物流管理外文翻译
物流管理外文资料翻译

Logistics is referred to the article flow, but not including the flow of the people.Daskin defined logistics as ……the design and operation of physical, managerial and informational systems needed to overcome time and space.‟The concept of article in logistics includes tangible goods and intangible service, such as customer service, freight agents and logistics network design.Three major functions of logistics(1) Creating time value: same goods can be valued different at different times. Goods often stop during the transfer process, which is professionally called the storage of logistics. It creates the time value for goods.(2) Creating location value: same goods can be valued differently at different locations. The value added during the transfer process is the location value of logistics.(3) Distribution processing value: sometimes logistics create distribution processing value, which changes the length, thickness and packages of the goods. Like popular saying, “ cutting into smaller parts” is the m ost commonly seen distribution processing within logistics create added value for goods.After completing a commercial transaction, logistics will execute the transfer of goods from the supplier( seller) to the customer( buyer) in the most cost-effective manner. This is the definition of logistics. During the transfer process, hardware such as logistics facilities and equipment( logistics carriers) are needed, as well as information control and standardization. In addition, supports from the government and logistics association should be in place.Logistics is a new commercial area, developing from the traditional stage to a modern one.Logistics is changing at a rapid and acceleration rate. There are two reasons are its rapid growth: Firstly, pressure to change by the development of the system itself(1) High–speed computing and data transmission can instantly transmit and react to user demand(2) More flexible and accurate logistic planning and control through computers and data processing(3) Flexible computer facilities help problem solving and increase decisions accuracy(4) Awareness of total cost measurement and management accountingSecondly, pressures for changes from the wider economy.(1) Be flexible in handling markets of different sizes for better competition(2) There is increasing specialization in markets and growth in retailing.(3) Life cycles for products are shortening. Logistics systems need to be more efficient, faster and more flexible(4) Move from mass production towards flexible manufacturing system( FMS). These systems enable a company to switch production quickly from one product to another(5) Competitive pressures lead to more efforts to improve customer service.Information technologies are most important for modern logistics. Bar Code, POS, EDI and GPS systems dramatically improve the efficiency and accuracy of the logistics activities. Internet further assists the market development, operation and management of the logistics industry.The 21st century is the era of information ,and e-commerce will become a development trend of commercial activity in this period . Our country , as a developing chuntry , is just at theearly-stage in the e-business field .The e-business has wide development space and huge market potential . Logistics delivery in E-Business can not only reduce industrial storage, accelerate funds revolvling, increase logistics efficiency, decrease logistics cost, but also it can stimulate social demand. It is propitious to whole social macroscopical control and it can gain whole social economical benefits, hasten the development of E-Business in depth.But under the rapid development there are also some problems exsit ,including the Internet technology, online payment, policies and regulations, logistics and so on .and logistics is a 'bottleneck' problem that immediately restricted the development of the e-business in our country .In the logistics information system, EDI plays the most important role.The revolution of information started with the introduction of the personal computer, followed by the optical fiber network, the explosion of the Internet and the World Wide Web. Internet assists market development, operational planning and management decisions in the logistics industry. Electronic commerce (EC) is the tool to be used to make deal between the seller and buyer by Internet in a paperless environment.Electronic Data Interchange (EDI) refer to a computer-to-computer information sharing of business documents in a standard format. EDI is widely applied in the field of commerce with the legal effect. Virtual logistics is based on logistics network, but more computerized and systematized than logistics operation. Logistics information system can be made up by three parts: inputs by terminal, data managed by CPU, the outputs managed by optical fiber. Virtual warehousing is not real logistics network but an information network based on warehouse management. Intranet is the internal network within an organization that promotes sharing of internal company related information, using similar technology as the InternetB2C is the Internet commerce designed for direct communications and commercial relationship between a firm and its end customer.With the development of network and electronic technology, logistics distribution has become the bottleneck of the E-commerce increasingly.The logistics distribution have important functions in B2C E-commerce, there are three existing loistics distribution models ,and the advantages and dissadcantages of the three models.In the circumstance of fixed sell quantity,if the scale of the logistics distribution gets larger, the cost will be lower.The need for outsourcing creates Third Party Logistics. Third Party Logistics refers to specialized logistics service providers that provide specific services for suppliers and customers.Third Part Logistics provides all the logistics services. They act as a bridge or facilitator between the first part( supplier or producer) and the second part( buyer or customer). The primary objectives of third part logistics providers are to lower the total cost of logistics for the supplier and improve the service level to the customer.Third Part Logistics have been growing rapidly. Cost reduction and demands for batter and cheaper services are the main drives behind the growth. A third part logistics provider will be in a position to consolidate business from several companies and offer frequent pick–ups and deliveries, whereas in–house transportation cannot. Other reasons are as follows:The company does not specialize in logistics;The company does not have sufficient resources;Eager to implement better logistics operation or does not have time to develop the requiredcapabilities in–house;The company is venturing into a new business with totally different logistics requirements; Merger or acquisition may make outsourcing logistics operations more attractive than to integrate logistics operations.Costs for logistics are similar to all other businesses and include fixed cost, variable cost and management cost.Transport does not need to change packages of goods or stop in any place between the departure point and destination location.Transportation creates location value in logistics. Transportation is usually the biggest logistic costs for most companies.The primary factor to influence transport cost is distance and competition.There are three kinds of freight in transport: full-car load, Less-than-truck load and Container. Transportation using multiple transportation means is also called combined transport. Grouping small shipment into large ones is the primary method to lower cost per unit of weight in transportation.Factors Influencing Transportation CostsAs transportation cost can be significant, the firm must identify and control the factors that affect these costs. In general, factors influencing transportation costs can be grouped into two major categories–product related factors and market–related factors.Factors to influence the cost of transportation can be grouped into the categories: (1) transport distances; (2) transport linkages; (3) transport equipment, and (4) transport time.Important market–related factors also affect transportation costs. The most significant ones include: (1) competition from different carriers; (2) location of markets; (3) government regulation of transportation carriers; (4) freight traffic in a region; (5) seasonality of product movements; and (6) whether the product is being transported domestically or internationally. Each of these factors will affect the overall transportation costs.Logistics system includes customer service, packaging, transportation, storage, distribution processing and information control. A standarized logistic system ensures better time management, location choices and distribution capacities.Distribution is one of functions in logistics, which deliver goods to customers directly according to the order in the most economic way. Distribution includes logistics activities related to the sales and delivery of goods. Distribution capacity is value added in the logistic system. Distribution center is a large and highly automated multi-store building destined to receive goods from various suppliers, take orders, fill them in container efficiently, deliver goods to the customer as quickly and satisfyingly as possible.Distribution center is a short-term storage center located close to a major market to facilitate the rapid processing of orders and shipment of goods to customers. The national distribution center is linked to the metropolitan‟s outer expressway, providing easy access to and from key ports, roads and other distribution channels for importers. The regional distribution center provides customized solution for supply chain management, warehousing and sea, air freight transport in theinternational logistics market. The distribution centers focus on maximizing the profit impact of fulfilling customer delivery requirement and distribution processing.Storage is a process in which goods are stored, protected and managed. Every manufacturer and wholesaler need inventory.Goods that are stored in warehouses for distribution and sales are called inventory. Warehouse rental represent a very significant proportion of total warehouse cost. Goods handling may account for only 50% of the direct labor cost in warehouse and 70% in distribution center.The size of warehouses are determined by the needs of the customer groups, such as their inventory level planning.Cycle stock is the maximum inventory based on the maximum needs. Safe stock refers to minimum inventory level given the forecasted market demand. The average time when the goods is moved in and out of warehouse is inventory cycle time. Inventory control is the method to keep the best inventory level and position with the minimum cost to satisfy the demand. When the inventory is reduced to a specific level, purchase for new parts and material will start. It is called the Order Point System. Zero stock is the best way for inventory control. Zero stock is means zero inventory.物流是指物品流动,不包括人的流动。
物流专业外文翻译--仓储管理
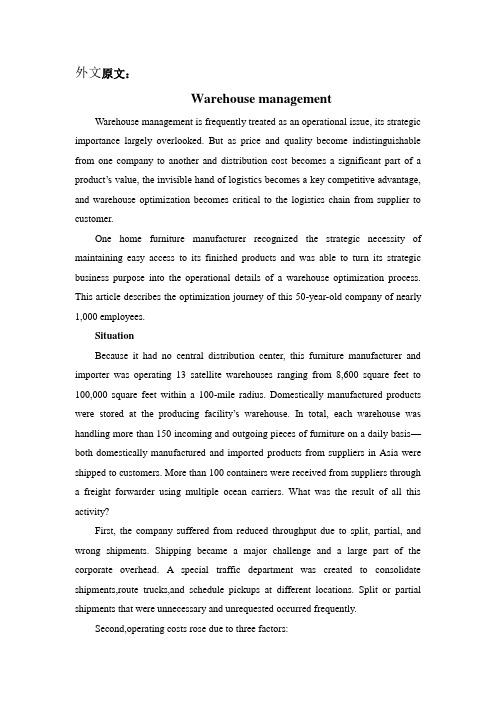
外文原文:Warehouse managementWarehouse management is frequently treated as an operational issue, its strategic importance largely overlooked. But as price and quality become indistinguishable from one company to another and distribution cost becomes a significant part of a product’s value, the invisible hand of logistics becomes a key competitive advantage, and warehouse optimization becomes critical to the logistics chain from supplier to customer.One home furniture manufacturer recognized the strategic necessity of maintaining easy access to its finished products and was able to turn its strategic business purpose into the operational details of a warehouse optimization process. This article describes the optimization journey of this 50-year-old company of nearly 1,000 employees.SituationBecause it had no central distribution center, this furniture manufacturer and importer was operating 13 satellite warehouses ranging from 8,600 square feet to 100,000 square feet within a 100-mile radius. Domestically manufactured products were stored at the producing facility’s warehouse. In total, each warehouse was handling more than 150 incoming and outgoing pieces of furniture on a daily basis—both domestically manufactured and imported products from suppliers in Asia were shipped to customers. More than 100 containers were received from suppliers through a freight forwarder using multiple ocean carriers. What was the result of all this activity?First, the company suffered from reduced throughput due to split, partial, and wrong shipments. Shipping became a major challenge and a large part of the corporate overhead. A special traffic department was created to consolidate shipments,route trucks,and schedule pickups at different locations. Split or partial shipments that were unnecessary and unrequested occurred frequently.Second,operating costs rose due to three factors:• Handling damage. Unnecessary product moves were creating major damages, which were having a significant impact on the company’s financial situat ion. Customer returns and allowances had reached 10 percent of net sales. A large number of pieces were put on hold and could not be shipped due to internally inflicted damage, delaying customer order fulfillment and increasing repair costs.• Exception c harges. Demurrage and per diem charges were a major financial hit to the company. Demurrage charges were incurred due to lack of space in warehouse facilities. Entire shipments were voluntarily held at port to avoid an overflow situation, not only increasing operating expenses but also delaying customer response time. Per diem charges (incurred when a container is not unloaded in a timely manner and held at the facility) were common due to the lack of a scheduling system for incoming containers.• Ineffici ent product flow. Direct labor cost was becoming a major part of the company’s cost structure. Excess handling, along with not being able to make good use of economies of scale, were driving inefficiencies up.These poor warehouse management practices resulted in excess operating costs. The lack of an adequate inventory method and the relatively short product life cycles created an obsolescence problem.Another problem was insufficient inventory turns due to the absence of first-in, first-out principles. Typically, pieces were received and warehoused in no orderly fashion, which did not allow the space required for a FIFO system and causes new and old products to be mixed. The jumble of products was generating color mismatches that were attributed to different supplier cuttings or even sourcing changes. The lack of an adequate information system worsened the situation because there was no way to track inventory location inside and outside each warehouse. Employees had to keep track of product locations manually or mentally, often creating duplicate locations and excess handling.ApproachThe warehouse optimization design was based on the principles of agility, lean manufacturing, and the theory of constraints. The goal was to be an agile company bybeing responsive to the customer. The material flows and storage concepts were designed to streamline flow and maximize throughput.In a time when every furniture company is importing from the same suppliers, there is little room to be creative and differentiate a company’s product because cost and quality end up the same. Cost and service become key aspects in the differentiation effort. Typically, consolidating and optimizing a warehouse can help both factors, which are translated into the following objectives:• Maximize throughput by providing agile response to customer orders because they do not have to be consolidated from different warehouses.• Minimize operating costs and be better than the industry benchmark by streamlining material handling in the warehouse, reducing handling damage by eliminating unnecessary shipping steps, decreasing exception charges, and reducing rent expense by consolidating warehouses.• Maximize inventory turns through FIFO inventory practices to reveal inventory problems to management quickly. Because products, their characteristics, and the global supply chain are rapidly changing in the furniture industry, today’s solution will not necessarily fit tomorrow’s needs. New product introduction or changing demand patterns could throw a perfectly optimized warehouse off balance. The company wanted to implement a solution that could support changing business conditions.Operational stepsThere are two major phases of warehouse optimization: planning and implementation. A project that involves and affects so many people requires an extraordinary effort to bring people on board at the start. Without the buy-in and cooperation of employees, this project would not have been successful, even with a flawless analysis and implementation. Steps taken are represented in Figure 1.PLANNINGFigure 1. The two major phases of warehouse optimizationPlanning phase. Cross-functional teams representing each affected unit wereformed to ensure project success and feasibility. The teams crossed organizational and functional boundaries, including personnel from safety,warehousing, information technology,finance,traffic, and senior management, which made the project a popular companywide effort.Data collection was an important piece that would help determine factors such as space requirements, products rate of sale, and inventory levels. Because of the seasonality of certain product lines, it was important to determine which periods were representative to use as a sample.The next step was to assign the product groups priorities and proximity to the shipping and receiving docks . An analysis of customers’ shipments helped the team establish a shipping pattern, which was typically a particular bedroom or dining group. Considering incoming product from the suppliers in Asia revealed the same conclusion— incoming and outgoing products move in sets (bed, nightstand, dresser, armoire, and mirror together) as opposed to individual pieces. It would not make sense to store the nightstand far from the dresser and bed of the same set. Therefore, a priority rating based on rate of sale for each collection as a whole was established. For cases in which the product weight was extreme, the rate of sale rule was overridden and the product was placed closer to shipping and receiving docks.The next phase of the optimizing process involved analyzing the warehouse capacity and managing the available space. Based on the space requirements and space available, the strategy for storing and managing inventory would vary. The requirements fell into three main categories: space required for peak inventory season, space required for temporary overflow situations, and space required for implementing the FIFO system.The amount of inventory required during peak periods for every product, not just at the collection level, was established. Allocating space for overflow situations required understanding the product’s inventory level fluctuation. Based on its variance, each product was assigned an extra percentage —ranging from 3 percent to 15 percent—of the total inventory required for peak season. The selected execution method for implementing a FIFO system was to allow extra space for product rotation.Product was to be pulled for customer shipments from one end and stored from supplier shipments at the other end. This required the product to be rotated within its assigned space. To facilitate the product rotation, an extra 5 percent (based on the space required for peak inventory) was allowed.With the help of the warehouse manager, stacking rules for each product category were determined, which would later become a guideline for how many of each product could be stacked without incurring damage. The main criteria for the stacking rules were product weight and height.When space is scarce, there are other techniques that could be applied to reduce space requirements at the expense of some handling. Combining product groups by their seasonality is one of them. If, for example, a particular category’s seasonality is offset from another by a given period of time, it would be wise to put each category next to each other and reduce the overall space required to handle peak season.Scenarios and trade-off analyses were developed after priorities were established and space allocated. A warehouse draft layout was created to visualize the results of the analysis and develop the alternate scenarios. This draft included all relevant product information (rate of sale, physical parameters, stacking rules, etc.) for understanding and handling ease. The warehouse manager and staff brought qualitative information to the decision-making process. An alternate scenario was developed to optimize the solution even further. Based on current business projections and anticipated product mix changes, the team increased the long-run potential savings.Implementation phase. A complete layout —including product positioning, space breakdown (baseline, FIFO, and overflow space), and quality control and staging areas —was developed and shared with the people involved. Safety and environmental personnel were asked to help develop escape routes and any other protection measures.The next part of the implementation phase was to develop operating procedures with the customer in mind. The three main issues addressed were training, exception charges, and pickups by appointment. Employees were trained on how to care for theproduct.Implementation took place in phases. Based on incoming container schedules, incoming product was mainly stored at the new location, while shipments took place out of the satellite warehouses. Within two months, most satellite warehouses were closed, and all the shipping and receiving operations were moved to the new 800,000-square-foot warehouse.ResultsWithin three months, the company began seeing benefits. The results over the two years since the implementation. The total warehouse space was reduced by 28 percent, which directly affected the amount of rent paid. In fact, the rent savings were around 36 percent.Operations-related exception charges were decreased. The new warehouse had enough capacity to sustain the peak inventory situation that would have previously caused product overflow and, therefore, demurrage charges. The newly implemented pick-up appointment system eliminated per diem charges.Labor efficiency improvements were achieved by eliminating unnecessary steps while handling the product in receiving and shipping. Excess internal transfers of product for consolidation also played a mayor role in reducing operating expenses.The implemented FIFO inventory practices brought to light existing inventory problems. Line-of-sight visibility allowed management to be aware of the problem and quickly devise a solution, which helped avoid obsolescence and improve inventory turns.Among other reasons, reduced material handling was responsible for decreased customer complaints and chargebacks. Handling-related returns and allowances were reduced significantly, creating a major boost in company profits.ConclusionThere is a systematic process that can be used to optimize warehouses to create a lean, agile organization. It is important first to identify all elements required for success, like this furniture company did. No matter what the space constraints are or which methodology is used, the strategic value to the company must be identified andthe right people must be involved if the project is to be successful.There are four key factors to a successful implementation of any project, regardless of the methodology, approach, or assumptions used:• Business purpose. Always start with the strategic business goal in mind. The company needed a long-term plan to compete in the global market. Warehousing is an unavoidable activity incurred by organizations. It is becoming a way to differentiate products and services from competitors.• Involve key personnel. Moving into a new workplace and operating under new procedures is not easy for employees. To make the transition easier and to get full support at all levels of the organization, involve key personnel from the start. Such action breaks existing boundaries and generates a sense of ownership, which will help during the implementation process as well as future success.• Design with the customer in mind. Consolidating produ cts under one roof, implementing a FIFO technique for inventory management, and establishing an appointmentdriven pick-up system are not just approaches to reduce operating costs. The intangible benefits of becoming more customer-friendly (which are key in a world driven by inter-mediaries) are tough to measure, but in the long run, they surely surpass the benefits of reducing operating expenses.• Develop flexible, qualitative, and experience-driven models. The model developed was not created simply from data. Involving experience-driven people added a qualitative element that cannot be captured by pure data in an analysis.Source:Justus Klemperer,Sekar Sundararajan,and Emory Zimmers Jr.2003.“careful with that warehouse” Industrial Engineer.September.pp.40-45中文译文:仓储管理仓储管理常常被认为是一种在战略上的重要性在很大程度上被管理者所忽略的操作问题。
交通运输与物流专业中英文对照外文翻译文献

(文档含英文原文和中文翻译)中英文翻译税收和运输外部性摘要综述的运输外部控制税收的作用(资料评论到税收的作用在于控制交通运输的运营状况)。
它认为,运输税的设计应预先考虑到现有的税收扭曲经济的影响(设计运输税时应该考虑到现有税收对经济的负面影响),在决策者的处置运输手段的限制。
运输定价的公平考虑的相关性探讨。
引言对欧盟数据显示乘客驾驶汽车行驶的公里数,1999是1970的两点五倍,汽车驾驶占有的份额达到79%( 1970年74%)。
在美国汽车运输中,汽车运输比例甚至在总额行驶千米数占更高比例, (1998年是84%)。
在1999年,欧盟的75%货物运输(包括短程海运和航运) 是通过公路运输的。
而美国的30%是公路运输(欧洲委员会,2001)。
汽车和卡车的模式在各自的运输市场占据着大份额,这反应出出它们的特性,比如灵活性和舒适性。
然而,当家庭和企业决定是否需要进行一个旅行,什么时候进行,采取什么旅行模式和途径,他们只会把自己的成本和收益考虑进去。
与社会最优化相比,由此产生的交通需求太高。
它在集中在特殊时刻的日子,分享不同的模式时是次优的。
这是因为,总体上,每个额外的运输用户还会增加其他运输用户和社会成本。
在人们决策过程中,这些没有考虑进去的成本是外部成本。
这些交通运输主要的边际外部成本包括交通堵塞,交通意外,环境成本和路面损坏 (针对重型车辆)。
大多数这些外部性具有一个反馈效应的特性:外部本身的水平也会影响经济主体的行为。
最明显的例子是交通堵塞和交通事故。
时间的成本影响着客运和货运交通的需求。
同样的道理,事故的风险影响着运输需求,模式的选择、路线的选择和驾驶行为等等。
反馈效应影响也包括空气污染和噪音,因为这些将导致厌恶或减轻此行为。
政府可以利用一些工具来应对这些外因素。
总体来说,一个人可以区分定价、监管和基础设施政策。
最后一类非常广泛。
例如, 它不仅包括实体基础设施或虚拟基础设施膨胀的能力,但也包括空间规划。
现代物流管理(外文翻译)

译文出处:Source: Economic Geography, V ol. 81, No. 3 (Jul., 2005), pp. 283-303译文标题:地理的生产联系在爱尔兰和苏格兰的微机行业:物流的作用译文:摘要:20世纪70年代中期的经济危机,标志着从福特主义传统的产业组织模式,以一个基于时间竞争(TBC)的过渡。
它已经假定,TBC的上升将导致在地方和区域的生产联系的增加。
争论的一部分是,相关的搜索后勤效率和采用即时(JIT)原则会拉近买家与供应商之间的买卖距离。
在这篇文章中,我们测试这个想法的相关性,在爱尔兰和苏格兰的微机硬件业为例。
大部分的数据收集与附属公司的所有业务中的两个国家之一的全球微机组装期间的多次采访。
研究结果显示,而不是局部或区域采购,装配导入绝大多数来自爱尔兰和英国以外地区的物质投入,特别是来自远东,大多数组件的内部物流管道涉及库存,往往在当地中心仓库。
这种供给系统已被解释为伪JIT,最理想的进货物流,传统的福特主义原则组织系统。
我们认为,物流系统和供应联系的地理不应该这样解释。
入境库存,严格管理,导致适度的目标缓冲区水平和发货频率高。
即使在JIT供应,生产联系和物流系统的细节的地理配置一系列的背景条件和元件特性上保持高度依赖。
这项研究的结果表明,围绕跨国企业的子公司的垂直综合生产集群的战略不再适用于爱尔兰和苏格兰,至少不会在微机行业的背景下。
关键词:计算机行业,生产的联系,物流。
据一些资料表明,20世纪70年代中期,标志着从福特主义传统的产业组织模式过渡到基于时间竞争(TBC)(Schoenberger1997年秸秆1988;秸秆和豪特,1990)。
作为工业的典范,“老”的理想型,后福特主义是一个“装配线基于大规模生产标准化的商品(Asheim1992)的系统。
制作了大型垂直整合,往往跨国公司集中控制的地方。
机械化、追求内部规模经济,详细的任务分工,加强工作(阿明1994年)的基础上提高生产力。
物流配送外文文献及翻译
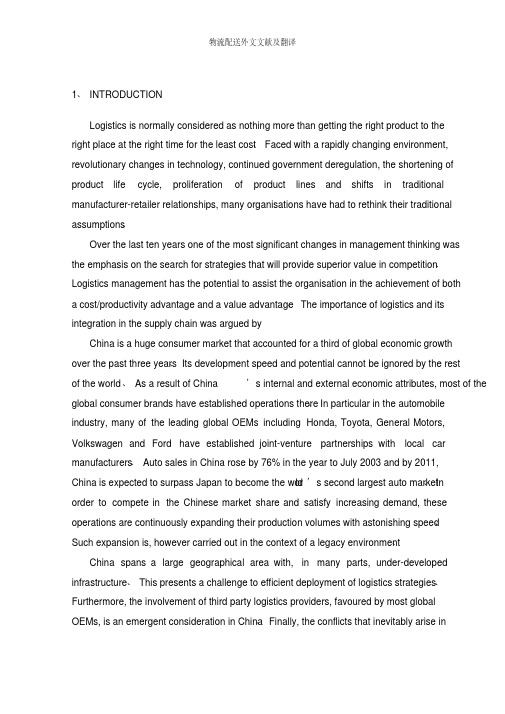
1、 INTRODUCTIONLogistics is normally considered as nothing more than getting the right product to theright place at the right time for the least cost、 Faced with a rapidly changing environment, revolutionary changes in technology, continued government deregulation, the shortening of product life cycle, proliferation of product lines and shifts in traditional manufacturer-retailer relationships, many organisations have had to rethink their traditional assumptions、Over the last ten years one of the most significant changes in management thinking wasthe emphasis on the search for strategies that will provide superior value in competition、Logistics management has the potential to assist the organisation in the achievement of botha cost/productivity advantage and a value advantage、 The importance of logistics and its integration in the supply chain was argued by、China is a huge consumer market that accounted for a third of global economic growthover the past three years、 Its development speed and potential cannot be ignored by the restof the world、 As a result of China’s internal and external economic attributes, most of the、 In particular in the automobileglobal consumer brands have established operations thereindustry, many of the leading global OEMs including Honda, Toyota, General Motors, Volkswagen and Ford have established joint-venture partnerships with local car manufacturers、 Auto sales in China rose by 76% in the year to July 2003 and by 2011,、 InChina is expected to surpass Japan to become the wor ld’s second largest auto marketorder to compete in the Chinese market share and satisfy increasing demand, these operations are continuously expanding their production volumes with astonishing speed、Such expansion is, however carried out in the context of a legacy environment、China spans a large geographical area with, in many parts, under-developed infrastructure、 This presents a challenge to efficient deployment of logistics strategies、Furthermore, the involvement of third party logistics providers, favoured by most globalOEMs, is an emergent consideration in China、 Finally, the conflicts that inevitably arise inthe joint venture partnerships lead to delays in the introduction of western logistics management e xperiences and methods from the OEMs、All these factors increase the、difficulties in managing logistics by China’s local auto makers2、 The overall development of foreign distribution Overview2、1 The United States of modern logistics developmentTwenty-first century from the 60s on wards, the rationalization of distribution of goodsin general are valued in the United States to take the following measures: First, the warehouse will replace the old distribution center: The second is the management of the introduction of computer networks, on the loading and unloading, handling, custody, standardized operation, improve operating efficiency; Third, the common chain distribution centers set up to promote the growth of chain-effective、 United States chain stores have a variety of distribution centers, mainly in the wholesale-based, r etail and warehouse-type three types、2、2 Japan's modern logistics developmentOn logistics and distribution of wood with the following features: well-developed distribution channels, frequent, low-volume stock, logistics and distribution reflects the common and set the trend sticks, logistics and distribution cooperative, the Government planning in the development of modern logistics and distribution play an important role inthe process of 、2、3 European modern development of logisticsCountries in Europe, especially Germany, logistics refers to the user's orders in accordance with the requirements of positions in the logistics sub-goods distribution, the goods will be sent to the consignee with good activities、Germany's logistics industry formed of basic commodities from origin to distribution center, from the distribution center (and sometimes through more than one distribution center) arrive at the modern mode of end customers、 Traveled in Germany, it can be said of the logistics and distribution in Germany has been formed to final demand-oriented to the modernization of transport and high-techinformation network as a bridge to a reasonable R69 distribution center hub to run a complete system、2、4 the main reasons of logistics industry developing faster in developed countriesRelying on high-tech to the core economies of scale to allow flexibility based on a variety of forms、3、China's 3PL enterprises are facing a major obstacle to business3、1 The current situation of China's 3PLChina's 3PL enterprises: service radius of a small, low entry barriers、 With the gradual warming heat logistics, urban logistics industry is also increasingly unitary covered by the importance and development、However, due to historical reasons in our country, the long-standing emphasis on production of a light flow, heavy flow to light the idea of the logistics, distribution of development in the not yet ripe at this stage, there is the issue more prominent in the following two aspects: the service delivery difficult to play a central role,the process of distribution of the low level of modernization、China's 3PL companies with foreign 3PL companies mainly in the gap between the three aspects: First, procurement capacity, and the other is logistics, and the third is cash flow、Aspects of logistics and distribution, foreign retailers have done very well, has a set of efficient logistics information system, which can effectively improve the inventory turnover rate, so as to enhance the return on assets and profitability、 And domestic retailers in this、area has just started, or have not yet started3、2 distribution center lower the overall distribution, commercial chain failed to give full play to the advantagesFrom our point of view the existing commercial retail enterprises, in addition to some large, well-known commercial enterprises, the general commercial "chain" businesses are not set up their own logistics and distribution centers or use third-party logistics center、Although these companies have also established some of his own "chain" stores, but in fact operating goods stores do not do "unified procurement, unified distribution, unified billing,"、 The which allows some commercial retail enterprises, "chain" seems to exist in name onlyother has been established in their own logistics and distribution centers or use third-party logistics distribution center of commodities in commercial enterprises, the effectiveness of distribution centers has not been effective, which in turn affected the procurement cost of an integrated chain advantages, including outstanding manifested by the distribution center for goods distribution ratio of unity is very low、 Uniform distribution logistics center can notbe achieved, indicating the store's commercial enterprises "unified purchase" did not、materialize, rather than a unified procurement chain has lost the core strengths3、3 China's more enterprises are facing a major obstacle of the higher logistics costWal-Mart 8 5% of the commodities distribution through the distribution center, in which 80% is through the "zero inventory" of the more complete form of the distribution database、Wal-Mart as a result of the use of the "Cross distribution" and "auto-replenishment" of supply chain technology, so that goods turnover in the Treasury down to 2 days、 And retail enterprises in China are in the 15-30 days, which reflects the retail , distribution enterprises, underdeveloped logistics system, distribution costs are too high、 Rapid expansion of retail enterprises in China's size and speed in the short term if they can not form a qualitative edge is a dangerous speculation、Over the years the practice has proved that the multi-purpose logistics distribution center, intensive, low-cost supply hub, as well as the use of information technology to reorganize and upgrade the entire flow of the supply chain management is the core of large-scale retail enterprises strategy is to support the retail giant super-conventional development、The face of large-scale retail and distribution businesses o f the main distribution center logistics requirements planning, focusing on how to reflect the integration of information flow in business flow, logistics, capital flow, so that the operation of retail enterprises to expand the logistics for the entire enterprise supply chain collaboration nodes and so that the whole positive and negative to minimize logistics cost of goods (including consumers, stores, logistics, distribution centers, headquarters, suppliers and partners), and a timely response t o sales demand and timely replenishment、This is also a large-scalecross-regional, multi-format, chain retail enterprises have the capacity of the core competitive advantage、3、4 Lack of modern logistics management knowledge and expertise of logistics personnel、This is the third-party logistics industry in restricting the development of China's most important one of the bottlenecks、Logistics knowledge, especially in modern integrated third party logistics knowledge is far from being universal, but that its main business areas is to provide transportation and warehousing services, not know that it is new to these traditional business integration of its business fields Far too simple to become connected with transport and storage of raw materials, semi-finished products supply, production process, material flow, the whole process of product distribution services, as cover flow, solid logistics, capital flow, information flow is equal to the integrated systemof systems、4 to enhance core competitiveness, the implementation of integrated management"integrated management" is the original English Integrated SupplyProcess, refers to the production enterprises, office, life of a non-core business areas of the operation and management of integration as a Overall, as a business-oriented t o manage outsourcing projects, by the special "integrated management" of the suppliers to provide full-service projects、"Integrated management" is not simply puts together the management of the business, but to improve management efficiency and reduce management costs as the core, combined with advanced information technology and network management features such as one organically integrated、Compared with the general outsourcing services, integrated management has the following characteristics:(1) It is not a business, but a complete outsourcing business from the operation of themanagement integration of outsourcing;(2) Outsourcing is not a core operation, but a comprehensive business management、Responsible for the entire business as a first-class suppliers, and its main task is to use its unique resources to conduct a comprehensive knowledge management, the operation of the specific is it managed by the secondary and tertiary suppliers to implement, so in themanagement of outsourcing functions based on the specific operation of the outsourcing; (3) In the case of the most important first-level suppliers, other than remuneration in thefixed service, its the only way to increase revenue for users to save costs as much as possible in order to share the proceeds of cost savings, rather than as general outsourcing as suppliers, mainly through an increase in turnover, that is, to increase spending to increase the user's own earnings、 "Double bottom" principle of cooperation between the two sides can make a stable and lasting、5 The third party logistics enterprise strategic choiceSummarized the latest of several foreign logistics theory and the development ofthird-party logistics with the current practice of foreign, third-party logistics firm's strategic choice to have the following three:(1)Lean Logistics StrategySince the lag theory and practice of logistics, our most extensive third-party logistics company or business, it can not accurately position their logistics services、 If you do not reverse this situation as soon as possible, will be third-party logistics industry in China have restricted role、 Lean production theory of logistics for our third-party logistics company provides a new development ideas for these enterprises to survive in the new economy and development opportunities、 Lean Logistics concept originated in lean manufacturing、 Itis produced from the Toyota Motor Corporation 70 years in the last century by the original "Toyota Production System", after research by the Massachusetts Institute of Technology professor and summary, was published in 1990 published "change the world of machines), a book、 Lean thinking is the use of various modern management methods and means, based on the needs of society to fully play the role of people as a fundamental and effective allocation and rational use of corporate resources to maximize economic benefits for enterprises to seek a new Management philosophy、 Lean Logistics Lean Thinking is the application in logistics management, logistics development must reflect、The so-called Lean Logistics means: the process by eliminating the production and supply of non-value added waste in order to reduce stocking time, improve customer satisfaction、 The aim ofLean Logistics according to customer needs, providing customers with logistics services, while pursuing the provision of logistics services in the process to minimize waste and delay, the process of increasing value added logistics services、Lean logistics system is characterized by its high-quality, low cost, continuous improvement, driven by customer demand oriented logistics system、 It requires establishing the customer first thought, on time, accurate and fast delivery of goods and information、In short, Lean Logistics, as a new management ideas, bound to have a third-party logistics enterprises in China have far-reaching impact, it will change the appearance of the extensive third party logistics management concept, the formation of third party logistics Core competitiveness、the establishment of small and medium third party logistics value chain allianceThird-party logistics enterprises of small and medium can not be independent because of their one-stop logistics services to provide full shortcomings, and because the small size of assets, services, not wide area so that small and medium enterprises in China's logistics third party logistics industry at a disadvantage、 Therefore, third party logistics for small and medium enterprises, starting from their own resources to construct their own core competence is the key、 As small and medium enterprise features of a single third-party logistics and incomplete, so based on their respective core competencies based on the structure of the logistics business enterprise cooperation is an effective capacity to make up for deficiencies, constitutes a feasible way of competitive advantage of logistics、 Value chain is the use of systems approach to investigate the interaction between business and the、 Value analysis of all activities and their access to the resources of competitive advantageof the business activities fall into two categories: basic activities and support activities、Basic activities are involved in product creation and sale of the material transferred to the buyer and after-sales service activities、 Basic activities of supporting activities is to assistthe revenue by providing outsourcing, technology, human resources and a variety of functions to support each other、 Theory to analyze the value chain study the value of third party logistics chain composition, can be found in auxiliary activities, third party logisticsenterprise and general business is no different, the basic activities in the third-party logistics companies has its own characteristics、 Third-party logistics enterprises there is generally no commodity production process, only the re-circulation process, d oes not account for major components of a wide range of third-party logistics companies and thus become the basic operating activities of storage, transport, packaging, distribution, customer service and marketing, etc、 link、 Various aspects of the basic work activities, due to their own limited resources and capacity, can not have every aspect of an advantage in that value chain in terms of some of the deficiencies, resulting in their overall logistics function not complete, lack of corresponding competitiveness and comparative advantage in some sectors of the value chain due to lack of overall effect should not play、 Therefore, third party logistics industry, small and medium sized logistics enterprises within the Union, should be based on the value chain between complementary on the basis of cooperation, make full use of professional logistics companies and logistics functions of specialized logistics organization and coordination of agents Flexible complementary integrated logistics capabilities、Third-party logistics for small and medium enterprises, value chain should start with the advantage of links to explore and develop the core competitiveness of enterprises, through the reconstruction of the value chain to avoid weaknesses、(2)Large third-party logistics enterprise virtualization of strategyRapid development in IT and the Internet era, companies can not fight alone singles, but must be in the competition and collaboration, in cooperation and development、Thus, under modern conditions resulting from modern large-scale virtualized development of third-party logistics has a strong necessity、Large third-party logistics enterprise virtualization is the logistics management resources of others who will have "all", through the network, the other part into its own logistics, with the help of others break the power of physical boundaries, extending to achieve their various Function, and thus expand their ability to enhance their strength、Therefore, the logistics information technology, virtualization is a means for the connection and coordination of temporary and dynamic alliance in the form of virtual logistics、 Integrated logistics virtualization technology as ameans of electronic communication, customer-focused, based on the opportunity to participate in members of the core competencies as a condition to an agreement for the common pursuit of goals and tasks, the different parts of the country's existing Resources to quickly mix into a no walls, beyond the space constraints, by means of electronic networks, contact the unified command of the virtual business entity, the fastest launch of high-quality, low-cost logistics service、Modern large-scale virtualization, including third-party logistics functions, organization, geographic three virtualization、Virtualization capabilities with third-party logistics enterprise IT technology will be distributed in different locations, different companies take different functions within the logistics resources (information, human, material and other resources) organized to accomplish a specific task, to achieve the optimization of social resources、 Virtualization refers to the organizational structure of the logistics organization is always dynamically adjusted, not fixed, but also decentralized, flexible, self-management, flat network structure, its objectives and in accordance with changes in the environmentre-combination, in a timely manner Reflect the market dynamics、 Virtual is the regional third party logistics network through the Internet link the global logistics resources, removing barriers and national barriers, to production management to achieve "virtual neighbors、 "1 导言物流通常被认为就是将恰当的产品以最低的成本,在恰当的时间送达恰当的地点。
现代物流管理(外文翻译)
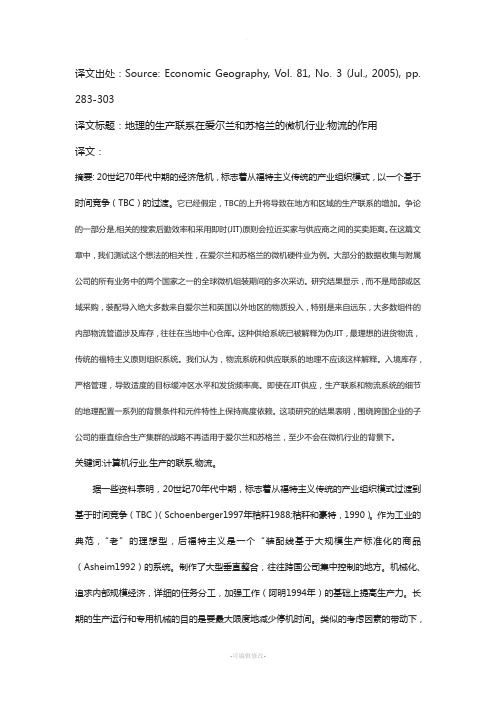
译文出处:Source: Economic Geography, Vol. 81, No. 3 (Jul., 2005), pp. 283-303译文标题:地理的生产联系在爱尔兰和苏格兰的微机行业:物流的作用译文:摘要: 20世纪70年代中期的经济危机,标志着从福特主义传统的产业组织模式,以一个基于时间竞争(TBC)的过渡。
它已经假定,TBC的上升将导致在地方和区域的生产联系的增加。
争论的一部分是,相关的搜索后勤效率和采用即时(JIT)原则会拉近买家与供应商之间的买卖距离。
在这篇文章中,我们测试这个想法的相关性,在爱尔兰和苏格兰的微机硬件业为例。
大部分的数据收集与附属公司的所有业务中的两个国家之一的全球微机组装期间的多次采访。
研究结果显示,而不是局部或区域采购,装配导入绝大多数来自爱尔兰和英国以外地区的物质投入,特别是来自远东,大多数组件的内部物流管道涉及库存,往往在当地中心仓库。
这种供给系统已被解释为伪JIT,最理想的进货物流,传统的福特主义原则组织系统。
我们认为,物流系统和供应联系的地理不应该这样解释。
入境库存,严格管理,导致适度的目标缓冲区水平和发货频率高。
即使在JIT供应,生产联系和物流系统的细节的地理配置一系列的背景条件和元件特性上保持高度依赖。
这项研究的结果表明,围绕跨国企业的子公司的垂直综合生产集群的战略不再适用于爱尔兰和苏格兰,至少不会在微机行业的背景下。
关键词:计算机行业,生产的联系,物流。
据一些资料表明,20世纪70年代中期,标志着从福特主义传统的产业组织模式过渡到基于时间竞争(TBC)(Schoenberger1997年秸秆1988;秸秆和豪特,1990)。
作为工业的典范,“老”的理想型,后福特主义是一个“装配线基于大规模生产标准化的商品(Asheim1992)的系统。
制作了大型垂直整合,往往跨国公司集中控制的地方。
机械化、追求内部规模经济,详细的任务分工,加强工作(阿明1994年)的基础上提高生产力。
物流专业外文翻译--物流配送的重要意义

物流专业外文翻译--物流配送的重要意义与专业有关的英文及译文The significance of logistics distributionModern distribution differs with common logistics, logistics is the product of the business and physical separation, and the distribution is, the unity of content, the distribution itself is more like a form of business, while the distribution in the concrete implementation, there are implemented in the form of business separation, but from the distribution trend of development, business flow and logistics more and more tightly integrated, distribution is the important guarantee of success. The significance of distribution can be analyzed from the following two aspects:(a) the Angle of economicsFrom the point of view of economics, resource allocation and distribution of final configuration of resources in the form of modern shipping economic activity. (1) distribution is part of the allocation of resources, because of the economic system is to distribute or a mechanism of resource allocation in distribution can be regarded as a form of economic system. (2) distribution in the resource allocation function of it is "" at the end of the configuration of resources, is close to the customer's configuration, and as close as possible to the customer is the enterprise management strategy is critical success factors, distribution is an important way of logistics, has very important strategic value for many enterprises, but the limitations make it can't solve all the problems in the field of logistics and distribution. (3) distribution of the main economic activity is delivery. Emphasizes the modern shipping, here shows difference with traditional delivery method, the distribution of major means of economic activity is the modern productive forces, the new labor as support, relying on science and technology, is a "match" and "send"a means of organic combination.(2) the distribution of the implementation of the wayFrom the perspective of the distribution way of implementation of logistics is in accordance with the requirements of customers orders, and in the distribution center or other logistics nodes equipped with goods, and sent to the users with the most reasonable way. (1) distribution is close to the user of the flow field during the process of resource allocation. Distribution is the essence of the delivery, but and general delivery is different: in general can be a random delivery, and distribution is a fixed form, there is a certain organization, channels, with modern technology to support, form a set of complete scientific management system, the distribution is a high level ofshipping method. (2) the distribution is a "transfer" form. Delivery from the logistics node to the user a special shipping method. Look from delivery function, its particularity is shown as: is full-time circulation enterprises engaged in shipping, not production enterprises; Distribution is a "transit" type of delivery, and general delivery especially to the user's delivery is often direct from the factory; Usually send what is the production, delivery and distribution is what companies need to send what. And to do what you need to send what, must be in transit link collection that need, and delivery must take the form of "transit". 3. Distribution is the combination of "match" and "send". Distribution and delivery, is the important difference between distribution by using effective sorting, distribution and so on tally work, make delivery reached a certain scale, in order to take advantage of scale achieved lower delivery cost. Without sorting, distribution, there is one shipment, need a send a, can greatly increase the consumption of manpower and material resources, cost less than pick up the goods delivery. So, want to reflect the advantage of distribution, sorting, distribution and so on a work is necessary. (4) distribution to users requirements as the starting point. Distribution from the user's interests, according to user requirements of an activity. Therefore, must be clear to set up "the user first", "quality first" concept. Distribution companies as a service provider, should from the user's interests first, on the basis of fully consider the interests of the users obtain the benefits of this enterprise. Distribution enterprises cannot use their own distribution channels to control to control the users of goods, cannot use distribution department division, industry division, cannot use distribution as department division, industry division, where the market approach.Logistics is along with the mass production and large circulation and appear a complete resource allocation and to meet consumer demand. Logistics due to realize the timing and quantitative, punctuality, planning, real-time, low cost, and even can realize zero inventory, customers that can completely replace the customer original supply system in the supply of the supply of higher quality and lower cost, realize the supply to the customer, to realize the integration of enterprise sales and customer supply.Second, the important role of logistics distributionLogistics is refers to the goods from supplier to recipient entity flow process. According to the actual need, transportation, storage, loading and unloading, handling, packaging, circulation processing, distribution, information processing and other basic functions. According to the concept of logistics and the definition of system,logistics system is to complete the goods entity flow from supplier to recipient and will transport, storage, loading and unloading handling, distribution processing, packaging and logistics information together, constitute the functional system of logistics system. The role of distribution performance in:(a) enterprises to adopt distribution systemDistribution system on which distribution, which can reduce logistics costs, improve service levels, in order to expand sales, expand the market, strengthen enterprise competition ability. (2) the product distribution system, distribution need how many, how much production, can realize products zero inventory, you can get the most economical and the biggest benefit. In (3) procurement and distribution system, can achieve how many enterprise, supplier delivery how much, when you need to, when suppliers on delivery. So companies don't need to set up raw material inventory, circulation enterprises don't need to set up inventory, can achieve zero inventory management, greatly reduce operating costs. 4. Zero inventory management, saved a large number of reserve funds, can improve enterprise's financial position, enhance the enterprise economic strength, promote enterprise development. (5) business in distribution system, leading to production system and distribution system as well as the procurement system corresponding revolutionary change, improve enterprise management level.(2) for the masses of users, to improve the logistics service level. Distribution to volume, variety complete, door-to-door delivery on time, on the one hand, the user on a business trip from purchasing transportation replenish onr's stock, such as labor, simplify the procedures, convenient for users, save the cost and improve the efficiency; On the other hand guarantee the supplies, and guarantee the normal production and circulation enterprises, can meet the needs of the people production and living supplies and services to enjoy.(3) distribution can improve the utilization rate of materials and inventory turns.Distribution in distribution center inventory, can use limited warehouse, make limited inventory might be used for a wider more customers, demand is bigger, the market is wide, will greatly improve the material utilization rate and inventory turnover ratio. Still can make warehousing and distribution译文物流配送的重要意义现代配送与普通物流的不同之处在于,物流是商、物分离的产物,而配送则是商物合一的产物,配送本身更像一种商业形式,虽然配送在具体实施时,也有以商物分离形式实现的,但从配送的发展趋势,商流与物流越来越紧密地结合,是配送成功的重要保障。
外文翻译--日本废旧家电的物流管理

本科毕业论文外文翻译外文题目:Material flows of end-of-life home appliances in Japan出处:Mater Cycles Waste Manag作者:Shinsuke Murakami · Atsushi Terazono · Naoya原文:Material flows of end-of-life home appliances in Japan Abstract .In Japan, the Law for the Recycling of Specified Kinds of Home Appliances came into effect in April 2001.This law aims to introduce appropriate waste treatment and promote the efficient use of resources so that we can achieve a sound material-cycle society. The law introduces a new framework for recycling that places obligations principally on the manufacturers and retailers of home appliances.Material flow analysis of this new framework is essential for evaluation of the system and for finding any problems that may exist.We th erefore analyzed the material flows in facilities that recycle electrical home appliances.The mass balances in the recycling facilities were appropriately estimated. Then the potential destinations were surveyed and analyzed, even though the legal framework does not include flows after the recycling facilities. The potential destination after the facilities varies and depends on both the economy and the related regulations. Currently, considerable amounts of recovered materials are exported and recycled. However, the sustainability of these trades is unknown.Therefore, we should keep a close eye on the situation and make sure that our recycling system is adaptable to meet any future changes.System for recycling of EOL home appliances The law for the recycling of specified kinds of home appliances.The law was enacted in June 1998 and came into effect in April 2001. The framework of the law was designed principally to place an obligation on manufacturers and retailers,whereas the recycling fee itself was to be paid by the consumer at the time of disposal. According to the framework,the consumer takes the EOL home appliance to the retailer and pays a recycling fee and a transfer fee.The retailer then takes the EOL home appliance to a designated collection site. Finally, the appliance is transferred to the recycling facility and recycled.Tasaki et al.1 analyzed the effectiveness of thislegislative system from four viewpoints: the achievement of material cycles, cost efficiency and monetary flows, the boundary within or outside the scope of the recycling system, and the behavioral changes of stakeholders. Their study proved the system to be certainly effective, especially in terms of recycling rates. However, they also pointed out that the system has some shortcomings. Manufacturers are obliged to fulfill the requirement of achieving the recycling rate, which is defined as the weight of the recovered materials divided by the weight of processed EOL appliances. Currently, air conditioners,TV sets (CRT only), refrigerators, and washing machines are within the scope of the recycling system,and the required recycling rates are 60%, 55%, 50%,and 50%, respectively. Refrigerant cholorofluorocarbons (CFCs) recovery from air conditioners and refrigerators is also required. Since April 2004, CFCs from insulation have also been required to be recovered. Recycling and transfer fees are decided by the manufacturers and retailers.Recycling facilities.In response to the establishment of the Home Appliances Recycling Law, manufacturers formed two groups –A group and B group –that shared common facilities to increase the efficiency of recycling, instead of having individual facilities.The reason why two groups were formed is not certain.Two reasons have commonly been propounded.The first is the policy of the Ministry of Economy,Trade and Industry (METI) to promote fair competition, as mentioned by Yoshida.2 As a general discussion about competition in the recycling market, the Fair Trade Commission of Japan issued guidelines in 2001.3 Another possible reason is a difference in philosophies, as was mentioned in the research report of the Economic and Industrial Research Department,Development Bank of Japan.4 A-group manufacturers tried to utilize the facilities of existing recycling industries and thus minimize their costs as much as possible,whereas B-group manufacturers tried to build new facilities specifically designed for home appliance recycling and to reduce the costs of the total recycling system by combining together for efficient supply chain management.These recycling facilities are basically independent business entities, even though they usually have financial relationships with manufacturers.According to METI, there were 44 home appliance recycling facilities operating in Japan at the beginning of FY 2005.The details of the processes vary amongfacilities. Previous studies such as those of the Development Bank of Japan4 or Matsuto et al.5 have classified facilities by manufacturer group, namely A group or B group. However, in light of the fact that the primary purpose of our study was material flow analysis, this categorization would not have been adequate if there had been differences in the outputs of different facilities in the same group. Therefore, we tried to classify these facilities by processes. By our interview surveys in 2003, we were able to classify all the facilities into three categories by the processes that they used.As mentioned, A-group manufacturers tried to utilize existing waste disposal businesses as much as possible.Most of these existing businesses had shredding machines.In this type of facility, EOL appliances are shredded after the required treatment, including manual dismantling, and are then intensively recovered from the shredded scraps.Therefore, the main material recovered from these A-group facilities is shredded metal scraps. We categorize these facilities as “sh redding first and then recovery” type (SR) facilities.There was also another type of existing facility, although the number of such facilities was small. According to our survey, five facilities belonging to the A group did not have shredding machines. In these facilities, EOL appliances are manually dismantled but never shredded. Hence, the outputs from these facilities are only unshredded parts and wastes. Considering the difference in output of this type of facility compared with that of the SR type, we needed to clearly distinguish this type among the A-group facilities. These facilities were therefore grouped as the“recovery without shredding” type (RwoS) facilities.Previous studies4,5 did not consider this last type of facilityindependently.In contrast, B-group manufacturers have built new facilities exclusively designed for EOL home appliance dismantling.SR facilities try to achieve higher recycling ratios by intensive separation after the shredding process, but these B-group facilities usually try to manually dismantle and recover the parts before shredding; we therefore called these “recovery first and then shredding” (RS) facilities.Mainly in response to market conditions, the differences between SR and RS facilities have narrowed but are still not negligible, especially when we consider the next stage of recycling. Details of the flows after materials leave the recycling facilities will be discussed inthe following sections.The processes used in all three types of facility are shown Fig.1,and all include the process of dismantling for recov-y of CFCs,since this is required.Table 1 summarizes the sults of our interview surveys of the outputs from all three pes of facility,clarifying the differences among the three pes in detail.The definition of valuable and nonvaluable ms had changed since our surveys were carried out in 2002.The definition was therefore adjusted with th e addi-tion of new information acquired in additional interviews.As can be seen from the table,there was little difference between the RwoS and RS processes.On the other hand,the SR process was not similar to either of the other two.SR facilities recover less than half the number of different types of parts compared with the other two types of facili-ties.However,this does not necessarily mean that this type of recycling recovers less overall:this can be evaluated only after we know the flows of the next sta ge of the recycling system.The yield ratio of the separation processes after crushing can also affect the evaluation and can change depending on the situation.According to our surveys,the recent high prices of scrap have led SR facilities to increase the yield ratio of their separation processes,even though this means an increase in processing costs.The manufacturers’ obligation is completed at the recycling facility stage,as mentioned in the previous section.However,unless the outputs from these facilities are com-pletely processed by the recycling industries,the materials or parts cannot be fully recovered.Therefore,we surveyed the material flows that occurred after the appliances had been through the facilities.The details are given in the section entitled material flows after leaving the recycling facility.Material balance in recycling facilities Number of appliances processed by each type of facility.As mentioned above,we performed interviews to deter-mine the processes used by each facility and then c lassified all the facilities into three types.At the same time,we esti-mated the number of appliances processed by each type of facility.The estimation methodology was basically inter-views and information disclosed on the manufacturers’ and recycling firms’ websites.Because we started our survey in 2003,the estimates given here are forFY 2002.The results are shown in Table 2.The RS facilities accounted for about two-thirds of the total number of appliances processed in the year.Consid-ering that RS facilities were newly built exclusively for home appliance recycling,it was not surprising that all RS facilities processed all four types of appliance.On the other hand,not all SR and RwoS facilities processed all four appliance types. RwoS facilities processed a limited number of appliances,and there were only five such facilities.There-fore,to determine the aggregated material flows in home appliance recycling,it was important for us to know the mass balances in the SR and RS facilities.Unit mass balances in r ecycling facilities.It is generally difficult to obtain mass balance information at recycling facilities because of the confidential nature of this information,and there have been very few previous studies:examples are those of Matsuto et al.5 and AEHA.6 Mat suto et al.performed a material flow analysis of home appliance recycling facilities and also weighed some of the parts at an RS facility.Although their weight data for parts are not as detailed as ours,they did estimate heavy metal balances.AEHA6 reported on a pilot home appliance re-cycling plant set up before the law came into effect.This report offers weight data on dismantled parts and scrap.Fortunately,we had access to the data from one recycling facility that allowed us to obtain its mass balances by weigh-ing.The facility’s process was categorized as RS type.Mass balance data were collected in November 2004,and 20 appliances of each of the four types were processed and weighed.Although we obtained most of the output weights for each part and material,we did not have access to the weights of some specific outputs,especially those of dust,because of trade secrets.Therefore,we estimated these inac-cessible weights through interviews and literature surveys.By combining the mass balances from this experiment and the estimated average weights of individual parts,we were able to estimate the mass balances of the other two types of facility.Therefore,acquired balances are for FY 2004.ConclusionWe have portrayed here a picture of the recycling of EOL home appliances.Wehave estimated the material balances in Japanese recycling facilities and have surveyed possible routes for after-facility material flows.We found that these facilities should be classified intothree types,rather than the two types often cited in previ-ous literature.The material balances of these three types of facility do not differ greatly;the principal difference is in the processes occurring after the materials leave the recycling facilities.The effectiveness of a recycling system in terms of phys-ical amounts should be analyzed on the basis of not only the processes used at the recycling facility but also the processes that occur after the material has left the facility.These latter processes often occur outside Japan,and it is often hard to ascertain the material balances of foreign processes.Our interviews revealed that the separation processes used in these importing countries are even better than those used in Japan,because they can utilize cheap labor.However,the sustainability of these trades is unknown,because there is much debate from two viewpoints:the appropriate treatment of hazardous contents,and natural resource policies in relation to scarcity.Therefore,we need to keep a close eye on the situation and make sure that our recycling system is able to adapt to meet any changes in these situations.译文:日本废旧家电的物流管理摘要:在日本,资源回收各种家用电器法律于2001年4月生效。
- 1、下载文档前请自行甄别文档内容的完整性,平台不提供额外的编辑、内容补充、找答案等附加服务。
- 2、"仅部分预览"的文档,不可在线预览部分如存在完整性等问题,可反馈申请退款(可完整预览的文档不适用该条件!)。
- 3、如文档侵犯您的权益,请联系客服反馈,我们会尽快为您处理(人工客服工作时间:9:00-18:30)。
随着社会的发展,行业竞争的日趋激烈,如何提高工作效率、降低管理成本、提高服务水平和企业的竞争能力,是每一个企业管理者最为关注的问题。
越来越多的管理者认为实行计算机科学化管理是解决这一问题的关键。
物流运输企业由于行业特点,传统操作过程复杂,文件繁多,竞争日趋激烈。
越来越多的信息问题涌现出来,例如:一方面,要不断开发客户市场,对客户的基本资料,货物分布情况、联系人的喜好及联系方式有较为全面的了解,另一方面,要作好财务的收付工作,确保运费能按时的收付,欠款一目了然,及时催缴。
以往查阅厚厚的文件资料的做法,显然是不可取的。
必须采取更有效的解决办法。
同时收集处理信息的速度、信息的准确性、安全性,还影响到公司整体的管理水平和决策层对整体业务的控制和协调。
采用计算机软件管理信息是解决上述问题的一个行之有效的办法。
物流管理软件,就是根据物流运输企业业务流程,将企业业务的各类数据联系起来,组成一个有机的系统,使得业务、财务、市场等方面的信息得以方便、快捷地传递,并经过综合处理生成各种报表送交给各个职能部门及决策层。
应用物流管理软件系统不仅可以节省大量的人力,减少工作中的失误,对客户的询问可以迅速的从电脑中查询信息答复客户,而且可以帮助决策者及时调整公司经营策略,提高公司在同行业中的知名度,增强公司的竞争力。
过去物流管理着重在企业内部作业与组织的整合,对下游顾客的对应,是以服务与品质为主要重心。
因此,评价物流的管理业绩和效果的准则,多半是以处理订单周期时间的速度,供货率及完成质量来量度。
随着物流业的发展,在供应链管理模式上增添新的内容,物流业出现了新的十大趋势。
(一)物流管理从物的处理,提升到物的加值方案设计、解决和管理上。
可以为客户提供度身订造式的,并带有个性化的服务,企业逐渐转向强调跨企业界限的整合,使得顾客关系的维护与管理变得越来越重要。
(二)由对立转向联合。
传统商业通道中,企业间多半以自我为中心,追求自我利益,因此往往造成企业间对立的局面。
然而在追求更大竞争力的驱动下,许多企业开始在各个商业流通机能上整合,通过联合规划与作业,形成高度整合的供应链通道关系,使通道整体成绩和效果大幅提升。
(三)由预测转向终测。
传统的流通模式通过预测下游通道的资源来进行各项物流作业活动,不幸的是预测很少会准确的,因而浪费了许多自然及商业资源。
新兴的物流管理趋势是强调通道成员的联合机制,成员间愿意互换营运及策略的信息,尤其是内部需求及生产的资料,使得上游的企业无需去预测,流通模式是逐渐由预测基础转向终测基础发展。
(四)由经验积累转向变迁策略。
一直以来经验曲线是企业用来分析市场竞争趋势及发展对应策略的方法,并以企业长年积累的经验作为主要竞争武器,然而科技的突飞进步,企业固守既有经验反而成为企业发展的障碍,因此在调度变化的环境下,经验及现存通道基础结构反变为最难克服的障碍,成功的企业要建立对策略方向的嗅觉和持续变迁管理体系才能生存。
(五)由绝对价值转向相对价值。
传统财务评价只看一些绝对数值,新的评估方法将着重在相对价值的创造,亦即在通道中提供加值服务,顾客所增加的价值中企业可占多少比例。
(六)由功能整合转向程序整合。
在竞争渠道日趋激烈的环境中,企业必须更快响应上、下游顾客的需要,因而必须有效整合各部门的营运,并以程序式的操作系统来动作,物流作业与活动多半具有跨功能,跨企业的特性,故程序式整合是物流管理成功的重点。
(七)由垂直整合转向虚拟整合。
在传统渠道中,一些大企业进行通道的垂直整合,以期对通过掌握有更大的力量,事实证明这并不成功,反而分散了企业的资源,并将主业削弱。
今日企业经营的趋势是专注核心业务,将非核心业务委托给专业管理公司去做,形成虚拟企业整合体系,使主体企业提供更好的产品及服务。
(八)由信息保留转向信息分享。
在供应链管理结构下,供应链内相关企业必须将供应链整合所需的信息与其他企业分享,否则,无法形成有效的供应链体系。
(九)由训练转向知识学习。
在可预见的未来,任何物流程序均以人力来完成。
然而,物流作业多半需要在各个物流据点和运输网络中进行,大约有90%的时间,物流主管无法亲自加以监控。
全球化的发展趋势,也增加了物流人力资源管理的复杂度。
物流主管必须将以个别人员技能训练的方式,转向知识基础的学习发展。
(十)由管理会计转向价值管理。
未来许多企业愿意投入许多资源建立基本会计系统,着重在提供增值创造,跨企业的管理信息,以期能确认可创造价值的作业,而非仅在于收益增加,成本升降上。
Along with society's development, the profession competition is day by day intense, how enhances the working efficiency, reduces the management cost, the enhancement service level and enterprise's competitive ability, is each enterprise superintendent most matter of concern. More and more many superintendents thought the implementation computer scientific style management solves this question key.The thing flows the transportation enterprise as a result of the profession characteristic, the tradition operating process complex, document many, thecompetition is day by day intense. The more and more many information question emerges, for example: On the one hand, must develop the customer market unceasingly, to the customer basic document, the cargo distribution situation, the contact person likes and the contact method has a more comprehensive understanding, on the other hand, must finish financial the receipts and disbursements work, guarantees the transport expense to be able on time receipts and disbursements, the debt to be clear, prompt press for payment. Formerly consulted the thick document material the procedure, obviously was cannot be taken. Must adopt more effective solution. At the same time collects the process information the speed, the information accuracy, the security, but also affects the company whole management level and the decision-making strata to the overall service control and the coordination. Uses the computer software management information is solution above question effective means.The thing class manages the software, is flows the transportation enterprise service flow according to the thing, according to relates the enterprise service various class numbers, composes an organic system, causes aspect the and so on service, finance, market information to be able to be convenient, to transmit quickly, and produces each kind of report form after synthesis processing to deliver for each function department and the decision-making strata. The appliance flows the management software system not only to be possible to save the massive manpower, reduces in the work the fault, may be rapid to the customer inquiry inquires the information answer customer from the computer, moreover may help the policy-maker promptly to adjust the company to manage the strategy, enhances company's in same profession well-knownness, the enhancement company's competitive power.In the past flowed the management emphatically in the enterprise interior work and organization's conformity, to the downriver customer's correspondence, was take serves and the quality as the main center of gravity. Therefore, the appraisal flows the management achievement and the effect criterion, is mostly by processes the order form period the speed, supplying goods rate and completes the quality to measure.Along with the thing flowing industry development, increased the new content in the supply chain management pattern, thing flowing industry had the new ten major tendencies.(1) thing flows the management from thing processing, promotes to in the thing Canadian value plan design, the solution and the management. May provides for the customer 度身订造-like, and has the personalization the service, the enterprise gradually changes emphasized the cross enterprise boundary theconformity, causes the maintenance and the management which the customer relates changes more and more importantly.(2) changes the union by the opposition. In the traditional commercial channel, the enterprise mostly take as the center, pursues the self- benefit, therefore often makes the aspect which the enterprise opposes. However in under the pursue bigger competitive power actuation, many enterprises starts in each commercial circulation function the conformity, through the union plan and the work, forms highly the conformity supply chain channel relations, causes the channel overall result and the effect large promotion.(3) changes the final survey by the forecast. The traditional circulation pattern carries on each thing through the forecast downriver channel resources to flow the work activity, unfortunately forecasts very little can accurate, thus has wasted many natures and the commercial resources. The emerging thing flows the management tendency is emphasized the channel member's union mechanism, between the member is willing to exchange transport business and the strategy information upstream, in particular internal demand and the production material, causes the enterprise not to need to forecast, the circulation pattern changes the final survey foundation development gradually by the forecast foundation.(4) accumulates by the experience changes the vicissitude strategy. The empirical curve has since always been the enterprise uses for to analyze the market competition tendency and the development correspondence strategy method, and the experience which accumulates by the enterprise elders takes the main competition weapon, however the science and technology flies suddenly the progress, the enterprise defends stubbornly already has the experience instead to become the barrier which the enterprise develops, therefore in under the dispatch change environment, the experience and the extant channel foundation structure instead becomes the barrier which most difficult to overcome, the success enterprise must establish to the strategy direction sense of smell and continues the vicissitude management system to be able to survive.(5) changes the relative value by the absolute value. The traditional finance appraisal will look only some absolute values, the new appraisal method emphatically in the relative value creation, that is will provide adds the value service in the channel, in the value which the customer will increase the enterprise may account for how many proportions.(6) changes the procedure conformity by the function conformity. In the competition channel intense environment, the enterprise must day by day in a quicker response, the downriver customer's need, thus must effective conformity various departments' transport business, and acts by the procedure -like operating system, the thing flows the work and the activity has the cross function mostly, cross enterprise's characteristic, therefore the procedure type conformity is the thing class manages the successful key point.(7) changes the hypothesized conformity by the vertical conformity. In the traditional channel, some big enterprises carry on the channel the vertical conformity, to through grasps by the time has a bigger strength, the fact proved this is not successful, instead dispersed enterprise's resources, and weakens the principal work. Today the enterprise manages the tendency is dedicated nucleus □0 □$.The service, makes the non- core business request for the specialized management company, forms the hypothesized enterprise conformity system, causes the main body enterprise to provide a better product and the service.(8) changes the information share by the information retention. Under the supply chain management structure, supplies in the chain to be connected the enterprise to have to supply the information which the chain conformity needs to share with other enterprises, otherwise, is unable to form the effective supply chain system.(9) changes the knowledge study by the training. In future which may foresee, any thing flows the procedure to complete by the manpower. However, the thing flows the work to need to flow the foothold and in mostly the transportation network in each thing carries on, probably some 90% time, the thing flows the manager to be unable to perform to monitor personally. Globalization development tendency, also increased the thing to flow the human resources management the order of complexity. The thing flows the manager to have by the individual personnel skill training way, changes the knowledge foundation the study development.(10) changes the value management by management accounting. Future many enterprises will be willing to invest many resources establishments basic accountant the system, in will provide the increment creation emphatically, the cross enterprise's management information, by the time will be able the true approval creation value work, but must only will lie in the income to increase, in cost fluctuation。