板形自动控制
阿亨巴赫铝箔轧机板形自动控制系统
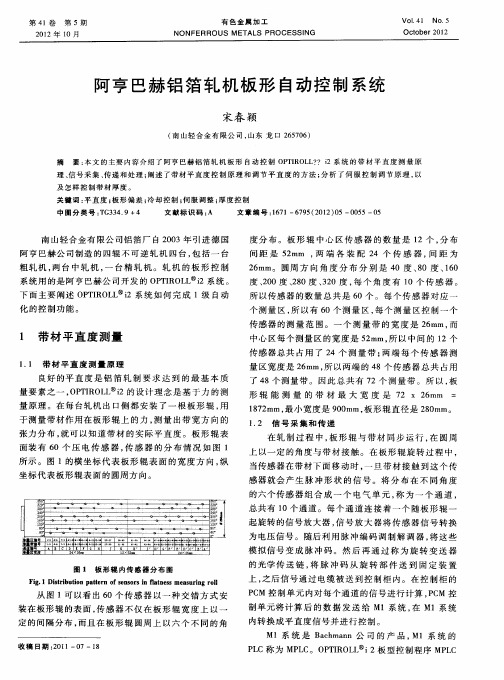
南 山轻 合金 有 限公 司铝箔 厂 自 2003年引 进德 国 阿 亨 巴赫 公 司 制 造 的 四 辊 不 可 逆 轧 机 四 台 ,包 括 一 台 粗轧 机 ,两 台 中轧 机 ,一 台精 轧 机 。 轧 机 的 板 形 控 制 系 统 用 的 是 阿 亨 巴 赫 公 司 开 发 的 OPTIROLL@i2系 统 。 下面 主要 阐述 OPTIROLL@i2系 统 如何 完成 1级 自动 化 的控 制 功能 。
收 稿 日期 :2011—07—18
度 分 布 。板 形 辊 中心 区传 感 器 的 数 量是 12个 ,分 布 间距 是 52r am ,两 端 各 装 配 24个 传 感 器 ,间 距 为 26mm。圆周 方 向 角 度 分 布 分 别 是 40度 、8O度 、160 度 、200度 、280度 、320度 ,每 个 角 度 有 10个 传 感 器 。 所 以传 感器 的数 量 总共 是 60个 。每个 传 感器 对 应 一 个 测量 区 ,所 以有 60个测 量 区 ,每个 测量 区控制 一 个 传感 器 的测 量 范 围。一 个 测 量 带 的宽 度 是 26r am,而 中心 区每个测 量 区 的宽 度是 52mm,所 以 中间 的 12个 传感 器 总共 占用 了 24个 测 量 带 ;两端 每个 传 感 器 测 量 区宽度 是 26r am,所 以两 端 的 48个 传 感 器 总共 占用 了 48个 测 量 带 。 因 此 总 共 有 72个 测 量 带 。所 以 ,板 形 辊 能 测 量 的 带 材 最 大 宽 度 是 72 X 26mm = 1872mm,最小 宽度是 900mm,板形 辊 直径是 280r am。 1.2 信 号 采 集 和 传 递
在轧 制 过 程 中 ,板 形 辊 与 带 材 同步 运 行 ,在 圆周 上 以一定 的角 度与 带材 接 触 。在 板 形辊 旋 转过 程 中 , 当传感 器在 带材 下 面移 动 时 ,一 旦 带 材接 触 到 这个 传 感 器 就会 产 生 脉 冲形 状 的信 号 。将 分 布 在 不 同角 度 的六个 传感 器 组 合 成 一 个 电气 单 元 ,称 为 一 个 通 道 , 总共有 10个 通道 。每 个 通 道连 接 着 一个 随板 形 辊 一 起 旋转 的信 号放 大器 ,信 号放 大 器 将传 感 器信 号转 换 为 电压 信号 。 随后 利 用 脉 冲编码 调 制 解 调器 ,将 这 些 模 拟信 号变 成 脉 冲码 。然 后 再 通 过称 为旋 转 变 送 器 的光 学 传 送 链 ,将 脉 冲 码 从 旋 转 部 件 送 到 固定 装 置 上 ,之后 信号 通过 电缆 被 送 到控 制 柜 内 。在控 制 柜 的 PCM 控制 单元 内对 每个通 道 的信号 进行计 算 ,PCM控 制单 元将 计算 后 的数 据 发 送 给 M1系 统 ,在 M1系统 内转 换成 平直 度信 号并进 行控 制 。
板形自动控制

2011-6-7
13
由上述条件和体积不变定律,在原料板形良好 的前提下,保证带钢轧后平直的条件为:
H h
H h
H 原料平均厚度 h 轧件出口平均厚度 原料凸度
轧件出口凸度 延伸系数
2011-6-7 14
由上式可知: (1) 带钢的平直度与凸度密切相关 (2) 控制带钢的平直度,可以通过控制带钢的 凸度实现 (3) 对于板形良好且横截面具有一定凸度Δ的 原料,为保持轧后平直,应使轧后带钢横截面 也具有一定的凸度δ,而且
2011-6-7
19
忽略带钢弹性变形,并认为轧辊和带钢间作用 的负荷及变形对称,则轧辊有载辊形凸度曲线 可以表示为:
1 f Wb FWb (DW 0 DWT DWm )u 2 2
其中:
u b/ L
b 工作辊与轧件接触长度 L 支撑辊辊面长度
2011-6-7 20
板形自动控制
2011-6-7
1
板形自动控制
板型:用于描述成品带钢的翘曲程度 主要指标:
横向:成品带钢的断面形状(凸度、楔形等) 纵向:成品带钢的平直度等
2011-6-7
2
10.3.1 板形的数量表示方法
(1) 凸度
绝对凸度CR:为带钢宽度方向中点与两侧左右标志点 厚度平均值之差。
her hel CR hc 2
h El
40mm
hel
hc
her
h Er
2011-6-7
3
(2) 楔形 左右标志点厚度之差
CT her hel
浅谈冷轧带钢板型自动控制技术

高。因而影 响轧机 的生产能力 。此外 ,板形 不 良也使轧
机所 能轧 出的最薄规格受到限制 。
2 . 冷轧带钢板型的测量方法 :1 1 目测板形 。 在冷轧
机上 采用大张力轧制时 ,借助 于木棍打击低 速轧制 的带
钢 。根据木棍 打击带 钢 的声 音 和回弹检测 张应力 的分
布 。2 ) 用磁 力板形仪 进行测量 。 在带 张力冷轧 的情况 下 ,由于导致产生板形缺陷的不均匀延伸将使轧制张力 沿板 宽方 向的分布发生改变。非接触式的磁 力板形仪是 利用 带钢张力分布不均而引起导磁率变化的原理而制作 的仪器。仪器 的测定部分 由编成一组 的多对 探测头所组 成 ,探测头 的数 目根据板宽不 同可分为5 ~ 1 1 对。上探测
斜 调节量 ,由轧辊 压下位置进行调整 。( 2 ) 弯辊 和C VC 调节 :弯辊调节具有动作快 、简单 ,没有滞后 的特点 ,
所 以首先进行弯辊调节 。当二次板形缺陷分量在弯辊调 节能力4 0 ~ 8 0 %范围以 内时 ,单独进行弯 曲调节 。当超
出这个范围时 ,则要投入C V C 系统 ,共 同对二次板形缺
右 。同时也发现该 系统还有不完善的地方 ,如系统对板
均 ,每一段测量 出与其相接触的- -4 , 段带材( 2 5 ~ 5 0 毫米
宽) 中的张应力 ,据此反推板形并 实行控制。
二 、板 形 自动控 制 技术
板形 自动控制系统是 由板形检测装置 、控制器和板
冷轧控制ASC(AFC)简介

倾斜
中浪,边浪,M型浪, 中浪,边浪,M型浪,W型浪 ,M型浪
弯 辊 板 形 控 制
W型浪
△F I : △F W :
边浪
△FI : △FW :
ε
ε
WS
DS
WS
DS
X0
X0
中浪
△F I : △F W :
M型浪
△FI : △FW :
ε
ε
X0
WS DS WS
X0
DS
ε WS DS WS
工作辊直径 特性 应用
弯辊、倾斜控制
实际模型
ε WS DS WS ε DS WS ε DS
-1.0 X -1.0 1.0 -X0 X0 X 1.0 X
中间辊弯辊
工作辊弯辊
倾斜
εc on = g a ⋅ ∆ F I ⋅ x 2 + g b ⋅ ∆ Fw ⋅ ( x − x 0 ) 2 + g c ⋅ ∆ SL ⋅ x
ε DS
X -1.0 1.0 -X0 X0
X
中间辊弯辊
工作辊弯辊
板 形 监 视 画 面
精细冷却模糊控制
精细冷却喷嘴
i-1 ch i ch i+1 ch
精细冷却 降低工作辊的热膨胀
冷却液
冷却液会影响相邻通道
需要考虑空间上的变化
工作辊
阀门开关控制
i-1 ch
i ch i+1 ch 板形仪分区
需要考虑时间上的变化
精细冷却模糊控制
分类
连续值 带钢板形偏差 幅值
A =ε(x, t)
BN BZ BP
IF (A=AP) AND (B=BP) AND (C=CF) THEN α=MID
冷轧钢板形自动控制技术

冷轧钢板形自动控制技术
冷轧钢板形自动控制技术是指采用冷轧钢板的控制和参数调整,以实现自动化生产的技术。
随着科技的发展,人们越来越依赖自动化设备来节省时间和精力。
冷轧钢板的自动控制是一种有效的工业自动化技术,可以有效提高生产效率。
冷轧钢板的自动控制技术主要依靠控制器和传感器,实现对冷轧钢板的自动控制和参数调整。
通过控制参数,可以调整冷轧钢板的厚度,宽度和长度等参数,以满足不同需求。
同时,可以根据不同的产品特性,调整钢板的结构,从而获得更好的产品性能。
冷轧钢板的自动控制技术不仅可以提高产品质量,而且可以大大减少生产成本,改善生产效率。
此外,还可以为客户提供更可靠的产品和服务,从而提高客户满意度。
冷轧钢板的自动控制技术为当代生产和制造提供了一种可靠、安全、高效的解决方案,它可以有效提高产品质量和生产效率,为企业提供更多的可能性和机会。
带材板形的自动控制
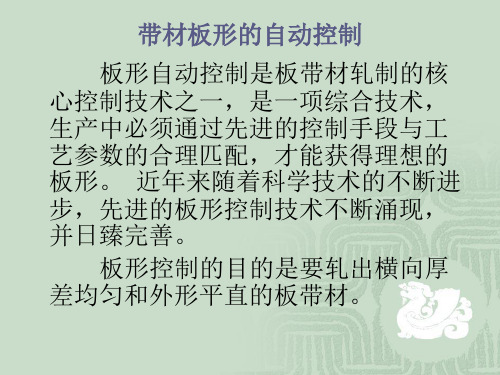
三、反馈控制的计算模型 板形测量信号一般都是离散的信号。 其计算模型有多种,其中主要的有4种方 法,即 模式识别法 参数评价法 影响函数法 人工智能法
带材板形的Байду номын сангаас动控制
板形自动控制是板带材轧制的核 心控制技术之一,是一项综合技术, 生产中必须通过先进的控制手段与工 艺参数的合理匹配,才能获得理想的 板形。 近年来随着科学技术的不断进 步,先进的板形控制技术不断涌现, 并日臻完善。 板形控制的目的是要轧出横向厚 差均匀和外形平直的板带材。
一、板形的概念 在直观上是指板带材的平直度, 即浪形、瓢曲、翘曲、折皱或旁弯等 板形缺陷的程度,其实质是指带钢内 部残余应力分布状况,即轧件在宽度 方向变形的均匀程度。 二、板形缺陷常见种类 有:浪形、瓢曲、翘曲、折皱或旁弯 等。
热连轧机的闭环反馈控制,主要是根
据精轧出口处的板形测量仪的实测结 果,反馈调整最后一个或几个机架的 弯辊力,达到保证带钢平直的目的。 冷连轧机的闭环反馈控制,一般在最 末机架安装板形测量辊,与最末机架 形成闭环反馈。有的轧机在第一机架 也装有板形测量辊和闭环反馈系统。
二、反馈控制策略:根据板形调控手段 的数量和各自特点,确定对于这些板 形调控手段如何分配板形偏差。 反馈控制策略总体上可以分为两 大类,即接力方式与分配方式。 接力方式:确定控制层次及优先调节 权。 分配方式:分配板形偏差,并计算各 个调控手段的调节量。
2. 板形目标曲线的确定 (1)概念 板形目标曲线:指板形控制系统调节带 钢板形(由板形仪测得的 前张应力)应达到的目 标。 板形目标曲线代表了生产者所期望 的实物板形质量,其研究过程经历了三 个发展阶段。
由于来料情况不同,或是根据客户 的需要,或是根据生产的实际情况,如 裂边、浪形、楔形等,可选择不同的目 标曲线组织生产。板形仪一般可以存贮 近50条目标曲线,供操作人员选择。 目标曲线的选用可分为两个参数: 形状,即目标曲线号 幅值,即曲线正负值的大小。
板形自动控制在热连轧中的应用

机 械 工 程 与 自 动 化
M ECHANI CAL ENGI NEERI NG & AUT( ) M ATI ( ) N
NO .5 Oc t .
文章 编 号 : 1 6 7 2 — 6 4 1 3 ( 2 0 1 3 ) 0 5 — 0 2 0 8 — 0 2
置 主要是 利用 传感 技 术来 实 现 对 带 钢 板 形 的检 测 , 板 形 检测 主要 分两种 : 测 量 带 材横 向 张力 分 布 的 隐 含板 形 和测量 带材 表 面波浪 度 的宏 观 波形 。热 轧过程 中使 用 的检测 装 置 以测 量宏 观 板 形 为 主 , 目前 钢 铁 公 司采 用 较 多的是 激光板 形仪 。 1 板 形控 制 系统构 成 带 钢热 连轧 板 形 质 量 控 制 的 区 域 主 要 是 在 精 轧 区, 在精 轧 区域 的出 口安装 凸度 仪 和平 坦 度 仪 是 保证 板 形控制 的关 键 。 目前 , 热 连轧 生 产 线 大 多 采 用 四辊 六 机架 连轧 机组 , 对 于每 个 机 架来 说 都 具 备 正 负 弯 辊 和窜 辊 的 功 能 。 系 统 设 定 弯 辊 力 的 最 大 调 节 值 达 4 0 0 0 k N, 机架 F 1 、 F 2 、 F 3的 最 大 窜 辊 量 为 1 5 0 mm, F 4 、 F 5 、 F 6的最 大 窜 辊 量 为 2 0 0 mm。弯 辊 控 制是 动 态 板形 调控 的重要 手段 , 凸度 控制 、 平坦 度控 制 为反馈 的辅助 手段 。 板 形控 制程序 根 据其 系统 结 构 图设 计 编 写 , 如 图 1 所示 。该 系 统 中 主要 包 含 板 形 设 定 、 弯辊 力 前 馈控 制、 弯辊 力正 弯与 负 弯控 制 、 凸度 仪 的反 馈 闭 环 控 制 、 平 坦度 的反馈 闭环 控 制 、 板 形 与板 厚 的解 耦 控 制 等 手 段 。其 中板 形设定 主要 是 由操 作 人员 根据 客户 的 生产 要求, 按 已设 计好 的数 学模 型计算 设定 , 以达 到工艺 要 求 。弯辊 力 前馈控 制 的 目的主要 是对 带钢 在轧 制生 产 中的轧 制力 波动进 行预 控制 。 凸度反馈 控 制 与平坦 度 闭环 反馈 控制 是 为了得 到理 想板 形 的一种 精 细控制 手
浅谈轧机板形控制系统的组成及控制原理

电荷放大器将压电传感器生成的电荷信号转换为电压。 旋转变送器(PCM 变送器)将这些电荷放大器的输出信号 转换为(PCM 编码的)数字信号。数据通过电缆从旋转变 送器传递给安装在控制柜内的 PCM 解码器插架(PCM 已 经停产,现在基本都采用集成的 SIKO 模块代替 IOP 模块及 PCM 插架)。下图是 SIKO 模块实物图。
[1] 阿 亨 巴 赫 .OPTIROLL i2 SFC and SCA Training[CP/ K].2004[2021.5]. 设备厂家 .
Fti = 每个测量区铝箔张力 Fri= 每个传感器的径向力 HExit= 铝箔出口厚度
图 2 传感器受力模型
图 1 板形辊结构
收稿时间 :2021-05 作者简介 :郭明明,生于 1985 年,男,助理工程师,高级技师,研究方向 : 自动化控制、传动控制、设备管理。
铝箔两边张力 Fti 会产生一个向下的压力 Fri 即传感器的 径向压力。那压电传感器上会产生电荷脉冲。每个脉冲的强 度取决于轧制铝箔在铝箔横截面上的长度分布情况 , 铝箔精 确位置对覆盖少的传感器影响很大,以至于只有传感器覆盖 面积超过额定 50%,系统才可以使用测量。
M 冶金冶炼 etallurgical smelting
- 1、下载文档前请自行甄别文档内容的完整性,平台不提供额外的编辑、内容补充、找答案等附加服务。
- 2、"仅部分预览"的文档,不可在线预览部分如存在完整性等问题,可反馈申请退款(可完整预览的文档不适用该条件!)。
- 3、如文档侵犯您的权益,请联系客服反馈,我们会尽快为您处理(人工客服工作时间:9:00-18:30)。
板形自动控制系统
1板形
1.1板形
板形是板带的重要质量指标,主要包括板带的平直度,横截面凸度(板凸度)、和边部减薄量三项内容。
1.1.1板形平直度是指板带纵向形状平直度,即板带纵向有无波浪形。
其实质是板带内部产生了不均匀的残余应力。
例如:我们在生产过程中常见的边波,主要是由于在轧制过程中板带纵向延伸量的不均匀造成的。
当板带两边压下量大于中部时,板带两边延伸量较大,就产生了边波,如图1.1。
我们在生产过程中当边波出现,通常采用用加大张力的方法来消除边波。
冷轧带钢平直设备设计指标如表1.1。
图1.1
表1.1冷轧带钢平直度设备设计指标。
带钢厚度范围(mm)带钢宽度(mm)1000~1500
0.2~0.6 9Unit
0.5~1.0 8Unit
1.0~1.5 6Unit
1.1.2板凸度
板凸度分为绝对板凸度和相对板凸度。
绝对板凸度是带板沿厚度方向中心处厚度与边部厚度的厚度差。
我们生产中的来料钢卷中高在五丝以内。
相对板凸度是将绝对板凸度除以板带的平均厚度。
带板在轧制过程中能够均匀延伸时,轧后板带绝对板凸度较轧前板带绝对凸度缩小一个延伸率,就能够获得良好的平直度。
1.1.3边部减薄量
边部减薄是在板带轧制时发生在轧件边部的一种特殊现象。
考虑这一现象后的板带横断面在接近板带边部处,其厚度突然减小,这种现象称为边部减薄。
故严格来说,实际的板凸度是针对除去边部减薄区以外的部分来说的。
边部减薄量也是板形的一个重要指标。
边部减薄量直接影响板带边部切损的大小,与成材率有密切关系。
我们生产的钢卷边部10~30公分为板型做松区,也就是边部减薄区。
发生边部减薄现象的主要原因有两个:
1)轧件与轧辊的压扁量,在轧件边部明显减小。
2)轧件边部金属的横向流动要比内部金属容易,这进一步降低了轧件边部的轧制力与其轧辊的压扁量,使轧件边部减薄量增加。
2板形控制
2.1板形控制目的
板形调控的目的是要轧制出横向厚差均匀和外形平直的板带材。
2.2板形控制分类
板形控制系统分为闭环板形控制系统、开环板形控制系统和复合板形控制系统。
我公司采用的的是闭环板形控制系统。
2.3闭环控制
2.3.1闭环控制
闭环控制是控制论的一个基本概念。
指作为被控的输出以一定方式返回到作为控制的输入端,并对输入端施加控制影响的一种控制关系。
在控制论中,闭环通常指输出端通过“旁链”方式回馈到输入,所谓闭环控制。
输出端回馈到输入端并参与对输出端再控制,这才是闭环控制的目的,这种目的是通过反馈来实现的。
2.3.2闭环控制原理
闭环控制系统控制原理:通过板形仪及其信号处理装置获取实际板形信号,计算实际板形与目标板形的偏差,经板形控制计算机处理后,将调节信号送到板形调节机构,由板形调节机构对带钢进行在线调节,使带钢板形得以纠正。
2.3.1闭环控制系统简介
板形闭环反馈控制的目的是为了消除板形实测值与板形目标曲线之间的偏差。
该系统有三部分组成即板形检测装置、控制系统和板形调节系统(执行机构)。
投入闭环反馈控制的前提条件是有准确的板形实测信号,而控制器是板形控制的重要组成部分,其控制精度,直接影响到实物板形的质量。
板形检测装置
我们的板形检测装置是板形仪(板形辊)。
我们用板形仪自动测量钢带平直度,这种板形仪,在轧制过程中能连续不断进行板型检测,并将带钢平直度状态直接描绘出来。
1>板型检测原理,板形仪是用压电晶体作为压力传感原件,带钢在进入卷取机前后在板型仪的测量辊上转向,并形成一个包角,包角前后张力就产生一个合力,合力作用在板型仪的压力传感器上,合力的测量值的变化被装在测量辊内的压力传感器接收,并将取得讯息通过处理器后直接在显示器的屏幕上显示,压力的变化曲线与板型是一致的,因为板型的状态直接反映了张力的变化。
2>板型辊的基本结构。
测量辊是一个实心辊,在它的外圆面上,有规律的钻有一排排小孔,每排之间的距离,以及每个圆周上安排空的数量,都可根据需要决定,排间距离越小,所测量的精度越高。
板形辊结构如图2.1
图2.1板形辊结构
3>宽带测量结果
传感器的等距离分布状态,就组合成整个带钢上的每个瞬间的板型状况,当其中某个带条上张力变小时,作用在压力传感骑上的力就小,这说明这个带条在这个部位上延伸量比相邻带条延伸量要大,也就是,如果将其切分成条,在同一原始段内的这条带钢长度,要比相邻的会稍长一些,这就是说,在这稍长的部位就出现了鼓包,如果这一情况出现在带钢边部就是褶皱。
所以在测量仪的显示器上显示的每个瞬间图形就是这一部分的整个宽度上的板型状态。
这些图形包含的讯息,通过编码器解析和转换,就变成带钢平直度数字指标IUnit,这样就能完成整个带钢平直度测量,即利用带钢条上的每一个瞬间张力变化转化成带钢平直度的变化。
如图2.1为测得的实际板形与理想板型曲线。
图2.1实际板型与理想板型曲线
②控制系统
控制系统由比较环节、板形控制计算机等构成。
板形控制系统接受到测量值后(如图2.1中柱状为板形测量的实际值),首先求出板形实测值与板形目标值之间的差值,并根据该差值进行板形控制。
通过辊箱倾斜、一中锥度调节和A、D辊凸度调节可以有效的消除大部分对称和不对称缺陷。
③板形调节系统
板型调节系统即板型控制的执行机构:启动、调节、控制板形。
板形控制的实质是对承载辊缝的控制,通过调节有载辊缝的形状,使其与来料断面形状保持一致,满足均匀变形条件,使板形平直。
凡是可以改变有载辊缝的形状的轧机部件、装置或工艺参数,均可作为调节板形的执行机构。
我们公司轧机所采用的调节方式有辊箱倾斜、一中锥度调节和A、D辊凸度调节。
这里对一中锥度调节和A、D辊凸度调节作简单介绍。
1)一中锥度调节
我们在更换一中时常会看到在一中表面包裹的衬纸上会写有一组数据。
Φ116.00、3/90、45/230。
Φ116.00是指一中直线段直径,我们生产所用的使用范围为Φ112.00~Φ116.00。
3、45分别指一段、二段锥的锥度。
90、230分别指一段、二段锥的锥长。
我们所用的一中辊面长度为1.55米。
这里的锥度是指圆锥底圆与高的比值。
在更换一中时,我们能够看到在一中辊头有两个“缺口”,其“缺口”的意思就在于表示锥度所在端。
我们将上一中的锥度端放在操作侧,将下一中的锥度端放在传动侧。
所以在调节板形时,上一中是控制操作侧板形,下一中是控制传动侧板形。
2)A、D辊凸度调节。
我们在轧制前会将A、D辊凸度调节至30、45、60、45、30。
这些数字是指凸度的变形值。
A、D辊凸度通过液压作用在被衬鞍座上的力使被衬芯轴发生微量形变,从而形成凸度,进行板形的控制。
在板形调节时系统根据板形调控手段的各自特点,确定对于这些板形调控手段如何分配板形偏差。
调节方式总体上可以分为两大类,即接力方式与分配方式。
接力方式:确定控制层次及优先调节权。
分配方式:分配板形偏差,并计算各个调控手段的调节量设定计算的基本过程。
根据各调控手段的优先权,按照选定的初值,具有高优先权的先进行计算,对辊缝凸度进行调节,当调节量达到极限值时,辊缝凸度尚未达到要求且还有控制手段可调时,剩余的偏差则由具有次优先权的调控手段进行调节,依次类推,直到辊缝凸度达到要求或再没有控手段可调为止。
板形自动控制的实现实际板形测量曲线减去目标曲线之差即为板形偏差,
板形偏差用于板形控制部分,根据板形偏差的大小来改变轧机板形执行机构的调整量,调节轧机有载辊缝形状,使实测板形趋近于目标曲线,而达到板形控制的目的。
我们公司调节系统中各调节部分占比和优先级这里不予介绍,详情可向技术部咨询。
李云飞
2016-5-6。