注塑产品常见缺陷
注塑缺陷描述及解决方案

注塑缺陷描述及解决方案一、注塑缺陷描述注塑是一种常用的塑料加工方法,但在注塑过程中常会出现一些缺陷。
以下是常见的注塑缺陷描述:1. 气泡:注塑制品表面出现小气泡,影响外观质量。
2. 热缩:制品在注塑后出现尺寸变化,导致尺寸不准确。
3. 热分解:注塑过程中,塑料材料发生热分解,导致制品表面出现黑斑或发黄。
4. 热裂纹:注塑制品在冷却过程中出现裂纹。
5. 短射:注塑模具中未完全填充塑料材料,导致制品缺少部分或完全缺失。
6. 缩痕:注塑制品表面出现凹陷或凸起的痕迹。
7. 毛边:注塑制品边缘出现毛糙或不平整。
8. 色差:注塑制品颜色不均匀或与预期颜色不符。
二、解决方案针对以上注塑缺陷,可以采取以下解决方案:1. 气泡:增加注塑过程中的压力和温度,使用抗气泡添加剂,调整注塑工艺参数。
2. 热缩:优化注塑模具设计,增加冷却系统,控制注塑过程中的温度。
3. 热分解:选择合适的塑料材料,避免过高的注塑温度,加强模具通风。
4. 热裂纹:优化注塑模具设计,增加冷却时间,降低注塑温度。
5. 短射:调整注塑工艺参数,增加注塑压力和速度,优化模具结构。
6. 缩痕:增加注塑压力和温度,调整模具结构,增加冷却时间。
7. 毛边:优化模具设计,增加模具表面光洁度,调整注塑工艺参数。
8. 色差:选择合适的塑料材料,控制注塑温度和时间,使用色母粒。
除了以上解决方案,还可以通过对注塑设备进行维护保养,提高操作人员的技术水平,加强质量检验等措施来预防和解决注塑缺陷问题。
总结:注塑缺陷是在注塑加工过程中常见的问题,但通过合理的解决方案可以有效降低缺陷率,提高注塑制品的质量。
在实际生产中,需要根据具体情况选择合适的解决方案,并进行持续改进和优化,以确保注塑制品的质量和生产效率。
注塑常见缺陷和原因分析
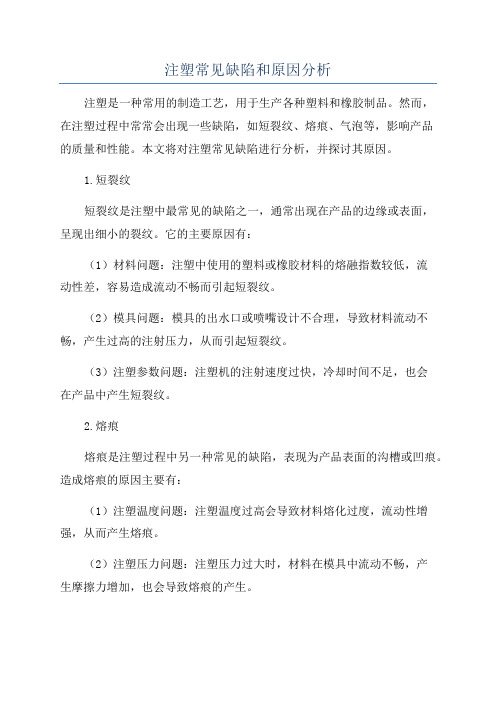
注塑常见缺陷和原因分析注塑是一种常用的制造工艺,用于生产各种塑料和橡胶制品。
然而,在注塑过程中常常会出现一些缺陷,如短裂纹、熔痕、气泡等,影响产品的质量和性能。
本文将对注塑常见缺陷进行分析,并探讨其原因。
1.短裂纹短裂纹是注塑中最常见的缺陷之一,通常出现在产品的边缘或表面,呈现出细小的裂纹。
它的主要原因有:(1)材料问题:注塑中使用的塑料或橡胶材料的熔融指数较低,流动性差,容易造成流动不畅而引起短裂纹。
(2)模具问题:模具的出水口或喷嘴设计不合理,导致材料流动不畅,产生过高的注射压力,从而引起短裂纹。
(3)注塑参数问题:注塑机的注射速度过快,冷却时间不足,也会在产品中产生短裂纹。
2.熔痕熔痕是注塑过程中另一种常见的缺陷,表现为产品表面的沟槽或凹痕。
造成熔痕的原因主要有:(1)注塑温度问题:注塑温度过高会导致材料熔化过度,流动性增强,从而产生熔痕。
(2)注塑压力问题:注塑压力过大时,材料在模具中流动不畅,产生摩擦力增加,也会导致熔痕的产生。
(3)模具设计问题:如果模具中的出水口或喷嘴设计不合理,也会在产品表面形成熔痕。
3.气泡气泡是注塑中常见的缺陷,表现为产品内部或表面的空腔。
气泡的形成原因有:(1)材料问题:注塑材料中含有过多的水分或挥发性物质,注塑过程中被加热蒸发,生成气泡。
(2)注塑温度过高:高温会导致材料熔化过度,容易产生气泡。
(3)注塑压力问题:过高的注塑压力会使材料在注塑过程中产生剧烈的振动,从而引起气泡。
(4)模具问题:模具中存在堵塞或不良的冷却系统,也会导致气泡的产生。
4.缩短问题缩短是指产品在冷却过程中出现尺寸缩小的现象。
产生缩短的主要原因有:(1)注塑温度过低:低温会使注塑材料的熔融程度不足,流动性降低,产生缩短。
(2)冷却时间不足:注塑材料冷却时间不足会导致产品未完全固化,容易产生缩短。
(3)注塑压力问题:过大的注塑压力会使产品产生内部的应力,引起尺寸缩小。
(4)模具问题:模具中存在过多的冷却系统,会导致材料过度冷却而使产品缩短。
注塑工艺与产品缺陷解决方案100例

注塑工艺与产品缺陷解决方案注塑工艺是一种常见的制造方法,用于生产各种塑料制品。
然而,在注塑过程中可能会出现一些产品缺陷。
以下是一些常见的注塑产品缺陷及其解决方案:1. 短射(Short Shot):指塑料注射不完整,导致产品部分或全部空洞。
解决方案包括:- 检查模具温度和压力,确保足够的塑料流动。
- 检查塑料熔融温度和压力,确保充分熔融。
- 检查模具设计,确保填充均匀。
2. 气泡(Air Traps):在产品内部形成气泡,影响外观和强度。
解决方案包括:- 调整注射速度和压力,以减少气体陷阱的形成。
- 优化模具通道和冷却系统,确保塑料充分流动并迅速冷却。
3. 热胀冷缩(Warping):产品在冷却后变形或扭曲。
解决方案包括:- 优化模具温度和冷却系统,确保均匀冷却。
- 调整注射速度和压力,避免内部应力积累。
- 使用合适的塑料材料,具有较低的热胀冷缩性能。
4. 流痕(Flow Marks):产品表面出现纹理或痕迹。
解决方案包括:- 调整注射速度和压力,确保塑料流动顺畅。
- 优化模具设计,减少填充阻力。
- 提高模具温度,增加塑料流动性。
5. 毛刺(Flash):产品边缘出现额外的塑料。
解决方案包括:- 检查模具关闭力,确保模具严密闭合。
- 检查模具设计,减少模具间隙。
- 控制注射速度和压力,避免过多的塑料溢出。
6. 熔接线(Weld Lines):由于塑料流动不畅导致的界面线。
解决方案包括:- 调整注射速度和压力,以减少熔接线形成。
- 优化模具设计,减少填充阻力。
- 提高模具温度,增加塑料流动性。
以上只是一些常见的注塑产品缺陷及其解决方案,具体解决方案还需要根据具体情况进行调整和优化。
为了确保产品质量,注塑过程中的工艺参数、模具设计以及塑料材料的选择都非常重要。
注塑件常见缺陷及原因

注塑件常见缺陷及原因注塑件常见缺陷包括飞边、欠注、翘曲、黑点、气泡、起皮、焦痕、龟裂、色差、脆化、喷流纹等。
这些缺陷的形成原因有很多,具体如下:1.飞边:模具分型面或成型区域的设计尺寸不当,注塑压力过高,注射时间过早,注射位置离口模过远,注射位置离型腔面过远或浇口过大。
2.欠注:注塑机压力过低,注射时间过短,模具温度过低,熔体温度过高,模具浇注系统有堵塞现象。
3.翘曲:模具设计不当,冷却时间过短或过长,注塑温度或模具温度过高或过低,塑料材料的收缩率过大。
4.黑点:塑料材料中含有杂质,螺杆转速过高,螺杆温度过高,塑料受热时间过长。
5.气泡:塑料材料中含有水分或挥发物,料温过高或过低,注射压力过小,流道和浇口的尺寸过大。
6.起皮:塑料材料中水分和挥发物含量高,料温过高或过低,注射压力过小,模具温度过高或过低。
7.焦痕:塑料材料中水分和挥发物含量高,料温过高或过低,注射压力过大或过小,模具排气不良。
8.龟裂:塑料材料中水分和挥发物含量高,料温过低,注射压力过小,模具温度过低。
9.色差:塑料材料中水分和挥发物含量高,料温过高或过低,注射压力过小或过大,模具温度过高或过低。
10.脆化:塑料材料中水分和挥发物含量高,料温过高或过低,注射压力过小或过大。
11.喷流纹:塑料材料中水分和挥发物含量高,料温过高或过低,注射压力过小或过大。
此外,注塑件缺陷的形成原因还可能包括设备原因、模具设计问题、原料问题等。
解决注塑件缺陷的方法包括调整操作条件、检查设备及模具设计、更换原料等。
如何避免注塑件常见的缺陷产生,可以从以下几个方面进行改进:材料准备:设定适当的干燥条件,避免过长的干燥时间和过高的干燥温度,以免塑料内挥发物被驱离。
同时,根据产品需求选择适当的塑料材料,如高强度和热稳定性良好的塑料。
模具设计:改善模具排气系统,特别是在流动路径的末端和盲孔位置。
确保排气孔大小合适,结晶性塑料和非结晶性塑料的排气孔大小应有所区别。
注塑缺陷原因分析与解决方案
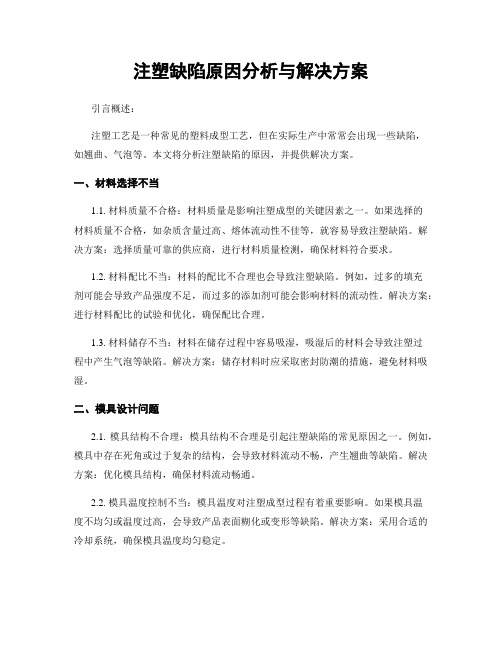
注塑缺陷原因分析与解决方案引言概述:注塑工艺是一种常见的塑料成型工艺,但在实际生产中常常会出现一些缺陷,如翘曲、气泡等。
本文将分析注塑缺陷的原因,并提供解决方案。
一、材料选择不当1.1. 材料质量不合格:材料质量是影响注塑成型的关键因素之一。
如果选择的材料质量不合格,如杂质含量过高、熔体流动性不佳等,就容易导致注塑缺陷。
解决方案:选择质量可靠的供应商,进行材料质量检测,确保材料符合要求。
1.2. 材料配比不当:材料的配比不合理也会导致注塑缺陷。
例如,过多的填充剂可能会导致产品强度不足,而过多的添加剂可能会影响材料的流动性。
解决方案:进行材料配比的试验和优化,确保配比合理。
1.3. 材料储存不当:材料在储存过程中容易吸湿,吸湿后的材料会导致注塑过程中产生气泡等缺陷。
解决方案:储存材料时应采取密封防潮的措施,避免材料吸湿。
二、模具设计问题2.1. 模具结构不合理:模具结构不合理是引起注塑缺陷的常见原因之一。
例如,模具中存在死角或过于复杂的结构,会导致材料流动不畅,产生翘曲等缺陷。
解决方案:优化模具结构,确保材料流动畅通。
2.2. 模具温度控制不当:模具温度对注塑成型过程有着重要影响。
如果模具温度不均匀或温度过高,会导致产品表面糊化或变形等缺陷。
解决方案:采用合适的冷却系统,确保模具温度均匀稳定。
2.3. 模具磨损严重:模具长时间使用后会出现磨损,磨损严重的模具会导致产品尺寸不准确或表面粗糙等缺陷。
解决方案:定期检查和维护模具,及时更换磨损严重的模具部件。
三、注塑工艺参数设置不当3.1. 注射压力过高或过低:注射压力是影响注塑成型的关键参数之一。
如果注射压力过高,会导致产品变形或开裂,而注射压力过低则会导致产品表面光洁度不高。
解决方案:根据产品要求和材料特性,合理设置注射压力。
3.2. 注射速度不合理:注射速度对产品的充填和冷却过程有着重要影响。
如果注射速度过快,会导致产品内部产生气泡或短射,而注射速度过慢则会导致产品表面瑕疵。
注塑成型缺陷及解决方法

注塑成型缺陷及解决方法注塑成型是一种常用的塑料制品生产工艺,但在实际操作过程中,难免会出现一些缺陷。
下面将介绍几种常见的注塑成型缺陷及其解决方法。
1.短射:短射指的是塑料在模腔中注入不完全,导致制品形状不完整或缺少一部分。
短射可能由于注射速度过快或进气不畅引起。
解决方法是调整注塑机的注射速度和压力,确保塑料充分进入模腔,并检查进气口是否畅通。
2.气泡:气泡是指制品表面或内部出现空洞。
气泡的形成可能由于塑料中含有水分、模具开放不当等原因。
解决方法是在注塑前将塑料干燥处理,确保塑料中不含水分,并检查模具密封性以防止气体进入模腔。
3.缩短:缩短是指制品尺寸比设计要小,可能由于塑料收缩不均匀或模具温度不稳定引起。
解决方法是通过调整模具温度和冷却系统,使塑料在注塑过程中均匀收缩,并确保模具温度稳定。
4.色差:色差是指制品表面颜色不均匀,可能由于塑料熔融不充分、颜料添加不均匀等原因。
解决方法是加长塑料的熔化时间,确保塑料充分熔融,并确保颜料充分混合均匀。
5.枝晶:枝晶是指制品表面出现树枝状的纹理,可能由于注塑温度过高或冷却时间不足引起。
解决方法是降低注塑温度,延长冷却时间,确保塑料在注塑过程中充分凝固。
6.毛刺:毛刺是指制品表面出现刺状的尖突物,可能由于模具间隙过大或模具磨损引起。
解决方法是调整模具间隙,确保模具紧密结合,并定期检查模具磨损情况。
7.烧焦:烧焦是指塑料在注塑过程中受热过度,产生发黑或炭化的现象。
烧焦可能由于注塑温度过高或注射速度过快引起。
解决方法是降低注塑温度,调整注射速度,确保塑料受热均匀。
总结起来,解决注塑成型缺陷的关键是调整注塑机参数、保证模具质量和稳定性,以及进行适当的后处理工艺。
此外,及时发现和修复模具的损坏也是避免缺陷的重要措施。
注塑缺陷及其解决方法
注塑缺陷及其解决方法注塑是一种常用的塑料加工方法,通过将加热熔融的塑料材料注入到模具中,冷却后形成所需的产品。
然而,在注塑过程中,往往会出现一些缺陷,影响产品的质量。
以下是一些常见的注塑缺陷及其解决方法。
1.气泡:气泡是注塑中最常见的缺陷之一、它们可能是由于塑料材料中的挥发性成分排放不完全,或者是熔融塑料中的气体在注射过程中迅速扩散而形成的。
解决气泡问题的方法包括:合理选择塑料材料、充分预干燥材料、提高注射速度和压力、优化模具结构等。
2.沉痕:沉痕是表面上的凹陷,通常是由于塑料材料的收缩不均匀或冷却不充分造成的。
解决沉痕问题的方法包括:调整注射温度和压力、改善模具冷却系统、增加冷却时间等。
3.翘曲:翘曲是注塑过程中产品变形的一种形式。
它可能是由于模具设计不合理、注射温度过高或产品冷却不充分引起的。
解决翘曲问题的方法包括:优化模具结构、调整注射温度和压力、增加冷却时间等。
4.热断裂:热断裂指的是在注塑加工过程中,产品的一些部位出现开裂或裂纹。
它可能是由于注射过程中产生的应力超过了材料的承受能力引起的。
解决热断裂问题的方法包括:调整注射速度和压力、改变注射顺序、增加降温时间等。
5.色差:注塑产品在颜色上出现不均匀或异色现象。
这可能是由于原料配比不准确或注射过程中的温度变化等原因造成的。
解决色差问题的方法包括:准确控制原料比例、稳定注射温度、使用色差控制剂等。
6.熔接线:熔接线是由于注塑模具的设计和操作问题导致两个或多个熔融塑料部分相互连接而形成的。
解决熔接线问题的方法包括:调整模具结构,避免部件交汇点过多,调整注射速度和压力等。
总之,注塑缺陷的解决方法主要包括调整材料配比、优化模具结构、控制注射温度和压力、增加冷却时间等。
同时,及时调整机器参数、进行模具维护和清洁,以保证注塑过程的稳定性和可靠性。
通过以上的措施,可以有效减少注塑缺陷,提高产品质量。
常见注塑产品缺陷及处理措施
现象
产生原因
处理措施
产品不足
填充不满
1、 注塑速度不足。2、塑料短缺。3、螺杆在行程结束处没留下螺杆垫料。4、运行时间变化。5、射料缸温度太低。6、注塑压力不足。7、射嘴部分被封。8、射嘴或射料缸外的加热器不能运作。9、注塑时间太短。10、塑料贴在料斗喉壁上。11、注塑机容量太小(即注射重量或塑化能力)。12、模温太低。13、没有清理干净模具的防锈油。14、止退环损坏,熔料有倒流现象。
注塑件尺寸差异
1、 输入射料缸内的塑料不均。2、射料缸温度或波动的范围太大。3、注塑机容量太小。4、注塑压力不稳定。5、螺杆复位不稳定。6、运作时间的变化、溶液黏度不一致。7、注射速度(流量控制)不稳定。8、使用了不适合模具的塑料品种。9、考虑模温、注射压力、速度、时间、和保压等对产品的影响。
1、 检查有无充足的冷却水流经料斗喉以保持正确的温度。2、检查是否劣质或松脱的热电偶。3、检查与温度控制器一起使用的热电偶是否属于正确类型。4、检查注塑机的注塑量和塑化能力,然后与实际注塑量和每小时的注塑料用量进行比较。5、检查是否每次运作都有稳定的熔融热料。6、检查回流防止阀有否泄露,若有需要就进行更换。7、检查是否错误的进料设定。8、保证螺杆在每次运作复回位置都是稳定的,即不多于0.4mm的变化。9、检查运作时间的不一致性。10、使用背压。11、检查液压系统运作是否正常,油温是否过高或过低(25-60℃)。12、选择适合模具的塑料品种(主要从缩率及机械强度考虑)。13、重新调整整个生产工艺。
1、 增加注塑速度。2、检查料斗内的塑料量。3、检查是否正确设定了注射行程,需要的话进行更改。4、检查止逆阀是否磨损或出现裂缝。5、检查运作是否稳定。6、增加熔胶温度。7、增加背压。8、增加注塑速度。9、检查射嘴孔有没有异物或未塑化塑料。1、增加螺杆向前时间。12、增加料斗喉区或降低射料缸后区温度。13、用较大的注塑机。14、适当升高模温。15、清理干净模具内的防锈剂。16、检查或更换止退环。
注塑产品常见缺陷
注塑产品常见缺陷注塑产品常见缺陷及其原因分析注塑产品在生产过程中可能会遇到各种缺陷,这些缺陷可能源于产品设计、模具制造、材料选择、注塑工艺等多个因素。
以下是一些常见的注塑产品缺陷及可能的原因分析:1.填充不足(缺料)这可能是由于注塑压力不足、注射时间过短、模具排气不良、浇口设计不合理等原因造成的。
解决这个问题的方法包括增加注塑压力、延长注射时间、优化模具排气设计、改进浇口位置等。
2.溢料(毛边)溢料通常是由于注射压力过高、浇口设计不当、模具磨损等原因造成的。
解决溢料问题的方法包括降低注塑压力、优化浇口设计、修复模具磨损等。
3.气泡(气孔)气泡可能是由于塑料在模具中未完全填满、气体未完全排出、注射速度过快等原因造成的。
解决气泡问题的方法包括降低注射速度、增加冷却时间、优化模具设计等。
4.变形变形可能是由于产品结构不合理、冷却不均匀、模具温度波动等原因造成的。
解决变形问题的方法包括优化产品结构设计、改善冷却条件、稳定模具温度等。
5.银纹(流纹)银纹可能是由于塑料流动不均匀、模具温度过低、注射速度过快等原因造成的。
解决银纹问题的方法包括优化注射条件、提高模具温度、降低注射速度等。
6.裂纹(龟裂)裂纹可能是由于产品结构设计不合理、材料韧性不足、注射压力过高等原因造成的。
解决裂纹问题的方法包括优化产品结构设计、更换韧性更好的材料、降低注射压力等。
7.翘曲(扭曲)翘曲可能是由于产品结构设计不合理、模具温度不均匀、注射压力过低等原因造成的。
解决翘曲问题的方法包括优化产品结构设计、改善冷却条件、提高注射压力等。
8.冷块(冷凝物)冷块可能是由于塑料在冷却过程中速度过快、模具温度过低等原因造成的。
解决冷块问题的方法包括降低冷却速度、提高模具温度等。
9.喷射痕迹(蛇形纹)喷射痕迹可能是由于注射速度过快、浇口设计不当等原因造成的。
解决喷射痕迹问题的方法包括降低注射速度、优化浇口设计等。
10.颜色分布不均(色差)颜色分布不均可能是由于材料混合不均匀、注塑条件不稳定等原因造成的。
注塑缺陷描述及解决方案
注塑缺陷描述及解决方案一、缺陷描述在注塑过程中,可能会浮现各种缺陷,这些缺陷会影响产品的质量和外观。
以下是常见的注塑缺陷描述:1. 气泡缺陷:在注塑制品表面或者内部浮现气泡,影响产品的美观度和强度。
2. 热胀冷缩缺陷:注塑制品在冷却过程中,由于热胀冷缩不均匀,导致产品尺寸不许确或者变形。
3. 短射缺陷:注塑模具中的塑料未能充满模腔,导致产品浮现不完整或者部份缺失。
4. 毛刺缺陷:注塑制品表面浮现细小的毛刺,影响产品的外观质量。
5. 沉痕缺陷:注塑制品表面浮现凹陷或者凸起的痕迹,影响产品的美观度。
6. 热裂缺陷:注塑制品在冷却过程中,由于塑料内部应力过大,导致浮现裂纹。
7. 毛躁缺陷:注塑制品表面浮现粗糙的纹理或者颗粒,影响产品的触感和外观。
二、解决方案针对以上注塑缺陷,可以采取以下解决方案:1. 控制注塑工艺参数:合理调整注塑机的注射速度、压力、温度等参数,确保塑料充满模腔,避免短射温和泡缺陷的发生。
2. 优化模具设计:对于容易浮现热胀冷缩缺陷的产品,可以通过优化模具结构和冷却系统设计,平衡热胀冷缩过程,减少尺寸偏差和变形。
3. 选择合适的塑料材料:根据产品的要求和使用环境,选择适合的塑料材料,以提高产品的强度和耐用性,减少热裂和毛刺缺陷的发生。
4. 加工后处理:对于浮现毛刺、沉痕和毛躁等缺陷的产品,可以采用打磨、抛光、喷涂等后处理方法,改善产品的外观质量。
5. 增加注塑模具的维护保养:定期清洁和保养注塑模具,确保模具表面光滑,减少缺陷的发生。
6. 引入质量控制措施:建立完善的质量控制体系,通过检测和测试,及时发现和解决注塑缺陷问题,确保产品质量符合要求。
总结:注塑缺陷的描述及解决方案是为了匡助生产企业更好地理解和解决注塑过程中可能浮现的问题。
通过合理调整工艺参数、优化模具设计、选择合适的材料、加工后处理和加强质量控制,可以有效地解决注塑缺陷问题,提高产品质量和客户满意度。
- 1、下载文档前请自行甄别文档内容的完整性,平台不提供额外的编辑、内容补充、找答案等附加服务。
- 2、"仅部分预览"的文档,不可在线预览部分如存在完整性等问题,可反馈申请退款(可完整预览的文档不适用该条件!)。
- 3、如文档侵犯您的权益,请联系客服反馈,我们会尽快为您处理(人工客服工作时间:9:00-18:30)。
制品缺陷
原因分析
应对措施
油污
(或水痕)
1.脱模剂使用过量,不均匀
2.模具局部漏油
3.操作工手上有油抹到产品上
4.放产品的地方有油
5.模具的冷却水道发生渗漏,冷却水渗入模腔形成水痕
1.少用脱模剂,且喷涂均匀
2.检修模具
3.洗手、带干净的手套
4.放产品的地方保持清洁
1.产品易划伤部位修边时要特别注意
2.车间安排新来的修边工进行培训
3.只修飞边不伤产品;必要时考虑修模
制品缺陷
ห้องสมุดไป่ตู้原因分析
应对措施
擦伤
1.产品取出时在模具或机器上擦伤
2.模具有毛刺,光洁度不好
3.产品周转过程中擦伤
4.放产品的地方太硬、太粗糙,平台上有杂物
5.包装不好,产品与包装袋或纸箱摩擦产生
6.装卸、运输过程导致擦伤
1.适当降低流速
2.修模具改浇口的位置
3.修模具改善排气系统
4.适当增长烘料时间,使原料充分烘干
熔接痕
1.浇口的位置和尺寸不对
2.模具排气不良
3.塑料件结构设计不合理,如果塑件厚度与长度不成比例、形状复杂、成型面很大,熔体易在塑件的薄壁部位入口处受阻;嵌件太多也易形成熔接痕
5.冷却时间太短,局部受力过大出现顶白
6.注射压力太大,保压压力太高,保压时间太长
7.材料原因
1.降低型腔表面粗糙度
2.将顶出装置置于壁厚处或提高顶出部位的强度
3.适当增加脱模斜度
4.降低熔体温度,减小熔体和模具间温差
5.适当延长冷却时间
6.适当降低注射压力,降低保压压力,缩短保压时间
7.调整材料配方
制品缺陷
原因分析
应对措施
缺料
1.注射压力太低,注射速度太慢
2.熔料温度过低
3.原料流动性太差
4.供料不足
5.模具排气不良
6.流道被杂质堵塞
7.浇口或流道截面积较小而长
1.适当加大注射压力,提高注射速度
2.提高熔料温度
3.换料
4.适当增加螺杆注射行程,增加供料量
5.修模,改善排气结构
6.疏通流道
7.修模,改善浇注系统
1.取出产品时注意产品表面不要擦伤
2.修模具使模具光洁
3.做好搬运、装配过程中的产品防护,轻拿轻放,切记勿拖、拉产品;
4.放产品的地方应柔软,保持工作平台清洁
5.改善包装
6.爱护产品,严禁高空抛扔产品,踩压产品
制品缺陷
原因分析
应对措施
排气疤
1.流量过快
2.浇口位置不当
3.模腔排气不畅通
4.原料没烘干
制品缺陷
原因分析
应对措施
收缩
1.原料不符合成型要求
2.塑件结构设计不合理,一般粗厚件易产生凹痕
3.成型条件控制不当
3.1收缩在浇口附近时
3.2收缩在壁厚处时
3.3收缩在嵌件周围时
3.4由于供料不足引起的
4.模具问题(收缩发生在远离浇口,一般由于模具结果中某一部分熔料流动不畅通)
1.对表面要求比较高的塑件,应采用低收缩率的原料
4.降低充填速度,特别是降低接近充填完成时的充填速度;降低注射压力和保压压力,可以减少所需的锁模力;避免使用太低的塑料温度,否则可能需要更高的注射压力。操作时针对具体情况采取相应措施
制品缺陷
原因分析
应对措施
杂料
1.料筒没清洗干净,一般在先打的几只产品有杂料现象
2.回料中混有杂质
1.彻底清洗料筒
2.粉碎前要先把杂质清除,粉碎后不能混装,加工时控制回料的使用量
8.堆放产品,纸箱压坏导致产品变形
1.适当降低注塑压力
2.适当降低熔体温度
3.适当降低保压压力
4.当增长保压时间
5.调整冷却系统使模温达到平衡
6.调整合适的脱模斜度,修模使模具光洁
7.正确装箱或改进包装
8.产品堆放不超过规定高度;改进包装
制品缺陷
原因分析
应对措施
飞边
1.合模力不足
2.料温太高
3.模具缺陷
4.工艺控制不当(注射速度太快、注射压力过大,时间过长,充模速率不均衡,加料量过多,润滑剂使用过量)
1.提高锁模力;在满足注射质量的前提下,还可以降低注射压力或降低注料口截面积,也可缩短保压及增压时间,减小射料杆行程,或考虑减少型腔数
2.适当降低料筒、喷嘴及模具温度
3.检查模具、尽量精密加工模具及研修模具,减小模具间隙
5.检修冷却水道,严防模腔渗漏
制品缺陷
原因分析
应对措施
断脚
1.断脚处有熔接痕易断裂
2.模具型芯断裂
3.从模具上取产品时掰断
4.装箱时碰断
1.按消除熔接的方法改进
2.修模
3.对易断裂的地方注意保护
4.装箱时注意保护该位置,避免产品受损
制品缺陷
原因分析
应对措施
划伤
1.修边时划伤
2.新修边工操作不熟练
3.修边过量
2.修改塑件的设计厚度,使得壁厚的变化小
3.适当提高注射压力及注射速度,增加熔料的压缩密度;延长注射和保压时间,补偿熔体的收缩,保压不能太高,否则会引起凸痕;增加注塑缓冲量
3.1可通过延长保压时间来解决
3.2可适当延长塑件在模的冷却时间
3.3可提高嵌件的温度
3.4应增加供料量
4.适当扩大模具浇注系统结构,对比较厚的塑料件,优先采用翼式结构
3.如各型腔的大小不一致必须注意浇口大小与塑件质量成正比
4.适当降低注射速度
5.降低熔体温度
6.干燥原料,筛除粉末料
7.控制回料加入量
8.设计时要注意避免塑料件厚薄悬殊过大
制品缺陷
原因分析
应对措施
顶白
1.型腔表面粗糙,使脱模阻力加大
2.顶杆顶在塑件的薄弱处
3.脱模斜度过小
4.熔体和模具温度相差过大,使部残余应力加大,在受局部力时易出现顶白
制品缺陷
原因分析
应对措施
气泡
1.模具的排气系统排气不良或堵塞
2.流道过长、过细,或流道中有贮气死角
3.多腔模具
4.注射速度过快
5.熔体温度过高,引起熔体降解产生大量气体
6.原料中含水分较多或粉末料太多
7.回料加入过多
8.塑料件上有厚薄悬殊过大的部分
1.检查排气系统,或疏通被堵塞的通道
2.缩短和加大流道,去除流道中的死角
制品缺陷
原因分析
应对措施
银纹
1.原料中水分多
2.回料、粉末过多,挥发物含量高
3.料筒有旧料
4.熔料温度过高,使塑料降解产生气体,从而产生降解银纹
5.模具问题
1.充分干燥原料
2.尽量选用粒径均匀的料,少用回料,筛除粉末,降低原料挥发物的含量
3.彻底清除料筒的旧料
4.降低料筒及喷嘴温度,降低螺杆转速及前进速度,缩短增压时间
制品缺陷
原因分析
应对措施
变形
1.注塑压力过高
2.熔体温度过高,塑件在急冷过程中会残留大量应力而导致变形
3.保压压力过高,塑料件成型时的应力会过高,脱模后应力的不均衡释放将使塑料件翘曲变形
4.保压时间短
5.模具的型腔和型芯温度不平衡
6.型腔拉模或模具的脱模斜度不够,模具光洁度不够
7.产品装箱位置或包装不合理