VDA6.3新版过程FMEA六步法
FMEA要求六步分析法
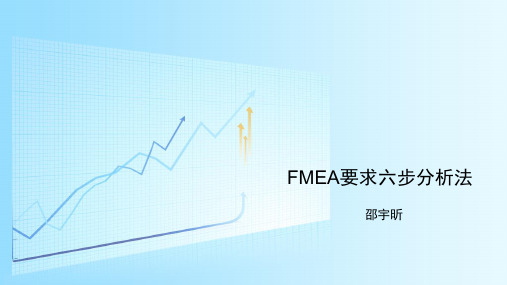
有的技术和材料,类似的应 但不足以确保不发生故障, 用随着周期/运行的条件变 分析能提供一些防止失效的
化,以前有测试或现场经验 原因
在预期使用寿命期间发生的 基于类似技术和材料的新设 标准、最佳实践和设计规则
7 可能性为较高
计,新的应用或改变工作周 适用于基准设计,但不适用 期/运行条件,以前未验证。 于创新,分析提供了有限的
标准不存在,最佳实践尚未 确定,分析不能预测实际性 能
• 从上表可以看出 • 新版 FMEA 的频度考虑了 • 设计成熟度(估计发生) • 产品成熟度(产品实践) • 和预防措施(预防控制) • • • • • 三个维度进行评分 • 增加了“公司或产品示例”栏
探测度(D) 是探测控制有效性的指标 以在产品发布、生产之前 可靠地探测失效原因或失效模式 探测度是指 在现行过程控制探测栏里的 最佳探测控制相关等级 探测度(D)打分表 (适用DFMEA)
第三步:功能分析
• 该步骤主要利用和接口矩阵等工具识别设计或过程的功能和要求并赋予给系统层 级和下一层级(产品、部件层级)如图所示
第四步:失效分析
• 该步骤是新版FMEA特色所在 • 将失效影响、失效模式和失效原因之间 • 的逻辑关系以“瀑布模型”的方式进行展示 • 上一层级的失效模式为下一层级的失效影响 • 下一层级的失效模式即为上一层级的失效原因
频度
估计发生
产品实践
预防控制
通过预防性控制和无故障 完成相同的成熟设计,相 设计经验符合标准、最佳
系列生产的历史,实际上 同的应用、工作周期和工 实践,考虑到经验教训,
1 可以消除故障的可能性 作条件,在可比较的操作 这有效的防止了条件失效
条件或成熟的设计下进行 的发生,分析能高信度的
新版VDA6.3-2016主要变化解读及过程审核培训教材25-12
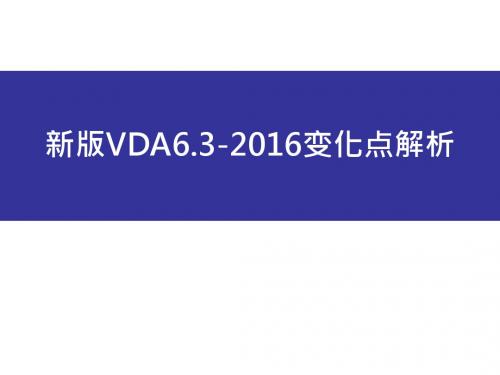
Key changes in new VDA6.3
主要变化点
• S/W issues added to questionary?提问表中加入 S/W 问题
• Audit result/ evaluation method weight of each questions same 每个问题对审核结果/评价方法的比 重一致
P5/P6/P7 audit (series)审核(量产): Number of questions 问题数量
P5/P6/P7 audit (series)审核(量产): Weighting of one question as % 每个问题的比重
Key changes in new VDA6.3
主要变化点
VDA6.3 new version 2016 (changes) VDA6.3新版 2016(变化)
Structure of VDA 6.3 same 结构和之前没有变化 Before 60 questions, now only 57 questions 之前60个问题,现在57个 All questions equal for final results 每个问题占相同的比重
Professional experience 工作经验:
At least 5 years of professional experience (from 3 years of professional experience, company training periods can be taken into account) preferably in producing companies from the automotive industry, of which at least 2 years quality management. 至少5年的工作经验(包括培训期),最好是汽车行业制造业领域,至少两年的质量管理 经验
vda6.3过程审核规程
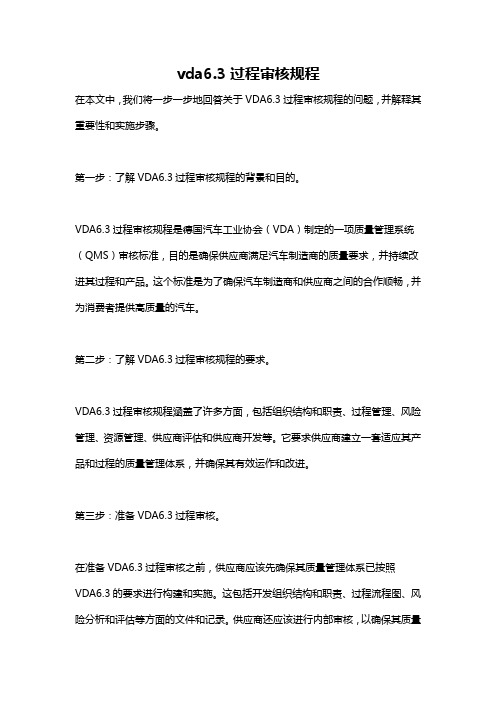
vda6.3过程审核规程在本文中,我们将一步一步地回答关于VDA6.3过程审核规程的问题,并解释其重要性和实施步骤。
第一步:了解VDA6.3过程审核规程的背景和目的。
VDA6.3过程审核规程是德国汽车工业协会(VDA)制定的一项质量管理系统(QMS)审核标准,目的是确保供应商满足汽车制造商的质量要求,并持续改进其过程和产品。
这个标准是为了确保汽车制造商和供应商之间的合作顺畅,并为消费者提供高质量的汽车。
第二步:了解VDA6.3过程审核规程的要求。
VDA6.3过程审核规程涵盖了许多方面,包括组织结构和职责、过程管理、风险管理、资源管理、供应商评估和供应商开发等。
它要求供应商建立一套适应其产品和过程的质量管理体系,并确保其有效运作和改进。
第三步:准备VDA6.3过程审核。
在准备VDA6.3过程审核之前,供应商应该先确保其质量管理体系已按照VDA6.3的要求进行构建和实施。
这包括开发组织结构和职责、过程流程图、风险分析和评估等方面的文件和记录。
供应商还应该进行内部审核,以确保其质量管理体系的有效性。
第四步:进行VDA6.3过程审核。
VDA6.3过程审核由经过培训和资格认证的审核员执行。
审核员将按照VDA6.3的要求进行审核,并与供应商的员工进行交流和访谈,以了解其质量管理体系的有效性和改进机会。
审核员还会检查供应商的文件和记录,以确保其符合VDA6.3的要求。
第五步:发现和记录审核结果。
在执行VDA6.3过程审核的过程中,审核员可能会发现一些不符合VDA6.3要求的问题。
这些问题将被记录下来,并与供应商的管理层和员工进行沟通,以便他们能够采取措施纠正问题并改进其质量管理体系。
第六步:审核结果的评估和认证。
一旦审核完成,审核员将评估供应商对不符合项进行纠正和改进的措施。
如果供应商能够有效地解决问题,并满足VDA6.3的要求,他们将获得VDA6.3过程审核的认证,并被列为合格供应商。
第七步:监督和持续改进。
VDA6.3_过程审查
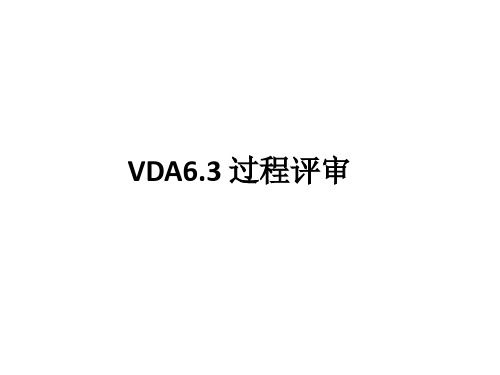
德国汽车工业联合会质量标准(VDA 6)
目的:1.开发以过程为导向的审核方法 2.作为产品生命周期的汽车标准
过程评审是实现过程监控的一种非常重要的工具。
VDA6.3过程审核
P1:潜力分析(新增内容) P2:项目管理(新增内容) P3:产品和过程开发的规划 P4:产品和过程开发的实现 P5:供应商管理 P6:过程分析/ 生产 P7:客户支持,客户满意度,服务 插图2:过程要素同产品生命周期之间的相互关联
KO (Communication CO) – 联络沟通 文件化、建立/保存记录(如:质量、问题)
RI (Risk-Oriented RI) --风险识别和导向 测量目标、监测过程有效性、数据分析、持续改进
VDA6.3过程审核
P3:产品和过程开发的策划:
提问概述 P3 产品和过程开发的策划
潜力
物流和
有形产品的过程
项目管理(P2)
EPM
产品和过程开发的策划(P3)
EPP
产品和过程开发的实现(P4)
EPR
供方管理(P5)
ELM
过程分析/生产(P6)
EPG
顾客支持/顾客满意/服务(P7)
Ek
定量评分定级方法:
VDA6.3过程审核
定级 A B C
符合率EG [%] EG >= 90
80 <= EG < 90 EG < 80
KPI? Effective & Efficiency
VDA6.3过程审核
VDA6.3过程审核
VDA6.3过程审核
过程导向式的审核—风险分析方法
Resources ? Equipments?
Input
新版DFMEA六步法
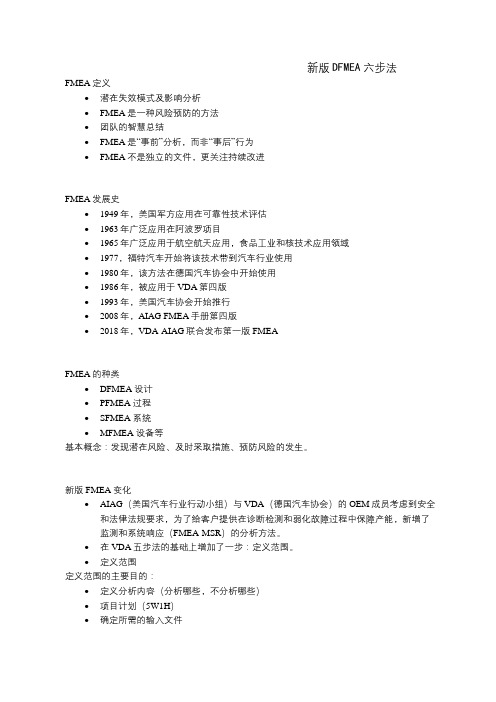
新版DFMEA六步法FMEA定义•潜在失效模式及影响分析•FMEA是一种风险预防的方法•团队的智慧总结•FMEA是“事前”分析,而非“事后”行为•FMEA不是独立的文件,更关注持续改进FMEA发展史•1949年,美国军方应用在可靠性技术评估•1963年广泛应用在阿波罗项目•1965年广泛应用于航空航天应用,食品工业和核技术应用领域•1977,福特汽车开始将该技术带到汽车行业使用•1980年,该方法在德国汽车协会中开始使用•1986年,被应用于VDA第四版•1993年,美国汽车协会开始推行•2008年,AIAG FMEA手册第四版•2018年,VDA-AIAG联合发布第一版FMEAFMEA的种类•DFMEA 设计•PFMEA 过程•SFMEA 系统•MFMEA 设备等基本概念:发现潜在风险、及时采取措施、预防风险的发生。
新版FMEA变化•AIAG(美国汽车行业行动小组)与VDA(德国汽车协会)的OEM成员考虑到安全和法律法规要求,为了给客户提供在诊断检测和弱化故障过程中保障产能,新增了监测和系统响应(FMEA-MSR)的分析方法。
•在VDA五步法的基础上增加了一步:定义范围。
•定义范围定义范围的主要目的:•定义分析内容(分析哪些,不分析哪些)•项目计划(5W1H)•确定所需的输入文件•定义团队指责定义范围输入:•法律法规•顾客要求(内部和外部)•框(边界)图•参数(P)图•原理图U物料清单(BOM)•QFD U可靠性分析在一规定时间内零件修理和更换的频率,以及长期可靠性/耐久性试验的结果。
常见可靠性测试:低温冲击、耐候性试验、盐雾试验、疲劳试验等•卡诺模型•以往质量问题等•结构分析③功能分析④失效分析⑤风险分析⑥优化全新的FMEA表格7大变化点。
VDA6.3-FMEA基础知识培训
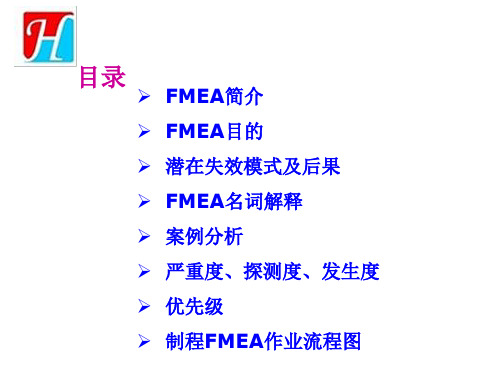
FMEA报告应至少每半年进行一次评审及更新。 然而,评审周期应增加到每月当:
任何重大的变更,如果会影响产品的质量和过程的稳定 客户对于质量及过程的投诉 识别了新的特殊特性 任何项目105
任何重大的变更如果会影响产品的质量和过程的稳定客户对于质量及过程的投诉任何项目105制程fmea作业流程认明每一操作之重要性决定通用之制程管制yes是否还yes有其他可能不良模式原因是否还有list所见特性项目并判定是否为不良模式指出其可能影响及发生决定不良模式之严重度发生度及难检度计分其他不良模式原因之组合存在求出rpn追踪确认依rpn研究改正措施持续改善记录改正措施并计算改正措施实施后之rpn改正措施之展开
Moderate 一般
2 per thousandBiblioteka / 1 in 5006
2 次每 1000 个 / 1 次每 500 辆中 0.5 per thousand / 1 in 2,000 0.5 次每 1000 个 / 1 次每 2000 辆中 0.1 per thousand / 1 in 10,000 0.1 次每 1000 个 / 1 次每 10,000 辆中 Low 低 0.01 per thousand / 1 in 100,000 0.01 次每 1000 个 / 1 次每 100.000 辆中 ≤0.001 per thousand / 1 in 1,000,000 ≤0.001 次每 1000 个中 / 1 次每 1,000,000 Very Low 非常低 Failure is eliminated through preventive control 失效通过预防控制消除了 3 4 5
01.过程审核VDA6.3

b)
公司收入金额=月平均工资*节约人数 *50%= 5200* 63人*50%=16.38万
c)
员工激励金额=月平均工资*节约人数 *50%= 5200* 63人*50%=16.38万
三、第一阶段减人绩效激励(QC)
按公司50%+员工50%激励方式进行激 励,预 计每月 激励金 额为:
(94) 序号 1 人均值+523
二、品质部增效减人:编制优化状况 (QC人 员)
序号
部门
减少人员
比例
1
一厂品质部
10
ቤተ መጻሕፍቲ ባይዱ
2
二厂品质部
0
3
三厂品质部
28
4
四厂品质部
22
线体数量 减少
560 13% 600 0% 720 31% 550 26%
原编制
76 92 90 84
优化后编制
66 92 62 62
5
客服
16
15
1
6%
6
来料
8
6
2
25%
序号
部门
编制人数
6.4:质量体系审核-生产装备 提升总金额
1
一厂品质部
80
人均值+523
2
二厂品质部
103
3
三厂品质部
73
16.38万
4
四厂品质部
75
5
客服
15
6
来料
6
7
实验室
10
总计
313
备注:第二阶段激励根据生产计件效 果及品 质第二 阶段减 人情况 确定绩 效激励 方案。
拟制:
审核:
VDA6.3 讲解
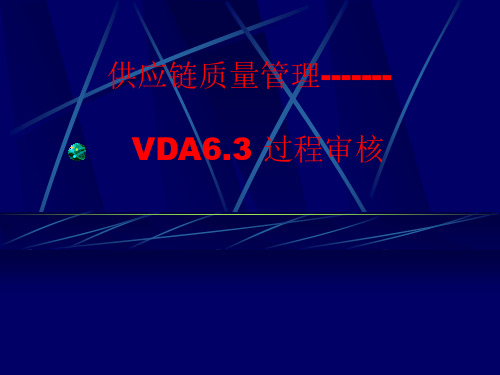
根据职业经验和素质选择合格的审核人员 安排审核任务。 按审核计划或根据发生的事件实施过程审核
3.4.3.2 审核员
与被审核组织/职能部门进行协商(确定要审核的过程、接 口等) 准备审核(研究资料,制订审核提问表,邀请专家参加或 利用专业诀窍等)
供应链质量管理------VDA6.3 过程审核
2 体系审核、过程审核及产品审 核之间的关系
体系审核、过程审核及产品审核是三种 审核方式。列举这三种审核方式并不说 明不存在其他审核方式。
2 体系审核、过程审核及产品审 核之间的关系
比较:
审核方式 体系审核 过程审核 产品审核 审核对象 质量管理体系 产品诞生过程/批量生产 服务过程/服务的实施 产品或服务 目的
3 关于过程审核的规定
实施审核 评分定级 末次会议和撰写报告 要求采取纠正措施 验证纠正措施的有效性 保密义务
保持应有的资格
熟悉最新的标准及文献 审核人员应具备的专业知识 过程知识
4 审核流程
审核总是按相同的系統方法进行:
准备 实施 报告和总结 纠正措施、跟踪、有效性验证。
审核开始前召开首次会议。根据不同情况确 定首次会议的时间和內容。 不同情况包括:
外部审核 內部审核 针对事件进行的审核 按计划进行的审核
6 实施审核
6.2 审核过程
按照事先已制订好的提问表进行审核。既可按照编码顺序也 可隨机提问。 提问的方式,例如:5W提问方式(为什么,何时,何人,如 何做等)以及其他的提问技巧是审核员培训的基本內容,在 此不再进一步闡述。 实践证明,多次用“为什么……”提问有利于对过程工艺进行 深入的分析。 在审核期间,可以提出新的提问并增加到提问表里。 通过提问把现场的人员也納入到审核过程中。建议隨时记录 发现的优点以及不足之处。 为了避免在末次会议上发生沖突,必须尽量在现场澄清不明 之处并达成一致意見。 在审核时若发现严重的缺陷,必须与过程負责人共同制订并 采取紧急措施。
- 1、下载文档前请自行甄别文档内容的完整性,平台不提供额外的编辑、内容补充、找答案等附加服务。
- 2、"仅部分预览"的文档,不可在线预览部分如存在完整性等问题,可反馈申请退款(可完整预览的文档不适用该条件!)。
- 3、如文档侵犯您的权益,请联系客服反馈,我们会尽快为您处理(人工客服工作时间:9:00-18:30)。
过程FMEA分六步进行
这六个步骤为失效模式和后果分析提供了一种系统的分析方法,并作为过程风险分析的记录。
PFMEA分析六步如下:
•PFMEA第一步:定义范围及项目计划
•PFMEA第二步:结构分析
•PFMEA第三步:功能分析
•PFMEA第四步:失效分析
•PFMEA第五步:风险评估
•PFMEA第六步:优化
PFMEA第一步:定义范围
过程范围定义的目的是:
•项目识别-哪些过程/哪些过程的部分要进行分析?
•项目计划- 培养一些有发展潜力的团队人员、创建项目时间表等
•定义分析界限- 包括什么,不包括什么。
•确定能够使用的相关经验教训和决策,例如:最佳实践、准则和标准、防错-防呆方法等等。
工厂可能影响产品质量的过程,以及考虑用于PFMEA分析的过程:
•接收过程、
•零件和材料存储、
•产品和材料交付、
•制造、
•组装、
•打包、
•贴标签、
•运输、
•存储、
•维护过程、
•检验过程
•返工和返修过程等。
图确定过程范围PFMEA第二步:结构分析
过程结构分析的主要目标是:
•结构化产品或过程元素
•可视化分析范围
•确定工步
•作为功能分析步骤的基础
流程图是结构分析的输入文件。
图过程流程图
结构树按层次排列系统元素,并通过结构连接说明关联关系。
这个形象化的结构考虑了过程项目、工步和过程工作要素之间的关系。
图结构分析-结构树示例(电机组装线)
工步是PFMEA分析的重点!
图工步
影响工步失效的潜在原因,其类别数量由4M、5M、6M等决定
4M类别:
机
人
材料(间接)
环境(环境)
其他类别但不限于:
方法
测量
图
结构分析扩展表格示例
PFMEA第三步:功能分析
过程工作要素功能通过实现工步来反应过程/产品的特性。
示例:用手从滑槽中取出烧结轴承
示例:将磨损的轴承压入定子壳内
功能和结构逻辑连接时,应该问以下这些问题:
“发生了什么”?
如何从左到右实现产品/过程要求-(过程项目- 工步- 过程工作元素)
“为什么”?
为什么从右到左实施产品过程的要求-(过程工作元素-工步- 过程项目)
功能网可视化
过程项目功能、工步功能和过程工作元素功能之间的交互通过链接来可视化:功能网、功能结构、功能树、功能矩阵或用PFMEA工具软件进行的功能分析。
图功能分析结构树示例
图功能分析表格示例PFMEA第四步:失效分析
工步的失效从产品特性和过程特性中推断出。
示例包括:
•不合格
•部分合格
•非预期的活动
•不必要的活动
失效链
几个系统元素的功能的交互必须是可展示的。
例如,用功能树/网或功能矩阵进行
在FMEA中分析失效有三个不同的方面:
•失效影响(FE)
•失效模式(FM)
•失效原因(FC))
图失效链理论模型
失效影响与过程项目(系统,子系统,部件元素或过程名称)的功能相关,失效影响应根据客户可能会注意或碰到的后果来描述。
可能影响安全或导致违反法规的失效需要在PFMEA 中明确标识。
客户可以是:
•内部客户(下一步操作/后续操作/操作指标)
•外部客户(下一层级/OEM /经销商)
•立法机构
•产品、产品最终用户/操作者
失效影响用严重度等级评价:
•工厂内:假设在工厂中检测到缺陷引起的失效模式的影响(工厂将采取什么行动,例如报废)•工厂转运:假设在运送到下一个工厂之前没有检测到缺陷引起的失效模式的影响(下一个工厂会采取什么行动?)
•车辆最终用户:过程项目影响的后果(车辆最终用户将注意到什么,感觉,听到,闻到什么,例如,窗户提升得太慢)
PFMEA第五步:风险评估
过程风险分析的主要目标是:
•预防控制措施的分配(现有和/或已计划的)
•探测控制措施的分配(现有和/或已计划的)
•评估每个失效链的严重度,发生度和探测度。
•客户和供应商之间的层连
有两个不同控制措施组:现行预防控制和现行探测控制。
现行探测措施示例:
•目视检查
•根据样件清单进行目检
•使用成相系统进行光学检查
•使用一定数量的样品进行光学测试
•使用XX设备属性测试
•用卡尺测量尺寸
•抽检
•扭矩监测
•负载检查
•终检等
图过程FMEA中的预防和探测
过程意图曲线
评估
评估每种失效模式,因果关系(失效链或失效网)以估计风险。
风险的评估标准:
严重度(S):代表失效影响的严重程度
发生度(O):表示失效原因发生度
探测度(D):表示探测失效原因/模式的探测度
S、O、D的评估等级分别分为1-10个等级,其中等级10的风险贡献最高。
通过分别检查S、O、D的评级和三者的组合,可以得到对风险因素采取降低风险行动的优先排序。
行动优先级(AP)
之前的FMEA手册建议使用RPN来确定动作优先级,然而并没有说明S. 0,D和RPN的所有组合的理性/逻辑的细节。
AP 表为FMEA团队提供了S. 0和D的所有1000种可能的逻辑组合,它基于逻辑描述每个行动优先级,根据每个S.O.D.值的个体评估对行动优先排序,根据组合的值确定可能需要降低的风险。
优先级高(H)
行动的最高优先级。
团队必须确定一个适用的改进探测和(或)/预防措施,或者证明/说明目前的措施是适当的。
优先级中等(M)
行动的中等优先权。
团队应该确定一个适用的改进预防和/或探测措施,或者由公司自行决定,证明/说明目前的措施是适当的。
优先级低(L)
行动的优先级低,团队可以确定要改进的预防或探测措施。
建议管理层至少审核潜在的严重程度等级9 - 10的失效影响与行动优先级高和中的措施,包括采取的所有建议措施。
6
PFMEA第六步:优化
过程优化的主要目标是:
•确定降低风险所需的措施
•确定责任和目标完成时间
•采取行动的实施和记录
•确认实施行动的有效性。
•采取措施后重新评估风险
•持续改进过程
•完善过程要求、预防和探测措施
如果团队决定不需要进一步的行动,在备注栏中写入“无”或“未计划”,以表示风险分析已完成。
PFMEA可以作为过程持续改进的基础
按以下顺序进行优化是最有效的:
•为了减少发生失效原因(FC)的可能性,修改过程。
•增加检测失效原因或失效模式的能力(FC或FM)。
•在进行过程修改的情况下,再次评估所有受影响的工步
行动的状态
悬而未决:
行动既没有被定义也没有讨论。
待确认(可选):
行动已经确定,但还没有决定。
决策文件正在创建。
待实施(可选):
该行动已经确定,但尚未执行。
已完成:
行动已确定并已经执行完成,其效果已经被证明和记录。
最后的评估已经完成。
放弃:
如果决定不执行某个措施,当与成本,实施时机或业务策略相关的风险大于技术风险时,可能会发生这种情况,则选择“放弃”状态。
图PFMEA优化及新风险评估报告。