工业控制网络发展
工业控制网络知识点总结

工业控制网络知识点总结一、工业控制网络的概念工业控制网络是指用于工业自动化领域的数据通信系统,其目的是实现对生产设备、工艺过程和生产信息的监控和控制。
工控网络主要包括传感器、执行器、PLC、DCS、SCADA系统等组成部分。
工控网络的设计目标是提高生产效率、降低生产成本和提高生产安全性。
二、工业控制网络的特点1. 实时性:工控网络需要能够实时响应生产过程的变化,及时更新数据和控制设备。
2. 可靠性:工控网络对通信的可靠性要求非常高,因为生产过程中可能会遇到各种干扰和故障,需要能够确保数据传输的准确性和完整性。
3. 安全性:工业控制网络需要能够防范各种网络攻击和恶意操作,保证生产过程的安全性和稳定性。
4. 实时性:工控网络需要能够实时响应生产过程的变化,及时更新数据和控制设备。
5. 可扩展性:工控网络需要能够根据生产需求进行扩展和升级,灵活适应不同的生产环境和设备组合。
三、工业控制网络的组成部分1. 传感器和执行器:传感器用于采集环境参数,例如温度、压力、流量等;执行器用于对生产设备进行控制,例如电动阀门、马达、启动器等。
2. PLC(可编程逻辑控制器):PLC是工控网络的核心设备,用于实现对生产过程的自动控制。
PLC能够根据预先编制的程序对输入信号进行处理,并输出控制指令,实现对执行器的控制。
3. DCS(分布式控制系统):DCS是用于对生产过程进行集中监控和控制的系统,通常包括多个控制节点和界面站,能够实现对整个生产线的远程控制。
4. SCADA系统:SCADA系统是用于对生产现场进行实时监控和数据采集的系统,能够通过图形界面对生产现场进行动态显示和实时数据查询。
四、工业控制网络的通信协议工业控制网络使用的通信协议通常包括有线和无线两种类型,其中有线协议主要用于固定式设备的数据通信,无线协议主要用于移动设备和无线传感器网络的数据通信。
1. 有线通信协议(1)Profibus:Profibus是一种用于工业自动化领域的现场总线通信协议,适用于实时数据传输和设备控制。
工业自动化中的网络控制技术
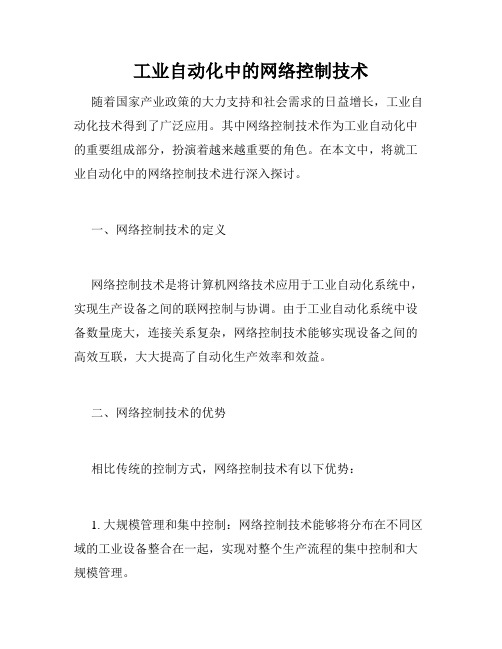
工业自动化中的网络控制技术随着国家产业政策的大力支持和社会需求的日益增长,工业自动化技术得到了广泛应用。
其中网络控制技术作为工业自动化中的重要组成部分,扮演着越来越重要的角色。
在本文中,将就工业自动化中的网络控制技术进行深入探讨。
一、网络控制技术的定义网络控制技术是将计算机网络技术应用于工业自动化系统中,实现生产设备之间的联网控制与协调。
由于工业自动化系统中设备数量庞大,连接关系复杂,网络控制技术能够实现设备之间的高效互联,大大提高了自动化生产效率和效益。
二、网络控制技术的优势相比传统的控制方式,网络控制技术有以下优势:1. 大规模管理和集中控制:网络控制技术能够将分布在不同区域的工业设备整合在一起,实现对整个生产流程的集中控制和大规模管理。
2. 实时监测和反馈:网络控制技术能够实时监测设备的状态,及时反馈异常情况,从而快速响应和解决问题,提高生产效率和质量。
3. 可靠性高:网络控制技术支持数据冗余备份和故障恢复机制,即使某个节点出现故障,也不会对整个系统造成太大的影响,保证生产系统的连续性和稳定性。
4. 节省成本:网络控制技术能够实现设备之间的无缝连接和交互,避免了设备之间的重复工作和资源浪费,从而降低生产成本,提高企业盈利能力。
三、网络控制技术的应用目前,网络控制技术已经广泛应用于各行各业的生产领域,如下:1. 工业生产:网络控制技术对工业生产具有重大意义。
它可以实时监测和控制生产设备的各项参数,灵活调整生产流程,提高生产效率和质量,降低生产成本。
2. 物流管理:网络控制技术可以实现物流设备和运输工具之间的互联互通,及时掌握物流信息,优化物流路线和运输方式,降低物流成本。
3. 能源管理:网络控制技术可以实时监控能源设备的能耗情况,研究出合理的用能方案,降低能源的浪费和损耗,为可持续发展做出贡献。
4. 环境管理:网络控制技术可以监测和控制环境污染源的排放,及时预警和响应环境突发事件,保护环境资源,提高环境质量。
工业控制网络技术基础
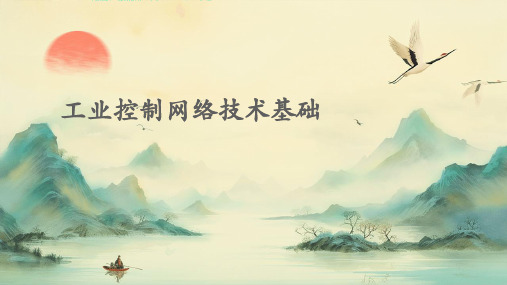
工业控制网络技术的发展历程
早期的工业控制网络技术主要基于模 拟信号传输,随着技术的发展,逐渐 演变为数字信号传输。
近年来,随着物联网、云计算和大数 据等技术的快速发展,工业控制网络 技术也得到了不断升级和完善。
工业控制网络技术的应用场景
工业控制网络技术广泛应用于能源、化工、制造、交通等领域的自动化生产过程中。 在智能制造、智能物流、智能监控等领域,工业控制网络技术也发挥着重要作用。
工业控制网络技术基础
• 引言 • 工业控制网络技术基础知识 • 工业控制网络技术实现方式 • 工业控制网络安全防护 • 工业控制网络技术的发展趋势
01
引言
工业控制网络技术的定义
01
工业控制网络技术是指用于连接 和控制工业生产过程中的各种设 备、传感器和执行器的网络技术 。
02
它通过实时、可靠的数据传输和 控制系统,实现了对工业过程的 精确监测和控制,提高了生产效 率和安全性。
工业控制网络的设备
01
02
03
网络交换机
用于连接各个设备和系统, 实现数据传输和通信。
网关
用于实现不同协议之间的 转换,以实现设备和系统 之间的互操作性。
服务器和客户端
用于存储、处理和监控数 据,实现远程管理和控制。
03
工业控制网络技术实现方式
现场总线技术
现场总线技术是工业控制网络 中的重要组成部分,它是一种 用于连接现场设备与控制系统
工业控制网络的通信协议
Modbus协议
一种串行通信协议,用于连接工业电子设备。
EtherNet/IP协议
一种工业以太网协议,支持实时数据传输和设备 管理。
ABCD
Profinet协议
工业以太网在工业控制网络中的应用与发展综述

较 大影 响力的现场总线主 要_ 如下 5种 : 仃 ① F n ain il b s 金 会现 场 总 线 u d t F ed u 基 o ( FF总 线 ) ② P o i u 过 程 现 场 总 线 。 。 r fb s
③ CAN 总 线 。 ④ L0 nW O k 总 线 。 ⑤ r
钺 _
__ Leabharlann T e p p r n rd c s h a pc t n cu lis o te h a e i o ue t e p la i a t a t f h t i o ie f l u o to n t a d n utilE h re i te fe i d s c n rl e n i s r t en t n h id eb d a l
干汽车 内部测 孑 执行部 件之 间的数据通 信协议 ,现 已逐步发展剁机械制造 、数控 机床 、变电站检 测设 备的监控 与应用 卜。 闩前阁内外工 业控制 络还没有形成 统 一的格局 ,协议 多种 多样 ,埘下用户而
言 ,各 种设 备很 难 实现 互 联 互 通 , 刚络 适 接较为 复杂 ,这 尢疑 埘工、 络的应用及
Po n t 8 rf e 共 种现场总线的 1 种类型。② i 0 2 工业 以太 网技 术分析
I 6 0 6包括的 4种现场总线 国际标 准 : EC 2 2 AS Acu trS n o itrae i( t ao e s r n e c )执 行 f 2 1工业以太叫发展现状 . 工 业 以 1 } 术是 普 通 以 太 技 术 仟 人网 支 工 业控 制 络 中的 延伸 。所 谓工 业以太 网 , 是 指 其 在 技 术 上 与 商 用 以 太
维普资讯
网络 中的应用与发展综述
自学工业控制网络之路1.1-工业控制系统发展历程CCSDCSFCS

⾃学⼯业控制⽹络之路1.1-⼯业控制系统发展历程CCSDCSFCS ⾃学⼯业控制⽹络之路1.1-⼯业控制系统发展历程CCS DCS FCS⼯业控制系统是对诸如图像、语⾳信号等⼤数据量、⾼速率传输的要求,⼜催⽣了当前在商业领域风靡的以太⽹与控制⽹络的结合。
这股⼯业控制系统⽹络化浪潮⼜将诸如嵌⼊式技术、多标准⼯业控制⽹络互联、⽆线技术等多种当今流⾏技术融合进来,从⽽拓展了⼯业控制领域的发展空间,带来新的发展机遇。
随着计算机技术、通信技术和控制技术的发展,传统的控制领域正经历着⼀场前所未有的变⾰,开始向⽹络化⽅向发展。
1. ⼯业控制系统发展历程控制系统的结构从最初的CCS(计算机集中控制系统),到第⼆代的DCS(分散控制系统),发展到现在流⾏的FCS(现场总线控制系统)。
2. DCS分散控制系统/分布式控制系统DCS是分布式控制系统的英⽂缩写(Distributed Control System),在国内⾃控⾏业⼜称之为集散控制系统。
是相对于集中式控制系统⽽⾔的⼀种新型计算机控制系统,它是在集中式控制系统CCS的基础上发展、演变⽽来的。
DCS它是⼀个由过程控制级和过程监控级组成的以通信⽹络为纽带的多级计算机系统,综合了计算机,通信、显⽰和控制等4C技术,其基本思想是分散控制、集中操作、分级管理、配置灵活以及组态⽅便。
2.1 DCS 发展历程第⼀阶段 1975-1980年,在这个时期集散控制系统的技术特点表现为:采⽤微处理器为基础的控制单元,实现分散控制,有各种各样的算法,通过组态独⽴完成回路控制,具有⾃诊断功能采⽤带CRT显⽰器的操作站与过程单元分离,实现集中监视,集中操作采⽤较先进的冗余通信系统第⼆阶段 1980—1985,在这个时期集散控制系统的技术特点表现为:微处理器的位数提⾼,CRT显⽰器的分辨率提⾼强化的模块化系统强化了系统信息管理,加强通信功能第三阶段 1985年以后,集散系统进⼊第三代,其技术特点表现为:采⽤开放系统管理操作站采⽤32位微处理器采⽤实时多⽤户多任务的操作系统进⼊九⼗年代以后,计算机技术突飞猛进,更多新的技术被应⽤到了DCS之中。
工业控制计算机网络技术发展与应用
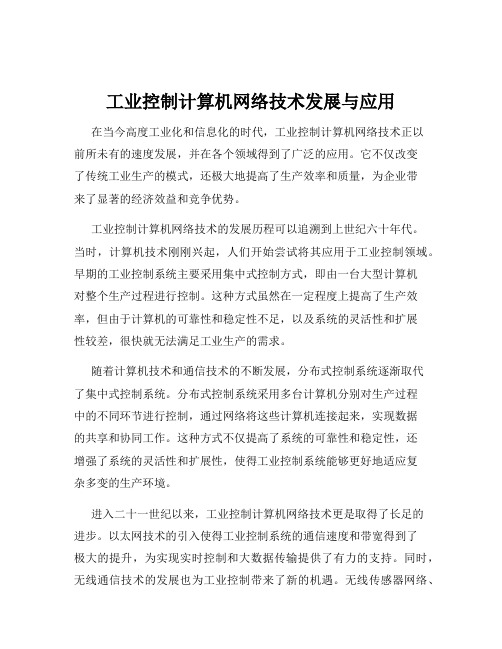
工业控制计算机网络技术发展与应用在当今高度工业化和信息化的时代,工业控制计算机网络技术正以前所未有的速度发展,并在各个领域得到了广泛的应用。
它不仅改变了传统工业生产的模式,还极大地提高了生产效率和质量,为企业带来了显著的经济效益和竞争优势。
工业控制计算机网络技术的发展历程可以追溯到上世纪六十年代。
当时,计算机技术刚刚兴起,人们开始尝试将其应用于工业控制领域。
早期的工业控制系统主要采用集中式控制方式,即由一台大型计算机对整个生产过程进行控制。
这种方式虽然在一定程度上提高了生产效率,但由于计算机的可靠性和稳定性不足,以及系统的灵活性和扩展性较差,很快就无法满足工业生产的需求。
随着计算机技术和通信技术的不断发展,分布式控制系统逐渐取代了集中式控制系统。
分布式控制系统采用多台计算机分别对生产过程中的不同环节进行控制,通过网络将这些计算机连接起来,实现数据的共享和协同工作。
这种方式不仅提高了系统的可靠性和稳定性,还增强了系统的灵活性和扩展性,使得工业控制系统能够更好地适应复杂多变的生产环境。
进入二十一世纪以来,工业控制计算机网络技术更是取得了长足的进步。
以太网技术的引入使得工业控制系统的通信速度和带宽得到了极大的提升,为实现实时控制和大数据传输提供了有力的支持。
同时,无线通信技术的发展也为工业控制带来了新的机遇。
无线传感器网络、蓝牙技术和 WiFi 技术等在工业现场的应用,使得工业控制系统的布线更加简洁,安装和维护更加方便,同时也提高了系统的灵活性和可移动性。
在工业控制计算机网络技术的发展过程中,相关的标准和协议也不断完善。
OPC(OLE for Process Control)技术的出现,实现了不同厂家设备之间的数据交换和互操作,大大降低了系统集成的难度和成本。
此外,IEC 61158、IEC 61784 等国际标准的制定,为工业控制网络的通信协议和接口规范提供了统一的标准,促进了工业控制网络技术的国际化和规范化发展。
工业控制网络发展历程

工业控制网络发展历程工业控制网络是指用于工业自动化过程中的数据通信和控制的网络。
随着信息技术的不断发展,工业控制网络也在不断进步和完善。
本文将从最早的电报系统开始介绍工业控制网络的发展历程。
工业控制网络的发展可以追溯到19世纪末的电报系统。
当时工业生产的数据传输主要依靠电报线路传输,通过电报机发送和接收信息,来实现远程控制。
但由于当时通信技术的限制,电报系统的速度较慢,只能传输简单的文本信息。
到了20世纪,随着电子技术的不断发展,出现了更先进的数据传输手段。
最早的工业控制网络可以追溯到20世纪50年代的模拟信号传输系统。
该系统使用模拟信号传输数据,通过模拟调制和解调来实现数据的传输和控制。
这种模拟信号传输系统具有速度快、传输距离远的优点,但受到了传输质量不稳定、容易受到干扰等问题的限制。
20世纪60年代至70年代,随着半导体技术和计算机技术的发展,数字信号传输技术开始应用于工业控制网络中。
这种数字信号传输系统使用二进制数字信号来传输数据,通信速度更快,传输质量更稳定。
并且通过将计算机与控制设备相连接,可以实现更复杂的数据处理和控制操作。
到了20世纪90年代,以太网技术开始应用于工业控制网络中。
以太网不仅具有传输速度快、容量大的特点,还可以支持多种协议和多种网络设备的连接。
这使得工业控制网络具有了更高的灵活性和可扩展性。
近年来,工业控制网络的发展又呈现出一些新的特点。
首先是无线通信技术的应用。
通过无线通信技术,工业控制网络可以实现更广范围的通信和控制,同时也方便了工业设备的布置和维护。
其次是工业物联网的兴起。
工业物联网通过将传感器、执行器和网络技术结合起来,实现对工业设备的实时监测和控制。
这使得工业控制网络更加智能化和自动化。
总之,工业控制网络的发展经历了从模拟信号传输到数字信号传输,再到以太网和无线通信技术的应用。
随着信息技术的不断进步,工业控制网络的功能和性能也不断提升,为工业自动化提供了强有力的支撑。
工业控制软件发展现状

工业控制软件发展现状工业控制软件是指用于自动化控制和监测工业过程的软件系统。
随着信息技术的发展和工业自动化的不断推进,工业控制软件也在不断发展。
目前,工业控制软件的发展现状主要表现在以下几个方面:1. 软件功能不断增强:工业控制软件的功能越来越强大和多样化。
传统的工业控制软件主要提供基本的监控和控制功能,如数据采集、报警处理、过程调节等。
而现在的工业控制软件已经具备了更高级的功能,如远程监控、智能诊断、数据分析和预测等。
这些功能的增强使得工业控制软件更加灵活和智能化。
2. 软件平台的集成化:为了满足工业控制系统的整体化需求,工业控制软件开始向平台化方向发展。
这意味着不同的软件功能将集成到一个统一的软件平台中,以便于系统的运行和管理。
这种集成化的软件平台可以提高系统的稳定性和可靠性,并提供更好的用户体验。
3. 软件与硬件的结合:工业控制软件与硬件设备的结合也是一个发展趋势。
随着物联网技术的快速发展,工业设备和控制系统之间的连接越来越紧密。
工业控制软件不仅需要与传感器、执行器等硬件设备进行通信,还需要能够与云端系统和其他软件进行数据交互和协同工作。
4. 安全性的提升:随着工业控制系统的网络化和智能化程度的提高,系统安全性成为一个重要的关注点。
工业控制软件的开发者和用户都需要加强对系统的安全保护措施,以防止潜在的攻击和破坏。
因此,工业控制软件的发展也要求具备更高的安全性和防护机制。
综上所述,工业控制软件在功能增强、平台集成化、软硬件结合和安全性提升等方面都呈现出不断发展的趋势。
这些发展趋势将进一步推动工业控制软件的创新和应用,为工业自动化带来更大的效益和变革。
- 1、下载文档前请自行甄别文档内容的完整性,平台不提供额外的编辑、内容补充、找答案等附加服务。
- 2、"仅部分预览"的文档,不可在线预览部分如存在完整性等问题,可反馈申请退款(可完整预览的文档不适用该条件!)。
- 3、如文档侵犯您的权益,请联系客服反馈,我们会尽快为您处理(人工客服工作时间:9:00-18:30)。
工业控制网络的发展初探摘要:工业自动化和信息技术的发展,使整个社会生产已经向自动控制、智能控制上转型。
作为21世纪工业生产的一个重要标志,工业控制网络逐渐应用于工业生产的各个方面。
工业控制网络既包括底部设备层的传感器,检测器等器件,也包括终端管理层的办公自动化操作系统,还包括串联起整个系统的现场总线技术。
工业控制网络在工业通信及先进制造领域起到关键性作用。
关键词:工业控制网络;现场总线;发展趋势0.引言随着计算机技术、网络技术、控制技术以及现场总线技术的迅速发展,嵌入式微处理器的广泛应用,国际工作研究方向逐渐从重工业、单一化转变为微电子、多元化。
自动化技术作为其中的一项重要内容,在工业控制上逐渐显现出了它的优势。
本文主要通过对工业控制网络的结构和现场总线技术的描述,来探究未来工业控制网络结构的发展方向。
1、传统工业控制网络结构从总体结构上来讲,传统企业网络可分为三个层次:管理层、监控层和现场设备层。
其结构示意图如下所示:图一传统工业控制网络●管理层。
主要是办公自动化系统,同时从监控层提取有关生产数据用于制定综合管理决策。
管理层一般使用通用以太网,方便操作,并可连入外部网络。
●监控层。
从现场设备中获取数据,完成各种控制、运行参数的监测、报警和趋势分析等功能,另外还包括控制组态的设计和安装。
监控层的功能一般由上位计算机完成,一方面,它通过扩展槽中网络接口板与现场总线相连,协调网络节点之间的数据通信;另一方面,通过专门的现场总线接口(转换器)实现现场总线网段与以太网段的连接。
其关键技术是以太网与底层现场设备网络间的接口,主要负责现场总线协议与以太网协议的转换,保证数据包的正确解释和传输。
监控层除上述功能外,还为实现先进控制利远程操作优化提供支撑环境。
●设备层。
现场设备以网络节点的形式挂接在现场总线网络上,依照现场总线的协议标准,设备采用功能块的结构,通过组态设汁,完成数据采集、a/d转换、数字滤波、温度压力补偿、pid控制等各种功能;此外,通过智能转换器对传统检测仪表电流电压进行数字转换和补偿。
2、现场总线技术现场总线技术的出现,打破了工业控制系统原有的信息孤岛的僵局,真正实现了网络化的控制系统,为自动化系统与其他信息系统的沟通创造了条件。
同时,由于各种现场总线技术的发展和竞争、各种计算机主流技术在工业控制领域的渗透和应用、以及自动化技术发展的延续性和继承性,工业控制系统必将呈现多总线共存、多种系统集成和多种技术集成的局面。
2.1每种现场总线形成了其特定的应用领域。
各种现场总线代表不同公司多年的研发投资和市场利益,不同总线技术的侧重面不同,各有特色,不存在能完全适应所有应用领域的现场总线。
据美国arc公司的市场调查,世界市场对各种fcs需求的实际份额为:过程自动化15%,主要采用ff、profibus-pa和worldfip;医药领域18%,主要采用ff、profibus-pa和worldfip;加工制造18%,主要采用profibus-dp和cc-link;交通运输15%,主要采用profibus-dp、can和devicenet;航空和国防34%,主要采用profibus-fms、lon、devicenet和controlnet;其它,如,农业主要采用p-net、can、profibus-pa/dp、devicene和controlnet, 楼宇主要采用lon、profibus-fms和devicenet。
由此可见,占有市场80%的现场总线将只有六七种,且其应用领域比较明确,某些总线能跨越多种应用领域,如profibus。
在过程控制领域以ff、profibus和worldfip为主,ff的市场占有率以较快的速度增长。
2.2 ethernet在工业应用领域异军突起。
ethernet在没有任何标准化组织支持的情况下,正在工业自动化和过程控制市场上迅速增长,成为新的热点。
有关专家预言,ethernet不仅可以成为工业高层网络上的通信系统,也可以上下贯通直插到底,与现场仪表相连。
采用ethernet作为自动化的骨干网,具有技术成熟,与办公自动化的无缝集成和与internet无缝集成等优点,颇具吸引力。
只是,目前技术尚未成熟,如数据冲突、安全性等还没有很好的解决方案。
2.3无线现场总线成为新亮点。
针对许多工业环境及过程控制环境下的对象,如移动对象或旋转设备上的传感器,手持的数据采集设备等,远距离的单设备、传感器、执行器等,临时安装的器件,仅通过有线的物理介质连接是较难或甚至无法实现的,在这种情况下就需要无线技术和现场总线的结合方案。
另外,随着工业控制对象类型的增加,传输的数据不仅是用于控制的数字量,还有包括音频、视频的多媒体数据。
同时,第三代无线通信技术的发展,如wap、wml、bluetooth等,为工业自动化网络与无线局域网联接提供了技术支持。
目前,已经有许多无线现场总线的实现方案被提出和研制,如r-fieldbus(high performance wireless fieldbus in industrial related multimedia environment),olchfa(open low-cost time-critical wireless fieldbus architecture)等。
2.4 fcs与dcs集成是现阶段的需要。
尽管现场总线技术具有很多优点而倍受欢迎,但是用户并不希望对他们现有的控制系统做大的改动。
目前,在现场总线的发展初期,大多数用户更倾向于对现有控制系统进行逐步的增添和替换;而且dcs系统及其仪表的消失或完全被取代,就费用或人力而言也都是不合理的。
另外,现场总线并不是在所有的控制场合下都能够发挥其优点,如简单的小规模数字模拟混合系统,特别是在现场和控制室距离近的情况下,混和控制在同一集中的cpu中进行将比较方便,所冒控制集中的风险也不大。
现阶段和今后的一段时间内,工业控制系统将面临fcs和dcs 共存的局面。
因此,在工业控制系统结构设计时,考虑如何使fcs 与dcs系统尽可能协同工作是很现实的方案,更具有推广和实用价值。
2.5多总线集成的fcs成为抢夺市场的重要策略。
各公司相继推出能够使多总线协同工作的控制系统,以适应目前现场测控设备多态性和用户需求多样性的需求。
如1999年interkama展览会上,一些典型系统包含多种总线标准:如,ff中坚力量之一的smar公司的系统包括profibus、ff、hart、4~20ma和foxboro公司的系统包括ff、profibus、modbus、devicenet等。
目前,siemens公司的pcs7系统和fisher-rosemount公司的delta v系统是两个典型的fcs系统。
pcs7是由ethernet、profibus-dp、profibus-pa、device-net和as-interface等组成,而delta v是由ethernet、ff h1以及hart组成,且也可与profibus兼容。
2.6 fcs与信息网络集成是建立企业综合实时数据库的基础。
企业综合实时数据库为企业优化控制、生产调度和计划决策提供依据。
实现现场总线与信息网络的紧密集成,可以建立统一的分布式数据库,保证所有数据的一致性、完整性和互操作性。
现场设备与信息网络实时通信,使用户能够通过信息网络中标准的图形界面随时、方便地了解生产情况。
同时,便于实现远程监控、优化调度、远程诊断和维护功能,以及实现远程的软件维护与更新。
3、结语随着计算机技术、通信技术、芯片技术、网络技术的飞速发展,人们在考虑如何直接利用其他领域的技术来带动本领域的发展,跟上时代的步伐。
最为典型的是ff在制定其高速现场总线标准时,直接采用100m的ethernet作为其高速现场总线标准。
功能块和设备描述是实现设备互操作的两大关键技术,在现场总线中的应用也分别借鉴程序设计中的模块组件技术和windows程序设计中的设备无关技术。
还有,标准化监控或者管理软件与现场设备之间的接口,建立统一数据存取规范的opc技术,其基础是微软的ole、com及dcom技术。
总体说来,自动化系统与设备将朝着现场总线体系结构的方向前进,这一发展趋势是肯定的。
既然是总线,就要向着趋于开放统一的方向发展,成为大家都遵守的标准规范,但由于这一技术所涉及的应用领域十分广泛,几乎覆盖了所有连续、离散工业领域,如过程自动化、制造加工自动化、楼宇自动化、家庭自动化等等。
大千世界,众多领域,需求各异,一个现场总线体系下可能不止容纳单一的标准。
几大技术均具有自己的特点,已在不同应用领域形成了自己的优势。
加上商业利益的驱使,它们都各自正在十分激烈的市场竞争中求得发展。
有理由认为:在从现在起的未来10年内,可能出现几大总线标准共存,甚至在一个现场总线系统内,几种总线标准的设备通过路由网关互连实现信息共享的局面。
现场总线技术的兴起,开辟了工厂底层网络的新天地。
它将促进企业网络的快速发展,为企业带来新的效益,因而会得到广泛的应用,并推动自动化相关行业的发展。
参考文献:[1]胡毅于东刘明烈. 工业控制网络的研究现状及发展趋势。
计算机科学,2010.1:23-27[2]赵新秋.工业控制网络的发展。
自动化与仪器仪表,2008,4:3-4[3]李正军.现场总线及其应用技术。
北京:机械工业出版社,2005.1作者简介:刘清华(1983.10-),男,辽宁沈阳人,沈阳建筑大学外国语学院,实习研究员。