中小型变压器铁芯叠片打工艺孔案例分析
变压器制造过程铁心问题浅析

变压器制造过程铁心问题浅析摘要:主变压器作为电站内最重要的电气设备之一,对于电厂的正常运行及经济发电有着重要作用。
本文对三门核电主变压器结构进行了简介,通过对制造过程中的问题进行分析,总结了主变压器监造过程中需要注意的重点,并提出了后续运行过程中需要关注的事项。
关键词:主变压器结构监造Abstract: As one of the most important electric equipments, Main Transformers Plays an important role for the normal operation and economic efficiency of the power plant. This article introduces the structure of the Main Transformers, analyzes the problems in the process of manufacture, summarizes some key points that need to pay attention to. In addition, it puts forward some matters that need to pay attention tothe follow-up operation process.Key words: Main Transformers Structural Manufacturing Process1.前言主变压器作为核电工程的关键设备之一,承担着电压变换、电能传输的关键作用。
确保主变压器的安全、高效运行,对于保证整个核电的供电稳定、确保经济生产具有重要意义。
为此,有必要对主变压器制造过程中常见问题进行分析,以期对后续主变压器的监督制造起到指导作用,并对后期运行维护提起预防。
2.主变压器简介2.1.主变压器主要参数三门核电主变压器额定容量484MVA,绕组额定电压单相为(535kV/3)2×2.5%/24 kV,高压侧额定电流为1567A(线电流),低压侧额定电流为34930A(线电流),额定频率50Hz,联接组别标号YNd11。
电力变压器监造发现质量问题分析及措施建议

电力变压器监造发现质量问题分析及措施建议摘要:文章介绍了国内变压器监造过程中发现的各种案例,同时对问题的产生原因做了深刻分析,并且提出了相应的整改和预防措施,为防止此类问题再次发生有很好的借鉴作用。
关键词:变压器;监造;质量问题;案例;分析1变压器生产质量监理发现的问题1.1铁芯柱绑扎存在尖角、毛刺1.1.1问题描述2016年10月5日,某变压器厂家对某省220kV主变压器和某省220kV1#主变铁芯叠片后绑扎(采用绿色聚酯带)起立,绑扎铁芯主柱、旁柱的绿色聚酯带压接处存在严重的尖角及毛刺,未做处理。
1.1.2原因分析该变压器厂家在工艺上对此问题未做规定,铁芯绑扎工人和专职检查员对此问题没有引起重视,导致变压器铁芯在绑扎时发生此类问题未做处理。
此类问题属于制造工艺问题,变压器最忌讳存在尖角、毛刺、杂质、水分等问题。
监造人员要提醒厂家工艺员在加强质量内控上不要走形式,要注意每个细节和过程。
1.1.3处理情况监造人员发现后,迅速向该厂合同履约处反映了情况,向厂家发出了工作联系单,合同履约处负责人也将此情况在该厂内部网上向相关部门进行了传递,要求迅速整改并拿出处理意见。
公司已将此问题纳入工艺检查的范畴和考核的范围,并补充更改工艺文件内容。
1.2铁芯油道间发生短路,电阻为零1.2.1问题描述2016年12月18日,监造人员和装一车间班长一起在某变压器厂摇测铁芯对夹件、铁芯油道间绝缘电阻时,发现铁芯从低压侧往高压侧数第二个铁芯油道间电阻为零(共4个油道,其他3个铁芯油道间电阻均为不通路,即为200MΩ)。
1.2.2原因分析一是线圈绕制的时间与铁芯制作时间不匹配,线圈绕制、压装、干燥时间拖得太长;二是整体铁芯起吊前未用吸尘器或吹风机对整体铁芯底部进行清洁和吸尘。
此类问题属于班组生产人员,未严格履行操作工艺,技术负责人未严格把控;属于质量管控问题。
同时也提醒监造人员一是要把控厂家生产安排的协调性;二是要认真监督班组人员严格执行工艺操作流程。
低噪声干式电力变压器铁心叠片新工艺
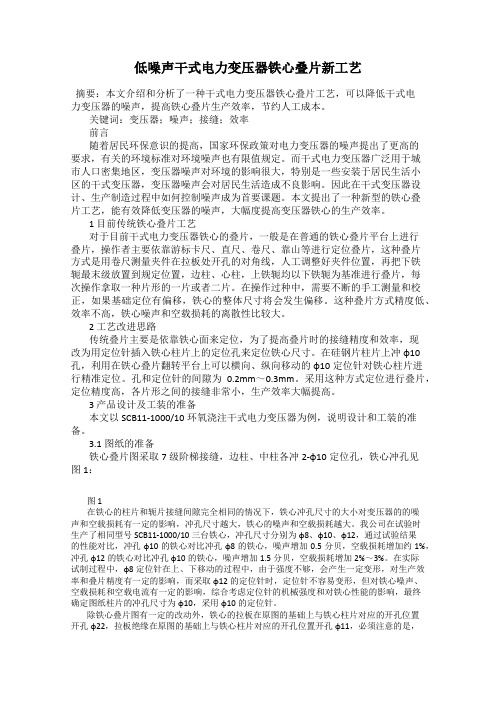
低噪声干式电力变压器铁心叠片新工艺摘要:本文介绍和分析了一种干式电力变压器铁心叠片工艺,可以降低干式电力变压器的噪声,提高铁心叠片生产效率,节约人工成本。
关键词:变压器;噪声;接缝;效率前言随着居民环保意识的提高,国家环保政策对电力变压器的噪声提出了更高的要求,有关的环境标准对环境噪声也有限值规定。
而干式电力变压器广泛用于城市人口密集地区,变压器噪声对环境的影响很大,特别是一些安装于居民生活小区的干式变压器,变压器噪声会对居民生活造成不良影响。
因此在干式变压器设计、生产制造过程中如何控制噪声成为首要课题。
本文提出了一种新型的铁心叠片工艺,能有效降低变压器的噪声,大幅度提高变压器铁心的生产效率。
1 目前传统铁心叠片工艺对于目前干式电力变压器铁心的叠片,一般是在普通的铁心叠片平台上进行叠片,操作者主要依靠游标卡尺、直尺、卷尺、靠山等进行定位叠片,这种叠片方式是用卷尺测量夹件在拉板处开孔的对角线,人工调整好夹件位置,再把下铁轭最末级放置到规定位置,边柱、心柱,上铁轭均以下铁轭为基准进行叠片,每次操作拿取一种片形的一片或者二片。
在操作过种中,需要不断的手工测量和校正,如果基础定位有偏移,铁心的整体尺寸将会发生偏移。
这种叠片方式精度低、效率不高,铁心噪声和空载损耗的离散性比较大。
2 工艺改进思路传统叠片主要是依靠铁心面来定位,为了提高叠片时的接缝精度和效率,现改为用定位针插入铁心柱片上的定位孔来定位铁心尺寸。
在硅钢片柱片上冲φ10孔,利用在铁心叠片翻转平台上可以横向、纵向移动的φ10定位针对铁心柱片进行精准定位。
孔和定位针的间隙为0.2mm~0.3mm。
采用这种方式定位进行叠片,定位精度高,各片形之间的接缝非常小,生产效率大幅提高。
3 产品设计及工装的准备本文以SCB11-1000/10环氧浇注干式电力变压器为例,说明设计和工装的准备。
3.1图纸的准备铁心叠片图采取7级阶梯接缝,边柱、中柱各冲2-φ10定位孔,铁心冲孔见图1:图1在铁心的柱片和轭片接缝间隙完全相同的情况下,铁心冲孔尺寸的大小对变压器的的噪声和空载损耗有一定的影响,冲孔尺寸越大,铁心的噪声和空载损耗越大。
中小型变压器铁芯叠片打工艺孔案例分析

挤压速 度 过 高 而破 裂 , 因此 生 产 过 程 中需 对 挤 压 速 度 进 行
控制 。 在液体介质冷挤 压工 艺中 , 应用 最多 的填充 介质 就是 水 ,
展前景极为可观 , 未来 , 对 于这一工艺 的研究 和应 用还应 继续
深化和完善 。 [ 参考 文献]
[ 1 ]王 会凤. 应用 广泛 的金属 挤压 工艺 F J ] . 金属 世界 , 2 0 1 1 ( 5 ) .
而 道远 , 车 间生产 仍受 各 方面制 约 , 诸 如生 产效 率提 不上 、 交货 进 度经 常推 迟 等一 系 列 问题 急需 改 善 , 特别 是 叠 片这 道 工 序影 响 较 大 。环 观 整个 行业 , 目前 叠 片工 序基本 上都 是纯 人工 操作 , 产 品的质 量及 使用 性能 对员 工 的素质及 业务 能力 要求 非常 高 , 目前 只 有极 少数 行 业龙 头 引入 了 自动叠 片机 , 但 是要付 出 的代价 非常 昂贵 , 仅仅 叠 片机就 得 上千 万 , 还需 要 将 整个 车 间 的布局 推 翻 重建 。在 此 背 景下 , 各 公 司都
体, 所 以 实 际 上 仍会 具有 一定 的 可 压 缩 性 。紫 铜 三 通 管 件 会 因
水作为填充介质 的冷 挤压 工艺 , 节能环保 , 具 有 良好 的生 产效 率, 并 且其挤 压成 型 的紫 铜三 通管 件光 洁度 及质 量都 比较 优
良, 能 大 大 降低 产 品生 产 制 造 成 本 , 提高企业综合 效益 , 因 而 发
以及 3 D技术在工业生产过程中的应用等 。工人将 会被越来 越
多 的 智 能设 备 代 替 , 未 来 工 厂 的 人 员 结 构 可 能 大 多 为 技 术 人 员、 设备操作人 员、 营 销 人 员 等 非 一 线 员 工 。 整 个 变 压 器 铁 芯 制造业的明天也会如此 , 最 依 赖 人 工 的 叠 片 将 会 被 引 进 的全 自
叠片式铁芯

叠片式铁芯一、引言叠片式铁芯是一种用于电力变压器、电感器和互感器等电力设备中的关键元件。
它由多个薄片叠放而成,具有较高的磁导率和低的磁滞损耗,能够有效地提高设备的工作效率和性能稳定性。
本文将详细探讨叠片式铁芯的结构、制造工艺、应用领域和未来发展趋势。
二、叠片式铁芯的结构叠片式铁芯由多个薄片组成,每个薄片都由高导磁材料制成,如硅钢片。
这些薄片通过绝缘材料隔开,形成一个整体结构。
叠片式铁芯通常采用矩形或圆形的形状,以适应不同设备的需求。
在叠片式铁芯的制造过程中,还需要考虑薄片的厚度、绝缘材料的选择和加工工艺等因素,以确保其性能和可靠性。
三、叠片式铁芯的制造工艺1. 材料准备叠片式铁芯的制造首先需要准备高导磁材料,如硅钢片。
硅钢片具有较高的导磁性能和低的磁滞损耗,能够有效地降低能量损耗和温升。
在选材过程中,需要考虑材料的磁导率、磁饱和磁感应强度和导电性能等因素。
2. 薄片加工选定合适的硅钢片后,需要对其进行加工。
首先,将硅钢片切割成所需的尺寸和形状。
然后,对薄片进行去毛刺和表面处理,以提高其表面光滑度和导电性能。
最后,对薄片进行绝缘处理,以防止相邻薄片之间的短路和电流损耗。
3. 叠片组装在薄片加工完成后,需要将它们按照一定的顺序叠放在一起。
叠片的顺序和叠放方式会对叠片式铁芯的性能产生重要影响。
一般来说,采用交错叠放的方式可以有效地减小铁芯的磁滞损耗和涡流损耗,提高设备的工作效率。
4. 绝缘处理叠片式铁芯的绝缘处理是确保其性能和可靠性的重要环节。
绝缘材料需要具有良好的绝缘性能和耐高温性能,以防止叠片之间的短路和电流损耗。
常用的绝缘材料有绝缘漆和绝缘纸等。
四、叠片式铁芯的应用领域叠片式铁芯广泛应用于电力变压器、电感器和互感器等电力设备中。
其主要作用是提供磁路,将电能转换为磁能或将磁能转换为电能。
叠片式铁芯具有较高的导磁性能和低的能量损耗,能够提高设备的工作效率和性能稳定性。
同时,叠片式铁芯还具有体积小、重量轻和成本低的优点,适用于各种不同规格和功率的电力设备。
对于变压器铁心制造问题分析与研究

对于变压器铁心制造问题分析与研究对于变压器铁心制造问题分析与研究摘要:本文主要就变压器铁心的制造技术以及未来的开展进行了详细的探索与研究,在此提出了自己的一些建议,可供同行工作人员共同探讨。
关键词:变压器铁心制造技术开展一、前言虽然如今我国变压器器制造行业得到了快速的开展,但是变压器铁心制造质量直接影响着变压器的质量,铁心制造技术,制造过程中存在的问题,都直接影响到设备运行过程中的功耗、稳定性等等;只有不断的推动制造工艺的进步才能够尽可能提高变压器制造真正的技术水平。
为了使我国的铁心制造有更大的开展空间,需要对变压器铁心制造问题作进一步的分析和研究。
二、变压器铁心的开展现状及制造技术通过各方面的调查研究,市场研究说明,目前变压器铁心在国内外开展有很大的空间。
铁心,是一个变压器最为重要的磁路部件,一个变压器的正常运行是不可能离开一个高质量的铁心,变压器的铁心必须要在有较好的技术性能的根底上,兼顾经济性与平安性,才能够让其在变压器运行中起到真正的作用。
对于一个铁心质量而言,其制造的材料,外表涂刷绝缘漆的质量都直接影响其寿命。
铁心的横截面积,铁心的材料都影响者变压器的功率寿命,而一般来说铁心的分类主要有以下几种:1、高频类:其中高频变压器中都是带有尖结晶石的晶状结构陶瓷体来构成,一般都采用金属作为主要的材料,常见的金属有铁金属,或者锰、锌、镍、镁、铜等这些具有导电性,且导电性较良好的金属。
2、低频类:低频变压器多采用“硅钢片〞来制造,并且其有多重制造工艺。
通常情况下按照钢片的形状和是否煅烧来进行区分,没有煅烧的钢片通称为“白片〞,而进行煅烧的钢片通称为“黑片〞,而形状划分往往都分为EI型、UI型、C型、口型等等。
铁心都是其两侧安装线圈,线圈的扎数一般都会影响到变压器的功率等,一般都是在铁心的两侧分别分配在两侧的线包中,要尽可能的减少索绕线圈的扎长数,这样就能够减少线圈所需要消耗掉的铜材增加线圈的经济性。
全自动变压器铁芯硅钢片叠片装置的研发
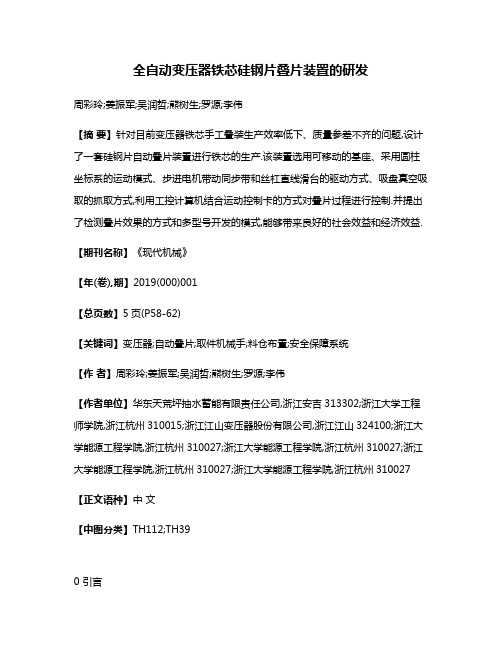
全自动变压器铁芯硅钢片叠片装置的研发周彩玲;姜振军;吴润哲;熊树生;罗源;李伟【摘要】针对目前变压器铁芯手工叠装生产效率低下、质量参差不齐的问题,设计了一套硅钢片自动叠片装置进行铁芯的生产.该装置选用可移动的基座、采用圆柱坐标系的运动模式、步进电机带动同步带和丝杠直线滑台的驱动方式、吸盘真空吸取的抓取方式,利用工控计算机结合运动控制卡的方式对叠片过程进行控制.并提出了检测叠片效果的方式和多型号开发的模式,能够带来良好的社会效益和经济效益.【期刊名称】《现代机械》【年(卷),期】2019(000)001【总页数】5页(P58-62)【关键词】变压器;自动叠片;取件机械手;料仓布置;安全保障系统【作者】周彩玲;姜振军;吴润哲;熊树生;罗源;李伟【作者单位】华东天荒坪抽水蓄能有限责任公司,浙江安吉313302;浙江大学工程师学院,浙江杭州310015;浙江江山变压器股份有限公司,浙江江山324100;浙江大学能源工程学院,浙江杭州310027;浙江大学能源工程学院,浙江杭州310027;浙江大学能源工程学院,浙江杭州310027;浙江大学能源工程学院,浙江杭州310027【正文语种】中文【中图分类】TH112;TH390 引言变压器行业是一个传统的行业[1],变压器铁芯作为变压器的核心部分,它的质量直接影响到变压器的技术性能、经济指标和运行的安全可靠,因此,它的制造技术改良和质量控制十分重要。
由于变压器铁芯叠装制造工艺的特殊性,现有的铁芯制造几乎都采用手工叠装硅钢片的方式生产。
以一台10kV小型变压器为例,铁芯叠片工序由两人操作,操作工在叠片过程中,均靠经验和肉眼观察来保持叠装精度,生产效率低下,产品质量参差不齐[2]。
人工铁芯叠装的弊端在自动化生产飞速发展的今天逐步显现,成为制约变压器产业发展的障碍[3]。
同时,国内外也没有专门针对变压器铁芯叠装的设备,只有加拿大MTM公司有类似设备,但不是完整的自动叠片机器人。
铁心叠装工艺

变压器有限公司共8 页第2 页4.工艺过程4.1测量中柱或中轭片根据产品图纸给定的铁心厚度,用游标尺准确地逐级测量中柱或上铁轭中轭片子的叠厚,以此作为叠装时控制叠厚的基准。
4.2布置叠装架一般情况下,小型铁心可以在适中的叠装台上叠装,而中型以上较大的铁芯适宜在翻身架上叠装。
这样较为安全、方便。
⑴.选择在叠装台上叠装时,首先,在叠装台上放置2~3根长度超出铁心总高度1.1倍、并且平直的槽钢作为基架。
基架槽钢的宽度和具体放置数量,应根据铁心的大小和重量确定,相互间应保持基本平行。
⑵.认准铁心上、下夹件的方向位置,平面朝上横放置在基架的两端。
并保持两夹件平行,然后测量它们的间隔距离必须与图纸要求的保持基本一致。
⑶.按图纸要求,在夹件上面放置夹件绝缘。
⑷.在两夹件中间,按200㎜~300㎜的间距,平行放置一定数量的长度超出铁心宽度,如图1所示的工艺夹紧槽钢,注意:放置时该槽钢上的长腰孔要避开铁心柱,置于两心柱中间,以方便以后夹紧操作。
注:材料一般采用10#槽钢,为增强夹紧槽钢的利用率和通用性,长腰孔数量与间距H可以根据铁心柱之间的开档距离确定长短和多少。
图1 工艺夹紧槽钢加工示意图⑸.再在工艺夹紧槽钢上面对应于铁心柱位置,放置长度适中的垫槽钢或垫块,目的是托住叠装的硅钢片,防止因跨距过大而使铁心柱最初几级硅钢片下陷,引起拱曲。
因此,要求垫槽钢或垫块的中心应线应可尽能地与铁心柱中心线保持重合,垫出的高度与两端的铁心夹件(包括夹件绝缘)的高度基本一致,处于同一水平面上。
⑹.如果铁心采用的是无吊螺杆的内置吊钢板结构形式,则先在夹件上按图纸规定的方式方法放置吊钢板和心柱绝缘封片;如果铁心的结构为常规普通的吊螺杆形式,则先在夹件心柱位置按图放置心柱绝缘封片。
如果图纸未明确规定心柱绝缘封片尺寸和放置要求时,则按本工艺要求,必须在各铁心柱对应位置,分别放一张厚度0.5㎜、与第一节片子等宽、等长的环氧玻璃布板绝缘封片。
- 1、下载文档前请自行甄别文档内容的完整性,平台不提供额外的编辑、内容补充、找答案等附加服务。
- 2、"仅部分预览"的文档,不可在线预览部分如存在完整性等问题,可反馈申请退款(可完整预览的文档不适用该条件!)。
- 3、如文档侵犯您的权益,请联系客服反馈,我们会尽快为您处理(人工客服工作时间:9:00-18:30)。
中小型变压器铁芯叠片打工艺孔案例分析
————————————————————————————————作者:————————————————————————————————日期:
中小型变压器铁芯叠片打工艺孔案例分析-机电论文
中小型变压器铁芯叠片打工艺孔案例分析
刘延昭
(特变电工衡阳电气分公司铁芯项目公司,湖南衡阳421007)
摘要:中小型铁芯产品是铁芯项目公司的拳头产品,但随着“十三五”的到来,要想顺利完成公司制定的战略计划,铁芯项目部任重而道远,车间生产仍受各方面制约,诸如生产效率提不上、交货进度经常推迟等一系列问题急需改善,特别是叠片这道工序影响较大。
环观整个行业,目前叠片工序基本上都是纯人工操作,产品的质量及使用性能对员工的素质及业务能力要求非常高,目前只有极少数行业龙头引入了自动叠片机,但是要付出的代价非常昂贵,仅仅叠片机就得上千万,还需要将整个车间的布局推翻重建。
在此背景下,各公司都在寻求一些突破方法来改善叠片工序。
现通过研究片型打孔定位及改变铁芯叠片模式来简化、改善叠片工序,减少叠片过程中人工修、敲等行为,以减少人为因素对铁芯的影响。
关键词:自动叠片机;生产效率;打孔定位
1案例背景
随着企业的发展朝着工业4.0的方向逼近,在各制造行业中,全机械自动化生产将是未来工厂发展的一个重大趋势。
“工业4.0”项目主要分为两大主题,一是“智能工厂”,重点研究智能化生产系统及过程以及网络化分布式生产设施的实现;二是“智能生产”,主要涉及整个企业的生产物流管理、人机互动以及3D技术在工业生产过程中的应用等。
工人将会被越来越多的智能设备代替,未来工厂的人员结构可能大多为技术人员、设备操作人员、营销人员等非一线员工。
整个变压器铁芯制造业的明天也会如此,最依赖人工的叠片将会被引进的全自动
化叠片机取代(现有的自动叠片设备均需打孔定位),这个过程不会太遥远,而目前对此最重要的一环则是全片型打孔定位。
2案例描述
铁芯车间制作铁芯主要是客户来图加工生产,均规定了铁芯结构及工艺步进方案,本案例的难点在改善的前提下必须保证客户几个硬性要求,即保证铁芯空载损耗值及客户的铁芯总体结构不可改变。
铁芯车间常规叠片方式均采用横向三步进或四步进、无孔定位模式,员工在叠完一定厚度的铁芯片后,需要用专用工具进行修、敲等工序,把铁芯修齐,然后再继续往上叠,不同的员工整修的技术不一样,导致相同的铁芯叠出来的离缝、外观各有差别。
采用打孔定位后,叠片时在打孔位置放上定位杆,然后员工只需要把硅钢片往叠片台上一组组落料即可,不需要进行整形,或者只需要最终拔出定位杆进行少量整形,从而最大化地减少了各员工叠的铁芯之间的差异。
2.1产品打孔试验
铁芯车间先期对铁芯打孔生产进行了试验探索,车间组织技术及员工配合,对型号为S11630/10的油变进行打孔试验,采用全片型打孔形式,即中柱、偏柱、边柱各打一个16mm(车间原有最小打孔模具)中心孔,上下轭铁各打两个16mm孔(图1)。
在下料中由检验员进行过程监控,逐级下料逐级检查。
过程控制如下:下完料
后进行叠片,叠片中员工要填写好叠片记录表,对每级厚度进行精确控制;采用熟练员工叠片,且两台试验品均由同一组人员叠片,不准过程中换人;料不能混乱,使用料必须一致。
叠片完后进行空载损耗试验,试验控制如下:均由叠片台上压完铁芯直接起吊到试验区进行试验,避免了多次吊动造成损耗增加,且做试验时间定在下班后,避免存在电压不稳的情况影响结果。
铁芯外观及尺寸检测结果:未打孔铁芯实测主级厚130mm,总厚256mm;打孔铁芯实测主级厚130mm,总厚256mm;实测空载损耗试验结果:未打孔铁芯空载损耗值835W,打孔铁芯空载损耗值926W,高于未打孔铁芯空载损耗10%。
2.2问题原因分析
以上试验结果超出预期,经过揣摩并查阅一些相关专业资料(《变压器铁芯制造工艺》机械工业出版社),对本次产品试验结果差异提出几点原因说明及改进措施:
(1)经查阅,一般行业中中小型铁芯打孔应用于干变铁芯较多,干变铁芯对空载损耗要求较油变铁芯低,且容易做合格,打孔铁芯在正常工作时,磁路在硅钢片中流通时,遇孔将改变运行轨迹,在孔的周边聚集,造成额外损耗(图2),并且容易产生噪音。
解决此方案的有效途径为将孔改小,将车间常用的20mm、24mm模具换成8mm或10mm,经后续试验验证,能有效降低损耗3%~5%。
(2)设备打孔毛刺较深,造成相同的级数在叠片时,同一厚度情况下,打孔铁芯所需要的片数要少。
解决此问题的方法是对打孔模具进行修模与精调,减少毛刺。
这就需要培养员工换模、调模、拆模的操作水平,不然,模具的使用寿命及精度会下降得很快。
笔者认为,此次试验结果意义较为重大,让我们看到了全片型打孔的一些优点,即叠片效率有较大幅度提高(约20%,随着工人熟练程度的提高可能更高),可节约人力成本,并减少人为因素对铁芯质量的影响;也有不可忽视的一些缺点,如空载损耗增大,影响铁芯性能;下料时换模用时较多,影响横剪班工序下料时间;下料产生毛刺,影响铁芯噪音。
2.3铁芯横向步进改纵向步进试验
经过打孔试验,从结果中我们发现全片型打孔模式的最大劣势在于空载损耗高于平常的空载损耗约10%。
这个数值基本上相当于铁芯用料的硅钢片升一个牌号,即使换成小孔模具后空载损耗也超过原不打孔铁芯的7%。
在此基础上,我们通过不断研究发现,将横向三步进、两片一叠模式改为纵向五步进、一片一叠可有效减少空载损耗。
于是,车间再次进行试验,进行认证。
车间组织员工配合,再次对型号为S11630/10的油变进行由横向步进改纵向步进的探索试验。
以下对试验过程及过程控制与技术支持做一个简单概述:
(1)针对以往打孔图纸及查阅资料算出步进打孔尺寸。
重新设计出该型号的叠片图,保证窗高、窗宽、各级厚度等参数不变,然后制作下料单,并与纵横剪
班讨论下料方案可行性。
(2)做下料拼接试验进行论证:下头几圈料时,对产品进行拼接试验,经过反复试制后成功将产品料按要求试制打孔及纵向步进成功。
(3)过程监控照前述打孔试验步骤执行。
(4)再次进行空载损耗试验,由叠片台上压完铁芯直接起吊到试验区进行试验,铁芯外观及尺寸检测结果:未打孔铁芯实测主级厚130mm,总厚256mm;打孔铁芯实测主级厚130mm,总厚256mm。
实测空载损耗试验结果:未打孔铁芯空载损耗值840W,打孔铁芯空载损耗值870W,高于未打孔铁芯3%~4%。
3案例总结
该案例我们通过两种试验暂时缩短了批量较大且产品为容易制作的干变铁芯或对空损要求不高的油变铁芯订单中的叠片时间。
该方案对于小批量产品来说并不存在优势,即便如此,笔者仍然认为其意义较为重大,它让我们看到了全片型打孔的优点及一些不可忽视的缺点,如横剪线下料效率将有所降低,而且料架的使用数目增加,但至少在全自动化道路上又迈进了一步。
每一个好的工艺及其变更都需要经历反复磨砺及不断试验验证,逐级推进,在新的“十三五”征程上,笔者会将课题继续推广落实,并不断优化。
收稿日期:20150917
作者简介:刘延昭(1986—),男,湖南衡阳人,助理工程师,研究方向:变压器制造。