第二章精密切削加工
合集下载
2精密磨削加工

精密磨削机理
②磨粒的等高性
微刃是由砂轮的精 细修整形成的,分布在 砂轮表层的同一深度上 的微刃数量多,等高性 好(即细而多的切削刃具 有平坦的表面) 。 由于加工表面的残 留高度极小,因而形成 了小的表面粗糙度值。
磨粒的等高性
1 粘结剂 2 磨料 3 砂轮表面
精密磨削机理
③微刃的滑擦、挤压、抛光作用
多用球磨机,而涂敷多用类似印刷机的涂敷机,可获得质量
良好的砂带。
静电植砂法:利用静电作用将砂粒吸附在已涂胶的基底上。
能使砂粒尖端朝上,因此切削性能强,等高性好、加工质量好。
2. 2
精密磨削加工机理
精密磨削是指加工精度为l--0.1μm、表面粗糙度值R a 达到0.2--0.025μm的磨削加工方法,又称低粗糙值磨削。 它是用微小的多刃刀具削除细微切屑的一种加工方法。一般 是通过氧化铝和碳化硅砂轮来实现的。 一般用于机床主轴、轴承、液压滑阀、滚动导轨、量规 等的精密加工。
补充概念
粒度指磨料颗料的大小。粒度分磨粒与微粉两组。磨粒用 筛选法分类,它的粒度号以筛网上一英寸长度内的孔眼数来表 示。例如 60#粒度的的磨粒,说明能通过每英寸长有 60 个孔 眼的筛网,而不能通过每英寸 70 个孔眼的筛网。 微粉用显微测量法分类,它的粒度号以磨料的实际尺寸来 表示( W )。如W20表示微粉的实际尺寸为20μm。 粒度号 适用范围 粗磨、荒磨、切断钢 坯、打磨毛刺 粗磨、半精磨、精磨 粒度号 适用范围 精磨、超精磨、螺纹 磨、珩磨 精磨、精细磨、超精 磨、镜面磨
涂覆磨具
涂覆磨具是将磨料用粘结 剂均匀的涂覆在纸、布或其它 复合材料基底上的磨具,又称 为涂敷磨具。 常用的涂敷磨具是有砂纸、 砂带、砂布、砂盘和砂布套等。
精密与特种加工

精密与超精密加工技术
表7-3 几种典型精密零件的加工精度
零件
激光光学零件 多面镜
加 工 精 度
形状误差 0.1μm 平面度误差 0.04μm
表面粗糙度
Ra 0.01~0.05μm Ra <0.02μm
磁头
磁盘 雷达导波管
平面度误差 0.04μm
波度 0.01 ~0.02μm 平面度垂直度误差 < 0.1μm
精密与超精密加工技术
金刚石晶体的面网距和解理现象 ◎金刚石晶体的(111)晶面面网密度最大,耐磨性最好。
◎(100)与(110)面网的面间距分布均匀;(111)面网 的面间距一宽一窄(图) ◎ 在 距 离 大 的 ( 111 ) 面之间,只需击破一个 共价键就可以劈开,而 在 距 离 小 的 ( 111 ) 面 之间,则需击破三个共 价键才能劈开。
精密与特种加工
绪
论
一、精密与特种加工在制造业中 的地位与作用
• 精密加工 • 特种加工
二、课程性质和任务
第一章 精密切削加工
§1-1 概述
一、精密加工及其关键技术简介
• 精密加工及其重要性 • 精密加工关键技术 精密加工机床、金刚石刀具、 精密切削机理、稳定的加工环境、 误差补偿、精密测量技术
二、精密切削加工分类 三、精密加工与经济性
Ra <0.02μm
Ra <0.02μm Ra <0.02μm
卫星仪表轴承
天体望远镜
圆柱度误差 <0.01μm
形状误差 < 0.03μm
Ra <0.002μm
Ra <0.01μm
精密与超精密加工技术
102 加工误差(μm) 101 加工设备 车床,铣床 测量仪器 卡尺 百分尺 比较仪
机加工工艺--机加工加工方法

4. 钻削的应用
钻孔主要用于粗加工。如螺钉孔、油孔、内螺纹底孔等。 单件、小批生产中、小型工件上的小孔(D<13mm),
常用台式钻床加工。 中、小型工件上较大的孔(D<50mm),常用立式钻床加工。
大型工件上的孔,则采用摇臂钻床加工。
回转体工件上的孔,多在车床上加工。
二、扩孔和铰孔
1. 扩孔 用扩孔钻对工件上已有的孔进行扩大加工。
ae
ae
端铣法可以通过 调整铣刀和工件 的相对位置,调 节刀齿切入和切 出时的切削厚度, 从而达到改善铣 削过程的目的。
铣削工艺特点及应用
1. 铣削特点
1)生产率高(多齿刀具、速度高); 2)散热条件好; 3)容易产生振动。
2. 铣削的应用
主要加工平面。同时可加工沟槽、成形面、切断等。
§5
磨削加工
第二章 切削加工方法
§1 车削加工
车削 — 用车刀在车床上加工工件的工艺过程。 加工精度:IT8~IT7,表面粗糙度:Ra=1.6~6.3um 主运动 — 工件的旋转运动。 进给运动 — 刀具的直线运动。
所以:车削加工适宜各种回转体表面的加工。
普通车床 — 适于各种中、小 型轴、盘、套类零件的单件、 小批量生产。 转塔式六角车床 — 适于加工 零件尺寸较小、形状较复杂的 中、小型轴、盘、套类零件。 立式车床 — 适于直径较大、 长度较短的重型零件。 (L/D=0.3~0.8) 数控车床 — 适于多品种、 小批量生产复杂形状的零件。
内圆磨与铰孔和拉孔相比较:
① 可以加工淬硬工件的孔; ② 不仅能保证孔本身的尺寸精度和表面质量,还可以提 高孔的位置精度和形状精度。 ③ 生产率低比铰孔低,比拉孔更低。
磨孔一般仅用于淬硬工件孔的精加工。
第二章 金刚石刀具精密切削加工

复习晶体结构
晶格模型
面心结构
晶体结构指晶体内部原子规则排列的方式.晶体结构不同, 其性能往往相差很大。为了便于分析研究各种晶体中原子 或分子的排列情况,通常把原子抽象为几何点,并用许多 假想的直线连接起来,这样得到的三维空间几何格架称为 晶格。
晶胞
Z
晶胞
c
b Y
a
X
晶格常数 a , b, c
人造单晶金刚石刀具 金刚石刀具 PCD刀具
多晶金刚石刀具
CVD金刚石薄膜涂层刀具
CVD金刚石刀具 金刚石厚度膜焊接刀具
金刚石刀具的性能特点
极高的硬度和耐磨性:硬度达HV10000,是自然界最硬的物质, 具有极高的耐磨性,天然金刚石耐磨性为硬质合金80-120倍,人 造金刚石耐磨性为硬质合金60-80倍。 各向异性能:单晶金刚石晶体不同晶面及晶向的硬度、耐磨性能 、微观强度、研磨加工的难易程度以及与工件材料之间的摩擦系 数等相差很大,因此,设计和制造单晶金刚石刀具时,必须进行 晶体定向。
二、典型机床简介
Pneumo 公司的MSG-325超精密车床
采用T形布局,机床空气主轴的径向圆跳动和轴向 跳动均小于等于0.05μm。床身溜板用花岗岩制造,导 轨为气浮导轨;机床用滚珠丝杠和分辨率为0.01μm的 双坐标精密数控系统驱动,用HP5501A双频激光干涉仪 精密检测位移。
DTM-3大型超精密车床
分为:液体静压和空气静压
供油压力恒定的液体静压轴承
主轴始终悬浮 在高压油膜上
液体静压轴承与气压轴承
1、液体静压轴承主轴
优点
回转稳定性好 刚度高 无振动
缺点
回转运动有温升 回油时有空气进入油源 注:空气静压轴承原理与静
《精密和超精密加工技术(第3版)》第2章超精密切削与金刚石刀具

3)积屑瘤呈鼻形并自切削刃前伸出,这导致实际切削 厚度超过名义值。超精密切削的切削厚度原来就很小 ,增加切削厚度将使切削力明显增加。
三、使用切削液减小积屑瘤,减小加工表面粗糙 度值
图2-11 超精密切削时切削速度对加工表面粗糙 度的影响 f=0.0075mm/r ap=0.02mm
加工硬铝时,如将航空汽油作为切削液,可明显减小 加工表面粗糙度值,并且在低速时表面粗糙度值也很 小。这说明使用切削液后,已消除了积屑瘤对加工表 面粗糙度的影响,从污染环境看,应在保证加工表面 质量的条件下,尽量少用切削液。加工黄铜时,切削 液无明显效果,低速时加工表面粗糙度值不大,故加 工黄铜时可不使用切削液。
加的原因如下:
1)鼻形积屑瘤前端的圆弧半径R为2~3μm,较原来金刚 石车刀的切削刃钝圆半径rn(0.2~0.3μm)大得多。
2)积屑瘤存在时,它代替金刚石切削刃进行切削,积屑 瘤和切屑间的摩擦及积屑瘤和已加工表面之间的摩擦 都很严重,摩擦力很大,大大超过金刚石和这些材料之 间的摩擦力,这导致切削力的增加。
超精密切削刀具磨损和寿命
图2-2 磨损的金刚石切削刃
正常刀具磨损情况,一般磨 损主要在后刀面上。
图2-3 剧烈磨损的金刚石切削刃
剧烈磨损情况,从图中可看 到磨损区呈层状,即刀具磨 损为层状微小剥落,这大概 是由金刚石沿(111)晶面有 解理现象产生而造成这样的 磨损形式。
超精密切削刀具磨损和寿命
一、超精密切削时切削参数对积屑瘤生成的影响
图2-8 背吃刀量㊀ap对积屑瘤高度的影响
硬铝v=314m/min f=0.0075mm/r
在实验的切削参数范围内都有积屑瘤产生。
背吃刀量ap<25μm时,积屑瘤的高度h0变化 不大,但ap大于25μm后,积屑瘤高度h0将随 ap值的增加而增加,这种变化的原因大概是
三、使用切削液减小积屑瘤,减小加工表面粗糙 度值
图2-11 超精密切削时切削速度对加工表面粗糙 度的影响 f=0.0075mm/r ap=0.02mm
加工硬铝时,如将航空汽油作为切削液,可明显减小 加工表面粗糙度值,并且在低速时表面粗糙度值也很 小。这说明使用切削液后,已消除了积屑瘤对加工表 面粗糙度的影响,从污染环境看,应在保证加工表面 质量的条件下,尽量少用切削液。加工黄铜时,切削 液无明显效果,低速时加工表面粗糙度值不大,故加 工黄铜时可不使用切削液。
加的原因如下:
1)鼻形积屑瘤前端的圆弧半径R为2~3μm,较原来金刚 石车刀的切削刃钝圆半径rn(0.2~0.3μm)大得多。
2)积屑瘤存在时,它代替金刚石切削刃进行切削,积屑 瘤和切屑间的摩擦及积屑瘤和已加工表面之间的摩擦 都很严重,摩擦力很大,大大超过金刚石和这些材料之 间的摩擦力,这导致切削力的增加。
超精密切削刀具磨损和寿命
图2-2 磨损的金刚石切削刃
正常刀具磨损情况,一般磨 损主要在后刀面上。
图2-3 剧烈磨损的金刚石切削刃
剧烈磨损情况,从图中可看 到磨损区呈层状,即刀具磨 损为层状微小剥落,这大概 是由金刚石沿(111)晶面有 解理现象产生而造成这样的 磨损形式。
超精密切削刀具磨损和寿命
一、超精密切削时切削参数对积屑瘤生成的影响
图2-8 背吃刀量㊀ap对积屑瘤高度的影响
硬铝v=314m/min f=0.0075mm/r
在实验的切削参数范围内都有积屑瘤产生。
背吃刀量ap<25μm时,积屑瘤的高度h0变化 不大,但ap大于25μm后,积屑瘤高度h0将随 ap值的增加而增加,这种变化的原因大概是
先进制造技术 第2章 高速切削技术2-1
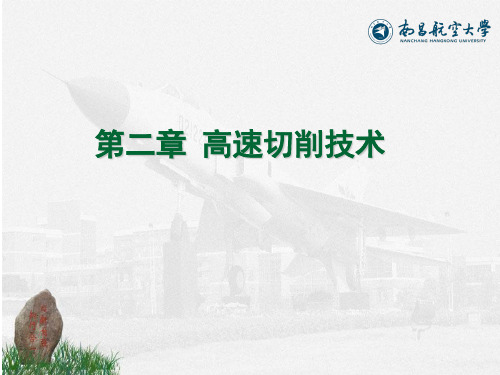
萨洛蒙在l924一1931年间,进行了一系列的高速切削实验: 在非黑色金属材料,如铝、铜和青铜上,用特大直径的刀 盘进行锯切,最高实验的切削速度曾达到14000m/min, 在各种进给速度下,使用了多达20齿的螺旋铣刀。l931年 申请了“超极限速度”专利,随后卖给了“Krupp钢与工 具制造厂”。 萨洛蒙和他的研究室实际上完成了大部分有色金属的切削 试验研究,并且推断出铸铁材料和钢材的相关曲线。 萨洛蒙理论提出了一个描述切削条件的区域或者是范围, 在这个区域内是不能进行切削的。萨洛蒙没有提出可靠的 理论解释,而且他的许多实验细节也没有人知道。
刀具磨损曲线
三、高速切削切屑形成
高速切削试验表明,工件材料及 性能对切屑形态 有决定性影响。
低硬度和高热物理性能的工件材料(铝合金、低碳钢、未 淬硬钢等)易形成连续带状切屑。 高硬度和低热物理性能的工件材料(钛合金钢、未淬硬钢 等)易形成锯齿状切屑。
切削速度对切屑形态有重要影响。对钛合金,在 (1.5~4800)m/min的切削速度范围内形成锯齿状 切屑,随切削速度的增加,锯齿程度(锯齿的齿 距)在增加,直至成为分离的单元切屑。
不同切削速度下车削45钢件的切削形态。
一方面,切削速度增加,应变速度加大,导致脆 性增加,易于形成锯齿状切屑;另一方面,切削 速度增加,切屑温度增加,导致脆性降低,不易 形成锯齿状切屑;
绝热剪切理论(Adiabatic Shear Theory) 周期脆性断裂理论(Periodic brittle fracture theoty)
萨洛蒙(Salomon)曲线
1600
切削温度/℃
钢
1200
青铜
铸铁 硬质合金980℃ Stelite合金850℃ 高速钢650℃ 碳素工具钢450℃
仪器制造工艺学2——精密机械加工(2)
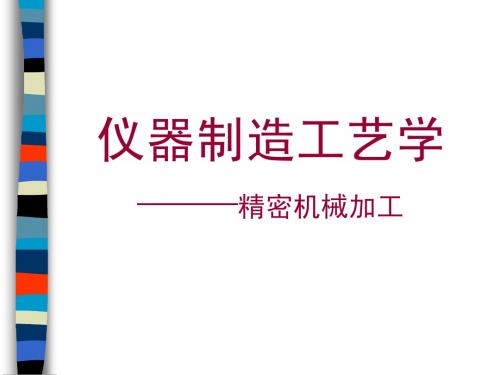
金刚石车床 加工4.5mm陶瓷球
图 金刚石车床及其加工照片
金刚石车床主要性能指标
表1 金刚石车床主要性能指标
最大车削直径和长度 /mm 最高转速 r/min 最大进给速度mm /min 数控系统分辩率 /μm 重复精度(±2σ) / μ m 主轴径向圆跳动 / μ m 主轴轴向圆跳动 / μ m 滑台运动的直线度 / μ m 横滑台对主轴的垂直度 / μ m 主轴前静压轴承(φ100mm)的刚 径向 度 /(N/μm) 轴向 主轴后静压轴承(φ80mm)的刚度 /(N/μm) 纵横滑台的静压支承刚度 /(N/μm)
超精密切削加工发展:20世纪60年代发展 起来的新技术,在国防和尖端技术领域具有重 要地位。 服从金属切削的普遍规律,但由于切削层 极薄,所以又具有一定的特殊性。 发展方向: 1、基本理论和工艺; 2、设备的精度、动态性及热稳定性; 3、精度检测和误差补偿; 4、环境控制技术; 5、加工材料。
精密磨削加工
刀具磨损、破损及耐用度
金刚石刀具可分为:机械磨损、破损和碳化磨损。(前 两种比较常见) 金刚石刀具破损的原因有:裂纹(结构缺陷)、破碎 (金刚石较脆)、解理(破坏晶面结构)。 刀具磨损分为:初期磨损阶段、正常磨损阶段、急剧 磨损阶段。 天然单晶金刚石是目前已知最硬的材料,是精密切削 中最重要的刀具。其磨损或破损到不能使用的标志是 加工表面的粗糙度超过规定值。耐用度以其切削路程 的长度表示。
切削热的来源:
1、弹塑性变形消耗功——热; 2、摩擦消耗功——热。 切削热通过改变切削温度影响切削过程。 切削温度是指:切屑、工件和刀具接触表面上的平均 温度。
刀具刀尖的温度最高,对切削过程的影的比例随刀具材料、切削用量及刀具几何 角度、加工情况等的变化有所不同。其中切削传 出的热量最多。采用微量切削方法进行精密切削 时,需要采用耐热性高、耐磨性强,有较好的高 温硬度和高温强度的刀具材料。
第二章 精密切削加工

2020/1/30
一、切削速度、进给量、修光刃和背吃刀量的影响 4、背吃刀量的影响
在刀具刃口半径足够小时,超精密切削范围内,背吃 刀量变化对加工表面粗糙度影响很小。
背吃刀量减少,表面残留应力也减少,但超过某临界 值时,背吃刀量减少反而使加工表面残留应力增加。
2020/1/30
一、刃口锋锐度对加工表面粗糙度的影响
2020/1/30
1、金刚石刀具切削部分的几何形状
金刚石车刀举例
4
3
3
1:主偏角45度
1
1
2
2:前角0度
3:后角5度
4:修光刃0.15mm
2020/1/30
2、金刚石刀具前、后刀面晶面选择
应考虑因素:刀具耐磨性好;刀刃微观强度高,不易产生微 观崩刃;刀具和被加工材料间摩擦系数低,使切削变形小, 加工表面质量高;制造研磨容易。(111)不适合作前后面。
刃口半径为0.6μm、0.3μm
刃口锋锐度对加工表面有一 定的影响,相同条件下(背 吃刀量、进给量),更锋锐 的刀具切出的表面粗糙度更 小;速度的影响不是很大。
2020/1/30
二、刀刃锋锐度对切削变形和切削力的影响
2020/1/30
锋锐车刀切削变形系数明显低于 较钝的车刀。 刀刃锋锐度不同,切削力明显不 同。刃口半径增大,切削力增大, 即切削变形大。背吃刀量很小时, 切削力显著增大。因为背吃刀量很 小时,刃口半径造成的附加切削变 形已占总切削变形的很大比例,刃 口的微小变化将使切削变形产生很 大的变化。所以在背吃刀量很小的 精切时,应采用刃口半径很小的锋 锐金刚石车刀。
2020/1/30
二、金刚石刀具的研磨加工 3、精研
提高研磨质量,使切削刃研制更为锋锐 磨料粒度越小,研磨表面粗糙度越小 研磨盘质量越好,研磨效果越好 研磨方向:逆磨,即沿切削刃口指向刀体内的方向研磨 精抛:研磨时让金刚石作垂直于研磨方向的法向运动,除
一、切削速度、进给量、修光刃和背吃刀量的影响 4、背吃刀量的影响
在刀具刃口半径足够小时,超精密切削范围内,背吃 刀量变化对加工表面粗糙度影响很小。
背吃刀量减少,表面残留应力也减少,但超过某临界 值时,背吃刀量减少反而使加工表面残留应力增加。
2020/1/30
一、刃口锋锐度对加工表面粗糙度的影响
2020/1/30
1、金刚石刀具切削部分的几何形状
金刚石车刀举例
4
3
3
1:主偏角45度
1
1
2
2:前角0度
3:后角5度
4:修光刃0.15mm
2020/1/30
2、金刚石刀具前、后刀面晶面选择
应考虑因素:刀具耐磨性好;刀刃微观强度高,不易产生微 观崩刃;刀具和被加工材料间摩擦系数低,使切削变形小, 加工表面质量高;制造研磨容易。(111)不适合作前后面。
刃口半径为0.6μm、0.3μm
刃口锋锐度对加工表面有一 定的影响,相同条件下(背 吃刀量、进给量),更锋锐 的刀具切出的表面粗糙度更 小;速度的影响不是很大。
2020/1/30
二、刀刃锋锐度对切削变形和切削力的影响
2020/1/30
锋锐车刀切削变形系数明显低于 较钝的车刀。 刀刃锋锐度不同,切削力明显不 同。刃口半径增大,切削力增大, 即切削变形大。背吃刀量很小时, 切削力显著增大。因为背吃刀量很 小时,刃口半径造成的附加切削变 形已占总切削变形的很大比例,刃 口的微小变化将使切削变形产生很 大的变化。所以在背吃刀量很小的 精切时,应采用刃口半径很小的锋 锐金刚石车刀。
2020/1/30
二、金刚石刀具的研磨加工 3、精研
提高研磨质量,使切削刃研制更为锋锐 磨料粒度越小,研磨表面粗糙度越小 研磨盘质量越好,研磨效果越好 研磨方向:逆磨,即沿切削刃口指向刀体内的方向研磨 精抛:研磨时让金刚石作垂直于研磨方向的法向运动,除
- 1、下载文档前请自行甄别文档内容的完整性,平台不提供额外的编辑、内容补充、找答案等附加服务。
- 2、"仅部分预览"的文档,不可在线预览部分如存在完整性等问题,可反馈申请退款(可完整预览的文档不适用该条件!)。
- 3、如文档侵犯您的权益,请联系客服反馈,我们会尽快为您处理(人工客服工作时间:9:00-18:30)。
➢ 超精密切削实际速度的选择根据所使用的超精密机 床的动特性和切削系统的动特性选取,即选择振动 最小的转速。
2020/8/13
总结:天然单晶金刚石刀具只能用在机床主轴转 动非常平稳的高精度车床上,否则由于振动金刚 石刀具将会很快产生刀刃微观崩刃。
2020/8/13
2020/8/13
图2-3:图a是刀刃磨损的正 常情况,图b是剧烈磨损情 况,可以看到磨损后成层状, 即刀具磨损为层状微小剥落。 图2-4:图中所示沿切削速 度方向出现磨损沟槽,由于 金刚石和铁、镍的化学和物 理亲和性而产生的腐蚀沟槽。 图2-5:金刚石切削时,若 有微小振动,就会产生刀刃 微小崩刃。
一、切削速度、进给量、修光刃和背吃刀量的影响 2、进给量的影响
在进给量f<5μm/r 时,均达到
Rmax<0.05μm的加工 表面粗糙度。
2020/8/13
一、切削速度、进给量、修光刃和背吃刀量的影响
3、修光刃的影响
修光刃长度常取0.05~ 0.20mm。 修光刃的长度过长,对 加工表面粗糙度影响不 大。 修光刃有直线和圆弧两 种,加工时要精确对 刀,使修光刃和进给方 向一致。圆弧刃半径一般 取2~5mm。
2020/8/13
一、切削速度、进给量、修光刃和背吃刀量的影响 4、背吃刀量的影响
在刀具刃口半径足够小时,超精密切削范围内,背吃 刀量变化对加工表面粗糙度影响很小。
背吃刀量减少,表面残留应力也减少,但超过某临界 值时,背吃刀量减少反而使加工表面残留应力增加。
2020/8/13
一、刃口锋锐度对加工表面粗糙度的影响
一、切削参数对积屑瘤生成的影响 1、切削速度的影响
2020/8/13
不管在多大的切削速度下都有积屑瘤生 成,切削速度不同,积屑瘤的高度也不 同。当切削速度较低时,积屑瘤高度较 高,当切削速度达到一定值时,积屑瘤 趋于稳定,高度变化不大。
2、进给量f和背吃刀量 p的影响
➢ 由图2-8可以看出在进给量很小时,积屑瘤的高度很大, 在f=5μm/r时,h0值最小,f值再增大时,h0值稍有增 加。
2020/8/13
2.2精密切削加工机理
➢ 切削速度向来是影响刀具耐用度最主要的因素,但 是切削速度的高低对金刚石刀具的磨损大小影响甚 微,刀具的耐用度极高。原因是:金刚石的硬度极 高,耐磨性好,热传导系数高,和有色金属间的摩 擦系数低,因此切削温度低,在加工有色金属时刀 具耐磨度甚高,可用很高的切削速度1000~ 2000m/min,而刀具的磨损甚小。
2020/8/13
精密加工的加工范畴
按加工精度划分,可将机械加工分为一般加工、精密加工、超 精密加工三个阶段。 精密加工:加工精度在0.1~1µm,加工表面粗糙度在Ra0.02~ 0.1µm之间的加工方法称为精密加工; 超精密加工:加工精度高于0.1µm,加工表面粗糙度小于 Ra0.01µm之间的加工方法称为超精密加工(微细加工、超微细 加工、光整加工、精整加工等 )。
2020/8/13
精密加工的关键技术
➢ 1.精密加工机床:主轴回转精度、工作台直线运动精度以 及刀具微量进给精度
➢ 2.金刚石刀具:金刚石晶面选择、刀具刃口锋利性(刀具 刃口圆弧半径)
➢ 3.精密切削机理:微量切削过程的特殊性 ➢ 4.稳定的加工环境:恒温、防振和空气净化 ➢ 5.误差补偿:根据规律设定补偿,反馈控制系统 ➢ 6.精密测量技术
第2章 精密切削加工
2.1概述 2.2精密切削加工的工艺规律和机理 2.3精密切削加工的机床及应用 2.4功率超声车削
2020/8/13
2.1概述
➢ 精密切削是使用精密的单晶天然金刚石刀具加工有色金属 和非金属,可以直接加工出超光滑的加工表面(粗糙度 Ra0.02~0.005µm,加工精度<0.01µm)。
刃口半径为0.6μm、0.3μm
刃口锋锐度对加工表面有一 定的影响,相同条件下(背 吃刀量、进给量),更锋锐 的刀具切出的表面粗糙度更 小;速度的影响不是很大。
2020/8/13
二、刀刃锋锐度对切削变形和切削力的影响
2020/8/13
锋锐车刀切削变形系数明显低于 较钝的车刀。 刀刃锋锐度不同,切削力明显不 同。刃口半径增大,切削力增大, 即切削变形大。背吃刀量很小时, 切削力显著增大。因为背吃刀量很 小时,刃口半径造成的附加切削变 形已占总切削变形的很大比例,刃 口的微小变化将使切削变形产生很 大的变化。所以在背吃刀量很小的 精切时,应采用刃口半径很小的锋
2020/8/13
1)积屑瘤前端R大约 2~3μm,实际切削 力由刃口半径R起 作用,切削力明显 增加 。
2)积屑瘤与切削层和 已加工表面间的摩 擦力增大,切削力 增大。
3)实际切削厚度超过 名义值,切削厚度 增力加 增加hD。-hDu,切削
二、积屑瘤对切削力和加工表面粗糙度的影响 2、对加工表面粗糙度的影响
积屑瘤高度大,表面粗糙度大,积屑瘤小表面粗糙度小。并 且可以看出,切削液减小积屑瘤,减小加工表面粗糙度。
2020/8/13
一、切削速度、进给量、修光刃和背吃刀量的影响 1、切削速度的影响
由图2-12知,在有切削液的条件下,切削速度对加工表面粗 糙度的影响很小。 图2-13说明,不同切削速度下均得到表面粗糙度极小的加工 表202面0/8—/13 镜面。
➢ 由图2-9所示,在背吃刀量<25μm时,积屑瘤的高度变 化不大,但在背吃刀量> 25μm后, h0值将随着背吃 刀量的增加而增加。
2020/8/13
二、积屑瘤对切削力和加工表面粗糙度的影响 1、对切削力的影响
积屑瘤高时切削力也大,积屑瘤小时切削力也小。 与普通切削规律正好相反。
2020/8/13
➢ 用于加工:陀螺仪、激光反射镜、天文望远镜的反射镜、 红外反射镜和红外透镜、雷达的波导管内腔、计算机磁盘、 激光打印机的多面棱镜、录像机的磁头、复印机的硒鼓、 菲尼尔透镜等。
➢ 精密切削也是金属切削的一种,当然也服从金属切削的普 遍规律。
➢ 金刚石刀具的精密加工技术主要应用于单件大型超精密零 件的切削加工和大量生产中的中小型超精密零件加工。
2020/8/13
总结:天然单晶金刚石刀具只能用在机床主轴转 动非常平稳的高精度车床上,否则由于振动金刚 石刀具将会很快产生刀刃微观崩刃。
2020/8/13
2020/8/13
图2-3:图a是刀刃磨损的正 常情况,图b是剧烈磨损情 况,可以看到磨损后成层状, 即刀具磨损为层状微小剥落。 图2-4:图中所示沿切削速 度方向出现磨损沟槽,由于 金刚石和铁、镍的化学和物 理亲和性而产生的腐蚀沟槽。 图2-5:金刚石切削时,若 有微小振动,就会产生刀刃 微小崩刃。
一、切削速度、进给量、修光刃和背吃刀量的影响 2、进给量的影响
在进给量f<5μm/r 时,均达到
Rmax<0.05μm的加工 表面粗糙度。
2020/8/13
一、切削速度、进给量、修光刃和背吃刀量的影响
3、修光刃的影响
修光刃长度常取0.05~ 0.20mm。 修光刃的长度过长,对 加工表面粗糙度影响不 大。 修光刃有直线和圆弧两 种,加工时要精确对 刀,使修光刃和进给方 向一致。圆弧刃半径一般 取2~5mm。
2020/8/13
一、切削速度、进给量、修光刃和背吃刀量的影响 4、背吃刀量的影响
在刀具刃口半径足够小时,超精密切削范围内,背吃 刀量变化对加工表面粗糙度影响很小。
背吃刀量减少,表面残留应力也减少,但超过某临界 值时,背吃刀量减少反而使加工表面残留应力增加。
2020/8/13
一、刃口锋锐度对加工表面粗糙度的影响
一、切削参数对积屑瘤生成的影响 1、切削速度的影响
2020/8/13
不管在多大的切削速度下都有积屑瘤生 成,切削速度不同,积屑瘤的高度也不 同。当切削速度较低时,积屑瘤高度较 高,当切削速度达到一定值时,积屑瘤 趋于稳定,高度变化不大。
2、进给量f和背吃刀量 p的影响
➢ 由图2-8可以看出在进给量很小时,积屑瘤的高度很大, 在f=5μm/r时,h0值最小,f值再增大时,h0值稍有增 加。
2020/8/13
2.2精密切削加工机理
➢ 切削速度向来是影响刀具耐用度最主要的因素,但 是切削速度的高低对金刚石刀具的磨损大小影响甚 微,刀具的耐用度极高。原因是:金刚石的硬度极 高,耐磨性好,热传导系数高,和有色金属间的摩 擦系数低,因此切削温度低,在加工有色金属时刀 具耐磨度甚高,可用很高的切削速度1000~ 2000m/min,而刀具的磨损甚小。
2020/8/13
精密加工的加工范畴
按加工精度划分,可将机械加工分为一般加工、精密加工、超 精密加工三个阶段。 精密加工:加工精度在0.1~1µm,加工表面粗糙度在Ra0.02~ 0.1µm之间的加工方法称为精密加工; 超精密加工:加工精度高于0.1µm,加工表面粗糙度小于 Ra0.01µm之间的加工方法称为超精密加工(微细加工、超微细 加工、光整加工、精整加工等 )。
2020/8/13
精密加工的关键技术
➢ 1.精密加工机床:主轴回转精度、工作台直线运动精度以 及刀具微量进给精度
➢ 2.金刚石刀具:金刚石晶面选择、刀具刃口锋利性(刀具 刃口圆弧半径)
➢ 3.精密切削机理:微量切削过程的特殊性 ➢ 4.稳定的加工环境:恒温、防振和空气净化 ➢ 5.误差补偿:根据规律设定补偿,反馈控制系统 ➢ 6.精密测量技术
第2章 精密切削加工
2.1概述 2.2精密切削加工的工艺规律和机理 2.3精密切削加工的机床及应用 2.4功率超声车削
2020/8/13
2.1概述
➢ 精密切削是使用精密的单晶天然金刚石刀具加工有色金属 和非金属,可以直接加工出超光滑的加工表面(粗糙度 Ra0.02~0.005µm,加工精度<0.01µm)。
刃口半径为0.6μm、0.3μm
刃口锋锐度对加工表面有一 定的影响,相同条件下(背 吃刀量、进给量),更锋锐 的刀具切出的表面粗糙度更 小;速度的影响不是很大。
2020/8/13
二、刀刃锋锐度对切削变形和切削力的影响
2020/8/13
锋锐车刀切削变形系数明显低于 较钝的车刀。 刀刃锋锐度不同,切削力明显不 同。刃口半径增大,切削力增大, 即切削变形大。背吃刀量很小时, 切削力显著增大。因为背吃刀量很 小时,刃口半径造成的附加切削变 形已占总切削变形的很大比例,刃 口的微小变化将使切削变形产生很 大的变化。所以在背吃刀量很小的 精切时,应采用刃口半径很小的锋
2020/8/13
1)积屑瘤前端R大约 2~3μm,实际切削 力由刃口半径R起 作用,切削力明显 增加 。
2)积屑瘤与切削层和 已加工表面间的摩 擦力增大,切削力 增大。
3)实际切削厚度超过 名义值,切削厚度 增力加 增加hD。-hDu,切削
二、积屑瘤对切削力和加工表面粗糙度的影响 2、对加工表面粗糙度的影响
积屑瘤高度大,表面粗糙度大,积屑瘤小表面粗糙度小。并 且可以看出,切削液减小积屑瘤,减小加工表面粗糙度。
2020/8/13
一、切削速度、进给量、修光刃和背吃刀量的影响 1、切削速度的影响
由图2-12知,在有切削液的条件下,切削速度对加工表面粗 糙度的影响很小。 图2-13说明,不同切削速度下均得到表面粗糙度极小的加工 表202面0/8—/13 镜面。
➢ 由图2-9所示,在背吃刀量<25μm时,积屑瘤的高度变 化不大,但在背吃刀量> 25μm后, h0值将随着背吃 刀量的增加而增加。
2020/8/13
二、积屑瘤对切削力和加工表面粗糙度的影响 1、对切削力的影响
积屑瘤高时切削力也大,积屑瘤小时切削力也小。 与普通切削规律正好相反。
2020/8/13
➢ 用于加工:陀螺仪、激光反射镜、天文望远镜的反射镜、 红外反射镜和红外透镜、雷达的波导管内腔、计算机磁盘、 激光打印机的多面棱镜、录像机的磁头、复印机的硒鼓、 菲尼尔透镜等。
➢ 精密切削也是金属切削的一种,当然也服从金属切削的普 遍规律。
➢ 金刚石刀具的精密加工技术主要应用于单件大型超精密零 件的切削加工和大量生产中的中小型超精密零件加工。