丙酮和水连续精馏塔的设计
化工原理课程设计--丙酮水连续精馏塔的设计
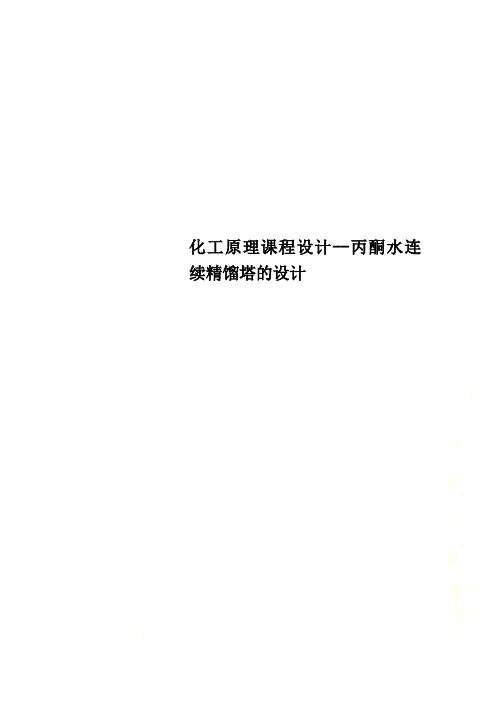
常用的加热介质有饱和水蒸气和烟道气。饱和水蒸汽是一种应用最广泛的加热介质,由于饱和水蒸汽冷凝时的传热系数很高,可以通过改变蒸汽压力准确地控制加热速度。燃料燃烧所排放的烟道气温度可达100~1000℃,适用于高温加热,烟道气的缺点是是比热容及传热系数很低,加热温度控制困难,本设计选用300KPa(温度为133.3)的饱和水蒸气作为加热介质,水蒸气易获得、清洁、不易腐蚀加热管,不但成本会相应降低,塔结构也不复杂。
得出全塔共16块板(包括再沸器),进料位置是第3块板。
第三章精馏塔主要工艺尺寸的设计计算
3.1物性数据计算
3.1.1密度计算
已知:混合液体密度: ( 为质量分数, 为平均相对分子质量)
混合气体密度:
已知: =57.117℃ =61.275℃ =97.737℃
=0.9564 =0.8263 =0.0784
由于 ,查图得出
验算降液停留时间
精馏段:
提馏段:
停留时间 ,故降液管可用。
⑷降液底隙高度
精馏段:
取降液底隙的流速
则
提馏段:
取降液底隙的流速
则
3.2.4塔板布置
⑴塔板的分块
因为 ,故塔板可采用分块式,查表可知,塔板可分为3块。
⑵边缘区宽度确定
取
⑶开孔区面积计算
开孔区面积 ,对单溢流型塔板,开孔区面积可用下式计算,即
⑴泡罩塔板
泡罩塔板是最早在工业上大规模应用的板型之一,有成熟的设计方法和操作经验。气体接触良好,操作弹性范围大,而且耐油污、不易堵塞。20世纪上半叶,随着化学工业、炼油与石油 化学工业的高速发展,在生产中大量应用着蒸馏、吸收等气液两相传质操作。
⑵筛孔塔板
筛板塔普遍用作H2S-H2O双温交换过程的冷、热塔。应用于蒸馏、吸收和除尘等。在工业上实际应用的筛板塔中,两相接触不是泡沫状态就是喷射状态,很少采用鼓泡接触状态的。
丙酮-水化工原理课程设计
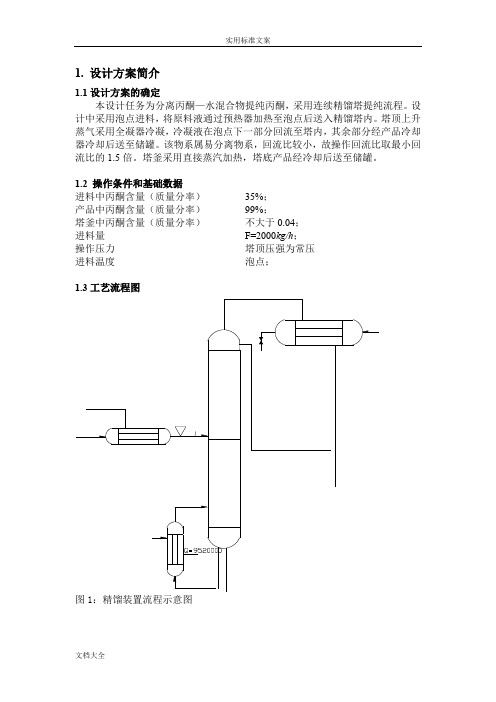
1. 设计方案简介1.1设计方案的确定本设计任务为分离丙酮—水混合物提纯丙酮,采用连续精馏塔提纯流程。
设计中采用泡点进料,将原料液通过预热器加热至泡点后送入精馏塔内。
塔顶上升蒸气采用全凝器冷凝,冷凝液在泡点下一部分回流至塔内,其余部分经产品冷却器冷却后送至储罐。
该物系属易分离物系,回流比较小,故操作回流比取最小回流比的1.5倍。
塔釜采用直接蒸汽加热,塔底产品经冷却后送至储罐。
1.2 操作条件和基础数据进料中丙酮含量(质量分率)35%;产品中丙酮含量(质量分率)99%;塔釜中丙酮含量(质量分率)不大于0.04;进料量F=2000kg/h;操作压力塔顶压强为常压进料温度泡点;1.3工艺流程图2.精馏塔的物料衡算2.1 原料液及塔顶、塔底产品的摩尔分率 丙酮的摩尔质量 M A =58.08kg/kmol 水的摩尔质量 M B =18.02kg/kmo l x F =02.18/56.008.58/35.008.58/35.0+=0.143x D =02.18/01.008.58/99.008.58/99.0+=0.968x W =02.18/69.008.58/40.008.58/40.0+=0.0132.2 原料液及塔顶、塔底产品的平均摩尔质量M F =0.143×58.08+(1-0.143)×18.02=23.75kg/kmol M D =0.968×58.08+(1-0.968)×18.02=56.80kg/kmol M W =0.013×58.08+(1-0.013)×18.02=18.54kg/kmol2.3 物料衡算原料进料量为2000kg/h F=2000/27.51=72.70kmol/h总物料衡算 72.70=D+W丙酮的物料衡算 72.70×0.143=0.968D+0.013W 联立解得 D=9.90 W=62.803.塔板数的确定3.1理论塔板数N T的求取3.1.1求最小回流比及操作回流比丙酮-水是非理想物系,先根据丙酮-水平衡数据(见下表1),绘出平衡线,如下图所示。
丙酮-水精馏分离板式塔设计
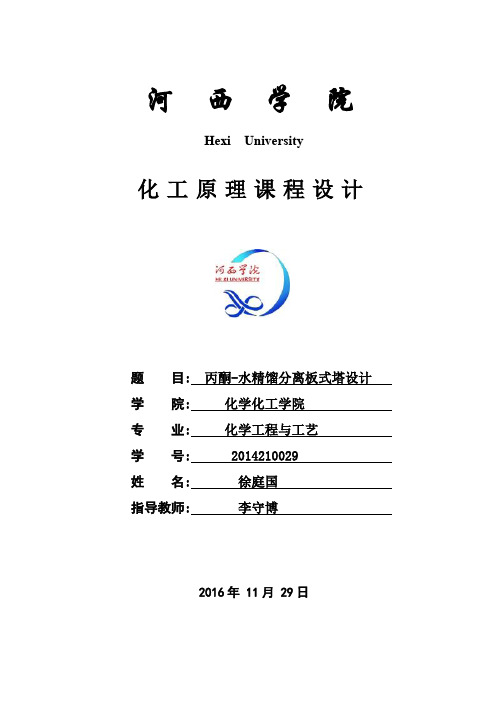
河西学院Hexi University化工原理课程设计题目: 丙酮-水精馏分离板式塔设计学院: 化学化工学院专业: 化学工程与工艺学号: ********** **: *******: ***2016年 11月 29日化工原理课程设计任务书一、设计题目丙酮-水精馏分离板式塔设计二、设计任务及操作条件1.设计任务生产能力(进料量)60000吨/年操作周期7200小时/年进料组成30%(丙酮)(质量分率,下同)塔顶产品组成≥96%(丙酮)塔底产品组成≤5%(丙酮)回流比,自选单板压降≤700Pa冷却水温度30℃2.操作条件操作压力塔顶为常压进料热状态进料温度60℃加热蒸汽 0.5MPa (表压)三、设计内容1.设计方案的选择及流程说明2.塔的工艺计算3.主要设备工艺尺寸设计(1)塔径、塔高及塔板结构尺寸的确定(2)塔板的流体力学校核(3)塔板的负荷性能图(4)总塔高、总压降及接管尺寸的确定4.辅助设备选型与计算5.设计结果汇总6.绘制生产工艺流程图及精馏塔设计条件图7.设计评述目录1.设计背景与原理 (1)1.1精馏塔的设计原理 (1)1.2确定设计方案 (1)1.3设计原则 (2)1.3.1满足工艺和操作的要求 (2)1.3.2满足经济的要求 (2)1.3.3满足安全生产的要求 (2)1.4板式塔的选择 (3)1.4.1塔设备的分类 (3)1.4.2筛板塔的优缺点 (3)2.工艺设计计算 (3)2.1设计方案的确定 (3)2.2工艺流程图 (4)2.3精馏塔的物料衡算 (4)2.3.1.料液.塔顶及塔底产品含甲醇的摩尔分率 (4)2.3.2.原料液,塔顶及塔底产品的平均摩尔质量 (4)2.3.3物料衡算原料处理量 (4)2.4塔板数的确定 (5)2.4.1理论塔板数的求取 (5)2.4.2实际塔板数NT的求取 (8)2.5精馏塔的工艺条件及有关物性数据的计算 (9)2.5.1操作压强的计算 (9)2.5.2平均摩尔质量计算 (9)2.5.3平均密度计算 (10)2.5.4液体平均表面张力的计算 (11)2.5.5液体平均粘度μLm的计算 (12)2.5.6精馏塔气液负荷计算 (13)3.精馏塔工艺尺寸设计 (13)3.1塔径的计算 (13)3.1.3空塔流速 (15)3.2精馏塔高度的计算 (15)3.2.1.精馏塔的有效高度 (15)3.2.2.精馏塔总高度 (15)3.3塔板主要工艺尺寸的计算 (17)3.3.1溢流装置计算 (17)3.3.2塔板布置 (19)3.4筛板的流体力学实验算 (20)3.4.1气体通过筛板压降相当的液柱高度 (20)3.4.2液面落差 (22)3.4.3雾沫夹带量的验算 (22)3.4.4漏液的验算 (22)3.4.5液泛 (23)3.5塔板负荷性能图 (24)3.5.1精馏段 (24)3.5.2提馏段 (26)4 辅助设备选型与计算 (29)4.1接头管设计 (29)4.2热量衡算 (30)4.2.1加热介质的选择 (30)4.2.2冷凝剂的选择 (30)4.2.3热量衡算 (30)4.3冷凝器的选择 (32)4.4再沸器的选择 (32)4.5贮罐的计算 (33)5操作说明 (33)附录 (33)参考文献 (34)致谢 (35)附图 (36)丙酮-水混合液筛板精馏塔设计徐庭国摘要:本次设计是针对二元物系的精馏问题进行分析、选取、计算、核算、绘图等,是较完整的精馏设计过程。
丙酮-水-连续精馏塔的设计

第一局部设计概述1设计题目:丙酮-水连续精馏塔的设计2工艺条件〔1〕生产能力:17000吨/年〔料液〕〔2〕工作日:300天,每天24小时连续运行〔3〕原料组成:50%丙酮,50%水〔质量分率,下同〕〔4〕产品组成:馏出液99.5%的丙酮溶液,塔底废水中丙酮含量0.05% 〔5〕进料温度:泡点〔6〕加热方式:直接蒸汽加热〔7〕塔顶压力:常压〔8〕进料热状态:泡点〔9〕回流比:自选〔10〕加热蒸气压力:0.5MPa〔表压〕〔11〕单板压降≤0.7kPa。
3设计内容1) 精馏塔的物料衡算;2) 塔板数确实定;3) 精馏塔的工艺条件及有关物性数据的计算;4) 精馏塔的塔体工艺尺寸计算;5) 塔板主要工艺尺寸的计算;6) 塔板的流体力学验算;7) 塔板负荷性能图;8) 精馏塔接管尺寸计算;9) 对设计过程的评述和有关问题的讨论。
第二局部塔的工艺计算1查阅文献,整理有关物性数据1.1水和丙酮的性质表1.水和丙酮的粘度表3.水和丙酮密度表4.水和丙酮的物理性质表5. 丙酮—水系统由以上数据可作出t-y〔x〕图如下〔图—1〕由以上数据作出相平衡y-x 线图相平衡线 x-y图00.10.20.30.40.50.60.70.80.9100.10.20.30.40.50.60.70.80.91xy图—22精馏塔的物料衡算2.1进料液及塔顶、塔底产品的摩尔分数丙酮的摩尔质量 A M =58.08 Kg/kmol 水的摩尔质量 B M =18.02 Kg/kmol2.2及塔顶、塔底产品的平均摩尔质量M F =0.2368⨯58.08+〔1-0.2368〕⨯18.02=27.506 kg/kmol M D = 0.9856⨯58.08+ (1-0.9856 )⨯18.02=57.442 kg/kmol M W =0.00016⨯58.08+〔1-0.00016〕⨯18.02=18.026 kg/kmol2.3物料衡算原料处理量 F=〔17000⨯1000/〔300⨯24〕〕/27.5060=85.84 kmol/h 总物料衡算85.84=D+W丙酮的物料衡算85.84⨯0.2368=0.9841D+0.00016 W 联立解得 D=20.65 kmol/hW=65.19 kmol/h3操作线方程与塔板数确实定3.1理论塔板层数N T 的求取丙酮—水可看成理想物系,可采用图解法求取理论塔板数。
分离丙酮---水连续浮阀式精馏塔工艺设计
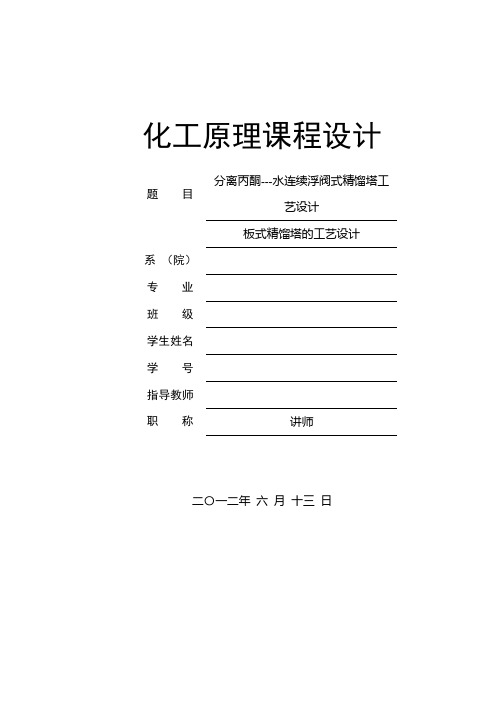
3.3热量恒算8
3.3.1热量示意图8
3.3.2加热介质的选择9
3.3.3热量衡算…………………………………………………………………………………9
3.4板数的确11
3.4.1精馏段与提馏段操作线方程及 线方程………………………………………………11
3.4.2全塔效率 13
3.4.3实际塔板数14
3.8塔板负荷性能图38
3.8.1液沫夹带线关系式………………………………………………………………………38
3.8.2液相负荷下限线关系式…………………………………………………………………39
3.8.3漏液线系式………………………………………………………………………………39
3.8.4液相负荷限线关系式……………………………………………………………………40
二、设计数据及条件
生产能力:年处理丙酮-水混合液(混合气):80000万吨(开工率300天/年);
原料:原料加料量F=11111.1kg/h
丙酮含量为30 %(质量百分率,下同)的常温液体(气体);
分离要求:塔顶丙酮含量不低于(不高于)98.0%;
塔底丙酮含量不高于(不低于)2.0%。塔顶压力p=0.101325Mpa(绝压)塔釜采用0.5Mpa(表压)饱和蒸汽间接加热
3.5精馏塔的工艺条件及有关物性数据的计算15
3.5.1操作温度的计算15
3.5.2操作压强的计算17
3.5.3塔内各段气液两相的平均分子量17
3.5.4各6平均温度下液体表面张力的计算22
3.5.7气液负荷的计算22
3.6精馏塔的塔体工艺尺寸计算23
0.815
62.1
0.80
0.898
丙酮水连续精馏塔设计方案

丙酮水连续精馏塔设计方案第一章流程的确定及说明一.加料方式加料方式有两种:高位槽加料和泵直接加料。
采用高位槽加料,通过控制液位高度,可以得到稳定的流量和流速,通过重力加料,可以节省一笔动力费用,但由于多了高位槽,建设费用相应增加;采用泵加料,受泵的影响,流量不太稳定,流速也忽大忽小,从而影响了传质效率,但结构简单,安装方便。
如果采用自动控制泵来控制泵的流量和流速,其控制原理较复杂,且设备操作费用高。
本设计采用高位槽进料。
二.进料状况进料状况一般有冷液进料和泡点进料。
对于冷液进料,当组成一定时,流量一定,对分离有利,省加热费用,但其受环境影响较大;而泡点进料时进料温度受季节、气温变化和前段工序波动的影响,塔的操作比较容易控制。
此外,泡点进料时,基于恒摩尔流假定,精馏段和提镏段的塔径基本相等,无论是设计计算还是实际加工制造这样的精馏塔都比较容易。
综合考虑,设计上采用泡点进料。
三.塔顶冷凝方式塔顶冷凝采用全凝器,塔顶出来的气体温度不高,用水冷凝。
四.回流方式回流方式可分为重力回流和强制回流。
对于小塔型,回流冷凝器一般安装在塔顶,其优点是回流冷凝器无需支撑结构,其缺点是回流冷凝器回流控制较难。
如果需要较高的塔处理量或塔板数较多时,回流冷凝器不适合于塔顶安装,且塔顶冷凝器不易安装、检修和清理。
在此情况下,可采用强制回流,塔顶上升蒸汽量采用冷凝器以冷回流流入塔中。
本次设计为小型塔,故采用重力回流。
五.加热方式加热方式分为直接蒸汽加热和间接蒸汽加热,直接蒸汽加热时蒸汽直接由塔底进入塔内,由于重组分是水,故省略加热装置。
但在一定的回流比条件下塔底蒸汽对回流液有稀释作用,使理论塔板数增加,费用增加。
间接蒸汽加热时通过加热器使釜液部分汽化,维持原来的浓度,以减少理论板数,缺点是增加加热装置。
本次设计采用间接蒸汽加热。
六.加热器采用U型管蒸汽间接加热器,用水蒸气作加热剂。
因为塔较小,可将加热器放在塔内,即再沸器。
这样釜液部分汽化,维持了原有浓度,减少理论塔板数。
(完整word版)丙酮与水的连续精馏塔课程设计

化工原理课程设计题目:丙酮-水分离板式回收塔设计系别: 化学与材料工程系专业:_ 化学工程与工艺学号: **********姓名:指导教师:2016年1 月8 日附: 回收塔设计任务书一、设计题目丙酮与水分离板式回收塔设计二、设计任务及操作条件1、生产能力(进料量):300000吨/年。
2、操作周期:7200小时/年。
3、进料组成:6.2%(质量分率,下同)。
4、塔顶产品组成:>72%。
5、塔底产品组成:<0.02%。
6、操作压力:塔顶为常压。
7、进料热状态:自选。
8、加热蒸汽:低压蒸汽。
9、设备类型:筛板、浮阀塔板。
10、回收率: η= 99%11、厂址:安徽地区。
三、设计内容设计方案的选择及流程说明。
塔的工艺计算。
主要设备工艺尺寸设计:塔径、塔高及塔板结构尺寸的确定;塔板的流体力学校核;塔板的负荷性能图;总塔高、总压降及接管尺寸的确定。
丙酮-水分离板式回收塔设计4、辅助设备选型及计算。
5、设计结果汇总。
6、设计评述。
7、工艺流程图及塔工艺条件图。
附图一:回收塔的工艺流程图。
附图二:回收塔的工艺条件图。
附图三:槽式液体分布器目录一、前言 (1)1.1 塔设备的类型 (1)1.2 操作条件确定 (2)1.3 换热器的选择 (3)1.4 泵的选择 (4)二、设计说明书符号表 (4)三、丙酮与水有关物性数据 (6)3.1 水和丙酮的性质 (6)四、精馏塔的工艺设计 (9)4.1 液相浓度计算 (9)4.2 温度计算 (10)4.3 气相组成计算 (10)4.4 平均相对挥发度的计算 (11)4.5 物料衡算 (11)4.6 提馏段操作线方程 (12)4.7 逐板法确定理论板数及进料位置 (13)4.8 全塔效率的计算 (13)4.8.1 粘度计算 (13)4.8.2 板效率计算 (14)4.9 实际塔板数及加料位置的计算 (14)4.10 物性数据计算 (14)4.10.1 密度计算 (14)4.10.2 摩尔组成计算 (16)4.10.3 操作压力计算 (17)4.10.4 混合液体表面张力计算 (17)4.11 精馏塔的主要工艺尺寸的计算 (21)4.11.1 体积流量的计算 (21)4.11.2 塔径的计算 (22)4.11.3 溢流装置的计算 (23)4.12 精馏塔流体力学校核 (24)4.12.1 塔板压降 (24)4.12.2 液面落差 (24)4.12.3 液沫夹带 (25)4.12.4 漏液 (25)4.12.5 液相负荷下限线 (25)4.12.6 液相负荷上限线 (26)4.12.7 液泛线 (26)五、热量衡算 (28)5.1 塔顶冷凝器和塔底再沸器的热负荷 (28)5.1.1 冷凝器的热负荷 (28)5.1.2 再沸器的热负荷 (28)5.2 塔的辅助设备的设计计算 (29)5.2.1 冷凝器和再沸器的计算与选型 (29)1、冷凝器的计算与选型 (29)2、再沸器的设计选型 (30)5.3 泵的设计选型 (30)5.3.1 塔总高度计算 (30)5.3.2 进料管线管径 (31)5.3.3 原料泵的选择 (32)六、参考文献 (34)七、结束语 (35)一、前言丙酮是重要的有机合成原料,用于生产环氧树脂、聚碳酸酯、有机玻璃、医药、农药等。
丙酮-水浮阀精馏塔设计

河西学院Hexi University化工原理课程设计题目: 丙酮-水浮阀精馏塔设计学院: 化学化工学院专业:_ 化学工程与工艺学号: 11姓名: 连亮国指导教师: 杨自嵘2016年 12 月 2 日化工原理课程设计任务书一、设计题目丙酮-水连续精馏塔设计二、设计任务及操作条件1.设计任务处理量: 9万吨/年操作周期: 7200 小时/年(300天/年)原料组成: 25%的丙酮和75%的水(质量分率,下同)产品要求:馏出液99%的丙酮溶液,塔底水中丙酮含量2%回流比:R/R min=单板压降:≤2.操作条件操作压力:塔顶为常压进料热状态:泡点进料进料状况:泡点进料加热蒸汽;间接水蒸气加热3.设备型式筛板或浮阀塔板4.厂址张掖地区三、设计内容1.设计方案的选择及流程说明2.塔的工艺计算3.主要设备工艺尺寸设计(1)塔径、塔高及塔板结构尺寸的确定(2)塔板的流体力学校核(3)塔板的负荷性能图(4)总塔高、总压降及接管尺寸的确定4.辅助设备选型与计算5.设计结果汇总6.绘制生产工艺流程图及精馏塔设计条件图7.设计评述目录1 概述 (1)设计方案的选择和论证 (2)设计思路 (2)选定设计方案的原则 (2)确定设计方案 (2)精馏方式的选定 (2)加热方式的选取 (2)操作压力的选取 (3)回流比的选择 (3)塔顶冷凝器的冷凝方式与冷却介质的选择 (3)板式塔的选择 (3)关于附属设备的设计 (3)设计流程 (3)2.精馏塔的物料衡算 (4)有关物性数据 (4)原料液及塔顶,塔底产品的摩尔分率 (5)原料液及塔顶塔底产品的平均摩尔质量 (6)总物料衡算处理 (6)用拉格朗日差值求温度 (6)3有关物性数据的计算 (6)精馏段和提留段平均摩尔质计算 (6)密度的计算 (7)液体表面张力计算 (8)平均表面张力计算 (9)粘度 (9)操作压力计算 (9)4.精馏塔的工艺条件的计算 (10)理论板数的确定 (10)求最小回流比及操作回流比 (11)求精馏塔的气、液相负荷 (12)求操作线方程 (12)用芬斯克方程式求理论塔板数 (12)实际板层数的求取 (14)总的塔板数 (14)E (14)全塔效率T5. 精馏塔的塔体工艺尺寸计算 (14)塔径的计算 (14)精馏塔有效高度的计算 (17)塔板主要工艺尺寸计算 (18)溢流装置计算 (18)塔板布置 (21)塔板的流体力学验算 (26)气体通过浮阀塔板的压降 (26)淹塔 (27)雾沫夹带验算 (28)塔板负荷性能图 (30)雾沫夹带线 (30)液泛线 (31)液相负荷上限线 (32)漏液线 (33)液相负荷下限线 (33)6.热量衡算 (36)塔顶热量 (36)冷却介质消耗量: (37)焓值衡算 (38)对全塔进行热量衡算: (39)加热水蒸汽用量: (39)7.塔的辅助设备及附件的计算与选型 (39)冷凝器 (39)再沸器 (40)塔顶回流管管径计算 (42)塔顶蒸气出口管径计算 (42)塔釜出料管径计算 (43)再沸器进料管径计算 (43)筒体与封头 (43)筒体 (43)封头 (44)除沫器 (44)裙座 (44)人孔 (45)塔总体高度的计算 (45)吊柱 (45)8. 精馏塔设计结果一览表 (45)9 设计评述 (47)参考文献 (47)致谢 (48)附图 (49)丙酮-水连续精馏塔设计连亮国摘要:本设计对丙酮和水的分离设备─浮阀精馏塔做了较为详细的叙述,本次设计是针对二元物系的精馏问题进行分析、选取、计算、核算、绘图等,是较完整的精馏设计过程,我对此塔进行了工艺设计,主要包括它的辅助设备及进出口管路的计算,画出了塔板负荷性能图,对设计结果进行了汇总,并且画出了精馏塔装配图,工艺流程图和部分主要部件图。
- 1、下载文档前请自行甄别文档内容的完整性,平台不提供额外的编辑、内容补充、找答案等附加服务。
- 2、"仅部分预览"的文档,不可在线预览部分如存在完整性等问题,可反馈申请退款(可完整预览的文档不适用该条件!)。
- 3、如文档侵犯您的权益,请联系客服反馈,我们会尽快为您处理(人工客服工作时间:9:00-18:30)。
化工原理设计任务书设计题目:丙酮-水二元物料板式精馏塔设计条件:常压: 1p atm =处理量: 60000吨/年进料组成: 25%丙酮,75%水(质量分率,下同)馏出液组成:0.965D X =釜液组成: 馏出液 99%丙酮,釜液2%丙酮塔顶全凝器 泡点回流回流比: R=1.5Rmin加料状态: 1.0q =单板压降: 0.7a kp ≤设计任务:完成该精馏塔的工艺设计(包括物料衡算、热量衡算、筛板塔的设计算)。
画出带控制点的工艺流程图、塔板负荷性能图、精馏塔工艺条件图。
写出该精馏塔的设计说明书,包括设计结果汇总和设计评价。
摘要利用混合物中各组分挥发能力的差异,通过液相和气相的回流,使气、液两相逆向多级接触,在热能驱动和相平衡关系的约束下,使得易挥发组分(轻组分)不断从液相往气相中转移,而难挥发组分却由气相向液相中迁移,使混合物得到不断分离,称该过程为精馏。
该过程中,传热、传质过程同时进行,属传质过程控制原料从塔中部适当位置进塔,将塔分为两段,上段为精馏段,不含进料,下段含进料板为提馏段,冷凝器从塔顶提供液相回流,再沸器从塔底提供气相回流。
气、液相回流是精馏重要特点。
在精馏段,气相在上升的过程中,气相轻组分不断得到精制,在气相中不断地增浓,在塔顶获轻组分产品。
在提馏段,其液相在下降的过程中,其轻组分不断地提馏出来,使重组分在液相中不断地被浓缩,在塔底获得重组分的产品,精馏过程与其他蒸馏过程最大的区别,是在塔两端同时提供纯度较高的液相和气相回流,为精馏过程提供了传质的必要条件。
提供高纯度的回流,使在相同理论板的条件下,为精馏实现高纯度的分离时,始终能保证一定的传质推动力。
所以,只要理论板足够多,回流足够大时,在塔顶可能得到高纯度的轻组分产品,而在塔底获得高纯度的重组分产品。
通过对精馏塔的运算,主要设备的工艺设计计算——物料衡算、热量衡算、工艺参数的选定、设备的结构设计和工艺尺寸的设计计算,可以得出精馏塔的各种设计如塔的工艺流程、生产操作条件及物性参数是合理的,以保证精馏过程的顺利进行并使效率尽可能的提高。
本设计是以丙酮――水物系为设计物系,以筛板塔为精馏设备分离丙酮和水。
筛板塔是化工生产中主要的气液传质设备,此设计针对二元物系丙酮--水的精馏问题进行分析,选取,计算,核算,绘图等,是较完整的精馏设计过程。
通过逐板计算得出理论板数11块,回流比为1.3032,算出塔效率为0.446,实际板数为25块,进料位置为第7块,在板式塔主要工艺尺寸的设计计算中得出塔径为1.2米,有效塔高6.6米。
通过浮阀塔的流体力学验算,证明各指标数据均符合标准。
在此次设计中,对塔进行了物料衡算,本次设计过程正常,操作合适。
目录第一部分设计概述 (1)一、设计题目: (1)二、工艺条件: (1)三、设计内容 (1)四、工艺流程图 (1)第二部分塔的工艺计算 (3)一、查阅文献,整理有关物性数据 (3)二、全塔物料衡算与操作方程 (7)三、全塔效率的估算 (7)四、实际塔板数 (8)五、精馏塔主题尺寸的计算 (10)1 精馏段与提馏段的汽液体积流量102 塔径的计算123 塔高的计算164 塔板结构尺寸的确定165弓形降液管176开孔区面积计算187 筛板的筛孔和开孔率18六、筛板的流体力学验算 (20)1塔板压降202液面落差20七、塔板负荷性能图 (22)1精馏段塔板负荷性能图222提馏段塔板负荷性能图25八、精馏塔的主要附属设备................................................ 错误!未定义书签。
1.塔顶全凝器设计计算292.料液泵设计计算3管径计算30九、设计结果一览表 (29)十、符号说明 (33)十一、附图 (1)十二、参考文献 (4)十三. 设计小结第一部分设计概述一、设计题目:筛板式连续精馏塔及其主要附属设备设计二、工艺条件:生产能力:90000吨/年(料液)年工作日:300天原料组成:25%丙酮,75%水(质量分率,下同)产品组成:馏出液 99%丙酮,釜液2%丙酮操作压力:塔顶压强为常压进料温度:泡点进料状况:泡点加热方式:直接蒸汽加热回流比: R/Rmin=1.5三、设计内容1、确定精馏装置流程,绘出流程示意图。
2、工艺参数的确定基础数据的查取及估算,工艺过程的物料衡算及热量衡算,理论塔板数,塔板效率,实际塔板数等。
3、主要设备的工艺尺寸计算板间距,塔径,塔高,溢流装置,塔盘布置等。
4、流体力学计算流体力学验算,操作负荷性能图及操作弹性。
5 、主要附属设备设计计算及选型塔顶全凝器设计计算:热负荷,载热体用量,选型及流体力学计算。
料液泵设计计算:流程计算及选型。
四、工艺流程图丙酮—水溶液经预热至泡点后,用泵送入精馏塔。
塔顶上升蒸气采用全冷凝后,部分回流,其余作为塔顶产品经冷却器冷却后送至贮槽。
塔釜采用间接蒸汽再沸器供热,塔底产品经冷却后送入贮槽。
精馏装置有精馏塔、原料预热器、冷凝器、釜液冷却器和产品冷却器等设备。
热量自塔釜输入,物料在塔内经多次部分气化与部分冷凝进行精馏分离,由冷凝器和冷却器中的冷却介质将余热带走。
丙酮—水混合液原料经预热器加热到泡点温度后送入精馏塔进料板,在进料板上与自塔上部下降的的回流液体汇合后,逐板溢流,最后流入塔底。
在每层板上,回流液体与上升蒸汽互相接触,进行热和质的传递过程。
流程示意图如下图图1:精馏装置工艺流程图第二部分塔的工艺计算一、查阅文献,整理有关物性数据(1)水和丙酮的性质表1.水和丙酮的粘度温度50 60 70 80 90 100水粘度mpa0.592 0.469 0.40 0.33 0.318 0.248丙酮粘度mpa0.26 0.231 0.209 0.199 0.179 0.160表2.水和丙酮表面张力温度50 60 70 80 90 100水表面张力67.7 66.0 64.3 62.7 60.1 58.4丙酮表面张力19.5 18.8 17.7 16.3 15.2 14.3表3.水和丙酮密度温度50 60 70 80 90 100相对密度0.760 0.750 0.735 0.721 0.710 0.699水998.1 983.2 977.8 971.8 965.3 958.4 丙酮758.56 737.4 718.68 700.67 685.36 669.92 表4.水和丙酮的物理性质分子量沸点临界温度K 临界压强kpa 水18.02 100 647.45 22050丙酮58.08 56.2 508.1 4701.50表5. 丙酮—水系统t—x—y数据沸点t/℃丙酮摩尔数x y10000 920.01 0.279 84.20.0250.47 75.60.050.63 66.90.10.754 62.40.20.813 61.10.30.832 60.30.40.842 59.80.50.851 59.20.60.86358.80.70.87558.20.80.89757.40.90.93556.90.950.96256.7 0.975 0.97956.5 1 1由以上数据可作出t-y(x)图如下由以上数据作出相平衡y-x线图(2)进料液及塔顶、塔底产品的摩尔分数酮的摩尔质量 A M =58.08 Kg/kmol水的摩尔质量 B M =18.02 Kg/kmol平均摩尔质量M F =0.0937⨯58.08+(1-0.0937)⨯18.02=21.774 kg/kmol0937.002.18/75.008.58/25.008.58/25.0=+=F x 968.002.18/01.008.58/99.008.58/99.0=+=D x 00629.002.18/98.008.58/02.008.58/02.0=+=W xM D = 0.968⨯58.08+ (1-0.968) ⨯18.02=56.798 kg/kmolM W =0.00629⨯58.08+(1-0.00629)⨯18.02=18.272 kg/kmol774.21)24*300/(90000000=F =574.08Kmol/h 最小回流比由题设可得泡点进料q=1则F x = e x ,又附图可得e x =0.0937, e y =0.749。
min D e e e x y R y x -=- =3342.00937.0749.0749.0968.0=-- 确定操作回流比:5.1min /=R R令5013.0min 5.1==R R二、全塔物料衡算与操作方程(1)全塔物料衡算W D F +=F D W Fx Dx Wx =+D=52.18Kmol/h W=521.9Kmol/h(2) 操作方程精馏段 111D n n x R y x R R +=+++= 0.33Xn+0.64 提馏段:因为泡点进料,所以q=1,042.0-'66.71'/16.26''1'n x n y hKmol RD L Xw WF L W n X W F L F L Xw WqF L W n X W qF L qF L n y =+==-+--++=-+--++=+代入数据 (3)由图可得当R=0.5013时,精馏段与平衡线相切,则即使无穷多塔板及组成也不能跨越切点,切点为(0.854,0.915),则: min min 0.9680.91510.9680.854R R -=+- 可解得:min R =0.8688 设R=1.5Rmin=1.3032则精馏段操作线方程:111D n n x R y x R R +=+++=0.57Xn+0.42 利用图解法求理论班层数,可得:总理论板层数 11T N = 块 , 进料板位置 7F N =三、全塔效率的估算用奥康奈尔法('O conenell )对全塔效率进行估算:根据丙酮—水系统t —x(y)图可以查得:c td 05.56= (塔顶第一块板) 0.968D x = 10.968y = 10.95x =设丙酮为A 物质,水为B 物质所以第一块板上: 0.968A y = 0.95A x = 0.032B y = 0.05B x = 可得: ()/ 1.59/A AAB D B By x a y x ==c t f 067.2= (加料板) 0.0937F x = 0.75F y =假设物质同上:0.750A y = 0.0937A x = 0.250B y = 0.9063B x = 可得: ()/29/A AAB F B By x a y x ==c t w 0100=(塔底) 0.00629W x = 0.00627W y =假设物质同上:0.00627A y = 0.00629A x = 0.99373B y = 0.99371B x = 可得: ()/0.997/A AAB W B By x a y x ==所以全塔平均挥发度: 33 1.59290.997 3.58D F W a a a a ==⨯⨯=精馏段平均温度: 0156.567.261.8522D F T T T C ++=== 查前面物性常数(粘度表):61.85 0C 时, 0.53m Pa s μ=⋅水 0.51m Pa s μ=⋅丙酮所以 0.530.2430.520.7570.515m i i x Pa s μμ==⨯+⨯=⋅∑精查61.850C 时,丙酮-水的组成0.175y =水 0.757x =水 0.825y =丙酮 0.243x =丙酮所以 -0.245(E =0.493.580.515=0.42T ⨯精)()同理可得:提留段的平均温度 0B F 210067.283.622T T T C ++=== 查表可得在83.60C 时 -0.245E =0.493.580.336=0.468T ⨯(提)()四、实际塔板数实际塔板数T TP E N N =(1)精馏段:R 6N ==14.30.42,取整15块,考虑安全系数加一块为15块。