智能避障机器人设计外文翻译
机器人机构设计中英文对照外文翻译文献
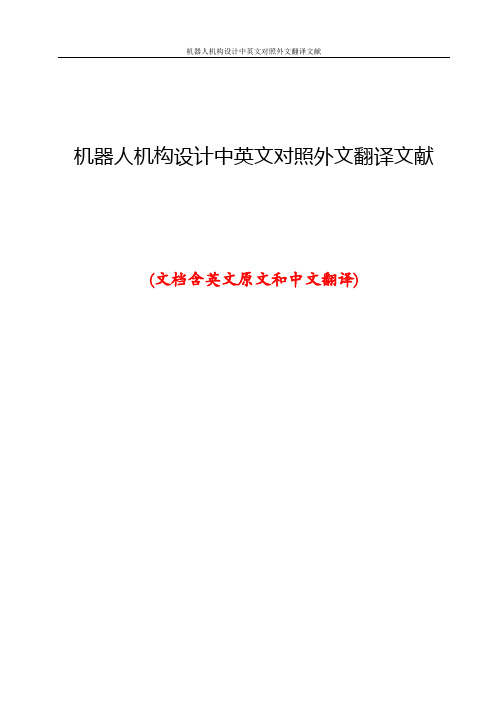
Abstract
In optimal design for robot structures, design modelsneed to he modified and computed repeatedly. Becausemodifying usually can not automaticallyberun, itconsumes a lot of time.Thispaper gives a method thatuses APDL language of ANSYS5.5software togenerate an optimal control program, which mikeoptimal procedure run automatically and optimalefficiency be improved.
A lot of methods are used in optimization design ofstructure. Finite element method is a much effectivemethod. In general, modeling and modifying are manual,whichisfeasible when model is simple. When modeliscomplicated, optimization timeislonger. In the longeroptimization time, calculation time is usually very little,a majorityoftime is used for modeling and modifying.It is key of improving efficiency of structureoptimization how to reduce modeling and modifyingtime.
智能避障机器人设计与研究(硬件)毕业设计论文

(3)遥控移动机器人。
(4)环境与机器人集成。像人需要道路、交通信号灯等一样,机器人为了在一个动态变化的环境中行动,也同样需要基础设施。
(5)生态机器人学(生物机器人学)。
(6)多机器人系统。主要是获取机器人团队协调和控制技术,并将其应用于战略重要情况。
关键词:智能避障机器人,红外传感器,单片机,L298N,PWM调速
THEDESIGN AND STUDY OF INTELLIGENT OBSTACLE AVOIDANCE ROBOT(HARDWARE)
ABSTRACT
In scientific exploration and emergency rescue often encounter some danger or human can not directly reach the area of detection,these will need to use the robot to complete. Therobot'sautomaticobstacleavoidancemovementin complex terrainis an essential and most basic function. Therefore,the automatic obstacle avoidance system development is made. Automatic obstacle avoidancerobotdevelopment based on thissystemis made of. With the development of technology for the unknown space and mankind can not be directly accessible to gradually become a hot area of exploration,which makes the automatic obstacle avoidance robot has great significance. Automatic obstacle avoidance robotcan serve as a regional exploration and emergency rescue robot system that allows robots to automatically avoid obstacles in the road.
机器人 外文翻译 外文文献 英文文献 采用模糊逻辑控制使自主机器人避障设计

Autonomous robot obstacle avoidance using a fuzzy logic control schemeWilliam MartinSubmitted on December 4, 2009CS311 - Final Project1. INTRODUCTIONOne of the considerable hurdles to overcome, when trying to describe areal-world control scheme with first-order logic, is the strong ambiguity found in both semantics and evaluations. Although one option is to utilize probability theory in order to come up with a more realistic model, this still relies on obtaining information about an agent's environment with some amount of precision. However, fuzzy logic allows an agent to exploit inexactness in its collected data by allowing for a level of tolerance. This can be especially important when high precision or accuracy in a measurement is quite costly. For example, ultrasonic and infrared range sensors allow for fast and cost effective distance measurements with varying uncertainty. The proposed applications for fuzzy logic range from controlling robotic hands with six degrees of freedom1 to filtering noise from a digital signal.2 Due to its easy implementation, fuzzy logic control has been popular for industrial applications when advanced differential equations become either computationally expensive or offer no known solution. This project is an attempt to take advantage of these fuzzy logic simplifications in order to implement simple obstacle avoidance for a mobile robot. 2. PHYSICAL ROBOT IMPLEMENTATION2.1. Chassis and sensorsThe robotic vehicle's chassis was constructed from an Excalibur EI-MSD2003 remote control toy tank. The device was stripped of all electronics, gears, and extraneous parts in order to work with just the empty case and two DC motors for the tank treads. However, this left a somewhat uneven surface to work on, so high-density polyethylene (HDPE) rods were used to fill in empty spaces. Since HDPE has a rather low surface energy, which is not ideal for bonding with other materials, a propanetorch was used to raise surface temperature and improve bonding with an epoxy adhesive.Three Sharp GP2D12 infrared sensors, which have a range of 10 to 80 cm, were used for distance measurements. In order to mount these appropriately, a 2.5 by 15 cm piece of aluminum was bent into three even pieces at 135 degree angles. This allows for the IR sensors to take three different measurements at 45 degree angles (right, middle, and left distances). This sensor mount was then attached to an HDPE rod with mounting tape and the rod was glued to the tank base with epoxy. Since the minimum distance that can be reliably measured with these sensors is 10 cm, the sensors were placed about 9 cm from the front of the vehicle. This allowed measurements to be taken very close to the front of the robot.2.2. ElectronicsIn order to control the speed of each motor, pulse-width modulation (PWM) was used to drive two L2722 op amps in open loop mode (Fig. 1). The high input resistance of these ICs allow for the motors to be powered with very little power draw from the PWM circuitry. In order to isolate the motor's power supply from the rest of the electronics, a 9.6 V NiCad battery was used separately from a standard 9 V that demand on the op amps led to a small amount of overheating during continuous operation. This was remedied by adding small heat sinks and a fan to the forcibly disperse heat.Fig. 1. The control circuit used for driving each DC motor. Note that the PWM signal was between 0 and 5 V.2.3. MicrocontrollerComputation was handled by an Arduino Duemilanove board with anATmega328 microcontroller. The board has low power requirements and modifications. In addition, it has a large number of prototyping of the control circuit and based on the Wiring language. This board provided an easy and low-cost platform to build the robot around.3. FUZZY CONTROL SCHEME FORIn order to apply fuzzy logic to the robot to interpret measured distances. While the final algorithm depended critically on the geometry of the robot itself and how it operates, some basic guidelines were followed. Similar research projects provided both simulation results and ideas for implementing fuzzy control.3,4,53.1. Membership functionsThree sets of membership functions were created to express degrees of membership for distances, translational speeds, and rotational speeds. This made for a total of two input membership functions and eight output membership functions (Fig.2). Triangle and trapezoidal functions were used exclusively since they are quick to compute and easy to modify. Keeping computation time to a minimum was essential so that many sets of data could be analyzed every second (approximately one every 40 milliseconds). The distance membership functions allowed the distances from the IR sensors to be quickly "fuzzified," while the eight speed membership functions converted fuzzy values back into crisp values.3.2.Rule baseOnce the input data was fuzzified, the eight defined fuzzy logic rules (Table I) were executed in order to assign fuzzy values for translational speed and rotation. This resulted in multiple values for the each of the fuzzy output components. It was then necessary to take the maximum of these values as the fuzzy value for each component. Finally, these fuzzy output values were "defuzzified" using themax-product technique and the result was used to update each of the motor speeds.(a)(b)(c)rotational speed. These functions were adapted from similar work done in reference 3.4. RESULTSThe fuzzy control scheme allowed for the robot to quickly respond to obstacles itcould detect in its environment. This allowed it to follow walls and bend aroundcorners decently without hitting any obstacles. However, since the IR sensors'measurements depended on the geometry of surrounding objects, there were times when the robot could not detect obstacles. For example, when the IR beam hit a surface with oblique incidence, it would reflect away from the sensor and not register as an object. In addition, the limited number of rules used may have limited the dynamics of the robot's responses. Some articles suggest as many as forty rules6 should be used, while others tend to present between ten and twenty. Since this project did not explore complex kinematics or computational simulations of the robot, it is difficult to determineexactly how many rules should be used. However, for the purposes of testing fuzzy logic as a navigational aide, the eight rules were sufficient. Despite the many problems that IR and similar ultrasonic sensors have with reliably obtaining distances, the robustness of fuzzy logic was frequently able to prevent the robot from running into obstacles.5. CONCLUSIONThere are several easy improvements that could be made to future iterations of this project in order to improve the robot's performance. The most dramatic would be to implement the IR or ultrasonic sensors on a servo so that they could each scan a full 180 degrees. However, this type of overhaul may undermine some of fuzzy logic's helpful simplicity. Another helpful tactic would be to use a few types of sensors so that data could be taken at multiple ranges. The IR sensors used in this experiment had a minimum distance of 10 cm, so anything in front of this could not be reliably detected. Similarly, the sensors had a maximum distance of 80 cm so it was difficult to react to objects far away. Ultrasonic sensors do offer significantly increased ranges at a slightly increased cost and response time. Lastly, defining more membership functions could help improve the rule base by creating more fine tuned responses. However, this would again increase the complexity of the system.Thus, this project has successfully implemented a simple fuzzy control scheme for adjusting the heading and speed of a mobile robot. While it is difficult to determine whether this is a worthwhile application without heavily researching other methods, it is quite apparent that fuzzy logic affords a certain level of simplicity in thedesign of a system. Furthermore, it is a novel approach to dealing with high levels of uncertainty in real-world environments.6. REFERENCES1 Ed. M. Jamshidi, N. Vadiee, and T. Ross, Fuzzy logic and control: software and hardware applications, (Prentice Hall: Englewood Cliffs, NJ) 292-328.2 Ibid, 232-261.3 W. L. Xu, S. K. Tso, and Y. H. Fung, "Fuzzy reactive control of a mobile robot incorporating a real/virtual target switching strategy," Robotics and Autonomous Systems, 23(3), 171-186 (1998).4 V. Peri and D. Simon, “Fuzzy logic control for an autonomous robot,” 2005 Annual Meeting of the North American Fuzzy Information Processing Society, 337-342 (2005).5 A. Martinez, E. Tunstel, and M. Jamshidi, "Fuzzy-logic based collision-avoidance for a mobile robot," Robotica, 12(6) 521–527 (1994).6 W. L. Xu, S. K. Tso, and Y. H. Fung, "Fuzzy reactive control of a mobile robot incorporating a real/virtual target switching strategy," Robotics and Autonomous Systems, 23(3), 171-186 (1998).采用模糊逻辑控制使自主机器人避障设计威廉马丁提交于2009年12月4日CS311 -最终项目1 引言其中一个很大的障碍需要克服,当试图用控制逻辑一阶来描述一个真实世界设计在发现在这两个语义评价中是个强大的模糊区。
毕业论文_全方位避障车辆实时轨迹生成与控制外文翻译

毕业设计(论文) 外文翻译外文题目:Obstacle Avoiding Real-Time Trajectory Generation and Control of Omnidirectional Vehicles中文题目:全方位避障车辆实时轨迹生成与控制学院名称:电子与信息工程学院专业:电子与信息工程班级:电信092班定稿日期:2013年1 月20日全方位避障的车辆实时轨迹生成与控制摘要:本文提出了一种计算有效的,全方位移动机器人的Trajectorygeneration 算法。
该算法的计划基于一个参考路径Bezier 曲线,符合避障标准。
然后该算法解决了运动规划问题机器人跟踪路径。
在很短的旅行时间,同时满足动态约束和对噪声的鲁棒性。
加速度机器人的计算,使得它们满足每个采样时间间隔的时间的最优条件。
数值模拟演示了改善的轨迹生成的旅行时间,与以前的研究相比,有动态约束的满意度和平滑的运动控制1.引言许多研究人员都工作于对汽车运动规划。
该车辆的形式,包括汽车,差驱动器,全方位,和其他车型。
Balkcom[3]提出的有限速度模型的差分驱动机器人的时间最优轨迹。
荣格[4]摩尔[5]处理全方位的车辆; 这些论文采用的控制策略包括建立的几何路径和跟踪的路径和使用反馈跟踪路径控制。
黄[6]提出一种视觉导引方法根据模型的非完整机器人的本地导航人类导航。
该方法使用相对标题的目标和障碍,到目标的距离,障碍物的角宽度,计算一个潜在的领域。
“势场控制机器人的角加速度,转向朝着目标和远离障碍。
哈姆纳[7]操纵的室外移动机器人学习,通过观察一个人的司机操作配有传感器的车辆,不断的产生对当地环境的地图,以避免碰撞。
介绍实施转向控制人类行为模式,试图避免的障碍,而试图按照一个理想的路径。
黄禹锡[8]发展的轨迹跟踪和障碍避免在一个智能轿车般的移动机器人通过混合 H H 2分散控制的空间。
两个CCD 摄像机是用来实现机器人的位置和障碍物的位置。
工业机器人中英文翻译、外文文献翻译、外文翻译
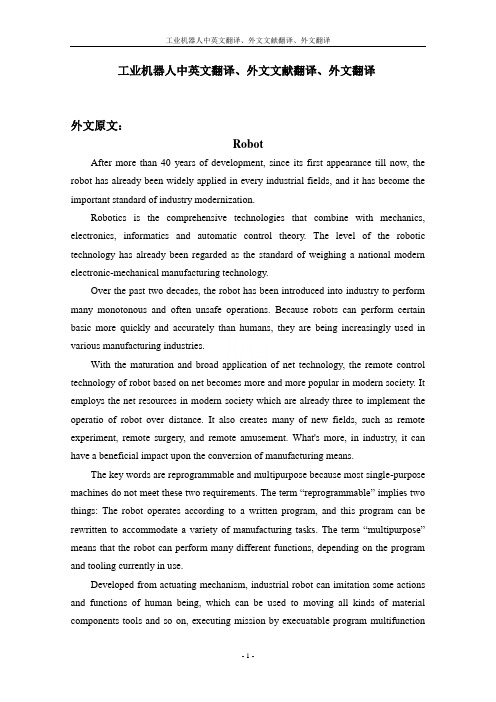
工业机器人中英文翻译、外文文献翻译、外文翻译外文原文:RobotAfter more than 40 years of development, since its first appearance till now, the robot has already been widely applied in every industrial fields, and it has become the important standard of industry modernization.Robotics is the comprehensive technologies that combine with mechanics, electronics, informatics and automatic control theory. The level of the robotic technology has already been regarded as the standard of weighing a national modern electronic-mechanical manufacturing technology.Over the past two decades, the robot has been introduced into industry to perform many monotonous and often unsafe operations. Because robots can perform certain basic more quickly and accurately than humans, they are being increasingly used in various manufacturing industries.With the maturation and broad application of net technology, the remote control technology of robot based on net becomes more and more popular in modern society. It employs the net resources in modern society which are already three to implement the operatio of robot over distance. It also creates many of new fields, such as remote experiment, remote surgery, and remote amusement. What's more, in industry, it can have a beneficial impact upon the conversion of manufacturing means.The key words are reprogrammable and multipurpose because most single-purpose machines do not meet these two requirements. The term “reprogrammable” implies two things: The robot operates according to a written program, and this program can be rewritten to accommodate a variety of manufacturing tasks. The term “multipurpose” means that the robot can perform many different functions, depending on the program and tooling currently in use.Developed from actuating mechanism, industrial robot can imitation some actions and functions of human being, which can be used to moving all kinds of material components tools and so on, executing mission by execuatable program multifunctionmanipulator. It is extensive used in industry and agriculture production, astronavigation and military engineering.During the practical application of the industrial robot, the working efficiency and quality are important index of weighing the performance of the robot. It becomes key problems which need solving badly to raise the working efficiencies and reduce errors of industrial robot in operating actually. Time-optimal trajectory planning of robot is that optimize the path of robot according to performance guideline of minimum time of robot under all kinds of physical constraints, which can make the motion time of robot hand minimum between two points or along the special path. The purpose and practical meaning of this research lie enhance the work efficiency of robot.Due to its important role in theory and application, the motion planning of industrial robot has been given enough attention by researchers in the world. Many researchers have been investigated on the path planning for various objectives such as minimum time, minimum energy, and obstacle avoidance.The basic terminology of robotic systems is introduced in the following:A robot is a reprogrammable, multifunctional manipulator designed to move parts, materials, tools, or special devices through variable programmed motions for the performance of a variety of different task. This basic definition leads to other definitions, presented in the following paragraphs that give a complete picture of a robotic system.Preprogrammed locations are paths that the robot must follow to accomplish work. At some of these locations, the robot will stop and perform some operation, such as assembly of parts, spray painting, or welding. These preprogrammed locations are stored in the robot’s memory and are recalled later for continuous operation. Furthermore, these preprogrammed locations, as well as other programming feature, an industrial robot is very much like a computer, where data can be stored and later recalled and edited.The manipulator is the arm of the robot. It allows the robot to bend, reach, and twist. This movement is provided by the manipulator’s axes, also called the degrees of freedom of the robot. A robot can have from 3 to 16 axes. The term degrees of freedom will always relate to the number of axes found on a robot.The tooling and grippers are not part of the robotic system itself: rather, they areattachments that fit on the end of the robot’s arm. These attachments connected to the end of the robot’s arm allow the robot to lift parts, spot-weld, paint, arc-well, drill, deburr, and do a variety of tasks, depending on what is required of the robot.The robotic system can also control the work cell of the operating robot. The work cell of the robot is the total environment in which the robot must perform its task. Included within this cell may be the controller, the robot manipulator, a work table, safety features, or a conveyor. All the equipment that is required in order for the robot to do its job is included in the work cell. In addition, signals from outside devices can communicate with the robot in order to tell the robot when it should assemble parts, pick up parts, or unload parts to a conveyor.The robotic system has three basic components: the manipulator, the controller, and the power source.ManipulatorThe manipulator, which dose the physical work of the robotic system, consists of two sections: the mechanical section and the attached appendage. The manipulator also has a base to which the appendages are attached.The base of the manipulator is usually fixed to the floor of the work area. Sometimes, though, the base may be movable. In this case, the base is attached to either a rail or a track, allowing the manipulator to be moved from one location to anther.As mentioned previously, the appendage extends from the base of the robot. The appendage is the arm of the robot. It can be either a straight, movable arm or a jointed arm. The jointed arm is also known as an articulated arm.The appendages of the robot manipulator give the manipulator its various axes of motion. These axes are attached to a fixed base, which, in turn, is secured to a mounting. This mounting ensures that the manipulator will remain in one location.At the end of the arm, a wrist is connected. The wrist is made up of additional axes and a wrist flange. The wrist flange allows the robot user to connect different tooling to the wrist for different jobs.The manipulator’s axes allow it to perform work within a certain area. This area is called the work cell of the robot, and its size corresponds to the size of the manipulator. As the robot’s physical size increases, the size of the work cell must also increase.The movement of the manipulator is controlled by actuators, or drive system. The actuator, or drive system, allows the various axes to move within the work cell. The drive system can use electric, hydraulic, or pneumatic power. The energy developed by the drive system is converted to mechanical power by various mechanical drive systems. The drive systems are coupled through mechanical linkages. These linkages, in turn, drive the different axes of the robot. The mechanical linkages may be composed of chains, gears, and ball screws.ControllerThe controller in the robotic system is the heart of the operation. The controller stores preprogrammed information for later recall, controls peripheral devices, and communicates with computers within the plant for constant updates in production.The controller is used to control the robot manipulator’s movements as well as to control peripheral components within the work cell. The user can program the movements of the manipulator into the controller through the use of a hand-held teach pendant. This information is stored in the memory of the controller for later recall. The controller stores all program data for the robotic system. It can store several different programs, and any of these programs can be edited.The controller is also required to communicate with peripheral equipment within the work cell. For example, the controller has an input line that identifies when a machining operation is completed. When the machine cycle is completed, the input line turns on, telling the controller to position the manipulator so that it can pick up the finished part. Then, a new part is picked up by the manipulator and placed into the machine. Next, the controller signals the machine to start operation.The controller can be made from mechanically operated drums that step through a sequence of events. This type of controller operates with a very simple robotic system. The controllers found on the majority of robotic systems are more complex devices and represent state-of-the-art electronics. This is, they are microprocessor-operated. These microprocessors are either 8-bit, 16-bit, or 32-bit processors. This power allows the controller to the very flexible in its operation.The controller can send electric signals over communication lines that allow it to talk with the various axes of the manipulator. This two-way communication between therobot manipulator and the controller maintains a constant update of the location and the operation of the system. The controller also controls any tooling placed on the end of the robot’s wrist.The controller also has the job of communicating with the different plant computers. The communication link establishes the robot as part of a computer-assisted manufacturing (CAM) system.As the basic definition stated, the robot is a reprogrammable, multifunctional manipulator. Therefore, the controller must contain some type of memory storage. The microprocessor-based systems operate in conjunction with solid-state memory devices. These memory devices may be magnetic bubbles, random-access memory, floppy disks, or magnetic tape. Each memory storage device stores program information for later recall or for editing.Power supplyThe power supply is the unit that supplies power to the controller and the manipulator. Two types of power are delivered to the robotic system. One type of power is the AC power for operation of the controller. The other type of power is used for driving the various axes of the manipulator. For example, if the robot manipulator is controlled by hydraulic or pneumatic drives, control signals are sent to these devices, causing motion of the robot.For each robotic system, power is required to operate the manipulator. This power can be developed from either a hydraulic power source, a pneumatic power source, or an electric power source. These power sources are part of the total components of the robotic work cell.Classification of RobotsIndustrial robots vary widely in size, shape, number of axes, degrees of freedom, and design configuration. Each factor influences the dimensions of the robot’s working envelope or the volume of space within which it can move and perform its designated task. A broader classification of robots can been described as blew.Fixed and Variable-Sequence Robots. The fixed-sequence robot (also called a pick-and place robot) is programmed for a specific sequence of operations. Its movements are from point to point, and the cycle is repeated continuously. Thevariable-sequence robot can be programmed for a specific sequence of operations but can be reprogrammed to perform another sequence of operation.Playback Robot. An operator leads or walks the playback robot and its end effector through the desired path. The robot memorizes and records the path and sequence of motions and can repeat them continually without any further action or guidance by the operator.Numerically Controlled Robot. The numerically controlled robot is programmed and operated much like a numerically controlled machine. The robot is servo-controlled by digital data, and its sequence of movements can be changed with relative ease.Intelligent Robot. The intellingent robot is capable of performing some of the functions and tasks carried out by human beings. It is equipped with a variety of sensors with visual and tactile capabilities.Robot ApplicationsThe robot is a very special type of production tool; as a result, the applications in which robots are used are quite broad. These applications can be grouped into three categories: material processing, material handling and assembly.In material processing, robots use to process the raw material. For example, the robot tools could include a drill and the robot would be able to perform drilling operations on raw material.Material handling consists of the loading, unloading, and transferring of workpieces in manufacturing facilities. These operations can be performed reliably and repeatedly with robots, thereby improving quality and reducing scrap losses.Assembly is another large application area for using robotics. An automatic assembly system can incorporate automatic testing, robot automation and mechanical handling for reducing labor costs, increasing output and eliminating manual handling concerns.Hydraulic SystemThere are only three basic methods of transmitting power: electrical, mechanical, and fluid power. Most applications actually use a combination of the three methods to obtain the most efficient overall system. To properly determine which principle method to use, it is important to know the salient features of each type. For example, fluidsystems can transmit power more economically over greater distances than can mechanical type. However, fluid systems are restricted to shorter distances than are electrical systems.Hydraulic power transmission systems are concerned with the generation, modulation, and control of pressure and flow, and in general such systems include:1.Pumps which convert available power from the prime mover to hydraulicpower at the actuator.2.Valves which control the direction of pump-flow, the level of powerproduced, and the amount of fluid-flow to the actuators. The power level isdetermined by controlling both the flow and pressure level.3.Actuators which convert hydraulic power to usable mechanical power outputat the point required.4.The medium, which is a liquid, provides rigid transmission and control aswell as lubrication of components, sealing in valves, and cooling of thesystem.5.Connectors which link the various system components, provide powerconductors for the fluid under pressure, and fluid flow return totank(reservoir).6.Fluid storage and conditioning equipment which ensure sufficient quality andquantity as well as cooling of the fluid..Hydraulic systems are used in industrial applications such as stamping presses, steel mills, and general manufacturing, agricultural machines, mining industry, aviation, space technology, deep-sea exploration, transportation, marine technology, and offshore gas and petroleum exploration. In short, very few people get through a day of their lives without somehow benefiting from the technology of hydraulics.The secret of hydraulic system’s success and widespread use is its versatility and manageability. Fluid power is not hindered by the geometry of the machine as is the case in mechanical systems. Also, power can be transmitted in almost limitless quantities because fluid systems are not so limited by the physical limitations of materials as are the electrical systems. For example, the performance of an electromagnet is limited by the saturation limit of steel. On the other hand, the powerlimit of fluid systems is limited only by the strength capacity of the material.Industry is going to depend more and more on automation in order to increase productivity. This includes remote and direct control of production operations, manufacturing processes, and materials handling. Fluid power is the muscle of automation because of advantages in the following four major categories.1.Ease and accuracy of control. By the use of simple levers and push buttons,the operator of a fluid power system can readily start, stop, speed up or slowdown, and position forces which provide any desired horsepower withtolerances as precise as one ten-thousandth of an inch. Fig. shows a fluidpower system which allows an aircraft pilot to raise and lower his landinggear. When the pilot moves a small control valve in one direction, oil underpressure flows to one end of the cylinder to lower the landing gear. To retractthe landing gear, the pilot moves the valve lever in the opposite direction,allowing oil to flow into the other end of the cylinder.2.Multiplication of force. A fluid power system (without using cumbersomegears, pulleys, and levers) can multiply forces simply and efficiently from afraction of an ounce to several hundred tons of output.3.Constant force or torque. Only fluid power systems are capable of providingconstant force or torque regardless of speed changes. This is accomplishedwhether the work output moves a few inches per hour, several hundred inchesper minute, a few revolutions per hour, or thousands of revolutions perminute.4.Simplicity, safety, economy. In general, fluid power systems use fewermoving parts than comparable mechanical or electrical systems. Thus, theyare simpler to maintain and operate. This, in turn, maximizes safety,compactness, and reliability. For example, a new power steering controldesigned has made all other kinds of power systems obsolete on manyoff-highway vehicles. The steering unit consists of a manually operateddirectional control valve and meter in a single body. Because the steering unitis fully fluid-linked, mechanical linkages, universal joints, bearings, reductiongears, etc. are eliminated. This provides a simple, compact system. Inapplications. This is important where limitations of control space require asmall steering wheel and it becomes necessary to reduce operator fatigue.Additional benefits of fluid power systems include instantly reversible motion, automatic protection against overloads, and infinitely variable speed control. Fluid power systems also have the highest horsepower per weight ratio of any known power source. In spite of all these highly desirable features of fluid power, it is not a panacea for all power transmission problems. Hydraulic systems also have some drawbacks. Hydraulic oils are messy, and leakage is impossible to completely eliminate. Also, most hydraulic oils can cause fires if an oil leak occurs in an area of hot equipment.Pneumatic SystemPneumatic system use pressurized gases to transmit and control power. As the name implies, pneumatic systems typically use air (rather than some other gas ) as the fluid medium because air is a safe, low-cost, and readily available fluid. It is particularly safe in environments where an electrical spark could ignite leaks from system components.In pneumatic systems, compressors are used to compress and supply the necessary quantities of air. Compressors are typically of the piston, vane or screw type. Basically a compressor increases the pressure of a gas by reducing its volume as described by the perfect gas laws. Pneumatic systems normally use a large centralized air compressor which is considered to be an infinite air source similar to an electrical system where you merely plug into an electrical outlet for electricity. In this way, pressurized air can be piped from one source to various locations throughout an entire industrial plant. The compressed air is piped to each circuit through an air filter to remove contaminants which might harm the closely fitting parts of pneumatic components such as valve and cylinders. The air then flows through a pressure regulator which reduces the pressure to the desired level for the particular circuit application. Because air is not a good lubricant (contains about 20% oxygen), pneumatics systems required a lubricator to inject a very fine mist of oil into the air discharging from the pressure regulator. This prevents wear of the closely fitting moving parts of pneumatic components.Free air from the atmosphere contains varying amounts of moisture. This moisture can be harmful in that it can wash away lubricants and thus cause excessive wear andcorrosion. Hence, in some applications, air driers are needed to remove this undesirable moisture. Since pneumatic systems exhaust directly into the atmosphere , they are capable of generating excessive noise. Therefore, mufflers are mounted on exhaust ports of air valves and actuators to reduce noise and prevent operating personnel from possible injury resulting not only from exposure to noise but also from high-speed airborne particles.There are several reasons for considering the use of pneumatic systems instead of hydraulic systems. Liquids exhibit greater inertia than do gases. Therefore, in hydraulic systems the weight of oil is a potential problem when accelerating and decelerating and decelerating actuators and when suddenly opening and closing valves. Due to Newton’s law of motion ( force equals mass multiplied by acceleration ), the force required to accelerate oil is many times greater than that required to accelerate an equal volume of air. Liquids also exhibit greater viscosity than do gases. This results in larger frictional pressure and power losses. Also, since hydraulic systems use a fluid foreign to the atmosphere , they require special reservoirs and no-leak system designs. Pneumatic systems use air which is exhausted directly back into the surrounding environment. Generally speaking, pneumatic systems are less expensive than hydraulic systems.However, because of the compressibility of air, it is impossible to obtain precise controlled actuator velocities with pneumatic systems. Also, precise positioning control is not obtainable. While pneumatic pressures are quite low due to compressor design limitations ( less than 250 psi ), hydraulic pressures can be as high as 10,000 psi. Thus, hydraulics can be high-power systems, whereas pneumatics are confined to low-power applications. Industrial applications of pneumatic systems are growing at a rapid pace. Typical examples include stamping, drilling, hoist, punching, clamping, assembling, riveting, materials handling, and logic controlling operations.工业机器人机器人自问世以来到现在,经过了40多年的发展,已被广泛应用于各个工业领域,已成为工业现代化的重要标志。
介绍机器人制作过程的英文作文

介绍机器人制作过程的英文作文Robotics: The Art of Creating Intelligent Machines.Robotics is an exciting and rapidly evolving field that combines elements of engineering, computer science, and artificial intelligence. The goal of robotics is to create machines that can automate tasks, perform complex operations, and interact with the world around them. The process of building a robot involves a series of steps, from design and programming to testing and deployment.1. Design and Conceptualization.The first step in the robotic creation process is to design the robot's physical structure and determine its functionality. This involves defining the robot's size, shape, and the materials that will be used in its construction. The designer must also consider the robot's intended purpose and the environment in which it will operate.2. Mechanical Engineering.Once the design is complete, the robot's mechanical components must be engineered. This includes designing and building the robot's body, joints, and actuators. The materials used in the robot's construction must becarefully selected to ensure that the robot is strong, durable, and lightweight.3. Electrical Engineering.The next step is to design and implement the robot's electrical systems. This includes the robot's power supply, sensors, and actuators. The robot's electrical system must be designed to be efficient and reliable, and it must be able to withstand the rigors of the robot's intended environment.4. Programming.Once the robot's mechanical and electrical systems arecomplete, the robot must be programmed. The robot's program will dictate how the robot behaves and interacts with its environment. The program must be written in a language that the robot's computer can understand, and it must be carefully tested and debugged to ensure that the robot functions as intended.5. Testing and Deployment.Once the robot is programmed, it must be thoroughly tested to ensure that it meets the design specifications. The robot should be tested in a variety of environments and conditions to ensure that it is robust and reliable. Once the robot has passed all of the necessary tests, it can be deployed for its intended purpose.Conclusion.The process of building a robot is a complex and challenging task, but it is also a rewarding one. By combining the fields of engineering, computer science, and artificial intelligence, robotics engineers are creatingmachines that are capable of performing amazing feats. As the field of robotics continues to evolve, we can expect to see even more incredible robots in the years to come.。
智能机器人外文翻译
智能外文翻译智能外文翻译:1、简介智能是一种具备和机械结构的智能设备,可以执行复杂的任务并与人类进行互动。
本文将介绍智能的基本原理、分类以及应用领域。
2、历史发展智能的发展可以追溯到20世纪初,随着计算机技术和机械工程的进步,智能逐渐成为可能。
自动驾驶汽车、智能和工业生产中的等都是智能在不同领域的应用。
3、工作原理智能的工作原理涉及多个学科领域,包括计算机科学、机器学习和机械工程等。
智能通过感知环境、处理信息和执行任务来与周围环境进行交互。
4、分类智能可以根据其功能和应用领域进行分类。
常见的分类包括家庭助方式器人、医疗、工业和军事等。
4.1 家庭助方式器人家庭助方式器人是一种智能,可以帮助处理日常家务,比如打扫房间、做饭和提供娱乐等。
4.2 医疗医疗是一种用于医疗治疗和手术操作的智能设备,可以提高手术的准确性和患者的治疗效果。
4.3 工业工业是在工业生产环节中使用的智能,可以自动执行重复性任务、提高生产效率和质量。
4.4 军事军事是用于军事作战和侦查目的的智能设备,可以替代人类执行危险任务,如拆除炸弹和侦察敌情。
5、应用领域智能的应用领域广泛,涵盖了家庭、医疗、农业、工业和军事等多个领域。
智能的使用可以提高生活质量、提高工作效率和降低人力成本。
6、附件本文档附带的附件包括相关研究论文、案例分析和技术报告等。
7、法律名词及注释7.1 (Artificial Intelligence):指由机器和计算机程序实现的模拟人类智能的能力。
7.2 机器学习(Machine Learning):是的一个分支,通过机器学习算法使机器能够根据以往的经验和数据进行学习和自我改进。
7.3 感知(Perception):智能通过感知技术获取环境信息,例如视觉、听觉和触觉等。
7.4 任务执行(Task Execution):智能根据输入信息执行特定的任务,例如物体抓取、路径规划和语音识别。
一种室内导航环境下自主智能移动机器人的研究外文文献翻译、中英文翻译、外文翻译
The investigation of an autonomous intelligent mobile robotsystem for indoor env ironment navigation AbstractThe autonomous mobile robotics system designed and implemented for indoor environmentnavigation is a nonholonomic differential drive system wih two driving wheels mounted on thesame axis driven by two PID controlled motors and two caster wheels mounted in the front andback respectively. It is furnished with multiple kinds of sensors such as IR detectors ,ulrasonicsensors ,laser line generators and cameras,constituting a perceiving system for exploring itssuroundings. Its compulation source is a simultaneously running system composed ofmultiprocessor with multitask and multiprocessing programming·Hybrid control architectureis employed on the rmbile robot to perform complex tasks. The mobile robot system isimplemented at the Center for Inelligen Design , Automation and Manufacturfing of CityUniversity of Hong KongKey words :mobile robot ; ntelligent control ; sensors ; navigationIntroductionWith increasing interest in application of autonomous mobile robots in the factory and inservice environments, many investigations have been done in areas such as design, sensing,control and navigation. etc, Autonomousreaction to the real wand, exploring the environmment,follownng the planned path wnthout collisions and carrying out desired tasks are the mainrequirements of intelligent mobile robots. As humans, we can conduct these actions easily.For robots however· it is tremendously difficult. An autonomous mobile robot should make useof various sensors to sense the environment and interpret and organize the sensed information toplan a safe motion path using some appropriate algorithms while executing its tasks. Manydifferent kinds of senors have been utilized on mobile robots, such as range sensors, lightsensors, force sensors, sound sensors, shaft encoders, gyro scope S, for obstacle aw idance,localizatio n, rmtion sensing, navigation and internal rmnitoring respectively.Many people useinfrared and ulrasonic range sensors to detect obstacles in its reaching domainLaser rangefinders are also employed in obstaclke awidance bchaivior of mobile robots in clutteredspace.Cameras are often introduced into the vision system for mobile robot navigation.Although nany kinds of sensors are available·sensing doesn't mean rmnation obtained by sensors from the environment must be carefully processed andorganized in order that it can be fully utilized for the mobile robot's reaction to the dynamicallychanging real world. Localizing locally or globally·orienting the direction of mbile robot inorder to eventually reach the destination and aพiding obstacles in the proximity normally are thefundamental elementary capabilities expected of rmbile robots. Some of the more popularmethods for achieving these tasks include edge-detection, certainty grids and potential fields.Due to the shortcoming of these methodobogies (for example. high burden ofcomputation. localminima. etc.)fuzzy logic and artic ia] neural networks have been introduced into integrating thesensed information for mobile robot localization and navigation. and rmtion control of mobilerobots. Using fuzzy logic we avid some of computational botlenecks associated wrath theplanning phase of the methods based on the model of warkspace employed in traditionalarifcial ntellignce systems.Although the fuzzy control method is robust. it cannot adaptto changing parameters over time.Learning of neural network is then used for de fning mappingbetween input and ouput data of fuzzy control. Surender enbeds fuzzy rules and membershipknowledge into a neural network for trining via a back propagation algorithm. Kalman filertechniques are also efficient approaches for integrating multi- sensor informationand tracking in incremental localization.For the control of mobile robots having multiple bchaviors, Brooks proposed thesubsumption architecture, which describes the mechanism of 'arbitration between the ayeredtask- achieving behaviors. Arbitration is a process of deciding which behavior should takeprecedence over other behaviors when confticting behaviors aretriggered. Arkin presented the schema- based reactive control idea that decomposes actions intoa set of multipl concurrent processes called motor schemas. Each schema represents พgeneral behavior;a collection of such schemas provides the potential family of actions forcontrol of a mobile robot. Fach of basic active bchaviors generates a velocity vector based onsensory data, and the result is transmitted to the robot for execution Lang used state nachinearchitecture to realize the transition armng basic bchaviors. In the mechanism based on thisarchiecture, basic behaviors as well as reasoning· inference and scarch procedures can beintegrated to achieve complex tasks. This paper reports the implementation of our auonomousintelligent mobile robot. The aspects menboned above are discussed in the paper, respectively.A verview of the mobile robot systemAn nelligent autonomous rmbile robot basically should have the abilities 10exploring its surrounding area, processing data, mke decisions as well as move itself. Ourrmbilerobot system is grouped into several subsysterns :mechanics and driving subsystem,sensing subsystern, computing sources subsystem·dec ision- making subsystem and powersupplingng subsystem.The mechanical shape and driving type are commonly first taken into cons ideration whileimplementing a rmbile robot. A robot's shape can have a strong impact on how robustit is, andDC serve rmtors or stepOper motors are often the two choices to employ as actuators. The shapeof a robot may ffect its configurations of components, ae sthetics, and even the movementbehaviors of the robot. An improper shape can make robot run a greater risk of being trapped inaluttered room or of failing to find its way through a narrow space. We choose an octahedralshape that has both advantages of rectangular and circular shapes, and overcomes theirdrawbacks. The framework of the octahedral shaped robot is easy to make, components insideare easily arrange and can pass through narrow places and rotate wrath corners and nearbyobjects, and is more aesthetic in appearance.The perception subsystem accomplishes the task of getting various data from thesurroundings, including distance of the robot from obstacles, landmarks, etc. Infrared andulrasonic range sen)rs, laser rangefinders and cameras are utilized and mounted on the rmbilerobot to achieve perception of the environment. These sensors are controlled independently bysome synchronously running microprocessors that are arranged wrath distributive manner, andactivated by the main processor on which a supervising programruns. At present, infrared andultranic sensors, laser rangefinders are programmed to detect obstacles and measure distance ofthe robot from objects in the environment, and cameras are programmed for the purpose ofkoalzaton 'and navigätion.h! che7llancomThe decision- mak ing subsystem is the most important part of an ntellient mobile robotthat organizes and utilizes the information obtained from the perception subsystem. It obtainsreasonable results by some intelligent control algorithm and guides the rmbile robot. On ourmobile robotic system intelligence is realized based on behaviourism and classicalplanning principles. The decision- making system is composed of twa levels global taskplanning based on knowledge base and map of work ing enviro nment, reactive control to dealwith the dynamic real workd. Reaction tasks in the decision- mak ing system are decomposedinto classes of behaviors that the robot exhibits to accomplish the task. Fuzzy logic is used toimplement some basic behaviors. A state machine mechanism is applied to coordinate differentbehaviors,Because many kinds of electronic components such as range sensors, cameras, framegrabbers, laser line generators , microprocessors, DC motors, encoders, are employed on themobile robot, a power source must supply various voltage levels which should are stable andhave sufficient power. As the most common solution to power source of mobile robots, twosealed lead acid batteries in series writh 24 V ouput are employed in our mobile robot for thermtor drive components and electronic components which require24V, 15V, 1 12V, +9V,1: 5V, variously. For the conversion and regulation of the voltage, swritching DC DCconverters are used because of theirhigh efficiency, low output ripple and noise, and wrideinput voltage range.Three main proce sors are Motorola MC68040 based single board computers on which somesupervisory programs and decision- making programs run. These MC68040 boards runin paralle1 and share memory using a VMEbus. Three motorola MC68HC11 basedcontrollers act as the lower level controllers of the infrared and ultranic range senors, whichcommunicate with the main processors through serial ports. The multi-processor system isorganized into a hierarchical and distributive structure to implement fast gathering of informationand rapid reaction. Harmony, a multiprocessing and multitasking operating system forreal-time control, runs on the main processors to implement multiprocessing and multitaskingprogramming. Harmony is a runtime only enviroment and program executions are performedby downloading crosscompiled executable images into target processors. The hardwarearchitecture of the mobile robot is shown in Fig.Robots controlFor robots, the three rmst comrmn drive systems are wheels, tracks and legs. Wheeled robotsare mechanically simpler and easier to construct than legged and tracked systens that generallyrequire more complex and heavier hardware, so our mobile robot is designed as a wheeled robot.For a wheeled robot, appropriate arrangements of driving and steering wheels should be chosenfrom differential, synchro, tricycle, and autonotive type drive mechanisms. Differentialdrives use twa caster wheels and two driven wheels on a common axis driven independenly,which enable the robot to move straight. in an are and turn in place. All wheels are rotalesimultaneously in the synchro drive;tricycle drive includes two driven wheels and one steeringwheel;automobile type drive rolates the front twa wheels together like a car. It is obvious thatdifferential drive is the simplest locomotion system for both programming and construction.However, a difficult problem for differentially driven robots is how to make the robot gostraight, espec ially when the motors of the two wheels encounter different loads. To followadesired path. the rmtor velocity must be controlleddynamically. In our mobile robot systemasemv motor controller is used which implements PID controlLIbwer amplifiers that drive themotors amplify the signals from each channel of serwcontroller. Feedback is provided by shaftencoders on the wheels. The block diagram of the motor control electronic components areshown in Fig.2, and the strategy of two wheel speed contro based PID principle is ilutrated inFig3.Top loop is for track ing the desired left motor velocity;bottom loop for track ing right motorvelocity;Integral loop ensures the robot to go straight as desired and controls the steering of therobot. This is a simple PI control that can satisfy the general requirements.Sensing subsystemSensor based planning makes use of sensor information reflecting the current state of theenvironment, in contrast to classical planning, W hich assumes full knowledge of the environmentprior to planning. The perceptive subsystem integrates the visual and proximity senors for thereaction of the robot. It plays an important role in the robot behavioral decision- makingprocesses and motion controlField of view of perceptive subsystem is the first cons ideration in the design of the sensingsystem Fneld of view should be wide enough with suffic ient depth of field to understand wellthe robot's surroundings. Multiple sensors can provide information that is difficult to extractfrom single sensor systems. Multiple sensors are complementary to each other, providing a betterunderstanding of the work environment. Omnidiretional sensory capability is endowed on ourmobile robot. When attempting to utilize multiple senors, it must be decided how manydifferent kinds of sensors are to be used in order to achieve the desired motion task, bothaccurately and economically,Ultrasonic range sensing is an attractive sensing rmdalityfor mobile robots becauseitis relatively simple to implement and process, has kow cost and energy consumption. Inaddition, high frequencies can be used to minimize interference from the suroundingenvironment. A special purpose built infrared ranging system operates similar to sonar,determining the obstacle" s presence or absence and also the distance to an object. Fordetecting smaller obstacles a laser rangefinder can be used. It can be titled down to the groundto detect the small objects near the robot. ldentifying robot self position and orientation is a basicbehavior that can be part of high level complex behaviors. For localizing a dead reckoningmethod is adopted using the output of shaft encoders. This method can have acc umulated erroron the position and orientation. Many externa sensors can be used for identification of 'positionand orientation. Cameras are the most popular sensor for this purpose, because of naturallyoccurring features ofa mom as landmarks, such as air conditioning system, fluorescent lamps,and suspended ciling frames.Any type of sensor has inherent disadvantages that need to be taken into consideration Forinfrared range senors, if there is a sharply defined boundary on the target betweendifferentmaterials, colors, etc., the sensor may not be able to calculate distance accurately. Some of theseproblems can bé ävöidëd if düe care is taken when installing and setting up the sensor.Crosstalk and specular reflection are the two main problems for ultrasonic sensors. The firingrates, blnking intervals, firing order, and timeouts of the ultrasonic sensor system canconfigured to improveperformance. Laser ranging systems can fail to detect objects made of transparent materials orwith poor light refectivity.In this work, we have chosen range sensors and imaging sensors as the primary source ofinformation The range sensors employed include ultrasonic sensors and short and longrange infrared sensors with features above mentioned. The imaging sensors comprise gray scalevideo cameras and laser range finders. Twenty- four ulrasonic sensors are arranged in a ringwith a separation angle of 15 degrees on our mobilerobot to detect the objects in a 3600 fiekd ofview. This will allow the robot to navigatearound an unstructured environment and to constructac curate sonar maps by using environmental objects as naturally occurring beacons. With thesonar system we can detect objects from a minimum range of 15 cm to a maximum range of 10.0 m Infrared range sensors use triangulation, emitting an infrared spot from an emitter, andmeasuring the pos ition of the imaged spot with a PSD (position sensitive detector).Since thesedevices use triangulation, object color, orientation, and ambient light have greater effect onsensitivity rather than accuracy. S ince the transmiss ion signal is light instead of sound, we mayexpect a dramatically shorter cycle time for obta ining all infrared sensor me asurements. A getupof 16 short and a group of 16 kong infrared sensors are mounted in twa rings with equal angularspacing on the robot. The long- range sensors have the depth of fiekds from 60 cmto3 m, andshort- range sensors from 10 em to 80 cem. An MC68HCII based controller controls each getupof senors. A task in main processor receives the digital range data via พseril port. Four EIA B/W cameras with 352 X288 pixel resolution and 65 X 50 vicw angle· and two laser linegeneratorsare set on the top of the mobile robot. The laser line generator has 2. 6 mW outputpower at 670 พm, a 60 degree fan angle withal mm line width. The line length is 20. 7"with18"distance from lens. Two of the four cameras on the top center of the robot book up at theceiling of moms for detecting the andmarks for localization, and building maps. Fach ofanother two cameras is grouped with a luser to serve as twa pairs laser range finders for objectdetection The laser range finders are fixed on the fringe of the top plate looking down to theground. Control structure and parallel computationA control architecture, in which dec ision- mmk ing strategies are embedded, determineshow a robot integrates is varous resouces(hardware and software) toachiewe a desired task. Two distinct archiectures curently being employed are behavioral andfunctional .Behavioral archiectures have quick response to highly dynamic enviro nmenlts, butlack reasoning about the environment; functionalarchitectures พuse atficial inelligencetech- niques such as search and inference operations for reaching a goal, however, haverelatively slow responsiveness to the environment. To incorporate the better qualities of botharchiectures, we employ hybrid architecture on our rmbile robot. It is composed of threelevets:functionallevel, bchavior level and task level,· shown in Fig. 4.The functional level is composed ofa set of modules that are concerned with control ofvarious sensors, senor data interpretation. and motor fcedback closed loop control, etc .This levelof modules furmishes the robot withsome basic functions.The mapping of perception and action is done at the behavioral and task leveL'Thebehavioral level is a behavioral executor that executes the behavior task accepted from tasklevel;this level guarantees quick reaction to the dynamic environment.The task level includes task planner and global planner, The mission of task planner is todecompose a task into classes of subtasks (functional task and bchavior task) some ofwhich are directed to behavioral level, and others that are first filtered by global planner and thensent to behavioral level .Based on a wand map a global planner uses Mme classical graph searchalgorithm. f or exampleA '· to produce trajectories. 'To improve the robot' s response to itsenvironment, the task planner and global planner run on the host computer, the functional andbehavioral level run on the processors embedded in the robot.一种室内导航环境下自主智能移动机器人的研究摘要:这种为室内境导航条件下设计生产的自主移动机器人系统是一个不完整的差速传动系统,它有两个安装在同一轴上通过两个PID控制的电机驱动的驱动轮和两个分别安装在前部和后部的脚轮。
机器人避障问题 (2)
机器人避障问题1. 简介机器人避障(obstacle avoidance)是指机器人通过使用各种传感器和算法来识别和避免障碍物的能力。
在自动驾驶、无人机和工业自动化等领域,机器人避障问题是一个非常重要的研究热点。
2. 避障传感器为了实现机器人的避障功能,需要配备各种传感器来获取环境信息。
常用的避障传感器包括:2.1 超声波传感器超声波传感器利用超声波的回波时间来测量机器人与障碍物之间的距离。
通过安装多个超声波传感器,可以实现对机器人周围环境的全方位感知。
2.2 激光雷达激光雷达是一种高精度的避障传感器,通过发射激光束并测量其回波时间来获取周围环境的三维信息。
激光雷达可以提供非常精确的障碍物位置和距离数据,因此被广泛应用于无人驾驶和导航系统中。
2.3 摄像头摄像头可以通过图像处理算法来识别和检测障碍物。
常用的算法包括边缘检测、目标跟踪和物体识别等。
利用摄像头可以获取丰富的视觉信息,对于机器人的避障任务具有重要意义。
3. 避障算法为了使机器人能够根据传感器获取的数据进行避障决策,需要设计和实现相应的避障算法。
常用的避障算法包括:3.1 基于障碍物距离的避障基于障碍物距离的避障算法利用传感器测量的障碍物距离信息来进行避障决策。
例如,当障碍物靠近时,机器人可以选择停下或改变方向来避免碰撞。
3.2 基于虚拟势场的避障基于虚拟势场的避障算法利用虚拟势场模型来描述机器人周围的环境。
机器人被视为一个负电荷,障碍物被视为正电荷,通过计算势能梯度来确定机器人应该前进的方向。
3.3 机器学习算法机器学习算法可以通过训练数据来学习和优化避障策略。
常用的机器学习算法包括神经网络、决策树和支持向量机等。
这些算法可以根据输入的传感器数据预测机器人的动作,从而实现避障功能。
4. 实际应用机器人避障技术已经被广泛应用于各个领域,包括但不限于以下几个方面:•自动驾驶车辆:通过避障技术,自动驾驶车辆能够在复杂的交通环境中安全地行驶。
智能机器人英文文档
Obstacle Avoidance Design for Humanoid RobotBased on Four Infrared SensorsChing-Chang Wong1*, Chi-Tai Cheng1, Kai-Hsiang Huang1, Yu-Ting Yang1,Hsiang-Min Chan1 and Chii-Sheng Yin21Department of Electrical Engineering, Tamkang University,Tamsui, Taiwan 251, R.O.C.2Metal Industries Research & Development Centre,Kaohsiung, Taiwan 811, R.O.C.AbstractAbehavior strategy of humanoid robot for obstacle avoidance based on four infrared sensors is proposed and implemented on an autonomous humanoid robot. A mechanical structure with 26 degrees of freedom is design so that an implemented small-size humanoid robot named TWNHR-III is able to accomplish five walking motions. Three walking experiments are presented to illustrate that the proposed biped structure lets TWNHR-III can move forward, turn, and slip. One electronic compass and four infrared sensors are mounted on TWNHR-III to obtain the head direction of the robot and detect obstacles, respectively. Based on the obtained information from these sensors, a decision tree method is proposed to decide one behavior from five movements: walk forward, turn right and left, and slip right and left. Two MATLAB simulations and one real experiment are presented to illustrate that the robot can avoid obstacles autonomously and go to the destination effectively.Key Words: Humanoid Robot, Autonomous Mobile Robot, Obstacle Avoidance, Decision Tree1. IntroductionAlthough the robot has been investigated for many years, there are still many issues to be studied, especially in the humanoid robots [1⎽4]. Hardware and software architectures,walking gait generation, and artificial intelligence are the main research fields of humanoid robots.Robot soccer games are used to encourage the researches on robotics and artificial intelligence (AI). Two international robot soccer associations, RoboCup [5] and FIRA[6], advance this research and hold the international competitions and the international symposiums. Robot soccer games are two teams constituted by several soccer robots to play soccer games under some size restrictions and rules. In the FIRA Cup event, several main categories are organized: the Mi cro-ro bot So ccer t ournament(MiroSot), the Simu lated ro bot So ccer t ournament (SimuroSot),the Robo t So ccer t ournament (RoboSot), and the Hu manoid ro bot So ccer t ournament (HuroSot). In the HuroSot category, the humanoid robot has to detect all information from the game field and decides its strategy by itself. There are many robots in the match field, so the robot must have the ability to avoid the collision with other robots and walk to an appropriate destination.Thus obstacle run is a competition category in the HuroSot league of FIRACup. The main idea of this competition category is used to test the ability of obstacle avoidance of the robot. In general, vision sensors, ultrasonic sensors, and infrared sensors are usually used todetect obstacles in the soccer game [7⎽11].In this paper, a mechanical structure with 26 degrees of freedom is design so that an implemented small-size humanoid robot named TWNHR-III (TaiWaN HumanoidRobot-III) is able to accomplish five walking motions:walk forward, turn right and left, and slip right and left. One digital electronic compass and four infrared sensors are installed on TWNHR-III. Based onthe information obtained from these sensors, a decision tree method is proposed to determine one behavior from these five movements in each decision so that TWNHR-III can avoid obstacles and go to a destination effectively.The rest of this paper is organized as follows: In Section 2, the system architecture of TWNHR-III is described.In Section 3, a decision tree method for obstacle avoidance is proposed and two simulation results and one practical test on TWNHR-III are described. In Section 4, some conclusions are made.2. System Architecture of TWNHR-IIIThe system architecture of TWNHR-III is described in this section. The height of TWNHR-III is 46 cm and the weight is 3.1 kg with batteries. The frameworks of TWNHR-III are mainly fabricated from aluminum alloy 5052 in order to realize the concepts of light weight, wear-resisting, high stiffness, and wide movable range.Each actuator system of the joint consists of a high torque and a gear. The rotating speed and rotating angle of each joint are designed based on the result of computer program. The mechanical structure and electronic structure of TWNHR-III are described as follows:2.1 Mechanical StructureMechanical structure design is the first step in the humanoid robot design. The degrees of freedom (DOFs) configuration for TWNHR-III is described in Figure 1,where 26 degrees of freedom are implemented and the rotational direction of each joint is defined by using the inertial coordinate system fixed on the ground. There are 2 degrees of freedom on the neck, 2 degrees of freedom on the waist and trunk, 8 degrees of freedom on the arm,and 14 degrees of freedom on the two legs. Aphotograph and some mechanical views of TWNHR-III are respectively described in Figure 2 and Figure 3.Human body mechanism basically comprises bones,joints, muscles, and tendons. It is impossible to replace all of the muscular-skeletal system by current mechanical and electronic components. Therefore, the primary goal of the humanoid robot mechanical design is to let the implemented robot can imitate equivalent human motion. A mechanical structure is designed and implemented so that the implemented humanoid robot can find the ball, walk forward, turn right and left, and slip right and left. The details of the development of the head,waist and trunk, arms, and legs are described as follows:2.1.1 HeadThe 3D mechanism design and DOFs diagram of the head are described in Figure 4, where the head of TWNHR-III has 2 degrees of freedom and each degree is described by the number in (b). The raw and pitch motions are implemented on the head so that it can turn right-and-left and up-and-down. Some corresponding behaviors between human and TWNHR-III in the joints of head are described in Table 1.2.1.2 Waist and TrunkThe 3D mechanism design and DOFs diagram of the waist and trunk are described in Figure 5, where each waist and trunk of TWNHR-III has 2 degrees of freedom and each degree is described by the number in (b). The waist and trunk are designed based on the concept that robot can adjust the trunk motions to compensate for the robot’s walk motion. Some corresponding behaviors between human and TWNHR-III in the joints of waist and trunk are described in Table 2.2.1.3 ArmsThe 3D mechanism design of the arms are described in Figure 6, where each arm of TWNHR-III has 4 degrees of freedom. The arms of the robot are designed based on some behaviors of human’sarms. For example,its arm can hold an object such as a ball. Some corresponding behaviors between human and TWNHR-III in the joints of arms are described in Table 3.2.1.4 LegsIn order to realize the normal walking motion of human,7 degrees of freedom are adopted to implement the joints of one leg. Leg is take great part weight of whole body, due to the knee joint. In order to improve the robust of the leg, two motors are designed and implemented in one knee joint. The 3D mechanism design and DOFs diagram of the legs are described in Figure 7, where each leg of TWNHR-III has 7 degrees of freedom and each degree is described by the number in (b). The legs are designed based on the concept that robot can accomplish the human walking motion. Some corresponding behaviors between human and TWNHR-III in the joints of legs are described in Table 4.2.2. Electronic StructureIn the electronic structure design for TWNHR-III,the system block diagram is described in Figure8, where 26 servomotors with high torques are used as the actuators of the robot. In order to build a fully autonomous vision based humanoid robot, a 16-bit DSP processor with a CMOS sensor is chosen to process the vision image of environment. The image of the field is captured by the CMOS sensor and the position information of the ball and goals is processed and extracted by the DSP processor.One electronic compass and four infrared sensors are mounted on TWNHR-III to obtain the head direction of the robot and detect obstacles, respectively. The installed positions and their detectable ranges of these four infrared sensors are described in Figure 9 and Figure 10, respectively.The electronic compass is mounted on the body to detect the head direction of the robot and the goal direction, respectively. The relative angle of goal direction and robot direction is shown in Figure 11. In the circuit design, the SoPC (System on a Programmable Chip) concept is applied and implemented on a FPGA chip to reduce the complexity of circuit design. The implemented FPGA chip can process the data obtained from the sensors and generate desired pulses to control the angles of servomotors. Many functions are implemented on the FPGAchip to process the data and control the robot so that the weight of the robot is reduced.2.3. Walking ExperimentsA mechanical structure with 26 degrees of freedom is design so that TWNHR-III is able to accomplish five walking motions: walk forward, turn right and left, and slip right and left. Its control method is based on the try and error method. In order to verify the effectiveness ofthe implemented humanoid robot, three basic walking skills: straight walk, turn, and slip are carried out on a horizontal even plane and described as follows:2.3.1 Straight WalkSome snapshots of straight walking of TWNHR-III are shown in Figure 12, where the distance between every white line is 5 cm. Every step of the straight walking is able to move forward 10 cm.2.3.2 TurnSome snapshots of left turning of TWNHR-III are shown in Figure 13, where the angle between every white line is 15 degrees. Each time of the robot turning is able to turn 30 degrees.2.3.3 SlipSome snapshots of right slipping of TWNHR-III are shown in Figure 14, where the distance between every white line is 5 cm. Every step of the robot slipping is able to slip 10 cm.From these experiment results, we can see that the proposed mechanical structure can let TWNHR-III move forward, turn, and slip effectively.3. Obstacle Avoidance3.1 Decision Tree MethodObstacle run is a competition category in the HuroSot league of FIRA Cup. As shown in Figure 15, there is a finish line marked on one side of the playing field. This side of the playing field is called the finish side. The opposite side of the playing field is called the start side. The two other sides are called side lines. Arobot has crossed the finish line when the robot crosses the finish plane and touches the ground in the end zone. During the obstacle run competition, the robot does not allow to touch any obstacles. The robot has to detect obstacles and the direction of the goal line. Adecision tree method based on four infrared sensors is proposed and described in Figure 16. The behavior output of the decision tree is the robot’s five basic motions including go forward, 30 degree right turn, 30 degree left turn, slip right, and slip left. Sixteen behavior situations and their corresponding movements are described in Table 5. The strategy will check the relative behavior from the decision tree before the robot move. In order to let the robot walk toward the goaldirection, the robot will adjust the robot direction to face the goal direction based on the electronic compass informationwhen he robot is in the safe situation (B16 situation).3.2 Simulation and Experiment ResultsIn order to illustrate the proposed method can successfully avoid obstacles and go to the destination,two MATLAB simulations and one real experiment are presented. Figure 17 and Figure 18 illustrate the obstacle avoidance ability of the robot by MATLAB simulation results. In Figure 17, there is one obstacle on the robot’s way to the goal line. When the robot detects the obstacle, the “slip right”behavior is made by the proposed decision tree method to avoid the obstacle based on the detected behavior situation B10. The robot keeps slipping to the right side, until there is no obstacle in front of the robot. When the detected behavior situation is changed from B10 to B16, the “move to goal line” behavior is made to let the robot walk toward the goal line. In Figure 18, there are two obstacles on the robot’s way to the goal line. The robot also chooses the behavior from the proposed behavior strateg y. At the location of “Safe point”,the robot is already in the safe situation. Therefore, the detected behavior situation is B16 to let the robot walk toward the goal line. As the robot moving forward, it detects the other obstacle. The “slip left” behavi or is made to avoid this obstacle based on the detected behavior situation B9. The detected behavior situation will change to B16 when the robot is away from this obstacle.The computer simulation results in Figure 17 andFigure 18 illustrate that the robot can effectively avoid obstacles and successfully arrive the goal line based on the proposed decision tree method. In the practical test, the proposed decision tree method implemented on the TWNHR-III in a real test ground is discussed. Six sequential image stills of TWNHR-III for a real experiment of obstacle avoidance are shown in Figure 19, where two obstacles are on the robot’s way to the goal line. Once TWNHR-III detects the obstacle via the infrared sensors, the robot will do an appropriate behavior to avoid obstacles. We can see that TWNHR-III can successfully avoid two obstacles by the proposed decision tree method.The soccer robot needs to play a soccer game autonomously. Playing soccer game is a good testplatform to verify the ability of the designed and implemented robot. There are many robots in thematch field, so the soccer robot must have the ability to avoid the collision with other robots and move to an appropriate destination. Thus the obstacle run is a competition category in the HuroSot league of FIRACup. Some basic walking experiments of TWNHR-III have been presented to illustrate that the proposed mechanical structure with 26 degrees of freedom can let TWNHR-III move forward, turn, and slip. Based on the obtained information from one compass and four infrared sensors installed on TWNHR-III, a decision tree method is proposed. Two MATLAB simulation results and one practical test on TWNHR-III have been presented to illustrate that the proposed decision tree method can let the robot effectively avoid obstacles and successfully go to the destination. One CMOS sensor is installed on TWNHR-III so that it can be a visionbased soccer robot to autonomously find a ball and kick a ball. Moreover, TWNHR-III won champion of the humanoid league in Taiwan Cup 2006. In the future, TWNHR-III will be used to investigate the walking gait and artificial intelligence. For example, some force sensors will be installed on TWNHR-III to study the biped walking control on even or uneven ground. More research on artificial intelligence will be carried on TWNHR-III to make it to be an intelligent robot.AcknowledgementThis research was supported in part by the National Science Council (NSC) of the Republic of China under contract NSC 95-2221-E-032-057-MY3 and the Metal Industries Research & Development Centre (MIRDC), Kaohsiung, Taiwan, Republic of China.References[1] Ogura, Y., Aikawa, H., Shimomura, K., Kondo, H.,Morishima, A., Lim, H. O. and Takanishi, A., “Development of a New Humanoid Robot WABIAN-2,”IEEE Int. Conf. on Robotics and Automation, pp. 835⎽840 (2006).[2] Hirai, K., Hirose, M., Haikawa, Y. and Takenaka, T.,“The Development of Honda Humanoid Robot,” IEEE Int. Conf. on Robotics and Automation, Vol. 2, pp. 1321⎽1326 (1998).[3] Kaneko, K., Kanehiro, F., Kajita, S., Hirukawa, H.,Kawasaki, T., Hirata, M., Akachi, K. and Isozumi, T.,“Humanoid Robot HRP-2,” IEEE Int. Conf. on Robotics and Automation, Vol. 2, pp. 1083⎽1090 (2004).[4] Lohmeier, S., Loffler, K., Gienger, M., Ulbrich, H. and Pfeiffer, F., “Computer System and Controlof Biped “Johnnie”,” IEEE Int. Conf. on Robotics and Automation, Vol. 4, pp. 4222⎽4227 (2004).[5] URL: [6] URL: [7] Borenstein, J. and Koren, Y., “Real-Time Obstacle Avoidance for Fact Mobile Robots,” IEEE Tran. On Systems, Man and Cybernetics, Vol. 19, pp. 1179⎽1187 (1989).[8] Crowley, J., “DynamicWorld Modeling for an Intelligent Mobile Robot Using a Rotating Ultra-Sonic Ranging Device,” IEEE Int. Conf. on Robotics and Automation,Vol. 2, pp. 128⎽135 (1985).[9] Rao, N. S. V., “Robot Navigation in Unknown Generalized Polygonal Terrains Using Vision Sensors,” IEEE Tran. on Systems, Man and Cybernetics, Vol. 25, pp. 947⎽962 (1995).[10] Innocenti, C., Mondino, G., Regis, P. and Sandini, G., “Trajectory Planning and Real-Time Control of an Autonomous Mobile Robot Equipped withVision and Ultrasonic Sensors,” IEEE/RSJ/GI Int. Conf. on Intelligent Robots and Systems, Vol. 3, pp. 1861⎽1866 (1994).[11] Wong, C. C., Cheng, C. T., Huang, K. H., Yang, Y. T., Chan, H. M. and Yin, C. S., “Me chanical Design of Small-Size Humanoid Robot TWNHR-3,” The 33rd Annual Conference of the IEEE Industrial Electronics Society, pp. 451⎽454 (2007).Manuscript Received: Jul. 27, 2007Accepted: Aug. 7, 2008258 Ching-Chang Wong et al.。
- 1、下载文档前请自行甄别文档内容的完整性,平台不提供额外的编辑、内容补充、找答案等附加服务。
- 2、"仅部分预览"的文档,不可在线预览部分如存在完整性等问题,可反馈申请退款(可完整预览的文档不适用该条件!)。
- 3、如文档侵犯您的权益,请联系客服反馈,我们会尽快为您处理(人工客服工作时间:9:00-18:30)。
INTELLIGENT VEHICLEOur society is awash in “machine intelligence” of various kinds.Over the last century, we have witnessed more and more of the “drudgery” of daily living being replaced by devices such as washing machines.One remaining area of both drudgery and danger, however, is the daily act ofdriving automobiles 1.2 million people were killed in traffic crashes in 2002, which was 2.1% of all globaldeaths and the 11th ranked cause of death . If this trend continues, an estimated 8.5 million people will be dying every year in road crashes by 2020. In fact, the U.S. Department of Transportation has estimated the overall societal cost of road crashes annually in the United States at greater than $230 billion.When hundreds or thousands of vehicles are sharing the same roads at the same time, leading to the all too familiar experience of congested traffic. Traffic congestion undermines our quality of life in the same way air pollution undermines public health.Around 1990, road transportation professionals began to apply them to traffic and road management. Thus was born the intelligent transportation system(ITS). Starting in the late 1990s, ITS systems were developed and deployed. In developed countries, travelers today have access to signifi-cant amounts of information about travel conditions, whether they are driving their own vehicle or riding on public transit systems.As the world energy crisis, and the war and the energy consumption of oil -- and are full of energy, in one day, someday it will disappear without a trace. Oil is not in resources. So in oil consumption must be clean before finding a replacement. With the development of science and technology the progress of the society, people invented the electric car. Electric cars will become the most ideal of transportation.In the development of world each aspect is fruitful, especially with the automobile electronic technology and computer and rapid development of the information age. The electronic control technology in the car on a wide range ofapplications, the application of the electronic device, cars, and electronic technology not only to improve and enhance the quality and the traditional automobile electrical performance, but also improve the automobile fuel economy, performance, reliability and emissions purification. Widely used in automobile electronic products not only reduces the cost and reduce the complexity of the maintenance. From the fuel injection engine ignition devices, air control and emission control and fault diagnosis to the body auxiliary devices are generally used in electronic control technology, auto development mainly electromechanical integration. Widely used in automotive electronic control ignition system mainly electronic control fuel injection system, electronic control ignition system, electronic control automatic transmission, electronic control (ABS/ASR) control system, electronic control suspension system, electronic control power steering system, vehicle dynamic control system, the airbag systems, active belt system, electronic control system and the automatic air-conditioning and GPS navigation system etc. With the system response, the use function of quick car, high reliability, guarantees of engine power and reduce fuel consumption and emission regulations meet standards.The car is essential to modern traffic tools. And electric cars bring us infinite joy will give us the physical and mental relaxation. Take for example, automatic transmission in road, can not on the clutch, can achieve automatic shift and engine flameout, not so effective improve the driving convenience lighten the fatigue strength. Automatic transmission consists mainly of hydraulic torque converter, gear transmission, pump, hydraulic control system, electronic control system and oil cooling system, etc. The electronic control of suspension is mainly used to cushion the impact of the body and the road to reduce vibration that car getting smooth-going and stability. When the vehicle in the car when the road uneven road can according to automatically adjust the height. When the car ratio of height, low set to gas or oil cylinder filling or oil. If is opposite, gas or diarrhea. To ensure and improve the level of driving cars driving stability. Variable force power steering system can significantly change the driver for the work efficiency and the state, so widely usedin electric cars. VDC to vehicle performance has important function it can according to the need of active braking to change the wheels of the car, car motions of state and optimum control performance, and increased automobile adhesion, controlling and stability. Besides these, appear beyond 4WS 4WD electric cars can greatly improve the performance of the value and ascending simultaneously. ABS braking distance is reduced and can keep turning skills effectively improve the stability of the directions simultaneously reduce tyre wear. The airbag appear in large programs protected the driver and passenger's safety, and greatly reduce automobile in collision of drivers and passengers in the buffer, to protect the safety of life.Intelligent electronic technology in the bus to promote safe driving and that the other functions. The realization of automatic driving through various sensors. Except some smart cars equipped with multiple outside sensors can fully perception of information and traffic facilities and to judge whether the vehicles and drivers in danger, has the independent pathfinding, navigation, avoid bump, no parking fees etc. Function. Effectively improve the safe transport of manipulation, reduce the pilot fatigue, improve passenger comfort. Of course battery electric vehicle is the key, the electric car battery mainly has: the use of lead-acid batteries, nickel cadmium battery, the battery, sodium sulfide sodium sulfide lithium battery, the battery, the battery, the flywheel zinc - air fuel cell and solar battery, the battery. In many kind of cells, the fuel cell is by far the most want to solve the problem of energy shortage car. Fuel cells have high pollution characteristics, different from other battery, the battery, need not only external constantly supply of fuel and electricity can continuously steadily. Fuel cell vehicles (FCEV) can be matched with the car engine performance and fuel economy and emission in the aspects of superior internal-combustion vehicles.Along with the computer and electronic product constantly upgrading electric car, open class in mature technology and perfected, that drive more safe, convenient and flexible, comfortable. Electric cars with traditional to compete in the market, the car will was electric cars and intelligent car replaced. This is the question that dayafter timing will come. ABS, GPS, and various new 4WD 4WS, electronic products and the modern era, excellent performance auto tacit understanding is tie-in, bring us unparalleled precision driving comfort and safety of driving.The hardware and software of the intelligent vehicle are designed based on AVR.This system could set the route in advance. The vehicle could communicate with the PC vianRF401 and could run safely with the help of ultra sound detection and infrared measuring circuit. Neural network self- study is used to improve the intelligence of the vehicle.The performance of servo systems will determine the property of the robot. Based on AVRseries MCU,the velocity servo system for driving motor is created in this paper,including a discrete PIregulator which will work out a PWM control signal with applying the skill of integral separation.The velocities of motors will be controlled real-time with the speed sampling frequency set for 2KHz by using the AVR-GCC compiler software pared to the servo system development based on the 51 Series MCU,the system here has these advantages of simpler peripheral circuit and faster data processing.The experiments demonstrate that,the mobile robot runs stably and smoothly by the control of AVR units,and that the design proposal especially benefits the development of intelligent mobile robots,also can be widely used in the development of other smart devices and product lines.A new design of contest robot control system based on AVR Atmega8 was put forward. According to the character of contest robot , the main control unit , motor drive unit , sense detection unit and LCD display unit were introduced. Furthermore the servo driver system based on MCBL3006S , the line t racker sensor system and the obstacle avoidance sensor system were presented in detail.Finally the performance shows that the control system is open,simple,easy programming,intelligent and efficiency.Avoidance rules of intelligent vehicle obstacle are intro ducted.Through the collection of infrared sensor formation,the rules use diode D1 to launch and diode D2 to receive infrared signals. Infrared transmitter signal without a dedicated circuitcomes directly from the MCU clock frequency, which not only simplifier the circuit and debugging, but also make the circuit stability and anti- jamming capability greatly enhanced.After the experimental verification,the system runs reliably meet the design requirements.A smart car control system of the path information identified based on CCD camera was introduced.The hardware structure and scheme were designed. The control strategy of s teering mechanism was presented. The smart car not only can identify the road precisely, but also have ant-interference performance, and small steady state error.This article designed smart car system,includes the aspects of the sensor information acquisition and processing, motor drive, control algorithm and control strategy ing laser sensor to collect the road information which can feedback to the micro-controller control system,then making analytical processing combined with the software.With velocity feedback and PID control algorithms to control steering engine and the speed of smart car.Verified by actual operation, this method makes smart car travel stably and reliably,and its average speed to reach 2.6m /s, and get a satisfied results.By the aid of the professional know ledge of control, patter n recognition, sensor technology, aut omotive electronics, electricity, computer, machinery and so on, an intelligent vehicle system is designed with PID control algorithm,CCD detection system and HC9SDG128 MCU. Code Warrior IDE integrated development programming environment is taken as a basic softy are platform that can automatically deal with the traffic and image pro cessing, and then adjust the moving direction along the scheduled or bit by t he aid of a CCD camera. The system has many advantages, such as high reliability , high stability, good speed ability and scalability.Based on the research background of the Free-Scale smart car competition,a smart track following car is designed. In the car, the photo electricity sensor is used to check the path and obtain the information of racing road, and calculate the errorbetween the car and the black line. The fuzzy control is used to control the velocity of the car. The experiments show that the smart car based on the fuzzy control has high accuracy on the judgment of the path, stability and velocity control.智能车我们的社会充斥着各种各样的“机器智能“。