压缩机动力学分析
活塞式压缩机主运动——曲柄滚动轴承系统动力学仿真分析

的条件下 ,宜缩短H1 ,以力求降低整机的高度尺寸 。
3顶岸高虏h( . 即第—道活塞环槽到活塞顶的距离 ) 1 越 小 ,第一 道环本 身的热 负荷也越 高。应根 )h 据热负荷及冷却状况确定h ,使 第一道活塞环 的工作温 度不超过允许极 限 ( 8~ 2 * 约10 20C)。 2)在 保证第 一道环工作可靠 的情况下 ,尽量缩小
1 O 信息系统工程 l 0 1 1 0 5 1. . 2 12
6 根据活塞 顶部应 力 、刚度及散 热要求来 决定 是 的,小型高速柴油机的铝活塞 ,如满 足顶部有足够的传
热截面 ,则顶部 的机械强度一般也是足够 的。热应力随
隙 △o 和垂直销孔方 向的裙部 间隙 △ 。减小 △o 上 可以降
低活塞头部的热负荷 ,减小 △ 可 以减弱活塞换 向时倾 上 侧摆动与敲击缸套 现象 ,从而可大大减轻缸套 的穴蚀 , 但活塞间隙过小 ,也容易引起 活塞 的损伤和拉缸 。在销 孔轴线方 向的裙部不 承受 推力负荷 ,其间 隙 △ 稍大一 x 些对活塞运行性 能的影响不很大 ,因此在设计上 AΒιβλιοθήκη 的 X 选择可以有较大的差别 。
4活塞环的数 日及排列 . 1 )活塞环数 目一般为 : 高速机 气环2 3 ,油环 12 ; ~道 ~道
中速机 气环3 4 ,油环2 ( ~道 道 少数用一道 )
2 )油环布置:采用一j油环时,油环装在销孔上方。 酋
5环槽尺寸 环槽 的轴 向高 度等于活塞环 的轴 向高 .
度b 。
1塞高度H . 1 )活塞高度取决 于以下因素 :
式 中 D活塞名义直径 ; t 活塞环径 向厚度 ;
2013压缩机课程设计指导书(热力学与动力学)

1绪论活塞式压缩机设计是装控专业课程设计的主要方向之一。
设计题目主要以排气量小于3m3/min的微型或小型角度式空气压缩机为主。
用于提供压缩空气的角度式空气压缩机包括V型、W型、S型等结构型式,主要分为单级和两级压缩两大类,润滑方式分有油润滑和无油润滑,冷却方式主要为风冷,气阀型式主要为舌簧阀。
目前市场上通用的排气压力系列有0.4MPa、0.7 MPa、1.0 MPa、1.25 MPa、2.5MPa五档。
设计计算内容主要包括分为热力学设计、动力学设计和结构设计三部分。
热力学设计主要是确定压缩机的结构方案,确定热力学参数和主要结构参数和气缸直径等。
热力学设计中参数选择是否合理,是否符合工程实际极为关键,选择必须要有据可依。
设计过程中部分参数可能需要反复修正计算才能获得比较满意的结果。
动力学计算的主要任务是确定飞轮矩和平衡惯性力。
课程设计中主要完成飞轮矩确定。
惯性力平衡只要求明了目的、方法和可能的结果,不做计算。
结构设计内容为主要为活塞、气缸、连杆、曲轴等主要零部件的简要结构设计和设计图绘制。
设计时间为三周。
2热力学计算示例热力学计算目的:压缩机的热力计算,是根据气体压力、容积和温度之间存在的热力学关系,结合压缩机的具体特性和使用要求而进行的,其目的是确定压缩机的结构型式、合理的热力参数(各级的吸排气温度、压力、功耗等)和合理的结构参数(活塞行程、曲轴转速和气缸直径等),为动力学计算和零部件结构设计提供依据。
2.1 设计参数设计题目:设计参数:压缩介质:空气排气量:3m3/min吸气压力:0.1MPa 吸气温度:20℃排气压力:0.4MPa、0.7MPa、1.0MPa、1.25MPa和2.5MPa排气温度:一级压缩时排气温度≤200℃;两级压缩时各级排气温度≤180℃。
气阀型式:舌簧阀2.2 结构型式选择和结构参数确定结构型式:V型、W型和S型压缩机结构和结构示意图见图2.1~图2.7。
其主要特点是连杆和活塞直接连接,无十字头和活塞杆,结构紧凑。
压缩机气体脉动分析和管道振动分析(2)
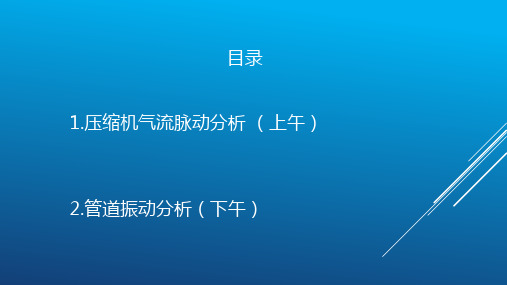
管道振动分析 : 有限元方法实例
结果提取: 1. 进一步可以选择频率21Hz,相位171.759 度时的整个管道的应力和变形情况。 2. 当然,程序也可观察任意频率、任意相位 角下的变形情况。 3. 由此可以看出,振动分析所产生的数据量 是非常巨大的。
管道振动分析 小结
1. 与静力分析相比,管道的振动分析无论是建模 输入还是结果数据都非常复杂,特别是对结果 的分析评判需要比较丰富的理论知识背景,同 时还需要比较丰富的经验和技巧。
管道振动分析 : 有限元方法
从前面的介绍可以知道,对于管道振动分析, 其基础在于构造整个系统的质量矩阵和刚度 矩阵,通过求解特征值和特征向量,得到固 有频率和模态,最后通过模态叠加法得到系 统振动响应。 但是,实际的管道系统结构形式和布置都非 常复杂,不可能直接写出其质量矩阵和刚度 矩阵,因此在分析中目前都使用有限元方法。
2. 随机振动:激力是随机的,响应也是随机的,不能用时间的确定性函数来表示,这类振 动问题通常需要用概率和统计方法来估算响应值(最大值、平均值、方差)
管道振动分析
由于动力学分析比静力分析运算量要大很多(在时间历程里面的每一个积分点都是一个静力计 算),因此对于管道工程来说,不可能对所有的振动都采用振动方法来分析,而是对大多数问 题采用简化方法~准静态方法来计算。下面简单介绍一下工程中常见的振动问题处理方法: 1. 风载荷引起的管道振动 风载荷是典型的随机振动,随机振动与确定性振动相比,其运算量更大,而通常管道由于截面 小,风载荷并非主要载荷因素,因此在实际分析中,分载荷往往是根据规范进行等效静力分析。 当然,特殊情况下,对于细长的垂直管道,有必要采用动力分析。 2. 地震引起的管道振动 与风载荷类似,地震载荷也是典型的随机振动。为了简化计算,在管道应力分析中如考虑地震 载荷的话,也是采用等效静力分析的方法。与设备相比,管道的质量相对较小,地震发生时管 道自身受到地震作用造成应力过大而破坏的可能性不大,通常是由于设备或者结构倒塌造成的 管道破坏。
博士后科研成就沈阳工业大学赵晶
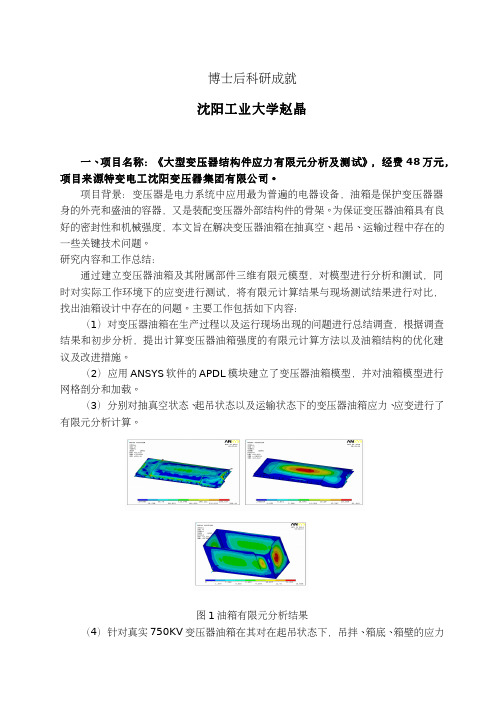
博士后科研成就沈阳工业大学赵晶一、项目名称:《大型变压器结构件应力有限元分析及测试》,经费48万元,项目来源特变电工沈阳变压器集团有限公司。
项目背景:变压器是电力系统中应用最为普遍的电器设备,油箱是保护变压器器身的外壳和盛油的容器,又是装配变压器外部结构件的骨架。
为保证变压器油箱具有良好的密封性和机械强度,本文旨在解决变压器油箱在抽真空、起吊、运输过程中存在的一些关键技术问题。
研究内容和工作总结:通过建立变压器油箱及其附属部件三维有限元模型,对模型进行分析和测试,同时对实际工作环境下的应变进行测试,将有限元计算结果与现场测试结果进行对比,找出油箱设计中存在的问题。
主要工作包括如下内容:(1)对变压器油箱在生产过程以及运行现场出现的问题进行总结调查,根据调查结果和初步分析,提出计算变压器油箱强度的有限元计算方法以及油箱结构的优化建议及改进措施。
(2)应用ANSYS软件的APDL模块建立了变压器油箱模型,并对油箱模型进行网格剖分和加载。
(3)分别对抽真空状态、起吊状态以及运输状态下的变压器油箱应力、应变进行了有限元分析计算。
图1油箱有限元分析结果(4)针对真实750KV变压器油箱在其对在起吊状态下,吊拌、箱底、箱壁的应力值,先进行了有限元计算分析,再对此台产品进行试验测量,通过对比、修正,获得了较为准确的应力数据。
图2变压器器身吊装过程有限元分析结果图3变压器箱体耐压实验现场(1)图4 实验现场(2)二、项目名称:《CAP1400屏蔽电机核主泵研制》,经费20万元,项目来源:沈阳市科技计划项目工业科技专项。
项目背景:在CAP1400核主泵自主研发的过程中,探明核主泵设计、制造中的关键科学问题,弄清其设计思想及机理,对实现核主泵顺利国产化,保障我国核电事业顺利健康发展有重大的现实意义。
在保证核主泵具有满足设计要求的水力性能同时,良好的结构特性也是设计者需要考虑的重要因素之一。
满足强度要求、具有良好的水力及振动特性以及低噪声是实现核主泵在高温、高压、强辐射环境中能够长期、稳定、可靠运行的保证。
离心压缩机动力学建模与分析

离心压缩机动力学建模与分析离心压缩机是广泛应用于工业生产和交通运输等领域的重要设备,其动力学建模与分析对于提高压缩机性能和优化系统运行至关重要。
在本文中,将探讨离心压缩机动力学建模与分析的方法和应用。
一、离心压缩机的基本原理离心压缩机是通过转子内部的离心力将气体吸入,并通过旋转转子将气体压缩,从而达到增加气体压力和流量的目的。
其基本原理可以归纳为三个关键步骤:吸入、压缩和排出。
吸入过程:当转子旋转时,压缩机的进气口打开,气体被离心力吸入到转子内部。
在这个过程中,进气量和进气温度对于压缩机的性能有着重要影响。
压缩过程:一旦气体进入到转子内部,随着转子的旋转,气体被推向离心压缩机的出口。
在这个过程中,气体被不断压缩,从而增加气体的压力和密度。
排出过程:离心压缩机的出口打开,经过旋转后的气体被排出到管道或其他设备中。
排出过程中,气体的压力和流量将达到设定的要求。
二、离心压缩机的动力学建模离心压缩机的动力学建模主要基于气体力学和旋转机械原理。
目前,常见的建模方法包括数学建模和计算流体力学(CFD)建模。
数学建模:数学建模主要依靠基于物理原理的方程组,通过建立各个部件的质量守恒、能量守恒和动量守恒等方程,对离心压缩机的性能进行模拟和预测。
数学建模方法包括等熵模型、多级模型和非等墒模型等。
CFD建模:CFD建模是利用计算流体力学方法对离心压缩机内部流场进行数值模拟和分析的方法。
通过离散化连续介质模型和求解流体连续方程、动量方程和能量方程等进行模拟计算,可以得到更详细的流动特性和参数分布。
三、离心压缩机动力学分析的应用离心压缩机动力学分析广泛应用于设计优化、性能评估、故障诊断和运行优化等方面。
设计优化:通过动力学分析,可以对离心压缩机的几何形状、材料选择和工艺参数等进行优化。
例如,通过改变叶轮的截面形状和叶片的角度,可以提高离心压缩机的效率和性能。
性能评估:通过动力学分析,可以对离心压缩机的性能进行评估和比较。
往复压缩机活塞杆反向角计算及分析

往复压缩机活塞杆反向角计算及分析往复活塞式压缩机是社会中各行的大型工业都不可或缺的设备。
尤其在石油相关行业中大量使用该种压缩机,成为了该行业的核心设备。
本文首先进行往复式活塞压缩机反向角以及其在变工况环境下的基于热力学、动力学计算,在计算的基础上得到了不同工况下的综合活塞力图,根据综合活塞力图分析分析了工况变化对反向角的影响规律。
标签:往复压缩机;动力计算;变工况;反向角1引言反向角的反向程度大小与十字头销、铜套的损坏程度以及压缩机工作正常与否有着密不可分的关系。
铜套和十字头销工作中紧紧贴合且受到加速度大的改变冲击,因此一个足够的反向角用来让他们得到充分的润滑、冷却。
倘若十字头在十字头销所受到的合力作用下贴紧于活塞侧,这时相对的一侧会出现一个缝隙。
在重力、压力相关因素作用下,润滑油流入该缝隙,润滑和冷却该侧的零部件[1]。
若十字头销所受合力仅指向一个方向,并且十字头销自始至终压紧在铜套的一侧,那么受压的另一侧始终没有间隙,冷却和润滑状况十分恶劣,十字头销和铜套便会迅速损坏,影响往复式压缩机正常的工作。
2 反向角的定义当曲轴旋转360度过程中,作用在十字头销和铜套而且和气缸中心线方向一致的总负载分量,角度产生180度变化,这个负向载荷连续作用的时间段内表征的曲柄转角,叫做反向角。
其中API618准则确定反向角不得低于15度,ARIAL 公司规定最小反向角不得低于25度,COOPER公司制定准则其反向角不得小于30度[2]3 往复式活塞压缩机的动力计算在这里把L型往复式活塞压缩机动力计算程序作为引例,其具备如下功能:(1)初始数据部分:根据任务书得到原始数据。
(2)热力计算部分:根据初始数据计算有关热力参数,为后续的动力计算部分做一个铺垫。
(3)动力计算部分:计算各级活塞压缩机的往复惯性力、气体力和摩擦力,进而计算得到综合活塞力和总切向力[3]。
往复式活塞压缩机动力计算初始数据截图如图1所示:在第1列单元数据表中键入曲柄转角α的数值,每隔5°进行一次取点分析计算,从0°到360°共取73个点。
(完整版)活塞式压缩机的受力分析

I I I II
因动力计算中规定使连杆产生拉伸应力的 力为正,反之为负故式中将负号去掉。
2
一阶往复惯性力
II msr 2 cos 为一阶往复惯
性力。其变化的周期等于曲轴转一周的时 间。
当 00 时,为最大值:
旋转的作用,故称为阻力矩。
自由力
至于PL 又可( P / PL cos )再分解
为一个侧向力 N 和活塞力 P 。 N
和十字头销上的 N 构成一个力矩 Nh'
(图2);
活塞力 P Pg I 。
自由力
气体力和从固定件传来的气体力相互
抵后,主轴O点处只作用着惯性力 I 。
它和曲柄销中心B点处作用着的旋转惯 性力(离心力),这两个力无法在内部 平衡,都会传到机器外,故称自由力或 外力。
卧式机器设计支承的问提
卧式机器由于气缸轴线方向串联有机身、 中体、接筒以及级差式气缸等零件而使机器 过长,为支承其重量应设计成为不要限制其 轴向位移的支承。否则会使中体与机身连接 法兰处受力不均,甚至造成中体连接螺栓在 下半周者断裂事故。
惯性力、活塞力
2)、惯性力 I ,也是交变力。其 和气体力构成活塞力。即:P Pg I
旋转惯性力
旋转惯性力的作用方向始终沿着曲柄
半径指向外,而且规定使曲柄承受拉伸为
正值,受压缩为负值,故式中负号可不顾
及。
mr —旋转质量=曲轴的旋转质量+
(0.6-0.7)连杆质量。
第二节、压缩机中的作用力
一、压缩机运行时的作用力
①空负载运行中:曲柄连杆机构只产生惯 性力和摩擦力。
②满负载运行而突然在止点停车时,压缩 机中只有最大气体力作用在有关零件上。
用转子动力学及有限元建模分析大型工业涡轮压缩机
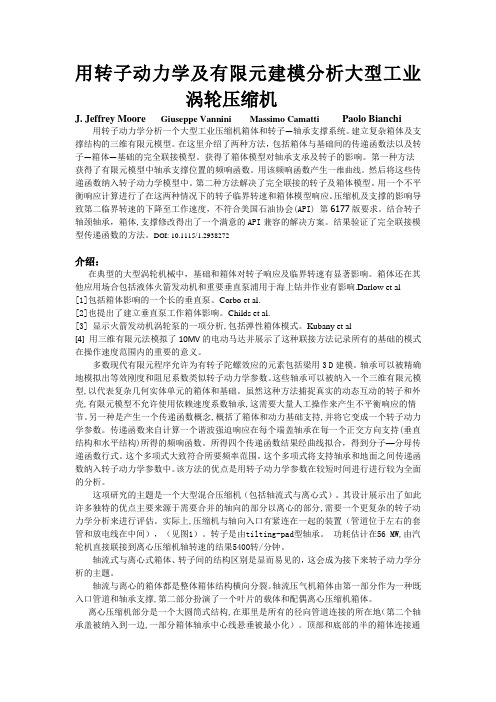
用转子动力学及有限元建模分析大型工业涡轮压缩机J. Jeffrey Moore Giuseppe Vannini Massimo Camatti Paolo Bianchi 用转子动力学分析一个大型工业压缩机箱体和转子—轴承支撑系统。
建立复杂箱体及支撑结构的三维有限元模型。
在这里介绍了两种方法,包括箱体与基础间的传递函数法以及转子—箱体—基础的完全联接模型。
获得了箱体模型对轴承支承及转子的影响。
第一种方法获得了有限元模型中轴承支撑位置的频响函数。
用该频响函数产生一维曲线。
然后将这些传递函数纳入转子动力学模型中。
第二种方法解决了完全联接的转子及箱体模型。
用一个不平衡响应计算进行了在这两种情况下的转子临界转速和箱体模型响应。
压缩机及支撑的影响导致第二临界转速的下降至工作速度,不符合美国石油协会(API)第6177版要求。
结合转子轴颈轴承,箱体,支撑修改得出了一个满意的API兼容的解决方案。
结果验证了完全联接模型传递函数的方法。
DOI: 10.1115/1.2938272介绍:在典型的大型涡轮机械中,基础和箱体对转子响应及临界转速有显著影响。
箱体还在其他应用场合包括液体火箭发动机和重要垂直泵浦用于海上钻井作业有影响.Darlow et al[1]包括箱体影响的一个长的垂直泵。
Corbo et al.[2]也提出了建立垂直泵工作箱体影响。
Childs et al.[3] 显示火箭发动机涡轮泵的一项分析,包括弹性箱体模式。
Kubany et al[4] 用三维有限元法模拟了10MV的电动马达并展示了这种联接方法记录所有的基础的模式在操作速度范围内的重要的意义。
多数现代有限元程序允许为有转子陀螺效应的元素包括梁用3 D建模。
轴承可以被精确地模拟出等效刚度和阻尼系数类似转子动力学参数。
这些轴承可以被纳入一个三维有限元模型,以代表复杂几何实体单元的箱体和基础。
虽然这种方法捕捉真实的动态互动的转子和外壳,有限元模型不允许使用依赖速度系数轴承,这需要大量人工操作来产生不平衡响应的情节。