叉车工作装置液压系统设计
2024年叉车工作装置和液压系统的安全要求(2篇)
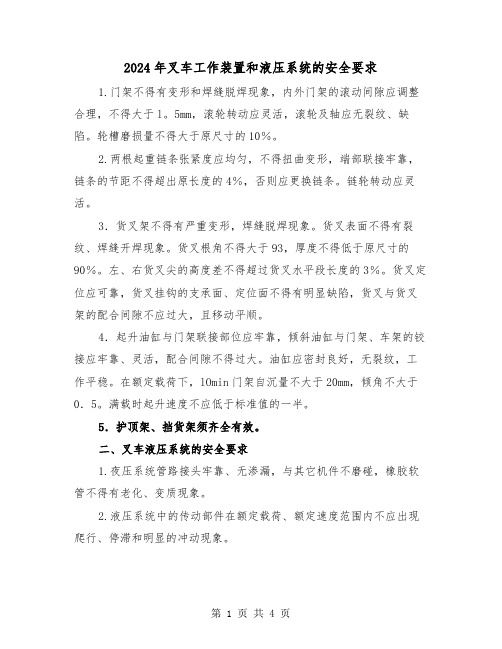
2024年叉车工作装置和液压系统的安全要求1.门架不得有变形和焊缝脱焊现象,内外门架的滚动间隙应调整合理,不得大于l。
5mm,滚轮转动应灵活,滚轮及轴应无裂纹、缺陷。
轮槽磨损量不得大于原尺寸的10%。
2.两根起重链条张紧度应均匀,不得扭曲变形,端部联接牢靠,链条的节距不得超出原长度的4%,否则应更换链条。
链轮转动应灵活。
3.货叉架不得有严重变形,焊缝脱焊现象。
货叉表面不得有裂纹、焊缝开焊现象。
货叉根角不得大于93,厚度不得低于原尺寸的90%。
左、右货叉尖的高度差不得超过货叉水平段长度的3%。
货叉定位应可靠,货叉挂钩的支承面、定位面不得有明显缺陷,货叉与货叉架的配合间隙不应过大,且移动平顺。
4.起升油缸与门架联接部位应牢靠,倾斜油缸与门架、车架的铰接应牢靠、灵活,配合间隙不得过大。
油缸应密封良好,无裂纹,工作平稳。
在额定载荷下,lOmin门架自沉量不大于20mm,倾角不大于0.5。
满载时起升速度不应低于标准值的一半。
5.护顶架、挡货架须齐全有效。
二、叉车液压系统的安全要求1.夜压系统管路接头牢靠、无渗漏,与其它机件不磨碰,橡胶软管不得有老化、变质现象。
2.液压系统中的传动部件在额定载荷、额定速度范围内不应出现爬行、停滞和明显的冲动现象。
3.多路换向阀壳体无裂纹、渗漏;工作性能应良好可靠;安全阀动作灵敏,在超载25%时应能全开,调整螺栓的螺帽应齐全坚固。
操作手柄定位准确、可靠,不得因震动而变位。
4.载荷曲线、液压系统铭牌应齐全清晰。
2024年叉车工作装置和液压系统的安全要求(2)引言:叉车是一种广泛使用的工业设备,具有起升、搬运和堆垛功能。
作为一种工作装置和液压系统的组合,叉车在运输和搬运物料中起着重要的作用。
然而,由于叉车的特殊性,其工作装置和液压系统的安全性非常重要。
本文将介绍2024年叉车工作装置和液压系统的安全要求,包括设计、制造、使用和维护方面的要求。
一、设计要求:1. 结构设计:叉车工作装置和液压系统的设计应符合国家相关标准和规范,保证其结构强度和稳定性,能够承受额定工作负荷。
叉车工作装置液压系统设计(液压系统经典设计实例)[仅供借鉴]
![叉车工作装置液压系统设计(液压系统经典设计实例)[仅供借鉴]](https://img.taocdn.com/s3/m/e10ee96e227916888586d74a.png)
3.1 叉组车合液机压床系动统力的滑设台计液要压求系统
根据叉车用途不同, 叉车可分为普通叉车和 特种叉车两类。
普通叉车如下图所 示。
几种典型的特种叉 车如右侧图所示,分别 是集装箱堆高车、伸缩 臂叉车、高速越野叉车。
3
3.1 叉组车合液机压床系动统力的滑设台计液要压求系统
根据叉车的结构特点,可分为平衡重式叉车、叉腿式叉车、 前移式叉车、侧面式叉车,其中,平衡重式叉车最常用。
3.1.5.2 倾斜装置液压系 统设计参数及技术要求
倾斜装置示意图如图 3-7 所 示 , 该 装 置 由 倾 斜 液压缸驱动门架绕一铰接 点做摆动式旋转。技术参 数如下表所示。
导轨(门架) 重物
叉架 铰接点
倾斜液压缸
38
3.2 初组步合例中叉车工作装置液压系统包括起升液压 系统和倾斜液压系统两个子系统,分别确定两个子系统 的设计方案和主要技术参数。
11
3.1 叉组车合液机压床系动统力的滑设台计液要压求系统
(4) 满载最大起 升速度,是指叉车在 停止状态下,将发动 机油门开到最大时, 起升大小为额定起重 量的货物所能达到的 平均起升速度。
12
3.1 叉组车合液机压床系动统力的滑设台计液要压求系统
(5) 满载爬坡度,是 指货叉上载有额定起重量 的货物时,叉车以最低稳 定速度行驶所能爬上的长 度为规定值的最陡坡道的 坡度值。
27
3.1 叉组车合液机压床系动统力的滑设台计液要压求系统
28
3.1 叉组车合液机压床系动统力的滑设台计液要压求系统
双向安全阀3保证液压回路双向工作的安全。
29
3.1 叉组车合液机压床系动统力的滑设台计液要压求系统
叉车转向频繁,为减轻驾驶员劳动强度,现在起重量2t以上的叉车 多采用助力转向-液压助力转向或全液压转向。某型号叉车液压助力转 向系统原理如图3-5所示。
手动液压叉车设计
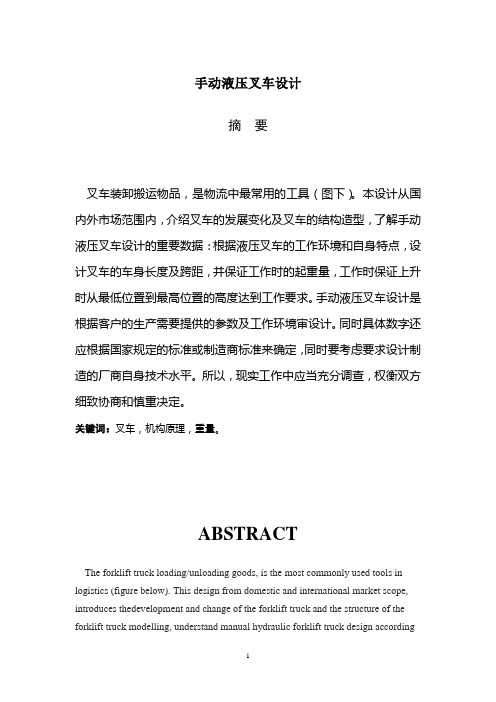
手动液压叉车设计摘要叉车装卸搬运物品,是物流中最常用的工具(图下)。
本设计从国内外市场范围内,介绍叉车的发展变化及叉车的结构造型,了解手动液压叉车设计的重要数据:根据液压叉车的工作环境和自身特点,设计叉车的车身长度及跨距,并保证工作时的起重量,工作时保证上升时从最低位置到最高位置的高度达到工作要求。
手动液压叉车设计是根据客户的生产需要提供的参数及工作环境审设计。
同时具体数字还应根据国家规定的标准或制造商标准来确定,同时要考虑要求设计制造的厂商自身技术水平。
所以,现实工作中应当充分调查,权衡双方细致协商和慎重决定。
关键词:叉车,机构原理,重量。
ABSTRACTThe forklift truck loading/unloading goods, is the most commonly used tools in logistics (figure below). This design from domestic and international market scope, introduces thedevelopment and change of the forklift truck and the structure of the forklift truck modelling, understand manual hydraulic forklift truck design accordingto the important data: hydraulic forklifts working environment and its own features and design of the body and the span length of the forklift truck and ensure that work, to guarantee the weight up from the lowest to the highest position the height of the position to work requirements. Manual hydraulic forklift truck design according to the customer's production is the need to provide the design parameters and working environment. At the same time the detailed Numbers also should according to the standards set by the state or manufacturer standard to determine, at the same time to consider to ask design and manufacture of manufacturer's skills. So, the reality of the work shall be fully survey, of both parties through consultations and careful meticulous decision.Keywords: forklift, the organization principle, weight.图:手动液压叉车绪论液压叉车是的物流业的必不可少的搬运设备。
叉车设计(原创最新版本

精品课件
13
叉车概述
3.叉车的历史与发展 世界叉车最早出现在1914~1915年之间,到二十世纪
三十年代在市场上开始出售叉车。 第二次世界大战期间,由于搬运军事物资的需要,
促进了叉车的发展。 1971年世界叉车的年产量约为20万台,2006年世界
叉车的年产量约为84万台。
精品课件
14
叉车概述
我国叉车工业起步于20世纪50年代末,当时主要仿制 前苏联5t机械传动叉车。60年代通过测绘日本的叉车 ,开创了整个叉车行业,也使得国内查车外观受日本 的影响较大。
精品课件
15
叉车概述
从70年代后期到80年代中期,全行业先后组织了2次联合设计 ,之后各叉车生产厂纷纷引进国外先进技术、消化吸收和国 产化,奠定了中国叉车行业的基础。
90年代以来一批中外合资与独资企业的建立,如林德叉车和 韩国现代叉车,形成了产品档次的多层次格局,使叉车行业 百花齐放。
精品课件
16
叉车概述
4叉车的基本参数: (1) 起重量,又称额定起重量Q,指货叉上的货物中心位于 规定的载荷中心距时,叉车能够举升的最大重量。 传统叉车吨位级别与常见主导产品吨位见下表。
精品课件
17
叉车概述
(2)载荷中心距C:货物重心到货叉垂直段前表面距离 。起重量越大,载荷中心距也越大。
平衡重式叉车载荷中心距如图1-7所示。
精品课件
18
叉车概述
(3) 最大起升高度Hmax, 是指叉车位于水平坚实地面上,门架垂直放置且承
受额定起重量的货物时,货叉所能升起的最大高度,即货叉 升至最大高度时水平段上表面至地面的垂直高度。
叉车设计
张荣芸
精品课件
1
叉车工作装置和液压系统的安全要求范本(二篇)
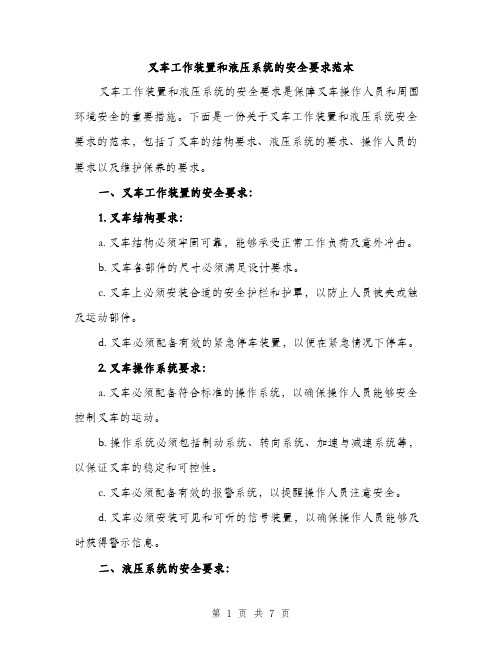
叉车工作装置和液压系统的安全要求范本叉车工作装置和液压系统的安全要求是保障叉车操作人员和周围环境安全的重要措施。
下面是一份关于叉车工作装置和液压系统安全要求的范本,包括了叉车的结构要求、液压系统的要求、操作人员的要求以及维护保养的要求。
一、叉车工作装置的安全要求:1. 叉车结构要求:a. 叉车结构必须牢固可靠,能够承受正常工作负荷及意外冲击。
b. 叉车各部件的尺寸必须满足设计要求。
c. 叉车上必须安装合适的安全护栏和护罩,以防止人员被夹或触及运动部件。
d. 叉车必须配备有效的紧急停车装置,以便在紧急情况下停车。
2. 叉车操作系统要求:a. 叉车必须配备符合标准的操作系统,以确保操作人员能够安全控制叉车的运动。
b. 操作系统必须包括制动系统、转向系统、加速与减速系统等,以保证叉车的稳定和可控性。
c. 叉车必须配备有效的报警系统,以提醒操作人员注意安全。
d. 叉车必须安装可见和可听的信号装置,以确保操作人员能够及时获得警示信息。
二、液压系统的安全要求:1. 叉车液压系统要求:a. 叉车液压系统必须符合相关标准,确保液压部件的质量和性能。
b. 叉车液压系统必须经过严格的检测和测试,以保证其安全可靠。
c. 叉车液压系统必须配备有效的泄压装置,以防止超压引发意外事故。
d. 叉车液压系统必须保持清洁,定期更换液压油和过滤器,以确保系统正常运行。
2. 液压油缸和管路要求:a. 叉车液压油缸和管路必须状况良好,无泄漏现象。
b. 叉车液压油缸和管路必须定期检查和维护,以确保其正常工作。
c. 叉车液压油缸和管路必须配备合适的保护装置,以防止外部物体对其造成损坏。
三、操作人员的安全要求:1. 操作人员培训和资质要求:a. 操作人员必须经过专业培训,了解叉车操作的规范和安全要求。
b. 操作人员必须持有相应的驾驶证书和资质,以确保其能够熟练操作叉车。
2. 操作人员的安全行为要求:a. 操作人员必须严格按照操作规程进行操作。
7吨叉车液压系统设计

7吨叉车液压系统设计叉车是一种用于搬运和堆垛货物的特种设备,广泛应用于物流仓储、制造业和建筑工地等场所。
叉车的液压系统是其重要的组成部分,负责提供动力和控制叉车的升降、倾斜等运动。
在设计叉车液压系统时,需要考虑到叉车的工作环境、负载要求和安全性等方面,以确保叉车能够顺利进行工作。
1.液压系统的工作原理叉车液压系统主要由液压泵、液压缸、油箱、控制阀、液压管路等组成。
液压泵将液压油吸入并压缩,通过液压管路输送到液压缸中,使活塞运动,从而实现对叉车进行升降、倾斜等控制。
控制阀则负责控制液压油的流向和流量,确保叉车能够按照要求进行操作。
2.设计参数的选择在设计叉车液压系统时,需要考虑到叉车的工作负载、升降高度、速度要求和工作环境等因素。
根据叉车的工作需求,选择合适的液压泵、液压缸和控制阀,确保叉车能够满足工作要求。
同时,还需要考虑到叉车的安全性和稳定性,确保叉车在使用过程中不会发生意外。
3.油路系统的设计叉车的油路系统需要具有良好的密封性和稳定性,以确保液压油能够有效地输送到液压缸中,并保持系统的正常工作。
在设计油路系统时,需要考虑到液压管路的长度、弯曲和连接方式等因素,确保系统的流动阻力小,流量稳定。
4.液压泵和液压缸的选择在设计叉车液压系统时,需要选择合适的液压泵和液压缸,以确保叉车能够顺利进行升降、倾斜等运动。
液压泵的选择应考虑到其流量、压力和功率等参数,选择适合叉车工作负载的泵。
液压缸的选择则需要考虑到其推力、行程和速度等参数,确保叉车能够按照要求进行运动。
5.控制阀的设计控制阀是叉车液压系统中的关键组成部分,负责控制液压油的流向和流量,确保叉车能够按照要求进行操作。
在设计控制阀时,需要考虑到其操作方式、阀口数量和流量控制精度等因素,以确保叉车的操作稳定性和精度。
总的来说,设计一台7吨叉车的液压系统需要考虑到叉车的工作环境、负载要求、安全性和稳定性等因素,选择合适的液压泵、液压缸和控制阀,并设计合理的油路系统,以确保叉车能够顺利进行工作。
叉车液压系统毕业设计
一个关于叉车液压系统的毕业设计项目是设计和制作一套叉车液压系统实验台,以下是该项目的主要功能和要求:
1. 液压系统的组成:设计并组装叉车液压系统实验台,包括液压泵、液压阀、液压缸、油箱、高压油管和各类传感器等。
2. 液压系统的控制:设计并开发液压系统控制面板,可进行液压泵、液压阀、液压缸等组件的控制和操作。
3. 系统参数的测量:通过传感器测量液压系统中的各项参数,如压力、流量、温度等,并将数据显示在监控屏幕上,方便用户实时了解系统运行情况。
4. 故障诊断和维护:设计并开发一套故障诊断和维护系统,可以检测和诊断液压系统中的故障,并提供相应的维修建议和方法。
5. 报警和保护功能:设置液压系统的报警和保护功能,确保系统运行的安全性和稳定性。
6. 操作手册和使用说明书:编写液压系统实验台的操作手册和使用说明书,方便用户进行操作和维护。
7. 性能测试和数据分析:进行系统的性能测试和数据分析,通过实验数据分析和比较,评估液压系统的性能和稳定性,并提供优化建议和方案。
以上是一个关于叉车液压系统的毕业设计项目的示例,你可以根据自己的兴趣和能力进行具体的设计和制作。
在项目中要注重理论和实践相结合,注意安全和质量控制,同时考虑系统的可维护性和可升级性。
祝你顺利完成毕业设计项目!。
3吨叉车液压系统设计
3吨叉车液压系统设计叉车液压系统设计是一项重要的技术任务,需要考虑到叉车的工作负载和运行环境,以确保系统的可靠性和有效性。
以下是一个关于3吨叉车液压系统设计的1200字以上的介绍:一、液压系统的组成和工作原理叉车液压系统由多个主要组成部分组成,包括液压泵、阀组、液压缸、液压马达和油箱等。
系统的工作原理是通过液压泵将液体压力传递到终端执行器(液压缸或马达)来实现工作效果。
液压泵的作用是将机械能转化为液压能,并提供所需的油流。
阀组用于控制和调节油流的方向、压力和流量。
液压缸通过油流的控制实现线性运动,而液压马达通过油流的控制实现旋转运动。
油箱作为液压系统的储油器,供应液压泵所需的液压油,并将系统中的油液维持在适当的温度和压力范围内。
二、叉车液压系统的设计要求1.承载能力:叉车液压系统的设计需要满足3吨货物的承载要求,确保系统在负载工作期间的稳定性和可靠性。
2.动作速度:液压系统需要具备快速响应速度和灵敏的控制性能,以实现对叉车动作的准确控制。
3.能效:系统设计时需要考虑能源效率,减少能量损失和能耗,以提高整体性能和经济性。
4.可靠性和安全性:系统的设计需要考虑到工作环境和条件,确保系统在恶劣环境下的可靠性和安全性。
5.维护和保养:系统设计应尽量简化,并提供易于维护和保养的接口和结构,以减少操作人员的工作负担。
三、液压泵的选择和设计选择合适的液压泵是设计液压系统的关键。
在叉车液压系统设计中,可以考虑使用变量柱塞泵或齿轮泵。
变量柱塞泵通过调节柱塞的位置来实现油流量的控制,可以提供精确的控制性能和较好的能效。
齿轮泵由于其结构简单且价格较低,常用于低要求的应用。
液压泵的排量和工作压力需要根据叉车的负载要求来确定。
液压泵的排量应满足叉车运行所需的液压油流量,而工作压力应满足叉车的最大负载能力和作业要求。
四、阀组的选择和设计叉车液压系统中的阀组主要包括方向控制阀、流量控制阀和压力控制阀等。
方向控制阀用于控制液压油流的方向,使液压系统能够实现正向和反向运动。
叉车工作装置和液压系统的安全要求
叉车工作装置和液压系统的安全要求叉车是一种用于搬运和堆垛物品的特种设备。
在叉车的工作过程中,工作装置和液压系统是至关重要的组成部分。
为了确保叉车的安全运行,工作装置和液压系统必须满足一系列严格的安全要求。
下面将介绍叉车工作装置和液压系统的安全要求。
首先,工作装置的安全要求是确保叉车在各种工作条件下能够稳定地搬运和堆垛物品。
工作装置必须具备足够的承载能力,以满足所搬运物品的重量要求。
同时,工作装置必须能够适应不同尺寸和形状的货物,并能够有效地进行装卸操作。
其次,工作装置必须具备良好的可见性和灵活性。
叉车驾驶员必须能够清晰地看到工作装置和搬运的物品,以便准确地操纵叉车。
工作装置的设计应尽可能减少对视线的阻碍,并具备可调节的功能,以适应不同高度和角度的工作情况。
另外,工作装置的操作方式必须简单直观,以确保叉车驾驶员能够轻松地控制工作装置的各种动作。
工作装置的控制杆或按钮应布置在驾驶员手触达范围内,并具备清晰明确的标识,以避免误操作。
总之,工作装置必须具备高度的可靠性和稳定性。
工作装置的各个零部件必须经过严密的设计和制造,以确保其在使用过程中不会出现故障或损坏。
此外,工作装置必须定期进行维护和检修,以保持其正常运行状态。
最后,液压系统的安全要求是确保叉车在提升、倾斜和转向等工作过程中能够平稳可靠地运行。
液压系统必须具备足够的压力和流量,以满足叉车工作中的各种需求。
同时,液压系统的操作方式必须方便简单,以便驾驶员能够轻松地控制液压系统的各项功能。
液压系统的各个元件必须具备高度的密封性和耐压性能,以防止液压油泄漏或系统破裂导致意外事故。
此外,液压系统必须配备过滤器、油温控制装置等附属装置,以确保液压油的净化和温度控制,从而延长液压系统的使用寿命。
总的来说,叉车工作装置和液压系统的安全要求是确保叉车在搬运和堆垛物品过程中能够稳定、可靠地工作。
工作装置必须具备足够的承载能力、良好的可见性和灵活性,以及简单直观的操作方式。
3吨叉车液压系统设计
3吨叉车液压系统设计叉车液压系统的设计是非常重要的,它直接影响到叉车的性能和稳定性。
一个高效的液压系统可以提供稳定的动力和控制叉车的运动。
以下是一个关于设计3吨叉车液压系统的详细说明,本文将超过1200字。
液压系统是叉车的核心部分,主要由以下组件组成:液压泵、液压缸、液压阀和液压油箱。
设计一个3吨叉车液压系统时,需要考虑以下几个关键因素。
首先,需要确定叉车所需的最大承载能力和升降高度。
这将决定液压泵和液压缸的规格。
一般来说,叉车的液压泵应具备足够的流量和压力以提供所需的动力。
在选择液压泵时,需要考虑到叉车的重量和升降高度,同时还要考虑到其他附加设备的需求,如辅助叉、夹具等。
其次,需要选择适当的液压阀。
液压阀的功能是控制液压系统的流量和压力,并确保系统的稳定性和安全性。
在设计3吨叉车的液压系统时,需要考虑到叉车的操作需求和环境条件。
例如,如果叉车需要在不同的高度上工作,那么需要选择有多个工作位置的多路阀。
或者,如果叉车需要具备液压过载保护功能,那么可以选择压力过载阀。
液压油箱是液压系统的重要组成部分,它储存和供给液压油。
设计一个适当的液压油箱可以确保系统的运行平稳和流畅。
液压油箱的容量应该能够满足叉车的需求,以及储存液压油的安全性和易用性。
油箱还应该具备一定的附件,如油位指示器、油温计和过滤器等,以监测和维护油液的质量。
液压油是液压系统的传动介质,其性能直接影响到叉车的稳定性和运行效果。
在设计3吨叉车液压系统时,需要选择适合的液压油,并根据叉车的工作条件和使用频率进行定期的维护和更换。
液压油的质量应该符合叉车制造商的要求,并能够提供足够的润滑和密封性能。
除了以上的主要组件,叉车液压系统还可能包括其他附加设备,如液压缓冲器、液压减压阀和液压控制阀等,以提供更高的控制精度和操作性能。
这些附加设备的选择和安装也需要根据叉车的工作条件和需求来确定。
总之,设计一个3吨叉车液压系统需要考虑叉车的工作负荷、升降高度、操作需求和环境条件等因素。
- 1、下载文档前请自行甄别文档内容的完整性,平台不提供额外的编辑、内容补充、找答案等附加服务。
- 2、"仅部分预览"的文档,不可在线预览部分如存在完整性等问题,可反馈申请退款(可完整预览的文档不适用该条件!)。
- 3、如文档侵犯您的权益,请联系客服反馈,我们会尽快为您处理(人工客服工作时间:9:00-18:30)。
叉车工作装置液压系统设计
1 提升装置的设计
根据设计条件,要提升的负载为2100kg ,因此提升装置需承受的负载力为:
2060081.92100=⨯==mg F l N
为减小提升装置的液压缸行程,通过加一个动滑轮和链条(绳),对装置进行改进,如图1所示。
图1 提升装置示意图 由于链条固定在框架的一端,活塞杆的行程是叉车杆提升高度的一半,但同时,所需的力变为原来的两倍(由于所需的功保持常值,但是位移减半,于是负载变为原来的两倍)。
即提升液压缸的负载力为
2 F l = 41200 N
如果系统工作压力为100bar ,则对于差动连接的单作用液压缸,提升液压缸的活塞杆有效作用面积为
451041.210100
004122--⨯=⨯==p F A l r m 2
42
1041.24-⨯==d A r π m 2
所以活塞杆直径为d = 0.0724 m ,查标准(63、70、80系列),取 d = 0.070m 。
根据液压缸的最大长径比20:1,液压缸的最大行程可达到1.40 m ,即叉车杆的最大提升高度为2.80 m ,能够满足设计要求的2 m 提升高度。
因此,提升液压缸行程为1m ,活塞杆和活塞直径为70/100mm (速比2)或70/125mm (速比1.46)。
因此活塞杆的有效作用面积为
42
2
1038.540.0704-⨯=⨯==ππd A r m 2
bar A F P r l S 107105.38412004
=⨯==- 当工作压力在允许范围内时,提升装置最大流量由装置的最大速度决定。
在该动滑轮系统中,提升液压缸的活塞杆速度是叉车杆速度(已知为0.2m/s)的一半,于是提升过程中液压缸所需最大流量为:
1.01038.54max ⨯⨯==-v A q r m 3/s
23.1max ==v A q r l/min
2 系统工作压力的确定
系统最大压力可以确定为大约在110bar 左右,如果考虑压力损失的话,可以再稍高一些。
3 倾斜装置的设计
倾斜装置所需的力取决于它到支点的距离,活塞杆与叉车体相连。
因此倾斜液压缸的尺寸取决于它的安装位置。
安装位置越高,即距离支点越远,所需的力越小。
图2 倾斜装置示意图
假设r =0.5m ,倾斜力矩给定为T =7500 N.m ,因此倾斜装置所需的作用力F 为:
150005
.07500===r T F N 如果该作用力由两个双作用液压缸提供,则每个液压缸所需提供的力为7500N 。
如果工作压力为100bar ,则倾斜液压缸环形面积A a 为:
45105.710100
7500--⨯=⨯==p F A a m 2 由于负载力矩的方向总是使叉车杆回到垂直位置,所以倾斜装置一直处于拉
伸状态,不会弯曲。
假设活塞直径D=40mm ,环形面积给定,则活塞杆直径可以用如下方法求出。
)(4
22d D A a -=π 0.025=d m
为了保证环形面积大于所需值,活塞杆直径必须小于该计算值,取0.022=d m ,则环形面积为:
24622221077.810)2240(4
)(4m d D A a --⨯=⨯-=-=ππ 倾斜机构所需最大压力为:
54105.8510
77.87500⨯=⨯==-a A F p Pa =85.5 bar 而液压缸工作压力为110bar ,因此有足够的余量。
倾斜系统所需的最大流量出现在倾斜液压缸的伸出过程中,此时液压缸无杆腔充满液压油,因此应按照活塞端部一侧计算,活塞面积用如下公式计算:
2204.04
4⨯==ππD A p =12.6×
10-4 m 2 倾斜装置所需最大速度给定为2º/s ,先转换成弧度制,然后再转换成线速度: 22deg/2/0.0349/360
s rad s rad s πω=== 0.03490.50.0175/V r m s ω=⨯=⨯=
因此,两个液压缸在伸出过程中所需的流量为:
0175.0106.122242⨯⨯⨯==-v A q p = 0.43981 m 3/s = 2.6 l/min
倾斜装置需要走过的行程为:
200.50.175180
S m π=⨯⨯= 综上,两个倾斜液压缸的可选尺寸为40/22mm/mm ,行程为200mm 。
4 油路设计
对于提升工作装置,单作用液压缸就能够满足工作要求,因为叉车体的重量能使叉车杆自动回到底部。
液压缸不必有低压出口,高压油可同时充满活塞环形面和另一面(构成差动缸),由于活塞两侧面积的不同而产生提升力。
为减少管道连接,可以通过在活塞上面钻孔实现液压缸两侧的连接。
倾斜装置通常采用两个液压缸驱动,以防止叉车杆发生扭曲变形。
行走机械液压系统中通常采用中位卸荷的多路换向阀(中路通)控制多个液压缸的动作,如图3所示。
图3 中位卸荷的多路换向阀(中路通)控制的液压系统也可采用另一种稍有不同的双泵供油方案,先确定基本油路组成,然后再加入安全装置,如图4所示。
注意前述大部分计算过程对所有油路设计方案都适用,包括引入中通多路换向阀的设计。
提升和倾斜两个装置都需要通过比例控制阀来控制,比例阀由手动操纵杆和对中弹簧来操纵。
液压系统原理图中还应增加液压泵,油箱和两个溢流阀以保证安全,溢流阀可以用于调节供油压力的大小。
由于提升和倾斜两个工作装置的流量差异很大但相对都比较小,因此采用两个串联齿轮泵比较合适。
大齿轮泵给提升装置供油,小齿轮泵给倾斜装置供油。
齿轮泵与中通比例换向阀相连,当系统不工作时,两个泵处于卸荷状态,这样可以提高系统的效率。
图4 双泵供油方案的液压系统
另外,用于提升装置的方向控制阀可选用标准的四通阀,其B口应该与油箱相连不应堵塞。
这样,当叉车杆处于下降状态,泵卸荷时,液压油可以直接流回油箱,有利于提高系统效率。
基本油路确定后,油路还不能正常工作,因为没有安全保护装置,也没有调节流量(为限制负载下降速度而流出液压缸的流量)的装置。
可以通过引入一个安全阀,从而在负载下落时限制负载下落速度来解决这个问题,也可以在每个进油路上加一个单向阀,防止油液倒流。
因为存在负值负载(与活塞运动方向相同的负载),所以倾斜系统的回路设计稍微有所不同。
上述回路设计过程中,应对如下两个问题加以注意:
1环形面一侧一直处于增压状态,有可能通过方向阀产生泄漏;
2防止在活塞另一侧产生气穴现象(设置防气穴阀)。
5 液压阀的选择
所有液压阀通过的流量至多为23.1l/min,所以阀的尺寸很小。
如果采用的是串联泵,则倾斜装置子系统流过的流量至多为3 l/min。
为考虑系统的压力损失(管路和各方向阀造成的),液压系统提供的压力应
比负载所需压力高15~20bar :
bar P s 12215107max =+=
溢流阀的调定压力应高于供油压力10%左右,即设成135bar 比较合适。
溢流阀的最大压力值可能比135bar 还高,甚至超过150bar 。
注意:
与使用中通旁路式多路换向阀相比,使用标准方向阀可以节省成本。
但是,使用标准方向阀需要多增加一个溢流阀和一个泵,即使用两个溢流阀和一个串联泵。
5.1 提升系统液压阀选择
由以上计算可知:提升子系统最大流量为23.1L/min 。
选择溢流阀的型号为DBDS10P10;
选择单向阀的型号为RVP-10-1-0;
选择顺序背压阀的型号为BXY-Fg6/10,通径10mm ,最高工作压力20MPa ; 选择手动换向阀的型号为WMM6。
5.2 倾斜系统液压阀选择
由以上计算可知:倾斜子系统最大流量为2.6L/min 。
选择溢流阀的型号为DBDH6P10,压力范围2.5~63MPa,额定流量330L/min ,公称直径6mm 。
选择单向阀的型号为RVP6-1-0,公称通径6mm,最大工作压力31.5MPa ,最大流量18~1500L/min 。
选择换向阀型号为4WMM6,通径6mm ,流量60L/min ,油口A 、B 、P 最大工作压力31.5MPa ,T 口最大工作压力16MPa 。
6 液压泵的参数确定
提升:
图3所示油路,采用结构简单、价格低廉的齿轮泵就能够满足设计要求。
假定齿轮泵的容积效率为90%,电机转速为1500r/m ,则泵的排量为:
1.171500
9.023100=⨯=req D cm 3/rev 从Sauer-Danfoss 目录中可查出,SNP2系列有排量为16.8和19.2cm 3/rev 的泵。
应选择排量为16.8cm 3/rev(与17.1更接近)的液压泵SNP2/019
倾斜:
92.11500
9.00026=⨯=
req D cm 3/rev 第二个泵的排量为1.92 cm 3/rev ,可选择SNP1/2.2
7 电动机功率
在最大压力下的流动功率为:
5.560000
8.19100168=⨯
⨯=⨯=q p W kw 上面的数值假定的是效率为100%时得到的。
齿轮泵的效率(包括容积效率和机械效率)在80~85%之间,所以所需的电机功率为: 9.68
.05.5===ηW
W d kw。