水线上进行连续的车身密封工序后,转到底漆涂装工序(下裙部喷漆、擦净、喷漆、通廊、流平、烘干),再转到面漆涂装工序(打磨、预留段处理、擦净、喷漆、通廊、流平、烘干),最后车身经检验工序后,转入装配车间。
车身前处理是轿车涂装生产的关键工序,包括预清洗、脱脂、磷化和吹净等内容。
按生产计划提取各种车型的车身文学艺术论文,并由双轨地面输送设备送到清洗工位,先在清洗平台上人工刷洗,再通过积放式悬挂输送机带着滑撬送至涂装车间;进入清洗处理的车身,先在20米左右长的生产线内进行化学清洗除锈,生产线上部一般均装有排气天篷罩,用于抽取清洗过程中产生的烟雾,车身在磷化处理时,行李箱和发动机罩处于打开状态,使磷化溶液能充分喷淋到金属表面,磷化生产线一般均安装在地面上,内有均匀分布在特殊结构坑道的加工槽。
清洗后车身吹干;车身应在干燥炉120℃左右的温度中干燥30分钟,车身表面吹干便可防止磷酸盐结晶,从而不致于令其影响车身的油漆质量。
汽车涂装修复工艺分析_毕业论文

汽车涂装修复工艺分析摘要汽车涂装,就像是每个人的脸一样,不能失去;也是给别人的第一映像,因此,非常的重要。
我国的汽车涂装工艺技术水平和涂装质量已与国际接轨, 在环保、节能减排和资源利用率方面尚存在一定差距, 但我国汽车涂装工艺技术产生了质的飞跃。
近20 年内新建的汽车车身塑料件涂装线, 引进了很多先进的、现代化的涂装设备及涂装工艺技术, 可称为世界一流, 尤其进入21 世纪后新建的轿车车身涂装线基本上汇集了世界各国汽车涂装领域尖端技术。
流水线生产的汽车车身几乎100% 采用喷浸结合的三元锌盐磷化处理和阴极电泳涂装工艺, 采用摆杆式, 旋转浸渍式或悬挂推杆输送链输送车身; 采用高速旋杯式自动静电喷涂往复机喷涂中涂、面漆。
进入21 世纪以来, 又被智能化的机器人杯式自动静电喷涂机所替代, 进一步提高了喷涂柔性和涂着效率; 在中途、面漆喷涂区, 烘干室和其他手工作业区采用滑橇输送机或倒置式积放输送机等地面输送系统, 能实现自由分流或合岔, 横向车转移, 上下垂直升降, 调整输送间距和积放等功能。
车身用喷漆室全部采用上供风下抽风湿式大型喷漆室, 确保在高清洁度的空间环境下进行涂装作业。
车身底板下表面喷涂车底涂料, 所有缝隙都涂密封胶, 以提高缝隙的耐蚀性, 车身的舒适性和密封性。
随着汽车市场竞争的不断加剧和汽车制造、修理技术的日益更新,基础涂装工艺已经引起了汽车制造商和维修服务人员的高度重视。
种类繁多、规格齐全和功能良好的涂装材料,无疑会进一步促进维修质量的提高,促进汽车使用寿命的延长。
关键词:涂装发展;涂装管理;电泳技术;注意三废第一章涂料的应用现状与发展前景1.粉末涂料的现状与发展1.1粉末涂料的应用领域1.1.1粉末涂料地理区域上的差异在不同的地区使用不同类型的粉末涂料,其在地理区域上的差异是十分明显的,如粉末涂料在全球有欧洲、美国和日本3个主要市场,但由于历史原因和原材料利用方面的因素,这些地区都发展了各自不同的产品体系。
车身涂装工艺设计研究(九院盖东辉)0902

乘用车车身涂装工艺规划研究盖东辉马汝成(机械工业第九设计研究院130011)[摘要]本文通过分析论述大型乘用车车身涂装车间的工艺规划设计理念,对大型多层乘用车车身涂装车间工艺布置、工艺设备、设施的选择应用以及设计思路等进行了研究探讨。
[关键词]工艺布置、分析与优化大型乘用车车身涂装车间代表了汽车涂装技术的最高水平,它通常都采用多层立体化、区域化工艺布置方式,工艺规划设计难度大,工艺布置复杂。
但是,可以充分的利用空间、有效的规划使用工艺面积和节省占地面积。
本文结合实际项目设计体会对大型多层乘用车车身涂装车间的工艺规划设计理念进行一些研究和探讨。
1工艺规划的关键点1.1 工艺布置区域化、立体化、洁净化区域化、立体化布置是把同类型、同洁净度要求的涂装设备布置在车间同一区域和楼层。
目的是按不同的洁净度分区。
通常涂装车间划分为一般洁净区、洁净区、烘干区及噪声区等。
一般洁净区布置密封、车底喷涂线及手工操作的检查、打磨、修整、返修等易产生尘埃颗粒的工位,并与各种辅助设备和洁净度要求较低的各类库房、物流输送频繁的各种材料存放地,在多层厂房底层布置。
洁净度要求高的喷漆设备为洁净区,在车间二层布置。
烘干室及各排空线在车间二层或三层布置,防止热污染。
空调机房噪声大布置在车间第三层或顶层。
喷漆排风机房和烟囱布置在喷漆室附近的侧面或端部区域。
为了防止脏物、噪声和热的污染,采用金属轻质密封隔墙将喷漆区、烘干区、空调机房封闭,空调机房设在顶层时用楼板封闭,用砖墙将喷漆排风机房、喷漆室下部的水洗系统和废漆处理设备封闭。
通过分区和分层工艺布置,实现了涂装车间区域化、立体化。
这样能充分利用使用面积,节省占地面积。
通过区域化、立体化布置,并满足不同的洁净度要求,实现全车间的洁净化。
1.2 车间物流顺畅、短捷大型多层乘用车车身涂装车间生产物流输送立体交叉,涉及机械化类型较多。
通常大型乘用车车身涂装车间内的机械化输送距离长达6-7公里,车身由涂装车间入口到涂装车间出口通常运行时间为基本型乘用车需要6.5-7小时,双色乘用车或多功能车(MPV)和运动型多用途车(SUV)等需要9-9.5小时。
- 1、下载文档前请自行甄别文档内容的完整性,平台不提供额外的编辑、内容补充、找答案等附加服务。
- 2、"仅部分预览"的文档,不可在线预览部分如存在完整性等问题,可反馈申请退款(可完整预览的文档不适用该条件!)。
- 3、如文档侵犯您的权益,请联系客服反馈,我们会尽快为您处理(人工客服工作时间:9:00-18:30)。
乘用车车身涂装工艺规划研究盖东辉马汝成 <机械工业第九设计研究院130011)[摘要]本文通过分析论述大型乘用车车身涂装车间的工艺规划设计理念,对大型多层乘用车车身涂装车间工艺布置、工艺设备、设施的选择应用以及设计思路等进行了研究探讨。
[关键词]工艺布置、分析与优化大型乘用车车身涂装车间代表了汽车涂装技术的最高水平,它通常都采用多层立体化、区域化工艺布置方式,工艺规划设计难度大,工艺布置复杂。
但是,可以充分的利用空间、有效的规划使用工艺面积和节省占地面积。
本文结合实际工程设计体会对大型多层乘用车车身涂装车间的工艺规划设计理念进行一些研究和探讨。
1工艺规划的关键点1.1 工艺布置区域化、立体化、洁净化区域化、立体化布置是把同类型、同洁净度要求的涂装设备布置在车间同一区域和楼层。
目的是按不同的洁净度分区。
通常涂装车间划分为一般洁净区、洁净区、烘干区及噪声区等。
一般洁净区布置密封、车底喷涂线及手工操作的检查、打磨、修整、返修等易产生尘埃颗粒的工位,并与各种辅助设备和洁净度要求较低的各类库房、物流输送频繁的各种材料存放地,在多层厂房底层布置。
洁净度要求高的喷漆设备为洁净区,在车间二层布置。
烘干室及各排空线在车间二层或三层布置,防止热污染。
空调机房噪声大布置在车间第三层或顶层。
喷漆排风机房和烟囱布置在喷漆室附近的侧面或端部区域。
为了防止脏物、噪声和热的污染,采用金属轻质密封隔墙将喷漆区、烘干区、空调机房封闭,空调机房设在顶层时用楼板封闭,用砖墙将喷漆排风机房、喷漆室下部的水洗系统和废漆处理设备封闭。
通过分区和分层工艺布置,实现了涂装车间区域化、立体化。
这样能充分利用使用面积,节省占地面积。
通过区域化、立体化布置,并满足不同的洁净度要求,实现全车间的洁净化。
1.2车间物流顺畅、短捷大型多层乘用车车身涂装车间生产物流输送立体交叉,涉及机械化类型较多。
通常大型乘用车车身涂装车间内的机械化输送距离长达6-7公里,车身由涂装车间入口到涂装车间出口通常运行时间为基本型乘用车需要6.5-7小时,双色乘用车或多功能车<MPV)和运动型多用途车<SUV)等需要9-9.5小时。
车间物流需经相关专业配合多次优化完成。
涂装车间物流要做到各种物流便捷顺畅,涂装产品、涂装材料、设备维修、废物输送等物流不能相互干涉;根据生产组织需要有相应的工序间产品排空、缓冲、编组输送线;不合格产品可随时就近下线,返回打磨返修;尽量缩短产品的物流路程。
切忌按涂装工序罗列生产物流,忽略其他物料运输。
1.3 柔性生产工艺、产品多元化涂装车间能够多品种混流生产,不仅需要合理确定通过的产品最大外形尺寸,还要考虑机械化输送能否满足不同平台产品输送要求,能否满足不同类型产品的喷漆质量。
根据不同产品的不同涂装工艺要求,实现涂装车间生产产品多元化、工艺柔性化。
1.4环保节能型厂房和设备全密闭厂房的涂装车间应采用封闭、隔热、减振、降噪等方法,保护车间工作环境。
厂房密闭和保温至关重要,在保证室内环境洁净的同时,要采取节能建筑结构和措施。
选择的涂装设备应可靠节能,特别是喷漆室和烘干室的结构形式的确定,将直接影响车间能耗。
充分考虑前处理和电泳设备水的循环使用及节水措施,烘干室的烟气热回收及余热再利用等。
1.5合理确定工艺基础参数工艺规划设计需要合理确定各类设备设计参数,如车身质量、表面积等,由于涂装产品向多元化发展,应综合考虑设计确定值。
列表说明如表1。
表1 工艺基础参数确定汇总表2 工艺规划设计分析2.1 区域化、立体化、洁净化的工艺规划设计在工艺规划设计时应考虑完整、全面,符合实际生产情况。
对于特大型工程,应事先根据产品的工艺流程,制定涂装车间的物流图、功能图,然后绘制工艺布置图。
物流图和功能图见图1、图2。
图1 乘用车车身涂装车间物流图图2乘用车车身涂装车间功能图物流图、功能图表示涂装车间生产过程和布置情况。
区域化、立体化布置很容易实现涂装车间洁净分区。
经验证明,涂装车间保持洁净度要求,可降低返修率达5%以上。
因此,区域化、立体化布置是降低涂装成本的有效手段。
新型涂装工艺布置思路:在实现区域化、立体化布置的同时,使电泳和密封线、中涂和面漆线分别布置在两个独立的厂房中,两个厂房分平行式和垂直式两种涂装工艺布置方式。
根据能耗和洁净不同要求分别考虑,以实现节能环保,达到需要洁净的区域更加洁净。
布置简图见图3。
图3新型涂装工艺布置简图2.2 可实施性思路工艺布置方案必须考虑下列因素:各种设备和设施齐全,但是,功能不过剩。
方便施工建设和安装维修,使各种施工周期尽量短。
在消防、环保、安全、卫生等方面符合国家法规。
要全面考虑车间物流,初步确定各种设备安装时进入车间的入口或位置;细分各种物流通道,包括消防、备件、材料、维修及人员疏散等通道;考虑各层物流、人流楼梯、电梯、设备安装孔洞等运输方式。
并且要充分利用通道上方的有效空间,实施公用管线布置。
使工艺方案具有可实施性,保证满足正常生产和生产管理。
2.3 注重环保,使工作环境人性化乘用车车身涂装车间厂房为密闭厂房,其中使用对人体有害的化学药品较多,各类设备会产生噪声和热量,对工作环境造成不良影响。
为了避免工人工作环境变得恶劣,保证工人正常工作和质量稳定,必须注重涂装车间工作环境人性化。
将烘干区布置在车间上层,将空调及排风风机布置在车间隔音的空调机房层,消除不良环境影响。
全车间通风换气,有化学药品的房间进行单独全室通风,改善房间空气质量。
设置应急设施对被化学品伤害人员进行紧急救治,夏季对操作工位、休息室送制冷后的新鲜风,设置更衣淋浴、卫生间、餐厅等,通过工艺规划设计实现工作环境人性化。
2.4涂装生产工艺柔性化,适应产品多元化生产为能实现多平台多品种混流生产,有些车型需套色及大返修,其套色喷涂工作量和大返修车身喷涂工作量较小,其喷涂位置变化较大,不适合返回机器人面漆线进行喷涂,可布置一条实用的综合喷漆线,完成该项工作。
有些高档乘用车采用四涂层珠光漆,四涂层车身一般只占生产纲领的一部分,无需增加满足四涂层的喷漆线,可利用面漆线或中涂线循环,或利用综合喷漆线,合理安排底色涂层打磨及面漆线前编组线路,实现四涂层工艺。
为满足定单化生产需要,在调漆间布置、喷涂机器人配置及工序间缓冲存放等几个方面要考虑小漆种工艺规划设计。
2.5主要工艺设备选型与节能环保涂装车间的各种工艺设备、辅助设备和公用设备的选型,要环保、节能、经济、适用,功能不应过剩。
2.5.1 前处理、电泳设备前处理、电泳设备的喷淋室、工作液槽、转移备槽及辅助设施分三层布置,这种布置形式设备规整,工作液槽与转移槽间倒槽方便,但相应设备投入较大。
根据实际情也可以采用喷淋室、工作液槽双层布置,转移槽及辅助设施合理布置在主体设备旁边,这种结构能节省材料,降低设备造价。
输送设备不同前处理和电泳设备的结构也不同。
采用推杆悬链或摩擦链输送机时,前处理、电泳室体上部按机械化轨迹进行仿形布置,通过采用大“C”型吊具及仿形室体设计能够将输送悬链与前处理、电泳产生的各种腐蚀性水汽隔离,有利于保护输送悬链系统。
前处理、电泳机械化装置采用摆杆输送机、Rodip输送机、多功能穿梭机、倒挂升降输送机,传动<链)驱动机构布置在浸槽两侧,室体顶部采用斜板结构将凝结的水滴导流,防止水滴、油滴落在车身及槽液里,确保涂装质量,明显缩短设备长度。
其中:Rodip 输送机、多功能穿梭机是滚浸式输送机,采用全旋转浸渍输送技术,使车身入槽后旋转180°或360°底板朝上反向前进,能大幅度缩短设备长度,节约投资;节省电能、化学药品和后冲洗水;显著提高产品涂装质量。
多功能穿梭机更适合柔性化生产。
2.5.2喷漆室喷漆室主要为文式和水旋式结构形式。
采用文式喷漆室,调输漆间位置及输漆管路走向规划较方便,并且容易布置在喷漆室下部或近旁。
布置方式为直线型和U型。
采用U型布置距离排风烟囱近,排风机布置方便,投资与运行费用低,适合水性漆的面漆喷漆室布置。
近年来多采用机器人喷漆,内置式机器人占用空间大,喷漆室能源浪费大。
外置式或壁挂式机器人是选用趋势,它使喷漆室宽度降至3.8m或更窄,大量减少喷漆送风量,节省能源和降低CO2排出量。
以前高速旋杯的出漆量为300~600ml/min,目前出漆量最大已达1000ml/min,使机器人数量减少,有些工位有减半的趋势。
文氏喷漆室的漆泥处理装置布置在下部,集中管理较方便。
水旋式喷漆室的漆泥处理集中布置在喷漆室附近的漆泥处理间内,大型多层涂装车间采用水旋式喷漆室正逐渐减少。
机械化运输设备采用滑橇输送机、反向积放链或摩擦链输送机等。
也有带托架的独立板链输送系统,其前后需要工件转载。
为喷漆室供风的空调机布置在喷漆室上方或侧面。
空调机布置在喷漆室上方,厂房需要加高,高层建筑超过24m会提高消防等级及增加投资。
因此,厂房高度应该控制在24m 以下。
将空调机布置在喷漆室侧面也是一种布置方式。
2.5.3烘干室烘干室尽量集中布置,便于动能集中供应和环境隔热。
烘干室常采用了Π型结构,也可采用Γ型结构,将换热系统放在烘干室顶部楼板以上,在烘干室下面可布置其它操作工序。
但是,电泳烘干室工作温度较高,烘干室形式应该采用传统的Π型。
胶烘干室可以采用直通型结构。
U型桥式烘干室便于集中布置,节能,省投资,管理方便。
Π型和Γ型烘干室的输送系统为带垂直升降装置的输送机,U型桥式烘干室的输送系统为反向积放链、摩擦链或反向单轨输送机<IMC)。
烘干室的废气处理装置可选用蓄热式热力直燃系统<RTO)或回收式热力直燃系统<TAR),烘干烟气中的热量应回收利用。
以前烘干室换热大多采用集中供热系统<TAR),由一套焚烧炉集中供热,使排放烟气温度达到160℃以下;最近采用蓄热式热力直燃系统<RTO)集中处理烘干废气也在逐渐增多。
国产烘干室排放的烟气温度大于200℃,应该回收利用余热。
可将排放的烟气收集,通过新风换热装置对新鲜空气加热后排放。
这样温度可降至160℃以下,能明显降低CO2排出量。
2.5.4电控设置先进的电控是现代化大型多层乘用车车身涂装车间必要的组成部分,电控通常按下几个方面考虑。
∙识别系统采用耐高温、耐化学腐蚀的数据载体。
∙用现场总线连接现场传感器、执行器等电气设备。
∙用带人机界面的PLC控制涂装设备。
∙用工业以太网连接各PLC,设中央控制室,通过网络服务器与办公自动化系统及生产管理ERP系统连接。
∙适量设置大屏幕显示装置,及时传达生产信息。
∙重点生产区域及重要车间物流门设摄像监控系统。
通过这些电控措施便于生产管理,提高生产效率,降低单车能耗和材料消耗等。
2.6工艺优化目前我国生产的乘用车产品主要源于美系、欧系、日系和韩系,以及国内自主系列产品。