石墨烯的制备
石墨烯常用制备方法

石墨烯常用制备方法石墨烯是一种由碳原子构成的单层二维晶体结构,具有极高的导电性、热导率和机械强度,因此在电子学、光电子学、能源储存等领域具有广泛的应用前景。
本文将介绍石墨烯的常用制备方法。
1. 机械剥离法机械剥离法是最早被发现的石墨烯制备方法之一,也是最简单的方法之一。
该方法的原理是通过机械剥离的方式将石墨材料剥离成单层石墨烯。
具体操作方法是将石墨材料放置在硅基底上,然后用胶带反复粘贴和剥离,直到得到单层石墨烯。
这种方法的优点是简单易行,但是制备的石墨烯质量较差,且产量低。
2. 化学气相沉积法化学气相沉积法是一种通过化学反应在基底上生长石墨烯的方法。
该方法的原理是将石墨材料放置在高温下,使其分解成碳原子,然后在基底上沉积成石墨烯。
具体操作方法是将石墨材料放置在石英管中,然后将氢气和甲烷气体通入管中,使其在高温下反应生成石墨烯。
这种方法的优点是制备的石墨烯质量高,但是设备成本较高。
3. 化学还原法化学还原法是一种通过还原氧化石墨材料制备石墨烯的方法。
该方法的原理是将氧化石墨材料放置在还原剂中,使其还原成石墨烯。
具体操作方法是将氧化石墨材料放置在还原剂中,如氢气、氨气等,然后在高温下反应生成石墨烯。
这种方法的优点是制备的石墨烯质量高,且产量较高,但是还原剂的选择和操作条件对制备的石墨烯质量有很大影响。
4. 液相剥离法液相剥离法是一种通过液相剥离的方式制备石墨烯的方法。
该方法的原理是将石墨材料放置在液体中,然后通过超声波或机械剥离的方式将其剥离成单层石墨烯。
具体操作方法是将石墨材料放置在液体中,如水、有机溶剂等,然后通过超声波或机械剥离的方式将其剥离成单层石墨烯。
这种方法的优点是制备的石墨烯质量高,且操作简单,但是产量较低。
石墨烯的制备方法有很多种,每种方法都有其优缺点。
在实际应用中,需要根据具体需求选择合适的制备方法。
随着石墨烯制备技术的不断发展,相信未来石墨烯的制备方法会越来越多样化,也会越来越成熟。
石墨烯的制备方法

采用粘胶带的方式,胶带采用特殊的3M思高牌胶带。使用镊子 夹取16 cm长的思高牌胶带贴附在高定向热解石墨片表面,轻轻压 实,使胶带和石墨片紧紧贴附,慢慢撕下。胶带表面会粘附有很薄 的一层石墨薄片,然后把胶带的两端对折,使石墨薄片夹在胶带具 有粘性一侧的中间,轻轻的压实,慢慢撕下,平稳的将石墨薄片一 分为二。完美的剥离,剥离的石墨薄片表面如原子般平滑,复制出 的石墨薄片是发亮的。重复3到l0次剥离,直到胶带上出现颜色如 墨水斑点一样的石墨薄片。小心的将附有石墨薄片的胶带贴附在氧 化的硅片上,轻轻挤压掉胶带和硅片之间的空气,使样品和胶带完 全贴附,保持l0 min,慢慢从硅片表面撕下胶带。这时数千小片石 墨都粘到了硅片上,而其中部分样品就是少层、甚至单层的石墨烯 。
1. 机械剥离法 2. 氧化石墨还原法
3. 化学气相沉积法 4. 外延生长发
机械剥离法:
是最早面剥离出石墨烯片层。早期的机械剥离法所制得的石墨薄片 通常含有几十至上百个片层,随着技术方法的改进,逐渐可以制备出 层数为几个片层的石墨薄片。 机械剥离法被广泛用于石墨烯片层的制备,特别在石墨烯的一 些光学、电学性能研究中,一般均以机械剥离法作为主要的制备方 法。与其他方法相比较,机械剥离法是最简单的方法,对实验室条 件的要求非常简单,并且容易获得高质量的石墨烯。 但制备的石墨烯薄片尺寸不易控制、重复性差,产率较低,而 且难以规模化制备单层石墨烯。
氧化石墨还原法
该方法主要采用强酸(如浓硫酸和发烟硝酸等)将本体石墨进行 氧化处理,通过热力学膨胀或者强力超声进行剥离,利用化学还原法 或其它方法将氧化石墨烯还原为石墨烯。所以,主要过程就分为氧 化和还原两个阶段。 氧化阶段:目前,对本体石墨进行氧化处理多采用 Hummers 法 。一般步骤为:将石墨粉和无水 NaNO3 加入置于冰浴内的浓 H2SO4 中,以 KMnO4 为氧化剂进行氧化处理,用 30% H2O2 还原剩余的氧 化剂,最后过滤、洗涤、真空脱水得到GO。 为了进一步强化其氧化强度,还可以利用过 K2S2O8 和 P2O5 对 本体石墨进行预氧化处理后,再进行 Hummers 法氧化。
论石墨烯的制备方法

论石墨烯的制备方法石墨烯是一种由碳原子组成的二维材料,由于其在电子、光学、机械等方面的独特性能,引起了广泛的关注和研究。
石墨烯的制备方法有很多种,下面就几种常见的制备方法进行介绍。
一、机械剥离法机械剥离法是最早发现的石墨烯制备方法之一。
这种方法是通过用胶带等机械手段将石墨材料中的层状结构分离得到石墨烯。
将石墨材料表面涂覆一层胶水或胶带,随后在胶面上用力撕去一小块,再将这块小块对折数次,然后再撕开,就可以得到一个更薄的石墨片,重复这个过程多次即可得到石墨烯。
这种方法简单易操作,但是比较耗时和耗力。
二、化学气相沉积法化学气相沉积法是一种较为常见的石墨烯制备方法。
该方法主要包括两个步骤,首先将金属催化剂(如铜、镍等)表面进行处理,然后将预先加热至高温的石墨片放入反应室中,在高温下与氢气、甲烷等碳源气体反应,然后通过冷却使其沉积在基底表面。
此时,石墨片原子层和基底表面结合,形成石墨烯薄膜。
三、化学还原法化学还原法是一种通过化学手段来制备石墨烯的方法。
这种方法一般是将氧化石墨氧化物如氧化石墨烯或氧化石墨烯纳米带等经过还原处理得到石墨烯。
常见的还原剂有氢气、氨气等。
四、电化学剥离法电化学剥离法是一种比较新颖的石墨烯制备方法。
该方法是通过在石墨基底和溶液中施加电场,将石墨片剥离成石墨烯。
具体操作过程是将石墨片作为阳极,放入含有离子溶液的电化学池中,然后施加电压,使石墨片与阳极之间发生剥离和离子交换,最终得到石墨烯。
电化学剥离法具有高效、可控性好等优点。
除了上述几种常见的制备方法外,还有许多其他的方法可以用来制备石墨烯,例如热解法、氧化还原法等。
这些方法各有优缺点,适用于不同的实际应用场景。
随着石墨烯研究的深入,相信会有更多更高效的制备方法被开发出来。
石墨烯制备

外延生长法
优点:能够制备出1—2碳原子层厚的石墨烯;
制得的石墨烯表现出较高的载流子迁移率等特性; 用于以SiC为衬底的石墨烯器件的研究。
缺点:SiC单晶衬底价格昂贵;SiC上的石墨烯难转移;
所制石墨烯无量子霍尔效应;难以获得大面积、 厚度均一的石墨烯(由于SiC晶体表面结构较为复杂)
化学合成法
以小分子或大分子有机物为前驱体,在碱金属催化 或环化脱氢等工艺条件下自下而上的石墨烯制备方法。
基本过程:
a 由环化脱氢过程得到连续的稠环芳烃结构 b 通过Diels-Alder反应、Pd催化的
Hagihara-Sonogashira等先合成六苯并蔻(HBC) c 在FeCl3等作用下环化脱氢得到较大平面的石墨烯
化学合成法
优点:结构完整;
有良好的加工性能; 产物具有质量高、纯度高;
缺点:反应复杂;
石墨烯的制备方法
➢微机械剥离法 ➢氧化石墨还原法 ➢外延生长法 ➢化学合成法 ➢化学气相沉积法
微机械分离法
⑴ 在高定向HOPG(热解石墨)表面用氧等离子 干刻蚀进行离子刻蚀,在表面刻蚀出一定大小 的微槽。 ⑵ 将其用光刻胶粘到玻璃衬底上。 ⑶ 用透明胶带进行反复撕揭, 去除多余HOPG。 ⑷ 将粘有微片的玻璃衬底放入丙酮溶液中超声 ⑸ 将单晶硅片放入丙酮溶剂中,将单层石墨烯 “捞出”。
石墨的氧化方法:Huminers、Brodie、Staudenmaiert 基本原理:用无机强质子酸(如浓硫酸)处理原始石墨, 将强酸小分子插入石墨层间,再用强氧化剂 (如KMn04、KCl04等)对其进行氧化。
还原的方法: 化学还原法、热还原法、 电化学还原法、激光照射还原
氧化石墨还量高,
石墨烯体材料完整地复制了泡沫
石墨烯制备

优点 • 大面积 • 高质量
ቤተ መጻሕፍቲ ባይዱ
缺点 • 条件比较苛刻 • 过程比较复杂
11
化学合成法
2.4化学合成方法
2010年,Mullen课题组 利用自下而上的化学合 成方法制备了石墨烯纳 米带。
1. 以10,100-dibromo9,90-bianthryl单体为前 驱体。
2. 单体热分解成双游离 基
3. 双游离基通过加聚反 应形成线性高分子链。
4. 通过环化脱氢作用形 成石墨烯纳米带。
12
化学合成法
自下而上的有机合成法
• 可以制备具有确定结构而且无缺陷的石墨烯纳米带 • 可以进一步对石墨烯纳米带进行功能化修饰
从有机小分子出发制备石墨烯
• 条件比较温和 • 易于控制 • 给连续化批量制备石墨烯提供了可能
13
其他方法及总结
除以上介绍的常见制备方法外,还有人研究了利用电弧法、切 割碳纳米管法、气相等离子体生长技术、静电沉积法口、原位自生 模板法等制备石墨烯。如何综合运用各种石墨烯制备方法的优势, 取长补短,解决石墨烯的不稳定性、量产等问题,完善其结构和电 性能是今后研究的热点和难点,也是今后开辟新的石墨烯合成途径 的关键。
2. 升温至生长温度,使碳通过扩散进入金属中
3. 快速降温使碳从金属中偏析出来。
9
CVD法
2010年,Bae课题组利用CVD法制备石墨烯,并将其转移到柔 性沉底上,得到尺寸达到30英寸的透明石墨烯电极,可作为触 摸屏幕。
10
CVD法
通过化学气相沉积在绝缘表面( 例如SiC) 或金属表 面( 例如Ni) 生长石墨烯, 是制备高质量石墨烯薄膜的重要 手段。
物理方法
1.物理方法
1.1机械剥离法 这类方法是通过机械力从石墨晶体的表面剥离出石墨烯 片层,即直接将石墨烯薄片从较大的晶体上剥离下来。
石墨烯的制备
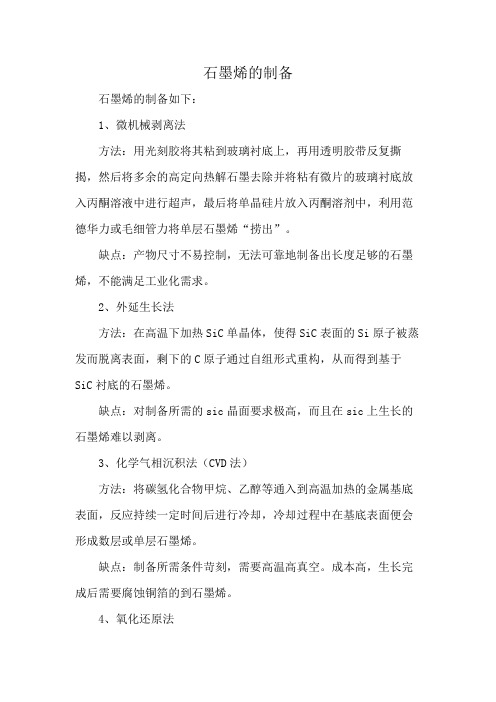
石墨烯的制备
石墨烯的制备如下:
1、微机械剥离法
方法:用光刻胶将其粘到玻璃衬底上,再用透明胶带反复撕揭,然后将多余的高定向热解石墨去除并将粘有微片的玻璃衬底放入丙酮溶液中进行超声,最后将单晶硅片放入丙酮溶剂中,利用范德华力或毛细管力将单层石墨烯“捞出”。
缺点:产物尺寸不易控制,无法可靠地制备出长度足够的石墨烯,不能满足工业化需求。
2、外延生长法
方法:在高温下加热SiC单晶体,使得SiC表面的Si原子被蒸发而脱离表面,剩下的C原子通过自组形式重构,从而得到基于SiC衬底的石墨烯。
缺点:对制备所需的sic晶面要求极高,而且在sic上生长的石墨烯难以剥离。
3、化学气相沉积法(CVD法)
方法:将碳氢化合物甲烷、乙醇等通入到高温加热的金属基底表面,反应持续一定时间后进行冷却,冷却过程中在基底表面便会形成数层或单层石墨烯。
缺点:制备所需条件苛刻,需要高温高真空。
成本高,生长完成后需要腐蚀铜箔的到石墨烯。
4、氧化还原法
方法:先用强氧化剂浓硫酸、浓硝酸、高锰酸钾等将石墨氧化成氧化石墨,氧化过程即在石墨层间穿插一些含氧官能团,从而加大了石墨层间距,然后经超声处理一段时间之后,就可形成单层或数层氧化石墨烯,再用强还原剂水合肼、硼氢化钠等将氧化石墨烯还原成石墨烯。
缺点:化学反应程度很难控制,反应不完全的情况下会有大量杂质。
石墨烯生产原料
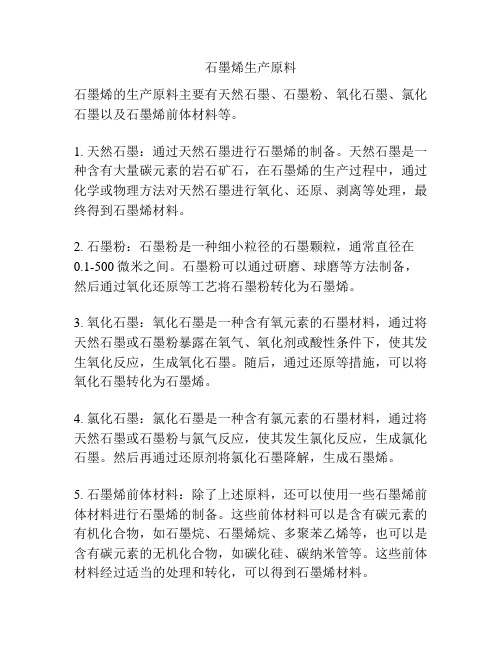
石墨烯生产原料
石墨烯的生产原料主要有天然石墨、石墨粉、氧化石墨、氯化石墨以及石墨烯前体材料等。
1. 天然石墨:通过天然石墨进行石墨烯的制备。
天然石墨是一种含有大量碳元素的岩石矿石,在石墨烯的生产过程中,通过化学或物理方法对天然石墨进行氧化、还原、剥离等处理,最终得到石墨烯材料。
2. 石墨粉:石墨粉是一种细小粒径的石墨颗粒,通常直径在0.1-500微米之间。
石墨粉可以通过研磨、球磨等方法制备,然后通过氧化还原等工艺将石墨粉转化为石墨烯。
3. 氧化石墨:氧化石墨是一种含有氧元素的石墨材料,通过将天然石墨或石墨粉暴露在氧气、氧化剂或酸性条件下,使其发生氧化反应,生成氧化石墨。
随后,通过还原等措施,可以将氧化石墨转化为石墨烯。
4. 氯化石墨:氯化石墨是一种含有氯元素的石墨材料,通过将天然石墨或石墨粉与氯气反应,使其发生氯化反应,生成氯化石墨。
然后再通过还原剂将氯化石墨降解,生成石墨烯。
5. 石墨烯前体材料:除了上述原料,还可以使用一些石墨烯前体材料进行石墨烯的制备。
这些前体材料可以是含有碳元素的有机化合物,如石墨烷、石墨烯烷、多聚苯乙烯等,也可以是含有碳元素的无机化合物,如碳化硅、碳纳米管等。
这些前体材料经过适当的处理和转化,可以得到石墨烯材料。
需要注意的是,石墨烯的生产原料选择主要取决于生产工艺和方法,不同的生产方式可能会采用不同的原料。
石墨烯常用制备方法

石墨烯常用制备方法
一、石墨烯常用制备方法
1、气相沉积(CVD)
气相沉积(CVD)属于一种分子气相化学反应,它是在高温(一般情况下在550-950℃)和高压(一般在100-1000pa)的条件下,将原料通过催化剂转变为石墨烯电催化膜的制备方法。
优点:有温控,可以控制膜的厚度和结构。
缺点:需要高温和高压的条件,可能导致电催化膜品质不好。
2、硅基模板制备法
硅基模板制备法是通过化学气相沉积(CVD)在硅基模板上形成石墨烯的制备方法。
此方法在多晶硅基模板上形成石墨烯膜,经过后续处理去除模板,形成石墨烯膜。
优点:此方法可以在室温条件下进行,操作简便;可以得到高质量的石墨烯膜。
缺点:膜的厚度受模板的厚度影响较大;制备过程比较复杂。
3、电沉积制备法
电沉积制备法是在电极上通过催化剂和原料的反应,利用催化反应产生的电子电子反馈参与沉积物质,从而制备石墨烯的方法。
优点:操作简便,制备过程较快;不受模板的厚度影响,可以控制膜的厚度;可以得到高质量的石墨烯膜。
缺点:需要精确的控制电极,否则可能影响膜的品质。
4、氢化焙烧法
氢化焙烧法主要是将不饱和的物质(如碳氢物质或酰酸物质等)在高温下进行氢化反应,从而形成石墨烯的方法。
优点:制备过程比较简单,不需要高温和高压的条件;可以得到结构良好的石墨烯膜。
缺点:制备过程的温控不够精确,可能影响石墨烯膜的品质。
- 1、下载文档前请自行甄别文档内容的完整性,平台不提供额外的编辑、内容补充、找答案等附加服务。
- 2、"仅部分预览"的文档,不可在线预览部分如存在完整性等问题,可反馈申请退款(可完整预览的文档不适用该条件!)。
- 3、如文档侵犯您的权益,请联系客服反馈,我们会尽快为您处理(人工客服工作时间:9:00-18:30)。
石墨烯的制备
摘要: 近年来, 石墨烯以其独特的结构和优异的性能, 在化学、物理和材料学界引起了广泛的研究兴趣. 人们已经在石墨烯的制备方面取得了积极的进展, 为石墨烯的基础研究和应用开发提供了原料保障. 本文大量引用近三年最新参考文献, 综述了石墨烯的制备方法: 物理方法(微机械剥离法、液相或气相直接剥离法)与化学法(化学气相沉积法、晶体外延生长法、氧化−还原法), 并详细介绍了石墨烯的各种修饰方法. 分析比较了各种方法的优缺点, 指出了石墨烯制备方法的发展趋势.
关键词: 石墨烯; 石墨烯氧化物; 制备; 功能化石墨烯。
背景摘要
2004年, 英国曼彻斯特大学的Geim研究小组首次制备出稳定的石墨烯, 推翻了经典的“热力学涨落不允许二维晶体在有限温度下自由存在”的理论, 震撼了整个物理界[1], 引发了石墨烯的研究热潮[2]. 理想的石墨烯结构可以看作被剥离的单原子层石墨, 基本结构为sp2杂化碳原子形成的类六元环苯单元并无限扩展的二维晶体材料, 这是目前世界上最薄的材料—单原子厚度的材料. 这种特殊结构蕴含了丰富而新奇的物理现象, 使石墨烯表现出许多优异性质[3-6], 石墨烯不仅有优异的电学性能(室温下电子迁移率可达
2×105cm2/(V·s))[7-8], 突出的导热性能
(5000 W/(m·K))[9-10], 超常的比表面积(2630 m2/g)[11], 其杨氏模量(1100 GPa)和断裂强度(125 GPa)[12-13]也可与碳纳米管媲美, 而且还具有一些独特的性能, 如完美的量子隧道效应、半整数量子霍尔效应、永不消失的电导率等一系列性质[14]等. 与碳纳米管相比, 石墨烯的主要性能均与之相当, 甚至更好, 避免了碳纳米管研究和应用中难以逾越的手性控制、金属型和半导体型分离以及催化剂杂质等难题, 而且制备石墨烯的原料价格便宜. 正是由于石墨烯材料具有如此众多奇特的性质, 引起了物理、化学、材料等不同领域科学家的极大研究兴趣, 也使得石墨烯在电子、信息、能源、材料和生物医药等领域具有重大的应用前景。
一.石墨烯的制备方法概述
目前有关石墨烯的制备方法, 国内外有较多的文献综述,石墨烯的制备主要有物理方法和化学方法. 物理方法通常是以廉价的石墨或膨胀石墨为原料, 通过微机械剥离法、液相或气相直接剥离法来制备单层或多层石墨烯, 此法原料易得, 操作相对简单, 合成的石墨烯的纯度高、缺陷较少, 但费时、产率低下, 不适于大规模生产. 目前实验室用石墨烯主要多用化学方法来制备, 该法最早以苯环或其它芳香体系为核, 通过多步偶联反应取代苯环或大芳香环上6个, 循环往复, 使芳香体系变大, 得到一定尺寸的平面结构的石墨烯(化学合成法)[20]. 2006年Stankovich等[21]首次用肼还原脱除石墨烯氧化物(graphene oxide, 以下简称GO)的含氧基团从而恢复单层石墨的有序结构(氧化−还原法), 在此基础上人们
不断加以改进, 使得氧化−还原法(含氧化−修饰−还原法)成为最具有潜力和发展前途的合成石墨烯及其材料的方法[16]. 除此之外, 晶体外延生长、化学气相沉积也可用于大规模制备高纯度的石墨烯. 本文重点总结近三年化学法, 尤其是氧化−还原法制备石墨烯的研究进展, 并对制备石墨烯的各种途径的优缺点加以评述. 二.物理法制备石墨烯
2.1 微机械剥离法
微机械剥离法是最早用于制备石墨烯的物理方法. Geim等[1]在1mm厚的高定向热解石墨表面进行干法氧等离子刻蚀, 然后将其粘到玻璃衬底上, 接着在上面贴上1μm 厚湿的光刻胶, 经烘焙、反复粘撕, 撕下来粘在光刻胶上的石墨片放入丙酮溶液中洗去, 最后将剩余在玻璃衬底上的石墨放入丙醇中进行超声处理, 从而得到单层石墨烯. 虽然微机械剥离是一种简单的制备高质量石墨烯的方法, 但是它费时费力, 难以精确控制, 重复性较差, 也难以大规模制备.
2.2 液相或气相直接剥离法
通常直接把石墨或膨胀石墨(EG)(一般通过快速升温至1000℃以上把表面含氧基团除去来获取)加在某种有机溶剂或水中, 借助超声波、加热或气流的作用制备一定浓度的单层或多层石墨烯溶液。
Coleman 等参照液相剥离碳纳米管的方式将石墨分
散在N-甲基-吡咯烷酮(NMP) 中, 超声1h后单层石墨烯的产率为1%[22], 而长时间的超声(462h)可使石墨烯浓度高达
1.2mg/mL, 单层石墨烯的产率也提高到4%[23]. 他们的研究表明[22], 当溶剂的表面能与石墨烯相匹配时, 溶剂与石墨烯之间的相互作用可以平衡剥离石墨烯所需的能量, 而能够较好地剥离石墨烯的溶剂表面张力范围为40~50mJ/m2; Hamilton等[24]把石墨直接分散在邻二氯苯(表面张力: 36.6mJ/m2)中, 超声、离心后制备了大块状(100~500nm)的单层石墨烯; Drzal等[25]利用液−液界面自组装在三氯甲烷中制备了表面高度疏水、高电导率和透明度较好的单层石墨烯. 为提高石墨烯的产率, 最近Hou等[26]发展了一种称为溶剂热插层(solvothermal-asssisted exfoliation)制备石墨烯的新方法(图1), 该法是以EG为原料, 利用强极性有机溶剂乙腈与石墨烯片的双偶极诱导作用(dipole- induced dipole interaction)来剥离、分散石墨, 使石墨烯的总产率提高到10%~12%. 同时, 为增加石墨烯溶液的稳定性, 人们往往在液相剥离石墨片层过程中加入一些稳定剂以防止石墨烯因片层间的范德华力而重新聚集. Coleman 研究小组在水/十二烷基苯磺酸钠( SDBS) 中超声处理石墨30min, 详细研究了石墨初始浓度以及SDBS浓度对石墨烯产率的影响, 发现所得的石墨烯多数在5层以下, 并且具有较高的导电率(~104 S/m)[27], 后来发现柠檬酸钠作为稳定剂也具有较好的剥离分散效果[28]. Englert等[29]合成一种新型的水溶性含大芳香环的两亲性物质并作为片层石墨的稳定剂(图2), 利用该物质与石墨片层的π−π堆积与疏水作用来制备稳定的石墨烯水溶液. 最近, 为同时提
高单层石墨烯的产率及其溶液的稳定性, Li等[30]提出“exfoliation-rein-tercalation-expansion”方法(图3), 以高温处理后
(图1 溶剂热剥离法制备石墨烯)
(图2 合成的水溶性两亲性物质)
(图3 “剥离−再插层−膨胀”法制备石墨烯)
的部分剥离石墨为原料, 用特丁基氢氧化铵插层后,再以DSPE-mPEG 为稳定剂, 合成的石墨烯90%为单层, 且透明度较(83%~93%). 另外,一些研究人员研究了利用气流的冲击作用来提高剥离石墨片层的效率, Janowska等[31]以膨胀石墨为原料, 微波辐照下发现以氨水做溶剂能提高石墨烯的总产率(~8%), 深入研究证实高温下溶剂分解产生的氨气能渗入石墨片层中, 当气压超过一定数值足以克服石墨片层间的范德华力而使石墨剥离. Pu等[32]将天然石墨浸入超临界CO2中30min以达到气体插层的目的, 经快速减压后将气体充入SDBS的水溶液中即制得稳定的石墨烯水溶液, 该法操作简便、成本低, 但制备的石墨烯片层较多(~10层).
因以廉价的石墨或膨胀石墨为原料, 制备过程不涉及化学变化, 液相或气相直接剥离法制备石墨烯具有成本低、操作简单、产品质量高等优点, 但也存在单层石墨烯产率不高、片层团聚严重、需进一步脱去稳定剂等缺陷. 为克服这种现象, 最近Knieke等
[33]发展了一种大规模制备石墨烯的方法, 即液相“机械剥
离”. 该法采取了一种特殊的设备, 高速剪切含十二烷基磺酸钠的石墨水溶液, 3h后溶液中单层和多层石墨烯的浓度高达
25g/L, 而5h后50%以上的石墨烯厚度小于3nm, 该法具有成本低、产率高、周期短等优势, 是一种极有诱惑力的大规模制备石墨烯的途径.。