数控车床螺纹加工方法
数控车床螺纹加工编程指令的应用

数控车床螺纹加工编程指令的应用济宁职业技术学院(山东)张玉香在目前的FANUC 和广州数控系统的车床上,加工螺纹一般可采用3 种方法:G32 直进式切削方法、G92直进式固定循环切削方法和G76 斜进式复合固定循环切削方法。
由于它们的切削方式和编程方法不同,造成的加工误差也不同,在操作使用时需仔细分析,以便加工出高精度的零件。
1.编程方法(1)G32 直进式螺纹切削方法指令格式:图1G32直进式螺纹切削方法指令格式:G32 X(U )_ Z(W )_ F_ ;该指令用于车削圆柱螺纹、圆锥螺纹、端面螺纹。
其编程方法与G01 相似,如图1所示。
使用说明:①式中(X ,Z )和(U ,W )为螺纹的终点坐标,即图1 中B 点的坐标值;F 后的数值为导程(单线时为螺距)。
②当α=0°时,作直螺纹加工,编程格式为G32 Z_F_或G32 W_F_ ;当α<45°时加工锥螺纹,螺距以Z轴方向的值指定;当α>45°时螺距以X 轴方向的值指定;当α=90°时,加工端面螺纹,编程格式为G32 X_ F_或G32 U_ F_ 。
③螺纹切削中进给速度倍率开关无效,进给速度被限制在100% ;螺纹切削中不能停止进给,一旦停止进给切深便急剧增加,非常危险。
因此,进给暂停在螺纹加工中无效。
④在螺纹切削程序段后的第一个非螺纹切削程序段期间,按进给暂停键时刀具在非螺纹切削程序段停止。
⑤主轴功能的确定。
在编写螺纹加工程序时,只能使用主轴恒转速控制功能(程序中编入G97 ),由于进给速度的最大值和最小值系统参数已设定,在加工螺纹时为了避免进给速度超出系统设定范围,所以主轴转速不宜太高,一般用如下公式计算:(取)且从粗加工到精加工,主轴转速必须保持恒定。
否则,螺距将发生变化,会出现乱牙。
⑥螺纹起点和终点轴向尺寸的确定。
螺纹加工时应注意在有效螺纹长度的两端留出足够的升速段和降速段,以剔除两端因进给伺服电动机变速而产生的不符合要求的螺纹段,通常:δ=(2~3 )螺距δ=(1~2 )螺距⑦螺纹起点和终点径向尺寸的确定。
数控车床螺纹编程实例

数控车床螺纹编程实例数控车床螺纹编程实例近年来随着制造业从传统制造向智能制造的转型升级,数控车床已经成为了制造业必不可少的一种设备。
而作为数控车床的关键部件之一,螺纹加工技术也日益被人们所重视。
因此,在这篇文章中,本人将为各位介绍数控车床螺纹编程实例。
一、螺纹加工的基本概念螺纹是机械制造中常见的加工方式,它的目的是为了加工成一个或多个长度为一定的螺旋状线条,以便用于紧固或传递运动。
与传统的非数控螺纹加工方式不同,数控车床的螺纹加工方式更加高效、精准、可靠。
数控螺纹加工技术可以广泛应用于机械、电子、航空、航天等领域。
数控螺纹加工技术的关键是编写好螺纹加工程序。
二、数控车床螺纹编程的基本方法数控车床螺纹加工的编程方法有两种,一种是跳刀螺纹,另一种是单刀螺纹。
前者有一个弹簧机构,使刀具在两个螺纹之间自行跳动,后者则可以实现“一刀成形”。
跳刀螺纹来说,首先需要编写圆形插补程序,经过计算得到所需螺距数,并转化为螺旋线的标准公式。
然后再编写螺纹加工程序。
单刀螺纹则需要编写其他程序,比如刀具半径补偿程序、主轴旋转程序等等。
三、数控车床螺纹加工的编程实例以G54坐标系下的一个长度为10mm、螺距为2mm、螺旋线圈数为3、外径为25mm的螺纹为例。
首先需要编写以下程序:N10G90G54X0Y0S1000M3(主轴转速为1000r/min,卡盘中心为坐标系原点)N20T3M6(选择刀具)接下来是具体的跳刀螺纹加工程序,程序如下:N30G00X25Z5(进刀到起点)N40G02X20I-2K0F0.25R2(第一段加工,方向为右)N50G02I-2K0F0.25R2(第二段加工,方向为上)N60G02I2K0F0.25R2(第三段加工,方向为左)N70G02I2K0F0.25R2(第四段加工,方向为下)N80G02X25I-2K0F0.25R2(最后一段加工,方向为右)N90G00X0Z0M9(回到起点,清除工作参数)程序说明:G02表示圆弧插补,G00表示快速定位移动,I、K分别表示圆心的X、Y方向上的偏移量。
数控车床加工螺纹尺寸计算方法【干货经验】

在数控车床上进行螺纹切削的方法称为使用可转位螺纹刀片的单点螺纹。
由于攻丝操作既是切削操作又是成型操作,因此攻丝刀片的形状和尺寸必须与成品螺纹的形状和尺寸相对应。
根据定义,单点螺纹加工是切削特定形状的螺旋槽的加工过程,该螺旋槽每主轴旋转均匀地前进。
螺纹的均匀性由编程的每转进给速度中的进给速度控制。
螺纹的进给速度始终是螺纹的导程,而不是螺距。
对于单头螺纹,导程和螺距是相同的。
由于单点螺纹加工是多次加工,因此CNC系统为每个线程通过提供主轴同步。
数控车床加工螺纹尺寸计算方法(方式)-数控车床加工螺纹尺寸如何计算首先,是需要知道该百度1/2锥管螺纹的大径,小径,螺距,才能加工出来。
查锥管螺纹标准,可以知道其牙数14,螺距为,牙高为,大径为,小径为,基准距离的基本值为,(最大为10,最小为),如果是外锥螺纹时,还需要知道它的有效螺纹长度应不小于(最长为15,最短为)如何应用以上查得的参数,来应用于数控加工编程以外锥管螺纹1/2为例,把外锥螺纹想象成一个梯形,底朝左,顶朝右。
底端即为大端直径,记为D,顶端即为小端直径,记为d,大径在距离小端的地方。
因为管螺纹锥度比=1:16 =(大D-小d)/锥轴线长,所以可以得到()/=1/16,计算得到d=;同理,有()/=1/16,计算得到D=)利用计算得到的D,d,加工出螺纹的外锥,“梯形”的高暂定为;计算出螺纹锥度R=(D-d)/2=下面开始编程G92和G76均可以以G92为例进行说明编程如下(此处以广数980T 为例,T0101M3 S300 G0Z5M8 X24数控车床数控小径数控车床怎样计算螺纹牙高…大径…小径…d的算法有很多种,根据不同的罗纹有不同的值。
下面我给你具体分开来算: 1:公制螺纹d=乘P;2:55度英制螺纹d=乘P; 3:60度圆锥管螺纹d=乘P; 4:55度圆锥管螺纹d=乘P; 5:55度圆柱管螺纹d=乘P; 6:60度米制锥螺纹d=乘P;注:d=螺纹小径,D=螺纹大径,P=螺距,H就是牙形高度粗牙就是M+公称直径(也就是螺纹大径)。
数控车床上加工梯形螺纹

数控车床上加工梯形螺纹内容摘要:在数控车床上加工梯形螺纹是一个全新的课题,本文通过对梯形螺纹加工的工艺分析和加工方法的研讨,探索出一套可以在数控车床上加工出合格梯形螺纹的方法在普通车床的生产实习过程中,加工梯形螺纹课题是最基本的实习课题,但在数控车床实习过程中,常常由于加工工艺方面的原因,却很少进行梯形螺纹的加工练习,甚至有人提出在数控车床上不能加工梯形螺纹,显然这种提法是错误的.其实,只要工艺分析合理,使用的加工指令得当,完全可以在数控车床上加工出合格的梯形螺纹。
一、梯形螺纹加工的工艺分析1。
梯形螺纹的尺寸计算梯形螺纹的代号梯形螺纹的代号用字母“Tr”及公称直径×螺距表示,单位均为mm。
左旋螺纹需在尺寸规格之后加注“LH”,右旋则不用标注。
例如Tr36×6,Tr44×8LH等.国标规定,公制梯形螺纹的牙型角为30°。
梯形螺纹的牙型如图(1),各基本尺寸计算公式如表1—1。
图1 梯形螺纹的牙型2。
梯形螺纹在数控车床上的加工方法直进法螺纹车刀X向间歇进给至牙深处(如图2a)。
采用此种方法加工梯形螺纹时,螺纹车刀的三面都参加切削,导致加工排屑困难,切削力和切削热增加,刀尖磨损严重。
当进刀量过大时,还可能产生“扎刀”和“爆刀”现象。
这种方法数控车床可采用指令G92来实现,但是很显然,这种方法是不可取的。
斜进法螺纹车刀沿牙型角方向斜向间歇进给至牙深处(如图2b)。
采用此种方法加工梯形螺纹时,螺纹车刀始终只有一个侧刃参加切削,从而使排屑比较顺利,刀尖的受力和受热情况有所改善,在车削中不易引起“扎刀"现象。
该方法在数控车床上可采用G76指令来实现。
交错切削法螺纹车刀沿牙型角方向交错间隙进给至牙深(如图2c)。
该方法类同于斜进法,也可在数控车床上采用G76指令来实现.切槽刀粗切槽法该方法先用切槽刀粗切出螺纹槽((如图2d),再用梯形螺纹车刀加工螺纹两侧面。
这种方法的编程与加工在数控车床上较难实现。
数控车床加工多头螺纹

数控车床加工多头螺纹摘要:数控车床主要用来加工盘类或轴类零件,利用数控车床加工多头螺纹,能大大提高生产效率,保证螺纹加工精度,减轻操作者的劳动强度。
我通过多年的实践经验,对多头螺纹的加工要点和操作要领进行了总结,为多头螺纹的数控加工提供了理论依据。
关键词:数控车床多头螺纹编程在普通车床上进行多头螺纹车削一直是一个加工难点:当第一条螺纹车成之后,需要手动进给小刀架并用百分表校正,使刀尖沿轴向精确移动一个螺距再加工第二条螺纹;或者打开挂轮箱,调整齿轮啮合相位,再依次加工其余各头螺纹。
受普通车床丝杠螺距误差、挂轮箱传动误差、小拖板移动误差等多方面的影响,多头螺纹的导程和螺距难以达到很高的精度。
而且,在整个加工过程中,不可避免地存在刀具磨损甚至打刀等问题,一旦换刀,新刀必须精确定位在未完成的那条螺纹线上。
这一切都要求操作者具备丰富的经验和高超的技能。
然而,在批量生产中,单靠操作者的个人经验和技能是不能保证生产效率和产品质量的。
在制造业现代化的今天,高精度数控机床和高性能数控系统的应用使许多普通机床和传统工艺难以控制的精度变得容易实现,而且生产效率和产品质量也得到了很大程度的保证。
下面我将从四个方面对数控车床加工多头螺纹进行分析:一、螺纹的基本特征在机械制造中,螺纹联接被广泛应用,例如数控车床的的主轴与卡盘的联结,方刀架上螺钉对刀具的紧固,丝杠螺母的传动等。
圆柱或圆锥母体表面上制出的螺旋线形的、具有特定截面的连续凸起部分。
螺纹按其母体形状分为圆柱螺纹和圆锥螺纹;按其在母体所处位置分为外螺纹、内螺纹,按其截面形状(牙型)分为三角形螺纹、矩形螺纹、梯形螺纹、锯齿形螺纹及其他特殊形状螺纹,三角形螺纹主要用于联接,矩形、梯形和锯齿形螺纹主要用于传动;按螺旋线方向分为左旋螺纹和右旋螺纹,一般用右旋螺纹;按螺旋线的数量分为单线螺纹、双线螺纹及多线螺纹;联接用的多为单线,传动用的采用双线或多线;按牙的大小分为粗牙螺纹和细牙螺纹等,按使用场合和功能不同,可分为紧固螺纹、管螺纹、传动螺纹、专用螺纹等。
数控车床加工内外螺纹的对刀技巧
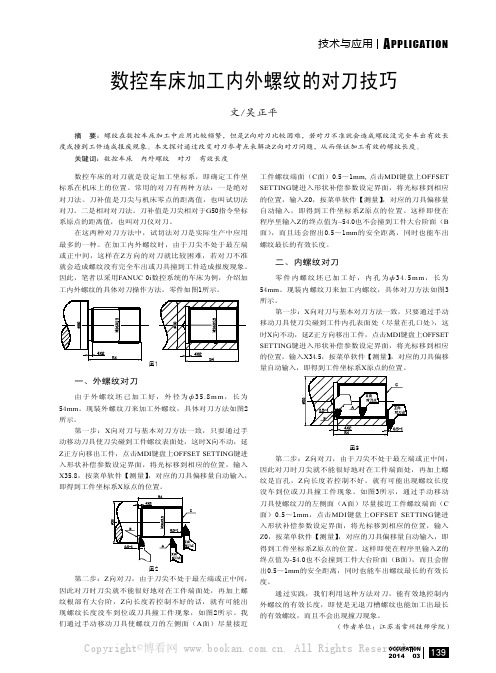
技术与应用A PPLICATION139OCCUPATION2014 03摘 要:螺纹在数控车床加工中应用比较频繁,但是Z向对刀比较困难,若对刀不准就会造成螺纹没完全车出有效长度或撞到工件造成报废现象。
本文探讨通过改变对刀参考点来解决Z向对刀问题,从而保证加工有效的螺纹长度。
关键词:数控车床 内外螺纹 对刀 有效长度数控车床加工内外螺纹的对刀技巧文/吴正平数控车床的对刀就是设定加工坐标系,即确定工件坐标系在机床上的位置。
常用的对刀有两种方法:一是绝对对刀法。
刀补值是刀尖与机床零点的距离值,也叫试切法对刀。
二是相对对刀法。
刀补值是刀尖相对于G 50指令坐标系原点的距离值,也叫对刀仪对刀。
在这两种对刀方法中,试切法对刀是实际生产中应用最多的一种。
在加工内外螺纹时,由于刀尖不处于最左端或正中间,这样在Z 方向的对刀就比较困难,若对刀不准就会造成螺纹没有完全车出或刀具撞到工件造成报废现象。
因此,笔者以采用FANUC 0i 数控系统的车床为例,介绍加工内外螺纹的具体对刀操作方法,零件如图1所示。
一、外螺纹对刀由于外螺纹坯已加工好,外径为ф35.8m m ,长为54mm 。
现装外螺纹刀来加工外螺纹,具体对刀方法如图2所示。
第一步:X 向对刀与基本对刀方法一致,只要通过手动移动刀具使刀尖碰到工件螺纹表面处,这时X 向不动,延Z 正方向移出工件,点击MDI 键盘上OFFSET SETTING 键进入形状补偿参数设定界面,将光标移到相应的位置,输入X 35.8,按菜单软件【测量】,对应的刀具偏移量自动输入,即得到工件坐标系X原点的位置。
图2第二步:Z 向对刀,由于刀尖不处于最左端或正中间,因此对刀时刀尖就不能很好地对在工件端面处,再加上螺纹根部有大台阶,Z 向长度若控制不好的话,就有可能出现螺纹长度没车到位或刀具撞工件现象,如图2所示。
我们通过手动移动刀具使螺纹刀的左侧面(A 面)尽量接近工件螺纹端面(C 面)0.5~1mm, 点击MDI 键盘上OFFSET SETTING 键进入形状补偿参数设定界面,将光标移到相应的位置,输入Z 0,按菜单软件【测量】,对应的刀具偏移量自动输入,即得到工件坐标系Z 原点的位置。
数控车床大螺距螺纹加工方法【技巧】
螺纹的车削工艺分析加工螺纹的加工有很多种:直进法、斜进法、左右切削法、车直槽法、分层法等等[1]。
由于螺纹较之三角螺纹,其螺距和牙型都大,而且精度高,牙型两侧面表面粗糙度值较小,致使螺纹车削时,吃刀深,走刀快,切削余量大,切削抗力大。
再[1]加工许多学校的数控车床刚性较差,这就导致了螺纹的车削加工难度较大,在数控车工技能培训中难于掌握,容易产生“扎刀”和“爆刀”现象,进而对此产生紧张和畏惧的心理。
在多年的数车工实习教学中,通过不断的摸索、总结、完善,对于螺纹的车削也有了一定的认知,我认为利用宏程序进行分层切削,可以很好地解决出现的问题。
“分层法”车削螺纹实际上是直进法和左右切削法的综合应用。
在车削较大螺距的螺纹时,“分层法”通常不是一次性就把槽切削出来,而是把牙槽分成若干层,每层深度根据实际情况而定。
转化成若干个较浅的槽来进行切削,可以降低车削难度。
每一层的切削都采用左右交替车削的方法,背吃刀量很小,刀具只需沿左右牙型线切削,螺纹车刀始终只有一个侧刃参加切削(如图2),从而使排屑比较顺利,刀尖的受力和受热情况有所改善,因此能加工出较高质量的螺纹,且容易掌握,程序简短,容易操作。
图2 分层切削法3 宏程序分层加工大螺距螺纹 3.2 程序以Fanuc 0i mateTC系统为例,图1所示螺纹的加工程序如下: O0001;T0101 M03 S300;换螺纹刀,主轴转速300r/min G00 X38 Z5;快速走到起刀点 M08;开冷却#101=36;螺纹公称直径 #102=0;右边借刀量初始值#103=-1.876;左边借刀量初始值(tg15*3.5*2或0.938*2) #104=0.2;每次吃刀深度,初始值N1 IF [#101 LT 29] GOTO2;加工到小径尺寸循环结束 G0 Z[5+#102] ;快速走到右边加工起刀点 G 92 X[#101] Z-30 F6;右边加工一刀 G0 Z[5+#103] ;快速走到左边加工起刀点 G92 X[#101] Z-30 F 6;左边加工一刀 #101=#101-#104;改变螺纹加工直径#102=#102-0.134*#104;计算因改变切深后右边借刀量(tg15/2=0.134) #103=#103+0.134*#104;计算因改变切深后左边借刀量(tg15/2=0.134) IF[#101 LT 34] THEN #104=0.15;小于34时每次吃刀深度为0.15 IF[#101 LT 32] THEN #104=0.1;小于32时每次吃刀深度为0.10 IF[#101 LT 30] THEN #104=0. 05;小于30时每次吃刀深度为0.05 GOTO 1;N2 G92 X29 Z-30 F6;在底径处精加工两刀 G92 X29 Z-30 F6;G00 X100 Z100 M09;刀架快速退回,关闭冷却 M05;主轴停M30;程序结束。
数控车床加工梯形螺纹的方法
数控车床加工梯形螺纹的方法摘要:梯形螺纹在普通车床上加工时劳动强度大,生产效率低,对操作者技术要求也高,尤其是批量生产更是不能满足实际生产。
当前数控机床应用逐步普及,利用数控机床代替普通机床进行加工趋势,已经是现在企业的发展方向。
今天我将对数控车床加工梯形螺纹的过程做分析和总结,从而解决在普通车床上加工梯形螺纹的难题,实际加工效果较好,值得推广。
关键词:梯形螺纹;数控车床;G76/G92指令加工(二)加工检测梯形螺纹的检测分综合测量、单针测量和三针测量三种。
综合测量是用标准梯形螺纹环规进行测量,受实验室条件影响,没有配备该标准环规。
单针测量就是用一根标准量针放在螺旋槽中,用千分尺测量出螺纹外径至顶针顶端点之间距离,通过数值对比进行检测,测量值受加工表面质量影响较大。
三针测量法测量螺纹中径值非常精密,我采用三针测量法进行测量。
测量方法如图所示。
首先把三根量针放置在螺纹两侧相对应图示的螺旋槽内,为了操作方便,可以用细线将三根量针连接起来,再用千分尺测量出两顶针之间的距离M,由M值间接计算出螺纹中径的尺寸值。
量针直径选定 dD=0.518P=0.518×6=3.1mm(0.518为系数),数量准备:三根。
(注d2=33mm查表得尺寸允许偏差为d2=33 mm)测量读数值:M=d2+4.864dD-1.866P=33+4.864×3.1-1.866×6=36.88mm按照中径值允许的极限偏差查询计算,千分尺测量的读数值M应为36.43~36.76mm。
加工工艺分析:(一)采用G76车削循环指令粗车梯形螺纹,G92指令精车梯形螺纹由于梯形螺纹的螺距和切削深度一般都较较大,加工余量就大,易扎刀的现象,可以用G76指令来解决螺纹加工梯形这个难题。
G76指令通过设置相关参数后自动加工粗(精)车螺纹,由于梯形螺纹低径宽度较大,精车时采用G92指令左右直进法精加工。
粗车时由顶部逐层切削,直到底部,每层切削下刀都按指定斜进法模式切入。
数控车床多头螺纹加工方法【干货】
下面通过螺纹零件的实际加工分析,阐述数控车床多头螺纹的加工步骤和方法。
一、螺纹的基本特性在机械制造中,螺纹联接被广泛应用,例如数控车床的主轴与卡盘的联结,方刀架上螺钉对刀具的坚固,丝杠螺母的传动等。
它是在圆柱或圆锥表面上沿着螺旋线所形成的具有规定牙型的连续凸起和沟槽,有外螺纹和内螺纹两种。
按照螺纹剖面形状的不同,主要有三角螺纹、梯形螺纹、锯齿螺纹和矩形螺纹四种。
按照螺纹的线数不同,又可分为单线螺纹和多线螺纹。
在各种机械中,螺纹零件的作用主要有以下几点:一是用于连接、紧固;二是用于传递动力,改变运动形式。
三角螺纹常用于连接、坚固;梯形螺纹和矩形螺纹常用于传递动力,改变运动形式。
由于用途不同,它们的技术要求和加工方法也不一样。
二、加工方法螺纹的加工,随着科学技术的发展,除采用普通机床加工外,常采用数控机床加工。
这样既能减轻加工螺纹的加工难度又能提高工作效率,并且能保证螺纹加工质量。
数控机床加工螺纹常用G32、G92和G76三条指令。
其中指令G32用于加工单行程螺纹,编程任务重,程序复杂;而采用指令G92,可以实现简单螺纹切削循环,使程序编辑大为简化,但要求工件坯料事先必须经过粗加工。
指令G76,克服了指令G92的缺点,可以将工件从坯料到成品螺纹一次性加工完成。
且程序简捷,可节省编程时间。
在普通车床上进行多头螺纹车削一直是一个加工难点:当第一条螺纹车成之后,需要手动进给小刀架并用百分表校正,使刀尖沿轴向精确移动一个螺距再加工第二条螺纹;或者打开挂轮箱,调整齿轮啮合相位,再依次加工其余各头螺纹。
受普通车床丝杠螺距误差、挂轮箱传动误差、小拖板移动误差等多方面的影响,多头螺纹的导程和螺距难以达到很高的精度。
而且,在整个加工过程中,不可避免地存在刀具磨损甚至打刀等问题,一旦换刀,新刀必须精确定位在未完成的那条螺纹线上。
这一切都要求操作者具备丰富的经验和高超的技能。
然而,在批量生产中,单靠操作者的个人经验和技能是不能保证生产效率和产品质量的。
怎样用车床车螺纹车螺纹的步骤与方法
怎样用车床车螺纹(包括正反丝) 车螺纹的步骤与方法问题:怎样用车床车螺纹(包括正反丝)车螺纹的步骤与方法:(低速车削三角形螺纹 Vく5米∕分) 1、车螺纹前对工件的要求: 1)螺纹大径:理论上大径等于公称直径,但根据与螺母的配合它存在有下偏差(—),上偏差为0;因此在加工中,按照螺纹三级精度要求。
螺纹外径比公称直径小。
螺纹外径D=公称直径—2)退刀槽:车螺纹前在螺纹的终端应有退刀槽,以便车刀及时退出。
3)倒角:车螺纹前在螺纹的起始部位和终端应有倒角,且倒角的小端直径く螺纹底径。
4)牙深高度(切削深度):h1= 2、调整车床:先转动手柄接通丝杠,根据工件的螺距或导程调整进给箱外手柄所示位置。
调整到各手柄到位。
3、开车、对刀记下刻度盘读数,向右退出车刀。
4、合上开合螺母,在工件表面上车出一条螺旋线,横向退出车刀,并开反车把车刀退到右端,停车检查螺距是否正确(钢尺)。
5、开始切削,利用刻度盘调整切深(逐渐减小切深)。
注意操作中,车刀将终了时应做好退刀、停车准备,先快速退出车刀,然后开反车退回刀架。
吃刀深度控制,粗车时t=~0.3mm,精车时tく0.05mm。
六、螺纹的测量: 1、单向测量法: 1)顶径的测量:螺纹顶径的尺寸,一般都允许有较大的误差,外螺纹顶径可用游标卡尺或千分尺测量,内螺纹顶径可用游标卡尺测量。
2)螺距的测量:螺距一般可用钢尺测量, 3)中径的测量:(1)用螺纹千分尺测量螺纹中径。
(2)用三针法测量螺纹中径。
三针法测量螺纹中径是一种比较精密的测量方法。
2、综合测量法:综合测量法就是对螺纹的各项尺寸用螺纹量规进行综合性的测量七、安全生产: 1)车螺纹前检查车床正反车操纵机构及开合螺母等,以防操作失灵。
2)在吃刀时注意不要多摇进一圈,否则会发生车刀撞坏,工件顶弯或飞出等事故。
3)不能用手模螺纹表面,更不能用棉纱去擦正在旋转的螺纹工件,以防发生事故。
普通车床上加工螺纹一般是用螺纹车刀进行加工。
- 1、下载文档前请自行甄别文档内容的完整性,平台不提供额外的编辑、内容补充、找答案等附加服务。
- 2、"仅部分预览"的文档,不可在线预览部分如存在完整性等问题,可反馈申请退款(可完整预览的文档不适用该条件!)。
- 3、如文档侵犯您的权益,请联系客服反馈,我们会尽快为您处理(人工客服工作时间:9:00-18:30)。
数控车床螺纹加工方法
【摘要】文章首先阐述数控车床螺纹加工现状及局限性,然后探讨了数控车床螺纹加工原理,最后对数控车床螺纹加工方法的问题进行了探讨。
【关键词】数控车床;螺纹加工;方法
一、前言
近年来,由于数控车床被广泛的应用在各个领域,所以,对数控车床螺纹加工的质量要求也就越来越高。
我国在数控车床螺纹加工方法上取得了一定的成绩,但依然存在一些问题和不足。
因此,科技不断发展的新时期下,我们要加大对数控车床螺纹加工方法的研究。
二、数控车床螺纹加工现状及局限性
在科技高速发展的今天,数控机床已经普遍运用于机械制造行业。
如加工多线螺纹零件,若用普通车床加工的话,不仅加工麻烦,生产率低,工人劳动强度还很大,并且加工精度不高,不能满足技术要求;如果采用数控车床来加工,不仅操作简单,编程容易,还能大大减少操作工人的劳动强度,提高生产率,而且加工精度会更高。
但是,在数控车床螺纹加工技术实际应用中,由于数控车床取消了丝杠的设计应用,却存在了很多不如普通车床实际加工方便的地方。
例如数控车床车削螺纹时只能一次成形,车削过程中不能象普通车床一样随意改变转速,否则螺纹就要乱扣,就算是螺纹切削由于转速选择不当造成加工螺纹时发颤也不能改变转速;另外,还有螺纹工件一但卸下机床就不能再上数控车床修调加工了,因而存在很多不方便的地方。
三、数控车床螺纹加工原理
1、在普通车床加工螺纹时,主轴与进给机构之间存在机械上的定比传动关系,是由复杂的机械传动链来保证的。
数控车床在设计上,简化了传动链,取消了主轴箱,主轴一般采用变频调速。
在数控车床的螺纹加工中,主轴与刀架之间不存在机械上的定比传动关系,而是依靠数控系统控制伺服进给电机,保障Z 轴进给速度与主轴的转速保持一线性比例关系。
只有了解数控车床螺纹加工原理,按照操作规程使用数控车床,对螺纹加工中常见故障现象进行分析,“据理析象”,才能解决实际加工生产中出现的一些问题,提高加工效率。
数控车床进行螺纹切削时,主轴工作在转进给状态下,其实质是主轴的角位移与Z轴进给之间进行的插补。
在数控车床中,一般采用光电编码器作为主轴角位移测量元件,通过机械部件与主轴连接,传动比为1:1,将编码器的Z脉冲(也称“一转信号”)作为主轴位置信号,经数控系统处理后驱动刀架运动。
主轴脉冲发生器送出两组信号脉冲,一组为计数脉冲,CK6140数控车床配置1200线主轴编码器,即每转送出1200个计数脉冲,另一组为主轴基准脉冲,每转送出一个同步脉冲信号。
车削螺纹时,数控系统检测到主轴基准脉冲同步信号到来
时开始切削,否则处于等待状态。
这样就保证螺纹加工时每次切削的初始位置在工件圆周的同一个位置上,以保证各次切削的螺纹牙形相重合,防止了多次切削乱扣现象发生。
在数控系统中,完成螺纹加工的要素为:主轴转速n和螺纹导程t,进给速度F=n*t;。
即主轴每转一圈,Z轴进给一个导程,主轴的旋转与进给轴必须保持严格的比例关系。
基准脉冲同步信号极为重要,它是保证在螺纹加工每次切削的初始位置在工件的同一个位置上,防止了“乱扣”现象发生。
2、数控车床螺纹加工切削原理分析
能不能找到一种克服数控车床这种加工不足的方法呢? 经过仔细观察分析,发现数控车床螺纹加工时是由主轴上的位置编码器与主轴转速同步来加工螺纹的,为什么在加工中改变主轴转速螺纹要乱扣呢? 通常,螺纹切削是沿着同样的刀具轨迹从粗切到精切重复进行的。
因为螺纹切削是在主轴上的位置编码器输出一转信号时开始的,所以螺纹切削是从固定点开始且刀具在工件上的轨迹不变而重复切削螺纹。
由于螺纹切入时系统有一个响应时间,而在同一个响应时间内,主轴的速度快慢不同,切入的角度也就不同,因而主轴速度从粗切到精切必须保持恒定,否则螺纹乱扣。
四、螺纹加工前的工作
1、加工工艺分析
在数控车床上加工螺纹,首先要制订合理的工艺方案,然后才能进行编程和加工。
工艺方案的好坏不仅会影响数控车床效率的发挥,而且将直接影响到螺纹的加工质量。
(1)走刀路线及进刀方式的确定
在数控车床上车螺纹时,要根据工件形状的复杂性考虑走刀路线,在加工过程中是否有干涉或者碰撞等现象,根据实际情况采用适合的编程指令,而且尽可能高速度高效率地完成加工避免走空刀。
其次要看螺纹的牙形及导程或螺距选择加工的进刀方式,一般情况下当螺距P<3mm时,采用直进法即G32或G92指令编程;螺距P>3mm时,采用斜进法即G76指令编程。
(2)螺纹车刀的选择
螺纹车刀的选择直接影响加工质量的好坏。
在保证加工螺纹的高质量高效率的前提下应根据工件的材料来确定刀具的材料,而最常用的车刀材质有高速钢和硬质合金。
在车削塑性材料螺纹工件时,应选用高速钢螺纹车刀,而硬度高脆性稍高的加工材料选用硬质合金螺纹车刀。
高速钢螺纹车刀的切削用量比较小,刃磨方便、切削刃锋利、韧性好,能承受较大的切削冲击力,加工的螺纹表面粗糙度小。
但它的耐热性差,不宜高速车削。
所以一般适合于大螺距的螺纹加工如梯形螺纹。
硬质合金螺纹车刀的硬度高、耐磨性好、耐高温,但抗冲击能力差,它适合于小螺距三角形螺纹加工。
数控车床一般选用硬质合金可转位车刀。
螺纹车刀属于成形
刀具,要保证螺纹牙型的精度,必须正确刃磨和安装车刀。
(3)切削用量的选择
主轴转速的确定在车削螺纹时,车床的主轴转速将受到螺纹的螺距(或导程)大小、驱动电机的升降频特性及螺纹插补运算速度等多种因素影响,故对于不同的数控系统,推荐有不同的主轴转速选择范围。
如大多数经济型车床数控系统推荐车螺纹时的主轴转速如下:n≤1200/P一K式中:P是螺纹的螺距(mm);K是保险系数,一般取为80。
背吃刀量的选择确定螺纹的切削次数。
螺纹加工中的走刀次数和背吃刀量会直接影响螺纹的加工质量,一般情况下工件材料的硬度、强度越高背吃刀量就越小,切削次数越多;同样,刀具材质不同背吃刀量也不同,如加工同样材质同样螺距的螺纹,高速钢的背吃刀量可略高于硬质合金的背吃刀量,但主轴转数要大大低于硬质合金车刀车削时的主轴转数。
2、螺纹的检查
螺纹加工完成后要检查它的合格性。
三角形螺纹的检测最普遍的就是用环规检测法。
通规必须全部旋人,而止规旋人的部分只能是止规厚度的1/3至2/3厚即可。
梯形螺纹的检测方法一般用的是三针测量法。
主要检测螺纹的中径是否在允许的范围内。
五、数控车床螺纹加工方法
1、螺纹的自动加工是数控车床的基本功能。
它与普通车床的螺纹加工不同,是靠数控系统控制伺服电机驱动刀架的进给,与主轴的旋转相配合,切削出所需的螺纹。
在编程过程中只要给出螺纹的起点、终点坐标和螺距P,数控系统就可以实现螺纹的自动加工。
在螺纹加工过程中必须要解决以下三个问题:
(1)要加工出所需的螺纹深度,一般要经过多次切削才能完成,要求每次开始进刀的工作坐标位置必须相同。
(2)当切制多头螺纹时(应错开相应的螺距),数控系统应能准确分度。
(3)主轴每转一圈,螺纹车刀必须沿纵向进给一个导程S。
这些问题的解决是靠安装在主轴尾部的增量式光电编码器来实现的。
2、增量式光电编码器工作原理
增量式光电编码器的工作原理是利用光电原理把机械角位移变换成电脉冲信号,结构如a)图所示。
其中,E为等节距的辐射状透光狭缝圆盘,狭缝越多则分辨率越高。
它由同步带带动,并与主轴同步转动。
Q1和Q2为光源,DA、DB、DC
为光电元件。
其中,DA和DB错开90b安装。
其目的是利用A相、B相的相位先后来判别编码器的旋转方向,如图b)和图c)所示。