国外特种加工技术的最新进展.
来自4个国家的5种全球顶级机加工技术,错过是你的损失!
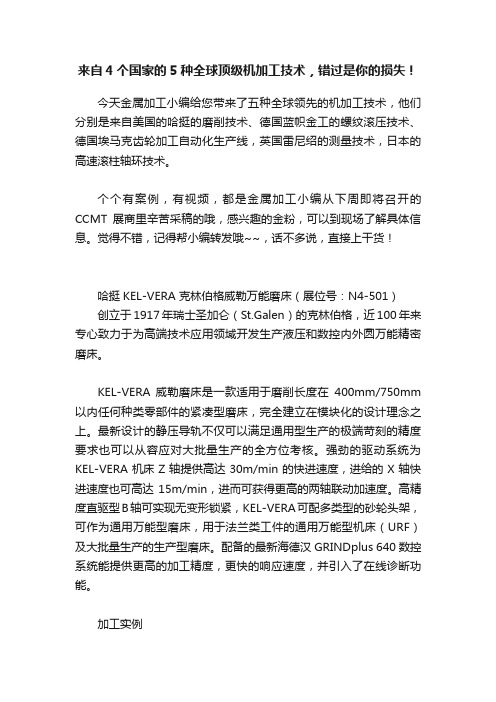
来自4个国家的5种全球顶级机加工技术,错过是你的损失!今天金属加工小编给您带来了五种全球领先的机加工技术,他们分别是来自美国的哈挺的磨削技术、德国蓝帜金工的螺纹滚压技术、德国埃马克齿轮加工自动化生产线,英国雷尼绍的测量技术,日本的高速滚柱轴环技术。
个个有案例,有视频,都是金属加工小编从下周即将召开的CCMT展商里辛苦采稿的哦,感兴趣的金粉,可以到现场了解具体信息。
觉得不错,记得帮小编转发哦~~,话不多说,直接上干货!哈挺KEL-VERA 克林伯格威勒万能磨床(展位号:N4-501)创立于1917年瑞士圣加仑(St.Galen)的克林伯格,近100年来专心致力于为高端技术应用领域开发生产液压和数控内外圆万能精密磨床。
KEL-VERA 威勒磨床是一款适用于磨削长度在400mm/750mm 以内任何种类零部件的紧凑型磨床,完全建立在模块化的设计理念之上。
最新设计的静压导轨不仅可以满足通用型生产的极端苛刻的精度要求也可以从容应对大批量生产的全方位考核。
强劲的驱动系统为KEL-VERA机床Z轴提供高达30m/min的快进速度,进给的X轴快进速度也可高达15m/min,进而可获得更高的两轴联动加速度。
高精度直驱型B轴可实现无变形锁紧,KEL-VERA可配多类型的砂轮头架,可作为通用万能型磨床,用于法兰类工件的通用万能型机床(URF)及大批量生产的生产型磨床。
配备的最新海德汉GRINDplus 640数控系统能提供更高的加工精度,更快的响应速度,并引入了在线诊断功能。
加工实例KEL-VERA万能外圆磨床的坐标磨削功能KEL-VERA, Heidenhain海德汉控制系统X,Z and B axis hydrostatic guideX,Z及B轴三轴流体静压导轨Direct drive for wheelhead swiveling and worhead工件头架及砂轮架旋转力矩电机直接驱动Part dimension工件尺寸: ?355 mmShape accuracy Polygon多棱体轮廓精度: <0.004>0.004>Shape accuracy Trochoid内轮廓轮廓精度: <0.005>0.005>Shape accuracy slot端槽轮廓精度: <0.003>0.003>Roundness of bore偏心孔的圆度: <0.003>0.003>德国LMT FETTE蓝帜菲特EVOline螺纹滚压头(展位号:E5-402)德国LMT FETTE蓝帜菲特针对外螺纹及外回转型面加工开发了一系列附有自身特色冷挤压加工产品,提高加工效率,提高被加工件的精度及质量,同时为客户节省降低成本,解决客户面临的疑难问题。
2023年国外特种陶瓷的发展及新动向
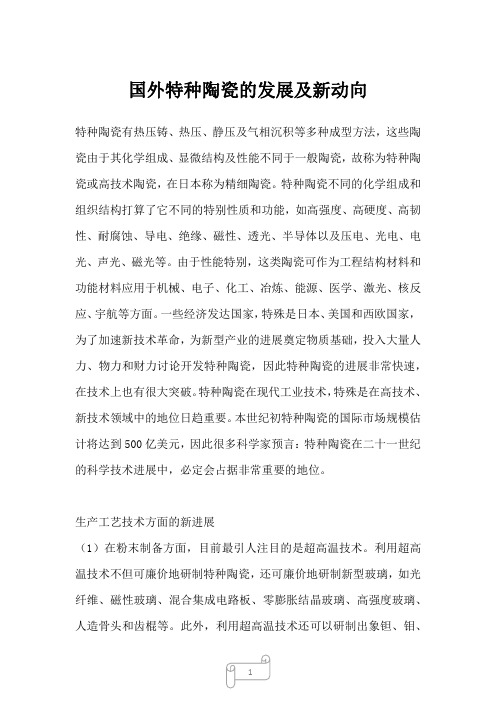
国外特种陶瓷的发展及新动向特种陶瓷有热压铸、热压、静压及气相沉积等多种成型方法,这些陶瓷由于其化学组成、显微结构及性能不同于一般陶瓷,故称为特种陶瓷或高技术陶瓷,在日本称为精细陶瓷。
特种陶瓷不同的化学组成和组织结构打算了它不同的特别性质和功能,如高强度、高硬度、高韧性、耐腐蚀、导电、绝缘、磁性、透光、半导体以及压电、光电、电光、声光、磁光等。
由于性能特别,这类陶瓷可作为工程结构材料和功能材料应用于机械、电子、化工、冶炼、能源、医学、激光、核反应、宇航等方面。
一些经济发达国家,特殊是日本、美国和西欧国家,为了加速新技术革命,为新型产业的进展奠定物质基础,投入大量人力、物力和财力讨论开发特种陶瓷,因此特种陶瓷的进展非常快速,在技术上也有很大突破。
特种陶瓷在现代工业技术,特殊是在高技术、新技术领域中的地位日趋重要。
本世纪初特种陶瓷的国际市场规模估计将达到500亿美元,因此很多科学家预言:特种陶瓷在二十一世纪的科学技术进展中,必定会占据非常重要的地位。
生产工艺技术方面的新进展(1)在粉末制备方面,目前最引人注目的是超高温技术。
利用超高温技术不但可廉价地研制特种陶瓷,还可廉价地研制新型玻璃,如光纤维、磁性玻璃、混合集成电路板、零膨胀结晶玻璃、高强度玻璃、人造骨头和齿棍等。
此外,利用超高温技术还可以研制出象钽、钼、钨、钒铁合金和钛等能够应用于太空飞行、海洋、核聚变等尖端领域的材料。
例如日本在4000—15000℃和一个大气压以下制造金钢石,其效率比现在普遍采纳的低温低压等离子体技术高一百二十倍。
超高温技术具有如下优点:能生产出用以往方法所不能生产的物质;能够获得纯度极高的物质:生产率会大幅度提高;可使作业程序简化、易行。
目前,在超高温技术方面居领先地位的是日本。
据统计,2000年日本超高温技术的特种陶瓷市场规模也将会超过20万亿日元。
此外,溶解法制备粉末、化学气相沉积法制备陶瓷粉末、溶胶K凝胶法生产莫来石超细粉末以及等离子体气相反应法等也引起了人们的关注。
国外特种加工技术的最新进展.

国外特种加工技术的最新进展中国机械工程学会电加工分会赵万生王振龙郭东明赵福令朱荻黄因慧摘要就当前国际特种加工技术研究的最新进展情况,从激光加工、电解加工、超声加工尤其是电火花加工等方面进行了较为详尽的阐述。
希望能从国外此方面的研究中,看出21世纪特种加工技术的走向,并为我国特种加工技术的研究提供借鉴。
Abstract This paper summaries and analyses the latest overseas ′advancem ents of nontra 2ditional machining methods such as electro 2discharge machining ,laser beam machining ,elec 2trolytic machining ,as well as ultrasonic machining.This review also gives a prospect on the de 2velopment of non 2traditional machining technology towards the 21st century and provides a refer 2ence to the domestic research.关键词特种加工电火花加工激光加工超声加工电解加工1引言伴随着难加工材料及复杂曲面加工而逐步发展成熟起来的特种加工技术,在计算机技术、现代电力电子技术、网络技术及航天、航空、模具制造等高新技术的推动及市场牵引下,正朝着更深层次发展。
目前国际上对特种加工技术的研究主要表现在以下几个方面:(1微细化。
随着工程技术领域对微型机械的迫切需求,微细加工已不再是微电子机械技术的代名词,目前国际上对微细电火花加工、微细超声加工、微细激光加工、微细电化学加工等的研究正方兴未艾,特种微细加工技术有望成为三维实体微细加工的主流技术;(2新型元器件在特种加工领域中得到了极为广泛的应用。
特种加工技术发展现状与展望
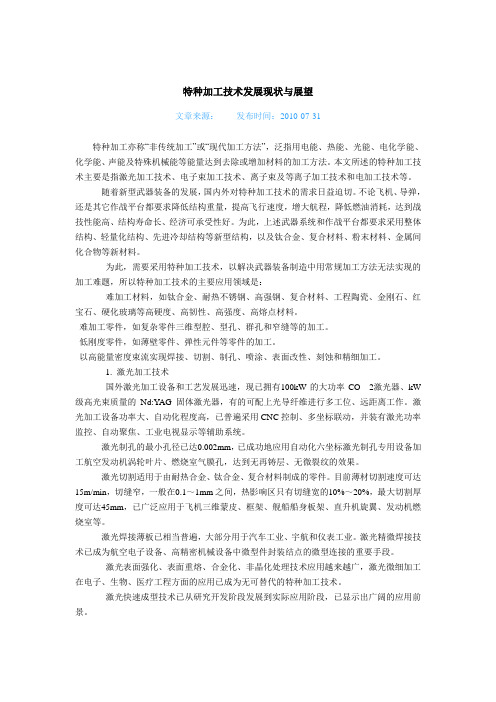
特种加工技术发展现状与展望文章来源:发布时间:2010-07-31特种加工亦称“非传统加工”或“现代加工方法”,泛指用电能、热能、光能、电化学能、化学能、声能及特殊机械能等能量达到去除或增加材料的加工方法。
本文所述的特种加工技术主要是指激光加工技术、电子束加工技术、离子束及等离子加工技术和电加工技术等。
随着新型武器装备的发展,国内外对特种加工技术的需求日益迫切。
不论飞机、导弹,还是其它作战平台都要求降低结构重量,提高飞行速度,增大航程,降低燃油消耗,达到战技性能高、结构寿命长、经济可承受性好。
为此,上述武器系统和作战平台都要求采用整体结构、轻量化结构、先进冷却结构等新型结构,以及钛合金、复合材料、粉末材料、金属间化合物等新材料。
为此,需要采用特种加工技术,以解决武器装备制造中用常规加工方法无法实现的加工难题,所以特种加工技术的主要应用领域是:难加工材料,如钛合金、耐热不锈钢、高强钢、复合材料、工程陶瓷、金刚石、红宝石、硬化玻璃等高硬度、高韧性、高强度、高熔点材料。
难加工零件,如复杂零件三维型腔、型孔、群孔和窄缝等的加工。
低刚度零件,如薄壁零件、弹性元件等零件的加工。
以高能量密度束流实现焊接、切割、制孔、喷涂、表面改性、刻蚀和精细加工。
1. 激光加工技术国外激光加工设备和工艺发展迅速,现已拥有100kW的大功率CO2激光器、kW 级高光束质量的Nd:Y AG固体激光器,有的可配上光导纤维进行多工位、远距离工作。
激光加工设备功率大、自动化程度高,已普遍采用CNC控制、多坐标联动,并装有激光功率监控、自动聚焦、工业电视显示等辅助系统。
激光制孔的最小孔径已达0.002mm,已成功地应用自动化六坐标激光制孔专用设备加工航空发动机涡轮叶片、燃烧室气膜孔,达到无再铸层、无微裂纹的效果。
激光切割适用于由耐热合金、钛合金、复合材料制成的零件。
目前薄材切割速度可达15m/min,切缝窄,一般在0.1~1mm之间,热影响区只有切缝宽的10%~20%,最大切割厚度可达45mm,已广泛应用于飞机三维蒙皮、框架、舰船船身板架、直升机旋翼、发动机燃烧室等。
国外数控机床的发展现状
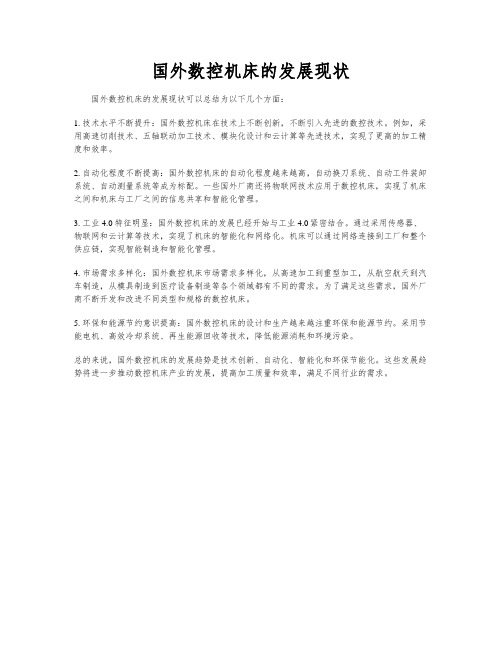
国外数控机床的发展现状
国外数控机床的发展现状可以总结为以下几个方面:
1. 技术水平不断提升:国外数控机床在技术上不断创新,不断引入先进的数控技术。
例如,采用高速切削技术、五轴联动加工技术、模块化设计和云计算等先进技术,实现了更高的加工精度和效率。
2. 自动化程度不断提高:国外数控机床的自动化程度越来越高,自动换刀系统、自动工件装卸系统、自动测量系统等成为标配。
一些国外厂商还将物联网技术应用于数控机床,实现了机床之间和机床与工厂之间的信息共享和智能化管理。
3. 工业
4.0 特征明显:国外数控机床的发展已经开始与工业4.0紧密结合。
通过采用传感器、物联网和云计算等技术,实现了机床的智能化和网络化。
机床可以通过网络连接到工厂和整个供应链,实现智能制造和智能化管理。
4. 市场需求多样化:国外数控机床市场需求多样化,从高速加工到重型加工,从航空航天到汽车制造,从模具制造到医疗设备制造等各个领域都有不同的需求。
为了满足这些需求,国外厂商不断开发和改进不同类型和规格的数控机床。
5. 环保和能源节约意识提高:国外数控机床的设计和生产越来越注重环保和能源节约。
采用节能电机、高效冷却系统、再生能源回收等技术,降低能源消耗和环境污染。
总的来说,国外数控机床的发展趋势是技术创新、自动化、智能化和环保节能化。
这些发展趋势将进一步推动数控机床产业的发展,提高加工质量和效率,满足不同行业的需求。
国外数控发展现状及未来趋势分析
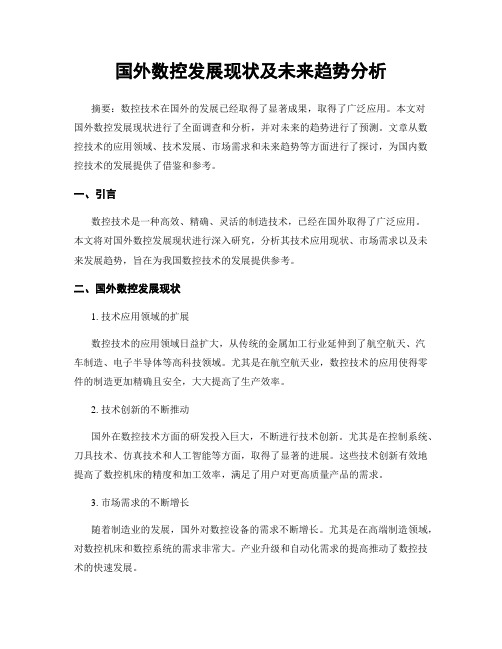
国外数控发展现状及未来趋势分析摘要:数控技术在国外的发展已经取得了显著成果,取得了广泛应用。
本文对国外数控发展现状进行了全面调查和分析,并对未来的趋势进行了预测。
文章从数控技术的应用领域、技术发展、市场需求和未来趋势等方面进行了探讨,为国内数控技术的发展提供了借鉴和参考。
一、引言数控技术是一种高效、精确、灵活的制造技术,已经在国外取得了广泛应用。
本文将对国外数控发展现状进行深入研究,分析其技术应用现状、市场需求以及未来发展趋势,旨在为我国数控技术的发展提供参考。
二、国外数控发展现状1. 技术应用领域的扩展数控技术的应用领域日益扩大,从传统的金属加工行业延伸到了航空航天、汽车制造、电子半导体等高科技领域。
尤其是在航空航天业,数控技术的应用使得零件的制造更加精确且安全,大大提高了生产效率。
2. 技术创新的不断推动国外在数控技术方面的研发投入巨大,不断进行技术创新。
尤其是在控制系统、刀具技术、仿真技术和人工智能等方面,取得了显著的进展。
这些技术创新有效地提高了数控机床的精度和加工效率,满足了用户对更高质量产品的需求。
3. 市场需求的不断增长随着制造业的发展,国外对数控设备的需求不断增长。
尤其是在高端制造领域,对数控机床和数控系统的需求非常大。
产业升级和自动化需求的提高推动了数控技术的快速发展。
三、未来趋势预测1. 智能制造将成为主要趋势随着人工智能和大数据技术的发展,智能制造将成为未来数控发展的主要趋势。
智能化的数控机床将具备自主学习、自主诊断和自主决策的能力,实现生产过程的智能化管理。
2. 个性化定制将成为市场需求的主流随着消费者需求的个性化和多样化,对产品的个性化定制需求越来越高。
数控技术的灵活性和自动化特性使其能够满足个性化定制的需求,未来个性化定制将成为数控技术发展的重要方向。
3. 高速、高精度加工技术的不断创新随着科技的进步,高速、高精度加工技术将得到进一步发展和创新。
新一代的数控机床将具备更高的加工精度,更快的加工速度和更长的使用寿命。
国外模具制造技术的现状和发展趋势
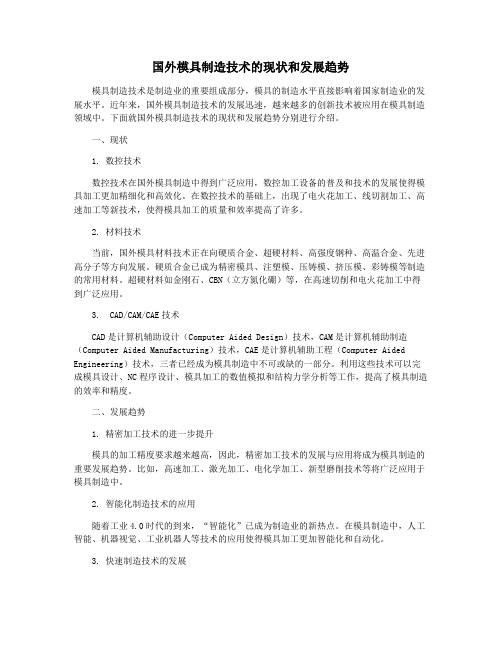
国外模具制造技术的现状和发展趋势模具制造技术是制造业的重要组成部分,模具的制造水平直接影响着国家制造业的发展水平。
近年来,国外模具制造技术的发展迅速,越来越多的创新技术被应用在模具制造领域中。
下面就国外模具制造技术的现状和发展趋势分别进行介绍。
一、现状1. 数控技术数控技术在国外模具制造中得到广泛应用,数控加工设备的普及和技术的发展使得模具加工更加精细化和高效化。
在数控技术的基础上,出现了电火花加工、线切割加工、高速加工等新技术,使得模具加工的质量和效率提高了许多。
2. 材料技术当前,国外模具材料技术正在向硬质合金、超硬材料、高强度钢种、高温合金、先进高分子等方向发展。
硬质合金已成为精密模具、注塑模、压铸模、挤压模、彩铸模等制造的常用材料。
超硬材料如金刚石、CBN(立方氮化硼)等,在高速切削和电火花加工中得到广泛应用。
3. CAD/CAM/CAE技术CAD是计算机辅助设计(Computer Aided Design)技术,CAM是计算机辅助制造(Computer Aided Manufacturing)技术,CAE是计算机辅助工程(Computer Aided Engineering)技术,三者已经成为模具制造中不可或缺的一部分。
利用这些技术可以完成模具设计、NC程序设计、模具加工的数值模拟和结构力学分析等工作,提高了模具制造的效率和精度。
二、发展趋势1. 精密加工技术的进一步提升模具的加工精度要求越来越高,因此,精密加工技术的发展与应用将成为模具制造的重要发展趋势。
比如,高速加工、激光加工、电化学加工、新型磨削技术等将广泛应用于模具制造中。
2. 智能化制造技术的应用随着工业4.0时代的到来,“智能化”已成为制造业的新热点。
在模具制造中,人工智能、机器视觉、工业机器人等技术的应用使得模具加工更加智能化和自动化。
3. 快速制造技术的发展在大型化、多品种、小批量的生产需求下,快速制造技术的发展势头迅猛。
现代特种加工技术的发展现状与展望

现代特种加工技术的发展现状与展望引言随着信息时代的不断发展,各行各业的技术都在不断地更新换代,特种加工技术也不例外。
作为现代制造业中必不可少的关键技术之一,特种加工技术的发展一直备受关注。
现代特种加工技术的发展现状现代特种加工技术是指通过精密的工艺、设备和材料,对具有特殊形状、性质或要求的工件进行加工和改造的一种高级制造工艺。
根据工艺原理和特点,特种加工技术可以分为多种类型,以下是目前主要的特种加工技术:激光加工技术激光加工技术通过激光束的聚焦和集中作用,对目标物进行加工和改造。
这种技术具有精度高、速度快、污染小等优点,已被广泛应用于电子、汽车、机械等领域。
等离子体加工技术等离子体加工技术是通过高温等离子体电弧对材料进行切割和加工。
这种技术具有速度快、精度高、材料损伤小等优点,已被广泛应用于金属材料和化学工业领域。
超声波加工技术超声波加工技术是通过超声波振动,对物质进行加工和改造的一种技术。
这种技术具有清洁、无侵入、无污染等优点,已被广泛应用于电子、制药、生物等领域。
光纤激光焊接技术光纤激光焊接技术是通过光纤激光束对金属进行焊接的一种技术。
这种技术具有高速、高效、低污染等优点,已被广泛应用于航空、航天、汽车、电子等领域。
现代特种加工技术的发展展望在特种加工技术的发展过程中,随着科技的进步和需求的不断变化,特种加工技术也在不断地发展和完善。
以下是未来特种加工技术的发展趋势:精密加工技术随着制造业的不断发展,对工件精度的要求也越来越高,精密加工技术将成为未来特种加工技术的主要发展方向之一。
环保加工技术环保加工技术已成为全球热议的话题,环保加工技术的发展将成为未来特种加工技术的重要方向之一。
如超声波加工技术,其使用无污染,对环境无任何负面影响,而且在对材料进行加工的同时,不会对材料的物理性能造成损害。
多功能加工技术特种加工技术的应用范围不断扩大,单一的加工技术已经无法满足市场需求。
未来,同时具备多种加工功能的特种加工技术将更受市场欢迎。
- 1、下载文档前请自行甄别文档内容的完整性,平台不提供额外的编辑、内容补充、找答案等附加服务。
- 2、"仅部分预览"的文档,不可在线预览部分如存在完整性等问题,可反馈申请退款(可完整预览的文档不适用该条件!)。
- 3、如文档侵犯您的权益,请联系客服反馈,我们会尽快为您处理(人工客服工作时间:9:00-18:30)。
国外特种加工技术的最新进展中国机械工程学会电加工分会赵万生王振龙郭东明赵福令朱荻黄因慧摘要就当前国际特种加工技术研究的最新进展情况,从激光加工、电解加工、超声加工尤其是电火花加工等方面进行了较为详尽的阐述。
希望能从国外此方面的研究中,看出21世纪特种加工技术的走向,并为我国特种加工技术的研究提供借鉴。
Abstract This paper summaries and analyses the latest overseas ′advancem ents of nontra 2ditional machining methods such as electro 2discharge machining ,laser beam machining ,elec 2trolytic machining ,as well as ultrasonic machining.This review also gives a prospect on the de 2velopment of non 2traditional machining technology towards the 21st century and provides a refer 2ence to the domestic research.关键词特种加工电火花加工激光加工超声加工电解加工1引言伴随着难加工材料及复杂曲面加工而逐步发展成熟起来的特种加工技术,在计算机技术、现代电力电子技术、网络技术及航天、航空、模具制造等高新技术的推动及市场牵引下,正朝着更深层次发展。
目前国际上对特种加工技术的研究主要表现在以下几个方面:(1微细化。
随着工程技术领域对微型机械的迫切需求,微细加工已不再是微电子机械技术的代名词,目前国际上对微细电火花加工、微细超声加工、微细激光加工、微细电化学加工等的研究正方兴未艾,特种微细加工技术有望成为三维实体微细加工的主流技术;(2新型元器件在特种加工领域中得到了极为广泛的应用。
如大功率激光器、新型压电材料等;(3人工智能技术、网络化制造、绿色制造等新概念正逐渐渗透到特种加工领域中。
可以预言在即将到来的21世纪,与当代高新技术密切结合的特种加工技术将在制造领域发挥更大的作用;(4特种加工的应用领域正在拓宽。
如非导电材料的电火花加工,电火花、激光、电子束表面改性等。
特种加工技术的工艺特点和技术进步已引起世界各国专家学者的高度重视。
相收稿日期:1999-09-20对于70年代、80年代而言,90年代后,国际上对特种加工技术的研究更为广泛和深入。
这一点从不完全统计的EI 数据库收录的有关特种加工技术的文献数量(通过主题词索引检索上可见一斑,如图1所示。
图1EI 收录的几种特种加工方法的文章数2电火花加工技术211微细电火花加工微细电火花加工技术的研究大致可以1984年线电极电火花磨削(WED G 技术的出现为界而分为两个阶段。
此前的研究主要是针对电火花加工用于微细加工的可行性,如对电极材料、电极损耗、工作液、排屑方式及加工间隙等状况的基础性研究;WED G 技术的出现,圆满地解决了微细电极的制作与安装问题,伴随着这一时期现代科技的飞速发展,使微细电火花加工技术进入了实用化阶段。
WED G 技术的出现,使得微细轴孔的电火花加工成为可能,在这一方面,日本东京大学增泽隆久等人已加工出Φ215μm 的微细轴和Φ5μm 的微细孔,代表了当前这一领域的世界前沿。
随着微型机械的发展和WED G 技术的逐步成熟,微细电火花加工技术的研究已拓展到了三维微细型腔的加工中。
据统计,微细电火花加工在电火花加工中所占的比重正逐年增加,目前已接近10%。
在微细电火花加工中使用微小成形电极,利用传统的电火花成形加工方法进行微细三维轮廓加工显然是不现实的,这是因为复杂形状成形微小电极本身就极难甚至无法制作,而且由于加工过程中严重的电极损耗现象,将使成形电极的形状很快改变而无法进行高精度的三维曲面加工。
因此,使用简单形状的电极,借鉴数控铣削的方法进行微细三维轮廓的电火花铣削加工,是当前微细电火花加工领域的研究热点。
1997年,日本东京大学余祖元博士、增泽隆久教授等提出了电极等损耗概念,并在实验中验证了这一规律。
由于在电极等损耗微细电火花加工过程中,电极的损耗只发生在电极底面,而且通过加工路径的合理规划,可使得电极端部处于等损耗状态,因此加工中电极损耗的补偿策略将变得极为简单,使得微三维轮廓的精密电火花加工成为可能。
图2是东京大学生产技术研究所利用简单形状的微细电极,通过微细电火花铣削加工而制作出的微汽车模具及用其翻制出的微汽车模型,其长、宽、高分别为500μm 、300μm 、200μm 。
为利用简单形状的电极进行复杂形状尤其是具有尖角锐边的微孔加工,日本冈山大学冈田晃等人提出了用三角形截面电极进行复杂形状微孔加工的方法。
这种方法使用经过拉拔成形的三角形截面银电极,利用精密数控技术,较好地解决了成形加工中复杂成形微细电极制作困难及线切割加工中尖角变钝等技术难题,成功地加工出了五边形及六边形等具有尖角的微孔,如图3所示。
虽从原理上讲这种方法本身并没有太大的想象空间,但这至少从另一个侧面告诉我们,用电火花加工技术实现微细加工的途径可能还有很多。
图2微细电火花加工实例照片图3用三角形截面电极加工出的多边孔212电火花加工新方法的研究21211气中放电加工技术一般认为,液体绝缘性工作液(如煤油或去离子水等在电火花加工中是不可替代的,其在加工中所起的冷却、排屑和压缩放电通道等作用,使得电火花加工得以稳定、可靠地进行。
但液中放电加工也同样带来了加工设备庞大复杂、电极损耗较大等显而易见的缺点。
如果能实现真正意义上的气中放电加工,将无疑对电火花加工工艺和设备本身产生革命性的变化。
日本东京农工大学国枝正典等人对此种加工方式进行了较为深入的研究,并取得了令人振奋的实验结果。
气中放电加工的原理如图4所示。
加工过程中,管状电极作回转和轴向伺服运动,高压气体从管中高速喷出以避免加工屑反粘凝固在电极和工件表面上,同时加速了熔融和汽化金属的抛出过程,并起到冷却电极的作用。
国枝正典的研究发现,气中放电加工的最大优越性在于其加工过程中的电极损耗率极低,图5是得出的实验曲线。
可以看出,其电极损耗几乎与脉冲宽度无关,这暗示了用气中放电进行窄脉宽精微电火花加工的可能性。
利用逐层扫描铣削加工方式,国枝正典等人还利用Φ013mm 的管状电极进行了气中放电三维型面的加工实验,图6是其加工实例照片。
图4气中放电加工原理图5电极损耗率比较图6三维型面加工实例21212混粉工作液电火花镜面加工技术电火花加工后的工件表面一般较为粗糙,且表层有一层厚度不均、具有微裂纹和残余拉应力的“白层”,这对零件的使用性能和寿命都是不利的,无法满足精度和表面质量要求较高零件的设计和使用要求。
为此通常需要对电火花加工后的表面进行抛光,这不但增加了产品的制造周期和制造费用,而且由于对复杂型面的抛光常常是采用手工操作,抛光后工件型面的精度难于保证。
为此,如果能通过适当的手段,改善电火花加工后的表面质量,进而省去抛光工序将具有非常重要的实际意义。
由电火花加工机理可知,要改善电火花加工后的表面粗糙度,只需减小电火花加工中的单脉冲放电能量即可。
对小面积电火花加工而言,这样做是非常有效的。
但对于大面积电火花加工,由于工件和电极间形成的极间电容相应变大,对放电能量的储能作用加强,当单个小能量脉冲到来时,工件和电极间并不发生放电;只有当多个脉冲到来,极间电容中储存了足够的能量,使极间电压达到击穿值,才能发生脉冲放电。
但此时的放电能量已远大于单个脉冲能量,因此单纯通过减小单脉冲放电能量并不能完成低粗糙度值的大面积电火花加工。
80年代末日本学者毛利尚武等人在研究中发现,在工作液中添加一定数量的硅、铝等微细粉末,会显著改善电火花加工后的表面粗糙度,达到类似镜面的效果,从而提出了混粉电火花镜面加工技术。
此后诸多学者从机理与工艺等方面对混粉电火花镜面加工技术展开了大量的实验研究。
研究表明,在工作液中添加适量的Si 、Al 、Ni 等粉末时,导致加工表面粗糙度降低的原因可能有:加工中放电间隙将明显增大,使放电对工件表面产生的冲击压力减小,从而使放电熔池中的熔融金属抛出量减小,形成较浅的放电蚀坑;金属及半导体粉末与工件加工表面之间将产生微放电,使放电电流分散于整个加工表面,形成放电分散,有效地防止了放电蚀坑的多次重叠;混粉工作液还将分散极间电容,从而使极间电容减小,有效地减小了放电脉冲能量;工作液中的硬脆性粉末,对电极和工件表面可能还具有研磨、抛光等作用。
当然对混粉工作液镜面电火花加工技术的研究目前还远未完善,有许多内容尚需进一步深入研究,但毕竟人们已经看到了实现大面积镜面电火花加工的可能性。
图7是用混粉工作液电火花加工出的三维曲面照片。
图7镜面电火花加工实例21213非导电材料的电火花加工近年来随着非导电工程陶瓷材料应用范围的日趋扩大,对其表面的加工性能要求也越来越高。
但这些材料大多是典型的难加工材料,用传统的接触式加工方法一般很难满足其加工性能要求。
长期以来,人们一直认为电火花加工的原理本身决定了其无法胜任对非导电材料的加工。
但由于电火花加工是一个非接触的热物理作用过程,因此对电火花加工过程进行重新认识,探索其对非导电材料的适应性问题成为目前电火花加工领域的又一研究热点。
在此方面的研究中,日本长冈技术科学大学福泽康与丰田工业大学的毛利尚武的研究具有相当的代表性。
国外许多学者还针对非导电陶瓷材料的复合电火花加工技术进行了广泛的研究。
福泽康等人的研究是基于工作液(如煤油在火花放电时的碳化导电现象而进行的。
其加工原理如图8所示。
在非导电陶瓷(工件端装有导电的辅助电极,这样在工具电极与辅助电极间就会产生通常的火花放电,并进而使非导电陶瓷材料得以蚀除。
福泽康、毛利尚武等人还就辅助电极的安装方式及材料进行了较为深入的研究,并对氧化物陶瓷(如ZrO 2和非氧化物陶瓷(如Si 3N 4进行了加工实验研究,取得了令人振奋的实验结果。
图9是其在陶瓷材料上加工出的星型孔照片。
图8非导电材料EDM原理图9赛隆陶瓷电火花加工实例21214电火花表面处理技术通常认为电火花加工是一个热物理作用过程,加工过程中其放电点附近可形成接近20000℃的局部高温。
因此适当控制加工条件,并对工作液和电极材料进行适当处理,应能在被加工表面上形成抗磨损和抗氧化性能良好的表层。
日本丰田工业大学毛利尚武等人对此进行了较为深入的研究。
在小脉宽正极性精加工条件下,用Si 电极对Crl3和SUS304不锈钢及用WC 2Co 粉末或Ti 基粉末压缩成形电极对碳钢进行表面电火花强化处理,均取得了令人满意的结果,其表面的抗腐蚀性和耐磨损性均大为提高。