压铸模具设计基础知识
压铸模具讲解
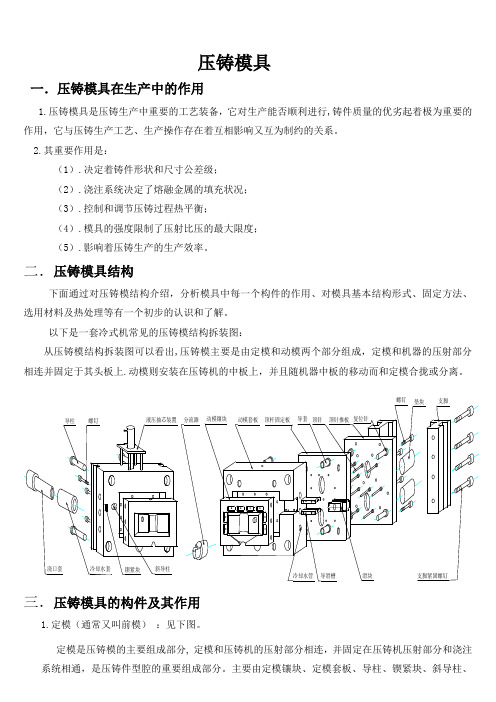
压铸模具一.压铸模具在生产中的作用1.压铸模具是压铸生产中重要的工艺装备,它对生产能否顺利进行,铸件质量的优劣起着极为重要的作用,它与压铸生产工艺、生产操作存在着互相影响又互为制约的关系。
2.其重要作用是:(1).决定着铸件形状和尺寸公差级;(2).浇注系统决定了熔融金属的填充状况;(3).控制和调节压铸过程热平衡;(4).模具的强度限制了压射比压的最大限度;浇口套、定模抽芯机构等部分组成。
定模动模2.动模(通常又叫后模):见上图。
动模是压铸模的另一个重要组成部分, 动模是和定模形成压铸模成型部分的另一个整体,它一般固定在压铸机中板上,随中板作并合运动,与定模部分分开合拢。
一般抽芯机构和顶出机构大多在这个部分。
3.抽芯机构(通常又叫行位):作用: 抽动与开模方向运动不一致成型零件的活动型芯机构。
抽芯机构主要包括:斜导柱、侧面型芯、滑块、导滑槽、限位块、螺杆、弹簧、螺母、螺钉等部分组成。
如下图所示。
4.斜销(通常又叫斜导柱):见下图。
作用: 在开模过程中,强制滑块运动,抽出芯型。
有内抽芯和外抽芯两种,其断面形状多采用扁圆形,防止抽芯时拉伤滑块。
主要参数: 斜角α的大小和抽芯力大小、抽芯行程长短、承受弯曲度力大小有关。
斜角α的数值一般取:10°、15°、18°、20°、25°。
斜销直径取决型芯包紧力的大小,斜销长度 = 固定部分 + 工作段尺寸 + (5~10) cm5.作用:6.作用:和导滑槽配合适当,其抽拔距离不能超过导滑槽长度的2/3,合模时滑块应受一定的预紧力,防止金属液窜入导滑槽,致使滑块卡死。
参数: 滑块的高度B ,宽度C按型芯尺寸决定,滑块的长度A与B、C有关,为使滑块工作时稳定要求 A≥0.7C A≥B。
13.定模座板(通常又叫A板):见上图。
作用:一端面紧固在压铸机头板上,使模具压紧定位,另一端面和模体结合承受机器压力,二个端面要求有足够受压面积,压铸机射咀和压室安装孔要求配和精确。
压铸模具设计基础知识

熱室壓鑄鋅合金中的合金元素
---雜質元素-鐵
鋅合金中鐵元素含不能>0.02%,鐵 元素可:
☺ 增加合金的硬度
但同時
增加合金的脆性
和合金中的鋁發生反應形成Al5Fe2金屬間化合物, 造成鋁元素的損耗並形成浮渣
在壓鑄件中出現硬點
2024/2/1
压铸模具设计基础知识
五.壓鑄合金及其性能
熱室壓鑄鋅合金中的合金元素 ---雜質元素-硅
t1:F1為克服磨擦力(壓室中)
壓
t2:開始進入型腔﹐因澆口急減﹐阻力 力
F
增大﹐F2>F1,達到高速充填
t3:(快速增壓階段)快速充填直止充滿
型腔最大值F3為壓射壓力
t4:F4靜壓力﹐對鑄件壓實
時間t
(壓射力與時間關係曲線見右圖)
2024/2/1
压铸模具设计基础知识
六.壓鑄工藝
定義2﹕壓射壓力就是在充模剛結束時壓射沖頭作用在金屬液面上的力。 定義3﹕壓射壓力是以壓射比壓來表示﹐壓射比壓就是充模結束時﹐壓射
沖頭作用于單位面積金屬液面上的壓力。
P ﹕壓射比壓( Pa ) P= F 4F F: 壓射壓力(N)
A πd 2 d ﹕壓室直徑 (m) A﹕沖頭截面積( m 2 )
壓射比壓與壓射壓力成正比﹐與壓射沖頭的截面積成反比。
鋅合金的 壓射比壓
壁厚 =<3mm 30MPa 簡單 40MPa 復雜
壁厚 >3mm 50MPa 簡單 60MPa 復雜
有害雜質元素:鐵(Fe),硅(Si),鉛(Pb),鎘(Gd),錫(Sn)
來源於鋁
來源於鋅
2024/2/1
压铸模具设计基础知识
五.壓鑄合金及其性能
2024/2/1
压铸模具设计基础知识

压铸模具设计基础知识一、概述压铸模具是用于压铸工艺的模具,在金属、塑料等材料的制品生产过程中起到关键作用。
压铸模具的设计质量直接影响产品的质量和生产效率。
本文将介绍压铸模具设计的基础知识,包括设计原则、材料选择、结构设计等内容。
二、设计原则1.功能性原则压铸模具应该符合产品的设计要求,能够满足产品的结构、尺寸、表面质量等要求。
设计过程中需要充分考虑产品的功能性需求,确保模具能够满足生产要求。
2.可制造性原则在设计压铸模具时,需要考虑到模具的加工工艺和生产成本。
设计应尽量简化,避免复杂的结构和加工工艺,以降低生产成本。
3.可靠性原则压铸模具在长期使用中需要具有稳定可靠的性能。
设计中需要考虑模具的寿命、耐磨性等因素,确保模具能够长时间稳定运行。
4.易维护性原则模具在使用过程中可能会有损坏或磨损,设计时需要考虑模具的易维护性,便于维修和更换受损部件。
三、材料选择压铸模具的材料选择直接影响模具的寿命和性能。
常用的模具材料包括工具钢、合金钢、硬质合金等。
在选择材料时需要考虑以下因素:1.硬度模具材料应具有足够的硬度和强度,能够抵抗压力和磨损,确保模具的稳定性和寿命。
2.热稳定性压铸过程中温度较高,模具材料需要具有良好的热稳定性,不易变形或烧损。
3.耐磨性压铸模具在长期使用中会有磨损,需要选择耐磨性好的材料,延长模具的使用寿命。
4.耐蚀性部分压铸过程中会有化学物质接触,模具材料需要具有良好的耐腐蚀性,避免腐蚀损坏。
四、结构设计压铸模具的结构设计直接影响产品质量和生产效率。
在设计时需要考虑以下因素:1.分型设计合理的分型设计能够提高产品的成型效率和质量,减少缺陷产生。
分型设计应考虑产品的结构特点和成型过程中的收缩变形。
2.冷却系统设计冷却系统设计影响压铸过程中的温度控制和冷却速度,直接影响产品的组织和性能。
设计时应考虑冷却系统的布局和冷却介质的选择。
3.排气系统设计在压铸过程中需要排除模具内的气体,避免气泡和气孔产生。
压铸工艺流程中的模具设计要点

压铸工艺流程中的模具设计要点压铸是一种常用的金属加工工艺,通过将熔融金属注入模具中,并在固化后取出成型件。
模具设计是整个压铸工艺中的关键环节,决定了成型件的质量和生产效率。
本文将从模具结构设计、材料选择和加工工艺三个方面讨论压铸工艺流程中的模具设计要点。
一、模具结构设计要点1. 合理选择模具结构模具结构的设计应根据产品的形状、尺寸和压铸工艺要求进行合理选择。
一般常见的模具结构包括单腔、多腔、合模和分模等。
对于形状复杂的产品,可以采用多腔结构来提高生产效率。
对于尺寸较大的产品,可以考虑采用合模结构来减少模具成本。
2. 考虑产品的冷却和顶针装置在模具设计中,需要考虑产品的冷却和顶针装置。
冷却系统的设计应能够有效地排除熔融金属的热量,以确保成型件的质量。
顶针装置的设计应满足产品的要求,并保证顶针在压铸过程中的精确位置。
3. 设计合理的浇口和溢流槽浇口和溢流槽是模具设计中的重要组成部分。
设计浇口时应考虑熔融金属的流动性和冷却速度,并确保浇口与产品的结合处处于合适的位置。
溢流槽的设计应考虑金属液体的顺利流动,以避免产生气体和杂质。
二、材料选择要点1. 选择耐磨耐热的材料模具在压铸过程中需要承受高温和高压的作用,因此材料的选择至关重要。
一般采用耐磨耐热的工具钢或合金钢作为模具材料,以保证模具的使用寿命和成型件的质量。
此外,还应考虑材料的加工性能和可靠性。
2. 考虑材料的强度和刚性模具的结构设计需要兼顾材料的强度和刚性。
材料的强度直接影响到模具的承载能力,而刚性则影响到模具的稳定性和精度。
因此,在模具设计中应根据产品的要求选择合适的材料,并进行合理的加工和热处理,以提高模具的性能。
三、加工工艺要点1. 精确计算和控制成型参数在压铸工艺中,成型参数的精确计算和控制是保证成型件质量和加工效率的关键。
成型参数包括注射速度、压力、温度和冷却时间等。
合理选择和控制这些参数,可以避免产生缺陷和变形,提高成型件的精度和表面质量。
压铸模具基础知识介绍ppt

对采购的材料进行质量检验,确保材料符合设计 要求。
材料储存与保管
对检验合格的原材料进行储存和保管,确保材料 在制造过程中不受损坏或变质。
模具加工阶段
粗加工
对模具毛坯进行粗加工,去除多余 的材料,初步形成模具的形状和结 构。
中间检查
对粗加工完成的模具进行中间检查 ,确保模具的形状和结构符合设计 要求。
02
压铸模具制造过程
设计阶段
1 2
模具设计
根据产品需求,进行模具的结构设计,确定模 具的形状、结构、尺寸等参数。
模具材料选择
根据模具的使用条件和寿命要求,选择合适的 材料,如铸铁、铸钢、铝合金等。
3
模具零件的标准化
对模具的零件进行标准化设计,以提高制造效 率和降低成本。
备料阶段
材料采购
根据模具设计要求,采购合适的材料,如钢材、 铝合金等。
04
压铸模具的使用与维护
压铸模具的使用方法
模具安装
根据模具尺寸、形状和压铸机型 号,正确安装模具,确保定位准 确、紧固可靠。
模具预热
使用前对模具进行预热,提高模 具温度,降低成型难度,提高产 品质量。
模具调试
根据产品要求和工艺参数,调试 模具压力、温度、时间等参数, 确保压铸件质量符合要求。
压铸模具的维护保养
压铸模具基础知识介绍ppt
xx年xx月xx日
contents
目录
• 压铸模具概述 • 压铸模具制造过程 • 压铸模具材料选择与处理 • 压铸模具的使用与维护 • 压铸模具的设计案例分析 • 总结与展望
01
压铸模具概述
定义与特点
定义
压铸模具是一种金属铸造工艺中使用的模具,通过将熔融的 金属注入到模具型腔中,冷却凝固后得到所需形状的零件。
压铸工艺及压铸模具设计要点

压铸工艺及压铸模具设计要点摘要:压铸机、模具与合金三者,以压铸件为本,压铸工艺贯穿其中,有机地将它们整合为一个有效的系统,使压铸机与模具得到良好的匹配,起到优化压铸件结构,优选压铸机、优化压铸模设计、提高工艺工作点的灵活性的作用,从而为压铸生产提供可靠保证。
所以,压铸工艺寓于模具中之说,内涵之深不言而喻。
关键词:压铸机;模具;压铸工艺;模具设计The Main Points of Die Casting Process andDie Casting Die DesignPAN Xian-Zeng, LIU Xing-fuAbstract: The die casting machine, die and alloy, the three on the basis of die castings, running through with the die casting process forms organically a whole and an effective system. Making the machines well to mate with dies, optimization of die casting construction, optimization of selecting die casting machine, optimization of die design and improving the flexibility of die casting process conveys in the die, this has a profound intension.Key words: die casting machine; die; die casting process; die design1 压铸机—模具—合金系统压铸机、模具和合金这三个因素,在压铸件生产过程中,它们构成了一个系统,即压铸机-模具—合金系统,它是以压铸件为本,工艺贯穿其中,赋予系统活力与效率,而模具则是工艺进入系统的平台。
压铸模具基础知识
模具生产一定数量后,应进行去应力回火 热处理,以便及早消除内应力,此是提高模具 寿命的一种方法,去应力回火温度比原有回火 温度低30~50℃,对中小型模型回火热处理可 在10000件以上,对较大型模具回火热处理可 在5000次左右进行。
MG 模具的分解顺序图.
※ 组装时分解的逆向作业.
ZN, MG 模具的盐酸洗涤顺序图.
(8)、检查试啤的材料是否符合零件图纸要求。
第二部分 压铸模维修和保养
压铸模在压铸生产中精度高、造价大、用料 多、制造周期长,是重要的工艺装备, 模具 使用和保养的好坏对铸件质量和模具的使用 寿命影响极大,模具保养和维护的目的是提 高压铸生产效率、降低生产成本,增加模具的 使用寿命。
(2)动模 :
动模是压铸模的另一个重要组成部分, 动模是和定 模形成压铸模成型部分的另一个整体,它一般固定 在压铸机中板上,随中板作并合运动,与定模部分 分开合拢。一般抽芯机构和顶出机构大多在这个部 分。
三 加热和冷却系统: 压铸模具在压铸生产前应进行充分地预热,并在压 铸过程中保持在一定温度范围内。 压铸生产中模具的温度由加热与冷却系统进行控制 和调节,以保持模具的热平衡。 1、 模具加热的方法。 (1)、用燃气加热。 (2)、用模具温度控制装置加热。 (3)、用电热棒加热。 2、 模具的预热温度
MG 模具的移动及保管
※ 模具移动时左,上警戒其他作业者及 躲开妨碍物的注意的作业事项
谢 谢
锌合金模具 140℃~180℃
铝合金模具 150℃~200℃ 镁合金模具 170℃~210℃ 铜合金模具 250℃~300℃
《压铸基本知识》课件
压铸技术逐渐应用于航空航天领域,如飞机零部件、卫星结构件等 。
环保要求
1 2
环保法规
随着全球环保意识的提高,各国政府对压铸行业 的环保法规日益严格,要求企业采取有效措施降 低环境污染。
节能减排
压铸企业应积极采取节能减排措施,如余热回收 、废弃物再利用等,以降低能耗和减少排放。
3
绿色生产
项参数。
02
操作过程
按照工艺流程,依次完成合模 、填充、增压、保压、开模等 步骤,确保压铸件的质量和稳
定性。
03
注意事项
注意安全操作,避免烫伤和机 械伤害,同时要定期维护和保 养设备,确保设备的正常运行
和使用寿命。
03
压铸模具
模具设计
03
模具结构设计
分模面选择
浇注系统设计
根据产品需求,设计合理的模具结构,确 保产品成型效果和生产效率。
推广绿色生产技术,使用环保材料和工艺,从源 头减少污染物的产生,促进压铸行业的可持续发 展。
THANKS
模具维护
定期检查
维修与更换
定期对模具进行检查,确保其处于良 好状态。
Hale Waihona Puke 对于损坏的模具部件,应及时进行维 修或更换。
保养与润滑
定期对模具进行保养和润滑,延长其 使用寿命。
04
压铸工艺
压铸温度
压铸温度
压铸过程中,模具和金属液的温 度是影响压铸件质量的重要因素 。合适的温度可以提高金属液的 流动性,减少气孔和裂纹等缺陷
《压铸基本知识》ppt课件
目录
• 压铸简介 • 压铸机 • 压铸模具 • 压铸工艺 • 压铸产品缺陷及防止措施 • 压铸行业发展趋势
压铸工艺与模具设计
压铸工艺与模具设计引言压铸工艺是一种常用的铸造工艺,在工业制造中广泛应用。
通过将熔化的金属注入到模具中进行冷却凝固,最终得到所需的金属零件。
本文将介绍压铸工艺的基本原理、流程以及模具设计的要点和考虑因素。
压铸工艺的原理和流程压铸工艺主要通过将金属材料加热到熔化状态,并将熔融金属注入到模具中,通过冷却凝固来得到所需的金属零件。
下面是一般的压铸工艺流程:1.准备模具:设计和制造适合所需零件的模具,通常使用铸造合金或钢材制作模具。
2.准备金属材料:根据需求选择合适的金属材料,并将其加热到熔化温度。
3.熔融金属注入:将熔化的金属材料注入到模具中,通常使用压铸机进行注入。
4.冷却凝固:待金属材料注入模具后,通过冷却凝固使金属快速凝固。
5.脱模:将凝固的金属零件从模具中取出。
6.毛坯处理:对取出的凝固金属零件进行表面处理和去除余料等工艺。
7.检验和加工:对凝固金属零件进行检验,如尺寸、重量、表面质量等,并根据需要进行进一步的加工。
模具设计的要点和考虑因素模具设计是压铸工艺中至关重要的一环,直接影响到最终零件的质量和性能。
以下是模具设计的一些要点和需要考虑的因素:1.零件结构:根据零件的结构和尺寸设计合适的模具,包括模具的外形、内腔和结构等方面。
2.材料选择:选择适合的模具材料,考虑到耐磨性、导热性和耐腐蚀性等因素。
3.流道设计:合理设计模具内的金属流道,以确保熔融金属能够均匀地填充整个模具腔体,并减少浇注过程中的气泡和杂质。
4.冷却系统设计:设计合理的冷却系统,以加速金属的凝固过程,并减少零件内部的应力和变形。
5.脱模设计:设计合适的脱模系统,以便顺利地将凝固的金属零件从模具中取出。
6.模具维护和修复:考虑到模具的使用寿命,设计易于维护和修复的结构,以延长模具的使用寿命。
结论压铸工艺是一种常用的铸造工艺,通过将熔化的金属注入到模具中进行冷却凝固,可以得到所需的金属零件。
模具设计是压铸工艺中关键的一环,直接影响到最终零件的质量和性能。
《压铸模讲义》课件
压铸模技术的创新与突破
3D打印技术
利用3D打印技术生产压铸模,提 高模具精度和生产效率。
新型材料应用
采用高强度、耐高温的新型材料制 作压铸模,提高模具使用寿命。
智能化技术
引入人工智能、机器学习等技术, 实现压铸模的智能化设计和生产。
压铸模在智能制造领域的应用
自动化生产
利用机器人和自动化设备进行压铸模的生产和加 工,提高生产效率。
通过合理的热处理工艺,提高模具材料的机 械性能和使用寿命。
检测与验收
对制造完成的模具进行检测和验收,确保其 符合质量要求。
04
压铸模的使用与维护
BIG DATA EMPOWERS TO CREATE A NEW
ERA
压铸模的使用规范
使用前检查
在使用压铸模前,应检查模具是否完好无损,各 部件是否正常工作。
为主,精度和寿命较低。
发展阶段
02
随着科技的发展,模具材料逐渐由木材转向钢材,模具设计和
制造技术也得到了提升。
成熟阶段
03
现代压铸模技术已经相当成熟,应用范围广泛,可满足各种复
杂铸件的生产需求。
02
压铸模的设计
BIG DATA EMPOWERS TO CREATE A NEW
ERA
压铸模设计的基本原则
裂纹
检查模具材料是否合格,更换合格材 料;检查模具热处理是否到位,加强
热处理工艺控制。
卡滞
检查模具各部件是否正常工作,调整 模具间隙;检查润滑系统是否正常工 作,补充润滑油。
精度下降
检查模具安装是否正确,调整安装精 度;检查压铸机参数是否正常,调整 参数。
05
压铸模的未来发展
- 1、下载文档前请自行甄别文档内容的完整性,平台不提供额外的编辑、内容补充、找答案等附加服务。
- 2、"仅部分预览"的文档,不可在线预览部分如存在完整性等问题,可反馈申请退款(可完整预览的文档不适用该条件!)。
- 3、如文档侵犯您的权益,请联系客服反馈,我们会尽快为您处理(人工客服工作时间:9:00-18:30)。
實際比壓應等于計算比壓乘以壓力損減系數K(約0.88). 比壓大小可通過調節壓鑄機的壓射力和更換不同直徑的 壓室來實現。
2020/8/1
六.壓鑄工藝
(二)充填速度及其選擇
充填速度是指熔融金屬地壓射沖頭壓力的作用下﹐通過內澆口時的線速度。
影響充填速度的因素有壓射速度﹐壓射比壓和內澆口截面積等。
根據等流量連續方程
鎂的加入可 ☺ 細化合金組織,從而增加壓鑄件的強度 ☺ 改善合金抗晶間腐蝕的能力 ☺ 改善合金的抗磨損性能 降低合金的流動性 易在合金熔融狀態下氧化損耗
2020/8/1
五.壓鑄合金及其性能
熱室壓鑄鋅合金中的合金元素
---雜質元素-鎘,鉛
鎘在合金中的含量絕對不能>0.003% 降低合金的機械性能 造成合金晶間腐蝕 鉛在合金中的翎量絕對不能>0.003% 降低合金的時效機械性能 當含量超過0.005%時,造成合金晶間腐蝕
2020/8/1
五.壓鑄合金及其性能
2020/8/1
五.壓鑄合金及其性能
熱室壓鑄鋅合金中的合金元素 ---合金元素-鋁
鋁的加入可`
☺ 降低合金對鐵的反應能力,因此降低了合金對鋅鍋,鵝 頸及模具的侵蝕 ☺ 降低合金的熔點 ☺ 增加合金的流動性能 ☺ 改善合金的機械性能 產生Fe2 Al5浮渣,造成其含量的下降
压铸模具设计基础知识
2020/8/1
一. 鑄造工藝
砂型鑄造 金屬型鑄造
特種鑄造
壓力鑄造 重力鑄造 低壓鑄造 熔模鑄造 陶瓷型鑄造 連續鑄造 離心鑄造 真空吸鑄
永久型鑄造
2020/8/1
二. 壓鑄概論
❖ 壓力鑄造概念: (鋁,錫,鋅,镁,鉛,銅,合金) 即將溶融合金在高壓,高速條件下充型並在高壓下冷卻凝固成型的一 種精密鑄造方法, 簡稱壓鑄,其最終產品是壓鑄件.
2. 減小充型反壓力,成型好,表面質量得到改善; 3. 可減小或不用排氣系統; 4. 結構復雜﹐成本高.
一般只適用于薄壁,流程較長的鑄件,而對壁厚不均,較厚凸台的 鑄件,則加重縮松. (二)充氧壓鑄(P.F法壓鑄)又稱無氣孔壓鑄(既氣孔無氧氣) 特點﹕1. 消除氣孔,提高力學性能; 2. 可對充氧壓鑄件進行熱處理,強度增高30%,屈服強度增強100%; 3. 充氧壓鑄可在200~300。C環境工作,可焊接; 4. 與真空相比,結構簡單,投資少,操作方便; 5. 操作時應注意安全.
A1 V1 = A2 V2
V2= V1A1 A2
πD 2 V1 4A2
V1 壓射速度( m/s)
V2 充填速度( m/s)
A1
壓室沖頭截面積(m 2)
A2
內澆口截面積
D
壓室沖頭直徑
在設計壓鑄模時﹐內澆口的設置一般應預留出修模位置﹐以便在試模時修整 截面大小。匿內澆口面積過小﹐充型壓力損失增加﹐加大壓鑄機負荷則充填速度 過大﹐液態金屬呈噴射狀進入型 腔﹐壓鑄件內部組織氣孔量增加﹐高速沖蝕型 腔﹐影響壽命。當澆口尺寸足夠大以后﹐充填速度控制主要是通過調節壓射速度 來實現。
2020/8/1
六.壓鑄工藝
沖頭空行程壓射速度﹕ (m/s) 鋅合金 ﹕ 0.3~0.5 鋁﹕ 0.5~1.1
伯努力方程
V=
2P
ρ
(理想)
V ﹕流體速度( m/s )
P ﹕流體壓力( Pa )
ρ ﹕流體密度(
3
Kg/m
)
V2 =μ
2P (因粘性﹐表面張力﹐內磨擦) ρ
μ﹕阻力系數
鋅合金 = 55.4V2 P
(三)再噴射 (四)補縮金屬流(保壓時間)
2020/8/1
四.成型工藝
(一)壁厚 鋅合金: 0.3MM (最小) 鋁﹕0.5MM 最小孔徑: 0.7MM 螺紋螺距﹕0.75MM 最大壁厚與最小壁厚之比不要大于3﹕1(應設計壁厚 均勻﹐保証足夠強度與剛度的前提)
2020/8/1
四.成型工藝
(二)加強肋﹕大于或等于2.5MM﹐會降低抗拉強度﹐易產生氣孔﹐ 縮孔。
壓
t2:開始進入型腔﹐因澆口急減﹐阻力 力
F
增大﹐F2>F1,達到高速充填
t3:(快速增壓階段)快速充填直止充滿
型腔最大值F3為壓射壓力
t4:F4靜壓力﹐對鑄件壓實
時間t
(壓射力與時間關係曲線見右圖)
2020/8/1
六.壓鑄工藝
定義2﹕壓射壓力就是在充模剛結束時壓射沖頭作用在金屬液面上的力。 定義3﹕壓射壓力是以壓射比壓來表示﹐壓射比壓就是充模結束時﹐壓射
2020/8/1
七.特殊壓鑄工藝
(三)精.速.密壓鑄(ACURAD) 特點﹕1. 雙沖頭壓鑄;
2. 克服卷氣,收縮產生針孔; 3. 內澆口采取定向凝固(下方),便于補縮. (四)半固態壓鑄 合金所呈現狀態﹕樹枝狀晶體 網狀 打碎呈球形團塊后壓鑄
2020/8/1
八.黑色金屬壓鑄
灰鑄鐵,可鍛鑄鐵﹐球墨鑄鐵﹐碳鋼﹐不銹鋼﹐合金 鋼都屬于黑色金屬
熱室壓鑄鋅合金中的合金元素 ---雜質元素-硅
硅在鋅合金中的含量絕對不能0.02%, 提高鋅合金的脆性轉變溫率~20度 降低鋅合金的可加工性
2020/8/1
五.壓鑄合金及其性能
熱室壓鑄鋅合金中的合金元素
----பைடு நூலகம்論
熱室壓鑄用鋅合金必須是以特高純度鋅為 基礎,加入特高純度鋁,鎂和銅
嚴格控制壓鑄溫度,避免攪拌 水口料重熔時,一定要嚴格控制重熔溫度以 避免鋁和鎂的損耗
2020/8/1
六.壓鑄工藝
(三)合金的澆注溫度 溶點﹕ 389。 C
澆鑄溫度﹕ 425。 C
逐層
混 合 糊狀凝固
(四)模具溫度 簡單﹕ 180。C~200。C (連續工作)模具預熱 復雜﹕ 190。C~220。C (連續工作)模具預熱
130。C~180。C 150。C~200。C
(五)充填時間與持壓時間
設計原則﹕1﹐受力大﹐減小壁厚﹐改善強度. 2﹐對稱布置﹐壁厚均勻﹐避免縮孔氣孔. 3﹐與料流方向一致﹐避免亂流. 4﹐避免在肋上設置任何零部件.
2020/8/1
四.成型工藝
(三)脫模斜度
β
2020/8/1
四.成型工藝
(四)圓角
2020/8/1
四.成型工藝
(五)孔 鋅: 0.8~1.5(最小直徑) 鋁: 2.0~2.5(最小直徑)
2020/8/1
五.壓鑄合金及其性能
熱室壓鑄鋅合金中的合金元素
---雜質元素-鐵 鋅合金中鐵元素含不能>0.02%,鐵
元素可:
☺ 增加合金的硬度 但同時 增加合金的脆性 和合金中的鋁發生反應形成Al5Fe2金屬間化合物,
造成鋁元素的損耗並形成浮渣 在壓鑄件中出現硬點
2020/8/1
五.壓鑄合金及其性能
我們經常遇到這樣的情況,工件剛壓鑄成型時,其表面 質量一切正常.可是,在室溫下存放數星期或幾個月後,表面 出現鼓泡.
2020/8/1
五.壓鑄合金及其性能
熱室壓鑄鋅合金中的合金元素
---雜質元素-錫
錫在鋅合金錠中的含量絕對不能>0.001%, 在太鑄件中的含量不能>0.002%
造成合金晶間腐蝕 降低合金的抗沖擊性能 降低合金的抗拉伸強度 引起尺寸不穩定
2020/8/1
五.壓鑄合金及其性能
熱室壓鑄鋅合金中的合金元素 ----合金元素-銅
銅的加入可
☺ 增加合金的強度 ☺ 提高合金的硬度 ☺ 改善合金的抗磨損性能 降低合金的可延伸性 造成壓鑄件的尺寸不穩定性(產生時效脹大)
(當銅的含量>1.25%時)
2020/8/1
五.壓鑄合金及其性能
熱室壓鑄鋅合金中的合金元素 ---合金元素-鎂
特點﹕熔點高,壽命短. 要求﹕1. 模溫:250~300。C;
2. 澆鑄溫度:鑄鐵1300~1350。C 中碳1440~1460。C 合金1550~1560。C;
3. 內澆口厚度為3~5mm,環形澆口多.
2020/8/1
五.壓鑄合金及其性能
(一)壓鑄合金
鋁(Al),鋅(Zn),镁(Mg),鉛(Pb),錫(Sn),銅(Gu)
(二)壓鑄合金之鋅合金
熱室壓鑄用鋅合金中
有效合金元素:鋁(Al),銅(Gu),鎂(Mg)
有害雜質元素:鐵(Fe),硅(Si),鉛(Pb),鎘(Gd),錫(Sn)
來源於鋁
來源於鋅
2020/8/1
五.壓鑄合金及其性能
2020/8/1
六.壓鑄工藝
影響金屬液充填成型的因素很多﹐主要有﹕壓射壓力﹐壓射速度﹐充填時間﹐ 壓鑄模溫。
(一)壓射壓力的概念
定義1﹕壓射力指壓射沖頭作用于金屬液面上的力。
(這個力在壓鑄過程中不是恆定不變的,它大小隨不同的壓鑄階段變化而改變.)
壓射液壓缸 壓射沖頭 壓室熔液 模具型腔
t1:F1為克服磨擦力(壓室中)
金屬液自開始進入模具型腔到充滿所需的時間稱為充模時間
因素﹕大小﹐復雜程度﹐澆口處的面積﹐充填速度.
t=
m ρA 2V
m-- 鑄件重量 (kg) ρ -- 流體密度(Kg/m3)
2020/8/1
A2--內澆口截面積 V--充填速度
七.特殊壓鑄工藝
產生氣孔疏松的原因:高速充模氣體末完全排出及凝固收縮得不到充分補縮。 (一)真空壓鑄 特點﹕1. 顯著減少氣孔,組織更致密,提高了力學性能;
卧式
壓室
❖ 熱室壓鑄機的壓室通常浸入坩鍋的
金屬液中,如圖示.
2020/8/1
三. 壓鑄制程溶湯的流動方式
(一)噴射及噴射流
壓力
運動能(碰壁)
熱能和壓力
由噴射﹑噴射流轉變為壓力流
2020/8/1
三. 壓鑄制程溶湯的流動方式
(二)壓力流
因沖撞,磨擦和氣體阻力等(抽象),運動能量耗盡(常發生在加強筋, 凸台,遠離澆口之部位),具有接受後繼金屬液中供給的壓力能,從而使金 屬液沿著型腔內壁前進的特性.利用這特性,可便以型腔排氣.在壓力流充 填的部位,匯集著由噴射和噴射流所充填部分的氣體﹐必須開設排氣槽.