8-热加工过程的模拟与仿真
Aspenplus浙大吴嘉老师热过程单元的仿真设计二PPT教学课件
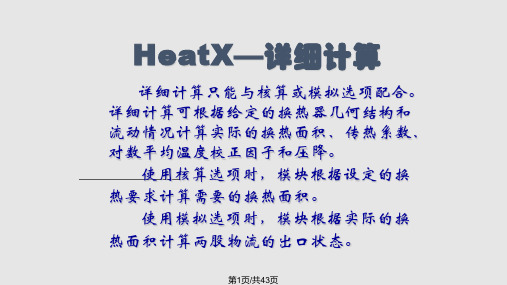
HeatX—— U-膜系数法
(2)
第7页/共43页
HeatX—几何结构
详细计算时需输入换热器的几何 结构参数。从数据浏览器左侧的目录 树中选择几何(Geometry)项目,然后在 右侧的壳程(Shell)、管程(Tubes)、管翅 (Tube fins) 、 挡 板 (Baffles) 和 管 嘴 (Nozzles)表单中输入相应的数据。
排列模式 Pattern 中心距 Pitch
材料 Material 导热系数 Conductivity
第15页/共43页
HeatX——管程参数(2)
第16页/共43页
HeatX——管程参数(3)
管程参数还有管尺寸(Tube size), 可用两种方式输入:
实际尺寸 Actual 内径 Inner diameter 外径 Outer diameter 厚度 Tube thickness
第37页/共43页
HeatX——压降/速度(2)
第38页/共43页
HeatX —— 分区
分区表单给出了换热器内根据冷、热 流体相态对传热面积分区计算的情况,包 括各区域的热流体温度、冷流体温度、对 数平均温差、传热系数、热负荷和传热面 积信息。我们可根据此信息分析换热方案 是否合理以及改进设计方案的方向。
HeatX—详细计算
详细计算只能与核算或模拟选项配合。 详细计算可根据给定的换热器几何结构和 流动情况计算实际的换热面积、传热系数、 对数平均温度校正因子和压降。
使用核算选项时,模块根据设定的换 热要求计算需要的换热面积。
使用模拟选项时,模块根据实际的换 热面积计算两股物流的出口状态。
第1页/共43页
第41页/共43页
8-热加工过程的模拟与仿真

常用软件
• 经多年研究开发,已经形成一批热加工工艺商业软件
• 主要有ProCast、Simulor、SolDIA、SolSIAR、AFS Solidification System3D(铸造)、ViewCAST、EForm、 AutoForge、SuperForge (体积塑性成形)、DYNA3D、 PAM-Stamp、ANSYS (板料塑性成形)、ABAQUS 等。
3、宏观工艺ቤተ መጻሕፍቲ ባይዱ拟研究方向
1) 单一分散→耦合集成 模拟功能由单一的温度场、流场、应力/应变场、组织场
模拟进入耦合集成阶段。包括:流场←→温度场;温度场 ←→应力/应变场;温度场←→组织场;应力/应变场←→组 织场等之间的耦合,以真实模拟复杂的实际热加工过程。
2) 共性、通用→专用、特性 由于建立在温度场、流场、应力/应变场数值模拟基础上的 常规热加工,特别是铸造、冲压、铸造工艺模拟技术的日益 成熟及商业化软件的不断出现,研究工作已由共性通用问题 转向难度更大的专用特性问题:
铸造工艺 设计
去应力及均
钢水冶炼
浇注
打箱
匀化热处理
组织及力学 性能检测
精加工
差硬热处理
无损检测
粗加工
铸钢支承辊生产流程图
铸件和铸型的 几何造型
对铸件作网格剖分,离 散到所需的单元尺寸,
修正表面形状
求解能量、动量等 控制方程及缺陷预 测的各种判据函数
计算结果显示与分析
边界条件与初始条件
金属与铸型材料热物 性参数数据的输入
缩孔位置模拟验 证初次工艺设计 思想是否合理
缩孔深964mm
充型凝固后产生的缩孔
2.2 根据凝固过初次模拟结果确定铸型设计方案
方案一:下辊颈金 属型直径2500mm. 方案二:下辊颈金 属型直径2167mm.
Aspenplus浙大吴嘉老师热过程单元的仿真设计一PPT教学课件

HeatX —— 概况 (2)
第50页/共56页
HeatX——换热器详情
(2)
第2页/共56页
Heater 加热器模型
Heater 模型用于模拟以下单元, 改变单股物流的温度、压力和相态: 1. 加热器 2. 冷却器 3. 阀门(仅改变压力,不涉及阻力) 4. 泵(仅改变压力,不涉及功率) 5. 压缩机(仅改变压力,不涉及功率)
第3页/共56页
Heater 加热器模型(2)
results),其下包括五张表单:
概况
Summary
衡算
Balance
换热器详情 Exchanger details
压降/速度 Pre drop/velocities
分区
Zones
第48页/共56页
HeatX —— 概况
概况表单给出了冷、热物流的 进、出口温度、压力、蒸汽分率 (Vapor fraction),以及换热器的热负 荷(Heat duty)。
第13页/共56页
Case Study— 案例研究
(2)
第14页/共56页
Case Study— 参数定义
首先在改变(Vary)表单中定义不 同案例中需要改变的变量:
使用变量序号(Variable number)下拉框中 的新建(new)选项增添新的变量;
使用调节变量(Manipulated variable)栏中 的一组下拉框设定每一个变量的定义。
(Cold stream outlet temperature)
有 7. 冷物流出口温升
13
(Cold stream outlet temperature increase)
个
8. 冷物流出口温差 (Cold stream outlet temperature approach)
CAPD基础第六讲 热过程单元的仿真设计
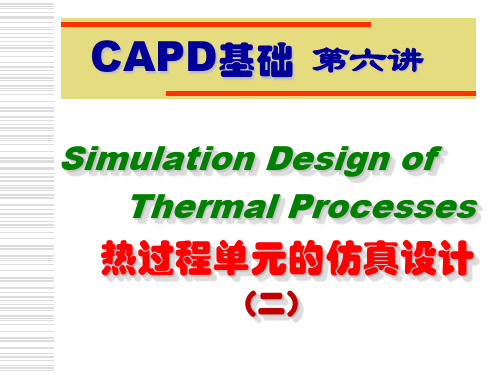
• 分区
Zones
HeatX —— 概况
概况表单给出了冷、热物流的 进、出口温度、压力、蒸汽分率 (Vapor fraction),以及换热器的热负 荷(Heat duty)。
HeatX —— 概况 (2)
HeatX——换热器详情
换热器详情表单给出了需要的换热器 面积(Required exchanger area) 、实际的换 热器面积(Actual exchanger area) 、清洁 (Clean)和结垢(Dirty)条件下的平均传热系 数(Avg. heat transfer coefficient)、校正后 的对数平均温差(LMTD corrected) 、热效 率 (Thermal effectiveness) 和 传 热 单 元 数 (Number of transfer units)等有用的信息。
HeatX——换热器详情(2)
HeatX——压降/速度
压降/速度表单给出了流道压降 (Exchanger Pressure drop)、管嘴压降和总 压 降 ; 壳 程 错 流 (Crossflow) 和 挡 板 窗 口 (Windows) 处 的 最 大 流 速 及 雷 诺 数 (Reynolds No.);管程的最大流速及雷诺数 等有用的信息,我们可以根据这些信息调 整管程数,挡板数目和切割分率,以及管 嘴尺寸。
CAPD基础 第六讲
Simulation Design of Thermal Processes
热过程单元的仿真设计
(二)
HeatX—详细计算
详细计算只能与核算或模拟选项配合。 详细计算可根据给定的换热器几何结构和 流动情况计算实际的换热面积、传热系数、 对数平均温度校正因子和压降。
使用核算选项时,模块根据设定的 换热要求计算需要的换热面积。
材料热加工数值模拟

内容提要:本文首先论述了材料热加工工艺模拟研究的重大意义;回顾、分析了国内外热加工工艺模拟的研究历程和技术发展趋势和方向;提出了我国在该领域开展研究与应用工作的建议。
当前,金属材料仍是应用范围最为广泛的机械工程材料,材料热加工(包括铸造、锻压、焊接、热处理等)是机械制造业重要的加工工序,也是材料与制造两大行业的交叉和接口技术。
材料经热加工才能成为零件或毛坯,它不仅使材料获得一定的形状、尺寸,更重要的是赋予材料最终的成份、组织与性能。
由于热加工兼有成形和改性两个功能,因而与冷加工及系统的材料制备相比,其过程质量控制具有更大的难度。
因此,对材料热加工过程进行工艺模拟进而优化工艺设计,具有更为迫切的需求。
近二十多年来,材料热加工工艺模拟技术得到迅猛发展,成为该领域最为活跃的研究热点及技术前沿。
一、引言1.1 使金属材料热加工由"技艺"走向"科学",彻底改变热加工的落后面貌金属材料热加工过程是极其复杂的高温、动态、瞬时过程,难以直接观察。
在这个过程中,材料经液态流动充型、凝固结晶、固态流动变形、相变、再结晶和重结晶等多种微观组织变化及缺陷的产生与消失等一系列复杂的物理、化学、冶金变化而最后成为毛坯或构件。
我们必须控制这个过程使材料的成分、组织、性能最后处于最佳状态,必须使缺陷减到最小或将它驱赶到危害最小的地方去。
但这一切都不能直接观察到,间接测试也十分困难。
长期以来,基础学科的理论知识难以定量指导材料加工过程,材料热加工工艺设计只能建立在"经验"基础上。
近年来,随着试验技术及计算机技术的发展和材料成形理论的深化,材料成形过程工艺设计方法正在发生着质的改变。
材料热加工工艺模拟技术就是在材料热加工理论指导下,通过数值模拟和物理模拟,在试验室动态仿真材料的热加工过程,预测实际工艺条件下材料的最后组织、性能和质量,进而实现热加工工艺的优化设计。
它将使材料热加工沿此方向由"技艺"走向"科学",并为实现虚拟制造迈出第一步,使机械制造业的技术水平产生质的飞跃。
5 热加工过程模拟问题

因此,通常可以假设,对于同一种材 料,在变形条件相同的条件下,等效 应力与等效应变曲线是单一的,称为 单一曲线假设。由此假设,就可以采 用最简单的实验方法来确定材料的等 效应力与等效应变曲线。
常用的实验方法有以下三种: (1)单向拉伸实验 (2)单向压缩实验 (3)平面应变压缩实验
(1)单向拉伸实验
2
2
1 , 1
采用圆柱体单向拉伸实验所得到的应力— 应变曲线就是等效应力—等效应变曲线。 但是,该关系仅适合于产生缩颈之前,产 生缩颈时,变形区内的应力状态已变为三 向应力状态,此时:
2 0、 3 0
1
(2)单向压缩实验 对于圆柱体单向压缩时的应力状态为: σ3 ,σ1=σ2=0; 和应变状态为: ε3=-(ε1+ε2), ε1=ε2=- ε3 /2。
-10 -15 0.04 0.24 0.42 0.62 0.83 轧制时间子步长
第一道实际尺寸
第一道模拟尺寸
第一道实际尺寸
第一道模拟尺寸
第二道实际尺寸
第二道模拟尺寸
第二道实际尺寸
第二道模拟尺寸
第三道实际尺寸 图 7.22 实际轧制中的轧件取样尺寸
第三道模拟尺寸 图 7.23 模拟计算所得的轧件尺寸
0.24
0.42
0.62
0.83
0.24
轧制时间子步长
0.42 0.62 0.83 轧制时间子步长
第三道轧制时压力和力矩的变化
800 400 0 -400 -800 0.04 0.24 0.42 0.62 0.83 轧制时间子步长 上辊 下辊
15 10
轧制力矩M/KN.m
轧制压力/KN
5 0 -5 上辊 下辊
热加工过程数值模拟仿真大赛
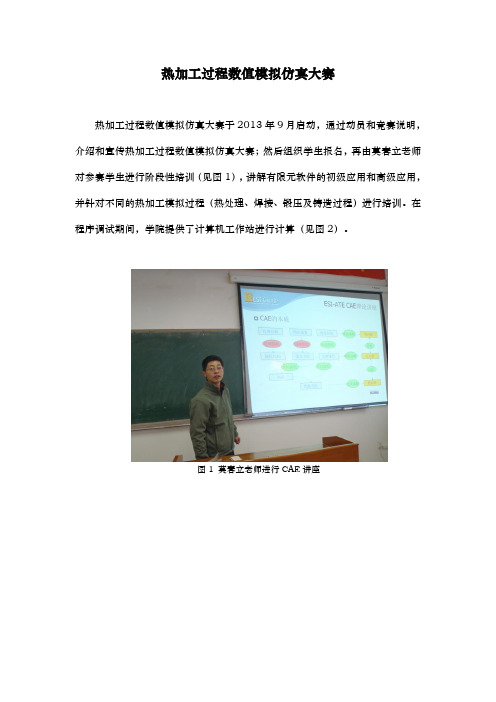
热加工过程数值模拟仿真大赛
热加工过程数值模拟仿真大赛于2013年9月启动,通过动员和竞赛说明,介绍和宣传热加工过程数值模拟仿真大赛;然后组织学生报名,再由莫春立老师对参赛学生进行阶段性培训(见图1),讲解有限元软件的初级应用和高级应用,并针对不同的热加工模拟过程(热处理、焊接、锻压及铸造过程)进行培训。
在程序调试期间,学院提供了计算机工作站进行计算(见图2)。
图1 莫春立老师进行CAE讲座
(a)工作站7500
(b)移动工作站4600 图2计算机仿真工作站
图3部分竞赛成果
历时近四个月,大赛于12月27日进行了汇报评比。
由沙桂英、国旭明、
徐前刚、王继杰教授和莫春立、王艳晶、黄震威副教授以及季书记组成的评委对参赛各队的模拟结果进行了评审,评出一等奖二项,二等奖三项,三等奖三项。
部分竞赛成果见图3。
此次模拟大赛参赛的主要是全校大二以上的学生和研究生。
通过热处理、焊接、锻压及铸造等零件的热加工过程进行数值模拟仿真,提高了学生的计算机应用能力,同时,在模拟过程中学生对热加工工艺如焊接、锻造、热处理等工艺有了进一步的理解,对学习专业课程的兴趣大大增加。
通过参加培训、模拟计算与仿真,同学表示收获颇丰,在意识上重视计算机技术的发展,了解了当前计算机数值模拟与仿真技术在国内许多大型企业和国外许多企业得到的广泛的应用,以及具有广阔的应用前景。
在实际专业学习过程中重视相关课程的学习,乐于拥有良好的数值计算基础,为将来毕业后的就业奠定良好的技术基础。
热设计基础知识及flotherm热仿真-PPT

导热介质-导热垫
我公司现有的导热硅胶垫:
对导热垫的性能要求和主要检测项目: 1)导热系数和热阻:热性能满足要求 2)硬度:优先选用硬度较低的材料 3)绝缘性能:要求耐压满足产品需求(一般3KV) 4)阻燃:要求材料阻燃级别达到V1及以上
导热介质-相变导热膜
导热介质-相变导热膜
导热介质-导热垫
热传导
热阻Rja:芯片的热源结(junction)到周围冷却空气(ambient)的总热 阻,乘以其发热量即获得器件温升。
热阻Rjc:芯片的热源结到封装外壳间的热阻,乘以发热量即获得结与壳的温差。
热阻Rjb:芯片的结与PCB板间的热阻,乘以通过单板导热的散热量即获得结 与单板间的温差。
热传导
单层平壁导热
热流量是指单位时间内通过某一给定面积的热量, 单位为W。
导热系数是指在稳定传热条件下,1m厚的材料,两 侧表面的温差为1度(K,°C),在1秒内,通过1平 方米面积传递的热量,单位为瓦/米·度(W/m·K,此 处的K可用°C代替)。它是表征材料导热能力优劣 的物性参数。在30 °C时,空气的导热系数为 0.027 W/m·°C ,因此可以利用空气夹层来绝热, 通常把导热系数小于0.23 W/m·°C 的材料称为 绝热材料。
电子设备冷却方法的选择
✓ 设备内部的散热方法应使发热元器件与被冷却表面或散热器之间有一 条低热阻的传热路径。
✓ 利用金属导热是最基本的传热方法,其热路容易控制。热辐射换热则 需要比较高的温差,且传热路径不容易控制。对流换热需要较大的面 积,在安装密度较高的设备内部难以满足要求。
✓ 大多数小型电子元器件最好采用自然冷却方法。自然对流冷却表面的 热流密度为0.039W/cm2 。有些高温元器件的热流密度可高达 0.078W/cm2 。
- 1、下载文档前请自行甄别文档内容的完整性,平台不提供额外的编辑、内容补充、找答案等附加服务。
- 2、"仅部分预览"的文档,不可在线预览部分如存在完整性等问题,可反馈申请退款(可完整预览的文档不适用该条件!)。
- 3、如文档侵犯您的权益,请联系客服反馈,我们会尽快为您处理(人工客服工作时间:9:00-18:30)。
铸造工艺 设计
打箱
钢水冶炼
浇注
去应力及均 匀化热处理
组织及力学 性能检测
精加工
差硬热处理
无损检测
粗加工
铸钢支承辊生产流程图
铸件和铸型的 几何造型
对铸件作网格剖分,离 散到所需的单元尺寸, 修正表面形状 边界条件与初始条件 求解能量、动量等 控制方程及缺陷预 测的各种判据函数
金属与铸型材料热物 性参数数据的输入
检验 粗加工
精加工
检验
零件
热加工过程是极其复杂的高温、动态、瞬时过程,难以 直接观察。 材料经液态流动充型、凝固结晶、固态流动变形、相变、 再结晶和重结晶等多种微观组织变化及缺陷的产生与消失 等一系列复杂的物理、化学、冶金变化而最后成为毛坯或 构件。要控制这个过程使材料的成分、组织、性能最后处 于最佳状态,必须使缺陷(如缩孔、缩松、热裂等)减到 最小或将它驱赶到危害最小的地方去。但这一切很难直接 观察到,间接测试也十分困难。
;冲压件的回弹;焊接件的变形、冷裂、 热裂;淬火中的 变形等常见缺陷的预防和消除方法的研究。
3) 重视提高数值模拟精度和速度的基础性研究
数值模拟是热加工工艺模拟的重要方法,提高数值模拟 的精度和速度是当前数值模拟的研究热点,为此非常重视在 热加工基础理论、新的数理模型、新的算法、前后处理、精 确的基础数据获得与积累等基础性研究,为此需要多个专业 学科的研究人员通力合作才能有所突破。
美国金属加工先进技术研究中心(NCEMT)在海军资助下,正在 开展并行工程环境下的RP2D(Rational Product/process Design) 技术。将铸造工艺模拟与产品、模具设计和加工结合起来。
(2) 与零件加工制造系统集成 在零件加工制造系统中,工艺模拟作为重要的支撑技术,并 朝着将模拟结果作为系统的过程闭环控制的参数这一方向努力
4) 重视物理模拟及精确测试技术 物理模拟揭示工艺过程本质,得到临界判据,检验、校核 数值模拟结果的有力手段,越来越引起研究工作者的重视。
5)工艺模拟与生产环节集成 在并行环境下,工艺模拟与生产系统其它技术环节实现集 成,成为先进制造系统的重要组成部分。起初,工艺模拟多是 孤立进行的,结果只用于优化工艺设计本身,且多用于单件小 批量毛坯件生产。近年来,已逐步进入大量生产的先进制造系 统中,实现以下三种不同方式的集成。 (1) 与产品、模具CAD/CAE/CAM系统集成
计算结果显示与分析
工艺是 否合理
否 修改工艺设计
是
确定工艺
铸造工艺自然冒口, 从底部到顶 部的顺序凝 固方式
整个工装有9m高,总 重约130吨。
整体铸造工艺装配图
应用计算机模拟技术进行工艺设计 设计冒口 •验证浇注系统设计是否合理 •设计铸型 •确定浇注工艺参数 •确定打箱时间
4. 微观组织模拟
随着铸件宏观凝固模拟技术的进一步完善,人们开始将目光转向 铸件微观组织的模拟。铸件微观组织是决定铸件产品最终质量的一个关 键因素, 它直接影响到铸件的使用性能。
微观组织模拟中的固液界面
纯金属:温度场,因过冷而长大,受潜热释放控制。 如果熔体温度低于平衡凝固温度,熔体产生过冷,如果此时有微 小固相质点或受到压力等干扰,凝固开始,固液界面向液相移动,同 时释放潜热,其移动驱动力是界面的过冷度,凝固界面移动存在固有 的不平衡性,如果一些界面周围过冷度大,生长快,凸起产生,直到 驱动力受到如表面张力、界面动力学效应等其他因素的平衡作用。 合金:浓度场,温度场。受潜热释放及溶质扩散控制 对于小于1的溶质平衡分配系数,溶质被排斥在界面附近,随着枝晶的
2.1 工艺初步设计及其计算机验证
2.1.1 计算机模拟方法设计冒口
模数法 传统冒口设计方法 比例法 补缩液量法 三次方程法
计算机模拟方法 计算无冒口铸 件的凝固过程 计算冒口
冒口计算结果
计算的高径比为1.5的冒口
计算的高径比为1的冒口
选用高径比 为1.5 冒口
2.1.2 浇注系统设计 控制浇注速度 控制浇注时间 控制金属液流入铸型时的线速度
缩孔深964mm
充型凝固后产生的缩孔
2.2 根据凝固过初次模拟结果确定铸型设计方案
方案一:下辊颈金 属型直径2500mm. 方案二:下辊颈金 属型直径2167mm.
初始条件:浇注温度为1540℃,铸型 预热温度为150℃,铸件/铸型的界面 换热系数为1000W/m2 · K,剖分200万
方案一的装配图
传统的热加工工艺设计只能凭经验,采用试错法(Test and Error Method),无法对材料内部宏观、微观结构的 演化进行理想控制。
如三峡水电机组,单机容量达70万千瓦,五大部件(转轮 、蜗壳、主轴、座环、顶盖)的重量和尺寸均居世界第一。其 转轮直径达9.8米,重量达500吨,由于大件形大体重,品种 多,批量小,生产周期长,造价高,迫切要求“一次制造成 功”,一旦报废,在经济和时间上都损失惨重,无法挽回。 总之,热加工工艺经历了从技艺→手册指导→专家系统的 过程,要达到更为完善的水平,必须进行过程/工艺模拟。因 为只有通过模拟仿真,人们才能认识过程的本质,预测并优 化过程的结果,并快速对瞬息万变的市场变化作出设计及工 艺的改变。
单元
(a) t=3745s
(b) t=7320s
(c) t=14471s
方案一温度场模拟结果
缩孔深 1046mm
方案一缩孔模拟结果
(a) t=3625s
(b) t=9013s
(c) t=16237s
方案二温度场模拟结果
缩孔深度 为948mm
优先选用第二种方案 金属型重量减轻20吨
方案二缩孔模拟结果
模拟目的主要是解释事物的本质,根据经验及凝固理论,推 测产生缺陷的位臵,并验证理论的正确性。工艺模拟可以做到 事前预测,防止缺陷发生。由于材料形成过程的复杂性,要真 正做到仿真还是有一定的距离。
2、宏观工艺过程模拟(以支承辊为例)
零件净重26吨
铸件:重40吨 φ1435mm×1615mm×4926 mm
(1) 解决特种热加工工艺模拟及工艺优化问题 铸造专业中的压铸、低压铸造、金属型铸造、实型铸造、 连续铸造、电渣熔铸等;锻压专业中的液压胀形、楔横轧、辊 锻等;焊接专业中的电阻焊、激光焊等。
(2) 解决热加工件的缺陷消除问题 大型铸钢件的缩孔、缩松,模锻件的折叠及冲压件的断
裂、起皱问题,铸件的热裂、气孔、偏析;大型锻件的混晶
热加工工艺过程
模拟与仿真
河南理工大学: 米国发 王狂飞 中科院金属所: 李 殿中 夏立军
报告内容
1. 意义 2. 工艺模拟 3. 工艺模拟研究方向 4. 微观组织模拟 5. 微观研究方向
6. 结论
1、意义
热加工是装备制造业的基础,热加工产品的质量和成本直 接影响着后道工序的产品质量和经济效益。
热加工
•辊身采用厚大金 属型+薄挂砂层 凝固速度最快,定向 向辊身凝固,圆弧处 快速建立起强度 获得柱状晶组织,提 高金属型使用寿命
金属型挂砂工艺
•上辊颈采用 厚的挂砂层
•自然保温冒口
保证顺序凝固
减少人为因 素的影响
2.1.4 铸型材料的选用
铸铁 金属型
铬铁矿砂
砂型
碱性酚醛树脂
锆英粉涂料
保温材料
保温板
发热覆盖剂
浇注系统的作用
铸件型腔
铸件型腔
直浇道 内浇道
直浇道 内浇道
横浇道
横浇道
开放式浇注系统
封闭式浇注系统
平稳充型浇注 系统
v控制充型过程的平稳性 v防止气体和夹杂物卷入金属液中 v提高工艺出品率
浇口杯
浇注系 统包括
直浇道 横浇道 内浇口
2.1.3 铸型设计
顺序凝固原则
•下辊颈采用厚大 金属型+薄挂砂层
计算机模拟预测缩孔位臵
2.4 生产实践
大型铸钢件实际浇注过程
铸钢支承辊毛皮粗检
轧辊的铸造毛坯
铸件整体表面质量完好,粗加
工后探伤内部没有缩孔缺陷
应力场模拟及热裂预测
铸造过程应力模拟的数学模型
•热弹性模型 •热弹塑性模型 •热粘弹塑性模型 •Heyn模型 •Perzyna模型 •内部统一变量模型 •准固相区间的流变学模型
(3) 与零件的安全可靠性能实现集成
美国西北大学在航空重要复杂铸件的研究中,将模拟结果与铸 件的性能,特别是安全可靠性联系起来,开发了铸件的安全临界设 计系统 (Safety critical casting design system) ,用于指导铸 件的损伤容限设计。
常用软件
• 经多年研究开发,已经形成一批热加工工艺商业软件 • 主要有ProCast、Simulor、SolDIA、SolSIAR、AFS Solidification System3D(铸造)、ViewCAST、EForm、 AutoForge、SuperForge (体积塑性成形)、DYNA3D、 PAM-Stamp、ANSYS (板料塑性成形)、ABAQUS 等。
模拟的初始条件:浇注 温度为 1540℃,铸型预 热 温 度 为 150℃, 剖 分 网 格数为100万单元。
带浇注系统铸钢支承辊
铸钢支承辊组装图
(a)t=2s
(c)t=565
(a)t=3s
流场模拟结果
2. 温度场模拟(计算机验证冒口设计是否合理)
(a)
(b)
(c)
(d)
温度场模拟结果
缩孔位臵模拟验 证初次工艺设计 思想是否合理
(b) t=13.5h
第一次浇注工艺的轴向应力模拟结果
两种工艺方 案的最大应 力相同,但 改进方案作 用时间短
(a) t=5h
(b) t=6.8h
改进工艺方案的轴向应力模拟结果
第一次浇注 工艺的热裂 倾向是改进 工艺的2.5倍