华为电缆组件技术规范DKBA3256
PCBA检验标准第五部分整板外观

DKBA 华为技术部技术标准DKBA3200.5-2009.12代替DKBA3200.5~2005.06代替Q/DKBA3200.5~9-2003PCBA检验标准第五部分:整板外观2009年12月31日发布 2010年01月01日实施华为技术Huawei Technologies Co., Ltd.所有侵权必究All rights reserved目录1围和简介 (6)1.1围 (6)1.2关键词 (6)2规性引用文件 (6)3金手指 (6)4板材 (8)4.1白斑和微裂纹 (8)4.2起泡和分层 (9)4.3显布纹/露织物 (10)4.4晕圈和板边分层 (11)4.5烧焦 (12)4.6弓曲和扭曲 (13)4.7柔性板及刚柔结合板 (14)4.7.1缺口/撕裂 (14)4.7.2加强板分层 (15)4.7.3变色 (15)4.7.4焊料灯芯效应(Wicking) (16)4.8导体/焊盘 (16)4.8.1横截面变小/宽度变小 (16)4.8.2焊盘撕起 (17)4.8.3机械损伤 (18)5标记 (19)5.1蚀刻标记 (20)5.2丝印标记 (21)5.3印章标记 (23)5.4激光打印标记 (25)5.5标签 (27)5.5.1条形码 (27)5.5.2可读性 (27)5.5.3粘结牢固性和破损 (27)5.5.4安放位置 (28)6清洁度 (29)6.1焊剂残留物 (29)6.2颗粒状物质 (30)6.3氯化物、碳化物、白色残留物 (31)6.4免清洗工艺焊剂残留物 (32)6.5其它外观 (34)7阻焊膜和敷形涂层 (36)7.1阻焊膜 (36)7.1.1阻焊膜起皱/开裂 (36)7.1.2阻焊膜空洞/起泡 (37)7.1.3阻焊膜裂解 (38)7.1.4阻焊膜变色 (39)7.2敷形涂层 (40)7.2.1总则 (40)7.2.2敷形涂层覆盖围 (40)7.2.3敷形涂层厚度 (42)前言本标准的其它系列标准:DKBA3200.1 PCBA检验标准第一部分:总要求和应用条件DKBA3200.2 PCBA检验标准第二部分:焊点基本要求DKBA3200.3 PCBA检验标准第三部分:SMD组件DKBA3200.4 PCBA检验标准第四部分:THD组件DKBA3200.6 PCBA检验标准第六部分:结构件、压接件、端子DKBA3200.7 PCBA检验标准第七部分:跨接线与对应的国际标准或其它文件的一致性程度:本标准参考IPC-A-610E的第10章容,结合我司实际制定/修订。
华为技术规范汇总
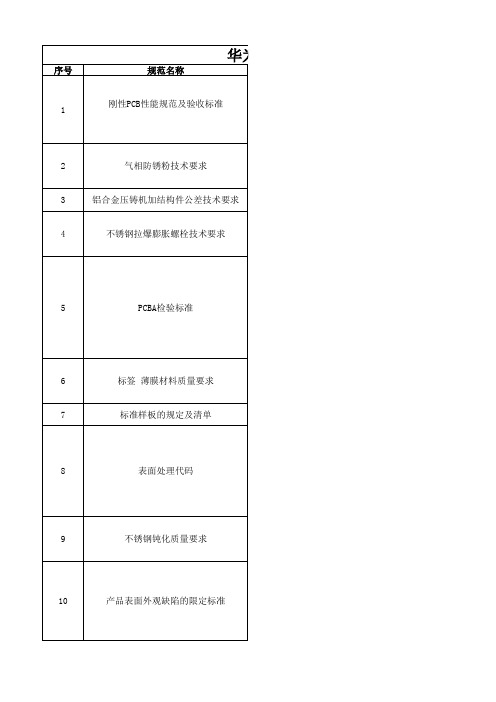
序号 规范名称 刚性PCB性能规范及验收标准
1
2
气相防锈粉技术要求
3
铝合金压铸机加结构件公差技术要求
4Leabharlann 不锈钢拉爆膨胀螺栓技术要求
5
PCBA检验标准
6
标签 薄膜材料质量要求
7
标准样板的规定及清单
8
表面处理代码
9
不锈钢钝化质量要求
10
产品表面外观缺陷的限定标准
11
通用电缆设计规范
12 13 14 15 16
PCB设计规范 钣金结构件可加工性设计规范 华为电缆组件测试规范 电缆组件检验标准 高密度PCB(HDI)检验标准
17
硬件质量标准
18
传输设备维护保障 技术支持服务规范
19 20 21 22 23
室外光缆接头盒技术要求 华为硬件设计规范 包装材料检验作业标准指导书 金属材料及其表面处理的选型设计要求 连接器、线缆选型及其组件设计规范
华为企业技术标准序号规范名称主要内容备注标签薄膜材料质量要求不锈钢钝化质量要求10产品表面外观缺陷的限定标准11通用电缆设计规范1213钣金结构件可加工性设计规范14华为电缆组件测试规范15电缆组件检验标准1617硬件质量标准1819室外光缆接头盒技术要求20华为硬件设计规范硬件工程师手册刚性pcb性能规范及验收标准1本标准规定了刚性pcb可能遇到的各种与可组装性可靠性有关的事项及性能检验标准
第一部分:《电缆设计过程》 第二部分:《电缆制图》 第三部分:《电缆标识设计》 第四部分:《电缆长度与公差设计》 本规范规定了PCB设计流程和设计原则,为PCB设计者提供必 要的设计原则和约定 本规范规定了钣金结构设计所要注意的加工工艺要求。 本规范适用于钣金结构设计必须遵守的加工工艺要求。 规范化华为电缆组件产品的测试要求,确保产品的机械物理 性能、电气性能、环境性能能够满足客户的要求。 本标准针对HDI印制板特点,对积层材料、微孔、细线等性 能及检测要求进行了描述。本标准没有提到的其他条款,依 照Q/DKBA3178.1《刚性PCB检验标准》执行。 本标准为客户监控检查华为技术有限公司安装的通信设备的 硬件工程质量提供依据,便于与客户协商明确客户对工程硬 件安装质量的要求,保证工程硬件安装质量满足客户要求, 交付给客户满意的工程硬件安装质量,为今后设备安全稳定 运行提供保证。 系统服务项目、服务承诺及双方维护部门在运行维护工作中 须共同遵守的流程进行全面界定。 华为提供的系统服务包括故障处理服务、巡检服务、技术咨 询服务、软件版本支持服务、资料更新服务、技术交流服务 等。 本技术要求适用于GJ2-72光缆接头盒和GLK-48光缆接头盒的 选型、采购与检验 硬件工程师手册 适用于HW所有包装和辅材类物料(含彩盒、纸箱、PE袋、气 泡袋、珍珠棉托、绝缘胶带、高温胶带、导电布等)样品承 认的测试。 本标准适用于CDMA通讯设备所用连接器、线缆选型及其组件 设计。
华为电缆组件技术规范DKBA3256
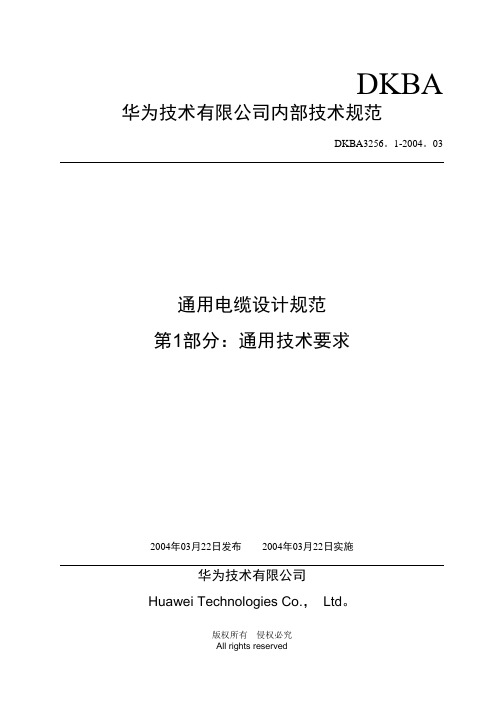
DKBA 华为技术有限公司内部技术规范DKBA3256。
1-2004。
03通用电缆设计规范第1部分:通用技术要求2004年03月22日发布2004年03月22日实施华为技术有限公司Huawei Technologies Co.,Ltd。
版权所有侵权必究修订声明Revision declaration本规范拟制与解释部门:结构造型设计部基础电缆专项组本规范的相关系列规范或文件:《通用电缆设计规范第2部分:电缆制图》;《通用电缆设计规范第3部分:电缆标识设计》;《通用电缆设计规范第4部分:电缆长度与公差设计》.相关国际规范或文件一致性:替代或作废的其它规范或文件:相关规范或文件的相互关系:《通用电缆设计规范》由以下四部分组成:第1部分:通用技术要求;第2部分:电缆制图;第3部分:电缆标识设计;第4部分:电缆长度与公差设计。
本规范是第1部分:通用技术要求。
本规范版本升级更改主要内容:本规范主要起草专家:结构造型设计部:孙宝亮(29642)本规范主要评审专家:结构造型设计部:涂修宇(16155)、吴炎辉(10448)、吴国祥(18066)、魏立新(8318)、方炜(19626)、杨东(28085)、王明聪(29661)、邱俊峰(20045)、技术质量认证部:魏喜鹏(14013)、物料品质部:龙君峰(7182)。
目录Table of Contents1正文图面要求 (6)1。
1图纸中的标注要求 (6)1。
1.1尺寸标注 (6)1。
1.2辅料的标注 (6)1.2接线表要求 (6)1.2。
1接线表的格式 (6)1。
2.2接线表的文字类别 (6)1.2.3接线表的内容 (6)1。
3视图的要求 (7)1。
4标签的要求 (7)2物料使用要求 (7)2.1物料的选用原则 (7)2。
2物料使用相关规定 (7)3加工要求 (7)3。
1注塑用塑胶材料的要求 (8)3.1.1塑胶材料的硬度 (8)3.1.2塑胶材料的阻燃等级 (8)3。
华为电缆组件测试规范标准

目录1、目的 (2)2、围 (2)2.1 围 (2)2.2 简介 (2)2.3 关键词 (2)3、规性引用文件 (3)4、术语和定义 (3)5、一般要求 (3)5.1 标准大气条件 (3)5.2 恢复条件 (3)5.3 干燥条件 (4)5.4 温度容许误差 (4)5.5 试验仪器、设备的误差 (4)5.6 测试夹具 (4)5.7 测试样本 (4)6、测试方法 (5)6.1 1000 类电气性能测试方法 (5)6.2 2000类机械物理性能测试方法 (28)6.3 3000类环境性能测试方法 (34)7、试判定标准 (41)7.1 电缆组件物理机械性能检验标准 (41)7.2 电缆组件电气性能检验标准 (44)7.3 电缆组件环境性能检验标准 (50)1、目的:规化华为电缆组件产品的测试要求,确保产品的机械物理性能、电气性能、环境性能能够满足客户的要求。
2、围:2.1 围本技术标准规定了华为电缆组件产品的测试方法、测试判定标准。
本技术标准适用于华为所以电缆组件的测试及判定。
如图纸有特殊要求,请依图纸要求执行。
2.2 简介本技术标准规定的测试方法分为电气性能测试方法、物理机械性能测试方法、环境性能测试方法共三类,并规定了此三类测试判定标准,每一类的测试方法编号如下:a、电气性能测试方法:1001-1999b、物理机械性能测试方法:2001-2999c、环境性能测试方法:3001-39992.3 关键词电缆组件测试方法电气性能参数物理机械性能参数环境性能3、规性引用文件:下列文件中的条款通过本规的引用而成为本规的条款。
4、术语和定义:4.1电源线类电缆组件:使用电源作为信号传输媒质的电缆组件。
4.2 特殊类电缆组件:电缆组件上含有扬声器、风扇、液晶显示器、蜂鸣器、变压器、指示灯等如此以非连接器的功能器件为主的电缆。
4.3 信号类电缆组件:使用通信电缆(包括双绞线和同轴电缆等)作为信号传输媒质的电缆组件。
华为技术有限公司内部技术规范--金属材料质量要求

DKBA 华为技术有限公司内部技术规范DKBA0.400.0114 REV.1.0金属材料质量要求Requirement for the metal material修订声明Revision declaration 本规范拟制与解释部门:整机工程部结构造型设计部本规范的相关系列规范或文件:无相关国际规范或文件一致性:无替代或作废的其它规范或文件:无相关规范或文件的相互关系:无目录Table of Contents1规定的材料81.1材料牌号及化学成份81.2材料的机械性能91.2.1基本力学性能91.2.2工艺性111.3对预镀钢板的特殊要求111.3.1表面镀层厚度及表面处理方式111.3.2表面外观质量111.3.3镀层附着性试验121.3.4表面耐蚀性121.3.5表面接触电阻131.3.6与有机涂层的结合力132替代材料133附录:预镀钢板外观花纹图片154参考文献REFERENCE DOCUMENT 16表目录List of Tables 表1 钢材牌号及化学化学成份8表2 材料力学性能要求10表3 替代材料表13图目录List of Figures 图1 耐指纹电镀锌钢板:均匀的灰色15图2 热镀铝锌板:小晶花15图3 热浸镀锌板:大晶花16图4 热浸镀锌板(GI料):无晶花、但有锌纹16金属材料质量要求Requirement for the metal material范围Scope:本规范规定了华为技术有限公司结构产品所用到的金属材料的质量要求。
本规范适用于华为技术有限公司结构产品的设计、生产、和质量检验。
简介Brief introduction:本文说明了华为技术有限公司结构产品中所用到的所有金属原材料的种类以及每种材料的详细质量指标要求、检测方法和质量控制要求。
包括材料牌号、化学成份、强度等等项目。
本文所提到的压铸材料仅是指压铸加工用的原材料,对于压铸件产品的质量请参见其它规范。
华为电缆组件检验标准(第一部分:电缆组件外观检验标准)
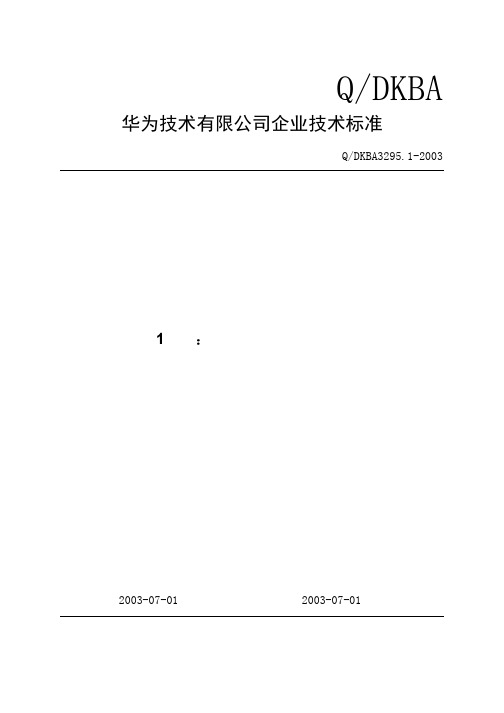
Q/DKBA 华为技术有限公司企业技术标准Q/DKBA3295.1-2003电缆组件检验标准第1部分电缆组件外观检验标准2003-07-01发布2003-07-01实施华为技术有限公司发布目录1范围 (9)1.1范围 (9)1.2基本要求 (9)1.3关键词 (9)2规范性引用文件 (9)3术语和定义 (10)4电缆组件中线材的外观检验 (10)4.1外护套 (10)5电缆组件中的连接器外观检验及加工工艺外观检验 (12)5.1电缆组件中连接器的外观部分 (12)5.2电缆组件的外观部分 (16)5.2.1同轴连接器 (16)1.套筒压接 (16)2.半刚半柔电缆的焊接 (18)3.弯式同轴连接器的压盖 (19)4.同轴连接器的插针与内绝缘 (21)5.2.2D型连接器 (23)1.焊接型D型连接器 (23)2.IDC型D型连接器 (32)3.IDC牛头连接器 (32)5.2.3IDC导线连接器 (35)5.2.4网口连接器 (40)5.2.5连续端子冷压端子OT端子类连接器 (42)6标签的外观检验 (53)7热缩套管的外观检验 (58)8电缆线束的外观检验 (59)8.1导线连接器的线扣绑扎 (59)8.2线束的线扣绑扎 (61)9过程检验 (64)10参考资料清单 (65)图目录图1 线材护套表面脏污 (10)图2 线材护套表面损伤或变形 (11)图3 线材护套表面损伤或变形 (11)图4 线材表面明显刮痕 (11)图5 线材表面明显刮痕 (11)图6 电缆弯曲造成的损伤 (12)图7 线材护套表面印字磨损无法辨认 (12)图8 连接器镀层划伤 (13)图9 非正常性损伤 (13)图10 非正常性损伤 (14)图11 镀层脱落 (14)图12 缩针 (14)图13 弯针 (15)图14 压接不到位且压线片遗失 (15)图15 连接器插孔堵有异物 (15)图16 合格的套筒压接 (16)图17 套筒与连接器主体之间的间距 (17)图18 套筒压接延长至电缆处 (17)图19 套筒的两次压接 (17)图20 压接套筒的耳朵 (18)图21 半刚半柔电缆的合格焊接 (18)图22 非360度圆周焊 (19)图23 焊锡堆积连接器主体残留焊锡 (19)图24 合格的平盖压接 (20)图25 合格的圆盖压接 (20)图26 压盖非规则形变并造成连接器主体损伤 (20)图27 压盖未实现充分压接 (21)图28 合格的插针与内绝缘 (21)图29 绝缘子凸出 (22)图30 绝缘子凹陷 (22)图31 绝缘子存在异常裂纹 (22)图32 含易导电物质 (23)图33 插针相对高度低于器件规格要求 (23)图34 绝缘子与外导体之间存在明显缝隙 (23)图35 焊点的湿润状态 (24)图36 焊锡充满焊杯 (24)图37 焊锡在导线上的爬接 (24)图38 导线紧贴焊杯后壁 (25)图39 导线未贴紧焊杯后壁 (25)图40 正确的热缩管套装 (25)图41 注塑件合格品 (26)图42 锡量不足 (26)图43 焊杯上残留锡尖 (27)图44 锡包 (27)图45 焊接导体裸露过长 (28)图46 导线焊接歪斜影响后续操作 (28)图47 不合格的热缩管套装 (29)图48 螺钉方向一致 (29)图49 外壳伸出螺钉过长或过短 (29)图50 非设计因素造成的印痕或台阶 (29)图51 压伤芯线 (30)图52 模脏脏污与走胶不齐 (30)图53 压伤连接器 (30)图54 冲胶/批峰 (31)图55 混色 (31)图56 缺胶1 (31)图57 缺胶2 (32)图58 合格的排线裁线 (32)图59 合格的排线压接 (33)图60 合格的排线折叠 (33)图61 不合格的排线裁线 (33)图62 排线撕开伤及芯线 (33)图63 压线片未充分锁紧 (34)图64 排线折叠余量过大 (34)图65 排线伸出压线片过长 (34)图66 排线与连接器的位置相对歪斜 (35)图68 芯线导体的深度范围 (35)图69 合格的芯线伸出量 (36)图70 两个包线片完全包覆芯线 (36)图71 芯线与包线片之间允许有一定缝隙存在 (36)图72 芯线悬浮于刀口上 (37)图73 芯线位置过低 (37)图74 芯线顶部与前刀口平齐 (37)图75 芯线顶部未伸出前刀口 (37)图76 芯线顶部伸出前刀口的长度过短 (38)图77 芯线过长发生卷曲 (38)图78 包线片未完全包覆芯线 (38)图79 包线片未完全包覆芯线 (38)图80 两根芯线压入同一端子 (39)图81 芯线打扭 (39)图82 未绑扎线扣 (40)图83 线扣扎反 (40)图84 网口连接器的压接1 (40)图85 网口连接器的压接2 (41)图86 网口连接器金片压接深度 (41)图87 适于单根导体的金片 (41)图88 适于多股绞合导体的金片 (41)图89 .连续端子的定义 (43)图90 OT端子的定义 (43)图91 端子压接区定义 (43)图92 标准端子绝缘压接片的合格压接 (44)图93 端子的绝缘压接片的合格压接 (44)图94 多根电源线的合压 (44)图95 绝缘压接片未穿透电线绝缘 (45)图96 绝缘压接片的包接 (45)图97 合格的导体压接区 (46)图98 导线与漏斗口平齐 (46)图99 填充导线的压接未伸出端子压接区 (46)图100 漏斗口高度 (47)图102 可接受的压接 (47)图103 绝缘压接片刺破电线绝缘层 (47)图104 绝缘压接片的绝缘支撑小于180度 (48)图105 绝缘压接片的张开角度大于45度 (48)图106 绝缘压接端子未实现顶部汇接 (48)图107 绝缘压接片压接在电线导体上 (48)图108 电线导体反折在端子的绝缘压接片中 (49)图109 绝缘在端子的导体压接区出现 (49)图110 电线绝缘压接在端子的导体压接区内 (49)图111 导线未伸出端子的导线压接区 (49)图112 导线未伸出端子的导线压接区 (50)图113 导线伸到端子接合区 (50)图114 导线伸到端子接合区 (50)图115 导线反折及未被包覆 (50)图116 非功能性形变香蕉型形变 (51)图117 导线在预绝缘管外 (51)图118 无漏斗口或漏斗口过大 (51)图119 导线伸出端子外 (51)图120 预绝缘管压接破裂导体伸出过长 (52)图121 热缩管包住安装区 (52)图122 热缩管未包住芯线导体 (52)图123 不合格的端子截断片 (53)图124 印字清晰 (53)图125 条形码标签 (53)图126 轻微褶皱 (54)图127 印字不清晰 (54)图128 环绕型标签未搭接 (55)图129 褶皱影响标签的识别与正常使用 (55)图130 标签的对折移位 (55)图131 没有将纸质内容完全覆盖 (56)图132 标签破裂与孔洞 (56)图133 标签中的字符被覆盖 (56)图134 标签在连接器上粘贴歪斜 (57)图136 标签脏污 (58)图137 标签打卷 (58)图138 热缩套管完全缩紧 (58)图139 热缩套管未完全缩紧 (58)图140 3*84*83*16导线连接器线扣绑扎位置正面 (59)图141 3*84*83*16导线连接器线扣绑扎位置侧面 (59)图142 2*22*3导线连接器线扣绑扎位置正面 (59)图143 2*22*3导线连接器线扣绑扎位置侧面 (60)图144 2*54*5导线连接器线扣绑扎位置正面 (60)图145 2*54*5导线连接器线扣绑扎位置侧面 (60)图146 4*6导线连接器线扣绑扎位置正面 (60)图147 4*6导线连接器线扣绑扎位置侧面 (61)图148 线扣带的伸出 (61)图149 合格的线束绑扎 (61)图150 各线缆的弯曲半径符合设计要求 (62)图151 线扣绑扎造成伤害性形变 (62)图152 线扣剪断时残留锐角 (63)图153 每一个单元的伸出对应一个线扣的绑扎 (63)图154 线束中单元线缆不规则交叉 (63)图155 线束中的单元线缆形成死结 (64)图156 同轴电缆的弯曲半径过小 (64)密级内部公开 Q/DKBA3295.1-2003前言本标准的其他系列规范Q/DKBA3295电缆组件检验标准分为四个部分第一部分电缆组件外观检验标准第二部分电缆组件物理机械性能检验标准第三部分电缆组件电气性能检验标准第四部分电缆组件环境性能检验标准与对应的国际标准或其他文件的一致性程度无标准代替或作废的全部或部分其他文件DKBA0.170.0008D型连接器类制成电缆的外观检验标准DKBA0.170.0006IDC导线连接器类制成电缆外观检验标准DKBA0.170.0003电源类连接器制成电缆外观检验标准DKBA0.170.0001路由器电缆检验通用规范DKBA0.170.0007特殊类制成电缆的外观检验标准DKBA0.100.0036同轴连接器类制成电缆外观检验标准DKBA0.170.0004网口连接器类制成电缆外观检验标准DKBA0.100.0004用户电缆检验通用规范DKBA0.100.0005中继电缆检验通用规范DKBA0.170.0009注塑类电缆外观检验标准与其他标准或文件的关系无与标准前一版本相比的升级更改的内容第一版无升级更改信息本标准由整机工程部结构技术基础研究部提出本标准主要起草和解释部门结构基础技术研究部电缆专项组本标准主要起草专家结构基础技术研究部电缆专项组:方炜19626本标准主要评审专家结构基础技术研究部电缆专项组孙宝亮29642邓庆龙26322王海召27062涂修宇16155王俊宁17614武鸿彬9317结构总体技术部陈念云4685结构设计部吴炎辉10448吴国祥18066魏立新8318来宝荣14357TQC魏喜鹏14013IQC楚友平2476本标准批准部门整机工程部结构造型设计中心本标准所替代的历次修订情况和修订专家为标准号主要起草专家主要评审专家姓名(工号)姓名(工号) 姓名(工号)姓名(工号)姓名(工号)姓名(工号) 姓名(工号)姓名(工号)密级内部公开 Q/DKBA3295.1-2003电缆组件检验标准第一部分电缆组件外观检验标准1 范围1.1 范围本标准规定了我司所有种类电缆组件的外观检验标准除非电缆设计图纸上有特殊要求否则参照此标准执行电缆组件的外观检验本标准适用于我司所有种类电缆组件的外观检验1.2 基本要求根据电缆组件的分类以及各类型电缆组件的加工特点对制造过程中的以及成品的状态外观进行了定义电缆组件外观检验前对于线材及连接器首先应该确认是否我司指定选用物料并根据相应的规格书对线材及连接器等几何尺寸等进行确认电缆组件的外观检验均应在光线充足的情况下目视条件进行检验尺寸等无法确认的情况可以借助测量工具1.3 关键词电缆组件测试方法外观2 规范性引用文件下列文件中的条款通过本规范的引用而成为本规范的条款凡是注日期的引用文件其随后所有的修改单不包括勘误的内容或修订版均不适用于本规范然而鼓励根据本规范达成协议的各方研究是否可使用这些文件的最新版本凡是不注日期的引用文件其最新版本适用于本规范序号编号名称1 GB(ITU IEC等) XX标准2 Q/DKBAXXXX XX技术标准密级内部公开 Q/DKBA3295.1-20033 术语和定义1电源线类电缆组件使用电源线作为信号传输媒质的电缆组件2特殊类电缆组件电缆组件上含有扬声器风扇液晶显示器蜂鸣器变压器指示灯等如此以非连接器的功能器件为主的电缆3信号类电缆组件使用通信电缆包括双绞线和同轴电缆等作为信号传输媒质的电缆组件本标准所采用的其它术语其定义按照GB4210和GJB724 电缆组件中线材的外观检验4.1 外护套合格1电缆线材护套表面清洁无脏污2电缆线材护套表面没有烫伤割伤严重磨损等损伤3电缆线材护套表面没有擦花或可以有浅度的擦花现象但轻擦外表面无毛刺和凸起感护套无变色情况4电缆线材护套表面印字清晰且印字连续5电缆线材护套或绝缘在注塑或加工后的没有起包现象6电缆线材护套或绝缘的颜色与PANTONE标准色号的色差E小于等于17电缆线材护套剥开后露出的屏蔽部分应保持完整无断裂或划伤现象不合格1电缆线材护套或绝缘表面脏污污点直径 1.0mm一般手段可清除的脏污干布可擦拭干净为2处以上为不合格存在任一无法清除脏污为不合格如图1所示图1线材护套表面脏污2电缆线材外护套或绝缘有任一损伤或变形如鼓包凹陷缺损等均为不合格如图2图3所示图2线材护套表面损伤或变形图3线材护套表面损伤或变形3电缆外表面存在由于加工造成的划痕长度 5.0mm,且深度0.15mm或损伤轻擦外表面有刮磨感划痕处线缆颜色有变化如图45半刚电缆弯曲造成电缆本身不可恢复的损坏如图6所示图4线材表面明显刮痕图5线材表面明显刮痕图6电缆弯曲造成的损伤4电缆线材外护套或绝缘表面由于加工造成护套表面印字磨损刮伤印字内容无法辨认等如图7所示图7线材护套表面印字磨损无法辨认5电缆线材护套或绝缘的颜色与PANTONE标准色号的色差E16电缆线材护套剥开后露出的屏蔽部分不完整或有断裂或划伤现象5 电缆组件中的连接器外观检验及加工工艺外观检验5.1 电缆组件中连接器的外观部分合格1连接器金属外表面无划伤或有轻度划伤但划伤处未露出镀层下的金属划伤长度小于10mm且数量小于3处2连接器无非正常的损伤裂纹和裂缝3连接器金属外壳无锈蚀或锈斑4无电镀层脱落情况无电镀不均匀情况5连接器的插针镀层无损伤锈蚀等6连接器插头无缺针断针弯针等不良7装配壳装配到位螺钉等连接器附件没有缺失密级内部公开 Q/DKBA3295.1-20038连接器外壳无不易清除的脏污插针或插孔没有涂有或堵有异物影响连接器之间的正常电接触9符合相应的器件规格书上外形尺寸的要求不合格1连接器有变形如图9或划伤并且划伤处已露出镀层下的金属或划伤长度深度大于100.15mm数量大于等于3处参见图8图8连接器镀层划伤2连接器金属外壳塑胶绝缘等有任一非正常的损伤裂纹和裂缝中的一项如图9图10图9非正常性损伤图10非正常性损伤3连接器导体金属外壳等有任一锈蚀或锈斑为不合格4有电镀层脱落情况或有电镀不均匀情况如图11所示图11镀层脱落5连接器插针有任一镀层损伤与主体颜色不同或露出镀层表面下金属为不合格6连接器插头内有缺针断针弯针缩针不良中的一项如图1213图12缩针图13弯针其中缩针的要求为除非有特别说明多针的连接器的任一针不得低于其他针的0.5mm单针的连接器的针需根据器件规格书进行检验7装配不到位螺钉等连接器附件缺失松动等如图14所示图14压接不到位且压线片遗失8连接器外壳不易清除的脏污插针或插孔涂有或堵有异物影响连接器之间的正常电接触如图15所示图15连接器插孔堵有异物9不符合相应的器件规格书的外观尺寸的要求密级内部公开 Q/DKBA3295.1-2003 5.2 电缆组件的外观部分5.2.1 同轴连接器1. 套筒压接合格1压接后的套筒紧贴在连接器主体2朝向电缆端的压接套筒应该为喇叭口喇叭口长度在0.75 1.0倍电缆外径之间3压接后的套筒不可以旋转或沿电缆的轴向移动4压接后套筒与连接器主体之间的距离 1.0mm对于开天窗式同轴连接器套筒上半部分将窗体完全遮住无天窗暴露5压接后套筒的截面形状应该为圆形或正六边形无异常飞边或耳朵出现合格品参见图16图16合格的套筒压接不合格1压接后套筒与连接器主体之间的距离 1.0mm对于开天窗式同轴连接器由于套筒与连接器主体之间距离过大造成天窗暴露参见图17密级内部公开 Q/DKBA3295.1-2003图17套筒与连接器主体之间的间距2套筒压接后可旋转并沿电缆轴向移动3套筒的压接一直延长至电缆处并无喇叭口喇叭口长度在0.75 1.0倍电缆外径范围之外参见图18图18套筒压接延长至电缆处4套筒的两次压接参见图19图19套筒的两次压接5套筒压接存在明显的耳朵超出套筒材料所能承受耳朵处有较为明显的材料裂纹参见图20a其中为正常的正六边形压接为不合格的耳朵压接耳朵的尺寸大于或等于1.0mm参见图20bab图20压接套筒的耳朵2. 半刚半柔电缆的焊接合格1焊锡100填充在连接器与线缆之间的连结区域中无任何可视缝隙或微孔存在2焊锡呈湿润状态3连接器区域之外没有焊锡4无残余锡渣存在5连接器主体非焊接区域没有焊锡存在或非焊接区域无锡尖或锡块的存在6线缆的屏蔽外导体必须完全置于连接器内合格品参见图21图21半刚半柔电缆的合格焊接不合格1焊接未形成360度圆周焊有漏焊现象存在如图22所示图22非360度圆周焊2焊锡过多连接器主体挂锡影响连接器的正常使用如图23所示图23焊锡堆积连接器主体残留焊锡3线缆的屏蔽层未完全与连接器外导体充分连结或未完全伸入连接器中3. 弯式同轴连接器的压盖合格1压盖与连接器主体平齐2连接器主体没有由于压盖操作而造成损伤合格品参见图24图25图24合格的平盖压接图25合格的圆盖压接不合格1压盖压接为非规则性压接表现为非对称性压接过浅或过深压接后压盖与连接器主体之间有缝隙存在等参见图26图26压盖非规则形变并造成连接器主体损伤2由于压盖的压接造成连接器主体严重受损参见图26密级内部公开 Q/DKBA3295.1-20033压盖未实现充分压接表现为压盖与连接器主体表面非平齐状态或为高低不齐参见图27图27压盖未实现充分压接4. 同轴连接器的插针与内绝缘合格1同轴连接器内绝缘与连接器外导体的相对位置与连接器规格书上的要求相符不得凸出或下陷如图28连接器绝缘与外导体须保持平齐2同轴连接器内绝缘无异常性损伤如裂纹凹陷等3同轴连接器内绝缘无金属屑等易导电物质存在4插针的高度符合相应的器件规格的要求5同轴连接器的内绝缘与外导体壳体间无明显缝隙存在合格品参见图28图28合格的插针与内绝缘不合格1同轴连接器内绝缘与连接器外导体不平齐有凸出或凹陷的情况存在如图29及30所示图29绝缘子凸出图30绝缘子凹陷2同轴连接器内绝缘有不允许的异常性损伤如裂纹凹陷等如图31所示图31绝缘子存在异常裂纹3同轴连接器内绝缘材料中含有或表面附有金属屑等易导电物质存在如图32所示图32含易导电物质4插针的高度不符合相应的器件规格的要求如图33所示图33插针相对高度低于器件规格要求5同轴连接器的内绝缘与外导体壳体间有明显缝隙存在如图34所示图34绝缘子与外导体之间存在明显缝隙5.2.2 D型连接器1. 焊接型D型连接器合格密级内部公开 Q/DKBA3295.1-20031焊杯与导线之间焊点光滑显示有良好的湿润状态湿润角应该小于90度焊点被有型连接件的轮廓所限除外端子与导线的轮廓应该容易辨认焊锡在零件与导线上呈扩散状焊点形成凹面为标准焊接参见图35图35焊点的湿润状态2焊锡锡点均匀一致焊点无明显的锡过剩锡过少等现象3焊锡应该10075充满焊杯参见图36焊杯外面不得残留影响电气性能的锡尖等图36焊锡充满焊杯4对于连接器中存有单板的焊接要求焊锡爬在导体上的高度不小于导线直径的25参见图37图37焊锡在导线上的爬接5焊接完后电缆芯线的绝缘以顶住连接器焊杯为准其裸露在焊杯外面的裸导体长度没有超过焊杯外径1.5倍密级内部公开 Q/DKBA3295.1-20036焊接的芯线应该垂直插在连接器的焊杯中且紧贴焊杯后壁参见图38对于导线未贴紧焊杯后壁参见图39若焊接的导线不影响后续相关操作可以接受为合格图38导线紧贴焊杯后壁图39导线未贴紧焊杯后壁7如果焊接需要吹缩热缩管参见图40套管应该完全套装焊接端子且套装在电缆芯线上的长度应该为芯线直径的24倍图40正确的热缩管套装密级内部公开 Q/DKBA3295.1-20038装配外壳上面的螺钉朝向一正一反9连接器所适配对接固定螺钉伸出外壳长度为3.50.5mm10注塑部分无混色脏污缺料冲胶等不良造成的缺陷也无由于模具不合适造成的连接器的伤害等为合格品参见图41图41注塑件合格品11电缆注塑体螺钉注塑体线材护套颜色之间颜色一致三者之间色差E小于等于1为合格品不合格1焊点不湿润或湿润角大于90度参见图35的第三张图面2无焊料或锡量不足锡量不足指焊锡在焊杯中的填充度小于75为不合格参见图42图42锡量不足3连接器焊杯外边存有任一锡尖影响电气可靠性参见图43图43焊杯上残留锡尖4焊点存在一定的污染例如助焊剂的残留为不合格5对于连接器中存有单板的焊接焊锡爬在导体上的高度小于导线直径的25为不合格6焊点存在扰动现象即焊锡未充分融化下发生的操作动作造成的例如明显的锡拉尖锡包锡过多或者桥接等现象不符合焊点间距的最小电气间隙的要求可参见图44图44锡包7电缆芯线剥皮过长裸露在焊杯外面的裸导体超过焊杯外径1.5倍参见图45图45焊接导体裸露过长8导线的焊接未贴紧连接器焊杯后壁进行焊接且电缆芯线歪斜影响后续相关操作为不合格参见图46图46导线焊接歪斜影响后续操作9参见图47在需要包覆热缩管的情况下对于热缩管破裂A热缩管包覆芯线长度小于导线芯线绝缘外径的2倍B未完全包覆连接器端子C热缩管未吹缩D 等均不合格密级内部公开 Q/DKBA3295.1-2003图47不合格的热缩管套装10装配壳上面的转配螺钉朝向统一为不合格参见图48图48螺钉方向一致11连接器所适配对接固定螺钉伸出外壳长度不在3.5+/-0.5mm范围内过长及过短均不合格参见图49图49外壳伸出螺钉过长或过短12注塑体表面出现非设计因素造成的台阶及印痕例如合模线模具错开等台阶高度大于等于0.2mm长度大于5mm为不合格参见图50图50非设计因素造成的印痕或台阶13注塑压伤电缆芯线为不合格参见图51密级内部公开 Q/DKBA3295.1-2003图51压伤芯线14模具模腔不干净所引起的任一注塑表面脏污或注塑体存在任一肉眼可观察到的不可清除的脏污为不合格参见图52图52模脏脏污与走胶不齐15走胶不齐造成注塑边与连接器之间有明显的缝隙任一缝隙大于1.5mm为不合格参见图5216由于模具尺寸与连接器尺寸不符或其他原因造成的可观察到的注塑模具压伤连接器为不合格参见图53图53压伤连接器17由于模具等原因造成的任一可观察到的注塑冲胶/批峰为不合格参见图54图54冲胶/批峰18由于注塑料混料等原因造成注塑表面可观察到的任一颜色不纯温度过高造成可观察到的任一颜色改变或碳化为不合格参见图55图55混色19注塑后注塑表面发生由于缺胶等原因造成的可观察到的凹坑无料气泡等现象为不合格参见图56图57图56缺胶1图57缺胶220注塑体存在缩水缩水范围大于规定要求长宽高 1.0mm*0.5mm*0..5mm为不合格21注塑体表面存在温度过高产生的光面且范围大于或等于5.0mm*5.0mm22非电缆设计要求的情况下注塑体颜色螺钉注塑体颜色线材护套颜色三者之间的色差E大于12. IDC型D型连接器本部分检验标准参见焊接型D型连接器的相关要求3. IDC牛头连接器合格1扁平排线的裁线应该与排线边线保持垂直并且无波浪线存在或满足牛头连接器的压接要求参见图58及图59图58合格的排线裁线密级内部公开 Q/DKBA3295.1-2003图59合格的排线压接2电缆多股铜线无裸露在绝缘外面的现象或伸出量小于等于导体直径的50参见图583排线折叠后折叠部分与连接器之间的间隙小于或等于2.0倍芯线绝缘外径合格品如图60所示图60合格的排线折叠4排线与连接器压接后芯线伸出压线片的余量在01倍芯线绝缘外径之间参见图59不合格1扁平排线的裁线与排线边线不垂直并且有波浪线存在电缆多股铜线无裸露在绝缘外面的现象或伸出量大于导体直径的50参见图61图61不合格的排线裁线2排线撕开使用时撕裂处导体裸露或绝缘层损坏变薄参见图62图62排线撕开伤及芯线3牛头连接器的压线片未充分锁紧可观察到的如图63所示。
QDKBA3178.2-2004 华为技术有限公司企业技术高密度标准PCB检验标准
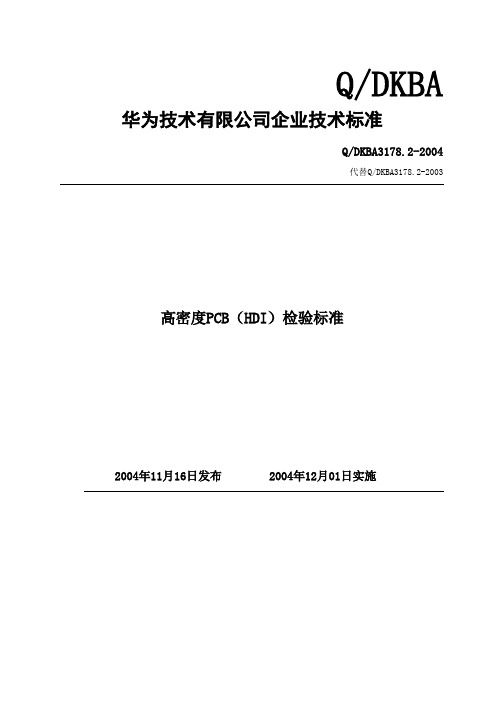
Q/DKBA 华为技术有限公司企业技术标准Q/DKBA3178.2-2004代替Q/DKBA3178.2-2003高密度PCB(HDI)检验标准2004年11月16日发布 2004年12月01日实施目次前言 (4)1范围 (6)1.1范围 (6)1.2简介 (6)1.3关键词 (6)2规范性引用文件 (6)3术语和定义 (6)4文件优先顺序 (7)5材料要求 (7)5.1板材 (7)5.2铜箔 (7)5.3金属镀层 (8)6尺寸要求 (8)6.1板材厚度要求及公差 (8)6.1.1芯层厚度要求及公差 (8)6.1.2积层厚度要求及公差 (8)6.2导线公差 (8)6.3孔径公差 (8)6.4微孔孔位 (9)7结构完整性要求 (9)7.1镀层完整性 (9)7.2介质完整性 (9)7.3微孔形貌 (9)7.4积层被蚀厚度要求 (10)7.5埋孔塞孔要求 (10)8其他测试要求 (10)8.1附着力测试 (10)9电气性能 (11)9.1电路 (11)9.2介质耐电压 (11)10环境要求 (11)10.1湿热和绝缘电阻试验 (11)10.2热冲击(Thermal shock)试验 (11)11特殊要求 (11)12重要说明 (11)前言本标准的其他系列规范:Q/DKBA3178.1 刚性PCB检验标准Q/DKBA3178.3 柔性印制板(FPC)检验标准与对应的国际标准或其他文件的一致性程度:本标准对应于“IPC-6016 Qualification and Performance Specification for High Density Interconnect(HDI) Layers or Boards”。
本标准和IPC-6016的关系为非等效,主要差异为:依照华为公司实际需求对部分内容做了补充、修改和删除。
标准代替或作废的全部或部分其他文件:Q/DKBA3178.2-2003 高密度PCB(HDI)检验标准与其他标准或文件的关系:上游规范Q/DKBA3061 《单面贴装整线工艺能力》Q/DKBA3062 《单面混装整线工艺能力》Q/DKBA3063 《双面贴装整线工艺能力》Q/DKBA3065 《选择性波峰焊双面混装整线工艺能力》DKBA3126 《元器件工艺技术规范》Q/DKBA3121 《PCB基材性能标准》下游规范Q/DKBA3200.7 《PCBA板材表面外观检验标准》Q/DKBA3128 《PCB工艺设计规范》与标准前一版本相比的升级更改的内容:相对于前一版本的变化是修订了RCC材料厚度及公差要求、微孔及埋孔孔径公差要求、镀铜厚度、热冲击条件等,增加了微孔形貌、积层被蚀厚度要求等。
华为电缆组件测试规范

华为电缆组件测试规范华为电缆组件是一种高质量的电缆配件,应用于各种类型的电缆系统中,以确保传输信号和能源的质量。
为了确保该组件的质量,华为制定了一套严格的电缆组件测试规范,以确保其符合产品标准和客户需求。
一、测试方法1.机械性能测试:该测试要求电缆组件在运输、安装和使用时具有足够的强度和硬度,以承受不同的负荷和环境。
测试方法包括拉力测试、皮扣强度测试、耐压测试和疲劳测试。
2.环境适应性测试:该测试要求电缆组件在不同的环境条件下具有良好的耐久性和可靠性,并且能够在常见的环境条件下工作。
测试方法包括高温测试、低温测试、湿度测试、盐雾测试和紫外线辐射测试。
3.电气性能测试:该测试要求电缆组件具有良好的电气性能,对信号传输和能源传输具有高效率和稳定性。
测试方法包括电阻测试、介电强度测试、故障电流能力测试和接触电阻测试。
4.安全性能测试:该测试要求电缆组件在安装和使用过程中不会对人员和设备造成任何危害,并确保任何故障时能够切断电源。
测试方法包括防火性测试、安全性能测试、绝缘性测试和触电安全性测试。
二、测试流程1.确定测试流程:确定电缆组件的测试流程,根据要求编制测试计划和测试用例。
2.检查测试设备:检查测试设备是否符合要求,并进行校准和调试。
3.测试准备:在测试前出具测试报告,进行初步的准备工作和标志。
4.执行测试:执行测试计划和测试用例,记录测试结果和异常情况。
5.评估测试结果:根据测试结果进行评估和分析,并对测试结果进行整合和归档。
6.生成报告:生成测试报告,包括测试结果、异常情况和建议。
三、质量标准华为电缆组件测试规范符合以下质量标准:1.国家质量标准:符合国家质量标准的电缆组件要求。
2.行业标准:符合行业标准的电缆组件要求。
3.应用标准:符合应用标准的电缆组件要求。
四、总结华为电缆组件测试规范为保证产品的质量和性能提供了一套严格的测试流程和质量标准。
该规范确保电缆组件在不同的环境和工作条件下具有优异的机械、环境、电气和安全性能,以满足客户的需求和要求。
- 1、下载文档前请自行甄别文档内容的完整性,平台不提供额外的编辑、内容补充、找答案等附加服务。
- 2、"仅部分预览"的文档,不可在线预览部分如存在完整性等问题,可反馈申请退款(可完整预览的文档不适用该条件!)。
- 3、如文档侵犯您的权益,请联系客服反馈,我们会尽快为您处理(人工客服工作时间:9:00-18:30)。
DKBA 华为技术有限公司内部技术规范通用电缆设计规范第1部分:通用技术要求2004年03月22日发布 2004年03月22日实施华为技术有限公司Huawei Technologies Co., Ltd.版权所有侵权必究All rights reserved修订声明Revision declaration本规范拟制与解释部门:结构造型设计部基础电缆专项组本规范的相关系列规范或文件:《通用电缆设计规范第2部分:电缆制图》;《通用电缆设计规范第3部分:电缆标识设计》;《通用电缆设计规范第4部分:电缆长度与公差设计》。
相关国际规范或文件一致性:替代或作废的其它规范或文件:相关规范或文件的相互关系:《通用电缆设计规范》由以下四部分组成:第1部分:通用技术要求;第2部分:电缆制图;第3部分:电缆标识设计;第4部分:电缆长度与公差设计。
本规范是第1部分:通用技术要求。
本规范版本升级更改主要内容:本规范主要起草专家:结构造型设计部:孙宝亮(29642)本规范主要评审专家:结构造型设计部:涂修宇(16155)、吴炎辉(10448)、吴国祥(18066)、魏立新(8318)、方炜(19626)、杨东(28085)、王明聪(29661)、邱俊峰(20045)、技术质量认证部:魏喜鹏(14013)、物料品质部:龙君峰(7182)。
目录Table of Contents1 .................................................................. 正文图面要求错误!未定义书签。
............................................................. 图纸中的标注要求错误!未定义书签。
..................................................................尺寸标注错误!未定义书签。
................................................................辅料的标注错误!未定义书签。
...................................................................接线表要求错误!未定义书签。
.............................................................. 接线表的格式错误!未定义书签。
.......................................................... 接线表的文字类别错误!未定义书签。
.............................................................. 接线表的内容错误!未定义书签。
...................................................................视图的要求错误!未定义书签。
...................................................................标签的要求错误!未定义书签。
2 .................................................................. 物料使用要求错误!未定义书签。
物料的选用原则.................................................. 错误!未定义书签。
............................................................. 物料使用相关规定错误!未定义书签。
3 ......................................................................加工要求错误!未定义书签。
......................................................... 注塑用塑胶材料的要求错误!未定义书签。
塑胶材料的硬度 .............................................. 错误!未定义书签。
........................................................ 塑胶材料的阻燃等级错误!未定义书签。
.................................................... 塑胶材料中的重金属含量错误!未定义书签。
..................................................................注塑颜色错误!未定义书签。
......................................................... 注塑类屏蔽电缆的加工错误!未定义书签。
............................. 电缆的设计使用芯数小于线材实物本身芯数的电缆加工错误!未定义书签。
................................... 电缆外径大于连接器装配壳出线口时电缆的加工错误!未定义书签。
................................... 一端无连接器的多芯电缆接线表打印和剥皮要求错误!未定义书签。
.................................................... 无总屏蔽的多芯双绞电缆错误!未定义书签。
.................................................... 无总屏蔽的多芯同轴电缆错误!未定义书签。
...................................................... 带总屏蔽多芯双绞电缆错误!未定义书签。
.................................................... 带总屏蔽的多芯同轴电缆错误!未定义书签。
...................................................................连接器附件错误!未定义书签。
.......................................................... 螺钉和螺母的要求错误!未定义书签。
.....................................................................加工辅料错误!未定义书签。
..................................................................热缩套管错误!未定义书签。
........................................................................ 线扣错误!未定义书签。
4 检验要求.......................................................... 错误!未定义书签。
5 .................................................... 参考文献Reference Document错误!未定义书签。
表目录 List of Tables表1 塑胶中重金属含量最大值 .................................... 错误!未定义书签。
表2 热缩套管的颜色 ............................................ 错误!未定义书签。
表3 热缩套管的性能要求 ........................................ 错误!未定义书签。
表4 线扣的强度 ................................................ 错误!未定义书签。
图目录 List of Figures图1 电缆的编织屏蔽层与铜箔焊接 ................................ 错误!未定义书签。
图2 铜箔焊接后的连接器 ........................................ 错误!未定义书签。
图3 螺钉和螺母的伸出长度要求 .................................. 错误!未定义书签。
图4 线扣...................................................... 错误!未定义书签。
通用电缆设计规范第1部分:通用技术要求范围Scope:本规范规定了电缆组件设计和加工中需要遵循的技术要求。
本规范适用于电缆组件的设计和加工。
简介Brief introduction:本规范规定了在电缆组件(以下简称电缆)设计必须遵循的关于电缆图纸设计的尺寸标注要求、辅料标注要求、电缆的物料选择要求。
规定了屏蔽电缆的加工要求、单端为空电缆的剥皮要求、使用芯数小于线材实物本身芯数的电缆加工要求、电缆外径大于连接器装配壳出线口时电缆的加工要求,以及电缆加工中使用的注塑材料、辅助物料(热缩套管、线扣、螺钉、螺母)的性能要求。
关键词Key words:电缆、标注、接线表、塑胶、色差、屏蔽加工、热缩套管、线扣引用文件:下列文件中的条款通过本规范的引用而成为本规范的条款。
凡是注日期的引用文件,其随后所有的修改单(不包括勘误的内容)或修订版均不适用于本规范,然而,鼓励根据本规范达成协议的各方研究是否可使用这些文件的最新版本。
凡是不注日期的引用文件,其最新版本适用于本规范。
术语和定义Term&Definition:1正文图面要求1.1图纸中的标注要求电缆图纸中需要标注的内容主要包括有电缆的设计尺寸标注及辅料的标注。
1.1.1尺寸标注图纸中必须标注的设计尺寸包括有电缆总长度,各分支电缆长度,电缆护套的剥皮长度,浸锡的长度,扁平电缆的撕开长度,射频电缆成型尺寸,射频电缆的过渡圆角半径,特殊要求的标签位置,热缩套管吹缩位置,线扣的绑扎位置等。
图纸中的设计尺寸和公差应符合通用电缆设计规范第4部分《电缆长度与公差设计》的规定。
电缆要求的尺寸公差符合《电缆长度与公差设计》所规定的公差时,公差不需要在图纸上标注。