材料力学实验报告1
材料力学实验报告
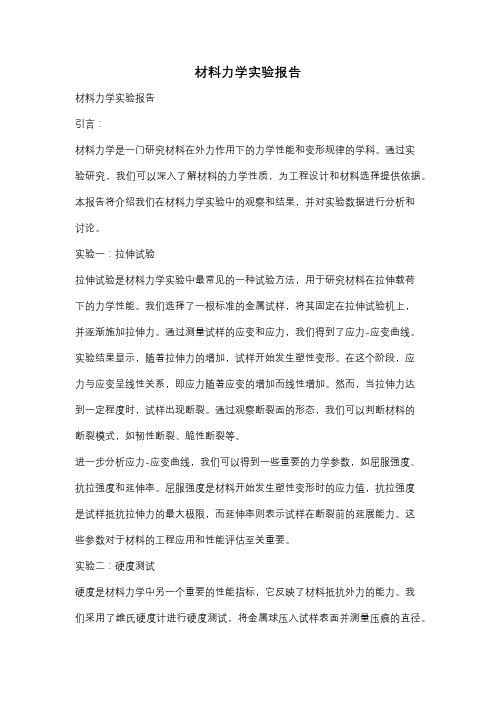
材料力学实验报告材料力学实验报告引言:材料力学是一门研究材料在外力作用下的力学性能和变形规律的学科。
通过实验研究,我们可以深入了解材料的力学性质,为工程设计和材料选择提供依据。
本报告将介绍我们在材料力学实验中的观察和结果,并对实验数据进行分析和讨论。
实验一:拉伸试验拉伸试验是材料力学实验中最常见的一种试验方法,用于研究材料在拉伸载荷下的力学性能。
我们选择了一根标准的金属试样,将其固定在拉伸试验机上,并逐渐施加拉伸力。
通过测量试样的应变和应力,我们得到了应力-应变曲线。
实验结果显示,随着拉伸力的增加,试样开始发生塑性变形。
在这个阶段,应力与应变呈线性关系,即应力随着应变的增加而线性增加。
然而,当拉伸力达到一定程度时,试样出现断裂。
通过观察断裂面的形态,我们可以判断材料的断裂模式,如韧性断裂、脆性断裂等。
进一步分析应力-应变曲线,我们可以得到一些重要的力学参数,如屈服强度、抗拉强度和延伸率。
屈服强度是材料开始发生塑性变形时的应力值,抗拉强度是试样抵抗拉伸力的最大极限,而延伸率则表示试样在断裂前的延展能力。
这些参数对于材料的工程应用和性能评估至关重要。
实验二:硬度测试硬度是材料力学中另一个重要的性能指标,它反映了材料抵抗外力的能力。
我们采用了维氏硬度计进行硬度测试,将金属球压入试样表面并测量压痕的直径。
根据硬度计的原理,我们可以计算出试样的硬度值。
硬度测试的结果显示,不同材料的硬度值存在明显差异。
硬度值高的材料通常具有较好的抗压性能,适用于承载大压力的工程应用。
而硬度值低的材料则更容易受到外力的破坏,适用于需要易变形的应用场景。
实验三:弯曲试验弯曲试验用于研究材料在弯曲载荷下的力学性能。
我们选择了一根长条状的试样,通过在试样两端施加力矩,使试样发生弯曲变形。
通过测量试样的挠度和应力分布,我们可以得到弯曲试验的结果。
实验结果表明,试样的挠度与施加的力矩呈线性关系。
在试样的底部,应力最大,而在试样的顶部,应力最小。
材料力学拉伸实验报告(1)
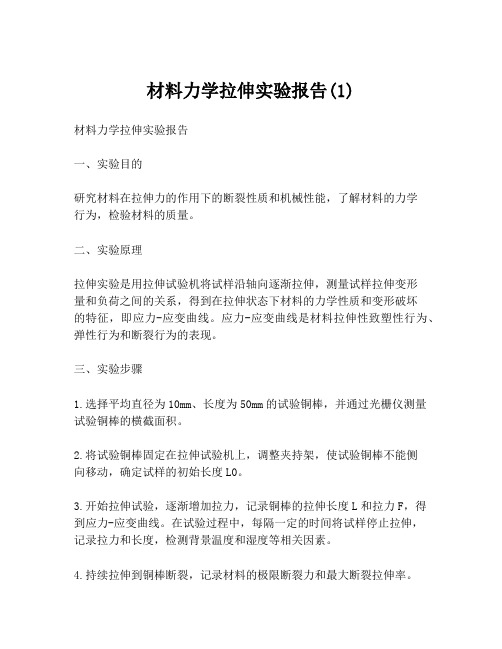
材料力学拉伸实验报告(1)材料力学拉伸实验报告一、实验目的研究材料在拉伸力的作用下的断裂性质和机械性能,了解材料的力学行为,检验材料的质量。
二、实验原理拉伸实验是用拉伸试验机将试样沿轴向逐渐拉伸,测量试样拉伸变形量和负荷之间的关系,得到在拉伸状态下材料的力学性质和变形破坏的特征,即应力-应变曲线。
应力-应变曲线是材料拉伸性致塑性行为、弹性行为和断裂行为的表现。
三、实验步骤1.选择平均直径为10mm、长度为50mm的试验铜棒,并通过光栅仪测量试验铜棒的横截面积。
2.将试验铜棒固定在拉伸试验机上,调整夹持架,使试验铜棒不能侧向移动,确定试样的初始长度L0。
3.开始拉伸试验,逐渐增加拉力,记录铜棒的拉伸长度L和拉力F,得到应力-应变曲线。
在试验过程中,每隔一定的时间将试样停止拉伸,记录拉力和长度,检测背景温度和湿度等相关因素。
4.持续拉伸到铜棒断裂,记录材料的极限断裂力和最大断裂拉伸率。
5.将数据记录到实验记录表中。
四、实验数据处理根据实验数据计算出拉伸试验的机械性能参数,如极限强度、屈服强度、断裂拉伸率等等。
1.极限强度:σmax = Fma x / S其中,Fmax为材料拉伸到断裂的最大力;S为试验铜棒的横截面积。
2.屈服强度:σs = Fs / S其中,Fs为材料开始塑性变形前的单位应力;S为试验铜棒的横截面积。
3.断裂拉伸率:A = (Lmax - L0)/ L0 × 100%其中,Lmax为材料拉伸到断裂时的长度;L0为材料载荷前的长度。
五、实验结果分析根据实验数据计算得到的拉伸试验机械性能参数可以反映出材料的力学行为。
在拉伸实验过程中,材料首先呈现弹性变形,后进入塑性变形阶段,这个过程体现在应力-应变曲线上就是曲线急速上升然后平缓变化,然后在拉伸到达一定程度后,材料会出现颈缩现象,最终断裂。
通过拉伸实验,我们可以得到应力-应变曲线,可以直观的看到材料的力学行为并计算出其力学性能参数。
材料力学工程实践报告(2篇)

第1篇一、实践背景随着我国经济的快速发展,基础设施建设、航空航天、交通运输等领域对高性能材料的依赖日益增强。
材料力学作为研究材料力学性能及其应用的科学,在材料工程领域具有举足轻重的地位。
本次实践旨在通过实验和理论分析,提高对材料力学性能的认识,为材料工程实践提供理论依据。
二、实践目的1. 理解材料力学的基本原理和实验方法;2. 掌握材料力学性能测试的基本技能;3. 分析材料力学性能与工程应用之间的关系;4. 提高实际工程问题的解决能力。
三、实践内容1. 材料力学基本原理实验(1)实验目的:验证胡克定律,研究材料的弹性模量和泊松比。
(2)实验方法:采用拉伸实验,测量材料的应力-应变关系,通过计算得到弹性模量和泊松比。
(3)实验步骤:①准备实验设备:万能试验机、拉伸试验机、测量仪器等。
②对试样进行预处理:去除表面氧化层,确保试样表面平整。
③安装试样:将试样安装在拉伸试验机上,确保试样与夹具接触良好。
④加载:按照实验要求,对试样进行拉伸,记录应力-应变数据。
⑤数据处理:根据实验数据,计算弹性模量和泊松比。
2. 材料力学性能测试实验(1)实验目的:测试材料的强度、硬度、韧性等力学性能。
(2)实验方法:采用压缩、拉伸、冲击等实验方法,测试材料的力学性能。
(3)实验步骤:①准备实验设备:万能试验机、冲击试验机、硬度计等。
②对试样进行预处理:去除表面氧化层,确保试样表面平整。
③安装试样:将试样安装在相应试验机上,确保试样与夹具接触良好。
④加载:按照实验要求,对试样进行加载,记录力学性能数据。
⑤数据处理:根据实验数据,分析材料的力学性能。
3. 材料力学性能与工程应用分析(1)实验目的:分析材料力学性能与工程应用之间的关系。
(2)实验方法:结合实际工程案例,分析材料力学性能在工程中的应用。
(3)实验步骤:①收集相关工程案例,了解材料力学性能在工程中的应用。
②分析工程案例中材料力学性能的重要性,总结材料力学性能对工程的影响。
材料力学性能测试实验报告

材料力学性能测试实验报告为了评估材料的力学性能,本实验使用了拉力试验和硬度试验两种常见的力学性能测试方法。
本实验分为三个部分:拉力试验、硬度试验和数据分析。
通过这些试验和分析,我们可以了解材料的延展性、强度和硬度等性能,对材料的机械性质有一个全面的了解。
实验一:拉力试验拉力试验是常见的力学性能测试方法之一,用来评估材料的延展性和强度。
在拉力试验中,我们使用了一个万能材料试验机,将试样夹紧在两个夹具之间,然后施加拉力,直到试样断裂。
试验过程中我们记录了试验机施加的力和试样的伸长量,并绘制了应力-应变曲线。
实验二:硬度试验硬度试验是另一种常见的力学性能测试方法,用来评估材料的硬度。
我们使用了洛氏硬度试验机进行试验。
在实验中,将一个试验头按压在试样表面,然后测量试验头压入试样的深度,来衡量材料的硬度。
我们测得了三个不同位置的硬度,并计算了平均值。
数据分析:根据拉力试验得到的应力-应变曲线,我们可以得到材料的屈服强度、断裂强度和延伸率等参数。
屈服强度是指材料开始塑性变形的应变值,断裂强度是指材料破裂时的最大应变值,延伸率是指试样在断裂前的伸长程度。
根据硬度试验得到的硬度数值,我们可以了解材料的硬度。
结论:本实验通过拉力试验和硬度试验对材料的力学性能进行了评估。
根据拉力试验得到的应力-应变曲线,我们确定了材料的屈服强度、断裂强度和延伸率等参数。
根据硬度试验的结果,我们了解了材料的硬度。
这些数据可以帮助我们判断材料在不同应力下的性能表现,从而对材料的选用和设计提供依据。
总结:本实验通过拉力试验和硬度试验对材料的力学性能进行了评估,并通过应力-应变曲线和硬度数值来分析材料的性能。
通过这些试验和分析,我们对材料的延展性、强度和硬度等性能有了全面的了解。
这些结果对于材料的选用和设计具有重要意义,可以提高材料的应用性能和可靠性。
大学材料力学实验报告
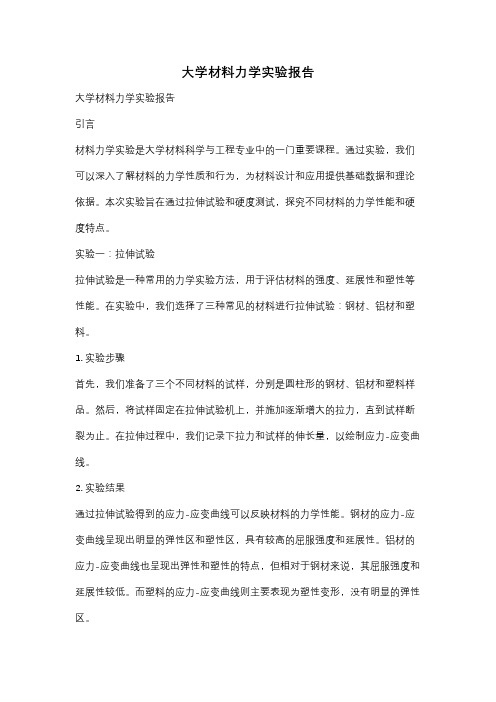
大学材料力学实验报告大学材料力学实验报告引言材料力学实验是大学材料科学与工程专业中的一门重要课程。
通过实验,我们可以深入了解材料的力学性质和行为,为材料设计和应用提供基础数据和理论依据。
本次实验旨在通过拉伸试验和硬度测试,探究不同材料的力学性能和硬度特点。
实验一:拉伸试验拉伸试验是一种常用的力学实验方法,用于评估材料的强度、延展性和塑性等性能。
在实验中,我们选择了三种常见的材料进行拉伸试验:钢材、铝材和塑料。
1. 实验步骤首先,我们准备了三个不同材料的试样,分别是圆柱形的钢材、铝材和塑料样品。
然后,将试样固定在拉伸试验机上,并施加逐渐增大的拉力,直到试样断裂为止。
在拉伸过程中,我们记录下拉力和试样的伸长量,以绘制应力-应变曲线。
2. 实验结果通过拉伸试验得到的应力-应变曲线可以反映材料的力学性能。
钢材的应力-应变曲线呈现出明显的弹性区和塑性区,具有较高的屈服强度和延展性。
铝材的应力-应变曲线也呈现出弹性和塑性的特点,但相对于钢材来说,其屈服强度和延展性较低。
而塑料的应力-应变曲线则主要表现为塑性变形,没有明显的弹性区。
实验二:硬度测试硬度是材料力学性能的重要指标之一,用于评估材料的抗压能力和耐磨性。
在实验中,我们选择了三种不同硬度的材料进行硬度测试:钢材、铝材和陶瓷。
1. 实验步骤我们使用了维氏硬度计和洛氏硬度计对试样进行硬度测试。
首先,将试样固定在硬度计上,然后施加一定的压力,观察压头对试样的印痕情况。
根据印痕的大小和形状,我们可以得出试样的硬度数值。
2. 实验结果通过硬度测试,我们发现钢材具有较高的硬度数值,表明其具有较高的抗压能力和耐磨性。
铝材的硬度数值相对较低,说明其相对较软。
而陶瓷的硬度数值最高,表明其具有极高的抗压能力和耐磨性。
结论通过本次实验,我们深入了解了材料的力学性能和硬度特点。
拉伸试验结果表明,钢材具有较高的屈服强度和延展性,铝材次之,而塑料则主要表现为塑性变形。
硬度测试结果显示,钢材具有较高的硬度数值,铝材较低,而陶瓷的硬度最高。
材料力学实验报告总结
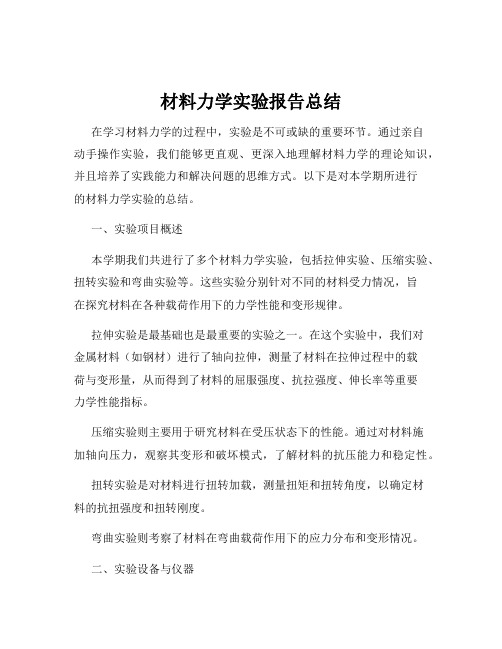
材料力学实验报告总结在学习材料力学的过程中,实验是不可或缺的重要环节。
通过亲自动手操作实验,我们能够更直观、更深入地理解材料力学的理论知识,并且培养了实践能力和解决问题的思维方式。
以下是对本学期所进行的材料力学实验的总结。
一、实验项目概述本学期我们共进行了多个材料力学实验,包括拉伸实验、压缩实验、扭转实验和弯曲实验等。
这些实验分别针对不同的材料受力情况,旨在探究材料在各种载荷作用下的力学性能和变形规律。
拉伸实验是最基础也是最重要的实验之一。
在这个实验中,我们对金属材料(如钢材)进行了轴向拉伸,测量了材料在拉伸过程中的载荷与变形量,从而得到了材料的屈服强度、抗拉强度、伸长率等重要力学性能指标。
压缩实验则主要用于研究材料在受压状态下的性能。
通过对材料施加轴向压力,观察其变形和破坏模式,了解材料的抗压能力和稳定性。
扭转实验是对材料进行扭转加载,测量扭矩和扭转角度,以确定材料的抗扭强度和扭转刚度。
弯曲实验则考察了材料在弯曲载荷作用下的应力分布和变形情况。
二、实验设备与仪器为了完成这些实验,我们使用了一系列专业的实验设备和仪器。
拉伸实验中,使用了万能材料试验机。
这台设备能够精确地施加拉伸载荷,并通过传感器测量载荷和变形量。
试验机配备了计算机控制系统,能够实时记录实验数据并生成相应的曲线。
压缩实验同样使用万能材料试验机,但需要配备不同的压头和夹具来适应压缩试验的要求。
扭转实验则使用扭转试验机,它可以精确地施加扭矩,并测量扭转角度。
在弯曲实验中,我们使用了三点弯曲试验机,通过加载点的位置和加载方式来模拟不同的弯曲情况。
此外,还使用了各种量具,如游标卡尺、千分尺等,用于测量材料的尺寸参数。
三、实验步骤与操作要点每个实验都有其特定的步骤和操作要点。
拉伸实验的步骤大致如下:首先,用游标卡尺测量试样的原始尺寸,包括直径或横截面尺寸以及标距长度。
然后,将试样安装在试验机的夹头上,确保试样的轴线与加载方向一致。
启动试验机,以一定的加载速度进行拉伸,同时观察计算机显示屏上的载荷变形曲线。
材料力学实验报告报告
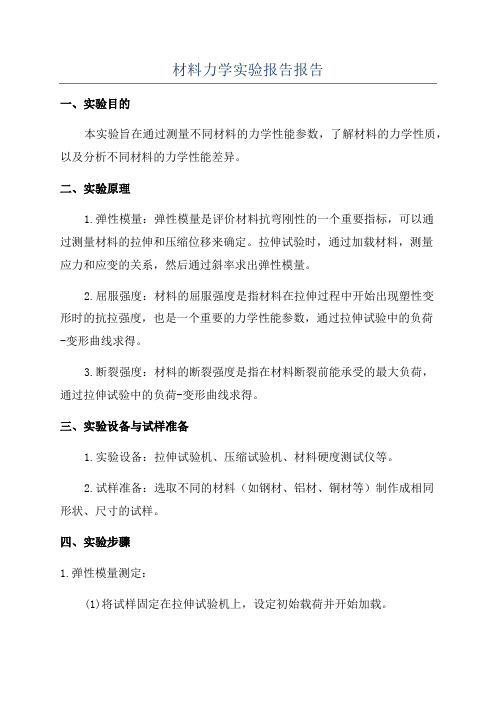
材料力学实验报告报告一、实验目的本实验旨在通过测量不同材料的力学性能参数,了解材料的力学性质,以及分析不同材料的力学性能差异。
二、实验原理1.弹性模量:弹性模量是评价材料抗弯刚性的一个重要指标,可以通过测量材料的拉伸和压缩位移来确定。
拉伸试验时,通过加载材料,测量应力和应变的关系,然后通过斜率求出弹性模量。
2.屈服强度:材料的屈服强度是指材料在拉伸过程中开始出现塑性变形时的抗拉强度,也是一个重要的力学性能参数,通过拉伸试验中的负荷-变形曲线求得。
3.断裂强度:材料的断裂强度是指在材料断裂前能承受的最大负荷,通过拉伸试验中的负荷-变形曲线求得。
三、实验设备与试样准备1.实验设备:拉伸试验机、压缩试验机、材料硬度测试仪等。
2.试样准备:选取不同的材料(如钢材、铝材、铜材等)制作成相同形状、尺寸的试样。
四、实验步骤1.弹性模量测定:(1)将试样固定在拉伸试验机上,设定初始载荷并开始加载。
(2)根据试验机上的位移计和负荷计,测量不同应力水平下的应变,并记录数据。
(3)通过绘制应力-应变曲线,根据直线部分的斜率求得材料的弹性模量。
2.屈服强度测定:(1)将试样固定在拉伸试验机上,设定初始载荷并开始加载。
(2)根据试验机上的压力计和位移计,测量不同载荷下的变形,并记录数据。
(3)通过绘制负荷-变形曲线,找到试样开始出现塑性变形的点,根据载荷计的读数求得材料的屈服强度。
3.断裂强度测定:(1)将试样固定在拉伸试验机上,设定初始载荷并开始加载。
(2)根据试验机上的压力计和位移计,测量试样在拉伸过程中的载荷和位移,并记录数据。
(3)通过绘制负荷-变形曲线,找到试样断裂前的最大负荷,并记录。
五、实验结果与讨论根据实验测量的数据,可以得到不同材料的力学性能参数,如弹性模量、屈服强度和断裂强度。
通过对比不同材料的实验结果,可以得出以下结论:1.钢材的弹性模量较大,机械性能优异。
2.铝材的屈服强度较低,耐腐蚀性能较好。
3.铜材的断裂强度较高,适用于承受较大载荷的工程应用。
材料力学实验报告1

材料力学实验报告院系班级学号姓名实验一金属材料拉伸实验实验日期:同组成员:一.实验目的1.测定低碳钢的屈服极限,强度极限,延伸率和断面收缩率。
2.测定铸铁的强度极限。
二.实验设备1.万能材料试验机2.游标卡尺三.实验步骤1.用游标卡尺在试件标距长度内取三处,测每一处截面两个相互垂直方向的直径,取其平均值。
最后以三处平均值中最小值作为试件的直径。
2.选择试验机的量程根据试件的强度极限和截面积,估算试件的最大载荷,选择合适的量程。
3.打开电源开关,打开油泵开关,关上回油阀,打开送油阀,将工作台抬高1-2厘米,消除自重,关上送油阀。
4.装夹试件,调读盘零点。
5.打开送油阀,缓慢加载,测试并观察,记录相关数据。
6.试件拉断后,关上送油阀,将试件取出,记录相关数据,测试件断后标距及断后直径。
7.实验整理四、实验记录及实验结果:1、试件尺寸记录- 1 -2、载荷及计算结果3、绘出低碳钢和铸铁的P-ΔL图五、实验结论与分析:1、分析比较两种典型金属材料的抗拉机械性能。
2、国家标准《金属拉伸实验方法》(GB228-87)中规定拉伸试样分为短试样和长试样,对同一材质、同一直径的圆形试样,短试样和长试样的断后延伸率是否相同?若不一样哪个大?- 2 -实验二铸铁材料压缩实验实验日期:同组成员:一.实验目的1.测定铸铁抗压强度极限σb。
2.观察铸铁在压缩时的变形和破坏现象。
二.实验设备1.万能材料试验机2.游标卡尺三.实验步骤1.测量试件直径用游标卡尺在试件相互垂直方向的直径各测一次,取其平均值。
2.选择试验机的量程根据试件的强度极限和截面积,估算试件的最大载荷,选择合适的量程。
3.打开电源开关,打开油泵开关,关上回油阀,打开送油阀,将工作台抬高1-2厘米,消除自重,关上送油阀。
4.安装试件,注意载荷对中。
调读盘零点。
5.打开送油阀,缓慢加载,测试并观察,试件压断后,关上送油阀,将试件取出,记录相关数据。
四、实验记录及实验结果:1、试件几何尺寸记录2、实验数据记录及处理五. 实验结论与分析:1、铸铁的破坏形式说明什么问题?2、铸铁压缩与拉伸破坏端面形状有什么不同?- 3 -- 4 - 实验三 弹性模量E 的测定实验日期:同组成员: 一.实验目的1.测定低碳钢的弹性模量E 。
- 1、下载文档前请自行甄别文档内容的完整性,平台不提供额外的编辑、内容补充、找答案等附加服务。
- 2、"仅部分预览"的文档,不可在线预览部分如存在完整性等问题,可反馈申请退款(可完整预览的文档不适用该条件!)。
- 3、如文档侵犯您的权益,请联系客服反馈,我们会尽快为您处理(人工客服工作时间:9:00-18:30)。
目录实验一金属材料的拉伸与压缩实验 (1)实验二金属材料的扭转实验…………………………………实验三金属材料的弹性模量E和波桑系数 测定…………………实验四桥路变换……………………………………………………实验五纯弯梁的正应力测定………………………………………实验六空心簿壁圆桶的主应力测定………………………………实验七偏心拉伸……………………………………………………实验一金属材料的拉伸与压缩试验一、一、实验目的1. 1.了解液压式材料试验机的工作原理,初步掌握试验机的操作规程。
2. 2.测定低碳钢的屈服(流动)极限σS,强度极限σb,延伸率δ和截面收缩率Ψ。
观察试件在拉伸过程中的各种现象(弹性、屈服、强化、颈缩)。
3. 3.测定铸铁材料的拉伸和压缩强度极限σb。
4. 4.比较低碳钢和铸铁的机械性质及破坏时的断口形式。
二、二、实验原理及计算测定金属材料的机械性质需要将试件制成符合国家标准的形状和尺寸。
一般规定,圆形截面的拉伸试件其标距L0与直径D0的关系为L0=10D0;压缩试件的高度H0与直径D0的关系为。
见图1.图1-1图1-2 为低碳钢和铸铁试件的P―ΔL图。
图1-2低碳钢试件在拉伸过程中,可分为四个阶段:1. 1.弹性阶段:载荷与变形成正比,P―ΔL图中表现为OA直线段。
屈服阶段:2. 2.P―ΔL图中的BC段,为一水平锯齿形曲线,此时材料暂时失去了抵抗变形的能力,表现为载荷在很小的范围内波动,而变形量则比较明显。
此时可观察到试验机测力盘上的主动针在某一刻度值范围内波动,取主动针回摆的最小读数值,即BC段中的下极限作为屈服载荷PS并记录下来,屈服极限σS可按下式计算:MN/m23. 3.强化阶段。
P―ΔL图中的CE阶段,在此阶段材料又恢复了抵抗变形的能力,要使它继续变形则必须增加载荷。
在此阶段(例如D点)卸载,则按图1-2所示的DD’斜直线回到D'短时间內若再加载,则P—∆L图大致仍按D'D斜直回到D点,然后又回沿DE曲线变化。
DD' OA。
4. 4.颈缩阶段P―ΔL图中的E点处,试件所承受的载荷为极限载荷P b,强度极限σb可按下式计算:MN/m2过E点后,试件局部某处的横截面积急剧变小,形成颈缩现象,使试件继续变形所需的载荷也相应减小,所以曲线下降,直至F点试件在颈缩处被拉断。
将拉断的试件紧密吻合后测得标距为L1,则延伸率按下式计算:测得断口处的最小直径D1,则截面收缩率为:由于铸铁是一种典型的脆性材料,不论是拉伸还是压缩,它均只有一个强度指标而且无塑性指标δ和Ψ,铸铁的唯一强度指标为强度极限σb,但是铸铁的抗拉和抗压能力是大不相同的。
三、三、实验设备及实验步骤实验所用设备为液压式材料试验机,其结构原理及操作步骤见附录A。
实验步骤:1. 1.用游标卡尺测量试件的原始尺寸。
2. 2.根据材料的强度极限σb和横截面积A0,估算试件的最大载荷(P0=σb A0)选择相应的测力盘,并配置对应的摆杆重锤。
3. 3.开启油泵马达钮,使工作油缸上升2cm左右,然后将主动针对准零位,被动针与主动针靠拢;调整好自动绘图器。
4. 4.安装试件。
5. 5.开始实验,加载应匀速缓慢。
对低碳钢拉伸试件,当主动针开始波动时,说明材料开始进入屈服阶段,应注意观察主动针回摆的范围,取最小值作为屈服载荷Ps。
6. 6.实验结束,取下试件。
测量低碳钢试件断裂后的标距L1和颈缩处的最小直径D1.7.7.清理实验场地,试验机一切机构复原。
8.8.根据实验记录进行有关计算四、四、注意事项1. 1.实验前应认真预习。
2. 2.试件夹紧后严禁使用电动机升降活动台。
3. 3.实验数据和计算经指导教师审阅后方能离开实验室。
五、五、实验报告及问题思考1. 1.实验设备(规格、型号)1)1)根据实验结果,绘制低碳钢和铸铁的曲线,叙述并标明低碳钢在拉伸过程中的四个变形阶段。
2)2)比较低碳钢和铸铁拉伸时的机械性质及破坏形式。
3)3)比较铸铁在拉伸和压缩时的强度极限σb。
4)4)为何铸铁试件在压缩时的破坏断面与轴线大致成.实验二扭转试验一、实验目的1. 1.观察并比较低碳钢和铸铁材料扭转变形现象及破坏形式。
2. 2.测定低碳钢的剪切屈极限τS和剪切强度极限τb。
3. 3.测定铸铁的剪切强度极限τb。
二、二、实验原理及计算圆形截面试件承受扭转时,材料处于纯剪应力状态。
因此常用扭转试验来分析研究不同材料在纯剪应力作用下的机械性质。
图2-1所示为低碳钢试件的扭矩Mn与扭转角Φ的关系曲线。
当扭矩Mn小于Mp时,材料处于弹性状态,Mn-Φ曲线的OA段为直线段,此时材料遵守剪切虎克定律。
扭矩Mn超过Mp后,试件横截面上的剪应力分布不再是线形的,首先,在圆形横截面的外部处材料产生屈服并逐渐向内扩展形成环形塑性区,见图2-2,同时Mn-Φ图变成曲线,见图2-1。
此后,随着试件继续扭转变形,塑性区不断向圆心扩展,Mn-Φ曲线稍微上升,直至B点趋于平坦,扭转试验机度盘上指针几乎不动或摆动,指针摆动的最小值既是试件全部屈服所对应的扭矩M s,这时塑性区占据了几乎全部截面,见图2-2.图2-1图2-2根据塑性理论τS,可按下列近似公式计算:式中,为圆形截面的抗扭截面模量。
继续对试件加载,则试件再继续变形,材料进一步强化,到达Mn-φ曲线上的C点,试件发生断裂破坏。
由扭转试验机度盘上读出最大扭矩M b。
与τS 相似,τb可按近似公式计算:铸铁的Mn-Φ曲线如图2-3所示。
从开始受扭,直到破坏,近似为一直线。
故近似地按弹性应力公式计算:试件受扭,材料处于纯剪应力状态,见图2-4。
在与试件轴线成角±45º的螺旋而上,分别受到主应力σ1=τ(拉应力)和σ3= τ(压应力)的作用。
由于低碳钢的抗拉能力大于抗剪能力,故从横截面剪断;而铸铁的抗拉能力较抗剪能力弱,故沿着与σ1方向呈正交的方向拉断。
图2-3 图2-4三、三、实验设备及实验步骤实验所用设备为K-50型扭转试验机或NJ-100B型扭转试验机,其结构原理及操作步骤见附录B。
实验步骤:1. 1.试件准备。
用游标卡尺在试件的中央和两端共三处按两个相互垂直的方向测量试件直径,取最小处的平均值D计算Wn。
2. 2.试验机准备。
根据试件的剪切强度极限τb估算M b,选择合适的测扭矩度盘。
调整度盘使指针对零,检查自动绘图器,安装试件。
3. 3.进行试验。
对低碳钢试件,先用粉笔在试件上沿轴线方向作一标记线,以便观察试件的扭转变形,用手动方式缓缓而匀速地加载,到达材料屈服时,记录M s,然后卸掉手柄,用电动机加载直至试件破坏,停机,记录M b,注意观察扭角指示器的读数并记录之。
4. 4.铸铁试件的实验步骤与低碳钢相同,可直接用手动的方式加载直至试件破坏。
四、四、注意事项参阅附录B扭转试验机使用时的注意事项。
五、五、实验报告及问题思考1. 1.实验设备(规格、型号)2. 2.实验前试件尺寸记录4,问题思考(1),比较两种材料破坏后的断口形式,并解释其破坏原因。
(2),根据拉伸、压缩和扭转三种试验结果,综合分析低碳钢和铸铁材料的机械性质实验三桥路联接变换实验一、实验目的1. 1.了解电阻应变仪的测量原理,练习用电阻应变仪进行单点半桥接法,单点全桥接法测量应变。
2. 2.熟练测量电桥的应用,了解温度补偿的特点,掌握单点半桥、全桥的接线方法。
3. 3.比较不同桥路接线方式的特点和测量精度。
二、实验设备电阻应变仪、等强度梁实验装置、百分表挠度仪、温度补偿块、游标卡尺、钢尺。
三实验原理应变测量电桥如图3-1,若四个桥臂分别接入规格相同的电阻应变R1、R2、R3、R4。
当构件变形时,贴在构件表面的应变片则应有相应的应变ε1,ε2,ε3,ε4。
根据应变仪的工作原理,应变仪测得的读数应变为由上式可知采用不同的布片,接桥方案,将得到不同精度的测量结果。
若利用测量电桥“对臂同号相加,异号相减;邻臂同号相减,异号相加”这一特性,合理布片,接桥,则可以消除温度效应,还可以提高电桥的放大系数,增大读数应变。
本实验所采用的是等强度梁装置(图3-2)。
在梁的上下表面沿纵向分别粘贴应变片R1、R2、R3、R4,在补偿块上粘贴补偿片R t。
在实验中采用三种不同的接桥方式,其具体形式见表3-1。
对半桥外补偿接法,,对半桥自补偿接法,,对全桥自补偿接法,,图3-2四、四、实验步骤1.1.半桥外补偿联接。
采用单点半桥接线法。
操作步骤参见静态电阻仪的使用说明书,预调平衡后先加初载,使得百分表读数为0.1mm。
然后逐级加载。
按百分表读数增量为0.2mm,自0.0mm加到1.0mm,记录相应的读数应变。
2.2.半桥自补偿联接。
采用单点半桥接线法:操作和加载步骤与半桥外补偿联接实验相同。
3.3.全桥自补偿联接。
采用单点全桥接线法。
操作步骤参见静态应变仪的使用说明书,加载方案与半桥联接实验相同。
五、五、注意事项参见附录C中YJ-X2型电阻应变仪操作步骤中(三、注意事项)。
六、六、实验报告及问题思考由公式,式中f为梁端挠度,h为梁的厚度,L为梁的长度,求出应c), 根据测试结果,试比较三种接桥方法的优缺点。
实验四金属材料弹性模量E和泊松比μ的测定一、一、实验目的1.1.在金属材料的弹性范围内验证虎克定律。
2.2.测定材料的弹性模量E和泊松比μ。
3.3.掌握电阻应变仪的操作方法和半桥联接。
二、二、实验原理及计算本实验采用电测法测定E和μ。
电测原理见附录C。
金属材料在弹性范围内服从虎克定律:σ=Eε写成式中P——载荷;A——试件截面积;——纵向应变;由电测法测得。
同样,横向应变也可由电测法测得,故可计算泊松比为此,沿试件的轴线和垂直于轴线的方向各贴一片电阻应变片作为工作片R1(R2),在与试件相同材料的外补偿块上贴一片电阻应变片作为温度补偿片R t,采用半桥外补偿按图4-1将R1(R2)、R t与电阻应变仪联接,即可进行测量。
为保证实验的精确性,本实验采用“增量法”加载,即每增加一级载荷,可在电阻应变仪上读得一个应变值,最后取应变值读数差的平均值Δε代入公式计算出材料的弹性模量E和泊松比μ,即三、三、实验设备及实验步骤实验所用设备为多用试验台,静态电阻应变仪。
(静态电阻应变仪的结构原理及操作步骤见附录C)。
实验步骤:1. 1.测量试件尺寸,将试件安装在多用试验台上。
2. 2.参照图4-1将电阻应变片以半桥外补偿法与应变仪联接。
3. 3.根据电阻应变片的灵敏系数调节应变仪灵敏系数拨钮,使其相对应(一般已调节完毕)。
4. 4.参照附录C中的电阻应变仪操作步骤将电阻应变仪调节到正常工作状态。
5. 5.逐级缓慢加载,并记录测点的应变值。
6. 6.重复实验2次,以获得理想的实验数据。
7.7.实验结束,清理场地,应变仪电源关闭,一切机构复原。