铸造过程温度场的数值模拟
连铸过程原理及数值模拟

连铸过程原理及数值模拟连铸是一种重要的金属成形工艺,广泛应用于钢铁、铝合金等金属材料的生产和加工中。
连铸过程原理及数值模拟是研究连铸工艺的关键内容,通过对连铸过程的原理分析和数值模拟,可以优化连铸工艺参数,提高产品质量和生产效率。
连铸过程是将熔融金属直接注入到连续运动的铸坯中,通过冷却和凝固过程,将熔融金属转化为固态铸坯。
连铸的基本原理是利用连续运动的铸坯带走热量,使熔融金属迅速凝固,形成连续的固态铸坯。
在连铸过程中,主要包括液相区、液固两相区和固相区三个区域。
在液相区,熔融金属通过连续浇注,填充到铸坯的空腔中。
熔融金属的温度高于固相线,处于液态状态。
随着熔融金属的注入,液相区的长度逐渐增加。
在液固两相区,熔融金属和正在凝固的铸坯同时存在。
由于熔融金属的温度高于固相线,所以熔融金属仍然保持液态。
而铸坯由于受到液相的热量传递,开始逐渐凝固。
在这个区域中,液相区的长度逐渐减小,凝固铸坯的长度逐渐增加。
在固相区,整个铸坯都已经完全凝固。
熔融金属已经完全转化为固态,形成连续的固态铸坯。
在这个区域中,液相区的长度为零,凝固铸坯的长度为整个连铸过程的长度。
为了研究连铸过程的细节和优化连铸工艺参数,数值模拟成为一种重要的方法。
数值模拟是通过数学模型和计算机仿真技术,对连铸过程进行模拟和分析。
数值模拟可以准确地计算连铸过程中的温度场、流场和凝固结构等关键参数,为工艺优化提供科学依据。
在连铸过程的数值模拟中,需要考虑多个物理过程的相互作用。
首先是流体力学过程,包括熔融金属的流动和铸坯带走热量的过程。
其次是热传导过程,包括熔融金属的冷却和凝固过程。
最后是凝固结构演化过程,包括铸坯的晶粒生长和偏析等现象。
为了建立连铸过程的数值模型,需要考虑材料的物理性质、流体力学和热传导方程等方面的参数。
同时,还需要考虑边界条件和初始条件等参数。
通过数值模拟,可以预测连铸过程中的温度分布、流速分布和凝固结构等重要参数,为工艺优化提供指导。
金属型铸造温度场的有限元数值模拟及确定热物理参数的_逆方法_
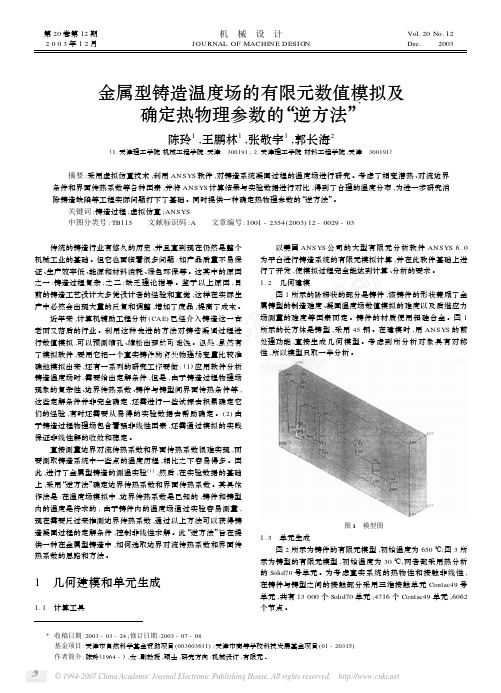
金属型铸造温度场的有限元数值模拟及确定热物理参数的“逆方法”Ξ陈玲1,王鹏林1,张敬宇1,郭长海2(1.天津理工学院机械工程学院,天津 300191;2.天津理工学院材料工程学院,天津 300191)摘要:采用虚拟仿真技术,利用ANSYS软件,对铸造系统凝固过程的温度场进行研究。
考虑了相变潜热、对流边界条件和界面传热系数等各种因素,并将ANSYS计算结果与实验数据进行对比,得到了合理的温度分布,为进一步研究消除铸造缺陷等工程实际问题打下了基础。
同时提供一种确定热物理参数的“逆方法”。
关键词:铸造过程;虚拟仿真;ANSYS中图分类号:TB115 文献标识码:A 文章编号:1001-2354(2003)12-0029-03 传统的铸造行业有悠久的历史,并且直到现在仍然是整个机械工业的基础。
但它也面临着很多问题:如产品质量不易保证、生产效率低、能源和材料消耗、绿色环保等。
这其中的原因之一:铸造过程复杂;之二:缺乏理论指导。
鉴于以上原因,目前的铸造工艺设计大多凭设计者的经验和直觉,这样在实际生产中必然会出现大量的反复和调整,增加了废品,提高了成本。
近年来,计算机辅助工程分析(CAE)已经介入铸造这一古老而又落后的行业。
利用这种先进的方法对铸造凝固过程进行数值模拟,可以预测缩孔、缩松出现的可能性。
但是,虽然有了模拟软件,要用它把一个真实铸件的有关物理场变量比较准确地模拟出来,还有一系列的研究工作要做:(1)应用软件分析铸造温度场时,需要给出定解条件,但是,由于铸造过程物理场现象的复杂性、边界传热系数、铸件与铸型间界面传热条件等,这些定解条件并非完全确定,还需进行一些试探去积累确定它们的经验,有时还需要从易得的实验数据去帮助确定。
(2)由于铸造过程物理场包含着强非线性因素,还需通过模拟的实践保证非线性解的收敛和稳定。
直接测量边界对流传热系数和界面传热系数很难实现,而要测取铸造系统中一些点的温度历程,相比之下容易得多。
铸件凝固过程温度场的数值模拟
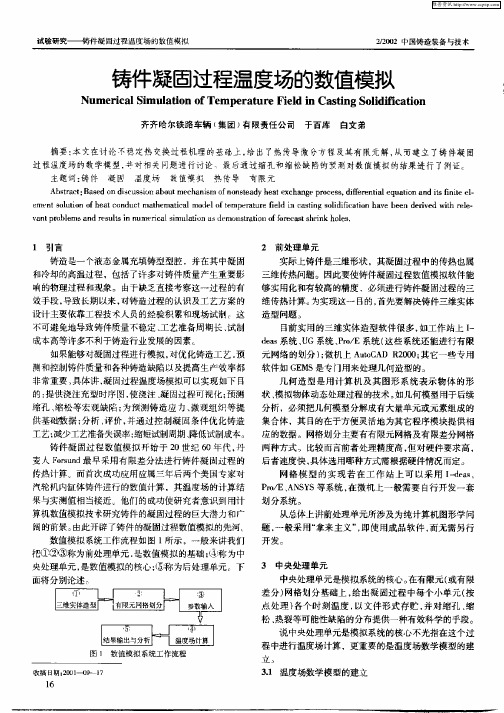
3 中央处 理 单元
从总体上讲前处理单拿来 主义” 即使用成品软件 , , 而无需另行
开 发。
中央处理单元是模拟系统 的核心。 在有限元 ( 或有限 差分) 网格划分基础上 , 给出凝 固过程 中每个小单元 ( 按
点处理 ) 各个时刻温度 , 以文件形式存贮 , 并对缩孔 、 缩
实际上铸件是三维形状 ,其凝固过程中的传热也属
三维传热问题 。因此要使铸件凝固过程数值模拟软件能
够实用化和有较高的精度 ,必须进行铸件凝固过程 的三 维传热计算 。 为实现这一 目的, 首先要解决铸件三维实体
造 型问题 。
目 前实用的三维实体造型软件很多 , 如工作站上 I — da 系统 、G系统、r E系统 ( es U Po / 这些系统还能进行有限
状、 模拟物体动态处理过程 的技术。 如几何模型用于后续
缩孔 、 缩松等宏观缺陷 ; 为预测铸造应力 、 微观组织等提 分析,必须把几何模型分解成有大量单元或元素组成的 供基础数据 ; 分析 、 评价 , 并通过控制凝固条件优化铸造 集合体 ,其 目的在于方便灵活地为其它程序模块提供相 工艺; 减少工艺准备失误率; 缩短试制周期 、 降低试制成本。 应的数据 。网格划分主要有有 限元网格及有限差分网格 铸件凝 固过程数值模拟 开始于 2 0世纪 6 年代 , o 丹 两种方式 比较而言前者处理精度高 , 但对硬件要求高, 麦人 Fr n 最早采用有 限差分法进行铸件凝 固过程 的 os d u 后者速度快 , 具体选用哪种方式需根据硬件情况而定 。 传热计算。而首次成功应用应属 三年后两个美国专家对 网格 模型 的实现 若在 工作 站上可 以采用 Ida 、 - es 汽轮机内缸体铸件进行的数值计算 ,其温度场的计算结 PoE A S S等系统 , r 、N Y / 在微机上一般需要 白行开发一套 果与实测值相当接近。他们 的成功使研究者意识到用计 划 分系统 。 算机数值模拟技术研究铸件的凝固过程的巨大潜力和广 阔的前景。 由此开辟了铸件的凝固过程数值模拟的先河。 数值模拟系统工作流程如图 1 所示 ,一般来讲我们 把①②⑧称为前处理单元 , 是数值模 拟的基础 ; ④称 为中 央处理单元 , 是数值模拟的核心 ; ⑤称为后处理单元 下 面将 分别论 述 ÷
基于ANSYS的铝合金铸件凝固过程温度场的数值模拟

中图分 类 号 : G 4 2 1 文献标 识码 : 文章 编号 : 0 6 9 5 ( 0 8) 4 4 T 1 6. : A; 1 0— 6 820 0—
固 过程 的温 度场 分 布进行 了数值模 拟 。 1 计 算 温度 场 的数 理模 型 实 验 所 用 材 料 为 A 一 %C l4 u合 金 ,由高 纯 度 A l ( 99 % ) 电 解 C ( 99 % ) 电 阻 炉 中 的石 墨 坩 9 .9 和 u 9. 9 在 埚里 熔炼 。采用 砂 型铸 造 。合 金 熔 体 的浇 注 温度 为 9 0C, 温 为 2 ℃。 为使 铸件 在 长 度方 向上 快 速凝 0 ̄ 室 5 固 , 铸 件 的末 端 放置 一冷 铁 。 在
铸造 凝 固过 程数 值 模拟 技术 是 学科 发 展 的前 沿 领域 , 括宏 观模 拟 ( co Mo e ig 和 微 观 模 拟 包 Mar— d ln ) l ( co Mo el g 。其 中 以研 究铸 件凝 固过 程 中温 Mi — d ln ) r i 度场 变化 规律 为基础 内容 的数值 模 拟 ,被许 多学 者 称 之 为铸 件凝 固过程 的宏 观 模拟 。它是 指从 传 热 学 角度 模拟 金属 从 液态 转 变为 固态 的过程 ,在存 在 相
维普资讯
基于 A Y NS S的铝合 金 铸 件 凝 固过 程温 度 场 的数 值 模 拟
Nu e i a i u a i n o m p r t r il eS l i c to o e s m rc l m l to f S Te e a u eF e d i t o i f a i nPr c s n h di o l y Ca t s d OnANS f Al s e Al o Ba YS
CAE-在铸造系统温度场和应力场数值模拟中对ANSYS的理论验证

瞬态温度场分析结果
•左图为 t=1.9s(第10步)时刻的温度云图。 •右图为 t=(第60步)时刻的温度云图。
温度云图
瞬态应力场分析结果
•由数值模拟的分析结果可以看出:初始时铸件温度高,铸型温度低,由于热传导的作用,铸件因温度降低 而收缩,铸型因温度升高而膨胀。 • 系统产生热应力的原因有二个:1.由于铸件左边壁面收缩时受到铸型的阻碍,在环向产生拉应力;2.铸件 热传导使其内部温度分布不均匀,中心温度高,靠壁面温度低,由于收缩程度不同,在铸件外层环向产生 拉应力,内层环向产生压应力。应力云图与理论分析完全吻合。
• 图示系统,由于铸件与铸型的材料不同, 二者之间的界面需采用接触单元分析。
• 在模拟分析中发现,无论采用直接法还是 间接法求解,当界面之间出现裂缝时,接 触单元失效,程序无法继续进行。
• 因此需要探索在这种情况下如何正确使用 ANSYS来求解问题,对其进行理论验证。
本文对ANSYS软件进行理论验证的方法是:
1.考虑较为简单的工况,其结果具有解析解,然后将ANSYS的分析结果 与解析解进行比较;
2.其次考虑稍微复杂一些的工程算例,对其结果可以进行直观判断和定性 分析。
验证的目的在于考察系统物理性质的非线性、接触单元模拟的正确性以 及热-应力耦合场的分析功能。
二、简单算例的理论验证
• 假设有一实心圆柱体A1,外面依次套上两个环形圆柱体A2和A3,该模型可视为厚壁筒, 这是一个二维轴对称问题,根据弹性力学的计算公式可以求出其解析解。
• 采用ANSYS对其进行求解,A1、A3视为铸型,材料为45钢,初始温度30,A2为铸件, 材料为铝合金,初始温度650 。各圆柱体之间的界面采用接触单元。
• 下图为几何模型和有限元模型。
铸件凝固过程中热应力场及热裂的数值模拟研究分析.
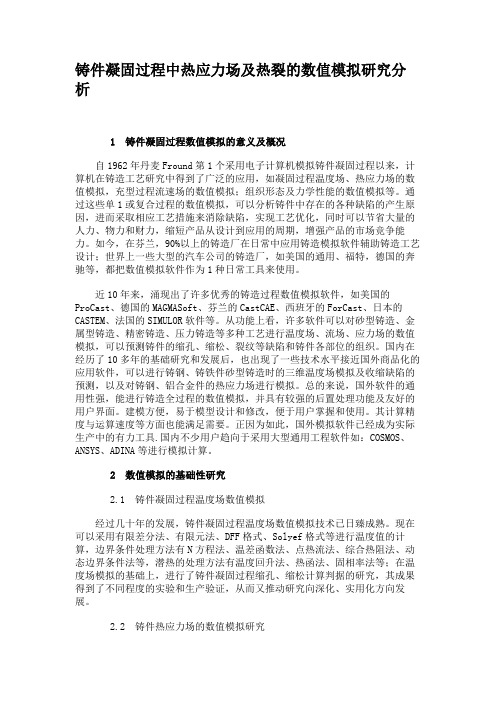
铸件凝固过程中热应力场及热裂的数值模拟研究分析1 铸件凝固过程数值模拟的意义及概况自1962年丹麦Fround第1个采用电子计算机模拟铸件凝固过程以来,计算机在铸造工艺研究中得到了广泛的应用,如凝固过程温度场、热应力场的数值模拟,充型过程流速场的数值模拟;组织形态及力学性能的数值模拟等。
通过这些单1或复合过程的数值模拟,可以分析铸件中存在的各种缺陷的产生原因,进而采取相应工艺措施来消除缺陷,实现工艺优化,同时可以节省大量的人力、物力和财力,缩短产品从设计到应用的周期,增强产品的市场竞争能力。
如今,在芬兰,90%以上的铸造厂在日常中应用铸造模拟软件辅助铸造工艺设计;世界上一些大型的汽车公司的铸造厂,如美国的通用、福特,德国的奔驰等,都把数值模拟软件作为1种日常工具来使用。
近10年来,涌现出了许多优秀的铸造过程数值模拟软件,如美国的ProCast、德国的MAGMASoft、芬兰的CastCAE、西班牙的ForCast、日本的CASTEM、法国的SIMULOR软件等。
从功能上看,许多软件可以对砂型铸造、金属型铸造、精密铸造、压力铸造等多种工艺进行温度场、流场、应力场的数值模拟,可以预测铸件的缩孔、缩松、裂纹等缺陷和铸件各部位的组织。
国内在经历了10多年的基础研究和发展后,也出现了一些技术水平接近国外商品化的应用软件,可以进行铸钢、铸铁件砂型铸造时的三维温度场模拟及收缩缺陷的预测,以及对铸钢、铝合金件的热应力场进行模拟。
总的来说,国外软件的通用性强,能进行铸造全过程的数值模拟,并具有较强的后置处理功能及友好的用户界面。
建模方便,易于模型设计和修改,便于用户掌握和使用。
其计算精度与运算速度等方面也能满足需要。
正因为如此,国外模拟软件已经成为实际生产中的有力工具.国内不少用户趋向于采用大型通用工程软件如:COSMOS、ANSYS、ADINA等进行模拟计算。
2 数值模拟的基础性研究2.1 铸件凝固过程温度场数值模拟经过几十年的发展,铸件凝固过程温度场数值模拟技术已日臻成熟。
CAE-铸造温度场数值模拟
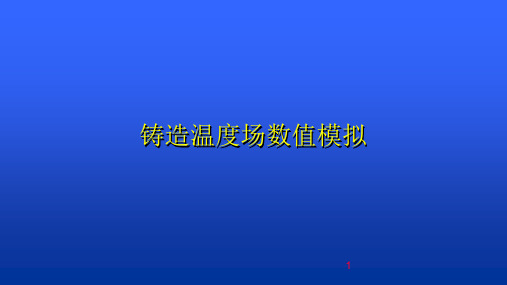
几何模型
几何模型图 4
模型描述
• 模型化过程中的技术难点 – 接触单元在瞬态非线性热应力耦合场中的使用
• 本模型特点:三维结构 • 采用的ANSYS单元:
Solid70和CONTAC49单元 • 材料:铸件(铝合金) 、铸型(45号钢) • 采用的ANSYS功能:前后处理、ANSYS参数语言求解
• 由于时间的关系,对于应力场的研究没有进行。
19
铸造温度场数值模拟
1
问题描述
• 工程背景 铸造系统凝固过程中耦合热应力的数值模拟已经成
为先进铸造工艺设计必不可少的重要部分,而有限元的 模拟结果与真实铸造凝固过程的逼近程度,直接影响模 拟软件的实际使用。利用ANSYS有限元软件,采用不同的 边界条件,更准确的模拟了瞬态非线性温度场,并采用 界面单元,模拟界面传热情况,并进一步进行耦合热应 力全过程的有限元模拟。
2
研究目的
1.应用软件分析铸造温度场和应力应变场时,需要给 出定解条件,但是由于铸造过程物理场现象的复杂性,有 些定解条件并非完全明确,如边界传热的系数、铸型与铸 件间界面传热条件等,需要进行一些试探去积累确定它们 的经验,有时还需要用易得的实验数据去帮助确定。
2.由于铸造过程物理现象的复杂性,使每一种物理量 的分析模拟的数学模型都包含着强非线性因素,怎样控制 解的过程以保证非线性解的收敛和稳定,就需要通过分析 模拟的实践去积累经验。
数值计算模拟结果与实验结果的比较
15
修改参数后的曲线与实验曲线比较
16
温度场动画
17
结果分析
• 结果分析
实践证明,接触界面传热系数的取值严重地影响着 热传导的过程。对不同的接触界面采取不同的界面传热 系数值是必要的。
离心铸造过程温度场和应力场的数值模拟

】巴
京
科
技^
孝
学
报
ⅦL28Supplt
竺!!!!
!!::型!!!:!兰!翌:!兰!:!::型竺型!!型:E
竺!竺
离心铸造过程温度场和应力场的数值模拟
刘利刚1’
杨庆祥‘’
李强1’
秦英方2’
袁乃博2’
张军田2’
I)#m^'##H#5IH}‰-《#"#M*#¥{H}¥^#%女女m日*∞04 21÷*女m¥en■##Hmom.目R
on
the finite element method(FEM)were
simulated.Firstly,the pre—simulation of the temperature field during mold filling and the solidification process
was
simula・
of
of
the variations of
temperature
with time
different Sci Tech
during the solidification of shaped
castings.
Mater,2001,2:157 M
H,Jin J z.Experimental research
l…cmlu"ncIdlimu)afi∞re,oml
曩≥挎{誊■
’■●一
&■日■200‘-os一0I■目日■圳一I¨…
iim目一-fnn#“々¥0
#女∞☆M“Ⅲf1…%HIⅫR’l
t洲删8)
n豪科技丈
学学报
2006年增刊
2温度场预模拟
温度场的模拟采用瞬态分析,单元类型为 PLANE55.模型如图I所示金属型的初始温度为 150℃.高铬钢的浇注温度为1450℃浇完高铬钢 膳1200 s后浇注球墨铸铁层.球铁的浇注温度为