组装工艺流程及常见问题
组装工艺流程

组装工艺流程1. 概述组装工艺流程是将零部件或组件按照一定的顺序和方法进行装配成成品的过程。
它涉及到材料准备、零部件装配、工装使用等多个环节。
本文将介绍一般的组装工艺流程,帮助读者了解如何有效地进行组装工艺。
2. 准备工作在开始组装工艺流程之前,需要进行一些准备工作,例如:•零部件准备:将需要装配的零部件准备齐全,并进行清洁和检查,确保无损坏或污染,以及准确无误的标识。
•工装准备:根据组装工艺流程的需要,选择合适的工装设备。
工装可以用于加工、装配、定位、固定等操作。
•人员培训:确保组装操作人员具备必要的技能和知识,以便他们能够正确地执行组装工艺流程。
3. 组装工艺流程步骤步骤一:组装准备在组装之前,需要进行一些准备工作,例如: - 确定组装区域,并确保该区域整洁、井然有序。
- 将所需零部件按照工艺要求摆放整齐,以便于取用。
- 检查工装设备是否正常工作,并进行必要的调整。
步骤二:零部件定位根据工艺要求,将需要装配的零部件放置在合适的位置。
可以使用工装设备,如定位夹具和导向板等,以确保零部件的位置准确无误。
步骤三:零部件连接根据组装工艺要求,选择合适的连接方式(如螺丝、焊接、粘接等)将零部件连接在一起。
务必确保连接牢固,以保证装配后的产品具有良好的性能和可靠性。
步骤四:调试和测试在完成零部件连接之后,对组装好的部件进行调试和测试。
此步骤旨在检查组装质量,并确保产品符合相关的规格和要求。
如果发现问题,及时进行调整和修复。
步骤五:产品整理和清洁在组装完成后,对产品进行整理,将工艺所需的标识和说明添加到产品上。
同时,对产品进行清洁,以确保产品的外观和性能符合要求。
4. 质量控制在整个组装工艺流程中,质量控制是至关重要的。
以下是一些建议的质量控制措施:•进行严格的零部件检查,确保零部件的质量和准确性。
•在每个步骤完成后进行自我检查,以确保每个工序都按照要求进行。
•定期进行产品抽样检验,并对抽样产品进行全面的物理和功能测试。
组装工艺流程与生产线
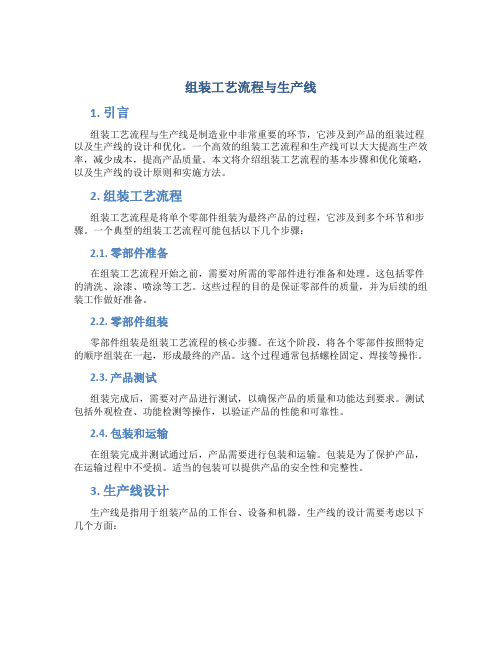
组装工艺流程与生产线1. 引言组装工艺流程与生产线是制造业中非常重要的环节,它涉及到产品的组装过程以及生产线的设计和优化。
一个高效的组装工艺流程和生产线可以大大提高生产效率,减少成本,提高产品质量。
本文将介绍组装工艺流程的基本步骤和优化策略,以及生产线的设计原则和实施方法。
2. 组装工艺流程组装工艺流程是将单个零部件组装为最终产品的过程,它涉及到多个环节和步骤。
一个典型的组装工艺流程可能包括以下几个步骤:2.1. 零部件准备在组装工艺流程开始之前,需要对所需的零部件进行准备和处理。
这包括零件的清洗、涂漆、喷涂等工艺。
这些过程的目的是保证零部件的质量,并为后续的组装工作做好准备。
2.2. 零部件组装零部件组装是组装工艺流程的核心步骤。
在这个阶段,将各个零部件按照特定的顺序组装在一起,形成最终的产品。
这个过程通常包括螺栓固定、焊接等操作。
2.3. 产品测试组装完成后,需要对产品进行测试,以确保产品的质量和功能达到要求。
测试包括外观检查、功能检测等操作,以验证产品的性能和可靠性。
2.4. 包装和运输在组装完成并测试通过后,产品需要进行包装和运输。
包装是为了保护产品,在运输过程中不受损。
适当的包装可以提供产品的安全性和完整性。
3. 生产线设计生产线是指用于组装产品的工作台、设备和机器。
生产线的设计需要考虑以下几个方面:3.1. 工作站布局工作站布局是指在生产线上安排各个工作站的位置。
布局应该考虑到工作站之间的物料流动和人员流动。
好的布局设计可以减少工作站之间的距离,提高工作效率。
3.2. 设备和工具选择选择适合的设备和工具是保证生产线顺利运行的关键。
应该根据产品的特点和要求,选择适合的设备和工具。
同时,还要考虑设备和工具的维护和维修工作,以保证生产线的可持续运行。
3.3. 自动化程度自动化程度是衡量生产线效率的重要指标。
在设计生产线时,应该尽可能地采用自动化设备和机器,减少人工操作,提高生产效率和产品质量。
装配工艺过程

装配工艺过程装配工艺过程是指将多个零部件按照特定的顺序和方法组装在一起,形成一个完整的产品的过程。
它是生产制造过程中非常重要的环节,决定着产品的质量和性能。
下面将详细介绍装配工艺过程的步骤和要点。
一、工艺准备装配工艺过程开始前,首先需要进行工艺准备工作。
这包括确定产品的装配工艺路线和流程,编制装配工艺文件,准备所需的工装、夹具和工具等。
工艺准备的目的是为了确保装配过程的顺利进行,提高装配效率和质量。
二、零部件准备装配工艺过程中需要使用各种零部件,因此在装配开始前,需要对各个零部件进行准备。
这包括清洗、检查、测量和标识等工作。
清洗零部件是为了去除表面的污垢和油脂,保证零部件的清洁度;检查零部件是为了发现零部件的缺陷和损坏,避免使用不合格的零部件;测量零部件是为了验证零部件的尺寸和形状是否符合要求;标识零部件是为了方便后续的装配操作。
三、装配顺序装配工艺过程中,需要按照一定的顺序进行装配。
一般来说,从简单的零部件开始,逐步向复杂的零部件过渡。
这样可以降低装配的难度和风险,提高装配的效率和质量。
在确定装配顺序时,需要考虑零部件之间的相互关系和依赖关系,合理安排装配的先后顺序。
四、装配方法装配工艺过程中,需要选择合适的装配方法。
常见的装配方法包括手工装配、自动装配和半自动装配等。
手工装配是指通过人工进行装配,适用于小批量、多品种的装配;自动装配是指通过机械设备和自动化控制系统进行装配,适用于大批量、单一品种的装配;半自动装配是手工装配和自动装配的结合,兼具了两者的优点。
选择合适的装配方法可以提高装配的效率和一致性。
五、质量控制装配工艺过程中,质量控制是非常重要的环节。
在装配过程中,需要进行各种质量控制措施,以确保装配的质量和性能。
这包括装配过程的检查和测试,以及对不合格产品的处理和修复等。
通过质量控制措施,可以及时发现和纠正问题,提高产品的质量稳定性和一致性。
六、工艺改进装配工艺过程是一个不断改进的过程。
电子装配工艺流程及注意事项

电子装配工艺流程及注意事项
《电子装配工艺流程及注意事项》
电子装配工艺流程是指将电子元件、器件和电路板进行组装和焊接的过程。
这个过程十分复杂,需要严格的操作规范和技术要求。
下面将介绍一下电子装配工艺流程以及在操作时需要注意的事项。
一、工艺流程
1. 元件预处理:在对元件进行安装之前,首先需要进行元件的预处理工作,包括清洗、防潮和去氧化处理。
2. 贴胶:在电路板上涂抹胶水,用来固定元件。
3. 贴元件:将预处理好的元件按照要求贴在电路板上,确保位置准确。
4. 固定元件:使用热风枪或者烤箱对电路板进行加热,使胶水固定元件。
5. 焊接:进行元件之间的焊接,确保焊点牢固。
6. 清洗:对焊接好的电路板进行清洗,去除残余的胶水和焊渣。
二、注意事项
1. 操作规范:严格按照工艺流程要求进行操作,不得马虎。
2. 器件保护:在操作过程中要注意保护电子元件和器件,避免损坏。
3. 清洁工作场所:保持工作场所的整洁和清洁,防止杂物污染电路板。
4. 检验质量:对于焊接好的电路板需要进行严格的质量检验,确保工艺流程的准确和可靠。
5. 人员技术:操作人员需要经过专业的培训,熟练掌握电子装配的工艺流程和技术要求。
总之,电子装配工艺流程是一个需要严谨操作和技术要求的过程,只有严格按照工艺要求进行操作,并且做好相应的注意事项,才能保证电子产品的质量和可靠性。
机械装配工艺的流程与注意事项

机械装配工艺的流程与注意事项机械装配是指将多个零部件按照一定的顺序和方法组装成为一个完整的机械设备或产品的过程。
正确的装配工艺能够保证产品的质量和性能,提高生产效率,降低成本。
本文将介绍机械装配的常见流程以及注意事项。
一、机械装配的流程1. 零部件准备:在开始机械装配之前,需要准备好所有需要使用的零部件。
确保零部件的数量、型号和规格与装配图纸一致,并进行检查和清洗。
2. 工具准备:根据装配图纸和工艺要求,准备好所需要的工具和设备。
例如,扳手、螺丝刀、钳子等常用工具,以及其他特定的工装和夹具。
3. 装配顺序:根据装配图纸和装配工艺,确定零部件的装配顺序。
通常是从大型部件到小型部件,从外部部件到内部部件的顺序进行。
4. 装配方式:选择合适的装配方式进行组装。
常见的装配方式包括插入、安装、连接等。
根据零部件的特性和要求,选择适当的方法进行操作。
5. 装配精度控制:在装配过程中,要严格控制装配精度。
通过测量和调整,确保零部件的位置、角度等参数符合要求。
6. 节点检查:在装配的每个关键节点,进行检查和确认。
验证装配结果与要求是否一致,是否存在问题或缺陷。
及时进行调整和修正。
7. 功能测试:在完成装配后,对机械设备或产品进行功能测试。
验证其运行是否正常,是否满足设计要求。
8. 清洁和保养:完成装配和测试后,对装配设备进行清洁和保养工作。
清除杂物和污垢,对设备进行润滑和维护,以延长其使用寿命。
二、机械装配的注意事项1. 安全操作:机械装配需要注意操作安全。
工作人员要熟悉装配工艺和操作规程,佩戴个人防护装备,注意避免人身和设备安全事故的发生。
2. 零部件保护:在装配过程中,要注意保护零部件的完整性和表面质量。
避免碰撞、摩擦和腐蚀等造成的损伤。
3. 装配图纸的正确使用:装配图纸是装配的重要依据,要正确理解和使用。
了解图纸上的标注和要求,按照图纸的要求进行装配。
4. 安装力的控制:在装配过程中,要控制好装配力的大小。
组装工艺流程课件

扬声器引线摆放到主 板与天线之间空隙处
组装工艺流程
14
xx
四、装摄像头、天线组件(3)
图五、安装振动器
图六、锁天线组件螺丝
螺钉
振动器安装位置(线不可露出 PCBA外,必须从天线组件开槽 位走线,并按此图方式整好)
组装工艺流程
15
xx
四、装摄像头、天线组件(4)
注意事项: 1.注意保持工作台面的清洁,做好5S; 2.作业前必须带好引线式防静电环; 3.操作需轻拿轻放,拿取时尽量拿PCBA两侧,单手一次性只可拿取1块PCBA, 且PCBA不可直接碰撞/叠放在一起,放置时不得采用抛、丢的动作; 4.作业中出现异常情况,须及时通知有关管理或工程人员处理; 5. 先调好规定的电批扭力0.65±0.05kgf.cm,试打2台确认OK后方可继续(各机型 扭力请参考SOP); 6.锁螺丝时电批要垂直对准螺丝孔位往下锁,螺丝需锁密合,不可有滑牙、段 差、未锁到位、漏锁等不良现象; 7.电批扭力每4hr.校准一次。
组装工艺流程
27
xx
八、装主板组合品至A壳(1)
图一、前工位主板组合品
图二、前工位A壳组合品
组装工艺流程
28
xx
八、装主板组合品至A壳(2)
图三、装主板至A壳
注:A壳上5个导电布 需与主板接触到并压 在主板下,不可翘起 (图示画圈位置)
各卡扣、卡位需对准 卡装到位且需平行
MIC及引线安装卡槽(MIC引 线边朝内,引线不能超出壳体 且不能露在PCBA上)MIC保 护套不可脱落
NG
OK
装孔塞、镜片、手写笔、贴 易碎贴
外观检查
NG
OK 贴保护膜
OK 修理
装PCBA组合品至A壳
装配工艺流程图及注意事项
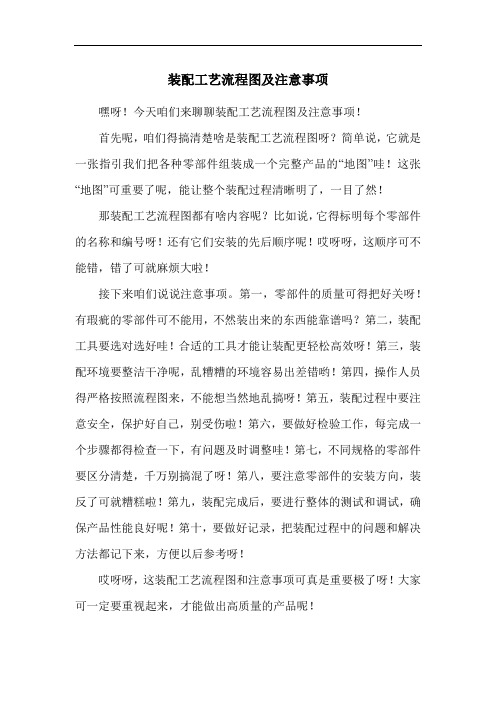
装配工艺流程图及注意事项
嘿呀!今天咱们来聊聊装配工艺流程图及注意事项!
首先呢,咱们得搞清楚啥是装配工艺流程图呀?简单说,它就是一张指引我们把各种零部件组装成一个完整产品的“地图”哇!这张“地图”可重要了呢,能让整个装配过程清晰明了,一目了然!
那装配工艺流程图都有啥内容呢?比如说,它得标明每个零部件的名称和编号呀!还有它们安装的先后顺序呢!哎呀呀,这顺序可不能错,错了可就麻烦大啦!
接下来咱们说说注意事项。
第一,零部件的质量可得把好关呀!有瑕疵的零部件可不能用,不然装出来的东西能靠谱吗?第二,装配工具要选对选好哇!合适的工具才能让装配更轻松高效呀!第三,装配环境要整洁干净呢,乱糟糟的环境容易出差错哟!第四,操作人员得严格按照流程图来,不能想当然地乱搞呀!第五,装配过程中要注意安全,保护好自己,别受伤啦!第六,要做好检验工作,每完成一个步骤都得检查一下,有问题及时调整哇!第七,不同规格的零部件要区分清楚,千万别搞混了呀!第八,要注意零部件的安装方向,装反了可就糟糕啦!第九,装配完成后,要进行整体的测试和调试,确保产品性能良好呢!第十,要做好记录,把装配过程中的问题和解决方法都记下来,方便以后参考呀!
哎呀呀,这装配工艺流程图和注意事项可真是重要极了呀!大家可一定要重视起来,才能做出高质量的产品呢!。
汽车前悬架装配工艺流程及注意问题

汽车前悬架装配工艺流程及注意问题汽车前悬架是汽车重要的组成部分之一,它直接影响着汽车的行驶稳定性和乘坐舒适性。
因此,汽车前悬架的装配工艺流程和注意问题非常重要。
本文将从以下几个方面进行阐述。
一、前悬架装配工艺流程1.准备工作:首先需要准备好前悬架的各个零部件,包括悬架臂、球头、减震器、弹簧等。
同时需要检查这些零部件是否完好无损,是否符合要求。
2.组装悬架臂:将悬架臂与球头进行组装,需要注意的是,球头的安装位置应该与悬架臂的安装位置相对应,同时需要使用扭力扳手进行拧紧,确保安装牢固。
3.安装减震器:将减震器安装到悬架臂上,需要注意减震器的安装方向,同时需要使用扭力扳手进行拧紧,确保安装牢固。
4.安装弹簧:将弹簧安装到减震器上,需要注意弹簧的安装方向,同时需要使用扭力扳手进行拧紧,确保安装牢固。
5.安装前悬架:将组装好的前悬架安装到车身上,需要注意前悬架的安装位置和方向,同时需要使用扭力扳手进行拧紧,确保安装牢固。
二、前悬架装配注意问题1.注意安全:在进行前悬架的装配过程中,需要注意安全,避免发生意外事故。
同时需要使用合适的工具和设备,确保操作安全。
2.注意零部件的质量:前悬架的各个零部件的质量直接影响着汽车的行驶稳定性和乘坐舒适性,因此需要选择质量可靠的零部件进行装配。
3.注意装配顺序:在进行前悬架的装配过程中,需要按照正确的顺序进行装配,避免出现错误。
4.注意拧紧力度:在进行前悬架的装配过程中,需要使用扭力扳手进行拧紧,确保拧紧力度符合要求,避免出现松动或过紧的情况。
5.注意调整角度:在进行前悬架的装配过程中,需要注意调整悬架的角度,确保符合要求,避免出现行驶不稳定的情况。
总之,前悬架的装配工艺流程和注意问题非常重要,需要严格按照要求进行操作,确保汽车的行驶稳定性和乘坐舒适性。
同时需要注意安全,避免发生意外事故。
- 1、下载文档前请自行甄别文档内容的完整性,平台不提供额外的编辑、内容补充、找答案等附加服务。
- 2、"仅部分预览"的文档,不可在线预览部分如存在完整性等问题,可反馈申请退款(可完整预览的文档不适用该条件!)。
- 3、如文档侵犯您的权益,请联系客服反馈,我们会尽快为您处理(人工客服工作时间:9:00-18:30)。
2014/8/23
SHIDE GROUP
Transparency No.18
塑料门窗组装工艺流程 制作常见问题及解决方法
大连实德集团客户服务部
五、铣五金件安装槽孔
1、采用仿形铣床加工传动器槽、锁孔、滑轮槽。 2、在具体加工时,可以根据传动器的尺寸更换刀具和进给 量,实现对槽、孔的加工。例如,在进行传动器执手孔 的加工时,要注意中间孔所用的铣刀直径为 Φ12,而两 边孔径为Φ10,切不可以刀具互用。 3、铣削后,孔径位置正确,周边光滑、无毛刺,利于DE GROUP
Transparency No.4
塑料门窗组装工艺流程 制作常见问题及解决方法
大连实德集团客户服务部
2、增强型钢:
(1)增强型钢一般采用钢带等捆扎包装。产品在运输中 避免冲击、挤压、雨淋、受潮。 (2)产品应贮存在无腐蚀性介质,空气流通,相对湿度 小于85%仓库中,堆放时,下面应有厚度不小于 100mm的软木,间距不大于500mm,堆放高度不得超 过0.5m。
2014/8/23
SHIDE GROUP
Transparency No.12
塑料门窗组装工艺流程 制作常见问题及解决方法
大连实德集团客户服务部
四、铣排水孔和气压平衡孔
塑料门窗要具有良好的水密性,必须在门窗 上打排水孔,使门窗内的积水能够排到室外;为 了保证雨水在排水腔内能够顺利排出,必须在门 窗的上侧或竖侧打气压平衡孔。 根据其所处的位置及作用,可将排水孔和气 压平衡孔分为内排水孔和外排水孔、内气压平衡 孔和外气压平衡孔。
2014/8/23
SHIDE GROUP
Transparency No.10
塑料门窗组装工艺流程 制作常见问题及解决方法
大连实德集团客户服务部
(4)注意事项: (a)开始切割时,根据下料依据和工艺要求确定下
料尺寸,要注意机器本身切割长度是否含有焊接余量。 如果含有,切割时可以不用考虑焊接余量,直接按照构 件尺寸进行切割;如果不含,切割尺寸为构件原尺寸加 上两端焊接余量(一般单端焊接余量为3mm)。 ( b)切割过程中,应保证锯片和工作台清洁,无水 、油污、灰尘等杂物,以免影响后续工序的进行。切割 后,做到首件三检,并抽检。
2014/8/23
SHIDE GROUP
Transparency No.21
塑料门窗组装工艺流程 制作常见问题及解决方法
大连实德集团客户服务部
4、装加原则:
(1)平开窗所有钢衬45°切割; (2)增强型钢距型材端部的最小垂直距离为5~10mm,保证五金件 的连接螺钉可以打到增强型钢上,加强五金件的牢固度;
2014/8/23
SHIDE GROUP
Transparency No.15
塑料门窗组装工艺流程 制作常见问题及解决方法
大连实德集团客户服务部
3、下列情况必须铣排水孔和气压平衡孔: (1)凡是外墙上的外门、外窗都应设置排水系统 ; (2)外门、外窗的每块玻璃下边框型材上都应开 有内、外排水孔,每块玻璃的上边框型材上都 应开有气压平衡孔,型材的内部也要开有气压 平衡孔。
2014/8/23
SHIDE GROUP
Transparency No.13
塑料门窗组装工艺流程 制作常见问题及解决方法
大连实德集团客户服务部
1、排水孔与气压平衡孔的规格与尺寸如图所示。
排水孔的规格尺寸一般为Φ×L(5mm×30mm); 气压平衡孔的规格尺寸一般为Φ×L(4.5mm×30mm)。
2014/8/23
(3)理论上双排铆固。
5、增强型钢的装配主要有两种方式:
(1)在不影响焊接的部位可预先插入;
(2)十字型或T型焊接部位,增强型钢在对接后及时插入。
2014/8/23
SHIDE GROUP
Transparency No.22
塑料门窗组装工艺流程 制作常见问题及解决方法
2014/8/23
SHIDE GROUP
Transparency No.16
塑料门窗组装工艺流程 制作常见问题及解决方法
大连实德集团客户服务部
4、推荐排水孔的数量及分布如下 (1)当下边框边长≤700mm时,开一个外排水孔,位置 在边长的正中处; (2)当下边框边长为 700~1800mm,开两个外排水孔, 位置在各距两端边长1/4处; (3)下边框边长≥1800mm时,开3个外排水孔,其中两 个的位置在距两端1/6处,第三个位于构件的中间处。 一般情况下,每一个外排水孔应该对应一个内排水 孔。对于平开门窗的扇和推拉门窗的扇而言,由于其制 作尺寸的限制,只需在其下边构件上打一个内排水孔和 一个外排水孔。 排水孔的数量及其分布,应视该地区的气候条件及 降雨量而定。降雨量较大的地区,排水孔的个数可以稍 多,规格尺寸也可以稍大一些。
塑料门窗组装工艺流程 制作常见问题及解决方法
大连实德集团客户服务部
塑料门窗组装工艺流程
制作常见问题及解决方法
大连实德化建集团
客户服务部
范怀瑾 2004年12月
2014/8/23
SHIDE GROUP
Transparency No.1
塑料门窗组装工艺流程 制作常见问题及解决方法
大连实德集团客户服务部
2014/8/23
SHIDE GROUP
Transparency No.8
塑料门窗组装工艺流程 制作常见问题及解决方法
大连实德集团客户服务部
(2)V型口的下料
(a)设备选择V型切割锯 (b)V型切割锯两锯片成90°,最大切口深度为75mm左右 ,切割后,应满足型材切割后的各项要求。 (c)V型切口深度应为所焊V口的中挺宽度的一半减去焊接 余量(2.5-3.0mm)。切口截面光滑、清洁、无料屑。 (d)所有构件切割后满足:切割后V口角度允差±0.3°;切 割后V口深度允差±0.5mm;构件切削面与型材两侧面的垂 直度有保证,待焊面清洁,无水、油污、料屑等杂物。
2014/8/23
SHIDE GROUP
Transparency No.7
塑料门窗组装工艺流程 制作常见问题及解决方法
三、下料:
1、PVC塑料型材下料 (1)PVC塑料型材框扇下料
大连实德集团客户服务部
(a)下料所用设备为双角切割锯和任意角度锯。 (b)双角切割锯可以在45度至90度之间调节。切割时,通过调节 双切锯的活动锯头来调节型材的切割长度,具体尺寸由导轨上的 定位标尺来确定。 (c)切割角的调节是通过松开紧固操纵杆来实现的。 ( d)一般情况下,电子装置的最小切割长度是 280 左右,最大切 割长度是3600左右。 (e)切割后做到首件必检,随时抽检。所有构件应满足以下:角 度允差±0.5°,长度误差±0.5mm,待焊面清洁、无水、油污、 料屑等杂物,构件切削面与型材两侧面的垂直度应不影响焊接质 量。
2014/8/23
SHIDE GROUP
Transparency No.20
塑料门窗组装工艺流程 制作常见问题及解决方法
大连实德集团客户服务部
3、建议所有型材增强型钢腔加装增强型钢。以下 条件下必须加装增强型钢: (1)经抗风压计算,框、扇、梃的强度达不到安 全值时,必须加装增强型钢; ( 2 )框、扇、梃上需要用自攻螺钉固定,安装五 金件时,必须加装增强型钢,使自攻螺钉拧紧在 增强型钢的壁上,保证五金件的安装有必要的牢 固度。
SHIDE GROUP
Transparency No.14
塑料门窗组装工艺流程 制作常见问题及解决方法
大连实德集团客户服务部
2、在加工门窗的内、外排水孔时,要特别注意以 下几点: (1)不要把排水腔与增强型钢腔打通,防止雨 水进入主腔体内,腐蚀增强型钢。 (2)开内、外排水孔时要注意尽量开在型材排 水腔最低的位置,防止造成型材内部积水,内 排水孔不能与外排水孔相对,应相互错开一定 距离。
2014/8/23
SHIDE GROUP
Transparency No.19
塑料门窗组装工艺流程 制作常见问题及解决方法
大连实德集团客户服务部
六、装配增强型钢
1、增强型钢的作用 (1)提高门窗的刚性和强度; (2)防止型材变形; (3)使安装的五金件更牢固。 2、增强型钢装加在PVC型材的增强型钢腔内, 增强型钢与增强型钢腔的配合间隙应为 1±0.5mm,以保证增强型钢加装方便,且受 风压后能恢复原状。增强型钢在加工时,外形 尺寸允差为-0.1~ -0.5mm。
2014/8/23
SHIDE GROUP
Transparency No.17
塑料门窗组装工艺流程 制作常见问题及解决方法
大连实德集团客户服务部
5、气压平衡孔的数量及分布 直接装在门窗框、门窗扇上的每一块玻璃,其 上边框室外一侧的中央应该铣一个或多个外气 压平衡孔,铣一个内气压平衡孔,内、外气压 平衡孔可以不错开。
全焊接组装工艺流程图
2014/8/23
SHIDE GROUP
Transparency No.2
塑料门窗组装工艺流程 制作常见问题及解决方法
按客户要求设计
主型材下料 辅 助 下 料 铣水槽锁孔滑轮孔 切V口 装加强筋固定 封 盖 玻 璃 压 条 密 封 条 装毛条 加 强 筋 毛 条 密 封 条 五 金 件
2014/8/23
SHIDE GROUP
Transparency No.9
塑料门窗组装工艺流程 制作常见问题及解决方法
大连实德集团客户服务部
(3)中梃的下料
(a)设备选择双角切割锯、任意角度锯及中梃锯。 (b)保证第一锯切割后型材端部角度为45°,允差 ±0.5°; (c)保证第二锯切割后型材端部角度为90°,允差 ±0.5°; (d)切割后型材端部尖角与中心线偏移允差±0.5mm; (e)下料长度符合设计要求,允差±0.5mm; (f)构件切削面与型材两侧面的垂直度有保证,待焊面 清洁,无水、油污、料屑等杂物。