注塑制品的常见缺陷与对策分析
注塑缺陷描述及解决方案

注塑缺陷描述及解决方案一、缺陷描述注塑是一种常见的塑料加工方法,广泛应用于各个行业。
然而,在注塑过程中,常常会出现一些缺陷,影响产品的质量和性能。
下面将描述一些常见的注塑缺陷。
1. 气泡缺陷:气泡是注塑过程中常见的缺陷之一。
它们通常出现在塑料制品的表面或内部,给产品的外观和强度带来不利影响。
气泡的形成可能是由于塑料材料中含有挥发性成分,或者注塑过程中存在过高的温度或压力。
2. 热流痕缺陷:热流痕是由于注塑过程中塑料材料的流动受到阻碍而形成的。
它们通常呈线状或条状,并且会降低产品的外观质量。
热流痕的形成可能是由于模具设计不合理、注塑温度过高或注塑速度过快等原因。
3. 毛刺缺陷:毛刺是指产品表面出现的细小突起,给产品的触感和外观带来不良影响。
毛刺的形成可能是由于模具表面粗糙、注塑温度过高或注塑压力过大等原因。
4. 缩孔缺陷:缩孔是指塑料制品内部出现的空洞或凹陷,降低了产品的强度和密封性能。
缩孔的形成可能是由于注塑过程中塑料材料的收缩不均匀或注塑温度不合适。
5. 热胀冷缩缺陷:热胀冷缩是指注塑制品在冷却过程中由于温度变化而引起的尺寸变化。
如果注塑制品的尺寸与设计要求不符,就会影响产品的装配和使用。
热胀冷缩的控制需要合理设计模具和控制注塑工艺参数。
二、解决方案针对上述注塑缺陷,以下是一些常见的解决方案,以帮助改善产品质量和性能。
1. 气泡缺陷解决方案:- 选择低挥发性的塑料材料,减少挥发性成分的含量。
- 调整注塑过程中的温度和压力,避免过高的温度或压力导致气泡的形成。
- 使用真空抽气装置,帮助排除塑料材料中的气泡。
2. 热流痕缺陷解决方案:- 优化模具设计,确保塑料材料的流动畅通无阻。
- 降低注塑温度,避免过高的温度导致热流痕的形成。
- 控制注塑速度,避免过快的注塑速度导致热流痕的产生。
3. 毛刺缺陷解决方案:- 改善模具表面的光洁度,减少毛刺的形成。
- 调整注塑温度和压力,避免过高的温度或压力导致毛刺的产生。
注塑缺陷原因分析与解决方案

注塑缺陷原因分析与解决方案注塑是一种常见的塑料加工方法,广泛应用于各个行业。
然而,在注塑过程中,可能会出现各种缺陷,如气泡、翘曲、短射等问题,影响产品的质量和性能。
为了解决这些问题,我们需要进行缺陷原因分析,并提出相应的解决方案。
一、缺陷原因分析1. 气泡缺陷气泡是注塑过程中常见的缺陷之一。
其主要原因可能包括以下几个方面:- 塑料材料中含有挥发性物质,如水分、溶剂等,这些物质在高温下蒸发产生气泡。
- 注塑机温度设置不当,过高的温度会使塑料材料中的气体膨胀形成气泡。
- 注塑模具设计不合理,存在气孔或死角,导致塑料充填不均匀,形成气泡。
2. 翘曲缺陷翘曲是注塑产品常见的缺陷之一,其主要原因可能包括以下几个方面:- 注塑机温度不均匀,导致塑料材料在冷却过程中收缩不均匀,引起产品翘曲。
- 注塑模具设计不合理,存在过于薄弱的部位,无法承受注塑过程中的压力,导致产品变形。
- 注塑过程中冷却时间不足,使得产品在脱模后还未完全固化,导致变形。
3. 短射缺陷短射是指注塑产品未能充填满模具而产生的缺陷,其主要原因可能包括以下几个方面:- 注塑机温度设置不当,导致塑料材料粘度过高,无法充填满模具。
- 注塑模具设计不合理,存在过于狭窄的充填道或浇口,导致塑料流动受阻,无法充填满模具。
- 注塑过程中注射速度过快,导致塑料材料无法充填满模具。
二、解决方案1. 气泡缺陷的解决方案- 检查塑料材料的质量,确保其含水量和挥发性物质含量符合要求。
- 调整注塑机的温度,确保塑料材料在注塑过程中不会过热。
- 优化注塑模具的设计,避免气孔和死角的存在,确保塑料充填均匀。
2. 翘曲缺陷的解决方案- 调整注塑机的温度分布,确保塑料材料在冷却过程中收缩均匀。
- 优化注塑模具的设计,增加产品的结构强度,避免过于薄弱的部位。
- 增加注塑过程中的冷却时间,确保产品完全固化后再进行脱模。
3. 短射缺陷的解决方案- 调整注塑机的温度,降低塑料材料的粘度,促进充填。
注塑缺陷原因分析与解决方案
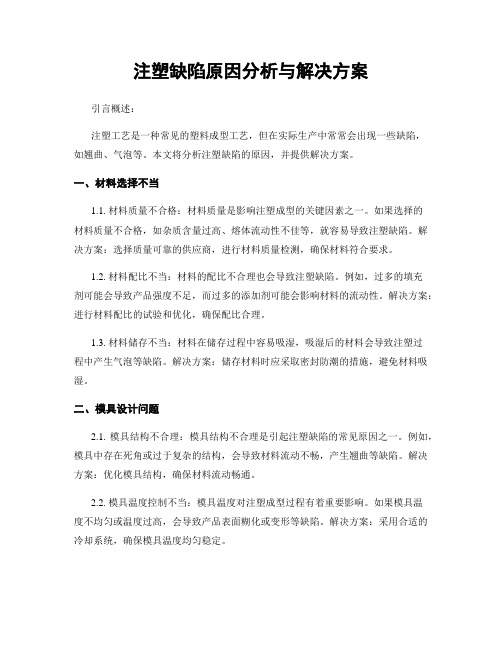
注塑缺陷原因分析与解决方案引言概述:注塑工艺是一种常见的塑料成型工艺,但在实际生产中常常会出现一些缺陷,如翘曲、气泡等。
本文将分析注塑缺陷的原因,并提供解决方案。
一、材料选择不当1.1. 材料质量不合格:材料质量是影响注塑成型的关键因素之一。
如果选择的材料质量不合格,如杂质含量过高、熔体流动性不佳等,就容易导致注塑缺陷。
解决方案:选择质量可靠的供应商,进行材料质量检测,确保材料符合要求。
1.2. 材料配比不当:材料的配比不合理也会导致注塑缺陷。
例如,过多的填充剂可能会导致产品强度不足,而过多的添加剂可能会影响材料的流动性。
解决方案:进行材料配比的试验和优化,确保配比合理。
1.3. 材料储存不当:材料在储存过程中容易吸湿,吸湿后的材料会导致注塑过程中产生气泡等缺陷。
解决方案:储存材料时应采取密封防潮的措施,避免材料吸湿。
二、模具设计问题2.1. 模具结构不合理:模具结构不合理是引起注塑缺陷的常见原因之一。
例如,模具中存在死角或过于复杂的结构,会导致材料流动不畅,产生翘曲等缺陷。
解决方案:优化模具结构,确保材料流动畅通。
2.2. 模具温度控制不当:模具温度对注塑成型过程有着重要影响。
如果模具温度不均匀或温度过高,会导致产品表面糊化或变形等缺陷。
解决方案:采用合适的冷却系统,确保模具温度均匀稳定。
2.3. 模具磨损严重:模具长时间使用后会出现磨损,磨损严重的模具会导致产品尺寸不准确或表面粗糙等缺陷。
解决方案:定期检查和维护模具,及时更换磨损严重的模具部件。
三、注塑工艺参数设置不当3.1. 注射压力过高或过低:注射压力是影响注塑成型的关键参数之一。
如果注射压力过高,会导致产品变形或开裂,而注射压力过低则会导致产品表面光洁度不高。
解决方案:根据产品要求和材料特性,合理设置注射压力。
3.2. 注射速度不合理:注射速度对产品的充填和冷却过程有着重要影响。
如果注射速度过快,会导致产品内部产生气泡或短射,而注射速度过慢则会导致产品表面瑕疵。
注塑制品缺陷的原因分析与解决措施

环境湿度变化大,影响塑料的稳定性和制品的外观。
空气污染
空气中存在灰尘、油雾等污染物,影响制品的外观和 质量。
03
注塑制品缺陷的解决措施
优化模具设计
模具设计合理化
确保模具设计符合产品要求,避免出现倒扣、 侧扣等设计不合理的地方。
避免模具损伤
提高模具的耐用性,避免使用过程中出现磨损 、断裂等问题。
优化浇口设计
合理设计浇口位置和大小,确保塑料能够均匀流入模具型腔。
把关原料质量
严格控制原料成分
确保原料中不含有杂质、异物等不良成分。
定期检测原料性能
对原料的性能进行定期检测,以确保其符合 生产要求。
加强原料存储管理
避免原料在存储过程中受潮、污染等问题。
调整工艺参数
合理调整注塑温度
根据塑料的性质和产品要求,合理调整注塑温度。
201 4
案例三:注塑制品出现银纹的原因及解决方法
原因分析
1. 塑料中含有水分或挥发性物质,导致银纹产 生。
2. 模具温度过低,导致塑料无法完全流动,出 现银纹。
案例三:注塑制品出现银纹的原因及解决方法
• 注射速度过快或压力过低,导致塑料在模具中流动不均匀,出现银纹。
案例三:注塑制品出现银纹的原因及解决方法
注塑制品缺陷的原因
分析与解决措施
汇报人:
日期:
• 注塑制品缺陷概述 • 注塑制品缺陷的原因分析 • 注塑制品缺陷的解决措施 • 注塑制品缺陷案例分析
目录
01
注塑制品缺陷概述
注塑制品常见缺陷
01 02 03 04
翘曲变形 缩痕 气泡 烧焦
注塑制品常见缺陷
01 02
溢边 裂纹
颜色差异
注塑缺陷原因分析与解决方案
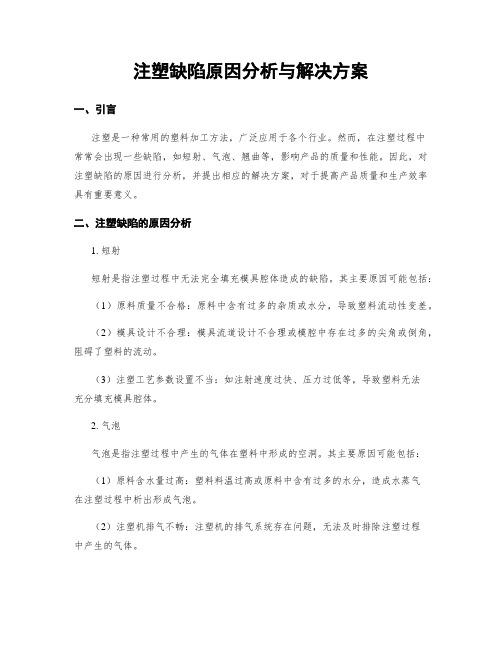
注塑缺陷原因分析与解决方案一、引言注塑是一种常用的塑料加工方法,广泛应用于各个行业。
然而,在注塑过程中常常会出现一些缺陷,如短射、气泡、翘曲等,影响产品的质量和性能。
因此,对注塑缺陷的原因进行分析,并提出相应的解决方案,对于提高产品质量和生产效率具有重要意义。
二、注塑缺陷的原因分析1. 短射短射是指注塑过程中无法完全填充模具腔体造成的缺陷。
其主要原因可能包括:(1)原料质量不合格:原料中含有过多的杂质或水分,导致塑料流动性变差。
(2)模具设计不合理:模具流道设计不合理或模腔中存在过多的尖角或倒角,阻碍了塑料的流动。
(3)注塑工艺参数设置不当:如注射速度过快、压力过低等,导致塑料无法充分填充模具腔体。
2. 气泡气泡是指注塑过程中产生的气体在塑料中形成的空洞。
其主要原因可能包括:(1)原料含水量过高:塑料料温过高或原料中含有过多的水分,造成水蒸气在注塑过程中析出形成气泡。
(2)注塑机排气不畅:注塑机的排气系统存在问题,无法及时排除注塑过程中产生的气体。
(3)注塑工艺参数设置不当:如注射速度过快、压力过高等,造成塑料内部气体无法顺利排出。
3. 翘曲翘曲是指注塑制品在冷却后出现变形的现象。
其主要原因可能包括:(1)模具温度不均匀:模具温度不均匀导致注塑制品冷却不均匀,从而引起翘曲。
(2)注塑过程中的应力积累:注塑过程中,塑料在注射后会受到冷却和收缩的影响,如果释放不及时,会导致应力积累引起翘曲。
(3)注塑工艺参数设置不当:如注射速度过快、冷却时间过短等,造成塑料冷却不充分,引起翘曲。
三、注塑缺陷的解决方案1. 短射的解决方案(1)优化原料质量:选择质量合格的原料,避免杂质和水分的存在。
(2)优化模具设计:合理设计模具流道,避免尖角和倒角的存在,保证塑料的顺畅流动。
(3)优化注塑工艺参数:合理设置注射速度和压力,确保塑料能够充分填充模具腔体。
2. 气泡的解决方案(1)控制原料含水量:确保塑料料温适宜,原料中的水分含量符合要求。
注塑成型缺陷及解决方法

注塑成型缺陷及解决方法注塑成型是一种常用的塑料制品生产工艺,但在实际操作过程中,难免会出现一些缺陷。
下面将介绍几种常见的注塑成型缺陷及其解决方法。
1.短射:短射指的是塑料在模腔中注入不完全,导致制品形状不完整或缺少一部分。
短射可能由于注射速度过快或进气不畅引起。
解决方法是调整注塑机的注射速度和压力,确保塑料充分进入模腔,并检查进气口是否畅通。
2.气泡:气泡是指制品表面或内部出现空洞。
气泡的形成可能由于塑料中含有水分、模具开放不当等原因。
解决方法是在注塑前将塑料干燥处理,确保塑料中不含水分,并检查模具密封性以防止气体进入模腔。
3.缩短:缩短是指制品尺寸比设计要小,可能由于塑料收缩不均匀或模具温度不稳定引起。
解决方法是通过调整模具温度和冷却系统,使塑料在注塑过程中均匀收缩,并确保模具温度稳定。
4.色差:色差是指制品表面颜色不均匀,可能由于塑料熔融不充分、颜料添加不均匀等原因。
解决方法是加长塑料的熔化时间,确保塑料充分熔融,并确保颜料充分混合均匀。
5.枝晶:枝晶是指制品表面出现树枝状的纹理,可能由于注塑温度过高或冷却时间不足引起。
解决方法是降低注塑温度,延长冷却时间,确保塑料在注塑过程中充分凝固。
6.毛刺:毛刺是指制品表面出现刺状的尖突物,可能由于模具间隙过大或模具磨损引起。
解决方法是调整模具间隙,确保模具紧密结合,并定期检查模具磨损情况。
7.烧焦:烧焦是指塑料在注塑过程中受热过度,产生发黑或炭化的现象。
烧焦可能由于注塑温度过高或注射速度过快引起。
解决方法是降低注塑温度,调整注射速度,确保塑料受热均匀。
总结起来,解决注塑成型缺陷的关键是调整注塑机参数、保证模具质量和稳定性,以及进行适当的后处理工艺。
此外,及时发现和修复模具的损坏也是避免缺陷的重要措施。
注塑缺陷描述及解决方案

注塑缺陷描述及解决方案注塑是一种常用的塑料加工方法,通过将熔化的塑料材料注入模具中,经过冷却固化后得到所需的塑料制品。
然而,在注塑过程中,可能会出现一些缺陷,影响产品的质量和性能。
本文将详细描述常见的注塑缺陷,并提供相应的解决方案。
一、缺陷描述1. 短射(Short Shot):指注塑过程中塑料未充满模具腔体,导致制品缺少某些部分或整体不完整。
解决方案:可能的原因包括模具温度过低、注塑速度过快、塑料材料不足等。
解决方法包括增加模具温度、调整注塑速度、增加塑料材料供给量等。
2. 翘曲(Warping):指注塑制品在冷却后产生变形,失去原本的平整形状。
解决方案:可能的原因包括模具温度不均匀、冷却时间不足、注塑压力过大等。
解决方法包括优化模具设计、增加冷却时间、减小注塑压力等。
3. 气泡(Air Traps):指注塑制品中出现气泡或空洞。
解决方案:可能的原因包括塑料材料中含有水分、注塑压力不稳定、模具排气不畅等。
解决方法包括使用干燥的塑料材料、调整注塑压力、改善模具排气系统等。
4. 热缩(Shrinkage):指注塑制品在冷却后出现尺寸缩小的现象。
解决方案:可能的原因包括模具温度过高、冷却时间不足、塑料材料收缩率不合理等。
解决方法包括降低模具温度、增加冷却时间、选择合适的塑料材料等。
5. 热裂纹(Hot Cracks):指注塑制品在冷却过程中出现裂纹。
解决方案:可能的原因包括注塑温度过高、冷却速度过快、塑料材料选择不当等。
解决方法包括降低注塑温度、控制冷却速度、选择合适的塑料材料等。
二、解决方案1. 优化模具设计:合理设计模具结构,确保充模充型均匀,避免短射、翘曲等缺陷的发生。
2. 控制注塑工艺参数:包括模具温度、注塑速度、注塑压力等。
通过调整这些参数,可以解决短射、翘曲、气泡等缺陷。
3. 选择合适的塑料材料:不同的塑料材料具有不同的性能和特点,选择合适的材料可以避免热缩、热裂纹等缺陷的发生。
4. 增加冷却时间:适当延长注塑制品的冷却时间,有助于避免翘曲、热缩等缺陷的产生。
注塑缺陷描述及解决方案

注塑缺陷描述及解决方案一、缺陷描述在注塑过程中,可能会浮现各种缺陷,这些缺陷会影响产品的质量和外观。
以下是常见的注塑缺陷描述:1. 气泡缺陷:在注塑制品表面或者内部浮现气泡,影响产品的美观度和强度。
2. 热胀冷缩缺陷:注塑制品在冷却过程中,由于热胀冷缩不均匀,导致产品尺寸不许确或者变形。
3. 短射缺陷:注塑模具中的塑料未能充满模腔,导致产品浮现不完整或者部份缺失。
4. 毛刺缺陷:注塑制品表面浮现细小的毛刺,影响产品的外观质量。
5. 沉痕缺陷:注塑制品表面浮现凹陷或者凸起的痕迹,影响产品的美观度。
6. 热裂缺陷:注塑制品在冷却过程中,由于塑料内部应力过大,导致浮现裂纹。
7. 毛躁缺陷:注塑制品表面浮现粗糙的纹理或者颗粒,影响产品的触感和外观。
二、解决方案针对以上注塑缺陷,可以采取以下解决方案:1. 控制注塑工艺参数:合理调整注塑机的注射速度、压力、温度等参数,确保塑料充满模腔,避免短射温和泡缺陷的发生。
2. 优化模具设计:对于容易浮现热胀冷缩缺陷的产品,可以通过优化模具结构和冷却系统设计,平衡热胀冷缩过程,减少尺寸偏差和变形。
3. 选择合适的塑料材料:根据产品的要求和使用环境,选择适合的塑料材料,以提高产品的强度和耐用性,减少热裂和毛刺缺陷的发生。
4. 加工后处理:对于浮现毛刺、沉痕和毛躁等缺陷的产品,可以采用打磨、抛光、喷涂等后处理方法,改善产品的外观质量。
5. 增加注塑模具的维护保养:定期清洁和保养注塑模具,确保模具表面光滑,减少缺陷的发生。
6. 引入质量控制措施:建立完善的质量控制体系,通过检测和测试,及时发现和解决注塑缺陷问题,确保产品质量符合要求。
总结:注塑缺陷的描述及解决方案是为了匡助生产企业更好地理解和解决注塑过程中可能浮现的问题。
通过合理调整工艺参数、优化模具设计、选择合适的材料、加工后处理和加强质量控制,可以有效地解决注塑缺陷问题,提高产品质量和客户满意度。
- 1、下载文档前请自行甄别文档内容的完整性,平台不提供额外的编辑、内容补充、找答案等附加服务。
- 2、"仅部分预览"的文档,不可在线预览部分如存在完整性等问题,可反馈申请退款(可完整预览的文档不适用该条件!)。
- 3、如文档侵犯您的权益,请联系客服反馈,我们会尽快为您处理(人工客服工作时间:9:00-18:30)。
1.气穴气穴指成型时模具型腔内的气体来不及排出, 被熔融的塑料包裹在型腔内。
在透明注塑件中可以很容易看到,但也可出现在不透明的塑料中。
成因主要包括:1)塑料未彻底干燥对策:充分干燥塑料2)预塑或注塑速度过快,气体来不及排出对策:降低注塑速度3)排气不良对策:加深排气槽深度,在填充末端与料流交汇处开设排气槽。
4)产品壁厚变化大对策:避免制品壁厚急剧变化或差异过大5)浇口位置不当,熔胶包抄气体对策:合理布置浇口位置2.毛边指熔融塑料在流入分型面或其它配件的配合间隙所形成的较薄的塑料薄面。
成因主要包括:1)流长太长,需高压才能填充模腔,模板有可能被高压撑开。
对策:改善流长2)锁模力不足或注射压力太大对策:加大锁模力或降低注射压力3)模具加工不当或装配不严实对策:检查模具加工活或装配情况4)排气不良或排气槽太深,熔胶溢出对策:检查排气5)树脂补给量过多对策:减少计量6)保压压力过高对策:合理调整保压7)料温或模温过高对策:降低料温或模温3.短射指塑料未能填满整个型腔而使成品出现不完整的情况。
成因主要包括:1)材料的流动不佳对策:选用流动性较好的材料2)残破的壁厚太薄,流阻大对策:增加产品壁厚3)料温和模温太低,熔胶过早的冷却对策:升高料温和模温4)流长过长或浇注系统尺寸不足对策:改善流长并加大浇口等尺寸5)浇口数目或位置不当对策:适当增加浇口的数目或优化浇口位置6)冷料井未设或设计不当对策:检查冷料井设计7)补料不足对策:加料8)排气不良对策:加排气9)注射压力或速度过低对策:增射压与射速10)注塑时间太短对策:适当延长射出时间11)注塑机塑化能力不足对策:更换有较大塑化能力的机器12)填充物过多,材料流动性降低对策:避免过多地添加填充物4.结合线结合线指的是两股料流交汇时形成的线条,它直接影响到产品的外观甚至机械性能。
成因主要包括:1)填充物添加太多,料流交汇处料流结合不良,结合线明显。
对策:减少填充物的填充量2)排气不良。
对策:加排气3)料温和模温太低,流动性不佳,料流结合处温度下降快,结合线明显。
对策:增加料温和模温以提高流动性4)射压或射速过低,料流接合不良。
对策:增加射压与射速5)浇注系统尺寸过小或进胶位置不当,流阻较大,料流结合处温度下降快,结合线明显。
对策:适当增加浇注尺寸,并优化进胶位置。
5. 喷流痕喷流痕指的是溶胶从浇口等受阻处进入较厚且宽阔的区域,形成的弯曲的流痕。
成因主要包括:1)产品壁厚断差过大。
对策:改善产品设计2)浇口位置不当,有自薄向厚流动或直接喷向较宽厚区域情形,导致料流不稳。
对策:优化进胶位置3)射压过大、射速过快。
对策:降低射压和射速4)浇口尺寸不当。
对策:调整浇口尺寸或改为冲击型浇口6. 冷流痕冷流痕指的是成型品表面出现的溶胶流动的痕迹。
成因主要包括:1)料温和模温太低,塑料流动性不好。
对策:调整料温和模温2)注塑速度过低。
对策:增加注塑速度3)保压压力不足。
对策:增加保压压力和时间4)塑料流动性差。
对策:更换材料5)模具冷却不良。
对策:改善冷却7. 缩痕缩痕指的是成型品表面的局部凹陷。
成因主要包括:1)射胶量不足。
对策:增加射胶量2)保压不足,不足以补偿塑料的收缩。
对策:加强保压3)产品结构不合理,加强肋过高、过厚。
对策:改善产品设计4)冷却效果不好,成型品脱模后继续收缩。
对策:平衡冷却系统以得到均匀冷却5)浇注系统不合理,浇口过小。
对策:优化浇注系统6)和加强肋相对的模面温度过高。
对策:调整模具温度7)料温太高或太低。
对策:调整料温8. 变形变形指的是成型品出现弯曲或扭曲,它影响产品的尺寸精度甚至产品的可装配性。
成因主要包括:1)成型品内部残留应力过多。
对策:改善成型条件以避免过多的残余应力2)过早顶出,产品过热。
对策:调整顶出时间3)冷却不均或公、母模温过大,产生热应力。
对策:平衡冷却,使公、母模温一致4)产品肉厚不均、产品结构不合理,加强肋集中于一面且相距较远。
对策:改善产品厚度和结构设计5)溶胶温度不一致。
对策:调整料温6)冲模速度过慢。
对策:提高射速9. 条纹条纹指的是产品表面沿溶胶流动方向形成的喷溅状条纹。
成因主要包括:1)料温过高,导致塑料裂解,出现裂解纹。
对策:降低料温2)烘料时温度过高或停留料管时间过长。
对策:降低烘料时温度及缩短停留时间3)射速过快。
对策:降低4)塑料干燥不足,含有水分,出现水纹。
对策:充分干燥5)浇注系统尺寸过小。
对策:加大尺寸6)排气不良,出现气纹。
对策:加排气7)螺杆转速太快,塑化时剪切率太大。
对策:降低转速1.4 关系曲线图本节将列举几组关于成型条件、产品厚度、流注系统尺寸与产品品质的关系曲线图。
1.4.1 浇口尺寸与收缩的关系曲线图1.1 表现的是浇口尺寸与产品收缩之间的关系。
随着浇口直径的增加,产品的收缩值就会随之变小。
足够的浇口尺寸是制件能够获得较好保压的保证。
当因浇口尺寸偏小而导致保压不足时,可以采用适当增加浇口尺寸的方法来增加保压效果。
浇口尺寸的大小不是决定保压压力大小的唯一因素,但它却会直接影响到成型时的保压效果,而保压效果的好坏又直接影响到产品的收缩情况。
浇口尺寸较小时,容易较早凝固而阻断保压压力传递,较大的浇口尺寸将会更有利于保压压力的传递从而改善产品收缩情况,但浇口尺寸的选择仍需视具体情况来定。
除浇口尺寸可以直接影响产品的收缩情况外,浇口位置同样也会影响到产品的收缩情况。
比如,当浇口位于产品壁厚较厚处时就比位于薄壁处时保压效果要好得多,因此收缩情况也会较后者要好。
1.4.2 保压压力与收缩的关系曲线图1-2表现的是保压压力与产品收缩之间的关系。
随着保压压力的增加,产品的收缩值会随之变小。
足够的保压压力是确保有效补偿收缩的前提条件,当产品收缩情况较严重时,采用提高保压压力的方法改善收缩情况也是很必要的方法之一。
保压压力的设置也应遵循适中的原则,保压压力不足时,会造成产品短射和收缩率大等问题,但保压压力设置过大时,也会产生保压问题,导致制品脱模时残留应力较大和成型周期延长。
1.4.3 保压时间与收缩的关系曲线图1-3 表现的是保压时间与产品收缩之间的关系。
随着保压时间的延长,产品收缩值会随之变小。
保压时间应持续至浇口凝固为止,如果保压时间过短,浇口还未凝固,则型腔内的溶胶会出现向浇口回流的情况,同时也会因得不到充足的保压而使产品出现较大的收缩。
在大多数情况下,采用延长保压时间的方法改善收缩情况也是很好的方法之一。
保压时间应该足够长,以确保得到充足的保压,当浇口凝固后,保压过程就无效果,保压过程应终止,以免影响整个成型周期。
1.4.4 保压压力与产品翘曲变形的关系曲线图1-4 表现的是保压压力与产品翘曲变形之间的关系。
随着保压压力的增加,产品翘曲变形情况会得到改善,但随着保压压力持续升高,产品的翘曲变形情况会越来越明显。
导致产品翘曲变形有3大主要原因:收缩不均匀、冷却不均匀和分子定向。
当保压压力增加时,收缩情况会得到明显改善,此时,如果产品翘曲变形的主要原因是收缩不均匀,则翘曲变形情况即会随保压压力的增加而得到改善。
但当保压压力过高时,就会导致产品内部残留应力过大,同时会出现过保压的情况,导致产品密度不一,收缩不一的情况发生,从而会加剧产品翘曲变形的程度。
1.4.5 模温与产品收缩的关系曲线图1-5 表现的是模温与产品收缩之间的关系。
随着模温的增加,产品收缩的程度会随之增大。
模温对塑件的收缩率、变形、尺寸稳定性、机械强度和表面质量等均有影响。
一般来说,适当地提高模温可以改善溶胶在型腔内的流动性、增加塑件的密度和结晶度、降低塑件表面粗糙度,以及减小冲模压力和塑件中的应力。
但模温过高时,成型收缩率大,脱模后塑件变形大,并且容易出现溢料、粘模等现象;模温过低时,模具型腔内溶胶流动性差,易导致塑件出现短射、机械强度降低。
表面无光泽等现象。
1.4.6 料温与产品收缩的关系曲线图1-6 表现的是料温与产品收缩之间的关系。
随着料温的增加,产品的收缩的程度会随之增大。
当料温过高时,所需冷却时间较长,从而会增加产品收缩的机会并会拖长成型周期,如曲线A。
实际上,料温过低时也可能会增加产品的收缩率,当料温较低时,不利于保压压力在型腔中传递而导致保压效果不佳,使产品出现收缩状况。
此时升高料温,反而能达到改善产品收缩的作用,如曲线B。
适当地提高料温,能够改善溶胶的流动性,使之更有利于填充和保压,但料温的设置不可高于材料的许可值,否则会使塑料降解,影响材料机械性能,同时也需要顾及料温与产品收缩之间的关系,并需注意成型周期等问题。
1.4.7 产品肉厚与产品收缩的关系曲线图1-7 表现的是产品肉厚与产品收缩之间的关系。
当产品肉厚增加时,产品收缩程度也随之增大。
对成型而言,产品肉厚过厚、过薄以及肉厚差异太大时对成型都是不利的,较厚的区域不易冷却,造成较大的收缩。
对于同一产品,当其肉厚分布不均匀时,往往会因厚区域较晚冷却、薄区域较先冷却而导致产品出现冷却不均的情况,这种情况极易引起产品翘曲变形的发生。
图1-7 表现的是产品肉厚与收缩的关系。
产品设计的好坏与成型品的质量是息息相关的,当因产品肉厚不合理而影响填充和保压等成型行为时,应建议更改产品的肉厚设计,如果不合理的肉厚是由于产品结构设计不合理所致,则应建议改善产品结构设计。
1.4.8 流道长度与型腔压力的曲线关系图1-8 表现的是流道长度与型腔压力之间的关系。
随着流道长度的增加,型腔压力逐渐降低。
一般而言,流道越长其压降也就越大,传递至型腔压力也就越小。
压降过大时,会影响填充的效果,易出现短射等成型缺陷。
当流道长度过长时,可以采用增加浇口数目或优化各支浇口进胶位置的方式避免。