典型连铸过程控制计算机系统的实现
DCS系统在钢铁生产中的应用
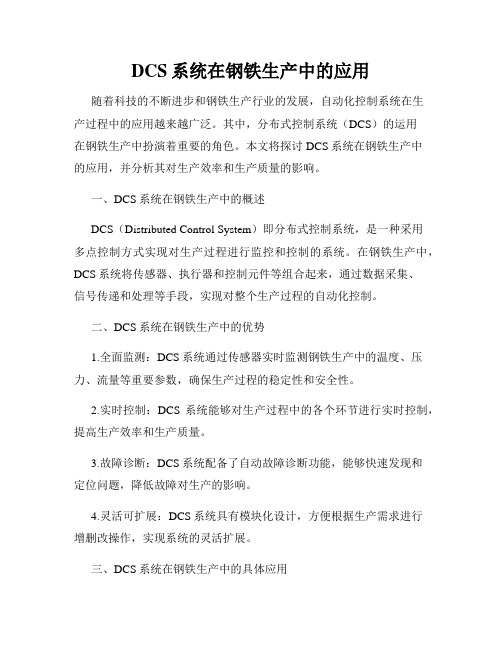
DCS系统在钢铁生产中的应用随着科技的不断进步和钢铁生产行业的发展,自动化控制系统在生产过程中的应用越来越广泛。
其中,分布式控制系统(DCS)的运用在钢铁生产中扮演着重要的角色。
本文将探讨DCS系统在钢铁生产中的应用,并分析其对生产效率和生产质量的影响。
一、DCS系统在钢铁生产中的概述DCS(Distributed Control System)即分布式控制系统,是一种采用多点控制方式实现对生产过程进行监控和控制的系统。
在钢铁生产中,DCS系统将传感器、执行器和控制元件等组合起来,通过数据采集、信号传递和处理等手段,实现对整个生产过程的自动化控制。
二、DCS系统在钢铁生产中的优势1.全面监测:DCS系统通过传感器实时监测钢铁生产中的温度、压力、流量等重要参数,确保生产过程的稳定性和安全性。
2.实时控制:DCS系统能够对生产过程中的各个环节进行实时控制,提高生产效率和生产质量。
3.故障诊断:DCS系统配备了自动故障诊断功能,能够快速发现和定位问题,降低故障对生产的影响。
4.灵活可扩展:DCS系统具有模块化设计,方便根据生产需求进行增删改操作,实现系统的灵活扩展。
三、DCS系统在钢铁生产中的具体应用1.原料处理:DCS系统能够对原料的配比、流量和质量进行控制和监测,确保原料的准确投入和混合工艺的精确控制。
2.高炉控制:DCS系统可通过温度、压力等传感器对高炉内部状态进行实时监测和控制,优化炼铁过程,提高炉温稳定性和炉渣质量。
3.连铸控制:DCS系统通过控制水流、板坯速度等参数,实现对连铸过程的精确控制,保证铸坯的质量和形状的一致性。
4.轧制控制:DCS系统对轧机的控制精度较高,可以准确控制轧辊力、板形和轧辊温度,提高轧制质量。
5.质量监控:DCS系统通过数据采集和分析,实现对产品质量的监测和报警,及时发现并解决质量问题。
四、DCS系统应用的效果评估DCS系统的应用在钢铁生产中已经取得了显著的效果。
首先,DCS系统的全面监测和实时控制能够提高生产效率,减少人工干预,降低生产成本。
钢铁连铸PLC技术体系
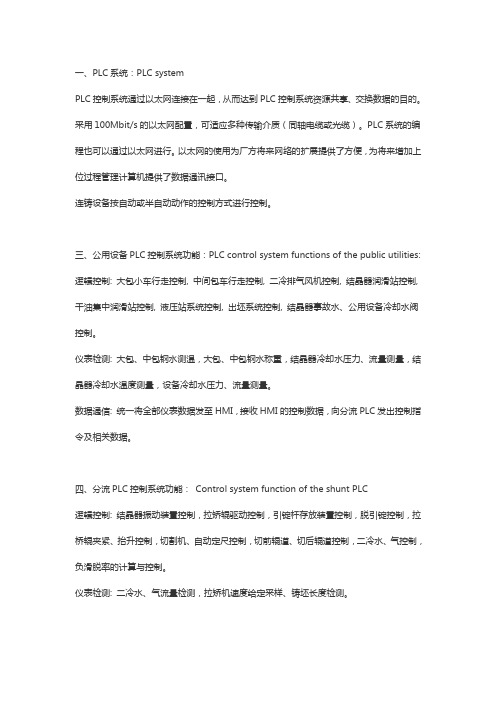
一、PLC系统:PLC systemPLC控制系统通过以太网连接在一起,从而达到PLC控制系统资源共享、交换数据的目的。
采用100Mbit/s的以太网配置,可适应多种传输介质(同轴电缆或光缆)。
PLC系统的编程也可以通过以太网进行。
以太网的使用为厂方将来网络的扩展提供了方便,为将来增加上位过程管理计算机提供了数据通讯接口。
连铸设备按自动或半自动动作的控制方式进行控制。
三、公用设备PLC控制系统功能:PLC control system functions of the public utilities: 逻辑控制: 大包小车行走控制, 中间包车行走控制, 二冷排气风机控制, 结晶器润滑站控制, 干油集中润滑站控制, 液压站系统控制, 出坯系统控制, 结晶器事故水、公用设备冷却水阀控制。
仪表检测: 大包、中包钢水测温,大包、中包钢水称重,结晶器冷却水压力、流量测量,结晶器冷却水温度测量,设备冷却水压力、流量测量。
数据通信: 统一将全部仪表数据发至HMI,接收HMI的控制数据,向分流PLC发出控制指令及相关数据。
四、分流PLC控制系统功能:Control system function of the shunt PLC逻辑控制: 结晶器振动装置控制,拉矫辊驱动控制,引锭杆存放装置控制,脱引锭控制,拉桥辊夹紧、抬升控制,切割机、自动定尺控制,切前辊道、切后辊道控制,二冷水、气控制,负滑脱率的计算与控制。
仪表检测: 二冷水、气流量检测,拉矫机速度给定采样、铸坯长度检测。
数据通信: 将仪表数据发至公用PLC,接收公用PLC的控制数据,向变频器发出控制数据,接收变频器相关数据。
轧线机由基础自动化系统控制自动或手动运行。
全面满足工艺生产要求,提高生产效率。
自动化由下列功能实现:- 级联控制- 微张力控制- 活套控制- 故障检测- 飞剪控制- HMI 系统- 物料跟踪- 其它功能。
所有任务均由分布式的PLC SIMATIC系统实现,带有开放式的通讯网络,便于扩展。
LF二级过程控制系统的研究与实现
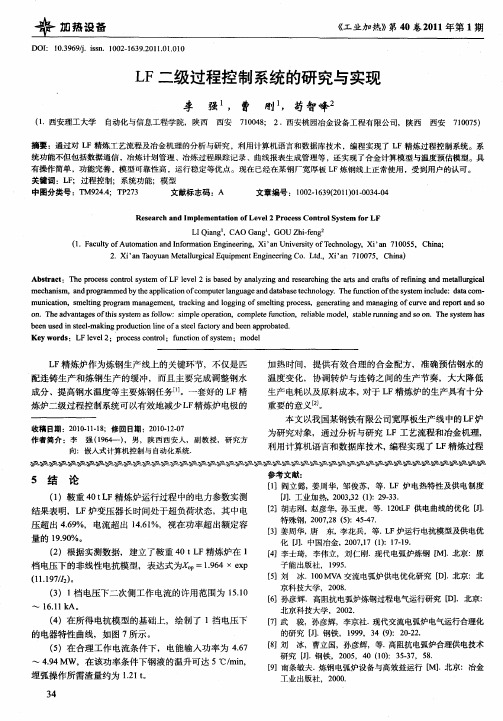
关键 词 : F L ;过程控制;系统 功能;模 型 中图分类号 :T 2 . P 7 M9 4 ;T 23 4 文献标志码 :A
文章编号 :10 —692 1) 103 .4 0 213 (0 10 .0 40
Re e r h a d I p e e t to f v l o e s n r l y t m o s a c n m lm n a i n o Le e Pr c s 2 Co t o se f r LF S
L F精炼炼钢生产 的缓冲 ,而且 主要完成调整钢水 成分 、提高钢水温度等主要炼钢任务 。一套好 的 L F精 炼炉二级过程控制系统可 以有效地减少 L 精炼炉 电极 的 F
收稿 日期 :2 1—11;修 回 日期 :2 1-20 001-8 001—7 作 者 简介 :李 强 (94 ) 男 ,陕 西 西安 人 , 副教 授 ,研 究方 16一 , 向 :嵌入 式计 算机 控 制与 自动化 系统 .
mu i ai n met g p o r m n g me t ra k n n o g n fs l n r c s ,g n r t g a d ma a i g o H V n p r a d S n c t ,s l n r g a ma a e n ,t c i g a d l g i g o met g p o e s e e a i n n gn f I e a d r o t o i i n C e O n o .T ea v n a e f h ss se a l w:s n h d a t g so t i y tm s o l f o i l p r t n o l t n t n eib emo e,s b er n i g a d S n mp eo e a i ,c mp e ef c i ,r l l d l t l n n n O o .T es se h s o u o a a u h y tm a
邯钢CSP过程控制系统安全架构的实现

能力 , 目前在 中高档服务器所采用 。如 H P公司的 Ap a P R S 、 l 和 A— I h C
IM 公 司的 Pw rP MIS公 司 的 MIS和 S N 公 司 的 S  ̄e B o e C、 P P U pr。
邯钢 C P过程控制 系统安全架构 的实现 S
刘建飞 王 鹏 刘延伟 河北钢铁 集团邯郸钢铁股份有限公 司连铸连 ̄ V 06 1 t t , 50 5
【 要】 摘 以河北钢铁集 团连铸连轧生产线过程控制 系统为例 , 对二级过程控制 系统的安 全冗余性能进行 分析, 详细介绍利用设备 冗余技术 、 于 基
1 言 前 邯钢薄板坯连铸连轧生产线( 简称 C P 是引进德 国西马克 9 S) O年代
世界先进技术 , 为我 国最早与珠钢 、 包钢 同期 引进了三条 C P生产线之 S
一
务器的运行 , 然后用一定的时间切换 至备用服务器 上面进行运行 , 才能
进行维修和恢复。 22 2 双机 热 备 ..
活 , 证应 用 在 短 时 间 内完 恢 复 正 常使 用 。 保 2 2 3单机 容 错 ..
情况下 , 过程控制系统的安全性就显 的非常必要及 迫切 。
2影 响 过 程控 制 系统 安全 的 因素
2 1服 务 器 的硬 件 架 构 .
单机容错技术则是在一 台服务 器实现高性 能容错的。它的容错能 力要远 比双机热备份中容错能力要 高。容 错服务器是通 过采用 同步技
的服 务器 操作 系统 主要有 : nosU i、iu Widw 、 n Lnx和 O V 。 x  ̄ MS
Wnos i w 操作系统 由于其最具人性化 的界 面, 且操作直观易 于使 d 并 用 , 目前最普及的操作系统 因此安全性也最差。随着 M c s t 是 io f r o 不断的
宝钢股份特钢事业部40T产线板带炼钢过程控制计算机系统
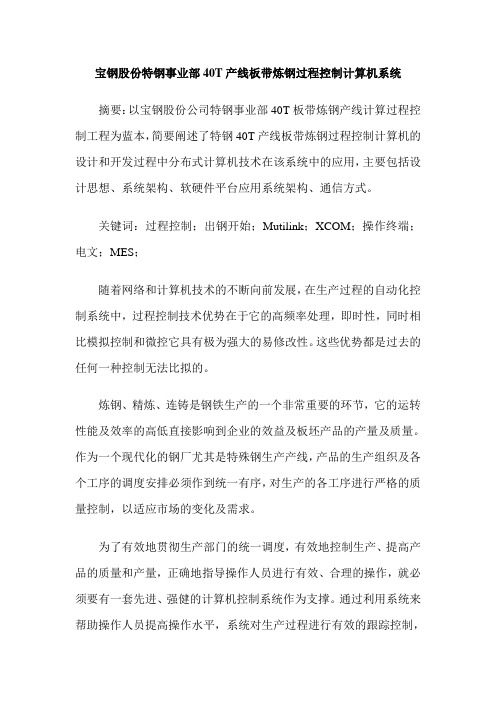
宝钢股份特钢事业部40T产线板带炼钢过程控制计算机系统摘要:以宝钢股份公司特钢事业部40T板带炼钢产线计算过程控制工程为蓝本,简要阐述了特钢40T产线板带炼钢过程控制计算机的设计和开发过程中分布式计算机技术在该系统中的应用,主要包括设计思想、系统架构、软硬件平台应用系统架构、通信方式。
关键词:过程控制;出钢开始;Mutilink;XCOM;操作终端;电文;MES;随着网络和计算机技术的不断向前发展,在生产过程的自动化控制系统中,过程控制技术优势在于它的高频率处理,即时性,同时相比模拟控制和微控它具有极为强大的易修改性。
这些优势都是过去的任何一种控制无法比拟的。
炼钢、精炼、连铸是钢铁生产的一个非常重要的环节,它的运转性能及效率的高低直接影响到企业的效益及板坯产品的产量及质量。
作为一个现代化的钢厂尤其是特殊钢生产产线,产品的生产组织及各个工序的调度安排必须作到统一有序,对生产的各工序进行严格的质量控制,以适应市场的变化及需求。
为了有效地贯彻生产部门的统一调度,有效地控制生产、提高产品的质量和产量,正确地指导操作人员进行有效、合理的操作,就必须要有一套先进、强健的计算机控制系统作为支撑。
通过利用系统来帮助操作人员提高操作水平,系统对生产过程进行有效的跟踪控制,对生产作业实绩进行有效的收集、统计以及对生产线上的主要设备进行有效管理,将大大地减少人力,提高生产效率。
本系统开发投入后,已经实现了实时地跟踪现场的生产,为生产提供必要的生产指导,实时收集生产实绩,统计必要的消耗,为MES 系统提供实绩数据。
1 系统结构本系统包含三大系统:电炉应用系统、精炼应用系统、连模铸应用系统。
其中电炉L2计算机系统:覆盖4个电炉的计算机系统;精炼L2计算机系统:覆盖5个LF炉、1个AOD炉、1个VD炉、1个VOD炉的计算机系统;连模铸L2计算机系统:覆盖1台连铸机本体、1套模铸工位的计算机系统。
1.1 系统构成特点为了系统的先进可靠,同时尽可能地降低、节约成本,本系统采用的是基于PC和PC Server的CLIENT/SERVER体系结构。
DCS系统在冶金行业中的应用及其关键技术
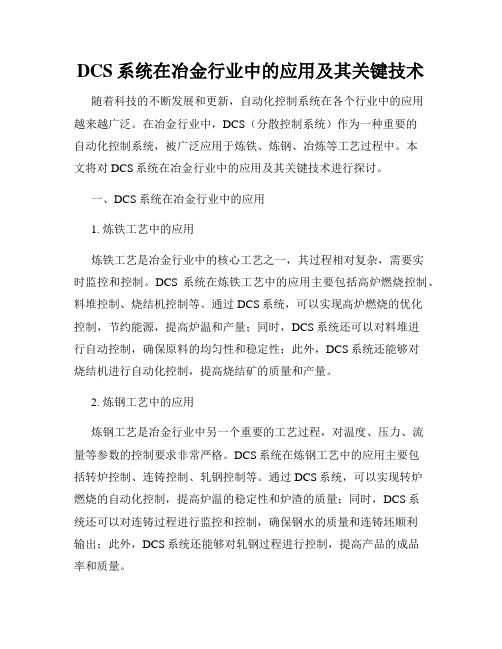
DCS系统在冶金行业中的应用及其关键技术随着科技的不断发展和更新,自动化控制系统在各个行业中的应用越来越广泛。
在冶金行业中,DCS(分散控制系统)作为一种重要的自动化控制系统,被广泛应用于炼铁、炼钢、冶炼等工艺过程中。
本文将对DCS系统在冶金行业中的应用及其关键技术进行探讨。
一、DCS系统在冶金行业中的应用1. 炼铁工艺中的应用炼铁工艺是冶金行业中的核心工艺之一,其过程相对复杂,需要实时监控和控制。
DCS系统在炼铁工艺中的应用主要包括高炉燃烧控制、料堆控制、烧结机控制等。
通过DCS系统,可以实现高炉燃烧的优化控制,节约能源,提高炉温和产量;同时,DCS系统还可以对料堆进行自动控制,确保原料的均匀性和稳定性;此外,DCS系统还能够对烧结机进行自动化控制,提高烧结矿的质量和产量。
2. 炼钢工艺中的应用炼钢工艺是冶金行业中另一个重要的工艺过程,对温度、压力、流量等参数的控制要求非常严格。
DCS系统在炼钢工艺中的应用主要包括转炉控制、连铸控制、轧钢控制等。
通过DCS系统,可以实现转炉燃烧的自动化控制,提高炉温的稳定性和炉渣的质量;同时,DCS系统还可以对连铸过程进行监控和控制,确保钢水的质量和连铸坯顺利输出;此外,DCS系统还能够对轧钢过程进行控制,提高产品的成品率和质量。
3. 冶炼工艺中的应用冶炼工艺是冶金行业中的另一个重要环节,其过程涉及到多个工序和设备的协同运行。
DCS系统在冶炼工艺中的应用主要包括矿石破碎、矿石浮选、冶炼反应、尾渣处理等。
通过DCS系统,可以对矿石破碎过程进行监控和控制,确保矿石的粒度和质量符合冶炼工艺要求;同时,DCS系统还可以对矿石浮选过程进行自动控制,提高选矿的效率和回收率;此外,DCS系统还能够对冶炼反应进行实时监控,确保反应的稳定性和产品质量;最后,DCS系统还能够对尾渣处理过程进行控制,减少环境污染。
二、DCS系统在冶金行业中的关键技术1. 数据采集和处理技术DCS系统需要采集大量的数据,并对数据进行实时处理和分析。
莱钢5#方坯连铸机自动控制系统的设计和实现

Abs r c : i a e r s n s t e s h me a d c n g r t n o e c n r ls s e o e n . i — ta d b le a t ri i a g t a t Th sp p rp e e t h c e n o f u a i ft — o to y t m ft o 5 s x sr n i t se n Lag n i o h h l c
其 自动化系统配置先进、合理、性能可靠 ,是先进工艺与先进 自 动化技术的完美结合 , 为莱钢年产 10万吨钢做 出了较大的贡献。 O0
22 拉矫 跨 .
2 工 艺过 程
连铸生产是钢铁冶炼企业中的—个承 匕 启下的关键环节 ,它 对钢材最终的质量好坏 , 产品开发都有着举足轻重的作用。 方坯连 铸生产线主要由钢水接受跨、 拉矫跨, 切割出坯跨三大部分组成 。1 【 1
Auo t n r I f l t se t mai Co t Bi c o o a l Ca t r e
W U a -h n , n , AN i YANG i n Zh o c e g LIHo g BI l , Ja ( GagA tmai e t no s e A e, aa 2 10 , hn ) n uo t nS ci f t l raT in, 7 14 C ia o o e
称重传感器 , 感应出的信号经过信号处理器处理后直接传到铸机 公共 P C,并通过 WI L NCC画面在主控室 HMI 上显示出来 。所
过程控制系统在石钢3号方坯连铸机的应用

A PLI P CATI ON OF ROCES P S
C T O YS E ON R L S T M
S UAR Ⅱ E AS E Q EB L T C T R
.
W AN G a — q Xi o i
( t l0k , h i h agI nadSel o ay S iah ag Hee, 50 ) se w rs S ia un o n te C mpn , h i un , b i 0 0 3 e jz r jz 1
年 第 3期
河 北 冶金
HE BEI M E TA L LU R GY
Toa 5 tl1 9 20 0 7, Nu e mb r3
过 程 控 制 系统 在 石 钢 3号 方坯 连 铸 机 的应 用
2 2 硬 件 配 置 .
过 程控 制 系 统 的 目标 是 利 用 先 进 的计 算 机 技 术 、网络通讯 技术 和数 据库 技术实 现控 制 系统 和 管 理 系统 的集成 ,达 到企 业 中信息上 传下 达 ,畅 通无 阻 ,实 现生 产过 程 中的物流 、信息 流 和经 营管 理 的 统 一和 优化 的 目标 。石 钢 3号方坯 连铸 机 在生 产 过
1 5套 P C( L 4台计 算 机 操 作 站 、 2台计 算 机服 务 器 )
以及 远程 I O组成 。整 个过 程监 控系统 底层 为远程 /
IO,负责对 分 布 的设 备 进 行 数据 采 集 及监 控 ;通 /
过 以太 网可 实 现 各 P C 系统 间 的可 靠 通 讯 ,通 过 L
ie z d.
Ke o d :p o e sc n o y tm ;s u e b l t a t r p l a o y W r s r c s o t ls s r e q a i e se ;a p i t n r l c ci
- 1、下载文档前请自行甄别文档内容的完整性,平台不提供额外的编辑、内容补充、找答案等附加服务。
- 2、"仅部分预览"的文档,不可在线预览部分如存在完整性等问题,可反馈申请退款(可完整预览的文档不适用该条件!)。
- 3、如文档侵犯您的权益,请联系客服反馈,我们会尽快为您处理(人工客服工作时间:9:00-18:30)。
典型连铸过程控制计算机系统的实现摘要:随着连铸工艺水平不断发展,对生产控制(结晶器液位,拉速,冷却水流量,切割长度等)的控制精度也越来越高,同时自动化技术和企业整体信息化也越来越趋向于一个整体,连铸过程控制计算机系统正是服务于这样一个大的发展趋势的计算机系统。
一方面它接受管理系统的生产指令,并利用数学模型对实时数据分析计算的结果指导和控制生产;另一方面采集基础电气仪表自动化的数据和信号对物流进行跟踪,并对采集到的生产实绩数据进行归纳。
它同时也是 mes/erp系统与电气仪表基础自动化系统之间的桥梁和纽带,三者紧密结合,实现了生产控制的自动化,也实现了信息技术与现代管理技术相结合。
本文以宝钢集团八一钢铁股份有限公司二炼钢连铸过程控制计算机系统为例,介绍了典型连铸过程控制计算机系统的具体实现。
关键词:l1 l2 l3 连铸过程控制中图分类号:tp273.5 文献标识码:a 文章编号:1672-3791(2012)08(c)-0032-021 系统概述宝钢集团八一钢铁二炼钢连铸过程控制计算机系统覆盖八一钢厂板带工程二炼钢区域的4台垂直弯曲板坯连铸机。
连铸机主要参数为:流数:各1流;切割机:各1台;喷印机:各1台;二冷区:各9个区,16个控制回路。
铸机拉速范围:0.25~2.5m/min;铸机工作拉速:1.0~1.6m/min;板坯厚度:220mm,板坯宽度:750~1600mm;板坯长度:7500~10500mm;板坯最大单重:28.8t/块。
该连铸过程控制计算机服务器硬件配置为2台高性能双路双模块冗余机架式容错服务器,其中一台为在线服务器,一台为备份服务器,磁盘采用阵列形式,采用共享磁盘管理技术,提高磁盘的可靠性,防止数据的丢失,减少系统切换的时间。
数据库数据存放在共享磁盘阵列上,在线服务器和备份服务器共享数据库数据,保证了服务器切换的速度和数据的一致。
服务器部署在l2中心机房,各个连铸电气室和操作室的边缘交换机通过多模光缆连接到l2中心机房的核心交换机,实现连铸过程控制计算机服务器与l1系统以及现场操作终端的网络互联。
现场终端采用工控机、一般场所终端采用商务pc机。
系统软件软件上的配置和使用上,服务器的操作系统采用linux redhat as4服务器数据库使用oracle 10g for linux版本,在终端上,安装oracle的客户端开发及运行环境包,包括forms和reports(开发/运行显示画面和报表),同时安装sql net(实现客户端和数据库服务器的数据交互)。
2 主要应用技术与电气仪表基础自动化的通讯,使用了opc方式,opc是ole process control的缩写,是一种主流的工业控制数据通讯的标准。
目前全世界大多数的知名plc厂家都提供了基于该标准的opc server,任何应用系统只要通过一个opc client软件就可以对plc数据进行读写访问。
通过这种机制,应用系统可以在不更改应用程序的前提下实现与不同的plc厂家的产品通讯。
我们使用的opc client软件是multilink(由宝信软件开发的基础通信中间件),它提供了一系列的api,应用开发人员可以方便的在应用程序中对plc的数据进行读写,实现对基础自动化数据的采集、设定及plc 数据变化后通知启动过程计算机的应用程序的功能,并提供了将plc数据点配置成电文以及查看这些数据点内容的的工具。
与mes(l3)系统以及其他相关系统的通讯使用基于tcp/ip协议socket方式,项目中使用xcom_pcs(由宝信软件开发的基于tcp/ip协议的socket通信中间件)来实现,与multilink类似,它也是提供了一系列简单方便的api(应用编程接口),实现在以太网环境下,基于tcp/ip协议的socket数据通信,同时提供了电文数据类型转换的功能(2进制与ascii码之间的转换,网络字节顺序和本地字节顺序之间的转换),同时也提供了查询通讯线路状态的工具和查询通讯电文内容历史记录的工具。
应用程序的开发,使用c++与pro c,pro c是oracle提供的预编译技术,将内嵌标准sql语句的又混合了c/c++语法的源程序预编译,转换成完全符合c/c++语法的源程序(后缀为.c/.cpp),这样在c++的环境下,就能如同在oracle的存储过程中一样使用标准sql语句方便的与oracle数据库交互,又能享受c++这种相对于oracle的存储过程要更强大而灵活的开发工具的各种优势。
画面的开发使用oracle的froms。
应用程序的运行平台中间件,使用plature 99(由宝信软件开发的运行平台中间件),它实现的功能包括实现各个应用程序之间的相互启动和调度,同时传递参数;在指定时刻启动某个/某些应用进程;定周期的启动某个/某些应用进程;提供管理维护和查看应用程序报警/log历史记录的功能。
3 应用功能关于连铸过程控制计算机系统的应用功能,主要是从mes和分析等系统接受出钢计划,制造命令和,根据出钢计划画面上的生产计划钢种和制造命令,制造标准等数据,并启动内部动态二冷水,切长优化计算模型,同时将计算结果发送到plc控制生产,连铸过程控制计算机系统在生产过程中对基础自动化(l1)上传的各个事件、信号进行跟踪,并将实绩生产实绩数据经过计算,过滤和组织,以连铸处理号作为键字来管理存储在连铸过程控制计算机系统的数据库,同时发送给mes(l3/l4)系统,供日后查阅分析,生成报表。
具体的,应用功能分为:工程数据管理,过程跟踪,过程数据采集,实绩数据生成,数学模型,人机界面几大模块。
系统内部各模块之间数据流及与外部系统关系如图1所示。
3.1 工程数据管理模块该模块主要功能为处理接受mes系统、分析系统及其它过程控制计算机系统发送来的信息,包括mes根据合同制定的计划类信息接收(铸造计划,炉次命令,板坯命令)、根据工艺需求制定的质量标准类信息接收(作业标准、制造标准)、其他工序作业实绩类接收(前工序实绩、分析信息,钢包信息等)和运转状况信息。
3.2 过程跟踪模块该模块主要功能为对于连铸从钢包到达回转台开始到钢包吊走的各作业状况进行跟踪。
进行作业状态变更的检查和接受、各作业时间的计算、同时收集浇铸过程中的各种浇铸信息。
连铸跟踪的主要作业点包括:钢包到达、钢包浇铸开始、铸流铸造开始、钢包浇铸结束、钢包吊走,铸流铸造开始、铸流铸造结束,切割开始、切割结束、喷印信号,去毛刺信号等。
3.3 过程数据采集模块该模块主要功能为周期性的收集连铸铸造过程数据,主要包括td钢水重量,ld钢水重量、铸造长、铸造速度,结晶器上端宽度、结晶器下端宽度、结晶器液面位置、结晶器冷却水温度、入出口温差,结晶器振动频率、振幅,结晶器冷却水流量、二次冷却水流量、二次冷却水压力,辊缝信息等。
3.4 实绩数据生成模块该模块主要功能为依据生产指令、过程采集及过程跟踪信息,生成板坯生产实绩、炉次生产实绩,把过程跟踪模块采集到的各个关键时刻和过程数据采集到的重要数据如重量,温度,长度等信息对应到具体的炉次和板坯上。
3.5 数学模型主要包含了动态二冷水,切长优化,品质异常判定三个主要数学模型。
3.5.1 动态二冷水模型连铸二冷区目标温度控制是通过对整个连铸过程铸坯表面温度的测定,由计算机控制沿拉坯方向的铸坯表面温度分布,使之符合设定的目标表面温度曲线来实现。
通过铸坯凝固传热模型计算各二冷段表面温度,与目标温度相比较。
当两者有偏差时,及时调整该冷却区的冷却强度,使铸坯表面温度与目标温度尽量靠近,实现二冷区目标温度的控制。
根据二冷模型原理,以钢水进入结晶器为其生命起点,以其根据铸造长对应的板坯出最后一个冷却段为其生命终点。
在此过程中,全过程定周期跟踪其接受的冷却水量等数据,实时计算其凝固状态,并推定出其各相区域的分布情况。
根据各铸片的计算结果,综合推定整个铸机内板坯的凝固状态,动态推定出凝固终点位置、两相区和液相区的分布情况。
3.5.2 切长优化模型切长优化模型以满足合同需求为目标,并兼顾板坯收得率为原则,针对浇铸异常点进行优化。
参照板坯制造命令中的切割长度及其上、下限为基准,同时考虑品质异常部位(插铁板、异钢种交接,中间包交换、切尾)计算出钢水不足、钢水多余并根据钢水量的多少应用相关的优化策略进行优化计算,以实现预定板坯的消化,同时争取较高的收得率。
钢包钢水浇注开始,参照制造命令,生成该炉次的切割预定,在浇铸过程中,跟踪发生的异常事件,考虑影响的区域(工艺规定),进行优化计算。
在板坯切割开始时,根据切割的实际情况进行切割优化的再计算。
并把优化结果通过人机界面展现给用户。
优化过程主要包括:切割缝隙的考虑,采样的考虑,异常段的优化,板坯在钢水不足和钢水多余情况下的优化。
3.5.3 品质异常判定模型该模型包含在线判定部分和分析部分2个模块。
在线判定:主要功能是:通过采集炼钢、连铸过程中对连铸的浇铸、板坯质量有可能产生影响的事件进行跟踪记录,并根据内建的模型进行分析,对连铸的质量给出一定的判断结论,从而达到连铸从上台到浇注成材的整个过程中对连铸浇注进行质量判断、提供操作指导,并在板坯产出时,对板坯的整体质量进行判断、提供操作指导。
并将以上数据与结论很好地展示给工艺人员。
离线分析:具备很好的开发性,提供足够的离线学习功能和在线扩展功能。
工艺人员不但能够对系统定义的异常进行调整,还能够利用模型提供的离线分析工具对历史数据进行分析,从而根据分析发现并定义新的约束条件,并将其加入到在线判定系统中实现自动判定。
3.6 人机界面人机界面主要提供了计划管理、设备管理、操作监视、模型、实绩、报警和提示信息等画面。
每个画面有共通的部分,主要是画面菜单、画面名称、报警或提示信息、工具栏功能键、班别、组别、当前时间。
各个操作室和控制室的终端画面的权限通过用户名和角色统一认证管理,不同的角色拥有的权限不一样,看到的画面数量也不一样,对同一幅画面的操作权限也不一样。
不同的用户可以拥有一个或者多个的角色。
4 结语通过实施了连铸过程控制系统,八钢二炼钢连铸区域实现了连铸生产过程的全程自动控制和对生产数据的全程监视,管理层亦能了解到现场的实时生产情况,并且所有生产都遵照合同和计划统一调度进行生产,从而提高连铸生产的自动化程度,降低生产人员的作业率,提高了生产效率。
通过模型的应用,提高和稳定了铸坯的质量,并提高了铸坯的成材率。
参考文献[1] 宝信八一钢铁二炼钢连铸过程计算机系统基本设计书.[2] 宝信自动化研究所连铸模型设计书.。