风力发电机叶片制造
风机叶片材料
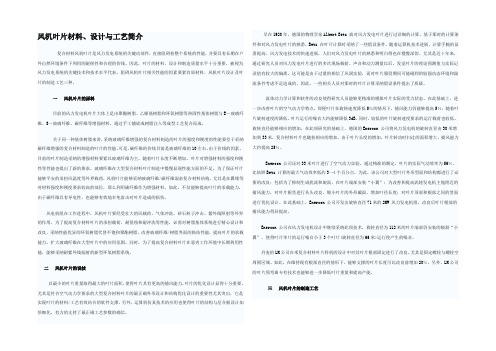
风机叶片材料、设计与工艺简介复合材料风机叶片是风力发电系统的关键动部件,直接阻碍着整个系统的性能,并要具有长期在户外自然环境条件下利用的耐候性和合理的价钱。
因此,叶片的材料、设计和制造质量水平十分重要,被视为风力发电系统的关键技术和技术水平代表。
阻碍风机叶片相关性能的因素要紧有原材料、风机叶片设计及叶片的制造工艺三种。
一风机叶片的原料目前的风力发电机叶片大体上是由聚酯树脂、乙烯基树脂和环氧树脂等热固性基体树脂与E-玻璃纤维、S-玻璃纤维、碳纤维等增强材料,通过手工铺放或树脂注入等成型工艺复合而成。
关于同一种基体树脂来讲,采纳玻璃纤维增强的复合材料制造的叶片的强度和刚度的性能要差于采纳碳纤维增强的复合材料制造的叶片的性能。
可是,碳纤维的价钱目前是玻璃纤维的10左右。
由于价钱的因素,目前的叶片制造采纳的增强材料要紧以玻璃纤维为主。
随着叶片长度不断增加,叶片对增强材料的强度和刚性等性能也提出了新的要求,玻璃纤维在大型复合材料叶片制造中慢慢显现性能方面的不足。
为了保证叶片能够平安的承担风温度等外界载荷,风机叶片能够采纳玻璃纤维/碳纤维混杂复合材料结构,尤其是在翼缘等对材料强度和刚度要求较高的部位,那么利用碳纤维作为增强材料。
如此,不仅能够提高叶片的承载能力,由于碳纤维具有导电性,也能够有效地幸免雷击对叶片造成的损伤。
风电机组在工作进程中,风机叶片要经受壮大的风载荷、气体冲洗、砂石粒子冲击、紫外线照射等外界的作用。
为了提高复合材料叶片的承担载荷、耐侵蚀和耐冲洗等性能,必需对树脂基体系统进行精心设计和改良,采纳性能优异的环氧树脂代替不饱和聚酯树脂,改善玻璃纤维/树脂界面的粘结性能,提高叶片的承载能力,扩大玻璃纤维在大型叶片中的应用范围。
同时,为了提高复合材料叶片在恶劣工作环境中长期利用性能,能够采纳耐紫外线辐射的新型环氧树脂系统。
二风机叶片的设技以最小的叶片重量取得最大的叶片面积,使得叶片具有更高的捕风能力,叶片的优化设计显得十分重要,尤其是符合空气动力学要求的大型复合材料叶片的最正确外形设计和结构优化设计的重要性尤其突出,它是实现叶片的材料/工艺有效结合的软件支撑。
风电机组叶片制作工艺
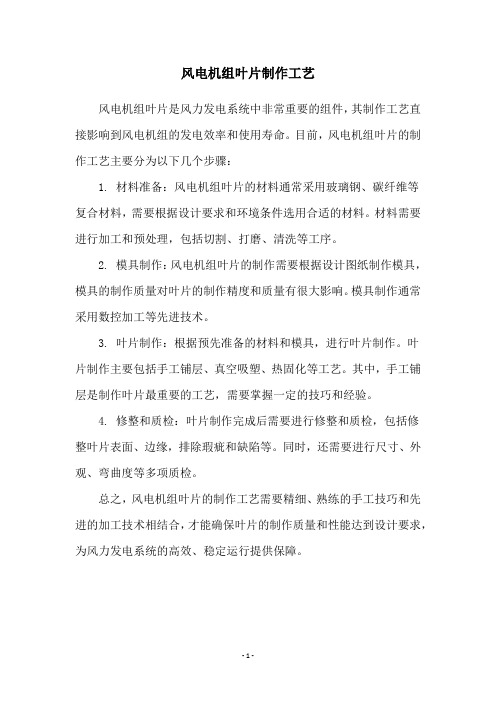
风电机组叶片制作工艺
风电机组叶片是风力发电系统中非常重要的组件,其制作工艺直接影响到风电机组的发电效率和使用寿命。
目前,风电机组叶片的制作工艺主要分为以下几个步骤:
1. 材料准备:风电机组叶片的材料通常采用玻璃钢、碳纤维等
复合材料,需要根据设计要求和环境条件选用合适的材料。
材料需要进行加工和预处理,包括切割、打磨、清洗等工序。
2. 模具制作:风电机组叶片的制作需要根据设计图纸制作模具,模具的制作质量对叶片的制作精度和质量有很大影响。
模具制作通常采用数控加工等先进技术。
3. 叶片制作:根据预先准备的材料和模具,进行叶片制作。
叶
片制作主要包括手工铺层、真空吸塑、热固化等工艺。
其中,手工铺层是制作叶片最重要的工艺,需要掌握一定的技巧和经验。
4. 修整和质检:叶片制作完成后需要进行修整和质检,包括修
整叶片表面、边缘,排除瑕疵和缺陷等。
同时,还需要进行尺寸、外观、弯曲度等多项质检。
总之,风电机组叶片的制作工艺需要精细、熟练的手工技巧和先进的加工技术相结合,才能确保叶片的制作质量和性能达到设计要求,为风力发电系统的高效、稳定运行提供保障。
- 1 -。
风电叶片结构介绍

风电叶片是风力发电机中将风能转换为机械能的关键部件。
大型风电叶片通常采用复合材料制造,以确保轻质、高强且耐腐蚀。
以下是关于风电叶片结构的简要介绍:1. 蒙皮:这是叶片的外表面,由多层玻璃纤维或碳纤维增强塑料(GRP或CFRP)制成。
这些材料具有很高的强度和刚性,并且能够抵抗恶劣天气条件下的磨损和冲击。
2. 主梁:主梁是叶片的主要承重结构,通常位于叶片的前缘。
它通常也是用复合材料制成的,其内部可能包含有金属或复合材料制成的加强筋。
3. 腹板:腹板是在叶片厚度方向上的加强结构,主要为了支撑主梁并保持整个叶片的形状。
腹板通常采用夹芯结构设计,以提高刚度并降低重量。
4. 叶尖帽:叶尖帽位于叶片的最前端,用于保护叶片免受风力冲击和磨损的影响。
5. 连接组件:叶片通过叶根与轮毂相连,这个区域需要承受很大的力和扭矩。
因此,叶根部分的设计非常关键,通常会使用高强度的合金钢或其他高性能材料。
6. 内部布线和传感器:现代风电叶片内部可能会安装各种传感器,用于监控叶片的工作状态,包括载荷分布、振动水平等。
此外,还有电力电缆和信号传输线缆,以便将电流从发电机输送到电网,以及传递控制信息。
7. 气动外形设计:叶片的气动外形对风能捕获效率至关重要。
在设计过程中,工程师们会运用空气动力学原理来优化叶片的截面形状和整体长度,使其能够在各种风速下高效地捕获风能。
8. 平衡和配重:为了保证叶片在旋转时保持稳定,有时会在叶片上加装配重,以平衡叶片的质量分布。
9. 防腐处理:由于叶片长期暴露在户外环境中,必须进行适当的防腐处理,以延长其使用寿命。
总的来说,风电叶片的设计是一个复杂的过程,需要考虑许多因素,包括材料选择、结构设计、空气动力学性能、制造工艺和成本效益分析等。
风电叶片分段技术
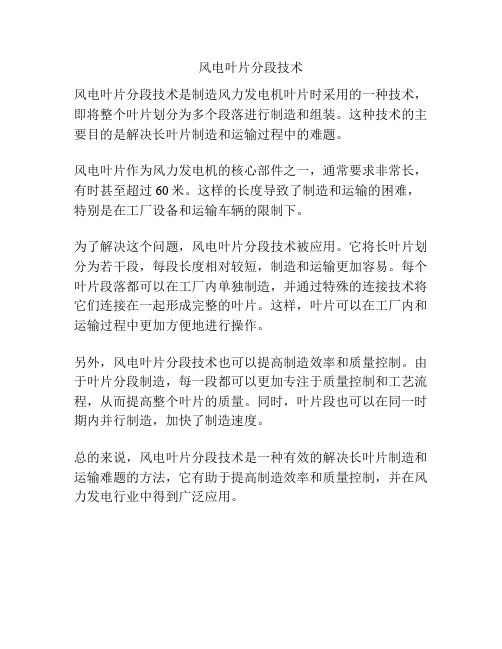
风电叶片分段技术
风电叶片分段技术是制造风力发电机叶片时采用的一种技术,即将整个叶片划分为多个段落进行制造和组装。
这种技术的主要目的是解决长叶片制造和运输过程中的难题。
风电叶片作为风力发电机的核心部件之一,通常要求非常长,有时甚至超过60米。
这样的长度导致了制造和运输的困难,特别是在工厂设备和运输车辆的限制下。
为了解决这个问题,风电叶片分段技术被应用。
它将长叶片划分为若干段,每段长度相对较短,制造和运输更加容易。
每个叶片段落都可以在工厂内单独制造,并通过特殊的连接技术将它们连接在一起形成完整的叶片。
这样,叶片可以在工厂内和运输过程中更加方便地进行操作。
另外,风电叶片分段技术也可以提高制造效率和质量控制。
由于叶片分段制造,每一段都可以更加专注于质量控制和工艺流程,从而提高整个叶片的质量。
同时,叶片段也可以在同一时期内并行制造,加快了制造速度。
总的来说,风电叶片分段技术是一种有效的解决长叶片制造和运输难题的方法,它有助于提高制造效率和质量控制,并在风力发电行业中得到广泛应用。
纺织复合材料在风力发电机叶片制造中的应用
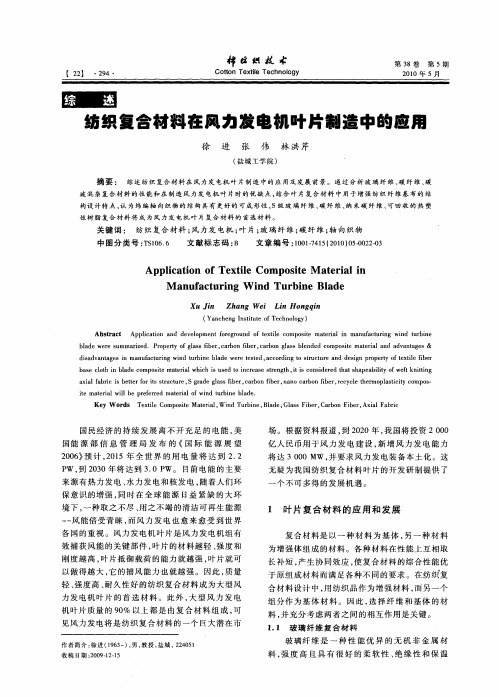
Ap lc to f Te tl m po ie M a e i li p i a i n o x ie Co st t r a n M a f c u i g W i d Tur i a e nu a t r n n b ne Bl d
Xu J n Zh n e Li n q n i a gW i n Ho g i
玻 混 杂复 合 材 料 的性 能 和 在 制 造 风 力发 电机 叶 片时 的 优缺 点 , 合 叶 片 复合 材 料 中 用于 增 强 纺 织 纤 维 基 布 的 结 结
构设 计 特 点 , 为纬 编 轴 向 织 物 的结 构 具 有 更 好 的 可戍 形 性 , 玻 璃 纤 维 、 纤 维 、 米 碳 纤 维 、 回 收 的 热 塑 认 s级 碳 纳 可
K e or s Te tl mp st ae il W i d Tur n Blde, a s Fie Cabo b r, ilFa rc yW d x i Co o ie M t ra , n bie, a e Gls b r, r n Fi e Axa b i
国民经济 的持 续发 展 离不 开 充 足 的 电能 , 美 国能 源 部 信 息 管 理 局 发 布 的 《国 际 能 源 展 望 2 0 ) 计 ,0 5年 全 世界 的用 电量 将 达 到 2 2 06 预 ) 21 .
性树 脂复 合 材 料将 成 为 风 力发 电机 叶 片 复合 材 料 的 首 选 材 料 。
关 键 词 : 纺 织 复合 材 料 ; 力 发 电 机 ; 片 ; 璃 纤 维 ; 纤 维 ; 向 织 物 风 叶 玻 碳 轴
中图分类号 :S0. T166
文献标 志码 : B
文章 编号 : 0 — 1l00 0- 2 - 1 1 45 21)5 02 3 0 7 0 0
风力发电机的叶片原理

风力发电机的叶片原理
风力发电机的叶片原理在于利用风的动能转化为机械能,进而驱动发电机产生电能。
风力发电机的叶片通常由光滑且 aerodynamic 的材料制成,具
有弯曲的形状。
当风经过叶片时,受到叶片的阻力和弯曲形状的影响,将产生一个向前的推力。
这个推力将转化为叶片上的力矩,使叶片开始旋转。
根据伯努利原理,风流通过叶片的同时,在叶片的凸面上会产生较高的气压,而在叶片的凹面上则会产生较低的气压。
这种气压差将使叶片受到一个来自气流的向前的力,从而使叶片继续旋转。
叶片的旋转转动将驱动发电机得以转动,发电机里的感应器将机械能转化为电能,通过连接的电网,将电能输送到各个使用户。
为了提高风力发电机的效率,叶片的设计变得越来越重要。
设计者通常会考虑叶片的数量、形状、长度、倾角等因素来优化叶片的性能。
通过合理的设计,风力发电机可以在不同风速下,以最佳的转速运行,从而提高能量转化效率。
总结起来,风力发电机的叶片利用了风的动能,通过叶片的形状和旋转运动,将风能转化为机械能,从而驱动发电机产生电能。
这一原理使得风力发电成为可再生能源的重要来源之一。
风力发电机的叶片

风力发电机的叶片技术领域[0001] 本发明涉及用于风力发电机的叶片技术领域,具体来说,本发明涉及一种水平轴风力发电机的叶片。
背景技术[0002] 目前,风力发电机可以分为水平轴风力发电机和垂直轴风力发电机。
水平轴风力发电机的叶片翼型多采用航空翼型,以航空翼型为主的升力型叶片。
在旋转的过程中,其相对的线速度从根部到叶尖部分为依次加大的。
为了追求更高的升力系数,叶片被做成根部尺寸大、尖部尺寸小。
但这样造成的缺陷是输出的力矩较小,风能利用率低。
发明内容[0003] 本发明所要解决的技术问题是提供一种水平轴风力发电机的叶片,能够更好地对来流风速进行处理,获得的输出力矩大,风能利用率高。
[0004] 为解决上述技术问题,本发明提供一种风力发电机的叶片,包括前缘部、上表面、后缘部、叶根部、叶尖部和下表面,所述前缘部为圆弧弧面或者弧线,所述叶尖部为圆弧弧面,所述上表面为曲面,所述叶根部为一圆弧弧面或者叶轮的圆心,所述后缘部为圆弧,所述下表面为曲面或者平面。
[0005] 可选地,所述前缘部的上前缘线和/或下前缘线是以所述叶轮的圆周的半径1/2R 处为圆心,从所述叶轮的圆周到所述叶根部所得的半圆圆弧或者劣弧。
[0006] 可选地,所述叶尖部的圆弧弧面的半径为所述叶轮的圆周的半径,所述叶尖部的弧长在180度以内,所述叶尖部的圆弧弧面与所述前缘部的圆弧弧面或者弧线是相结合的。
[0007] 可选地,所述上表面是由以所述叶轮的圆心作为参照点的多条横向圆弧弧线以及多条纵向圆弧弧线扫描而成的;[0008] 其中,所述横向圆弧弧线是以所述叶轮的圆心或者圆心线的上端点为圆心,在所述上前缘线和所述后缘部之间作的多条密集的横向圆弧弧线;[0009] 所述纵向圆弧弧线是由所述叶尖部的叶尖部上弧线到所述叶轮的圆心或者所述圆心线之间作的多条密集的纵向圆弧弧线。
[0010] 可选地,所述叶根部为圆弧弧面或者所述叶轮的中心部,所述叶根部的圆弧弧面位置是选择以所述叶轮的圆心为参照点作所述叶片的所述前缘部与所述后缘部之间的横向圆弧弧线为切割线,切除从所述切割线到所述叶轮的圆心的实体,剩余的实体为叶片,得到从所述切割线到所述叶片的下表面之间的弧面即为所述叶根部,所述叶根部与所述叶轮的轮毂相连。
风力发电机叶片简介演示

实时监测叶片状态,一旦发现叶片性能严重下降或达到预定更换条 件,立即进行更换。
THANK YOU
感谢观看
先进制造技术
采用先进的制造技术,如3D打印和复合材料成型工艺,可以制造出具有更复杂几何形状和更高性能的叶 片。这为进一步优化叶片设计提供了技术保障。
04
叶片的检测与维护
叶片的缺陷与损伤检测
01
Байду номын сангаас
02
03
视觉检测
通过高清相机捕捉叶片表 面的图像,利用计算机视 觉技术识别裂纹、变色、 变形等缺陷。
超声波检测
力学性能和耐候性,同时重量较轻,适用于大型风力发电机叶片。
02 03
碳纤维
碳纤维是一种高性能、高强度的材料,用于叶片制造可显著提高叶片的 刚度和抗疲劳性能。然而,碳纤维成本相对较高,目前主要用于高端风 力发电机。
木材和复合材料
一些小型风力发电机叶片采用木材或其他复合材料制造。这些材料具有 成本低、环保等优点,但性能相对较差,适用于低风速地区。
利用超声波在叶片材料中 的传播特性,检测叶片内 部的裂纹、气泡等缺陷。
红外线热像检测
通过红外线热像仪观察叶 片表面的温度分布,从而 发现潜在的缺陷和损伤。
叶片的维护与修复
表面清洗
定期清除叶片表面的污垢 、沙尘等附着物,保持叶 片的光洁度,减少风阻。
防腐涂层
对叶片表面进行防腐处理 ,涂抹专用防腐涂层,延 长叶片使用寿命。
先进复合材料成型工艺
随着技术的发展,一些先进的复合材料成型工艺如拉挤成型、模压成型和3D打印等也逐 渐应用于风力发电机叶片的制造。这些工艺具有生产效率高、材料利用率高、产品设计灵 活等优点,代表了未来叶片制造技术的发展方向。
- 1、下载文档前请自行甄别文档内容的完整性,平台不提供额外的编辑、内容补充、找答案等附加服务。
- 2、"仅部分预览"的文档,不可在线预览部分如存在完整性等问题,可反馈申请退款(可完整预览的文档不适用该条件!)。
- 3、如文档侵犯您的权益,请联系客服反馈,我们会尽快为您处理(人工客服工作时间:9:00-18:30)。
风力发电机叶片制造
摘要:以某企业研制生产的1.5 MW变速变桨距型风力发电机叶片为例,介绍叶片的规格、材料、性能参数、模具制作以及生产过程,并对其进行综合评价。
关键词:风力发电风电叶片叶片生产制造
1 背景介绍
风力发电机是一种将风能转化为机械能,再由机械能转化为电能的机组和系统,前一种转化是由风轮实现的,后一种转化是由发电机实现的。
风轮主要由两部分组成:叶片(一般为3片)和轮毂,轮毂只起连接的作用,叶片是将风能转化为机械能的唯一关键部件。
叶片的外形决定了整个机组的空气动力性能,一个具有良好空气动力外形的叶片,可以使机组的能量转换效率更高,获得更多的风能。
同时,叶片又承受着很大的载荷(风力和质量力),自然界中的风况复杂多变,叶片上承载的载荷也就很复杂,整个风力发电机组主要载荷的来源是叶片,所以叶片必须有足够的强度和刚度。
由此可见,叶片的材料、结构和工艺是非常关键的。
材料和结构保证叶片的强度和刚度,并且重量要轻,还要有合适的工艺和方法,保证能够做出带有复杂的外形、符合空气动力学原理的外形的大尺寸构件。
叶片的关键技术有下面几个部分:气动外形设计及性能和载荷计算、材料选择、结构设计与强度和刚度计算、成型工艺、模具设计与
制造。
下面以某企业研制生产的1.5 MW变速变桨距型风力发电机组叶片为例,介绍叶片的规格、使用材料、性能、主要技术参数以及生产工艺过程等。
2 产品介绍
2.1 概述
该产品为某公司自行研制设计并生产,适用于发电机组为水平轴、上风向、3叶片、变速变桨距调节型。
叶片分两种规格:XF37.5型和XF40.25型,具有良好的空气动力性能:φ82.5 m风轮(叶片长40.25 m)最大风能利用系数Cpmax可达到0.493, φ77m风轮(叶片长37.5 m)最大风能利用系数Cpmax可达到0.488。
叶片与轮毂联接方式为叶根法兰连接,在法兰盘直径1800 mm圆周上均布M30的螺栓孔。
两种叶片的翼型均选用适用于风电叶片的先进的NACA、DU、FFA等系列翼型,所用翼型的空气动力特性(升力、阻力、力矩系数等)在试验数据的基础上应用专业软件Rfoil进行了雷诺数和三维修正,对叶片的气动设计进行了优化设计,气动性能达到了国际先进水平。
XF37.5型采用不饱和聚酯复合材料,XF40.25型采用环氧复合材料。
两种叶片均采用真空导注工艺,采用该工艺制造叶片的质量稳定性好,整体性好,尺寸精度高,叶片重量更易于控制,能显著提高叶片的
强度、刚度和其他物理特性。
2.2 主要技术参数
叶片主要安装尺寸、叶片参数、风轮参数、材料及运行条件如表1所示。
3 叶片生产过程
叶片的生产过程大致有下料、大梁和翼梁制作、层铺、真空吸注、合模和起模、型修、检验配平出厂等工序。
3.1 下料
根据强度、工艺性、经济性要求选择主要复合材料和金属材料。
基体树脂选用进口的真空导注专用环氧树脂,固化温度在80 ℃左右;增强材料选用国产玻璃纤维制品,国内产品可大量供应,成本低,而且质量可靠;结构粘接胶选用可室温固化的环氧树脂类粘接胶,进口或国产产品都有合适的产品;金属材料:主要是叶片连接金属件用材料,采用国产优质合金钢。
除按照工艺设计要求准备主材料之外,下列准备工作也许格外注意以下几点。
(1)螺栓套准备:堵盖、喷砂、缠丝、清洗、打压。
(2)配合打磨组下料:前后缘外补强、内补强(大梁)所用布。
(3)配合合模组下料:硫化阻尼板、斜纹布、海绵条、短切毡等。
(4)叶片下料:PVC泡沫板缝制、聚氨脂泡沫、粘接舌头、楔形条切割打磨。
3.2 大梁、翼梁制作
在大梁模具和翼梁模具上分别制作和组装大梁(前梁和后梁),制作和组装翼梁(也称梁盖),粘结组装制动梁,并制作叶尖和主体端头组件。
其中的层铺和真空吸注、型修工艺参见后述有关叶片相关工艺。
3.3 层铺
在正式层铺之前,先要将模具准备好,包括:起模(撬开预离模装置,松模具锁紧装置,松螺栓套螺丝,吊半圆法兰)、清理副模(打蜡,铺脱模布)、清理半圆法兰、安装螺栓套、领料,然后再按照工艺要求逐层进行铺布并缝布。
3.4 真空吸住
真空吸注是叶片生产过程中的关键工艺之一,密封性、负压控制、导流管的铺设等,都非常重要,直接影响叶片的各项性能指标。
真空吸注工序包括以下过程:准备(铺放密封胶条,铺放双面胶条,铺放螺旋包套,铺放脱模布)、备料(准备树脂、固化剂、真空罐标识)、吸注(连接真空罐、真空泵,抽真空达到规定负压,配胶、注胶)、固化、清理注胶用Ω管和注胶块。
3.5 合模、起模
(1)准备工作:真空吸注后要先对现场进行清理,然后撕去脱模布、导流网和Ω管,手糊预离模装置,打磨分模面,清理副模,分胶。
(2)试合模:固定梁、小梁、大梁划线,上下壳铺阻尼,清理大梁上脱模布。
(3)合模:大梁锁紧,叶壳内刮胶,清理卫生。
起模:结构胶固化后,松开锁紧装置,将模具与叶片分离。
3.6 型修
将叶片吊运到一定高度,切去飞边,打磨需进行内补强和大梁补强的地方。
然后将叶片吊上大圈车,打磨需外补强的地方,之后切13切面和窗口,再进行内外补强和大梁补强。
待内外补强和大梁补强固化后,修理外补强光滑度,再喷胶衣,修理13切面和叶尖,对胶衣光滑面处理。
3.7 检验、配平、出厂
对产品进行进行总体检验,安装法兰盘、接闪器、标牌,配平成套(将3个质量、重心相近的叶片采取补充材料的办法,使其质量相等、重心一致,并编号成套),最后进行出厂检验。
4 结论
该叶片产品进行了结构优化设计,结构简单、重量轻,具有良好的
工艺性。
企业自主研发的1.5 MW叶片(叶片长度40.25 m) 产品更适合我国大面积的低速风场,增加了机组的发电量。
叶片成型工艺采用先进的真空导注工艺,使产品的强度和质量更稳定可靠,并大大改善了生产环境。
自主开发的模具设计与制造技术,技术先进成本低,能更方便的满足工艺和生产需要。